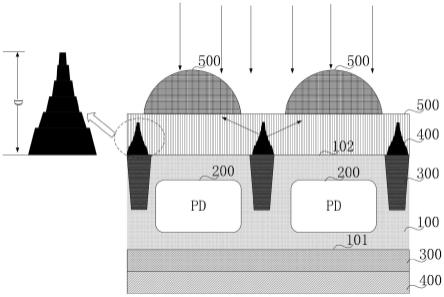
1.本发明涉及半导体集成电路技术领域,尤其涉及一种背照式像元结构及其制备方法。
背景技术:2.目前,随着互补金属氧化物半导体(complementarymetal oxide semiconductor,cmos)图像传感器在工业、车载、道路监控和高速相机中越来越广泛的应用,对于可以捕捉高速运动物体图像的图像传感器的需求进一步提高。为了监控高速运动的物体,就需要使用全局曝光式快门像元结构,其中,寄生光灵敏度是全局曝光式快门像元结构中一个非常重要的指标。
3.图1示出了传统的背照式像元结构示意图,传统的背照式图像传感器包括光电二极管(photo diode,pd)、传输管(transmission tube,tx)、复位管(restore tube,rst)和电荷存储的浮置扩散区(floating diffusion,fd)。如图1所示的背照式结构,光线直接入射到感光单元,无需经过金属互连层和介质层,这极大提高了入射光量。随着像元尺寸的不断减小,感光单元上可接受到的光更少,目前主要通过添加微透镜的方式,将光线集中到感光单元中,进而提高进光量。但是,如图2所示,现有微透镜一般都是半圆形的结构,其存在的问题是每个感光单元四周无微透镜,导致感光单元四周入射的光线无法被微透镜收集,进而导致入射光线损失,量子效率降低。
4.因此,如何改善感光单元四周因没有微透镜而导致入射光线损失的问题,是本领域技术人员亟待解决的问题。
技术实现要素:5.本发明实施例提供一种背照式像元结构及其制备方法,用改善光损失问题,增加感光单元的入射光量,提高量子效率。
6.第一方面,本发明提供一种背照式像元结构,包括:半导体衬底100,所述半导体衬底100具有正表面101和背表面102;感光单元200设于半导体衬底100内,且靠近半导体衬底100的正表面;金属互连层300及介质层400,叠加覆盖于所述半导体衬底100的正表面;光线入射层500,覆盖于所述半导体衬底100的背表面;微透镜600,覆盖于所述光线入射层且微透镜600位置与所述感光单元200相对应;深槽隔离103位于所述半导体衬底100内,且位于感光单元200旁侧,并靠近半导体衬底100的背表面;所述光线入射层500包括金属栅格501,且所述金属栅格501与所述深槽隔离103对应设置,所述金属栅格501沿着由底部指向顶部的方向,金属栅格501的关键尺寸逐渐缩小,所述金属栅格501的顶部远离感光单元200,所述金属栅格501的底部靠近感光单元200。
7.本发明提供的背照式像元结构的有益效果在于:因金属栅格501的关键尺寸沿着由底部指向顶部的方向逐渐缩小,所以可以有效地将感光单元四周的入射光线折射至微透镜,进而提高微透镜的入射光量,提高量子效率。
8.可选地,金属栅格为金属堆叠结构,所述金属堆叠结构包括至少两层长度不等的金属层。
9.可选地,金属堆叠结构的每层金属层的剖面形状为底部宽且顶部窄的梯形状,所述金属层的底部靠近感光单元200,所述金属层的底部远离感光单元200,梯形状进一步地有助于将感光单元四周的入射光线折射至微透镜。
10.可选地,所述金属堆叠结构中的第二金属层的关键尺寸小于第一金属层的关键尺寸,所述第一金属层和所述第二金属层为金属堆叠结构中任意相邻的两金属层。
11.可选地,所述金属层的梯形形状的倾斜角度落入区间[45
°
,90
°
)。
[0012]
可选地,所述金属栅格501的厚度大于0.1um。
[0013]
第二方面,本发明提供一种背照式像元结构的制备方法,该方法包括如下步骤:提供半导体衬底,所述半导体衬底具有正表面101和背表面102;在所述半导体衬底100的正表面101形成感光单元200;在所述半导体衬底100的正表面101上形成金属互连层300及介质层400;在所述半导体衬底100内形成深槽隔离103,所述深槽隔离103靠近半导体衬底100的背表面;在所述半导体衬底100的背表面102上形成光线入射层500,所述光线入射层500包括金属栅格501,所述金属栅格501与所述深槽隔离103对应设置,所述金属栅格501沿着由底部指向顶部的方向,金属栅格501的关键尺寸逐渐缩小,所述金属栅格501的顶部远离感光单元200,所述金属栅格501的底部靠近感光单元200;在所述光线入射层500的背表面102上形成微透镜600;所述微透镜600置于相邻的金属栅格501之间,且微透镜600位置与所述感光单元200相对应。
[0014]
可选地,在所述半导体衬底100的背表面102上形成光线入射层500,包括:在所述半导体衬底100的背表面102上沉积阻挡层;在所述阻挡层上方沉积金属并刻蚀,形成一金属层;在所述一金属层上方沉积介质层并平坦化;在所述一金属层上方沉积金属并刻蚀,形成另一金属层;在所述二金属层上方沉积介质层并平坦化;重复执行在所述阻挡层上方沉积金属并刻蚀,直至金属层达到预设层数。
[0015]
可选地,在所述光线入射层500的背表面102上形成微透镜600,包括:通过光刻胶回流方式,在所述光线入射层500的背表面102上形成微透镜600。
[0016]
可选地,所述金属堆叠结构中的第二金属层的关键尺寸小于第一金属层的关键尺寸,所述第一金属层和所述第二金属层为金属堆叠结构中任意相邻的两金属层。
[0017]
本发明提供的制备方法的有益效果可以参见上述结构部分的描述,该制备方法通过在感光单元周围形成金属栅格501,有效地将感光单元四周的入射光线折射至微透镜,进而提高微透镜的入射光量,提高量子效率。
附图说明
[0018]
为了更清楚地说明本发明实施例中的技术方案,下面将对实施例描述中所需要使用的附图作简要介绍,显而易见地,下面描述中的附图仅仅是本发明的一些实施例,对于本领域的普通技术人员来讲,在不付出创造性劳动的前提下,还可以根据这些附图获得其他的附图。
[0019]
图1和图2为现有技术提供的一种背照式像元结构示意图;
[0020]
图3为本发明实施例提供的一种背照式像元结构示意图;
[0021]
图4为本发明实施例提供的另一种背照式像元结构示意图;
[0022]
图5为本发明实施例提供的一种金属层的剖面结构示意图;
[0023]
图6为本发明实施例提供的背照式像元结构的金属栅格的剖面结构示意图;
[0024]
图7为本发明实施例提供的背照式像元结构的金属栅格的另一种剖面结构示意图;
[0025]
图8为本发明实施例提供的一种背照式像元结构的制备方法流程示意图;
[0026]
图9a和图9e为本发明实施例提供的形成金属栅格的工艺制备各中间阶段示意图。
[0027]
元件标号说明
[0028]
100半导体衬底;101半导体衬底的正面;102半导体衬底的背面;103深槽隔离;
[0029]
200感光单元;
[0030]
300金属互连层;
[0031]
400介质层;
[0032]
500光线入射层;501金属栅格;
[0033]
600微透镜。
具体实施方式
[0034]
为使本发明的内容更加清楚易懂,以下结合说明书附图,对本发明的内容作进一步说明。当然本发明并不局限于该具体实施例,本领域内的技术人员所熟知的一般替换也涵盖在本发明的保护范围内。
[0035]
需要说明的是,在下述的具体实施方式中,在详述本发明的实施方式时,为了清楚地表示本发明的结构以便于说明,特对附图中的结构不依照一般比例绘图,并进行了局部放大、变形及简化处理,因此,应避免以此作为对本发明的限定来加以理解。
[0036]
根据本发明的主旨构思,本发明提供一种背照式像元结构,如图3所示,包括:半导体衬底100、感光单元200、金属互连层300、介质层400、光线入射层500、微透镜600。
[0037]
具体来说,半导体衬底100具有正表面101及背表面102。感光单元200设于半导体衬底100内,且靠近半导体衬底100的正表面。金属互连层300及介质层400,叠加覆盖于所述半导体衬底100的正表面。光线入射层500,覆盖于所述半导体衬底100的背表面102,微透镜600覆盖于所述光线入射层500,且微透镜600位置与所述感光单元200相对应。
[0038]
其中,深槽隔离103位于所述半导体衬底100内,且位于感光单元200旁侧,并靠近半导体衬底100的背表面。深槽隔离103的形成方法可以是通过利用氮化硅掩膜经过沉积、图形化、刻蚀硅后形成槽,并在槽中填充沉积氧化物,从而与半导体衬底100相隔离,深槽隔离103能作为有效的阻挡层,对感光单元200起到隔离作用,以改善电学串扰。
[0039]
所述光线入射层500中包括金属栅格501,且所述金属栅格501与所述深槽隔离103对应设置,所述金属栅格501沿着由底部指向顶部的方向,金属栅格501的关键尺寸逐渐缩小。所述金属栅格501的顶部远离感光单元200,所述金属栅格501的底部靠近感光单元200。可选地,如图3所示,金属栅格为金属堆叠结构,所述金属堆叠结构包括至少两层长度不等的金属层,从图3中可见,一方面,金属栅格501可以改善光学串扰,另一方面因金属栅格501的关键尺寸沿着由底部指向顶部的方向a逐渐缩小,所以可以有效地将感光单元四周的入射光线折射至微透镜,进而提高微透镜的入射光量,提高量子效率。
[0040]
可选的,金属堆叠结构的每层金属层的剖面形状为底部宽且顶部窄的梯形状,所述金属层的底部靠近感光单元200,所述金属层的底部远离感光单元200。可选地,所述金属栅格501的厚度d大于0.1um,以达到充分折射感光单元周围的光线。示例性地,如图5所示,单层金属层的梯形状的倾斜角度α落入区间[45
°
,90
°
)。
[0041]
可选的,所述金属堆叠结构中的第二金属层的关键尺寸小于第一金属层的关键尺寸,所述第一金属层和所述第二金属层为金属堆叠结构中任意相邻的两金属层。
[0042]
可选的,金属栅格501的剖面形状还可以是如图6所示的直角三角状,或者是如图7所示的等腰三角状,应理解,本实施例对金属栅格的剖面形状并不作具体限定,金属栅格501的侧壁具有一定的倾斜度,能够实现反射入射光线至微透镜600即可。
[0043]
为使本发明的目的、技术方案和优点更加清楚,下面进一步结合图3示出了一种背照式像元结构的制备方法流程示意图。参见图8所示,本发明实施例提供的背照式像元结构的制备工艺包括如下步骤:
[0044]
s801,提供半导体衬底100,所述半导体衬底具有正表面101和背表面102。
[0045]
如图4所示,半导体衬底100可以是n型或p型硅衬底。所述半导体衬底202的材料包括硅、锗、锗化硅、碳化硅、砷化镓、镓化铟中的一种或多种组合,所述半导体衬底202还可以为绝缘体上的硅半导体衬底或者绝缘体上的锗半导体衬底。
[0046]
s802,在所述半导体衬底100的正表面101形成感光单元200。
[0047]
该步骤中,可以采用离子注入工艺对所述半导体衬底100进行离子注入形成所述感光单元201,离子注入工艺的注入能量可以为为10kev~1200kev,感光单元201可以为光电二极管。
[0048]
s803,在所述半导体衬底100的正表面101上形成金属互连层300及介质层400。
[0049]
s804,在所述半导体衬底100内形成深槽隔离103,所述深槽隔离103靠近半导体衬底100的背表面。
[0050]
上述s803和s804中,首先在半导体衬底100的正面形成金属互连层300和介质层400;金属互连层300和介质层400形成之后,通过成熟的背照式工艺,在半导体衬底背面通过键合、减薄、图形化等步骤形成深槽隔离103。所述深槽隔离103临近所述感光单元200,通过深槽隔离以形成深沟槽,进而对感光单元200起到隔离作用,以改善电学串扰。
[0051]
s805,在所述半导体衬底100的背表面102上形成光线入射层500,所述光线入射层500包括金属栅格501,所述金属栅格501与所述深槽隔离103对应设置,所述金属栅格501沿着由底部指向顶部的方向,金属栅格501的关键尺寸逐渐缩小,所述金属栅格501的顶部远离感光单元200,所述金属栅格501的底部靠近感光单元200。
[0052]
s806,在所述光线入射层500的背表面102上形成微透镜600;所述微透镜600置于相邻的金属栅格501之间,且微透镜600位置与所述感光单元200相对应。
[0053]
示例性地,该步骤可以通过光刻胶回流方式,在所述光线入射层500的背表面102上形成微透镜600。
[0054]
应理解,上述s805中的金属栅格501的结构可以参见上述产品实施例。示例地,参见图9,在所述半导体衬底100的背表面102上形成光线入射层包括如下步骤:a、在所述阻挡层上方沉积一层金属,如图9a所示;b、对该层金属刻蚀,形成一金属层,如图9b所示;c、在所述一金属层上方沉积介质层并平坦化,如图9c所示;d、在所述一金属层上方沉积金属并刻
蚀,形成另一金属层,如图9d所示;e、在所述二金属层上方沉积介质层并平坦化,如图9e所示;f、重复执行在所述阻挡层上方沉积金属并刻蚀,直至金属层达到预设层数,如图3所示。可选地,在执行上述步骤a之前,还可以所述半导体衬底100的背表面102上沉积阻挡层。该实施例中,金属栅格501的结构一方面改善光学串扰,另一方面因金属栅格501的关键尺寸沿着由底部指向顶部的方向a逐渐缩小,所以可以有效地将感光单元四周的入射光线折射至微透镜600,进而提高微透镜600的入射光量,提高量子效率。
[0055]
综上所述,本实施例在感光单元周围形成具有上述结构形状的金属栅格501,有效地将感光单元四周的入射光线折射至微透镜,进而提高微透镜的入射光量,提高量子效率。
[0056]
以上所述的仅为本发明的优选实施例,所述实施例并非用以限制本发明的专利保护范围,因此凡是运用本发明的说明书及附图内容所作的等同结构变化,同理均应包含在本发明的保护范围内。
[0057]
对所公开的实施例的上述说明,使本领域专业技术人员能够实现或使用本发明。
[0058]
对这些实施例的多种修改对本领域的专业技术人员来说将是显而易见的,本文中所定义的一般原理可以在不脱离本发明的精神或范围的情况下,在其它实施例中实现。因此,本发明将不会被限制于本文所示的这些实施例,而是要符合与本文所公开的原理和新颖特点相一致的最宽的范围。