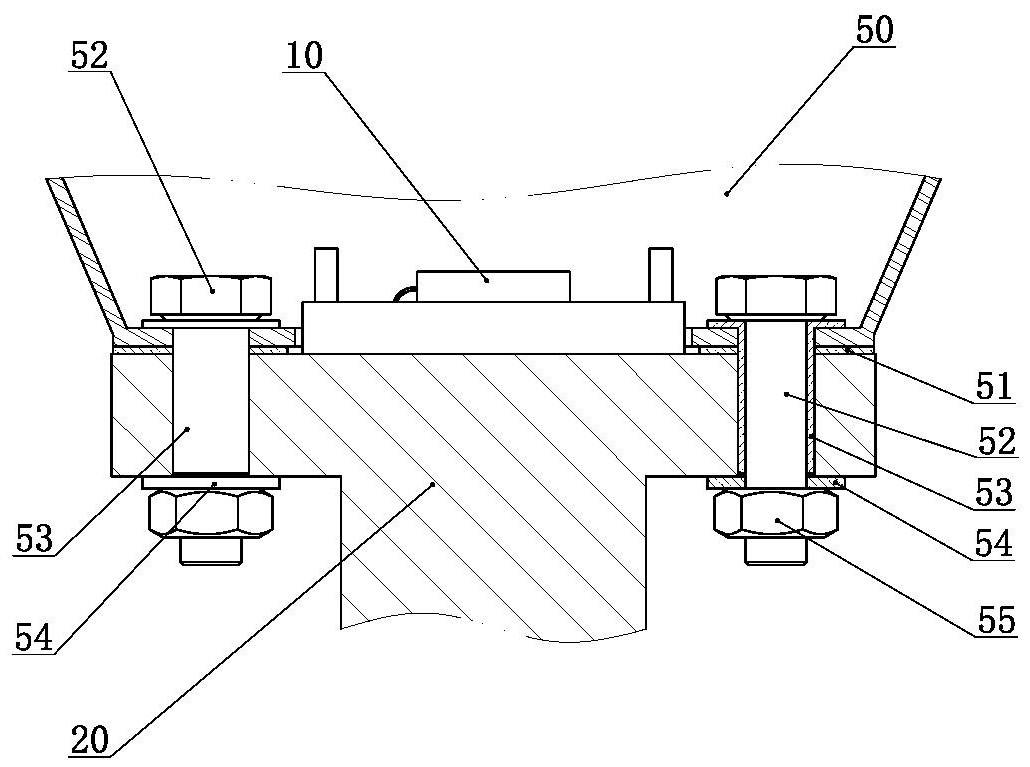
1.本发明涉及太阳能发电装置,尤其涉及一种砷化镓电池散热结构。
背景技术:2.砷化镓电池是近年来发展的一种高效太阳能发电技术,砷化镓电池高光电转换率、高发电效能。但高发电性能的同时,砷化镓电池伴随着高发热,且当温度超过180℃时,砷化镓电池会发生损毁,通常的散热装置往往不能满足砷化镓电池的散热条件。因此,解决砷化镓电池的散热技术是砷化镓电池应用中面临的一个主要技术问题。
技术实现要素:3.本发明的目的在于提出一种砷化镓电池散热结构,提高砷化镓电池的散热性能。
4.为了实现上述目的,本发明的技术方案是:一种砷化镓电池散热结构,包括砷化镓芯片、电源正极、电源负极和散热器,所述砷化镓芯片的基面通过焊接层连接第一导体,所述电源负极通过所述第一导体连接所述砷化镓芯片的基面,所述砷化镓芯片通过正极导线连接第二导体,所述第二导体连接所述电源正极。
5.更进一步,一种散热结构是,所述第一导体是基础铜板,所述基础铜板通过第一导热层连接所述散热器;所述第二导体是铜箔线路板,所述第二导体通过第二导热层粘接在所述基础铜板上。
6.更进一步,所述第一导热层可以是环氧树脂绝缘导热涂层。
7.更进一步,所述第一导热层可以是陶瓷镀铜绝缘导热层。
8.更进一步,所述第一导热层可以是钎焊层。
9.更进一步,所述基础铜板的厚度为1mm~2mm,所述第二导热层是环氧树脂绝缘导热涂层。
10.更进一步,为了获得最佳的导热效果,一种散热结构是,所述第一导体是所述散热器;所述第二导体是铜箔线路板,所述第二导体通过第二导热层粘接在所述散热器上。
11.更进一步,一种优选的散热器材质是,所述散热器是铝合金材质的散热器。
12.更进一步,为了实现安全的砷化镓电池太阳能发电,所述散热器连接聚光罩,所述散热器与所述聚光罩之间设有绝缘层。
13.更进一步,一种安全的聚光罩与散热器连接结构是,所述散热器通过连接螺栓连接聚光罩,所述连接螺栓与聚光罩和散热器之间设有绝缘法兰套和绝缘垫圈。
14.本发明的有益效果是:通过改进砷化镓电池的封装结构,提高砷化镓电池自身的导热效率,使砷化镓电池产生的热量高效传导到散热器,防止砷化镓电池发生过热损毁。
15.下面结合附图和实施例对本发明进行详细描述。
附图说明
16.图1 是现有的砷化镓电池结散热构示图,基础铜板与散热器的接触面采用导热
胶;图2 是现有的砷化镓电池结散热构示图,基础铜板与散热器的接触面采用钎焊;图3是本发明结构图,基础铜板与砷化镓芯片采用焊接层连接,基础铜板与散热器之间采用导热胶;图4是本发明结构图,基础铜板与砷化镓芯片采用焊接层连接,基础铜板与散热器之间采用陶瓷镀铜绝缘导热层;图5是本发明结构图,基础铜板与砷化镓芯片采用焊接层连接,基础铜板与散热器之间采用钎焊连接;图6是本发明结构图,砷化镓芯片与散热器之间采用焊接层连接;图7是本发明与聚光罩组合的结构图,散热器与聚光罩之间设有绝缘层;图8是图7结构的局部剖视图,散热器、聚光罩和连接螺栓之间的绝缘结构。
具体实施方式
17.如图3至图8,一种砷化镓电池散热结构,包括砷化镓芯片10、电源正极11、电源负极12和散热器20,所述砷化镓芯片的基面10a通过焊接层13连接第一导体,所述电源负极通过所述第一导体连接所述砷化镓芯片的基面,所述砷化镓芯片通过正极导线14连接第二导体15,所述第二导体连接所述电源正极11。
18.如图3至图5所示,所述第一导体是基础铜板30,所述基础铜板通过第一导热层(31,32,33)连接所述散热器;所述第二导体15是铜箔线路板,所述第二导体通过第二导热层40粘接在所述基础铜板30上。
19.所述第一导热层可以是环氧树脂绝缘导热涂层31,如图3所示。
20.所述第一导热层是可以陶瓷镀铜绝缘导热层32,如图4所示。
21.所述第一导热层可以是钎焊层33,如图5所示。
22.所述基础铜板的厚度h1为1mm~2mm,所述第二导热层40是环氧树脂绝缘导热涂层。
23.如图6所示,所述第一导体是所述散热器20;所述第二导体15是铜箔线路板,所述第二导体通过第二导热层40粘接在所述散热器20上。
24.所述散热器是铝合金材质的散热器。
25.如图7、图8所示,所述散热器连接聚光罩50,所述散热器与所述聚光罩之间设有绝缘层51。
26.所述散热器通过连接螺栓51连接聚光罩,所述连接螺栓与聚光罩和散热器之间设有绝缘法兰套53和绝缘垫圈54。
27.如图1所示,一种现有的砷化镓电池结散热构是,砷化镓芯片10的基面10a通过焊接层13连接一块铜箔线路板16,砷化镓芯片的正极导线14也连接铜箔线路板16,电源正极11通过焊接点11a连接铜箔线路板、并连通正极导线14。电源负极12通过焊接点12a连接铜箔线路板、并连通砷化镓芯片的基面。所述铜箔线路板16是一片厚度为0.05mm的铜箔,铜箔线路板16分隔电源正极11和电源负极12。铜箔线路板16连接一层绝缘导热涂层17,绝缘导热涂层17采用环氧树脂,绝缘导热涂层17连接一块基础铜板30,基础铜板30是一块厚度h1为1mm~2mm的铜板,具备良好的导热性能。基础铜板30连接散热器20,在基础铜板与散热器
的接触面涂覆有导热胶18,用于提高热传递。为了保护铜箔线路板16,在铜箔线路板16的上表面涂覆有一层绝缘保护层19。
28.砷化镓电池是一种高效太阳能发电技术,但高发电效能的同时,砷化镓电池伴随着高发热,当温度超过180℃时,砷化镓电池会发生损毁。现有技术中,砷化镓芯片10产生的热量,需要经过铜箔线路板16、绝缘导热涂层17、基础铜板30和导热胶18传递到散热器20。多层次的热传导会降低导热效能,使砷化镓电池的温度升高。另外铜箔线路板16是一片厚度仅为0.05mm的铜箔,当砷化镓电池发生过热时,铜箔线路板16易首先发生损毁。
29.如图2,目前采用的一种提高散热效能的方法是采用钎焊18a替代导热胶18,可以改进基础铜板30到散热器20的热传递效能,但也不能彻底解决砷化镓电池的散热问题。解决砷化镓电池的散热技术是砷化镓电池应用中面临的一个主要技术问题。
30.为此,本发明提出了一种砷化镓电池散热结构。
31.实施例一:如图3至图5,一种砷化镓电池散热结构,包括砷化镓芯片10、电源正极11、电源负极12和散热器20。
32.砷化镓芯片的基面10a通过焊接层13连接第一导体,第一导体即是基础铜板30,电源负极12通过焊接点12a焊接在一导体(基础铜板30)上,电源负极通过所述第一导体(基础铜板30)连接砷化镓芯片的基面。砷化镓芯片通过正极导线14连接第二导体15(正极导线14通过焊接点14a焊接在第二导体上),第二导体15是一层铜箔线路板,第二导体15连接电源正极11(电源正极11通过焊接点11a焊接在第二导体上),第二导体通过第二导热层40粘接在基础铜板30上。基础铜板30是厚度h1为1mm的铜板,第二导热层40是环氧树脂绝缘导热涂层。
33.本实施例的砷化镓电池散热结构撤除了原有技术中砷化镓芯片10与基础铜板30之间的铜箔线路板16及绝缘导热涂层17,使基础铜板30替代了铜箔线路板16,减少了砷化镓芯片至散热器之间的热传递层次,提高热传导效能,并可避免出现铜箔线路板16发生过热损毁的问题。作为第二导体15的铜箔线路板仅连接正极导线14,与砷化镓芯片10分离,不会产生过热损毁的问题。
34.本实施例中,基础铜板30通过第一导热层连接散热器20,散热器采用铝合金材质的散热器。
35.第一导热层可以采用环氧树脂绝缘导热涂层31,如图3所示。
36.第一导热层也可以采用陶瓷镀铜绝缘导热层32,如图4所示,陶瓷镀铜绝缘导热层是陶瓷双面覆铜的绝缘体,两面采用锡焊接,一面与基础铜板30板焊接,另一面与散热器焊接。
37.第一导热层还可以是钎焊层33,如图5所示,钎焊层采用锡为焊料。
38.根据实验,对于现有技术的砷化镓电池散热结构,采用在基础铜板与散热器的接触面涂覆导热胶18时(如图1所示),砷化镓芯片10与散热器20之间的温差为30℃。采用在基础铜板与散热器的接触面钎焊18a时(如图2所示),砷化镓芯片10与散热器20之间的温差为10℃。
39.采用本实施例的结构,当第一导热层采用环氧树脂绝缘导热涂层31时(如图3所示),砷化镓芯片10与散热器20之间的温差为10℃;当第一导热层采用陶瓷镀铜绝缘导热层
32时(如图4所示),砷化镓芯片10与散热器20之间的温差为小于5℃;当第一导热层采用钎焊层33时(如图5所示),砷化镓芯片10与散热器20之间的温差为小于3℃。
40.采用本实施例的砷化镓电池散热结构明显减小了砷化镓芯片与散热器之间的温差,验证了砷化镓芯片与散热器之间具有更好的导热效能,也可以使砷化镓电池获得更好的散热效果。
41.实施例二:如图6,一种砷化镓电池散热结构,本实施例是实施例一的进一步改进。
42.本实施例中,将散热器20作为第一导体,砷化镓芯片10的基面10a通过焊接层13连接散热器,电源负极12通过焊接点12a焊接在散热器20上,电源负极12通过散热器连通砷化镓芯片的基面。第二导体15仍采用铜箔线路板,第二导体通过第二导热层40粘接在散热器20上,第二导热层40是环氧树脂绝缘导热涂层。
43.与实施例一相比较,本实施例的技术方案撤除了基础铜板30,采用散热器替代了基础铜板30的功能,砷化镓芯片通过钎焊直接接触散热器,使砷化镓芯片与散热器之间获得最佳的热传递效果。根据实验,砷化镓芯片10与散热器20之间的温差接近0℃。
44.综上所述,可归纳不同的砷化镓电池散热结构及效能如下:第一种散热结构,即现有的砷化镓电池结散热构,如图1所示,砷化镓芯片10的基面10a通过焊接层13连接铜箔线路板16,铜箔线路板16连接一层绝缘导热涂层17,绝缘导热涂层17连接基础铜板30,基础铜板30连接散热器20,在基础铜板与散热器的接触面涂覆有导热胶18。实验砷化镓芯片与散热器间的温差为30℃。
45.第二种散热结构,如图2所示,将第一种散热结构中,基础铜板与散热器的接触面之间的导热胶改换为钎焊18a。实验砷化镓芯片与散热器间的温差为10℃。 此种散热结构可显著提高砷化镓芯片与散热器间的导热性能,但需要配置固定的散热器。
46.第三种散热结构,如图3所示,砷化镓芯片的基面10a通过焊接层13连接基础铜板30,基础铜板30连接散热器20,在基础铜板与散热器的接触面涂覆有环氧树脂绝缘导热涂层31。实验砷化镓芯片与散热器间的温差为10℃。此种散热结构与第二种散热结构具有相同的砷化镓芯片与散热器间的导热性能,但可选配不同的散热器。
47.第四种散热结构,如图4所示,在基础铜板30与散热器20之间设置陶瓷镀铜绝缘导热层32,替换将第三种散热结构中基础铜板与散热器之间的导热胶,实验砷化镓芯片与散热器间的温差小于5℃。此种散热结构进一步提高了砷化镓芯片与散热器间的导热性能,并保持了基础铜板与散热器之间的绝缘性能。
48.第五种散热结构,如图5所示,基础铜板与散热器之间采用钎焊层32,替换将第三种散热结构中基础铜板与散热器之间的导热胶,实验砷化镓芯片与散热器间的温差小于3℃。此种散热结构较第4种散热结构进一步提高了砷化镓芯片与散热器间的导热性能,但基础铜板与散热器处于导通状态,散热器成为带电体。
49.第六种散热结构,如图6所示,砷化镓芯片的基面10a通过焊接层13直接连接散热器20,实验砷化镓芯片与散热器间的温差接近0℃,较其它散热结构具备最佳的热传递效果。但散热器作为导体,成为带电体。
50.上述第三种散热结构、第四种散热结构、第五种散热结构和第六种散热结构属本发明改进的技术方案,均改进了砷化镓电池散热的散热效果。
51.第三种散热结构、第四种散热结构、第五种散热结构将砷化镓电池封装在基础铜板上,制成独立的砷化镓电池产品,再通过不同的方式连接散热器。其中第三种散热结构可方便地配置不同的散热器。第四种散热结构具有较好的热传递效果,并可保持砷化镓电池与散热器之间的绝缘性能。第五种散热结构较第三种散热结构和第四种散热结构具有更好的热传递效果。
52.第六种散热结构将散热器制成砷化镓电池的一个组成部分。在使用特定散热器的应用中,具有最佳的热传递效果。
53.实施例三:如图7、图8,一种砷化镓电池散热结构。
54.在上述第五种散热结构和第六种散热结构中,散热器会形成带电体,由于单只砷化镓电池的产生的电压仅为3v左右,砷化镓电池串联后的输出电压一般是36v,因此对于应用环境是安全的。砷化镓电池在太阳能发电装置中,会采用聚光罩50将阳光聚焦,聚光罩通常需要与散热器固定连接,且聚光罩会暴露在阳光和雨水环境中,为了避免是聚光罩带电,本实施例中,散热器20连接聚光罩50,在散热器与聚光罩之间设有绝缘层51,绝缘层51在散热器与聚光罩之间形成绝缘体。
55.散热器20通过连接螺栓52连接聚光罩,连接螺栓与聚光罩和散热器之间设有绝缘法兰套53和绝缘垫圈54。绝缘法兰套53在连接螺栓的螺杆与散热器之间形成绝缘体,并在螺栓头与聚光罩之间形成绝缘体。绝缘垫圈54在螺母55与散热体之间形成绝缘体。
56.本实施例避免了聚光罩带电,使聚光罩更安全。