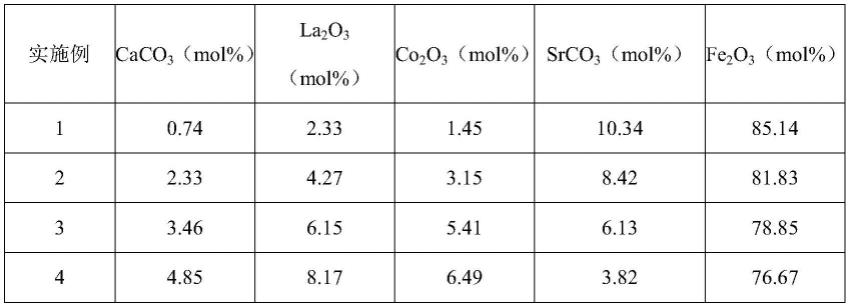
x波段自偏置器件用双相复合铁氧体材料及其制备方法
技术领域
1.本发明属于铁氧体材料制备技术领域,特别涉及x波段自偏置器件用双相复合铁氧体材料及其制备方法。
背景技术:2.随着单片微波集成电路(mmic)技术的不断提升,环行器、隔离器等微波器件也不断朝着小型轻量化、集成化方向发展。基于铁氧体旋磁特性设计的微波器件,在信息公用和级间隔离中起到至关重要的作用,成为决定电子通信系统可靠性和稳定性的关键。根据晶体结构,可将微波器件用铁氧体旋磁材料分为尖晶石型、石榴石型与磁铅石型三种类型。由于材料特性的差异,所应用的频率也不同;例如石榴石型铁氧体兼具适宜的饱和磁化强度和低的损耗特性,被广泛应用于x波段微波器件设计。但为了实现微波器件的功能,通常需要外置磁钢提供偏置磁场,大大增加了微波器件的重量与体积,不利于整机系统小型轻量化、集成化发展。
3.在三种铁氧体旋磁材料中,m型六角铁氧体(srm),具有高矫顽力、高各向异性场和高剩磁比等特性。高矫顽力可以保持六角铁氧体的永磁特性;高剩磁比可以使磁矩倾向于强各向异性方向进动,进而使磁矩在无外加稳恒磁场或稳恒磁场很小的情况下与微波/毫米波作用产生铁磁共振,利用m型六角铁氧体材料上述独有优势可为微波器件工作提供自偏置场,完全摆脱外置磁钢束缚,实现自偏置特性。但m型六角铁氧体材料由于具有高各向异性场,应用频率一般高于ka波段,无法应用于x波段微波器件设计。因此本发明结合石榴石铁氧体与m型六角铁氧体各自的优势,开展x波段自偏置器件用双相复合铁氧体材料研制,对实现x波段微波器件自偏置特性具有十分重要的意义。
4.针对目前x波段自偏置器件用微波铁氧体材料的研究,约旦大学(mater.res.bull.,2016,74:192-210)公布的一种bafe
11.6
cu
0.4o19
铁氧体材料性能指标:比饱和磁化强度σs=68.5g/emu,剩磁比mr/ms=0.32,矫顽力hc=459oe,各向异性场ha=10.7koe,铁磁共振线宽δh未公布,虽然六角铁氧体材料的ha大幅降低,但是材料的mr/ms和hc较低,不利于保持自偏置特性;电子科技大学(j.mater.sci.-mater.electron.,2018,29(12):10311-10316)公布的一种basc
0.1
fe
11.9o19
铁氧体材料性能指标为:饱和磁化强度4πms=4700gs,剩磁比mr/ms=0.65,矫顽力hc=2400oe,各向异性场ha=7.8koe,铁磁共振线宽δh未公布,虽然材料具有适宜的hc与ha,但mr/ms较低;专利cn11204731a公布的一种la,sc取代m型六角铁氧体材料性能指标为:饱和磁化强度4πms》3790gs,剩磁4πmr》3415gs,矫顽力hc》550oe,各向异性场ha》13.6koe,铁磁共振线宽δh》389oe,但材料的hc较低,δh较大;专利cn111732427b公布的一种ga取代六角铁氧体材料性能指标:饱和磁化强度4πms》4167gs,矫顽力hc》2280oe,剩磁比ms/mr》0.88,各向异性场ha》18.02koe,铁磁共振线宽δh》260oe,虽然材料具有适宜的ms/mr与δh,但ha较高。从上述结果中不难看出,通过sc、cu等离子取代虽然可以降低m型六角铁氧体各向异性场,但磁性能恶化较为严重,不利于x波段微波器件设计。此外,印度尼赫鲁大学(j.alloys.compd.,2018,736:266-275)公布了一种溶胶凝胶
法制备bam/yig复合铁氧体,随着yig含量增加,各向异性场ha降低,铁磁共振线宽δh从2000oe下降到385oe,但此时矫顽力hc《600oe较低,不利于保持自偏置特性;陕西科技大学(mater.res.bull.,2014,60:195-200)公布的一种溶胶凝胶法一步合成bafe
12o19
/y3fe5o
12
复合材料性能指标:矫顽力hc=689oe、比饱和磁化强度σs=34.13emu/g、剩磁比mr/ms=0.584,铁磁共振线宽δh与各向异性场ha未公布,通过化学法合成的复合磁体虽然一定程度上能够改善磁体的微波性能,但制备技术复杂、反应过程难以控制、污染较大并且磁体取向困难,不适于自偏置器件应用。
5.基于上述,现有x波段自偏置器件用铁氧体材料难以兼具适宜各向异性场、高矫顽力和剩磁比特性。本发明提供一种x波段自偏置器件用双相复合铁氧体材料及其制备方法,将硬磁相高mr/ms和hc特性“嫁接”到高介低损耗软磁相上,研制兼具适宜各向异性场、高矫顽力和剩磁比、低铁磁共振线宽、高介电常数特性的双相复合铁氧体材料。
技术实现要素:6.本发明的目的在于,针对现有技术所涉及的x波段自偏置器件用铁氧体材料难以兼具适宜各向异性场、高矫顽力和剩磁比特性的技术难题,提出一种x波段自偏置器件用双相复合铁氧体材料及其制备方法,所研制的材料兼具适宜的饱和磁化强度(4πms≥3028gs)、适宜的各向异性场(ha≤11.56koe)、高的矫顽力(hc≥3754oe)、高剩磁比(mr/ms≥0.90)、低的铁磁共振线宽(δh≤350oe)和高的介电常数(ε'≥23)特性,适用于x波段自偏置器件设计。
7.本发明的核心思想是:将硬磁相高mr/ms和hc特性“嫁接”到高介低损耗软磁相上。硬磁相主配方采用适量缺铁、高矫顽力和剩磁比calaco取代srm铁氧体;软磁相主配方采用适量缺铁、高介电常数、低损耗bizrcav取代yig铁氧体。首先,硬磁相兼具高剩磁比和高矫顽力特性,根据各向异性补偿机制,引入低各向异性场的软磁相对高各向异性场的硬磁相进行补偿,可有效降低双相复合铁氧体的各向异性场,并且由于软磁相与硬磁相间的交换耦合作用,使得双相复合铁氧体仍保持较高的剩磁比与矫顽力。其次,在制备过程中,将软磁相以原料的形式加入到硬磁相预烧料之中;一方面,混合料在二次预烧过程中,富集在硬磁相颗粒周围的软磁相原料会逐渐在硬磁相颗粒表面反应生成软磁相,并将硬磁相“包裹”起来,接触面增加,有利于两相间发生交换耦合作用,并且在硬磁相颗粒表面生成的软磁相会与硬磁相表面悬挂键结合,两相结合更加稳定,保证了两相分布的均匀性;另一方面,两相间所形成的是非共格相界,这种相界里存在着一个成分起伏很大的过渡区,在双相复合铁氧体反磁化过程中会对畴壁位移产生较大的阻力,与交换耦合的共同作用下使双相复合铁氧体保持高的矫顽力。第三,bi
3+
、v
5+
的助熔效果可以降低yig铁氧体的烧结温度,使之与srm铁氧体烧结温度匹配,并且还可以使双相复合铁氧体进行致密化烧结,减小气孔率,有利于提高剩磁比,同时降低铁磁共振线宽;在烧结过程中,bi
3+
通过扩散进入六角铁氧体晶格之中能够提高双相复合铁氧体的介电特性,zr
4+
、v
5+
等高价离子的扩散能够抑制fe
2+
的生成,提高双相复合铁氧体的电阻率,降低微波介电损耗。最后,引入caco3、bi2o3、sio2、h3bo3与纳米batio3陶瓷粉末等掺杂剂,caco3、bi2o3、sio2、h3bo3等掺杂剂通过促晶/阻晶影响机制,调控双相复合铁氧体的晶粒与晶界特性,窄化粒度分布,提高取向度,改善烧结体的微观性能与磁性能,纳米batio3陶瓷粉末可以增加晶界电阻,提高电阻率,减小微波介电损
耗。即:通过各向异性补偿机制的控制,引入低各向异性yig铁氧体降低双相复合铁氧体材料的各向异性场;通过两次预烧,基于交换耦合与非共格相界磁化阻力作用实现双相复合铁氧体高的剩磁比与矫顽力;通过yig铁氧体主配方中bi
3+
、v
5+
的低温助熔作用提高双相复合铁氧体致密化程度,减小铁磁共振线宽,结合zr
4+
、v
5+
的扩散与纳米batio3陶瓷粉末掺杂剂的引入提高双相复合铁氧体晶粒/晶界电阻特性,同时bi
3+
的扩散提高双相复合铁氧体的介电特性;通过caco3、bi2o3、sio2、h3bo3掺杂剂阻晶/促晶作用机制,调控晶粒晶界特性,提高取向度,改善双相复合铁氧体的微结构与磁特性。
8.为实现上述目的,本发明采用的技术方案如下:
9.一种x波段自偏置器件用双相复合铁氧体材料,所述双相复合铁氧体材料包括srm铁氧体、yig铁氧体和掺杂剂;所述srm铁氧体的组分为:3.82~10.34mol%srco3、0.74~4.85mol%caco3、2.33~8.17mol%la2o3、1.45~6.49mol%co2o3、76.67~85.14mol%fe2o3,所述yig铁氧体的组分为:17.43~30.22mol%y2o3、5.22~10.41mol%bi2o3、5.56~10.68mol%zro2、5.23~11.32mol%caco3、3.2~14.2mol%v2o5、39.57~46.96mol%fe2o3,yig铁氧体与srm铁氧体的重量比为1:(0.11~9);
10.掺杂剂占复合铁氧体材料的重量百分比为:0.2~0.6wt.%sio2、0.1~0.8wt.%h3bo3、0.3~1.5wt.%caco3、0.4~1.2wt.%bi2o3、0.4~1.4wt.%batio3。
11.一种x波段自偏置器件用双相复合铁氧体材料的制备方法,包括以下步骤:
12.步骤1、配料
13.以srco3、caco3、la2o3、co2o3、fe2o3为原料,按照“3.82~10.34mol%srco3、0.74~4.85mol%caco3、2.33~8.17mol%la2o3、1.45~6.49mol%co2o3、76.67~85.14mol%fe2o
3”的比例称料,混料,得到srm铁氧体初始粉体;
14.步骤2、一次球磨
15.将步骤1得到的初始粉体在球磨机内混合均匀,球磨时间为8~20h;
16.步骤3、一次预烧
17.将步骤2得到的一次球磨料烘干,过筛,在1100~1400℃下进行预烧,升温速率为0.5~1.6℃/min,保温时间为1.5~6h,得到srm铁氧体预烧料;
18.步骤4、二次球磨
19.以y2o3、bi2o3、zro2、caco3、v2o5、fe2o3为原料,按照“17.43~30.22mol%y2o3、5.22~10.41mol%bi2o3、5.56~10.68mol%zro2、5.23~11.32mol%caco3、3.2~14.2mol%v2o5、39.57~46.96mol%fe2o
3”的比例配料,得到yig铁氧体;按照yig铁氧体与srm铁氧体初始粉体的重量比为1:(0.11~9)的比例,将yig铁氧体加入srm铁氧体预烧料中,球磨混合均匀,球磨时间为5~21h;
20.步骤5、二次预烧
21.将步骤4得到的二次球磨料烘干,在1000~1300℃下进行预烧,预烧时间为1~7h;
22.步骤6、掺杂
23.在步骤5得到的二次预烧料中加入掺杂剂,掺杂剂占复合铁氧体材料的重量百分比为:0.2~0.6wt.%sio2、0.1~0.8wt.%h3bo3、0.3~1.5wt.%caco3、0.4~1.2wt.%bi2o3、0.4~1.4wt.%batio3;
24.步骤7、三次球磨
25.将步骤6得到的混合粉料在球磨机中球磨15~28h混合均匀,粉料粒度控制在0.6~1.0μm之间;
26.步骤8、成型
27.将步骤7得到的三次球磨料脱水,脱水后浆料含水量控制在18wt%~35wt%之间,然后在磁场成型机下压制成型,成型磁场为1.3~1.6t,成型压力为85~130mpa;
28.步骤9、烧结
29.将步骤8压制得到的坯件进行烧结,烧结温度为1050~1200℃,保温时间为3~8h,烧结完成后,即可得到x波段自偏置器件用双相复合铁氧体材料。
30.对步骤9得到的双相复合铁氧体材料进行性能测试:饱和磁化强度4πms、剩余磁化强度4πmr、剩磁比mr/ms、矫顽力hc采用美国lakeshore 8604型振动样品磁强计测试,介电常数ε'采用美国keysight e4991b阻抗分析仪进行测试,铁磁共振线宽δh采用美国agilent n5227a矢量网络分析仪测试,各向异性场ha通过基特尔公式推导得出。
31.本发明制备的双相复合铁氧体材料最终技术指标如下:
32.饱和磁化强度4πms≥3028gs;
33.剩磁比mr/ms≥0.90;
34.矫顽力hc≥3754oe;
35.各向异性场ha≤11.56koe;
36.线宽δh≤350oe;
37.介电常数ε'≥23。
38.与现有技术相比,本发明的有益效果为:
39.本发明提供的一种x波段自偏置器件用双相复合铁氧体材料,兼具适宜的饱和磁化强度(4πms≥3028gs)、适宜的各向异性场(ha≤11.56koe)、高的矫顽力(hc≥3754oe)、高剩磁比(mr/ms≥0.90)、低的铁磁共振线宽(δh≤350oe)和高的介电常数(ε'≥23)特性。高的矫顽力与剩磁比能够保持高的内场,有利于实现自偏置特性;适宜的各向异性场可使自偏置器件工作在x波段,有利于自偏置器件低频应用;低的铁磁共振线宽有利于减小自偏置器件的插入损耗;高的介电常数可进一步减小自偏置器件的重量和体积,有利于整机系统小型轻量化、集成化发展。
附图说明
40.图1为实施例1得到的双相复合铁氧体材料的磁滞回线;
41.图2为实施例1得到的双相复合铁氧体材料的铁磁共振线宽拟合图;
42.图3为实施例1得到的双相复合铁氧体材料的扫描电镜照片;
43.图4为实施例2得到的双相复合铁氧体材料的扫描电镜照片;
44.图5为实施例3得到的双相复合铁氧体材料的扫描电镜照片;
45.图6为实施例4得到的双相复合铁氧体材料的扫描电镜照片。
具体实施方式
46.针对x波段微波器件小型轻量化、集成化的应用需求,本发明提供了一种x波段自偏置器件用双相复合铁氧体材料及其制备方法,克服现有x波段自偏置器件用铁氧体材料
难以兼具适宜各向异性场、高矫顽力和剩磁比特性的技术难题。将srm铁氧体材料高mr/ms和hc特性“嫁接”到高介低损耗yig铁氧体上。在固相法的基础上采用两次预烧,确保反应可控并实现两相分布的均匀性。利用各向异性补偿机制、交换耦合理论、磁化阻力机制、材料表界面理论、扩散理论深入分析yig的引入对双相复合铁氧体性能的影响机制。结合烧结动力学和促晶/阻晶机制明确添加剂对双相复合铁氧体显微结构和磁性能的影响,制定最佳的主配方与添加剂配方,并对工艺进行优化,最终研制出兼具适宜各向异性场、高矫顽力和剩磁比、低铁磁共振线宽、高介电常数特性的双相复合铁氧体材料。
47.实施例1~4
48.步骤1、配料
49.srm铁氧体以srco3、caco3、la2o3、co2o3、fe2o3为原料,按照下表所示比例配制srm铁氧体初始粉体,实施例1~4中srm铁氧体配方见下表:
[0050][0051]
步骤2、一次球磨
[0052]
将步骤1得到的初始粉体在行星式球磨机内混合均匀,球磨时间为12h;
[0053]
步骤3、一次预烧
[0054]
将步骤2得到的一次球磨料烘干,过筛,在1250℃下进行预烧,升温速率为0.8℃/min,保温时间为4h,得到srm铁氧体预烧料;
[0055]
步骤4、二次球磨
[0056]
yig铁氧体以y2o3、bi2o3、zro2、caco3、v2o5、fe2o3为原料,按照下表所示比例配料,实施例1~4中yig铁氧体配方见下表:
[0057][0058]
按照yig铁氧体与srm铁氧体初始粉体的重量比为1:0.82的比例,将yig铁氧体加入srm铁氧体预烧料中,在行星式球磨机中球磨混合均匀,球磨时间为16h;
[0059]
步骤5、二次预烧
[0060]
将步骤4得到的二次球磨料烘干,在1100℃下进行预烧,预烧时间为3h;
[0061]
步骤6、掺杂
[0062]
在步骤5得到的二次预烧料中加入掺杂剂,掺杂剂占复合铁氧体材料的重量百分比为:0.4wt.%sio2、0.6wt.%h3bo3、1.2wt.%caco3、0.8wt.%bi2o3、0.7wt.%batio3;
[0063]
步骤7、三次球磨
[0064]
将步骤6得到的混合粉料在行星式球磨机中球磨18h混合均匀,粉料粒度控制在0.6~1.0μm之间;
[0065]
步骤8、成型
[0066]
将步骤7得到的三次球磨料脱水,脱水后浆料含水量控制在30wt%~35wt%之间,然后在磁场成型机下压制成型,成型磁场为1.4t,成型压力为120mpa;
[0067]
步骤9、烧结
[0068]
将步骤8压制得到的坯件进行烧结,烧结温度为1160℃,保温时间为5h,烧结完成后,即可得到x波段自偏置器件用双相复合铁氧体材料。
[0069]
对步骤9得到的双相复合铁氧体材料进行性能测试:饱和磁化强度4πms、剩余磁化强度4πmr、剩磁比mr/ms、矫顽力hc采用美国lakeshore 8604型振动样品磁强计测试,介电常数ε'采用美国keysight e4991b阻抗分析仪进行测试,铁磁共振线宽δh采用美国agilent n5227a矢量网络分析仪测试,各向异性场ha通过基特尔公式推导得出。
[0070]
基于上述工艺研制的双相复合铁氧体材料,实施例1~4性能参数如下:
[0071]