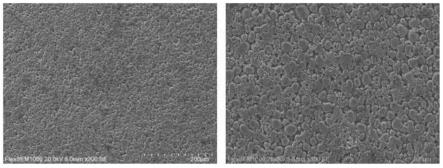
1.本技术涉及锂离子电池技术领域,尤其涉及复合导电剂、电池浆料、锂离子电池和制备方法。
背景技术:2.目前锂离子电池导电剂分散通常是在匀浆工艺阶段进行,如图1所示。在匀浆阶段进行导电剂的分散会总体延长电池的制备时间,并且由于分散时间的限制会使导电剂分散不够彻底从而在涂布、辊压后出现导电剂的团聚和黑点,影响电池的性能。尤其是当浆料中使用两种或两种以上的导电剂时,常规的匀浆阶段分散将变得更加困难。
技术实现要素:3.本技术的目的在于提供一种复合导电剂,旨在解决现有锂离子电池导电剂分散不够彻底的问题。
4.为实现以上目的,本技术提供一种复合导电剂,各组分以质量百分比计包括:导电剂1%-15%、分散剂0.1%-5%、悬浮剂0.001%-5%、溶剂80%-98%。
5.优选地,所述导电剂包括一种或多种碳系无机物;所述溶剂包括n-甲基吡咯烷酮;所述分散剂包括阳离子型聚合分散剂、阴离子型聚合分散剂、非离子型聚合分散剂中的任一种;所述悬浮剂为油性悬浮剂。
6.优选地,所述碳系无机物包括炭黑、碳纳米管、纳米石墨微片中的任一种或多种;
7.优选地,所述阳离子型聚合分散剂包括聚合酰胺;
8.优选地,所述油性悬浮剂包括高乙烯基硅油。
9.本技术还提供一种上述的复合导电剂的制备方法,包括:
10.在所述溶剂中加入所述导电剂,进行第一低速搅拌;
11.第一低速搅拌完成后,在真空环境下进行第一高速搅拌得到预混液;
12.所述预混液在干燥气体环境下加入所述分散剂和所述悬浮剂,并进行第二低速搅拌;
13.第二低速搅拌完成后,在真空环境下进行第二高速搅拌得到所述复合导电剂。
14.优选地,所述第一高速搅拌的温度为25~30℃,所述第二高速搅拌的温度为40~50℃。
15.优选地,所述第一低速搅拌和所述第二低速搅拌的速度分别为10~100rpm,搅拌时间分别为10~20min。
16.优选地,所述第一高速搅拌和所述第二高速搅拌的速度分别为1800~2400rpm,所述第一高速搅拌时间为1~3h,所述第二高速搅拌时间为3~5h。
17.本技术还提供一种电池浆料,包括上述的复合导电剂。
18.本技术还提供上述的电池浆料的制备方法,包括:
19.将粘结剂和溶剂混合搅拌,得到胶液;
20.将所述胶液、所述复合导电剂、活性物质混合搅拌,得到所述电池浆料。
21.本技术还提供一种锂离子电池,包括上述的电池浆料。
22.与现有技术相比,本技术的有益效果包括:
23.本技术提供的复合导电剂由于加入一定的分散剂,使导电剂在分散时可以减少活化能过高引起的团聚现象,并且配合机械分散可以进一步降低分散后存在的团聚。
24.本技术提供的复合导电剂预完成导电剂的分散,在电池浆料制备时可直接将已经分散完成的复合导电剂加入到胶液中与活性物质混合搅拌,省去了导电剂在匀浆过程中的分散时间,有效缩短了电池浆料的制备时间、提升了浆料固含量、降低了极片细度和电池内阻。与现有技术相比,本技术使用的浆料制备方法可有效完成导电剂的完全分散,提升分散效果。
附图说明
25.为了更清楚地说明本技术实施例的技术方案,下面将对实施例中所需要使用的附图作简单地介绍,应当理解,以下附图仅示出了本技术的某些实施例,因此不应被看作是对本技术范围的限定。
26.图1为现有的锂离子电池导电剂分散示意图;
27.图2为本技术的锂离子电池导电剂分散示意图;
28.图3为对比例1的电池浆料的细度图;
29.图4为实施例3的电池浆料的细度图;
30.图5为对比例1的正极极片辊压后的sem图;
31.图6为实施例3的正极极片辊压后的sem图;
32.图7为本技术的复合导电剂的制备流程示意图。
具体实施方式
33.如本文所用之术语:
[0034]“由
……
制备”与“包含”同义。本文中所用的术语“包含”、“包括”、“具有”、“含有”或其任何其它变形,意在覆盖非排它性的包括。例如,包含所列要素的组合物、步骤、方法、制品或装置不必仅限于那些要素,而是可以包括未明确列出的其它要素或此种组合物、步骤、方法、制品或装置所固有的要素。
[0035]
连接词“由
……
组成”排除任何未指出的要素、步骤或组分。如果用于权利要求中,此短语将使权利要求为封闭式,使其不包含除那些描述的材料以外的材料,但与其相关的常规杂质除外。当短语“由
……
组成”出现在权利要求主体的子句中而不是紧接在主题之后时,其仅限定在该子句中描述的要素;其它要素并不被排除在作为整体的所述权利要求之外。
[0036]
当量、浓度、或者其它值或参数以范围、优选范围、或一系列上限优选值和下限优选值限定的范围表示时,这应当被理解为具体公开了由任何范围上限或优选值与任何范围下限或优选值的任一配对所形成的所有范围,而不论该范围是否单独公开了。例如,当公开了范围“1~5”时,所描述的范围应被解释为包括范围“1~4”、“1~3”、“1~2”、“1~2和4~5”、“1~3和5”等。当数值范围在本文中被描述时,除非另外说明,否则该范围意图包括其端
值和在该范围内的所有整数和分数。
[0037]
在这些实施例中,除非另有指明,所述的份和百分比均按质量计。
[0038]“质量份”指表示多个组分的质量比例关系的基本计量单位,1份可表示任意的单位质量,如可以表示为1g,也可表示2.689g等。假如我们说a组分的质量份为a份,b组分的质量份为b份,则表示a组分的质量和b组分的质量之比a:b。或者,表示a组分的质量为ak,b组分的质量为bk(k为任意数,表示倍数因子)。不可误解的是,与质量份数不同的是,所有组分的质量份之和并不受限于100份之限制。
[0039]“和/或”用于表示所说明的情况的一者或两者均可能发生,例如,a和/或b包括(a和b)和(a或b)。
[0040]
本技术提供一种复合导电剂,各组分以质量百分比计包括:导电剂1%-15%、分散剂0.1%-5%、悬浮剂0.001%-5%、溶剂80%-98%。
[0041]
其中,导电剂包括一种或多种碳系无机物,所述碳系无机物包括炭黑、碳纳米管、纳米石墨微片中的任一种或多种。导电剂的质量百分比例如可以为(1、2、3、4、5、5.5、6、6.5、7、7.5、8、8.5、9、9.5、10、10.5、11、11.5、12、12.5、13、13.5、14、14.5或15)%,或1%-15%之间的任一值。
[0042]
其中,分散剂包括阳离子型聚合分散剂、阴离子型聚合分散剂、非离子型聚合分散剂中的任一种。优选地,所述阳离子型聚合分散剂包括聚合酰胺。其中,分散剂的质量百分比例如可以为(0.1、0.5、1、1.5、2、2.5、3、3.5、4、4.5或5)%,或0.1%-5%之间的任一值。
[0043]
其中,悬浮剂为油性悬浮剂。优选地,所述油性悬浮剂包括高乙烯基硅油。悬浮剂的质量百分比例如可以为(0.001、0.01、0.05、0.1、0.5、1、2、3、4或5)%,或0.001%-5%之间的任一值。
[0044]
其中,所述溶剂为n-甲基吡咯烷酮。溶剂的质量百分比例如可以为(80、80.5、81、81.5、82、82.5、83、83.5、84、84.5、85、85.5、86、87、88、89、90、91、92、93、94、95、96、97或98)%,或80%-98%之间的任一值。
[0045]
本技术还提供一种上述的复合导电剂的制备方法,请参阅图7,包括:
[0046]
s100:在所述溶剂中加入所述导电剂,进行第一低速搅拌。
[0047]
具体的,所述第一低速搅拌的速度为10~100rpm,搅拌时间为10~20min。例如第一低速搅拌的速度可以为(10、20、30、40、50、60、70、80、90或100rpm,或10~100rpm之间的任一值。第一低速搅拌的搅拌时间可以为(10、11、12、13、14、15、16、17、18、19或20)min,或10~20min之间的任一值。
[0048]
s200:第一低速搅拌完成后,在真空环境下进行第一高速搅拌得到预混液。
[0049]
具体的,真空环境的气压为-1mpa~-0.01mpa,例如可以为(-1、-0.9、-0.8、-0.7、-0.6、-0.5、-0.4、-0.3、-0.2、-0.1、-0.09、-0.08、-0.07、-0.06、-0.05、-0.04、-0.03、-0.02或-0.01)mpa,或-1mpa~-0.01mpa之间的任一值。
[0050]
具体的,第一高速搅拌的速度为1800~2400rpm,例如可以为(1800、1850、1900、1950、2000、2100、2200、2300或2400)rpm,或1800~2400rpm之间的任一值。
[0051]
第一高速搅拌的搅拌时间为1~3h,例如可以为(1、1.5、2、2.5或3)h,或1~3h之间的任一值。第一高速搅拌的温度为25~30℃,例如可以为(25、26、27、28、29或30)℃,或25~30℃之间的任一值。
[0052]
s300:所述预混液在干燥气体环境下加入所述分散剂和所述悬浮剂,并进行第二低速搅拌。
[0053]
具体的,所述干燥气体可以为干燥惰性气体,也可以为干燥空气。
[0054]
具体的,所述第二低速搅拌的速度为10~100rpm,搅拌时间为10~20min。例如第二低速搅拌的速度可以为(10、20、30、40、50、60、70、80、90或100rpm,或10~100rpm之间的任一值。第二低速搅拌的搅拌时间可以为(10、11、12、13、14、15、16、17、18、19或20)min,或10~20min之间的任一值。
[0055]
s400:第二低速搅拌完成后,在真空环境下进行第二高速搅拌得到所述复合导电剂。
[0056]
具体的,真空环境的气压为-1mpa~-0.01mpa,例如可以为(-1、-0.9、-0.8、-0.7、-0.6、-0.5、-0.4、-0.3、-0.2、-0.1、-0.09、-0.08、-0.07、-0.06、-0.05、-0.04、-0.03、-0.02或-0.01)mpa,或-1mpa~-0.01mpa之间的任一值。
[0057]
具体的,所述第二高速搅拌的速度为1800~2400rpm/min,例如可以为(1800、1850、1900、1950、2000、2100、2200、2300或2400)rpm/min,或1800~2400rpm/min之间的任一值。
[0058]
所述第二高速搅拌时间为3~5h,例如可以为(3、3.5、4、4.5或5)h,或3~5h之间的任一值。
[0059]
所述第二高速搅拌的温度为40~50℃,例如可以为(40、41、42、43、44、45、46、47、48、49或50)℃,或40~50℃之间的任一值。
[0060]
本技术还提供一种电池浆料,包括上述的复合导电剂。
[0061]
本技术还提供上述的电池浆料的制备方法,包括:
[0062]
将粘结剂和溶剂混合搅拌,得到胶液;
[0063]
将所述胶液、所述复合导电剂、活性物质混合搅拌,得到所述电池浆料。
[0064]
优选地,粘结剂和溶剂的混合比例应满足所述胶液中粘结剂固含量为7%。
[0065]
本技术还提供一种锂离子电池,包括上述的电池浆料。
[0066]
下面将结合具体实施例对本技术的实施方案进行详细描述,但是本领域技术人员将会理解,下列实施例仅用于说明本技术,而不应视为限制本技术的范围。实施例中未注明具体条件者,按照常规条件或制造商建议的条件进行。所用试剂或仪器未注明生产厂商者,均为可以通过市售购买获得的常规产品。
[0067]
实施例1
[0068]
一种锂离子电池复合导电剂,包括以下质量百分比的各组分:炭黑9%;聚合酰胺0.99%;高乙烯基硅油0.01%;n-甲基吡咯烷酮(nmp)90%。
[0069]
该锂离子电池复合导电剂的制备方法:将90%n-甲基吡咯烷酮全部投入到搅拌罐中,加入已烘烤干燥的9%炭黑,低速20rpm/min搅拌15min,降罐后用刮板刮下边缘以及搅拌桨上的物质,升上搅拌罐后抽真空至罐内气压-0.1mpa,开启循环冷却水,保持罐内温度25-30℃,低速30rpm/min/高速2200rpm/min搅拌2h;充入干燥惰性气体至正常大气压后降罐,加入0.99%聚合酰胺和0.01%高乙烯基硅油,低速20rpm/min搅拌15min,降罐后用刮板刮下边缘以及搅拌桨上的物质;抽真空至-0.1mpa,开启循环冷却水,保持罐内温度40~50℃,低速30rpm/min/高速2200rpm/min搅拌4h得到复合导电剂,将粘结剂pvdf和溶剂nmp混
合搅拌得到胶液,将复合导电剂、胶液和三元正极材料混合搅拌得到实施例1的锂离子电池复合导电浆料。
[0070]
实施例2
[0071]
一种锂离子电池复合导电剂,包括以下质量百分比的各组分:炭黑9.5%;聚合酰胺0.49%;高乙烯基硅油0.01%;n-甲基吡咯烷酮90%。
[0072]
该锂离子电池复合导电剂的制备方法:将90%n-甲基吡咯烷酮全部投入到搅拌罐中,加入已烘烤干燥的9.5%炭黑,低速20rpm/min搅拌15min,降罐后用刮板刮下边缘以及搅拌桨上的物质,升上搅拌罐后抽真空至罐内气压-0.1mpa,开启循环冷却水,保持罐内温度25-30℃,低速30/高速2200rpm/min搅拌2h;充入干燥惰性气体至正常大气压后降罐,加入0.49%聚合酰胺和0.01%高乙烯基硅油,低速20rpm/min搅拌15min,降罐后用刮板刮下边缘以及搅拌桨上的物质;抽真空至-0.1mpa,开启循环冷却水,保持罐内温度40~50℃,低速30rpm/min/高速2200rpm/min搅拌4h得到复合导电剂,将粘结剂pvdf和溶剂nmp混合搅拌得到胶液,将复合导电剂、胶液和三元正极材料混合搅拌得到实施例2的锂离子电池复合导电浆料。
[0073]
实施例3
[0074]
一种锂离子电池复合导电剂,包括以下质量份数的各组分:炭黑11.5%;聚合酰胺0.49%;高乙烯基硅油0.01%;n-甲基吡咯烷酮88%。
[0075]
该锂离子电池复合导电剂的制备方法:将88%n-甲基吡咯烷酮全部投入到搅拌罐中,加入已烘烤干燥的11.5%炭黑,低速20rpm/min搅拌15min,降罐后用刮板刮下边缘以及搅拌桨上的物质,升上搅拌罐后抽真空至罐内气压-0.1mpa,开启循环冷却水,保持罐内温度25~30℃,低速30rpm/min/高速2200rpm/min搅拌2h;充入干燥惰性气体至正常大气压后降罐,加入0.49%聚合酰胺和0.01%高乙烯基硅油,低速20rpm/min搅拌15min,降罐后用刮板刮下边缘以及搅拌桨上的物质;抽真空至-0.1mpa,开启循环冷却水,保持罐内温度40~50℃,低速30rpm/min/高速2200rpm/min搅拌4h得到复合导电剂,将粘结剂pvdf和溶剂nmp混合搅拌得到胶液,将复合导电剂、胶液和三元正极材料混合搅拌得到实施例3的锂离子电池复合导电浆料。
[0076]
实施例4
[0077]
一种锂离子电池复合导电剂,包括以下质量份数的各组分:炭黑14.5%;聚合酰胺0.49%;高乙烯基硅油0.01%;n-甲基吡咯烷酮85%。
[0078]
该锂离子电池复合导电剂的制备方法:将85%n-甲基吡咯烷酮全部投入到搅拌罐中,加入已烘烤干燥的14.5%炭黑,低速20rpm搅拌15min,降罐后用刮板刮下边缘以及搅拌桨上的物质,升上搅拌罐后抽真空至罐内气压-0.1mpa,开启循环冷却水,保持罐内温度25~30℃,低30rpm/min/高速2200rpm/min搅拌2h;充入干燥惰性气体至正常大气压后降罐,加入0.49%聚合酰胺和0.01%高乙烯基硅油,低速20rpm/min搅拌15min,降罐后用刮板刮下边缘以及搅拌桨上的物质;抽真空至-0.1mpa,开启循环冷却水,保持罐内温度40~50℃,低速30rpm/min/高速2200rpm/min搅拌4h得到复合导电剂,将粘结剂pvdf和溶剂nmp混合搅拌得到胶液,将复合导电剂、胶液和三元正极材料混合搅拌得到实施例4的锂离子电池复合导电浆料。
[0079]
对比例1
[0080]
如图1所示常规工艺中,粘结剂使用5130聚偏氟乙烯、溶剂使用n-甲基吡咯烷酮,初始粘结剂胶液中粘结剂固含量为7%。导电剂1使用碳纳米管,导电剂2使用炭黑,溶剂:粘结剂:导电剂1:导电剂2质量比为28:1:1:0.6。
[0081]
将初始粘结剂与所有溶剂全部加入,低速20rpm/min搅拌15min;加入碳纳米管悬液,低速20rpm/min搅拌15min,降罐后用刮板刮下边缘以及搅拌桨上的物质,升上搅拌罐后抽真空至罐内气压-0.1mpa,开启循环冷却水,保持罐内温度25~30℃,低速30/min/高速2200rpm/min搅拌2h;充入干燥惰性气体至正常大气压后降罐,得到导电胶液1。
[0082]
导电胶液1加入已烘烤干燥的炭黑,低速20rpm/min搅拌15min,降罐后用刮板刮下边缘以及搅拌桨上的物质,升上搅拌罐后抽真空至罐内气压-0.1mpa,开启循环冷却水,保持罐内温度25~30℃,低速30rpm/min/高速2200rpm/min搅拌2h;充入干燥惰性气体至正常大气压后降罐,得到导电胶液2。
[0083]
将1/2的正极主材加入导电胶液2中,低速20rpm/min搅拌15min,降罐后用刮板刮下边缘以及搅拌桨上的物质,升上搅拌罐不开真空,开启循环冷却水,保持罐内温度25~30℃,低速30rpm/min/高速2200rpm/min搅拌30min,将剩余的1/2的正极主材加入并重复上一部分1/2主材加入后操作。
[0084]
刮板刮下边缘以及搅拌桨上的物质,升上搅拌罐后抽真空至罐内气压-0.1mpa,开启循环冷却水,保持罐内温度25~30℃,低速30/min/高速2200rpm/min搅拌4h;充入干燥惰性气体至正常大气压后降罐,加入适量n-甲基吡咯烷酮(nmp)升罐后真空20rpm/min搅拌30min调节粘度后得到对比例1的正极浆料。
[0085]
性能测试
[0086]
一、固含量的测试方法
[0087]
1、准备测试固含量样品;
[0088]
2、取样,均匀涂抹到干净和干燥的已称取质量的铝箔制平底圆盘,称量涂抹样品后平底圆盘重量,称量精确到0.001g;
[0089]
3、放入120℃或其它商定温度的烘箱内烘烤30min;
[0090]
4、到规定的加热时间后(或直至样品恒重),将盘移入干燥器内,冷却到室温再称重,精确到0.001g;
[0091]
5、测量结束,通过净质量差计算固含量。
[0092]
浆料固含量的提升有利于涂布过程中厚度稳定性控制,可用于高厚度的涂布,并且可减少nmp的使用而降低成本。理论上来说提升固含量需要与粘度匹配,高的固含量会有高的粘度,过高的粘度也不利于涂布。
[0093]
二、内阻测试方法
[0094]
在电池组两端接入放电负载,根据在不同电流i1、i2下的电压变u1、u2来计算内阻值,由e-i1*r=u1、e-i2*r=u2得:r=(u1-u2)/(i2-i1)。
[0095]
浆料内阻降低,有利于电池后续的电化学性能测试。
[0096]
三、细度测试方法
[0097]
1、用溶剂洗浸刮板和刮刀,并用棉纱擦干。
[0098]
2、将符合产品标准粘度的试样用调油刀充分搅匀。
[0099]
3、在刮板细度计的沟槽深部分,滴入试样数滴,以能充满沟槽而略有多余为宜。
[0100]
4、以双手拇指食指及中指持刮刀。横置在刮板细度计上端,使刮刀与刮板细度计表面垂直,以合适的速度将刮刀由沟槽深部向浅部拉过,使漆样充满沟槽而平板上不留有过多余样。
[0101]
5、立即(不超过5秒)横捏细度计并倾斜,使视线与沟槽平面成15-30度角对光观察沟槽中颗粒均匀显露处的刻度值,读数值即所测样之细度。
[0102]
浆料的细度越低,说明分散效果更好,有利于涂布,从而不会在涂布表面出现颗粒。
[0103]
四、正极极片的sem检测
[0104]
sem为电子扫描显微镜,由专业操作员完成,用于观察正极极片的形貌特征。
[0105]
实验结果
[0106]
实施例1制备的锂离子电池复合导电浆料,与现有技术中未进行导电剂预浆料制备方案相比,其固含量提升3%,内阻下降4%,nmp用量减少17%,匀浆工艺时间缩短26%,细度降低66%。
[0107]
实施例2制备的锂离子电池复合导电浆料,与现有技术中未进行导电剂预浆料制备方案相比,其固含量提升2%,内阻下降10%,nmp用量减少11%,匀浆工艺时间缩短26%,细度降低63%。
[0108]
实施例3制备的锂离子电池复合导电浆料,与现有技术中未进行导电剂预浆料制备方案相比,其固含量提升5%,内阻下降13%,nmp用量减少14%,匀浆工艺时间缩短26%,细度降低68%。实施例3的电池浆料的细度拍照结果如图4所示,实施例3的正极极片辊压后sem图片如图6所示。
[0109]
实施例4制备的锂离子电池复合导电浆料,与现有技术中未进行导电剂预浆料制备方案相比,其固含量提升5%,内阻下降6%,nmp用量减少10%,匀浆工艺时间缩短26%,细度降低55%。
[0110]
对比例1的电池浆料的细度拍照结果如图3所示,对比例1的正极极片辊压后sem图片如图5所示。
[0111]
根据实施例1至实施例4相对于对比例1的结果可知,实施例1至实施例4的方案均能够有效提升浆料的固含量,降低内阻,减少nmp用量,降低细度,缩短工艺时间。
[0112]
根据实施例1至实施例4可知,适当的提高导电剂含量可以有效降低内阻,但加入过多导电剂会减少主材的用量,反而影响电池的性能。
[0113]
实施例4中加大了炭黑的用量,使导电浆料的固含量提升,但是大量的炭黑会影响加入主材后的分散,需要加入比实施例3中更多的nmp。
[0114]
最后应说明的是:以上各实施例仅用以说明本技术的技术方案,而非对其限制;尽管参照前述各实施例对本技术进行了详细的说明,本领域的普通技术人员应当理解:其依然可以对前述各实施例所记载的技术方案进行修改,或者对其中部分或者全部技术特征进行等同替换;而这些修改或者替换,并不使相应技术方案的本质脱离本技术各实施例技术方案的范围。
[0115]
此外,本领域的技术人员能够理解,尽管在此的一些实施例包括其它实施例中所包括的某些特征而不是其它特征,但是不同实施例的特征的组合意味着处于本技术的范围之内并且形成不同的实施例。例如,在上面的权利要求书中,所要求保护的实施例的任意之
一都可以以任意的组合方式来使用。公开于该背景技术部分的信息仅仅旨在加深对本技术的总体背景技术的理解,而不应当被视为承认或以任何形式暗示该信息构成已为本领域技术人员所公知的现有技术。