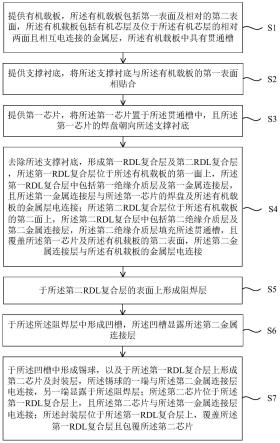
基于有机载板与rdl的堆叠型封装结构及制备方法
技术领域
1.本发明属于封装技术领域,涉及一种基于有机载板与rdl的堆叠型封装结构及制备方法。
背景技术:2.随着电子产品向着高密度及小型化方向发展,封装特征尺寸越来越小而且逐渐接近极限,依靠减小特征尺寸来不断提高集成度的方式已不再适用,电子封装开始在之前2d封装基础上向垂直方向(z方向)发展,形成了以堆叠(stacked package)和硅通孔(through-silicon-via,tsv)为代表的3d封装技术,封装由此进入三维高密度封装时代。目前,2.5d、3d高密度封装逐渐取代传统的2d封装(如qfp,pqfn,bga和csp等封装),成为封装技术的发展潮流。
3.作为一种广泛使用的堆叠式三维封装技术,pop(package-on-package)封装在兼容现有的标准表面贴装技术(smt)工艺的基础上,pop封装可以在不增加产品尺寸的前提下,在垂直方向上进行芯片的灵活堆叠,具有很强的组装灵活性和扩展性,可以完全替代以前单独式或并列式分布的封装形式,实现更高数量不同器件的混合集成,在智能手机、平板电脑和笔记本电脑等多种移动通讯消费类电子产品中应用广泛。
4.传统的pop封装结构,如图1,通常采用bga结构作为上下两层封装之间的连接,这种封装结构使得封装成本较大,封装尺寸较大,线路互联密度低,芯片的连接方式使得电流、信号的传递效率低,上下两层封装结构的间隙较大,上下层隔着空气,而空气作为一种不良导体,会导致芯片散热问题。
技术实现要素:5.鉴于以上所述现有技术的缺点,本发明的目的在于提供一种基于有机载板与rdl的堆叠型封装结构及制备方法,用于解决现有技术中堆叠式封装的问题。
6.为实现上述目的及其他相关目的,本发明提供一种基于有机载板与rdl的堆叠型封装结构,所述封装结构包括:
7.有机载板,所述有机载板包括第一表面及相对的第二表面,所述有机载板包括有机芯层及位于所述有机芯层的相对两面且相互电连接的金属层,所述有机载板中具有贯通槽;
8.第一芯片,所述第一芯片置于所述贯通槽中,且所述第一芯片的焊盘与所述有机载板的第一表面位于同一侧;
9.第一rdl复合层,所述第一rdl复合层位于所述有机载板的第一面上,所述第一rdl复合层中包括第一绝缘介质层及第一金属连接层,且所述第一金属连接层与所述第一芯片的焊盘及所述有机载板的金属层电连接;
10.第二rdl复合层,所述第二rdl复合层位于所述有机载板的第二面上,所述第二rdl复合层中包括第二绝缘介质层及第二金属连接层,所述第二绝缘介质层填充所述贯通槽,
且覆盖所述第一芯片及所述有机载板的第二表面,所述第二金属连接层与所述有机载板的金属层电连接;
11.第二芯片,所述第二芯片位于所述第一rdl复合层上,且所述第二芯片与所述第一金属连接层电连接;
12.封装层,所述封装层位于所述第一rdl复合层上,覆盖所述第一rdl复合层且包覆所述第二芯片;
13.阻焊层,所述阻焊层位于所述第二rdl复合层上,覆盖所述第二rdl复合层且所述阻焊层中具有显露所述第二金属连接层的凹槽;
14.锡球,所述锡球位于所述凹槽中,且所述锡球的一端与所述第二金属连接层电连接,另一端显露于所述阻焊层。
15.可选地,所述封装结构中包括多个所述第一芯片,且所述第一芯片所对应的焊盘位于同一平面;所述封装结构中包括多个所述第二芯片。
16.可选地,所述第二芯片与所述第一金属连接层通过电镀形成的金属凸点电连接。
17.可选地,所述第一rdl复合层中包括叠置的且电连接的所述第一金属连接层;所述第二rdl复合层中包括叠置的且电连接的所述第二金属连接层。
18.可选地,所述第一金属连接层的线宽≥1μm,所述第一金属连接层的线间距≥1μm;所述第二金属连接层的线宽≥1μm,所述第二金属连接层的线间距≥1μm。
19.可选地,所述第一绝缘介质层包括感光介质层或非感光介质层;所述第二绝缘介质层包括感光介质层或非感光介质层。
20.可选地,所述封装结构包括扇出型封装结构或扇入型封装结构。
21.另本发明还提供一种基于有机载板与rdl的堆叠型封装结构的制备方法,包括以下步骤:
22.提供有机载板,所述有机载板包括第一表面及相对的第二表面,所述有机载板包括有机芯层及位于所述有机芯层的相对两面且相互电连接的金属层,所述有机载板中具有贯通槽;
23.提供支撑衬底,将所述支撑衬底与所述有机载板的第一表面相贴合;
24.提供第一芯片,将所述第一芯片置于所述贯通槽中,且所述第一芯片的焊盘朝向所述支撑衬底;
25.去除所述支撑衬底,形成第一rdl复合层及第二rdl复合层,所述第一rdl复合层位于所述有机载板的第一面上,所述第一rdl复合层中包括第一绝缘介质层及第一金属连接层,且所述第一金属连接层与所述第一芯片的焊盘及所述有机载板的金属层电连接;所述第二rdl复合层位于所述有机载板的第二面上,所述第二rdl复合层中包括第二绝缘介质层及第二金属连接层,所述第二绝缘介质层填充所述贯通槽,且覆盖所述第一芯片及所述有机载板的第二表面,所述第二金属连接层与所述有机载板的金属层电连接;
26.于所述第二rdl复合层的表面上形成阻焊层;
27.于所述阻焊层中形成凹槽,所述凹槽显露所述第二金属连接层;
28.于所述凹槽中形成锡球,以及于所述第一rdl复合层上形成第二芯片及封装层,所述锡球的一端与所述第二金属连接层电连接,另一端显露于所述阻焊层;所述第二芯片位于所述第一rdl复合层上,且所述第二芯片与所述第一金属连接层电连接;所述封装层位于
所述第一rdl复合层上,覆盖所述第一rdl复合层且包覆所述第二芯片。
29.可选地,所述第二芯片与所述第一金属连接层通过金属凸点电连接,形成所述金属凸点的方法包括电镀法。
30.可选地,所述第一绝缘介质层包括感光介质层或非感光介质层;所述第二绝缘介质层包括感光介质层或非感光介质层;当为非感光介质层时,图形化的方法包括镭射,当为感光介质层时,图形化的方法包括干法蚀刻或湿法蚀刻。
31.如上所述,本发明的基于有机载板与rdl的堆叠型封装结构及制备方法,将有机载板与第一rdl复合层及第二rdl复合层相结合,将第一芯片容置于有机载板中并与第一rdl复合层电连接,且第二芯片与第一rdl复合层电连接,且第一rdl复合层结合有机载板与第二rdl复合层电连接,以通过锡球进行电性引出。
32.本发明适用于大面积制造,可提高产能,降低成本;通过rdl复合层的设置可代替一部分芯片内部线路的设置,且堆叠结构提供了芯片设计的灵活性,可进行灵活的混合装联,以满足需求,降低了设计的复杂性及设计成本;第一rdl复合层直接与第一芯片的焊盘电连接,第二芯片与第一rdl复合层通过金属凸点电连接,从而可减小应力,提高封装可靠性;结合rdl复合层可降低封装厚度,缩短芯片之间的导通距离,实现线路致密化和精细化,满足薄、小的封装需求;扇出型封装结构,可以使封装的芯片尺寸更大,还可以使i/o触点间距更灵活;从而本发明中的基于有机载板与rdl的堆叠型封装结构及制备方法可降低成本、减小热阻,提高可靠性,缩短互连路径,实现封装致密化、精细化、灵活化,使信号传输更快,提高适用范围,可应对未来如云基础设施、5g、自动驾驶和人工智能等方面的需求。
附图说明
33.图1显示为现有技术中的pop封装结构示意图。
34.图2显示为本发明实施例中基于有机载板与rdl的堆叠型封装结构的制备工艺流程图。
35.图3~图20显示为本发明实施例中基于有机载板与rdl的堆叠型封装结构在制备过程中各步骤所呈现的结构示意图。
36.元件标号说明
37.100
ꢀꢀꢀꢀꢀꢀꢀꢀꢀꢀꢀꢀꢀꢀꢀꢀꢀꢀꢀꢀꢀ
有机载板
38.101
ꢀꢀꢀꢀꢀꢀꢀꢀꢀꢀꢀꢀꢀꢀꢀꢀꢀꢀꢀꢀꢀ
有机芯层
39.102
ꢀꢀꢀꢀꢀꢀꢀꢀꢀꢀꢀꢀꢀꢀꢀꢀꢀꢀꢀꢀꢀ
金属层
40.201
ꢀꢀꢀꢀꢀꢀꢀꢀꢀꢀꢀꢀꢀꢀꢀꢀꢀꢀꢀꢀꢀ
第一芯片
41.202
ꢀꢀꢀꢀꢀꢀꢀꢀꢀꢀꢀꢀꢀꢀꢀꢀꢀꢀꢀꢀꢀ
第二芯片
42.301
ꢀꢀꢀꢀꢀꢀꢀꢀꢀꢀꢀꢀꢀꢀꢀꢀꢀꢀꢀꢀꢀ
第一子绝缘介质层
43.3011
ꢀꢀꢀꢀꢀꢀꢀꢀꢀꢀꢀꢀꢀꢀꢀꢀꢀꢀꢀꢀ
第一子绝缘介质层开口
44.302
ꢀꢀꢀꢀꢀꢀꢀꢀꢀꢀꢀꢀꢀꢀꢀꢀꢀꢀꢀꢀꢀ
第二子绝缘介质层
45.3021
ꢀꢀꢀꢀꢀꢀꢀꢀꢀꢀꢀꢀꢀꢀꢀꢀꢀꢀꢀꢀ
第二子绝缘介质层开口
46.303
ꢀꢀꢀꢀꢀꢀꢀꢀꢀꢀꢀꢀꢀꢀꢀꢀꢀꢀꢀꢀꢀ
第三子绝缘介质层
47.3031
ꢀꢀꢀꢀꢀꢀꢀꢀꢀꢀꢀꢀꢀꢀꢀꢀꢀꢀꢀꢀ
第三子绝缘介质层开口
48.401
ꢀꢀꢀꢀꢀꢀꢀꢀꢀꢀꢀꢀꢀꢀꢀꢀꢀꢀꢀꢀꢀ
第一ti/cu金属沉积层
49.402
ꢀꢀꢀꢀꢀꢀꢀꢀꢀꢀꢀꢀꢀꢀꢀꢀꢀꢀꢀꢀꢀ
第二ti/cu金属沉积层
50.403
ꢀꢀꢀꢀꢀꢀꢀꢀꢀꢀꢀꢀꢀꢀꢀꢀꢀꢀꢀꢀꢀ
第三ti/cu金属沉积层
51.501
ꢀꢀꢀꢀꢀꢀꢀꢀꢀꢀꢀꢀꢀꢀꢀꢀꢀꢀꢀꢀꢀ
第一抗蚀层
52.502
ꢀꢀꢀꢀꢀꢀꢀꢀꢀꢀꢀꢀꢀꢀꢀꢀꢀꢀꢀꢀꢀ
第二抗蚀层
53.601
ꢀꢀꢀꢀꢀꢀꢀꢀꢀꢀꢀꢀꢀꢀꢀꢀꢀꢀꢀꢀꢀ
第一子金属连接层
54.602
ꢀꢀꢀꢀꢀꢀꢀꢀꢀꢀꢀꢀꢀꢀꢀꢀꢀꢀꢀꢀꢀ
第二子金属连接层
55.603
ꢀꢀꢀꢀꢀꢀꢀꢀꢀꢀꢀꢀꢀꢀꢀꢀꢀꢀꢀꢀꢀ
第三子金属连接层
56.700
ꢀꢀꢀꢀꢀꢀꢀꢀꢀꢀꢀꢀꢀꢀꢀꢀꢀꢀꢀꢀꢀ
阻焊层
57.701
ꢀꢀꢀꢀꢀꢀꢀꢀꢀꢀꢀꢀꢀꢀꢀꢀꢀꢀꢀꢀꢀ
凹槽
58.800
ꢀꢀꢀꢀꢀꢀꢀꢀꢀꢀꢀꢀꢀꢀꢀꢀꢀꢀꢀꢀꢀ
锡球
59.900
ꢀꢀꢀꢀꢀꢀꢀꢀꢀꢀꢀꢀꢀꢀꢀꢀꢀꢀꢀꢀꢀ
金属凸点
60.110
ꢀꢀꢀꢀꢀꢀꢀꢀꢀꢀꢀꢀꢀꢀꢀꢀꢀꢀꢀꢀꢀ
封装层
具体实施方式
61.以下通过特定的具体实例说明本发明的实施方式,本领域技术人员可由本说明书所揭露的内容轻易地了解本发明的其他优点与功效。本发明还可以通过另外不同的具体实施方式加以实施或应用,本说明书中的各项细节也可以基于不同观点与应用,在没有背离本发明的精神下进行各种修饰或改变。
62.如在详述本发明实施例时,为便于说明,表示器件结构的剖面图会不依一般比例作局部放大,而且所述示意图只是示例,其在此不应限制本发明保护的范围。此外,在实际制作中应包含长度、宽度及深度的三维空间尺寸。
63.为了方便描述,此处可能使用诸如“之下”、“下方”、“低于”、“下面”、“上方”、“上”等的空间关系词语来描述附图中所示的一个元件或特征与其他元件或特征的关系。将理解到,这些空间关系词语意图包含使用中或操作中的器件的、除了附图中描绘的方向之外的其他方向。此外,当一层被称为在两层“之间”时,它可以是所述两层之间仅有的层,或者也可以存在一个或多个介于其间的层。
64.在本技术的上下文中,所描述的第一特征在第二特征“之上”的结构可以包括第一和第二特征形成为直接接触的实施例,也可以包括另外的特征形成在第一和第二特征之间的实施例,这样第一和第二特征可能不是直接接触。
65.需要说明的是,本实施例中所提供的图示仅以示意方式说明本发明的基本构想,遂图示中仅显示与本发明中有关的组件而非按照实际实施时的组件数目、形状及尺寸绘制,其实际实施时各组件的型态、数量及比例可为一种随意的改变,其组件布局型态也可能更为复杂。
66.参阅图2,本实施例提供一种基于有机载板与rdl的堆叠型封装结构的制备方法,包括以下步骤:
67.s1:提供有机载板,所述有机载板包括第一表面及相对的第二表面,所述有机载板包括有机芯层及位于所述有机芯层的相对两面且相互电连接的金属层,所述有机载板中具有贯通槽;
68.s2:提供支撑衬底,将所述支撑衬底与所述有机载板的第一表面相贴合;
69.s3:提供第一芯片,将所述第一芯片置于所述贯通槽中,且所述第一芯片的焊盘朝向所述支撑衬底;
70.s4:去除所述支撑衬底,形成第一rdl复合层及第二rdl复合层,所述第一rdl复合层位于所述有机载板的第一面上,所述第一rdl复合层中包括第一绝缘介质层及第一金属连接层,且所述第一金属连接层与所述第一芯片的焊盘及所述有机载板的金属层电连接;所述第二rdl复合层位于所述有机载板的第二面上,所述第二rdl复合层中包括第二绝缘介质层及第二金属连接层,所述第二绝缘介质层填充所述贯通槽,且覆盖所述第一芯片及所述有机载板的第二表面,所述第二金属连接层与所述有机载板的金属层电连接;
71.s5:于所述第二rdl复合层的表面上形成阻焊层;
72.s6:于所述阻焊层中形成凹槽,所述凹槽显露所述第二金属连接层;
73.s7:于所述凹槽中形成锡球,以及于所述第一rdl复合层上形成第二芯片及封装层,所述锡球的一端与所述第二金属连接层电连接,另一端显露于所述阻焊层;所述第二芯片位于所述第一rdl复合层上,且所述第二芯片与所述第一金属连接层电连接;所述封装层位于所述第一rdl复合层上,覆盖所述第一rdl复合层且包覆所述第二芯片。
74.以下结合附图3~图20,对有关基于有机载板与rdl的堆叠型封装结构的制备作进一步的介绍。
75.如图3,首先,执行步骤s1,提供有机载板100,所述有机载板100包括第一表面及相对的第二表面,所述有机载板100包括有机芯层101及位于所述有机芯层101的相对两面且相互电连接的金属层102,所述有机载板100中具有贯通槽。
76.具体的,所述有机载板100在制备时,可包括钻孔
→
电镀
→
贴膜
→
曝光
→
显影
→
蚀刻的步骤,以在所述有机芯层101上钻出导通孔及在所述有机芯层101的相对两面形成图形化的且电连接的所述金属层102,然后可采用如激光在无所述金属层102的裸露所述有机芯层101的区域制作出用以放置所述第一芯片201的所述贯通槽,所述贯通槽的尺寸优选与后续待贴合的所述第一芯片201尺寸相近,只需在所述第一芯片201的尺寸上单边各加5μm~100μm,如5μm、10μm、50μm、100μm等,具体可根据需要设置。
77.其中,所述有机载板100可为玻璃纤维布涂树脂覆铜板,树脂可以是环氧树脂、耐高温环氧树脂、聚酰亚胺树脂(pi)、聚四氟乙烯树脂(ptfe)、双马来酰亚胺改性三嗪树脂(bt)、聚丙乙烯树脂(ppe)、聚醚酮树脂(pek)、聚醚酰亚胺树脂(pei)、聚乙烯(pe)、聚砜系树脂和聚苯醚树脂(ppo)等,所述金属层102可为铜箔包括电解铜和压延铜,但并非局限于此。
78.接着,执行步骤s2及s3,提供支撑衬底(未图示),将所述支撑衬底与所述有机载板100的第一表面相贴合;提供第一芯片201,将所述第一芯片201置于所述贯通槽中,且所述第一芯片201的焊盘朝向所述支撑衬底。
79.具体的,可在所述有机载板100的第一表面贴一层有机胶带以作为所述支撑衬底,然后将具有焊盘的所述第一芯片201的有源面朝向所述支撑衬底,置于所述贯通槽中,但所述支撑衬底的种类并非局限于此。
80.其中,所述第一芯片201的焊盘优选与位于所述有机载板100的第一表面的所述金属层102具有同一高度,即位于同一平面,以便于后续进行电性连接。
81.其中,所述有机载板100中可包括多个所述贯通槽,用以容置多个所述第一芯片
201,且多个所述第一芯片201所对应的焊盘优选位于同一平面,以便于后续进行电性连接。关于所述第一芯片201的数量及分布此处不作过分限制。
82.接着,执行步骤s4,去除所述支撑衬底,形成第一rdl复合层及第二rdl复合层,所述第一rdl复合层位于所述有机载板100的第一面上,所述第一rdl复合层中包括第一绝缘介质层及第一金属连接层,且所述第一金属连接层与所述第一芯片201的焊盘及所述有机载板100的金属层电连接;所述第二rdl复合层位于所述有机载板100的第二面上,所述第二rdl复合层中包括第二绝缘介质层及第二金属连接层,所述第二绝缘介质层填充所述贯通槽,且覆盖所述第一芯片201及所述有机载板的第二表面,所述第二金属连接层与所述有机载板100的金属层电连接。
83.作为示例,所述第一rdl复合层中包括叠置的且电连接的所述第一金属连接层;所述第二rdl复合层中包括叠置的且电连接的所述第二金属连接层。
84.具体的,本实施例中,所述第一rdl复合层包括2层所述第一金属连接层,即第一子金属连接层601及第二子金属连接层602,以及对应的包括第一子绝缘介质层301及第二子绝缘介质层302,所述第二rdl复合层中包括1层所述第二金属连接层,即第三子金属连接层603以及对应的包括第三子绝缘介质层303,但所述第一rdl复合层及所述第二rdl复合层中的金属连接层的层数并非局限于此。
85.参与图3~图18,关于所述第一rdl复合层及第二rdl复合层的制备具体可包括以下步骤:
86.首先,执行步骤s4-1,去除所述支撑衬底,显露所述第一芯片201的焊盘。
87.接着,执行步骤s4-2,先形成第三子绝缘介质层303,所述第三子绝缘介质层303填充所述贯通槽,且覆盖所述第一芯片201及所述有机载板100的第二表面。通过所述第三子绝缘介质层303可对所述第一芯片201和所述有机载板100之间的空隙进行填充并固化,以埋入所述第一芯片201,其中,所述第一芯片201的厚度可为100μm,尺寸可为10
×
10mm,所述第三子绝缘介质层303优选为具有良好流动性、散热性且便于进行后续工艺的abf材料,当然根据需要也可采用其它有机材料将所述贯通槽剩余部分填满,关于所述第一芯片201的厚度、种类及尺寸可根据需要进行选择。
88.接着,参阅图3及图4,执行步骤s4-3,可在所述有机载板100的第一面上通过涂布或真空贴膜的方法形成第一子绝缘介质层301,而后可在所述第一子绝缘介质层301上通过曝光、显影或激光加工的方式形成所述第一子绝缘介质层开口3011。
89.作为示例,所述第一绝缘介质层可包括非感光绝缘介质层或感光绝缘介质层;所述第二绝缘介质层可包括非感光绝缘介质层或感光绝缘介质层。
90.具体的,若所述第一子绝缘介质层301为非感光介质层时,可采用镭射的方式形成所述第一子绝缘介质层开口3011,若所述第一子绝缘介质层301为感光绝缘介质层时,则可采用干法或者湿法蚀刻形成所述第一子绝缘介质层开口3011,且所述第一子绝缘介质层301的材料可包括pi、abf、环氧树脂等,所述第一子绝缘介质层301的厚度可为5μm,所述第一子绝缘介质层开口3011的直径可为35μm,开口间距可为60μm,关于所述第一子绝缘介质层301的厚度、开口的尺寸及形貌此处不作过分限制。对应的所述第二子绝缘介质层302及第三子绝缘介质层303均可参阅所述第一子绝缘介质层301,后续不作赘述。
91.特别的,在干法制程下,所述第一子绝缘介质层301可经贴膜
→
曝光
→
显影
→
uv固
化
→
热固化的方式制作;在湿法制程下,可采用旋涂或者狭缝涂布工艺进行,旋涂工艺下,图形化可通过冷板
→
旋涂
→
烘板
→
冷却
→
曝光
→
后烘
→
显影
→
后固化的方式制作;狭缝涂布工艺下,图形化可通过等离子体除杂
→
涂布
→
vcd真空烘烤
→
预烘
→
曝光
→
显影
→
后固化的工艺制作。
92.接着,参阅图5,执行步骤s4-4,形成第一ti/cu金属沉积层401。
93.具体的,在此步骤中所述第一ti/cu金属沉积层401可通过物理气相沉积pvd的方式沉积,因为物理气相沉积出来的ti/cu层厚度的可控性和重复性好,适用范围广,且与基片的结合力较好,可经过排气
→
等离子蚀刻
→
溅射ti
→
溅射cu的工艺完成。其中,先沉积一层ti金属层是因为ti金属层电导率和附着力较高,且厚度均匀性较好,可将后续形成的第一子金属连接层601牢牢固定在所述第一子绝缘介质层301上。其中,沉积后的所述第一ti/cu金属沉积层401的厚度可为300nm~500nm,厚度偏差《5%。
94.接着,参阅图6,执行步骤s4-5,在所述第一ti/cu金属沉积层401上形成第一抗蚀层501。
95.接着,参阅图7,执行步骤s4-6,对所述第一抗蚀层501进行曝光、显影形成图形化所述第一抗蚀层501。
96.具体的,所述第一抗蚀层501可为感光抗蚀层,可通过贴膜、旋涂或狭缝涂布形成,所述第一抗蚀层501的材料可包括丙烯酸和聚合物粘合剂等。所述第一抗蚀层501的制作,可采用干法或湿法制程制作。特别的,在干法制程下,图形制作工艺包括贴膜
→
曝光
→
显影
→
uv固化
→
热固化;在湿法制程下,可采用旋涂或者狭缝涂布工艺进行,旋涂工艺下,图形制作工艺可包括冷板
→
旋涂
→
烘板
→
冷却
→
曝光
→
后烘
→
显影
→
后固化;狭缝涂布工艺下,图形制作工艺包括等离子体除杂
→
涂布
→
vcd真空烘烤
→
预烘
→
曝光
→
显影
→
后固化。
97.接着,参阅图8,执行步骤s4-7,可通过电镀的方式在图形化的所述第一抗蚀层501间形成第一子金属连接层601,如cu金属连接层。
98.具体的,由于高速电镀有更高的电镀效率和质量传递性,可产生更高质量和均匀性更好的镀铜层,从而可在所述第一抗蚀层501间采用高速电镀形成cu金属连接层以作为所述第一子金属连接层601。电镀cu金属层的制作工艺可包括高压水洗
→
高压酸洗
→
电镀
→
水洗
→
烘干。rdl是超精细线路,从而镀铜厚与线宽比优选为1:1,镀铜层材质应包括延展性不低于22%,硫元素含量不高于9.6ppm的中高纯电镀铜,镀铜层厚度偏差《5%,厚度可为5μm。
99.再参阅图9及图10,执行步骤s4-8,通过去膜、闪蚀、ti层刻蚀的方式在所述第一子绝缘介质层301上制作形成所述第一子金属连接层601。
100.具体的,使用去膜、闪蚀、ti蚀刻的工艺依次对所述第一子金属连接层601间的所述第一抗蚀层501、cu、ti进行蚀刻,以完成所述第一子金属连接层601的制作。其中,蚀刻可采用湿法或干法蚀刻,湿法蚀刻的化学试剂可包括h2so4+h2o2和弱酸+h2o2,hf或非hf(naoh+h2o2),nahco3,naoh,nahco3/h2o2的混合物,nahco3/naoh/h2o2的混合物,或碱金属氢氧化物水溶液。碱金属氢氧化物水溶液可以是naoh,koh等溶液;干法可采用离子铣削、活性离子蚀刻和电浆蚀刻的方式实现,包括但不限于氩气,氮气,氟基气体或其组合的工艺气体来执行蚀刻。
101.根据需要,参阅图11~图18,可接着重复上述步骤s4-3~s4-8,依次形成所述第二
子绝缘介质层302、第二子绝缘介质层开口3021、第二ti/cu金属沉积层402、第二抗蚀层502、第二子金属连接层602、第三子绝缘介质层开口3031、第三ti/cu金属沉积层403、第三子金属连接层603。
102.其中,可根据需要进行多次的上述步骤s4-3~s4-8,使得所述第一rdl复合层中可包括叠置的、基于下层的所述金属连接层制备的且电连接的n层所述金属连接层,n≥2,如2层、3层、4层等,以及使得所述第二rdl复合层中可包括叠置的、基于下层的所述金属连接层制备的且电连接的m层所述金属连接层,m≥2,如2层、3层、4层等,具体重复次数可根据需要进行选择,本实施例中仅以形成具有2层金属连接层的第一rdl复合层及具有1层第二rdl复合层作为示例,但并非局限于此。
103.作为示例,所述第一rdl复合层中的所述金属连接层的线宽≥1μm,如1μm、2μm、5μm等,所述第一rdl复合层中的所述金属连接层的线间距≥1μm,如1μm、2μm、5μm等;所述第二rdl复合层中的所述金属连接层的线宽≥1μm,如1μm、2μm、5μm等,所述第二rdl复合层中的所述金属连接层的线间距≥1μm,如1μm、2μm、5μm等。
104.接着,参阅图19,执行步骤s5,于所述第二rdl复合层的表面上形成阻焊层700,以及执行步骤s6,于所述阻焊层700中形成凹槽701,所述凹槽701显露所述金属连接层。
105.接着,参阅图20,执行步骤s7,于所述凹槽701中形成锡球800,以及于所述第一rdl复合层上形成第二芯片202及封装层110,所述锡球900的一端与所述第二金属连接层电连接,另一端显露于所述阻焊层700;所述第二芯片202位于所述第一rdl复合层上,且所述第二芯片202与所述第一金属连接层电连接;所述封装层110位于所述第一rdl复合层上,覆盖所述第一rdl复合层且包覆所述第二芯片202。
106.具体的,可通过贴膜
→
曝光
→
显影
→
后固化的流程制作所述阻焊层700,并在对应位置制作所述凹槽701以显露所述第二金属连接层,然后在所述凹槽701处植入所述锡球800。以及在所述第一rdl复合层上对应所述第二子金属连接层602上电镀金属凸点900以连接所述第二芯片202,所述金属凸点900可以是但不局限于铜、铜合金、铁、铁合金、锡、锡银合金、镍、镍合金、钨等金属材料。其中,所述第二芯片202可包括多个,如2个、3个、5个等,且优选所述第二芯片202的有源面与所述金属凸点900的上表面保持同一平面,以便进行电性连接,关于所述第二芯片202的具体个数此处不作过分限制,制作完成后可使用如封装树脂等对所述第二芯片202进行封装,最终形成基于有机载板与rdl的堆叠型封装结构。
107.作为示例,所述封装结构可包括扇出型封装结构或扇入型封装结构。
108.具体的,本实施例中,优选所述封装结构为扇出型封装结构。
109.参阅图3~图20,本实施例还提供一种基于有机载板与rdl的堆叠型封装结构,所述封装结构包括:
110.有机载板100,所述有机载板100包括第一表面及相对的第二表面,所述有机载板100包括有机芯层101及位于所述有机芯层101的相对两面且相互电连接的金属层102,所述有机载板100中具有贯通槽;
111.第一芯片201,所述第一芯片201置于所述贯通槽中,且所述第一芯片201的焊盘与所述有机载板100的第一表面位于同一侧;
112.第一rdl复合层,所述第一rdl复合层位于所述有机载板100的第一面上,所述第一rdl复合层中包括第一绝缘介质层及第一金属连接层,且所述第一金属连接层与所述第一
芯片201的焊盘及所述有机载板100的金属层电连接;
113.第二rdl复合层,所述第二rdl复合层位于所述有机载板100的第二面上,所述第二rdl复合层中包括第二绝缘介质层及第二金属连接层,所述第二绝缘介质层填充所述贯通槽,且覆盖所述第一芯片201及所述有机载板100的第二表面,所述第二金属连接层与所述有机载板100的金属层电连接;
114.第二芯片202,所述第二芯片202位于所述第一rdl复合层上,且所述第二芯片202与所述第一金属连接层电连接;
115.封装层110,所述封装层110位于所述第一rdl复合层上,覆盖所述第一rdl复合层且包覆所述第二芯片202;
116.阻焊层700,所述阻焊层700位于所述第二rdl复合层上,覆盖所述第二rdl复合层且所述阻焊层700中具有显露所述第二金属连接层的凹槽701;
117.锡球800,所述锡球800位于所述凹槽701中,且所述锡球800的一端与所述第二金属连接层电连接,另一端显露于所述阻焊层700。
118.作为示例,所述封装结构中包括多个所述第一芯片201,且所述第一芯片201所对应的焊盘位于同一平面;所述封装结构中包括多个所述第二芯片202。
119.作为示例,所述第二芯片202与所述第一金属连接层通过电镀形成的金属凸点900电连接。
120.作为示例,所述第一rdl复合层中包括叠置的且电连接的所述第一金属连接层;所述第二rdl复合层中包括叠置的且电连接的所述第二金属连接层。
121.作为示例,所述第一金属连接层的线宽≥1μm,所述第一金属连接层的线间距≥1μm;所述第二金属连接层的线宽≥1μm,所述第二金属连接层的线间距≥1μm。
122.作为示例,所述第一绝缘介质层包括感光介质层或非感光介质层;所述第二绝缘介质层包括感光介质层或非感光介质层。
123.作为示例,所述封装结构包括扇出型封装结构或扇入型封装结构,本实施例优选为扇出型封装结构,以增加i/o触点的数量及分布。
124.关于所述封装结构的具体材质、制备、结构等均可参阅上述有关所述封装结构的制备,此处不作赘述,但所述封装结构的制备并非仅局限于此上述制备方法。
125.综上所述,本发明的基于有机载板与rdl的堆叠型封装结构及制备方法,将有机载板与第一rdl复合层及第二rdl复合层相结合,将第一芯片容置于有机载板中并与第一rdl复合层电连接,且第二芯片与第一rdl复合层电连接,且第一rdl复合层结合有机载板与第二rdl复合层电连接,以通过锡球进行电性引出。
126.本发明适用于大面积制造,可提高产能,降低成本;通过rdl复合层的设置可代替一部分芯片内部线路的设置,且堆叠结构提供了芯片设计的灵活性,可进行灵活的混合装联,以满足需求,降低了设计的复杂性及设计成本;第一rdl复合层直接与第一芯片的焊盘电连接,第二芯片与第一rdl复合层通过金属凸点电连接,从而可减小应力,提高封装可靠性;结合rdl复合层可降低封装厚度,缩短芯片之间的导通距离,实现线路致密化和精细化,满足薄、小的封装需求;扇出型封装结构,可以使封装的芯片尺寸更大,还可以使i/o触点间距更灵活;从而本发明中的基于有机载板与rdl的堆叠型封装结构及制备方法可降低成本、减小热阻,提高可靠性,缩短互连路径,实现封装致密化、精细化、灵活化,使信号传输更快,
提高适用范围,可应对未来如云基础设施、5g、自动驾驶和人工智能等方面的需求。
127.上述实施例仅例示性说明本发明的原理及其功效,而非用于限制本发明。任何熟悉此技术的人士皆可在不违背本发明的精神及范畴下,对上述实施例进行修饰或改变。因此,举凡所属技术领域中具有通常知识者在未脱离本发明所揭示的精神与技术思想下所完成的一切等效修饰或改变,仍应由本发明的权利要求所涵盖。