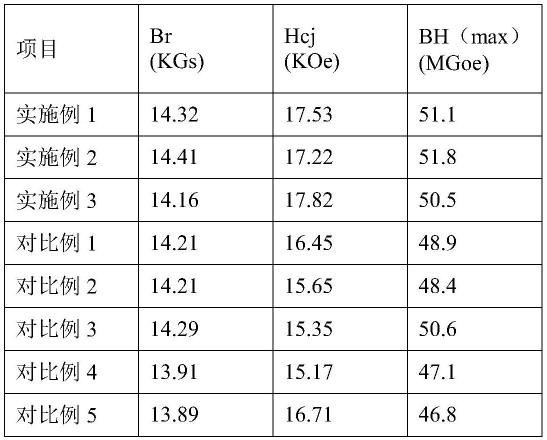
1.本发明涉及一种烧结钕铁硼磁体,尤其是涉及一种高剩磁高矫顽力无重稀土烧结钕铁硼磁体及其制备方法。
背景技术:2.钕铁硼永磁体是现今所知的综合性能最高的稀土永磁材料,故在消费类电子产品、节能家电、医疗设备等领域有着广泛的应用。最近,以混合电动汽车、电动汽车、风力发电为代表的环境友好型产业对钕铁硼永磁体的需求进一步扩大,对钕铁硼永磁体的综合磁性能的要求越来越高,既要有较高的剩磁能以提供足够强的磁场,又要有较高的矫顽力以满足高温条件下的应用。
3.而目前主要是通过引入重稀土(dy、tb及ho等)以提高nd~fe~b主相的磁晶各向异性场,进而提高矫顽力。但随着重稀土元素的加入,磁体的剩磁和磁能积都会不同程度的下降,并且重稀土价格昂贵,通常是轻稀土价格的几倍,极大的提高了产品的制备成本。因此非常有必要开发设计一种不掺有重稀土元素的烧结钕铁硼磁体。
技术实现要素:4.本发明是为了解决现有技术是在通过引入重稀土来提高钕铁硼永磁体矫顽力的同时会导致剩磁和最大磁能积的下降,以及制备成本的迅速上升的问题,提供了一种高剩磁高矫顽力无重稀土烧结钕铁硼磁体,有利于降低烧结钕铁硼磁体的生产成本。
5.本发明还提供了一种高剩磁高矫顽力无重稀土烧结钕铁硼磁体制备方法,工艺步骤简单,可操作性强,适合大批量生产。
6.为了实现上述目的,本发明采用以下技术方案:本发明的一种高剩磁高矫顽力无重稀土烧结钕铁硼磁体,以高剩磁高矫顽力无重稀土烧结钕铁硼磁体总质量计,由质量百分含量2~4%的副相合金和余量的主相合金组成,其中,所述主相合金由以下质量百分含量的成分组成:28~32%pr
25
nd
75
,0.9~1.5%b,0.1~0.5%al,0.05~0.2%zr,0.05~0.3%ti,余量fe;所述副相合金由以下原子百分比的成分组成:55%nd,20%cu,25%ga。本发明中限定副相合金以下原子百分比的成分组成:55%nd,20%cu,25%ga,这样的原子比例是申请人经过大量的理论推演以及试验验证得出的一个最佳比例,在这个比例下,烧结钕铁硼磁体能获得最优的综合磁性能。
7.一种高剩磁高矫顽力无重稀土烧结钕铁硼磁体制备方法,包括以下步骤:
8.(1)制备主相合金:按主相合金的成分组成进行配料,配料后将原料加入真空速凝甩片炉,经熔炼、浇注、冷却结晶后,得速凝薄片。
9.(2)制备副相合金:按副相合金的成分组成进行配料,配料后将原料加入真空熔炼炉,经熔炼、浇注后,得合金钢锭。本发明采用ndcuga合金作为副相合金,在主相合金熔炼以后添加混合以改善晶界相和主相的浸润性,并在主相合金的外延层形成一种非晶的层壳结构,起到弱化主相之间的交换耦合作用,也极大的减少了晶粒的尖角等优先反磁化的区域,
使晶界相的铁磁性弱化,从而实现提高矫顽力的作用,不同于将ndcuga以相同的名义成分直接配入到主相合金中同时进行熔炼的工艺,同时熔炼并不能形成主相外层的层壳结构,当然也就起不到改善晶界相以及主相浸润性,消除尖角等作用;ga大部分掺杂进入了主相而非晶界相,主相外延层及晶界相失去了大部分的ga以后,过多的cu不能均匀的在主相周围均匀分布,不但起不到提升矫顽力的作用,有时甚至会引起方形度的恶化。
10.(3)制粉:将合金钢锭与速凝薄片混合后进行氢破碎,再经气流磨,得粉体。
11.(4)磁场成型:将粉体置于磁场压机中,在惰性气体保护下压制成型,得压坯。
12.(5)冷等静压:将压坯在真空塑封状态下放入冷等压设备进行再压制,将压坯密度提高10~15%,得冷等静压坯。
13.(6)烧结:将冷等静压坯置于真空烧结炉中,经烧结、回火后,得烧结钕铁硼磁体毛坯。
14.作为优选,步骤(1)中,熔炼温度为1420~1480℃。
15.作为优选,步骤(2)中,熔炼温度为950~1050℃。
16.作为优选,步骤(3)中,步骤(3)中,氢破碎温度为420~500℃。常规的氢破碎工艺温度为560~600℃,本发明中采用低温氢破碎工艺,氢破碎温度控制在420~500℃,目的是降低ga在本工序形成其他难以分解的化合物,例如ga的b、n等化合物的可能性,确保不被非预期的化合物占有。
17.步骤(3)中,所述粉体的表面积平均粒径为2.6~3.2μm。
18.作为优选,步骤(5)中,再压制压强为150~280mpa。
19.作为优选,步骤(6)中,烧结程序为:980~1030℃烧结6h,冷却至100℃以下;回火程序为:880~920℃一级回火2~3h,冷却至80℃以下后升温至460~560℃二级回火4~6h,冷却至室温。烧结和回火是关键步骤之一,决定了磁体是否密实,晶界结构是否优化等因素,因而会极大地影响磁体的磁性能;本发明中采用低温烧结工艺,晶界性质发生了改变以后,传统的高温烧结工艺会使主相晶粒发生异常长大,以及造成过多的烧损挥发,因此本发明采用980~1030低温长时间烧结的工艺以保证晶粒一致性,同时采用二级退火。
20.因此,本发明具有如下有益效果:
21.(1)对钕铁硼磁体的成分进行了设计改进,成分中不含有重稀土元素,降低了生产成本,且具有较高的剩磁能及矫顽力;
22.(2)提供了一种钕铁硼磁体制备方法,工艺步骤简单,可操作性强,适合大批量生产,并能优化晶界结构,制得的磁体具有较高的剩磁能及矫顽力。
具体实施方式
23.下面通过具体实施方式对本发明做进一步的描述。
24.实施例1
25.(1)制备主相合金:按主相合金的成分组成进行配料,主相合金由以下质量百分含量的成分组成:28.4%pr
25
nd
75
,0.94%b,0.15%al,0.1%zr,0.1%ti,余量fe;配料后将原料加入真空速凝甩片炉,经1450℃熔炼、浇注、冷却结晶后,得速凝薄片;
26.(2)制备副相合金:按副相合金的成分组成进行配料,副相合金由以下原子百分比的成分组成:55%nd,20%cu,25%ga,配料后将原料加入真空熔炼炉,经1000℃熔炼、浇注
后,得合金钢锭;
27.(3)制粉:以高剩磁高矫顽力无重稀土烧结钕铁硼磁体总质量计,将3%的合金钢锭与97%的速凝薄片混合后进行氢破碎,氢破碎温度为450℃,再经气流磨,得表面积平均粒径为2.8μm的粉体;
28.(4)磁场成型:将粉体置于磁场压机中,在惰性气体保护下压制成型,得压坯;
29.(5)冷等静压:将压坯在真空塑封状态下放入冷等压设备进行再压制,再压制压强为220mpa,将压坯密度提高13%,得冷等静压坯;
30.(6)烧结:将冷等静压坯置于真空烧结炉中,经烧结、回火后,得烧结钕铁硼磁体毛坯;烧结程序为:1020℃烧结4h,冷却至100℃以下;回火程序为:900℃一级回火3h,冷却至80℃以下后升温至460℃二级回火5h,冷却至室温。
31.对比例1
32.对比例1与实施例1相比,区别在于:步骤(3)中,氢破碎温度为580℃,其余与实施例1完全相同。
33.对比例2
34.对比例2与实施例1相比,区别在于:步骤(6)中,烧结程序为:1060℃烧结4h,冷却至100℃以下;回火程序为:900℃一级回火3h,冷却至80℃以下后升温至460℃二级回火5h,冷却至室温,其余与实施例1完全相同。
35.对比例3
36.对比例3与实施例1相比,区别在于:步骤(2)中,副相合金由以下原子百分比的成分组成:75%nd,20%cu,5%ga,其余与实施例1完全相同。
37.对比例4
38.对比例4与实施例1相比,区别在于:步骤(2)中,将副相合金中的ga用al替代,其余与实施例1完全相同。
39.对比例5
40.对比例5与实施例1相比,区别在于:步骤(3)中,合金钢锭的质量百分比为6%,其余与实施例1完全相同。
41.实施例2
42.(1)制备主相合金:按主相合金的成分组成进行配料,主相合金由以下质量百分含量的成分组成:29.4%pr
25
nd
75
,0.94%b,0.15%al,0.08%zr,0.08%ti,余量fe;配料后将原料加入真空速凝甩片炉,经1420℃熔炼、浇注、冷却结晶后,得速凝薄片;
43.(2)制备副相合金:按副相合金的成分组成进行配料,副相合金由以下原子百分比的成分组成:55%nd,20%cu,25%ga,配料后将原料加入真空熔炼炉,经1000℃熔炼、浇注后,得合金钢锭;
44.(3)制粉:以高剩磁高矫顽力无重稀土烧结钕铁硼磁体总质量计,将2%的合金钢锭与98%的速凝薄片混合后进行氢破碎,氢破碎温度为460℃,再经气流磨,得表面积平均粒径为2.8μm的粉体;
45.(4)磁场成型:将粉体置于磁场压机中,在惰性气体保护下压制成型,得压坯;
46.(5)冷等静压:将压坯在真空塑封状态下放入冷等压设备进行再压制,再压制压强为220mpa,将压坯密度提高13%,得冷等静压坯;
47.(6)烧结:将冷等静压坯置于真空烧结炉中,经烧结、回火后,得烧结钕铁硼磁体毛坯;烧结程序为:1010℃烧结6h,冷却至100℃以下;回火程序为:890℃一级回火3h,冷却至80℃以下后升温至480℃二级回火5h,冷却至室温。
48.实施例3
49.(1)制备主相合金:按主相合金的成分组成进行配料,主相合金由以下质量百分含量的成分组成:27.6%pr
25
nd
75
,0.94%b,0.1%al,0.12%zr,0.1%ti,余量fe;配料后将原料加入真空速凝甩片炉,经1480℃熔炼、浇注、冷却结晶后,得速凝薄片;
50.(2)制备副相合金:按副相合金的成分组成进行配料,副相合金由以下原子百分比的成分组成:55%nd,20%cu,25%ga,配料后将原料加入真空熔炼炉,经1050℃熔炼、浇注后,得合金钢锭;
51.(3)制粉:以高剩磁高矫顽力无重稀土烧结钕铁硼磁体总质量计,将4%的合金钢锭与96%的速凝薄片混合后进行氢破碎,氢破碎温度为480℃,再经气流磨,得表面积平均粒径为2.8μm的粉体;
52.(4)磁场成型:将粉体置于磁场压机中,在惰性气体保护下压制成型,得压坯;
53.(5)冷等静压:将压坯在真空塑封状态下放入冷等压设备进行再压制,再压制压强为220mpa,将压坯密度提高12%,得冷等静压坯;
54.(6)烧结:将冷等静压坯置于真空烧结炉中,经烧结、回火后,得烧结钕铁硼磁体毛坯;烧结程序为:1030℃烧结4h,冷却至100℃以下;回火程序为:920℃一级回火3h,冷却至80℃以下后升温至520℃二级回火5h,冷却至室温。
55.将实施例1~3及对比例1~5得到的烧结钕铁硼磁体毛坯进行常规的机械加工及表面处理后,进行磁性能检测,检测结果如表1所示。
56.表1实施例1~3及对比例1~5中得到的烧结钕铁硼磁体毛坯磁性能检测结果
[0057][0058]
从表1中可以看出,实施例1中得到的烧结钕铁硼磁体毛坯磁性能与的对比例1~5中得到的烧结钕铁硼磁体毛坯磁性能相比,其磁性能更为优异;实施例1~3得到的烧结钕铁硼磁体剩磁达到14kgs以上,内禀矫顽力达到17koe以上,最大磁能积达到50mgoe以上,说明通过本发明制得烧结钕铁硼磁体在不添加重稀土的情况下,能获得较好的综合磁性能。
[0059]
以上所述的实施例只是本发明的一种较佳的方案,并非对本发明作任何形式上的
限制,在不超出权利要求所记载的技术方案的前提下还有其它的变体及改型。