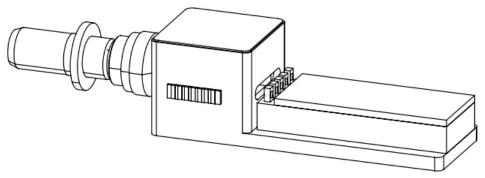
1.本发明涉及光通信领域,具体涉及一种高速率调制器封装结构及封装方法。
背景技术:2.近年来,得益于我国重点发展人工智能、远程医疗以及工业互联网等新兴产业,云计算和数据中心产业不断发展,同时,大力推动5g网络建设,这对高速率传输光模块产生了极大的需求,包括200g、400g,以及在研的800g、1.6t光模块。
3.现阶段传输速率在400g以下的光模块发射端有三种方案:eml(electro-absorption laser,电吸收调制激光器)方案、soi modulator chip(silicon on insulator modulator chip,硅光调制器芯片)方案和lnoi(lithium niobate on insulator,薄膜铌酸锂调制器)方案,对于非气密光模块,调制信号可通过金丝键合由pcba(printed circuit board assembly,印刷电路板组件)传输到eml芯片或调制器芯片上;对于气密模块,调制器信号需从pcba传输到陶瓷基板,再到eml芯片或调制器芯片上,pcba与陶瓷基板、陶瓷基板与eml芯片(或调制器芯片)间通过金丝键合连接。
4.如图15-17所示,现有方案中,调制器芯片上的射频接口,即位于芯片右侧的金属图形,通过金丝键合方式与陶瓷17一侧连接,陶瓷17另一侧与pcba16连接,连接方式可以为金丝键合/柔板焊接。可见,调制器芯片与pcba16间需要两次连接。
5.相比于在pcba和陶瓷基板上传输,射频信号经过金丝传输会有较大的损耗,导致信号失真,故为使光模块能够支持更高的传输速率,需要尽可能的减少射频信号通过金丝键合传输的次数。
技术实现要素:6.发明目的:本发明的目的在于提供一种能够减少射频信号的传输损耗,提高光模块的信号传输质量及传输速率的高速率调制器封装结构及封装方法。
7.技术方案:本发明的高速率调制器封装结构包括半气密的管壳壳体,所述管壳壳体一端向上延伸形成腔室,腔室上方设置管壳盖板,形成气密空间,气密空间内底面安装第一陶瓷基板;所述管壳壳体另一端表面安装第二陶瓷基板;所述第一陶瓷基板表面纵向排布多个激光器载体,第二陶瓷基板表面贴近端面安装调制器芯片,第二陶瓷基板表面靠近第一陶瓷基板的一端为预留空间,用以安装透镜;所述激光器载体靠近调制器芯片一侧的第一陶瓷基板上布置多个第一准直透镜,激光器载体与第一准直透镜一一对应;所述腔室的管壳壁一侧开设第一通孔,用以安装光窗支架,第一光窗支架外侧连接适配器;所述管壳壁另一侧设置通光孔,第二陶瓷基板上的透镜与通光孔对应;所述第一光窗支架内侧、通光孔内侧均用透光装置封装。
8.所述透光装置采用蓝宝石,第一光窗支架内置蓝宝石,通光孔内侧设置卡槽,将蓝宝石放置在卡槽中,可以在保证管壳气密性的同时支持信号光通过。
9.所述激光器载体出光口、调制器芯片入光口、准直透镜光轴及第二陶瓷基板上的
透镜光轴处于同一高度,有利于降低耦合工艺难度并提高耦合效率。
10.所述管壳壁正面开设第二通孔,用以安装陶瓷板,陶瓷板表面及侧面均设置金属图形,金属图形与管壳壳体的气密空间内部的多个激光器载体连接,起到电气导通作用。
11.所述准直透镜外侧的第一陶瓷基板表面设置隔离器,隔离器与第一准直透镜相对应,可以防止杂散光影响激光器工作。
12.本发明还包括一种高速率调制器封装方法,包括以下步骤:
13.s1:将多个激光器芯片通过共晶固定在多个第三陶瓷基板上,形成多个激光器载体;将多个激光器载体通过银胶贴片固定在第一陶瓷基板表面,并呈纵向排布;在激光器载体靠近调制器芯片一侧的第一陶瓷基板上布置多个准直透镜,并使激光器载体与准直透镜一一对应;
14.s2:将第二陶瓷基板通过银胶贴片固定在管壳壳体表面,之后将调制器芯片通过银胶贴片固定在第二陶瓷基板表面,调制器芯片紧贴第二陶瓷基板端面安装,预留的端面安装一个第二准直透镜,或多个聚焦透镜和一个第二准直透镜;
15.s3:为第一通道激光器加电,进行耦合;其中,激光器芯片通过单透镜或双透镜方式耦合至调制器芯片;
16.s4:任选一通道或多通道激光器加电,调节第二陶瓷基板上的透镜位置和适配器位置,进行调制器芯片到适配器中光纤插芯的耦合;
17.s5:用管壳盖板对管壳壳体的腔室进行封盖。
18.步骤s2中,所述调制器芯片贴装过程中,需满足以下要求:z方向激光器载体的出光口与调制器芯片的入光口对齐,y方向激光器载体到调制器芯片的距离由仿真软件得出,x方向激光器载体的出光口与制器芯片的入光口等高,提高耦合效率。
19.本发明的工作原理如下:多通道激光器同时发光,光通过单/双透镜方案耦合到调制器芯片中,通过调制器芯片mux(multiplexing,复用)功能,多通道光信号合为1通道,之后由调制器芯片发出,通过第二陶瓷基板上的准直透镜耦合到适配器的光纤插芯。
20.有益效果:本发明的技术方案与现有技术相比,其有益效果在于:(1)采用半气密管壳,调制器芯片放置在管壳非气密部分,芯片上的射频接口直接与外部结构pcba通过金丝键合连接,相比于传统气密管壳射频接口先连接管壳陶瓷件,再连接pcba射频接口的结构,能够极大降低高频信号损耗,提高传输速率;(2)激光器载体放置在管壳的气密内部,此器件兼容了传统非气密器件高传输速率及气密器件高可靠性的优点。此外,该器件通过混合集成和调制器芯片mux功能,提高了器件集成度。
附图说明
21.图1为本发明的结构示意图;
22.图2为未安装管壳盖板状态下的结构示意图;
23.图3为管壳壳体的结构示意图;
24.图4为管壳壳体安装光窗支架状态下的主视图;
25.图5为管壳壳体安装光窗支架状态下的俯视图;
26.图6为管壳壳体安装光窗支架状态下的左视图;
27.图7为当激光器载体按1通道+3通道排布情况下采用双透镜耦合方式时的俯视图;
28.图8为当激光器载体按1通道+3通道排布情况下采用单透镜耦合方式时的俯视图;
29.图9为当激光器载体按2通道+2通道排布情况下采用双透镜耦合方式时的俯视图;
30.图10为当激光器载体按2通道+2通道排布情况下采用单透镜耦合方式时的俯视图;
31.图11为当激光器载体按3通道+1通道排布情况下采用双透镜耦合方式时的俯视图;
32.图12为当激光器载体按3通道+1通道排布情况下采用单透镜耦合方式时的俯视图;
33.图13为本发明的高速率调制器封装结构在使用状态的示意图;
34.图14为图13中a处的放大示意图;
35.图15为现有的调制器封装结构在使用状态的示意图;
36.图16为图15中b处的放大示意图;
37.图17为图15中c处的放大示意图。
具体实施方式
38.下面结合具体实施方式和说明书附图对本发明的技术方案进行详细介绍。
39.如图1所示,本发明的高速率调制器封装结构包括管壳壳体5,管壳壳体5设置成半气密结构,具体为:管壳壳体5包括管壳壁51和可伐管壳基板52,管壳壳体5一端向上延伸形成腔室,腔室的四周为管壳壁51,腔室上方设置管壳盖板2,形成气密空间,气密空间内充入氮气。气密空间内的底面安装第一陶瓷基板8,第一陶瓷基板8为无图形的陶瓷基板;管壳壳体5另一端为可伐管壳基板52,可伐管壳基板52表面安装第二陶瓷基板6,第二陶瓷基板6为无图形的陶瓷基板。
40.第一陶瓷基板8表面纵向排布多个激光器载体,激光器载体由激光器芯片10通过共晶固定在第三陶瓷基板9上而形成的,第三陶瓷基板9表面设有金层及金锡焊料。本实施例中,激光器载体的数量为4个,所以能够产生4个光道。第二陶瓷基板6表面贴近端面安装调制器芯片15,调制器芯片15采用的是薄膜铌酸锂调制器芯片,内置单模光纤插芯。第二陶瓷基板6表面靠近第一陶瓷基板8的一端为预留空间,根据单耦合方式或者双耦合方式来确定所要安装的透镜的种类和数量,这里的透镜包括聚焦透镜13和第二准直透镜14;激光器载体靠近调制器芯片15一侧的第一陶瓷基板8上布置多个第一准直透镜11,激光器载体与第一准直透镜11一一对应,保证激光器载体产生的光能够穿过第一准直透镜11。为了防止杂散光影响激光器载体工作,在第一准直透镜11外侧的第一陶瓷基板8表面设置隔离器12,隔离器12与第一准直透镜11相对应。本实施例中,激光器载体出光口、调制器芯片15入光口、第一准直透镜11光轴及第二陶瓷基板6上的透镜光轴均处于同一高度,有利于降低耦合工艺难度并提高耦合效率。
41.腔室的管壳壁51一侧开设第一通孔,在第一通孔上安装光窗支架1,光窗支架1外侧连接适配器6;管壳壁51另一侧设置通光孔3,第二陶瓷基板6上的透镜与通光孔3对应,确保光线穿过通光孔3之后能够通过第二陶瓷基板6上的透镜中心;第一光窗支架1内侧、通光孔3内侧均用透光装置封装,实现支持信号光通过的同时保证气密空间的密封性能。本实施例中,通光孔3呈水平设置的椭圆形结构,透光装置采用蓝宝石,第一光窗支架1内置蓝宝
石,通光孔3内侧设置卡槽,将蓝宝石放置在卡槽中。透光装置不限于蓝宝石,只要能够同时满足支持信号光通过和保证气密性即可。管壳壁51正面开设第二通孔,用以安装陶瓷板4,陶瓷板4表面及侧面均设置金属图形,金属图形与管壳壳体5的气密空间内部零件连接,内部零件指激光器载体。如果在激光器载体下端添加tec,金属图形还需要与tec进行连接,此种情况下,内部零件指激光器载体和tec。
42.本发明还包括一种高速率调制器封装方法,具体包括以下步骤:
43.s1:将多个激光器芯片10通过共晶固定在多个第三陶瓷基板9上,形成多个激光器载体;将多个激光器载体通过银胶贴片固定在第一陶瓷基板8表面,并呈纵向排布;本实施例中,将四个激光器芯片10分别固定在四个第三陶瓷基板9上,从而形成了四个激光器载体。第一陶瓷基板8通过银胶贴片固定在管壳壳体5的气密空间底面。在激光器载体靠近调制器芯片15一侧的第一陶瓷基板8上布置多个准直透镜11,并使激光器载体与准直透镜11一一对应;本实施例中,准直透镜11的数量也为四个,与四个激光器载体一一对应。
44.s2:将第二陶瓷基板6通过银胶贴片固定在管壳壳体5中的可伐管壳基板52表面,之后将调制器芯片15通过银胶贴片固定在第二陶瓷基板6表面,调制器芯片15紧贴第二陶瓷基板6端面安装,预留的端面安装一个第二准直透镜14,或多个聚焦透镜13和一个第二准直透镜14;
45.调制器芯片15贴装过程中,需满足以下要求:如图7所示,z方向激光器载体的出光口与调制器芯片15的入光口对齐,y方向激光器载体到调制器芯片15的距离由仿真软件得出,x方向激光器载体的出光口与制器芯片15的入光口等高。第一陶瓷基板8、第二陶瓷基板6、第三陶瓷基板9的高度根据实际需求调整。
46.隔离器12通过紫外固化胶贴装在第一陶瓷基板8上,贴装时,需要确保在z方向上,激光器载体的出光通过隔离器12中心,可通过预先调整隔离器12高度实现,y方向贴装位置由仿真得出;
47.s3:为第一通道激光器加电,进行耦合;其中,激光器芯片10通过单透镜或双透镜方式耦合至调制器芯片15;两种耦合方式的最终目的均为尽可能提高光学系统1的耦合效率,不同的激光器芯片和调制器芯片会使用不同的耦合方式,通过对系统仿真模拟得出,选出耦合效率最高的方式制作产品。对于双透镜耦合方案(如图7、9、11所示),通过调节第二准直透镜14和聚焦透镜13位置提高耦合效率;对于单透镜耦合(如图8、10、12所示),通过调节第二准直透镜14位置提高耦合效率。其他三通道均参考第一通道方法进行耦合;上述6种可能耦合方案中,对应了三种激光器分布结构,即三个适配器的位置,最终方案的选择取决于光模块封装形式及rosa结构。
48.s4:任选一通道或多通道的激光器加电,调节第二陶瓷基板6上的透镜位置和适配器6位置,进行调制器芯片15到适配器6中光纤插芯的耦合,提高耦合效率;
49.s5:用管壳盖板2对管壳壳体5的腔室进行封盖。
50.另外,可根据实际产品需求,在激光器载体下端添加tec(thermo electric cooler,半导体制冷器),并在第一陶瓷基板8上贴装热敏电阻,用于监控激光器芯片10的工作温度。
51.本方案中,四个通道激光器同时发光,光透过单/双透镜耦合到调制器芯片15中,通过调制器芯片mux(multiplexing,复用)功能,4通道光信号合为1通道,由调制器芯片15
发出,通过第二准直透镜14耦合到适配器6的光纤插芯。其中,为防止杂散光影响激光器载体工作,在激光器载体和调制器芯片15间设置隔离器12。
52.如图13和图14所示,本方案采用半气密tosa,其调制器芯片15上的射频接口可直接与pcba射频接口通过金丝键合连接,芯片上的射频接口,即位于芯片右侧的金属图形,通过金丝键合方式与外接的pcba16连接。可见,调制器芯片15与pcba16间只需要一次连接。
53.相比于传统气密管壳射频接口先连接管壳陶瓷件,再连接pcba射频接口的结构,本发明提出的封装结构能够极大降低高频信号损耗,提高传输速率。采用本方案的结构封装得到的调制器调制速率最高可达112gbaud,且能够兼容光模块qsfd-dd(quad small form factor pluggable-double density,小型可插拔-双密度)封装。