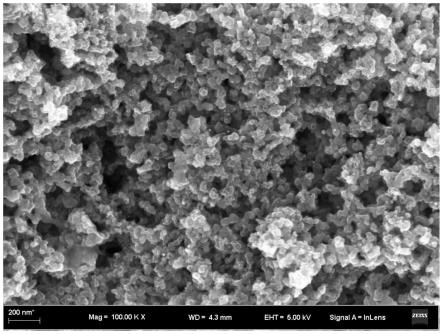
1.本发明属于燃料电池领域,具体涉及一种膜电极催化剂涂层的制备方法。
背景技术:2.燃料电池是一种把燃料所具有的化学能直接转换成电能的化学装置,又称电化学发电器。它是继水力发电、热能发电和原子能发电之后的第四种发电技术。由于燃料电池是通过电化学反应把燃料的化学能中的吉布斯自由能部分转换成电能,不受卡诺循环效应的限制,因此效率高;另外,燃料电池用燃料和氧气作为原料,同时没有机械传动部件,故排放出的有害气体极少,使用寿命长。因此,从节约能源和保护生态环境的角度来看,燃料电池是最有发展前途的发电技术。
3.膜电极(mea),又称膜电极“三合一”或“五合一”组件,是质子交换膜燃料电池的核心部件,是燃料电池内部能量转换的场所,其中,“三合一”组件是指只含有催化层和质子交换膜的膜电极。膜电极的性能和成本影响甚者决定质子交换膜燃料电池的性能、寿命及成本。
4.申请号为cn202010127015.x的发明专利公开了一种燃料电池膜电极,在质子交换膜的一面涂覆有阴极催化剂层,在质子交换膜的另一面涂覆有阳极催化剂层,在阴极催化剂层、阳极催化剂层的外侧分别热压有气体扩散层,阴极催化剂层由两层以上阴极子催化剂层组成或/和阳极催化剂层由两层以上阳极子催化剂层组成,阴极子催化剂层的孔隙率或/和阳极子催化剂层的孔隙率自最靠近质子交换膜的一层起往外逐渐增大或逐渐减小。其制备方法中,先在质子交换膜的一面涂覆上一层阴极催化剂浆料并干燥形成阴极催化剂层;之后在质子交换膜的另一面依次涂覆上m层阳极子催化剂浆料并依次干燥分别形成阳极子催化剂层。
5.申请号为200510132153.2的发明专利提供一种催化剂涂层膜的制备方法,包括:将微孔膜与催化剂分散液接触,得到含有催化剂的微孔膜;将含有催化剂的微孔膜与树脂分散液接触,得到半催化剂涂层膜层,该半催化剂涂层膜层包括催化层和与催化层结合的树脂膜层;并且将两个半催化剂涂层膜层压合得到催化剂涂层膜。在本发明提供的催化剂涂层膜的制备方法中,通过在微孔膜的微孔中分步骤地填充催化剂和树脂,从而使微孔膜内催化剂和树脂的分布一致,三者的结合牢固,并且微孔膜可以起疏水作用,可以改善一般催化剂涂层膜的排水障碍问题。
6.上述申请中均未考虑到采用常规涂布干燥技术制备阴阳极催化剂层会导致涂层过于致密,涂层孔隙率小,从而造成催化层排水困难的问题。
技术实现要素:7.本发明旨在解决上述问题,提供了一种膜电极催化剂涂层的制备方法,通过控制干燥程序,在使涂层分布均匀、无开裂的同时可以增大催化剂涂层的孔隙率。
8.按照本发明的技术方案,所述膜电极催化剂涂层的制备方法,包括以下步骤,
9.s1:将催化剂和电解质树脂溶液分散在混合溶剂中,得到浆料;所述混合溶剂为水和醇的混合液;
10.s2:将所述浆料涂布在质子交换膜上,形成浆料涂层;
11.s3:对所述浆料涂层进行分段干燥,得到所述膜电极催化剂涂层;所述分段干燥包括依次进行的流平干燥、定型干燥和烘干。
12.进一步的,所述催化剂包括ptm/c催化剂或pt/c催化剂,优先的,所述催化剂包括40-80wt%的ptm/c催化剂(pt占ptm/c催化剂质量的40-80%)或30-75wt%的pt/c催化剂(pt占pt/c催化剂质量的30-75%)。其中m指铜、钻、镍、钯或钌。
13.进一步的,所述催化剂占分散浆料总质量的1-10%。
14.进一步的,所述电解质树脂溶液为agc、dupont(杜邦)、sovlay(索尔维)、3m品牌的电解质树脂溶液,电解质树脂溶液中的固体质量占分散浆料总质量的1-5%。
15.进一步的,所述醇选自甲醇、乙醇、异丙醇、正丙醇、乙二醇和丙三醇中的一种或多种。
16.进一步的,所述混合溶剂中水和醇的体积比为1-9:1。
17.进一步的,所述步骤s1中,分散方式为超声、剪切、球磨或均质。
18.进一步的,所述步骤s2中,浆料涂布的方式为狭缝涂布、刮刀涂布、气刀涂布、浸渍涂布或辊式涂布。
19.进一步的,所述步骤s2中,浆料涂布的厚度为80-200um。
20.进一步的,所述步骤s3中,流平干燥的温度为30-40℃,时间为0.4-0.6min,流平阶段主要是使浆料在涂布面上再均匀分布。
21.进一步的,所述步骤s3中,定型干燥的温度为40-50℃,时间为0.8-1.2min,定型阶段用于涂层的整体形状的定型。
22.进一步的,所述步骤s3中,烘干的温度为80-100℃,时间为2.4-3.6min,烘干阶段用于快速干燥,使溶剂快速挥发使颗粒没有更多的时间重排而留下大的孔隙。
23.本发明的技术方案相比现有技术具有以下优点:催化剂浆料涂布过程中,均匀的湿浆料涂敷在质子交换膜上,然后通过干燥去除湿涂层中的溶剂。干燥过程中,溶剂蒸发时,涂层经历一定的收缩,固体物质在湿涂层中彼此接近,最后形成多孔的干燥催化剂涂层。本发明通过优化干燥程序,采用三段式干燥,严格控制各干燥阶段的温度和时间,形成多孔的催化剂涂层,相比于普通涂布干燥方式所得的催化剂涂层,涂层分布均匀,无开裂,排水性能良好,稳定性佳。
附图说明
24.图1为实施例1中催化剂涂层的扫描电镜图。
25.图2为实施例1中催化剂涂层的外观图。
26.图3为对比例1中催化剂涂层的外观图。
27.图4为对比例3中催化剂涂层的外观图。
28.图5为对比例4中催化剂涂层的扫描电镜图。
具体实施方式
29.下面结合附图和具体实施例对本发明作进一步说明,以使本领域的技术人员可以更好地理解本发明并能予以实施,但所举实施例不作为对本发明的限定。
30.实施例1
31.1、浆料制备
32.通过超声分散的方式,将25g60wt%的pt/c催化剂和40g的d2020(dupont,固含量为20%)分散在320g水与130g乙醇的混合液中,得到浆料。
33.2、涂布干燥
34.采用刮刀涂布的方式,将浆料涂布在质子交换膜上,形成厚度为110um的浆料涂层;
35.对浆料涂层进行三段干燥,其中,流平干燥的温度为35℃,时间为0.5min;定型干燥的温度为45℃,时间为1min;烘干阶段的干燥温度为90℃,时间为3min。
36.所得催化剂涂层的外观如图2所示,其扫描电镜图如图1所示,可以看出催化剂层具有大量空隙,且分布均匀,无开裂。
37.实施例2
38.1、浆料制备
39.通过超声分散的方式,将25g60wt%的pt/c催化剂和40g的d2020(dupont,固含量为20%)分散在320g水与130g乙醇的混合液中,得到浆料。
40.2、涂布干燥
41.采用刮刀涂布的方式,将浆料涂布在质子交换膜上,形成厚度为110um的浆料涂层;
42.对浆料涂层进行三段干燥,其中,流平干燥的温度为30℃,时间为0.6min;定型干燥的温度为40℃,时间为1.2min;烘干阶段的干燥温度为80℃,时间为3.6min。
43.实施例3
44.1、浆料制备
45.通过超声分散的方式,将25g60wt%的pt/c催化剂和40g的d2020(dupont,固含量为20%)分散在320g水与130g乙醇的混合液中,得到浆料。
46.2、涂布干燥
47.采用刮刀涂布的方式,将浆料涂布在质子交换膜上,形成厚度为110um的浆料涂层;
48.对浆料涂层进行三段干燥,其中,流平干燥的温度为40℃,时间为0.4min;定型干燥的温度为50℃,时间为0.8min;烘干阶段的干燥温度为100℃,时间为2.4min。
49.对比例1
50.1、浆料制备
51.通过超声分散的方式,将25g60wt%的pt/c催化剂和40g的d2020(dupont,固含量为20%)分散在320g水与130g乙醇的混合液中,得到浆料。
52.2、涂布干燥
53.采用刮刀涂布的方式,将浆料涂布在质子交换膜上,形成厚度为110um的浆料涂层;
54.对浆料涂层进行干燥,干燥温度为90℃,时间为3min。
55.所得催化剂涂层的如图3所示,可以看出整体外观差,开裂。
56.对比例2
57.1、浆料制备
58.通过超声分散的方式,将25g60wt%的pt/c催化剂和40g的d2020(dupont,固含量为20%)分散在320g水与130g乙醇的混合液中,得到浆料。
59.2、涂布干燥
60.采用刮刀涂布的方式,将浆料涂布在质子交换膜上,形成厚度为110um的浆料涂层;
61.对浆料涂层进行两段干燥,其中,第一段干燥温度为45℃,1min;第二段的干燥温度为90℃,3min。
62.所得催化剂涂层出现了一边厚一边薄的现象。
63.对比例3
64.1、浆料制备
65.通过超声分散的方式,将25g60wt%的pt/c催化剂和40g的d2020(dupont,固含量为20%)分散在320g水与130g乙醇的混合液中,得到浆料。
66.2、涂布干燥
67.采用刮刀涂布的方式,将浆料涂布在质子交换膜上,形成厚度为110um的浆料涂层;
68.对浆料涂层进行两段干燥,其中,第一段干燥温度为35℃,0.5min;第二段的干燥温度为90℃,3min。
69.所得催化剂涂层的如图4所示,可以看出整体外观差,开裂。
70.对比例4
71.1、浆料制备
72.通过超声分散的方式,将25g60wt%的pt/c催化剂和40g的d2020(dupont,固含量为20%)分散在320g水与130g乙醇的混合液中,得到浆料。
73.2、涂布干燥
74.采用刮刀涂布的方式,将浆料涂布在质子交换膜上,形成浆料涂层(湿膜厚度110um);
75.对浆料涂层进行三段干燥,其中,流平干燥的温度为35℃,时间为0.5min;定型干燥的温度为45℃,时间为1min;烘干阶段的干燥温度为50℃,时间为3min。
76.所得催化剂涂层的扫描电镜图如图5所示,可以看出其孔隙率低。
77.实施例1-3和对比例4中所得催化剂涂层平均孔径和孔体积结果如表1所示。
78.表1实施例1-3和对比例4中催化剂涂层平均孔径和孔体积
[0079] 平均孔径/nm孔体积(cm3/g)实施例11.8720.133实施例21.8350.130实施例32.0230.155对比例41.5060.102
[0080]
显然,上述实施例仅仅是为清楚地说明所作的举例,并非对实施方式的限定。对于所属领域的普通技术人员来说,在上述说明的基础上还可以做出其它不同形式变化或变动。这里无需也无法对所有的实施方式予以穷举。而由此所引申出的显而易见的变化或变动仍处于本发明创造的保护范围之中。