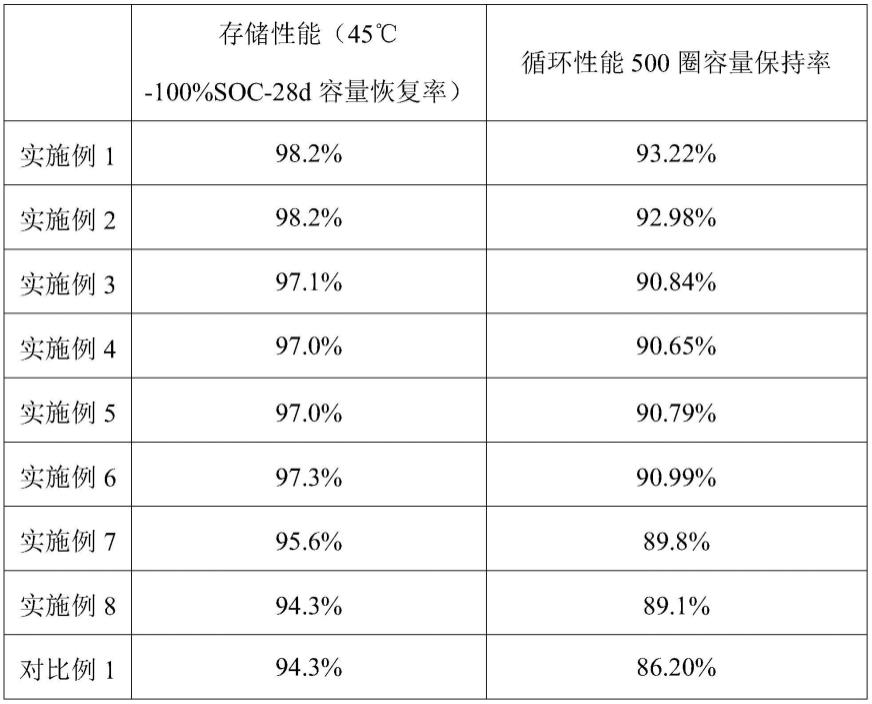
1.本发明属于正极材料制备技术领域,涉及一种复合高铁酸钾正极材料及其制备方法和应用。
背景技术:2.高铁酸钾(k2feo4)是铁的﹢6价态的化合物,由于其3电子的还原特性,可以进行多电子还原,因此可提供较高的阴极容量。目前k2feo4的合成主要采用化学合成方法,利用合成出的k2feo4与zn电极配对组装成电池,结果显示该电池具有较好的存储与循环性能。
3.研究发现,使用k2feo4包覆二氧化钛的复合材料(k2feo4/tio2)作为正极材料可进一步改善单纯k2feo4作为正极材料时电芯的存储与循环性能,但k2feo4/tio2材料的制作成本昂贵。
4.cn105047876a公开了一种高铁电池复合正极材料的制备方法,其通过在高铁酸钾表面包覆一层导电聚合物,导电聚合物能够阻碍高铁酸钾与电解液的接触,同时增强电极材料的导电性,降低电极中电荷转移电阻,而提高了高铁酸盐正极材料的利用率。
5.cn103259012a公开了一种三维导电高铁电池k2feo4/c复合正极材料的制备方法。其通过原位共沉淀法,在高铁酸钾结晶过程中,加入表面活性剂及纳米碳材料,使纳米碳材料嵌入高铁酸钾晶体中,形成三维导电的复合材料。
6.上述方案所述高铁酸钾正极材料存在有循环性能差的问题,严重限制了其在实际中的应用。
技术实现要素:7.本发明的目的在于提供一种复合高铁酸钾正极材料及其制备方法和应用,本发明所述复合高铁酸钾正极材料具有存储性能优良、循环寿命长的优势,且制备过程简单,制备成本低廉。
8.为达到此发明目的,本发明采用以下技术方案:
9.第一方面,本发明提供了一种复合高铁酸钾正极材料的制备方法,所述制备方法包括以下步骤:
10.(1)将硅源、高铁酸钾和有机溶剂混合,搅拌后过滤得到预混料;
11.(2)对步骤(1)得到的预混料进行烧结处理得到所述复合高铁酸钾正极材料。
12.本发明采用特定的硅源作为包覆源,再搭配适用其包覆的特定有机液相混合法和鼓氧烧结法,可使硅源与高铁酸钾充分预混,还能够保证高铁酸钾在混合和高温烧结过程中均不会变质。
13.优选地,步骤(1)所述硅源包括硅酸四乙酯和/或硅酸四丙酯。
14.优选地,所述有机溶剂包括醇类溶剂。
15.优选地,所述醇类溶剂包括甲醇、乙醇或异丙醇中的任意一种或至少两种的组合。
16.优选地,步骤(1)所述高铁酸钾的中值粒径d50为10~15μm,例如:10μm、11μm、12μ
m、13μm、14μm或15μm等。
17.优选地,所述硅源和高铁酸钾的质量比为(1.5~2):5,例如:1.5:5、1.6:5、1.7:5、1.8:5、1.9:5或2:5等。
18.优选地,所述高铁酸钾和有机溶剂的质量比为1:(4~10),例如:1:4、1:5、61:、1:7、1:8、1:9或1:10等。
19.优选地,步骤(1)所述搅拌的气氛为惰性气氛。
20.优选地,所述惰性气氛包括氩气、氦气、氖气、氪气或氡气中的任意一种或至少两种的组合。
21.优选地,所述搅拌的时间为4~8h,例如:4h、5h、6h、7h或8h等。
22.优选地,所述搅拌的转速为200~500rpm,例如:200rpm、250rpm、300rpm、400rpm或500rpm等。
23.优选地,所述过滤后取滤饼进行烘干后,得到预混料。
24.优选地,步骤(2)所述烧结处理的气氛包括氧气和/或臭氧。
25.优选地,所述烧结处理的温度为700~900℃,例如:700℃、750℃、800℃、850℃或900℃等。
26.优选地,所述烧结处理的时间为4~6h,例如:4h、4.5h、5h、5.5h或6h等。
27.优选地,所述烧结处理的升温速度为5~15℃/min,例如:5℃/min、8℃/min、10℃/min、12℃/min或15℃/min等。
28.优选地,步骤(2)所述烧结处理后进行清洗和烘干处理。
29.优选地,所述清洗的清洗液包括甲醇、乙醇或异丙醇中的任意一种或至少两种的组合。
30.第二方面,本发明提供了一种复合高铁酸钾正极材料,所述复合高铁酸钾正极材料通过如第一方面所述方法制得,所述复合高铁酸钾正极材料包括高铁酸钾内核和设置在所述高铁酸钾内核表面的硅氧化物包覆层。
31.本发明所述的复合高铁酸钾正极材料的存储性能和循环性能大大提高,作为正极材料时的性能远优于常规正极材料。
32.优选地,所述硅氧化物包覆层的厚度为10~50nm,例如:10nm、20nm、30nm、40nm或50nm等。
33.第三方面,本发明提供了一种正极极片,所述正极极片包含如第二方面所述的复合高铁酸钾正极材料。
34.第四方面,本发明提供了一种电池,所述电池包含如第三方面所述的正极极片。
35.相对于现有技术,本发明具有以下有益效果:
36.(1)本发明所述制备方法采用特定的硅源作为包覆源,再搭配适用其包覆的特定有机溶剂,通过液相混合法和鼓氧烧结法,可使硅源与高铁酸钾充分预混,还能够保证高铁酸钾在混合和高温烧结过程中均不会变质,制得正极材料的存储性能和循环性能大大提高。
37.(2)本发明所述复合高铁酸钾正极材料存储28d后容量恢复率可达98.2%以上,45℃,1c循环性能500圈容量保持率可达92.98%以上。
具体实施方式
38.下面通过具体实施方式来进一步说明本发明的技术方案。本领域技术人员应该明了,所述实施例仅仅是帮助理解本发明,不应视为对本发明的具体限制。
39.实施例1
40.本实施例提供了一种复合高铁酸钾正极材料,所述复合高铁酸钾正极材料的制备方法如下:
41.(1)在25℃下,将1.8mg的硅酸四乙酯、5mg的k2feo4、40ml乙醇于200ml烧杯中混合,在转速300rpm的条件下搅拌5h,搅拌结束过滤后取滤饼进行烘干后,得到预混料;
42.(2)将步骤(1)中制备的预混料在氧气/臭氧与氦气混合气氛中以10℃/min升温速率升温至800℃,烧结5h,即得到所述复合高铁酸钾正极材料。
43.实施例2
44.本实施例提供了一种复合高铁酸钾正极材料,所述复合高铁酸钾正极材料的制备方法如下:
45.(1)在25℃下,将1.6mg的硅酸四丙酯、5mg的k2feo4、45ml乙醇于200ml烧杯中混合,在转速320rpm的条件下搅拌5h,搅拌结束过滤后取滤饼进行烘干后,得到预混料;
46.(2)将步骤(1)中制备的预混料在氧气/臭氧与氦气混合气氛中以10℃/min升温速率升温至850℃,烧结5h,即得到所述复合高铁酸钾正极材料。
47.实施例3
48.本实施例提供了一种复合高铁酸钾正极材料,所述复合高铁酸钾正极材料的制备方法如下:
49.(1)在25℃下,将1.2mg的硅酸四乙酯、5mg的k2feo4、40ml乙醇于200ml烧杯中混合,在转速300rpm的条件下搅拌5h,搅拌结束过滤后取滤饼进行烘干后,得到预混料;
50.(2)将步骤(1)中制备的预混料在氧气/臭氧与氦气混合气氛中以10℃/min升温速率升温至800℃,烧结5h,即得到所述复合高铁酸钾正极材料。
51.实施例4
52.本实施例提供了一种复合高铁酸钾正极材料,所述复合高铁酸钾正极材料的制备方法如下:
53.(1)在25℃下,将2.2mg的硅酸四乙酯、5mg的k2feo4、40ml乙醇于200ml烧杯中混合,在转速300rpm的条件下搅拌5h,搅拌结束过滤后取滤饼进行烘干后,得到预混料;
54.(2)将步骤(1)中制备的预混料在氧气/臭氧与氦气混合气氛中以10℃/min升温速率升温至800℃,烧结5h,即得到所述复合高铁酸钾正极材料。
55.实施例5
56.本实施例提供了一种复合高铁酸钾正极材料,所述复合高铁酸钾正极材料的制备方法如下:
57.(1)在25℃下,将1.8mg的硅酸四乙酯、5mg的k2feo4、40ml乙醇于200ml烧杯中混合,在转速300rpm的条件下搅拌5h,搅拌结束过滤后取滤饼进行烘干后,得到预混料;
58.(2)将步骤(1)中制备的预混料在氧气/臭氧与惰性气体氦气混合气氛中以10℃/min升温速率升温至600℃,烧结5h,即得到所述复合高铁酸钾正极材料。
59.实施例6
60.本实施例提供了一种复合高铁酸钾正极材料,所述复合高铁酸钾正极材料的制备方法如下:
61.(1)在25℃下,将1.8mg的硅酸四乙酯、5mg的k2feo4、40ml乙醇于200ml烧杯中混合,在转速300rpm的条件下搅拌5h,搅拌结束过滤后取滤饼进行烘干后,得到预混料;
62.(2)将步骤(1)中制备的预混料在氧气/臭氧与氦气混合气氛中以10℃/min升温速率升温至1000℃,烧结5h,即得到所述复合高铁酸钾正极材料。
63.实施例7
64.本实施例与实施例1区别仅在于,使用二氧化硅作为硅源,其他条件与参数与实施例1完全相同。
65.制备方法如下:
66.(1)在25℃下,将1.8mg的二氧化硅、5mg的k2feo4、40ml乙醇于200ml烧杯中混合,在转速300rpm的条件下搅拌5h,搅拌结束过滤后取滤饼进行烘干后,得到预混料;
67.(2)将步骤(1)中制备的预混料在氧气/臭氧与氦气混合气氛中以10℃/min升温速率升温至800℃,烧结5h,即得到所述复合高铁酸钾正极材料。
68.实施例8
69.本实施例与实施例1区别仅在于,使用甲苯作为有机溶剂,其他条件与参数与实施例1完全相同。
70.制备方法如下:
71.(1)在25℃下,将1.8mg的硅酸四乙酯、5mg的k2feo4、40ml甲苯于200ml烧杯中混合,在转速300rpm的条件下搅拌5h,搅拌结束过滤后取滤饼进行烘干后,得到预混料;
72.(2)将步骤(1)中制备的预混料在氧气/臭氧与氦气混合气氛中以10℃/min升温速率升温至800℃,烧结5h,即得到所述复合高铁酸钾正极材料。
73.对比例1
74.本对比例与实施例1区别仅在于,直接使用高铁酸钾作为正极材料。
75.性能测试:
76.测试实施例1-6和对比例所述复合高铁酸钾正极材料的存储性能和循环性能:
①
45℃-100%soc存储28d后容量恢复,
②
45℃-1c循环性能,测试结果如表1所示:
77.表1
[0078][0079]
由表1可以看出,由实施例1-2可得,本发明所述复合高铁酸钾正极材料存储28d后容量恢复率可达98.2%以上,45℃,1c循环性能500圈容量保持率可达92.98%以上。
[0080]
由实施例1和实施例3-4对比可得,本发明所述复合高铁酸钾正极材料的制备过程中,硅源和高铁酸钾的质量比会影响制得复合高铁酸钾正极材料的性能,将硅源和k2feo4的质量比控制在1.5~2:5,制得正极材料的性能较好,若硅源添加量过大,存储以及循环性能变差,若硅源的添加量过小,循环以及存储性能变差。
[0081]
由实施例1和实施例5-6对比可得,本发明所述复合高铁酸钾正极材料的制备过程中,步骤(2)烧结处理的温度会影响制得复合高铁酸钾正极材料的性能,将烧结处理的温度控制在700~900℃,制得正极材料的性能较好,若烧结处理的温度过高,存储以及循环性能变差,若烧结处理的温度过低,存储以及循环性能变差。
[0082]
由实施例1和实施例7-8对比可得,本发明采用特定的硅源作为包覆源,再搭配适用其包覆的特定有机溶剂,通过液相混合法和鼓氧烧结法,可使硅源与高铁酸钾充分预混,还能够保证高铁酸钾在混合和高温烧结过程中均不会变质,制得正极材料的存储性能和循环性能大大提高。若选用的硅源和有机溶剂不对,循环及存储性能将大幅降低。
[0083]
由实施例1和对比例1对比可得,本发明在高铁酸钾表面设置包覆层,所得的复合材料的存储性能和循环性能大大提高,作为正极材料时的性能远优于常规正极材料。
[0084]
由实施例1和对比例2对比可得,本发明预先将高铁酸钾、硅源和有机溶剂混合后制成预混料,可使硅源与高铁酸钾充分预混,还能够保证高铁酸钾在混合和高温烧结过程中均不会变质。
[0085]
申请人声明,以上所述仅为本发明的具体实施方式,但本发明的保护范围并不局
限于此,所属技术领域的技术人员应该明了,任何属于本技术领域的技术人员在本发明揭露的技术范围内,可轻易想到的变化或替换,均落在本发明的保护范围和公开范围之内。