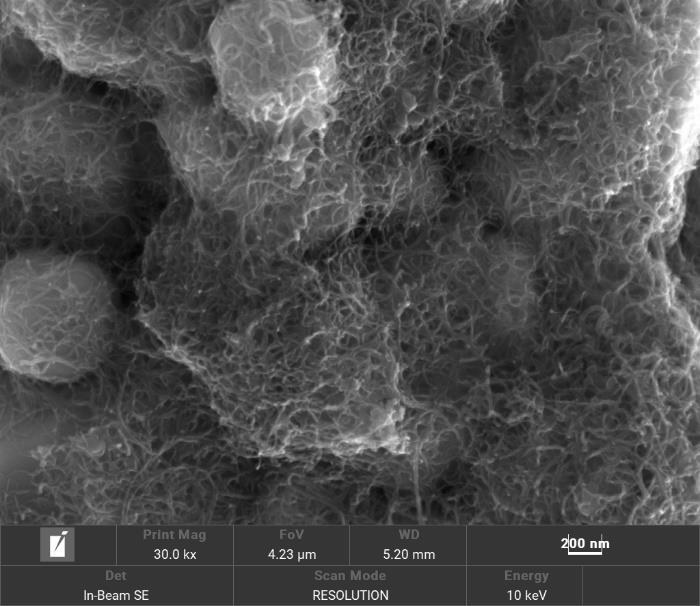
1.本发明属于锂离子电池技术领域,尤其涉及一种锂离子电池正极浆料的制备方法和正极浆料、正极极片。
背景技术:2.锂离子电池的正负极材料普遍存在着导电性差的问题,在电极中加入导电剂增强电极电子传输效率降低电极极化对发挥活性材料有效容量是十分重要的。
3.锂离子电池目前的生产过程中,通常采用的是导电炭黑和新型导电剂如碳纳米管、石墨烯及相关复合导电剂。导电炭黑通常以粉料的形式出现,但是其导电性能较差,而且要想获得较好的导电网络需添加较多用量,影响了锂离子电池的容量。而新型导电剂虽然导电性能优异,但均以nmp为分散介质。nmp体系的新型导电浆料有效固含较低,nmp占90%以上,导致了较高的生产物料成本和仓储及运输成本,对生产企业和使用成本均造成了较大的成本压力。同时导电浆料由于其易沉降的特性,使用有效期短,且每次使用前都需要再搅拌,不便于使用。因此采用新型导电剂粉料可以有效规避锂电池厂在导电剂上的仓储及运输成本。
4.目前锂电池厂普遍选择湿法混料工艺作为主流工艺进行正极浆料的制备,其基本过程为溶胶-导电剂-添加剂-活性物质。然而常规配料搅拌的工艺周期长,溶胶、添加导电剂、加上主材的总体搅拌混合时间超过10h,并伴有加工性能不良的隐患,影响涂布效果,分散效果差、涂覆不均匀还会导致电池容量分布比较分散。
5.综上所述,开发一种工序时间短、浆料内物质良好分散、涂布性能好、极片质量高且与粉料导电剂适配的锂离子电池正极浆料的制备工艺具有重要的意义。
技术实现要素:6.本发明提供一种锂离子电池正极浆料的制备方法和正极浆料、正极极片,旨在提供制备效率高且效果好的锂离子电池正极浆料的制备方法。
7.第一方面,本技术提供了一种锂离子电池正极浆料的制备方法,包括:提供预定比例的正极活性物质粉料、粘结剂粉料和导电剂粉料,其中,预定比例为94-96:2:2-4;在水浴冷却且密封的环境中将正极活性物质粉料、粘结剂粉料和导电剂粉料进行混合搅拌,以得到第一混合物;在所述第一混合物加入有机溶剂,以使所述第一混合物湿润,后用有机溶剂稀释、搅拌、分散、捏合和刮料,以得到第二混合物;将所述第二混合物在真空负压条件下进行脱泡,以得到所述锂离子电池正极浆料。
8.可选的,所述正极活性物质粉料包括锰酸锂、磷酸铁锂、镍钴锰三元锂中至少一种。
9.可选的,所述粘结剂粉料包括聚偏二氟乙烯、聚偏氟乙烯、偏二氟乙烯的均聚物、聚偏二氟乙烯共聚物中至少一种。
10.可选的,所述有机溶剂选自n-甲基吡咯烷酮、n-二甲基酰胺、二甲基亚砜中的一种。
11.所述导电剂粉料包括导电炭黑、碳纳米管、石墨烯中至少一种。
12.可选的,混合搅拌中,搅拌的速度为25-40rpm/min、分散的速度为600-1000rpm/min,混合搅拌的时间为20-45min。
13.可选的,所述在所述第一混合物加入n-甲基吡咯烷酮,以使所述第一混合物湿润包括:在所述第一混合物加入n-甲基吡咯烷酮总量的30%-50%,以30-45rpm/min的速度进行搅拌、在600-1000rpm/min的速度进行分散,进行24-48min,以使第一混合物充分与n-甲基吡咯烷酮接触;以40-50rpm/min的速度进行搅拌、在10000-1400rpm/min的速度进行分散,进行24-48min,以使所述第一混合物湿润。
14.可选的,所述用n-甲基吡咯烷酮稀释、搅拌、分散、捏合和刮料包括:1)用n-甲基吡咯烷酮总量的15%-25%加入所述第一混合物,以40-50rpm/min的速度进行搅拌、以1000-1400rpm/min的速度进行分散,时长为6-15min;2)以40-50rpm/min的速度进行搅拌、以1600-2000rpm/min的速度进行分散,时长为12-25min,并刮料;3)将n-甲基吡咯烷酮总量的10%-15%加入,以40-50rpm/min的速度进行搅拌、以1600-2000rpm/min的速度进行分散,时长为30-65min,随后进行刮料;4)将n-甲基吡咯烷酮总量的剩余部分加入,以40-50rpm/min的速度进行搅拌、以1600-2000rpm/min的速度进行分散,时长为30-65min,随后进行刮料;5)当第一混合物在25-40℃时的粘度为2000-8000mpa
·
s,以40-50rpm/min的速度进行搅拌、以1300-1700rpm/min的速度进行分散,时长为15-25min。
15.可选的,在真空度为-0 .09mpa~-0 .14mpa的条件下进行进行脱泡。
16.可选的,脱泡时,以15-25rpm/min的速度进行搅拌,搅拌时长为12-25min。
17.可选的,锂离子电池正极浆料的固含量为60-70%。
18.第二方面,本技术提供了一种锂离子电池正极浆料,由第一方面的制备方法得到。
19.第三方面,本技术提供了一种正极极片,包括集流体、以及设置于所述集流体至少一侧的正极活性材料层,所述正极活性材料层由权利要求9得到。
20.本技术提供的正极浆料的制备方法,通过改变现有投料的顺序,再通过湿润、稀释、搅拌、分散、捏合和刮料,从而改善分散效果,提高浆料的加工性能,使混料均匀、易于涂布,缩短搅拌周期,提高设备利用率;使制得的正极浆料分散性高、均一性强以及粘度和细度处在合适的范围,从而载涂布于集流体后显著降低了正极极片的电阻,提升了电池性能。
附图说明
21.图1为本发明实施例1正极浆料涂布制得正极极片辊压前的sem图。
具体实施方式
22.下面将详细描述本技术的各个方面的特征和示例性实施例,为了使本技术的目的、技术方案及优点更加清楚明白,以下结合具体实施例,对本技术进行进一步详细描述。应理解,此处所描述的具体实施例仅意在解释本技术,而不是限定本技术。对于本领域技术人员来说,本技术可以在不需要这些具体细节中的一些细节的情况下实施。下面对实施例的描述仅仅是为了通过示出本技术的示例来提供对本技术更好的理解。
23.需要说明的是,在本文中,诸如第一和第二等之类的关系术语仅仅用来将一个实体或者操作与另一个实体或操作区分开来,而不一定要求或者暗示这些实体或操作之间存在任何这种实际的关系或者顺序。而且,术语“包括”、“包含”或者其任何其他变体意在涵盖非排他性的包含,从而使得包括一系列要素的过程、方法、物品或者设备不仅包括那些要素,而且还包括没有明确列出的其他要素,或者是还包括为这种过程、方法、物品或者设备所固有的要素。在没有更多限制的情况下,由语句“包括
……”
限定的要素,并不排除在包括所述要素的过程、方法、物品或者设备中还存在另外的相同要素。
24.锂离子电池的正负极材料普遍存在着导电性差的问题,在电极中加入导电剂增强电极电子传输效率降低电极极化对发挥活性材料有效容量是十分重要的。与常用的导电石墨等导电剂相比石墨烯具有更优异的导电性能以及更高的比表面积,更少量的石墨烯即可达到同等导电效果等优点,因而石墨烯作为电极导电剂开始被广泛应用。
25.锂离子电池目前的生产过程中,通常采用的导电剂以nmp为分散介质。但是nmp体系导电浆料有效固含较低,nmp占90%以上,导致生产材料成本较高,仓储及运输成本较高,对企业成本压力较大。而导电剂粉料可以通过预分散工艺有效规避锂电池厂在导电剂上的仓储及运输成本,同时与干法混料匀浆工艺完美适配。
26.目前,锂电池厂普遍选择湿法混料工艺进行匀浆,基本过程为制备溶胶、添加导电剂、添加添加剂、添加活性物质。然而常规配料搅拌的工艺周期长,溶胶、添加导电剂、加上主材的总体搅拌混合时间超过10h,并伴有加工性能不良的隐患,影响涂布效果,分散效果差、涂覆不均匀还会导致电池容量分布比较分散。然而,目前却没有完善的适配干粉导电剂的锂离子电池匀浆浆料的制备工艺。
27.经研究,本技术第一方面提供了一种锂离子电池正极浆料的制备方法,包括:提供预定比例的正极活性物质粉料、粘结剂粉料和导电剂粉料,其中,预定比例为94-96:2:2-4;在水浴冷却且密封的环境中将正极活性物质粉料、粘结剂粉料和导电剂粉料进行混合搅拌,以得到第一混合物;在所述第一混合物加入有机溶剂,以使所述第一混合物湿润,后用有机溶剂酮稀释、搅拌、分散、捏合和刮料,以得到第二混合物;将所述第二混合物在真空负压条件下进行脱泡,以得到所述锂离子电池正极浆料。
28.在上述制备方法中,混合、搅拌和分散等可以在搅拌缸中常压态进行,可以加入加入适量n-甲基吡咯烷酮润湿泥状进行搅拌;搅拌和高速分散并分次加入n-甲基吡咯烷酮,可以调节锂离子电池正极浆料的均匀性和粘度。
29.上述制备方法能大大缩短正极匀浆工艺时间,出料的正极浆料固含量高且粘度适
宜、分散性好、涂布效果好。
30.在水浴冷却且密封的环境中将正极活性物质粉料、粘结剂粉料和导电剂粉料进行混合搅拌,以得到第一混合物,可以使用循环冷却水达到降低搅拌温度的目的,还可以在低温环境中进行搅拌,以避免第一混合物在搅拌产生的高温中改变其性能,从而影响浆料性能。
31.使用时,正极活性物质粉料的平均粒径可以为0.5-25μm、粘结剂粉料的平均粒径可以为10-50μm;导电剂粉料的平均粒径可以为4.5-12μm;可以采用马尔文激光粒度仪mastersizer3000型号进行检测得到,通过上述制备方法,锂离子电池正极浆料中的固态颗粒可以为4.5-50μm,且在n-甲基吡咯烷酮中分布均匀,特性粘度为2000-8000mpa
·
s,可选为4000mpa
·
s。
32.进行脱泡处理后,可以关闭循环水,排气直到内外气压平衡,得到浆料制品。预定比例为还可以为95.5:2:2.5。
33.在一些实施例中,正极活性物质粉料包括锰酸锂、磷酸铁锂、镍钴锰三元锂中至少一种。正极活性物质粉料包括但不限于:锰酸锂((limn2o4)、:镍钴锰酸锂(lini
x
coymn
1-x-y
o2)、钴酸锂(licoo2)、镍酸锂(linio2)、锰酸锂(limn2o4)。
34.在一些实施例中,粘结剂粉料包括聚偏二氟乙烯、聚偏氟乙烯、偏二氟乙烯的均聚物、聚偏二氟乙烯共聚物中至少一种。
35.在一些实施例中,所述有机溶剂选自n-甲基吡咯烷酮、n-二甲基酰胺、二甲基亚砜中的一种。
36.在一些实施例中,导电剂粉料包括导电炭黑、碳纳米管、石墨烯中至少一种。导电剂粉料包括还包括石墨烯复合干粉导电剂,石墨烯复合干粉导电剂包括但不限于:石墨烯复合导电炭黑(sp)、石墨烯复合碳纳米管(cnt)、石墨烯复合导电石墨(ks6、sfg6)、石墨烯复合科琴黑(ec-300j、ecp、ecp-600jd)以及石墨烯、炭黑、碳纳米管三元复合导电剂。
37.在一些实施例中,锂离子电池正极活性物质采用磷酸铁锂锂,导电剂采用石墨烯+sp+cnt复合干粉导电剂,粘接剂采用聚偏氟乙烯(pvdf)。
38.在一些实施例中,混合搅拌中,搅拌的速度为25-40rpm/min、分散的速度为600-1000rpm/min,混合搅拌的时间为20-45min。
39.在上述实施例中,搅拌器里面可以有个搅拌轴和分散轴,搅拌轴的转度可以为搅拌的速度;分散轴的转度可以为分散的速度为600-1000rpm/min。
40.在一些实施例中,所述在所述第一混合物加入n-甲基吡咯烷酮,以使所述第一混合物湿润包括:在第一混合物加入n-甲基吡咯烷酮总量的30%-50%,以30-45rpm/min的速度进行搅拌、在600-1000rpm/min的速度进行分散,进行24-48min,以使第一混合物充分与n-甲基吡咯烷酮接触;以40-50rpm/min的速度进行搅拌、在10000-1400rpm/min的速度进行分散,进行24-48min,以使所述第一混合物湿润。
41.上述添加n-甲基吡咯烷酮总量的30%-50%,进行两阶段的搅拌和分散,还可以进行捏合,使第一混合物与n-甲基吡咯烷酮充分接触,使粉末物料充分接触,避免粉末物料中的空隙仍被空气等填充,没有与n-甲基吡咯烷酮接触。
42.在上述搅拌和分散速度中使混合物湿润,可以提高效率,同时使液体与粉料充分接触。
43.在一些实施例中,所述用n-甲基吡咯烷酮稀释、搅拌、分散、捏合和刮料包括:1)用n-甲基吡咯烷酮总量的15%-25%加入所述第一混合物,以40-50rpm/min的速度进行搅拌、以1000-1400rpm/min的速度进行分散,时长为6-15min;2)以40-50rpm/min的速度进行搅拌、以1600-2000rpm/min的速度进行分散,时长为12-25min,并刮料;3)将n-甲基吡咯烷酮总量的10%-15%加入,以40-50rpm/min的速度进行搅拌、以1600-2000rpm/min的速度进行分散,时长为30-65min,随后进行刮料;4)将n-甲基吡咯烷酮总量的剩余部分加入,以40-50rpm/min的速度进行搅拌、以1600-2000rpm/min的速度进行分散,时长为30-65min,随后进行刮料;5)当第一混合物在25-40℃时的粘度为2000-8000mpa
·
s,以40-50rpm/min的速度进行搅拌、以1300-1700rpm/min的速度进行分散,时长为15-25min。
44.上述稀释、搅拌、分散、捏合可以改变混合物的粘度,使混合物更加均匀稳定。将n-甲基吡咯烷酮(nmp)分批次加入,可以在高固量的情况下(如50-70%),有利于浆料在高剪切力的作用下将各粉料混合物分散均匀,和之前的大批量加入的稀释步骤和分步逐步加入n-甲基吡咯烷酮,可以保证活性物质、导电剂分散得更均匀,混合状态更好。
45.上述粘度的的检测方法为使用上海平轩ndj-9s型号的粘度计在25-40℃时进行检测得到。
46.在上述搅拌和分散速度中使混合物充分混合均匀,可以在保护其电学性能的基础上,使其充分混合,并提高效率。
47.在粉料混合物进行润湿搅拌的基础上,上述稀释、搅拌、分散、捏合工艺,可以有效实现活性物质粉料、粘结剂与干粉导电剂在高剪切力的作用下有效混合与分散,改善导电剂和导电浆料分散效果,大大缩短制程周期。
48.在一些实施例中,在真空度为-0 .09mpa~-0 .14mpa的条件下进行进行脱泡。具有去除浆料内气泡,防止极片表面出现缺陷,提高极片质量的积极作用。
49.在一些实施例中,脱泡时,以15-25rpm/min的速度进行搅拌,搅拌时长为12-25min。上述搅拌速度具有促进浆料脱泡的作用,没有使用分散轴进行分散的原因在于此时浆料已有效均匀分散,无需再用分散轴进行分散,而且高速分散时浆料可能会飞溅进入真空管中,导致真空泵堵塞或者损坏。
50.在一些实施例中,锂离子电池正极浆料的固含量为60-70%。
51.根据本技术的制备方法,从传统湿法混料工艺的10小时以上,可以缩短到3-6小时,同时可以将浆料锂离子电池正极浆料固含量提升到60-70%,并将粘度降低到2000-8000mpa
·
s。
52.第二方面,本技术提供了一种锂离子电池正极浆料,由第一方面的制备方法得到。
53.第三方面,本技术提供了一种正极极片,包括集流体、以及设置于所述集流体至少一侧的正极活性材料层,所述正极活性材料层由权利要求9得到。
实施例
54.下述实施例更具体地描述了本技术公开的内容,这些实施例仅仅用于阐述性说明,因为在本技术公开内容的范围内进行各种修改和变化对本领域技术人员来说是明显的。除非另有声明,以下实施例中所报道的所有份、百分比、和比值都是基于重量计,而且实施例中使用的所有试剂都可商购获得或是按照常规方法进行合成获得,并且可直接使用而无需进一步处理,以及实施例中使用的仪器均可商购获得。
55.实施例1-5锂离子电池正极浆料的制备:s1、将正极活性物质粉料(锰酸锂、磷酸铁锂、镍钴锰三元锂等)、粘结剂粉料(聚偏二氟乙烯等)和导电剂粉料(导电炭黑、碳纳米管、石墨烯以及石墨烯基复合干粉导电剂)按一定比例加入行星搅拌机中,并常温常压密封,均匀搅拌混合,得到干粉混合物;s2、进行混合操作,开启循环冷却水,开启搅拌25-40rpm/min、分散600-1000rpm/min,搅拌时长20-45min,使各粉末状物料充分混合;s3、开罐,将50%的nmp溶剂加入充分混合后的物料中,随后开启搅拌30-45rpm/min、分散600-1000rpm/min,时长为24-48min,进行初步溶解与混合;接着将转速提升到搅拌40-50rpm/min、分散1000-1400,时长为24-48min,结束后下降开罐并将壁内和转子上的浆料刮下;s4、将20%的nmp溶剂加入,以使粉料湿润,随后开启搅拌40-50rpm/min、分散1000-1400rpm/min,时长为6-15min;接着转速提升到搅拌40-50rpm/min、分散1600-2000rpm/min,时长为12-25min,结束后进行刮料操作;s6、将12%的nmp溶剂加入,随后开启搅拌40-50rpm/min、分散1600-2000rpm/min,时长为30-65min,随后进行刮料操作;s7、将剩余的18%nmp溶剂加入,随后开启搅拌40-50rpm/min、分散1600-2000rpm/min,时长为30-65min,进行刮料操作;s8、取样测试浆料的粘度与温度,浆料25-40℃时处于2000-8000mpa
·
s,随后进行最后一次搅拌操作,开启搅拌40-50rpm/min、分散1300-1700rpm/min,时长为15-25min;s9、抽真空进行脱泡处理,真空度降至-0 .09mpa~-0 .14mpa内,开启搅拌15-25rpm、分散0rpm,搅拌时长12-25min,后关闭循环水,排气直到内外气压平衡;正极片的制备:将各实施例对应的正极浆料分别涂覆在铝箔的两侧表面上,干燥后,在铝箔上形成正极材料层,得到未压正极极片,将未压正极极片制成40*100mm的大小,然后利用大野压片机进行压片,得到压片后的正极片。可以根据极片的面密度和压片后的厚度,计算极片的压实密度,结果汇总在表2。
56.电池的制备:先将各实施例对应的正极浆料制备成面密度为2.0g/dm2、压实密度为2.65g/cm3的单面正极片,将各单面正极片制作2025的扣式电池。
57.表1实施例1-5的锂离子电池正极浆料原料组分。
项目正极活性物质粉料粘结剂粉料导电剂粉料正极活性物质粉料、粘结剂粉料和导电剂粉料的质量比锂离子电池正极浆料的原料最大粒径实施例1锰酸锂、磷酸铁锂、镍钴锰三元锂,质量比为1:1:1聚偏二氟乙烯、聚偏氟乙烯,其质量比为1:3石墨烯、炭黑、碳纳米管,质量比为5:1:195.5:2:2.515实施例2锰酸锂、磷酸铁锂、镍钴锰三元锂,质量比为1:3:1聚偏二氟乙烯、聚偏氟乙烯,其质量比为1:1石墨烯、炭黑、碳纳米管,质量比为3:1:195.5:2:2.515
实施例3锰酸锂聚偏二氟乙烯共聚物炭黑95:2:314实施例4磷酸铁锂聚偏氟乙烯石墨烯95:2:35实施例5镍钴锰三元锂聚偏二氟乙烯导电炭黑95.5:2:2.515
58.对比例1本技术对比例与实施实例1不同之处在于:n-甲基吡咯烷酮在s2步骤后,一次性添加剩余n-甲基吡咯烷酮。
59.对比例2本技术对比例与实施实例1不同之处在于:n-甲基吡咯烷酮在s3步骤后,一次性添加所有n-甲基吡咯烷酮。
60.对比例3本技术对比例与实施实例1不同之处在于:一直以40-50rpm/min搅拌、以1300-1700rpm/min分散,时长为3.5-4h。
61.性能测试将实施例1-5和对比例1-3制得的匀浆进行测试。
62.锂离子电池正极浆料的细度的测试方法为:测试设备为量程100μm细度板与刮刀,。测试方法是:将各锂离子电池正极浆料滴入细度板沟槽最深处即刻度值最大部位,随后将刮刀以双手的大拇指和食指捏住刮刀,将刮刀刀口横置于刮板刻度值最大部位(在试样边缘处)使刮刀长边与刮板宽边平行,并与刮板表面垂直接触。在1~2秒钟内,将刮刀由最大刻度部位向刻度最小部位刮过,刮完样后立即(不得超过5秒钟)使视线与沟槽平面成20
°
~30
°
角,对光观察沟槽中颗粒均匀显露处,并记下相应的刻度值。进行测试,得到各锂离子电池正极浆料的细度如下表。
63.将得到的锂电池正极浆料进行性能测试,包括浆料稳定时间测试、做成正极片后的极片剥离强度测试、极片纵向电阻率测试、正极片柔韧性测试、做成电池后的电池阻抗性能测试。
64.浆料稳定时间测试方法:将浆料按照实验配方配制浆料,测试初始粘度,粘度的范围在4000
±
500mpa
·
s;将浆料放置在控制温湿度的环境中(温度:25℃
±
3℃,露点:-20℃),间隔不不同时间测试浆料粘度,当粘度变化超过25%时,视为浆料失效,浆料存在不稳定。
65.极片剥离强度测试方法:将面密度为200g/dm2、压实密度为3.6g/mm3的正极片裁成4*10cm的正极片,利用剥离力测试仪上进行测试。
66.极片纵向电阻率测试方法:将面密度为200g/dm2的正极片,利用胶带将极片从箔材上剥离,裁成直接为1.5cm的极片,在ber1300极片电阻仪上进行测试。
67.正极片柔韧性测试方法:采用三点压弯折的测试方法,为在万能试验机上开发的一种测试方法。具体为:将极片裁成4cm*15cm的形状,放在两个垫块上,两个垫块与极片垂直,采用厚度为4mm的钢片从垂直于极片的方向自上而下走,钢片连着压力传感器,由传感器记录钢片与极片之间的力与钢片压力导致极片位移之间的关系曲线,采用最大力下所对应的位移,最大力的50%的位移变化来定义极片柔韧性。
68.电池阻抗性能测试方法:将电池调至60%soc,采用电流3c,充放电时间为10s的测试方法,测试电池dcir,将dcir的数值与电池1/3c放电容量的乘积作为电池阻抗的表征。
69.具体请参阅下表,其中,a表示正极浆料的特性粘度的值,单位为g-1;d表示正极材
料的一次颗粒的dv50粒径的值,单位为μm。
70.除本发明实施实例所得样品外,其他原料皆为常见市售原料,为本领域技术人员所公知和容易获取的。
71.测试配方只为说明本发明实施例正极浆料的性能,不作为限制本发明锂电池正极浆料的用途和其他性能。
72.表2实施例和对比例的锂电池正极浆料、极片和电池性能。
编号特性粘度(mpa
·
s)细度(μm)浆料稳定时间(h)正极极片柔韧性(mm)极片压后剥离力(n/mm)极片纵向电阻率(ω
·
m)电池阻抗(mω
·
ah)实施例14182≤18723.90.618.371实施例23548≤16724.00.645.563实施例33645≤16723.80.5920.489实施例46759≤21484.00.6512.775实施例54129≤17483.80.5716.482对比例115430≤43243.50.4839.795对比例212185≤37243.60.5116.181对比例34978≤19723.80.5915.278
73.从上述表可以看出,实施例1制得的浆料用显微镜观察,如图1所示。实施例1-实施例5所制备的正极浆料,稳定时间最长可以保持72h,最短有24h,浆料稳定时间越长,说明电极浆料的抗凝胶性越好;所制备的极片柔韧性最大有4.0mm,极片柔韧性值越大,说明所制备的电极片越柔软;所制备的电极片在压后的剥离强度可达0.65n/mm,剥离强度值越大,说明电极片不容易电料,电极片中的材料颗粒粘结的越好;所制备的电极片的极片纵向电阻率最低可达5.5(ω
·
m),极片纵向电阻率越低,说明电极片的导电性能更佳;所制备的电池的电池阻抗z最低可达63mω
·
ah,电池阻抗越低,说明电池的导电性能越好。
74.还需要说明的是,本技术中提及的示例性实施例,基于一系列的步骤或者装置描述一些方法或系统。但是,本技术不局限于上述步骤的顺序,也就是说,可以按照实施例中提及的顺序执行步骤,也可以不同于实施例中的顺序,或者若干步骤同时执行。
75.以上所述,仅为本技术的具体实施方式,所属领域的技术人员可以清楚地了解到,为了描述的方便和简洁,上述描述的系统、模块和单元的具体工作过程,可以参考前述方法实施例中的对应过程,在此不再赘述。应理解,本技术的保护范围并不局限于此,任何熟悉本技术领域的技术人员在本技术揭露的技术范围内,可轻易想到各种等效的修改或替换,这些修改或替换都应涵盖在本技术的保护范围之内。