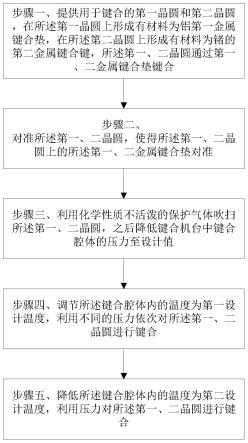
1.本发明涉及半导体技术领域,特别是涉及一种改善铝锗键合程度的方法。
背景技术:2.共晶键合近年来被广泛应用于加速度计、陀螺仪等mems(微机电系统)器件开发及应用中,共晶键合采用金属层作为中间键合介质层,利用了某些共晶合金熔融温度低的特点,通过加热熔融使两种金属紧密结合实现键合。
3.铝锗作为常用的键合金属,在共晶键合过程中,由于键合材料的不同,键合过程中晶片之间存在着热失配及晶格失配等问题,界面处易形成错位和孔洞缺陷,孔洞的存在减少了实际接触界面,严重时能破坏铝锗共晶键合形成密闭腔体的气密性,造成器件功能性及可靠性降低。
4.为解决上述问题,需要提出一种新型的改善铝锗键合程度的方法。
技术实现要素:5.鉴于以上所述现有技术的缺点,本发明的目的在于提供一种改善铝锗键合程度的方法,用于解决现有技术中铝锗作为常用的键合金属,在共晶键合过程中,由于键合材料的不同,键合过程中晶片之间存在着热失配及晶格失配等问题,界面处易形成错位和孔洞缺陷,孔洞的存在减少了实际接触界面,严重时能破坏铝锗共晶键合形成密闭腔体的气密性,造成器件功能性及可靠性降低的问题。
6.为实现上述目的及其他相关目的,本发明提供一种改善铝锗键合程度的方法包括:
7.步骤一、提供用于键合的第一晶圆和第二晶圆,在所述第一晶圆上形成有材料为铝第一金属键合垫,在所述第二晶圆上形成有材料为锗的第二金属键合键,所述第一、二晶圆通过第一、二金属键合垫键合;
8.步骤二、对准所述第一、二晶圆,使得所述第一、二晶圆上的所述第一、二金属键合垫对准;
9.步骤三、利用化学性质不活泼的保护气体吹扫所述第一、二晶圆,之后降低键合机台中键合腔体的压力至设计值;
10.步骤四、调节所述键合腔体内的温度为第一设计温度,利用不同的压力依次对所述第一、二晶圆进行键合;
11.步骤五、降低所述键合腔体内的温度为第二设计温度,利用压力对所述第一、二晶圆进行键合。
12.优选地,步骤一中的所述第一、二晶圆的材料均为硅。
13.优选地,步骤一中所述第一、二金属键合键的形成方法包括:在所述第一、二晶圆上分别形成第一、二介质层;分别刻蚀部分厚度的所述第一、二介质层形成第一、二凹槽;分别在所述第一、二凹槽内形成铝材料层与锗材料层。
14.优选地,步骤一中的所述第一金属键合垫超出所述第一晶圆表面的厚度为0.5至1纳米。
15.优选地,步骤一中的所述第二金属键合垫超出所述第二晶圆表面的厚度为0.5至1纳米。
16.优选地,步骤二中的所述对准所述第一、二晶圆时,还包括在所述第一、二晶圆间插入间隔层。
17.优选地,步骤二中的所述间隔层的厚度为100至200微米。
18.优选地,步骤四中在利用压力对所述第一、二晶圆进行键合之前,还包括移除所述第一、二晶圆间的所述间隔层。
19.优选地,步骤三中所述利用惰性气体吹扫所述第一、二晶圆以及所述降低键合机台中键合腔体的压力至设计值的步骤至少交替进行2轮。
20.优选地,步骤三中的所述保护气体为氮气或惰性气体。
21.优选地,步骤三中所述设计值小于等于0.001mbar。
22.优选地,步骤三中所述键合腔体中的温度为200至250摄氏度。
23.优选地,步骤四中升高所述键合腔体内的温度为所述第一设计温度,所述第一设计温度为高于铝锗共晶温度5至10摄氏度;其中,温度在升高至所述锗硅共晶温度前,键合时的压力为10至20kn;温度在升高至所述锗硅共晶温度后,键合时的压力为30至40kn。
24.优选地,步骤五中所述第二设计温度为200至250摄氏度。
25.优选地,步骤五中所述第一、二晶圆键合时的压力为30至40kn。
26.如上所述,本发明的改善铝锗键合程度的方法,具有以下有益效果:
27.本发明在键合过程中分段施加压力,在晶片键合前对晶片预先施压,键合前预先施压可减少初始键合过程中的应力释放,减少错位的产生;降温过程步骤中维持一定的压力控制,可形成更为致密的铝锗合金化合物结构,减少孔洞的形成。
附图说明
28.图1显示为本发明的工艺流程示意图。
具体实施方式
29.以下通过特定的具体实例说明本发明的实施方式,本领域技术人员可由本说明书所揭露的内容轻易地了解本发明的其他优点与功效。本发明还可以通过另外不同的具体实施方式加以实施或应用,本说明书中的各项细节也可以基于不同观点与应用,在没有背离本发明的精神下进行各种修饰或改变。
30.请参阅图1,本发明提供一种改善铝锗键合程度的方法包括:
31.步骤一、提供用于键合的第一晶圆和第二晶圆,在第一晶圆上形成有材料为铝第一金属键合垫,在第二晶圆上形成有材料为锗的第二金属键合键,第一、二晶圆通过第一、二金属键合垫键合;
32.在本发明的实施例中,步骤一中的第一、二晶圆的材料均为硅。
33.在本发明的实施例中,步骤一中第一、二金属键合键的形成方法包括:在第一、二晶圆上分别形成第一、二介质层,第一、二介质层的材料包括氧化硅、氮氧化硅和碳氧化硅
中的一种或多种,本实施例中,介质层的材料为氧化硅,并且覆盖完全第一、二晶圆的表面;在第一、二晶圆的表面上分别形成光刻胶层,之后通过光刻打开光刻胶层,使得第一、二晶圆上的介质层裸露,之后分别刻蚀部分厚度的第一、二介质层形成第一、二凹槽;分别在第一、二凹槽内形成铝材料层与锗材料层;之后可通过去除第一、二晶圆上的介质层来形成具有特定图形的第一、二金属键合键,第一、二金属键合键的形状通常为矩形,也可为其他类型的形状,此处不做具体限定。
34.在本发明的实施例中,步骤一中的所述第一金属键合垫超出所述第一晶圆表面的厚度为0.5至1纳米。
35.在本发明的实施例中,步骤一中的所述第二金属键合垫超出所述第二晶圆表面的厚度为0.5至1纳米。
36.步骤二、对准第一、二晶圆,使得第一、二晶圆上的第一、二金属键合垫对准;
37.在本发明的实施例中,步骤二中的对准第一、二晶圆时,还包括在第一、二晶圆间插入间隔层,间隔层的材料通常为金属合金,例如镍合金。
38.在本发明的实施例中,步骤二中的间隔层的厚度为100至200微米,具体地,可为100微米、150微米或200微米,间隔层用于在第一、二晶圆间形成阻隔,此处的厚度不作具体限定。
39.步骤三、利用化学性质不活泼的保护气体吹扫第一、二晶圆,之后降低键合机台中键合腔体的压力至设计值;
40.在本发明的实施例中,步骤三中利用惰性气体吹扫第一、二晶圆以及降低键合机台中键合腔体的压力至设计值的步骤至少交替进行2轮。
41.在本发明的实施例中,步骤三中的保护气体为氮气或惰性气体。
42.在本发明的实施例中,步骤三中设计值小于等于0.001mbar。
43.在本发明的实施例中,步骤三中键合腔体中的温度为200至250摄氏度。
44.步骤四、调节键合腔体内的温度为第一设计温度,利用不同的压力依次对第一、二晶圆进行键合,即在晶片键合前对晶片预先施压,键合前预先施压可减少初始键合过程中的应力释放,减少错位的产生;降温过程步骤中维持一定的压力控制,可形成更为致密的al ge合金化合物结构,减少孔洞的形成;
45.在本发明的实施例中,步骤四中在利用压力对第一、二晶圆进行键合之前,还包括移除第一、二晶圆间的间隔层。
46.在本发明的实施例中,步骤四中升高键合腔体内的温度为第一设计温度,第一设计温度为高于铝锗共晶温度5至10摄氏度,即第一设计温度为400至420摄氏度;其中,温度在升高至锗硅共晶温度前,键合时的压力为10至20kn(千牛),例如10kn、15kn、20kn;温度在升高至锗硅共晶温度后,键合时的压力为30至40kn,例如30kn、35kn、40kn。
47.步骤五、降低键合腔体内的温度为第二设计温度,通常可在键合腔室中通入氮气进行降温,利用压力对第一、二晶圆进行键合。
48.在本发明的实施例中,步骤五中第二设计温度为200至250摄氏度,例如200摄氏度、210摄氏度、2200摄氏度、230摄氏度、240摄氏度、250摄氏度。
49.在本发明的实施例中,步骤五中第一、二晶圆键合时的压力为30至40kn,例如30kn、35kn、40kn。
50.需要说明的是,本实施例中所提供的图示仅以示意方式说明本发明的基本构想,遂图式中仅显示与本发明中有关的组件而非按照实际实施时的组件数目、形状及尺寸绘制,其实际实施时各组件的型态、数量及比例可为一种随意的改变,且其组件布局型态也可能更为复杂。
51.综上所述,本发明在键合过程中分段施加压力,在晶片键合前对晶片预先施压,键合前预先施压可减少初始键合过程中的应力释放,减少错位的产生;降温过程步骤中维持一定的压力控制,可形成更为致密的铝锗合金化合物结构,减少孔洞的形成。
52.所以,本发明有效克服了现有技术中的种种缺点而具高度产业利用价值。
53.上述实施例仅例示性说明本发明的原理及其功效,而非用于限制本发明。任何熟悉此技术的人士皆可在不违背本发明的精神及范畴下,对上述实施例进行修饰或改变。因此,举凡所属技术领域中具有通常知识者在未脱离本发明所揭示的精神与技术思想下所完成的一切等效修饰或改变,仍应由本发明的权利要求所涵盖。