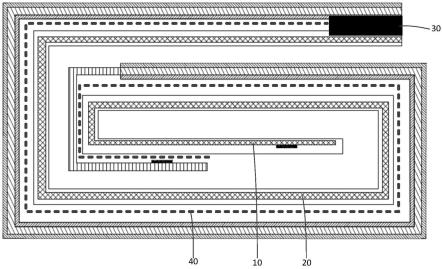
1.本技术涉及电池技术领域,具体涉及一种电芯和电池。
背景技术:2.近年来,随着锂离子电池的能量密度的提高,使得锂离子电池的安全性问题愈发严峻,特别是高温热失控导致的电池起火爆炸的问题。
3.一般来说,电池的热失控过程被划分为三个阶段,依次为自生热阶段(电池温度为50℃-100℃)、热失控阶段(100℃-850℃)以及终止阶段(850℃-常温),其中,热失控的主要原因为电池内的隔膜受热收缩,使得电池内的正负极材料直接接触,进而出现剧烈的电化学反应(正负极材料存在电势差),并导致电池迅速升温,最终引发热失控问题。
4.也就是说,现有技术的锂离子电池的安全性较差。
技术实现要素:5.本技术实施例的目的在于提供一种电芯和电池,用于解决现有技术的锂离子电池存在的安全性较差的问题。
6.第一方面,本技术实施例提供一种电芯,包括:
7.正极片、负极片、隔膜和复合涂层,所述隔膜设置于所述正极片和所述负极片之间,所述复合涂层设置于所述正极片和所述负极片之间,所述隔膜和所述复合涂层抵接;
8.所述复合涂层包括层叠设置的变阻子层和绝缘子层,所述变阻子层包括负温度系数材料,所述绝缘子层的熔点大于或等于80摄氏度且小于或等于100摄氏度。
9.可选的,所述正极片包括正极集流体,所述负极片包括负极集流体,所述复合涂层位于所述正极集流体和/或所述负极集流体上。
10.可选的,所述正极片还包括设置于所述正极集流体上的正极活性涂层,所述负极片还包括设置于所述负极集流体上的负极活性涂层;
11.所述正极活性涂层的厚度、所述负极活性涂层的厚度以及所述隔膜的厚度之和为第一厚度值,所述复合涂层的厚度为第二厚度值,所述第二厚度值小于或等于所述第一厚度值。
12.可选的,所述正极片包括正极集流体以及设置于所述正极集流体上的正极活性涂层,所述负极片包括负极集流体以及设置于所述负极集流体上的负极活性涂层;
13.所述正极活性涂层和/或所述负极活性涂层上设置有凹槽,所述复合涂层位于所述凹槽内。
14.可选的,所述正极活性涂层的厚度、所述负极活性涂层的厚度以及所述隔膜的厚度之和为第一厚度值,所述复合涂层的厚度为第二厚度值,所述第二厚度值小于所述第一厚度值。
15.可选的,所述复合涂层位于所述电芯的尾部。
16.可选的,所述电芯的尾部的长度大于或等于0.5厘米,且小于或等于10厘米。
17.可选的,所述变阻子层的厚度大于或等于5微米,且小于或等于100微米;
18.所述绝缘子层的厚度大于或等于1微米,且小于或等于50微米。
19.第二方面,本技术实施例还提供一种电池,包括电池外壳、电解液以及如第一方面所述的电芯。
20.上述技术方案具有如下优点或有益效果:
21.本技术实施例提供的电芯,利用隔膜、包括有负温度系数材料的变阻子层、以及绝缘子层的配合设置,在电芯使用温度范围内,使正极片和负极片相互绝缘,而在电芯实际温度超过电芯使用温度范围时,变阻子层的电阻值下降,绝缘子层溶化,使得正极片和负极片通过变阻子层形成短路,以降低电芯正负极之间的电势差,避免电芯热失控问题的出现,提升电池的安全性。
附图说明
22.图1是本技术实施例提供的一种电芯的结构示意图之一;
23.图2是本技术实施例提供的一种电芯的结构示意图之二;
24.图3是本技术实施例提供的另一种电芯的结构示意图;
25.附图标记:
26.10、负极片;
27.11、负极集流体;
28.12、负极活性涂层;
29.20、正极片;
30.21、正极集流体;
31.22、正极活性涂层;
32.30、复合涂层;
33.31、变阻子层;
34.32、绝缘子层;
35.40、隔膜。
具体实施方式
36.下面将结合本技术实施例中的附图,对本技术实施例中的技术方案进行清楚、完整地描述,显然,所描述的实施例是本技术一部分实施例,而不是全部的实施例。基于本技术中的实施例,本领域普通技术人员在没有做出创造性劳动前提下所获得的所有其他实施例,都属于本技术保护的范围。
37.请参阅图1和图2,图1是本技术实施例提供的一种电芯的结构示意图之一,图2是本技术实施例提供的一种电芯的结构示意图之二,如图1和图2所示,所述电芯包括:
38.正极片20、负极片10、隔膜40和复合涂层30,所述隔膜40设置于所述正极片20和所述负极片10之间,所述复合涂层30设置于所述正极片20和所述负极片10之间,所述隔膜40和所述复合涂层30抵接;
39.所述复合涂层30包括层叠设置的变阻子层31和绝缘子层32,所述变阻子层31包括负温度系数材料,所述绝缘子层32的熔点大于或等于80摄氏度且小于或等于100摄氏度。
40.所述隔膜40位于正极片20和负极片10之间,起绝缘作用,即阻隔正极片20和负极片10直接接触。
41.复合涂层30也位于正极片20和负极片10之间,如图1所示,复合涂层30与隔膜40相互配合(可理解为复合涂层30在电芯厚度方向上的位置与隔膜40在电芯厚度方向上的位置部分重叠或完全重叠,电芯厚度方向即为图2中双向箭头所示出方向),以避免正极片20和负极片10直接接触。
42.在电芯使用温度范围内,形成变阻子层31的负温度系数材料的电阻值高,可使正极片20和负极片10保持绝缘的状态,以确保电芯使用温度范围内的电芯得以正常工作;而在电芯实际温度超过电芯使用温度范围时,形成变阻子层31的负温度系数材料的电阻值低,可使正极片20和负极片10发生短路(此时电芯正负极之间将以一个稳定的倍率电流进行短路放电),这能降低电芯正负极之间的电势差,避免电芯热失控问题的出现,提升电池的安全性。示例性的,所述电芯使用温度范围可以为[0℃,100℃]。
[0043]
由于变阻子层31的电阻值会随电芯温度升高而相应降低,因此,在复合涂层30仅包括变阻子层31的情况下,电芯的正负极之间可能存在微短路现象,为避免上述微短路现象的出现,保障电芯在电芯使用温度范围内的正常应用,即在复合涂层30内额外增设了熔点较低的绝缘子层32,在电芯使用温度范围内,绝缘子层32的设置保障了电芯正负极之间的有效绝缘,避免了变阻子层31的电阻值降低造成的微短路现象。
[0044]
而在电芯实际温度超过电芯使用温度范围时,绝缘子层32会相应融化或溶于电解液中,同时变阻子层31的电阻值也会急剧降低至预设电阻值,通过变阻子层31的存在,使得电芯正负极之间能以一个稳定的倍率电流进行短路放电,从而降低电芯的电压值,避免电芯的热失控问题,进而达到提高电芯安全性的目的。
[0045]
需要指出的是,变阻子层31和绝缘子层32层叠设置可理解为,变阻子层31在电芯厚度方向上的位置和绝缘子层32在电芯厚度方向上的位置不重叠,应用中,用户可根据实际需求适应性调整变阻子层31和绝缘子层32的相对位置(如设置变阻子层31与正极片20之间的间距大于绝缘子层32与正极片20之间的间距,或者,设置变阻子层31与正极片20之间的间距小于绝缘子层32与正极片20之间的间距),本技术实施例对此并不加以限定。
[0046]
其中,形成所述绝缘子层32的绝缘材料可以为聚对苯二甲酸乙二醇酯、聚丙烯、聚碳酸酯、聚氯乙烯、聚酰亚胺、聚乙烯、聚偏二氟乙烯、聚四氟乙烯等有机聚合物中的至少一种。
[0047]
需要说明的是,负温度系数(negative temperature coefficient,ntc)材料可以为过渡金属氧化物或者其多元氧化物复合体系,如锰、铜、硅、钴、铁、镍、锌的金属氧化物、cuo-mno二元系、coo-mno二元系、含mn三元系(mn-co-ni系、mn-cu-ni系和mn-cu-co系)等。也可以为复合型导电聚合物,如导电填料分散于非晶聚合物中,如聚乙烯/乙酸乙烯酯、乙丙三元共聚物、氯丁橡胶等。
[0048]
示例性的,可以设置所述负温度系数材料在100℃时的电阻值范围为100-1000欧姆。
[0049]
可选的,所述正极片20包括正极集流体21,所述负极片10包括负极集流体11,所述复合涂层30位于所述正极集流体21和/或所述负极集流体11上。
[0050]
其中,正极集流体21包括铝箔,涂炭铝箔、打孔铝箔、不锈钢箔、覆有导电金属的聚
合物基底中的至少一种,负极集流体11包括铜箔,涂炭铜箔、打孔铜箔、覆有导电金属的聚合物基底中的至少一种。
[0051]
如上所述,在一些实施方式中,复合涂层30可以仅设置于正极集流体21上,或者仅设置于负极集流体11;在另一些实施方式中,复合涂层30也可以一部分设置于正极集流体21上,另一部分设置于负极集流体11上(位于正极集流体21上的一部分复合涂层30和位于负极集流体11上的另一部分复合涂层30相对)。
[0052]
需要说明的是,复合涂层30设置于正极集流体21上应理解为:复合涂层30平铺设置于正极集流体21的外露部分上(该外露部分可以为正极活性材料在涂布操作时预留出的空箔部分,也可以为正极活性材料涂布后经清洗操作获得的空箔部分);同理,复合涂层30设置于负极集流体11上应理解为:复合涂层30平铺设置于负极集流体11的外露部分上。
[0053]
通过上述设置,在电芯实际温度超过电芯使用温度范围时,复合涂层30中的变阻子层31将直接接触正极集流体21和负极集流体11的方式,这能使电芯正负极之间维持稳定的短路关系,使电芯正负极之间以一个稳定的倍率电流进行短路放电,达到进一步增强电芯的安全性的目的。
[0054]
复合涂层30仅设置于正极集流体21上的情况可理解为:
[0055]
变阻子层31平铺设置于正极集流体21上,绝缘子层32平铺设置于变阻子层31远离正极集流体21的一侧;
[0056]
或者,
[0057]
绝缘子层32平铺设置于正极集流体21上,变阻子层31平铺设置于绝缘子层32远离正极集流体21的一侧。
[0058]
复合涂层30仅设置于负极集流体11上的情况可理解为:
[0059]
变阻子层31平铺设置于负极集流体11上,绝缘子层32平铺设置于变阻子层31远离负极集流体11的一侧;
[0060]
或者,绝缘子层32平铺设置于负极集流体11上,变阻子层31平铺设置于绝缘子层32远离负极集流体11的一侧。
[0061]
复合涂层30一部分设置于正极集流体21上,另一部分设置于负极集流体11上的情况可理解为:
[0062]
变阻子层31平铺设置于负极集流体11上,绝缘子层32平铺设置于正极集流体21上;
[0063]
或者,
[0064]
变阻子层31平铺设置于正极集流体21上,绝缘子层32平铺设置于负极集流体11上;
[0065]
或者,
[0066]
变阻子层31的一部分设置于负极集流体11上,变阻子层31的另一部分设置于正极集流体21上,绝缘子层32设置于变阻子层31远离负极集流体11/正极集流体21的一侧;
[0067]
或者,
[0068]
绝缘子层32的一部分设置于负极集流体11上,绝缘子层32的另一部分设置于正极集流体21上,变阻子层31设置于绝缘子层32远离负极集流体11/正极集流体21的一侧。
[0069]
可选的,所述正极片20还包括设置于所述正极集流体21上的正极活性涂层22,所
述负极片10还包括设置于所述负极集流体11上的负极活性涂层12;
[0070]
所述正极活性涂层22的厚度、所述负极活性涂层12的厚度以及所述隔膜40的厚度之和为第一厚度值,所述复合涂层30的厚度为第二厚度值,所述第二厚度值小于或等于所述第一厚度值。
[0071]
如上所述,在复合涂层30设置于正极集流体21和/或负极集流体11的情况下,通过限制第二厚度值小于或等于所述第一厚度值,以避免复合涂层30过厚的情况出现,使电芯能具备较好的平整性。
[0072]
可选的,如图3所示,所述正极片20包括正极集流体21以及设置于所述正极集流体21上的正极活性涂层22,所述负极片10包括负极集流体11以及设置于所述负极集流体11上的负极活性涂层12;
[0073]
所述复合涂层30位于所述正极活性涂层22和/或所述负极活性涂层12上。
[0074]
正极活性涂层22可以位于正极集流体21的相背两侧,或者仅位于正极集流体21靠近负极集流体11的一侧,或者仅位于正极集流体21远离负极集流体11的一侧;同理,负极活性涂层12可以位于负极集流体11的相背两侧,或者仅位于负极集流体11靠近正极集流体21的一侧,或者仅位于负极集流体11远离正极集流体21的一侧。
[0075]
通过上述设置,将复合涂层30设置在正极活性涂层22和/或负极活性涂层12上,提高复合涂层30的设置位置的灵活性,以适配复杂场景下的电芯短路需求,在保障电芯安全性的前提下增强电芯的适用性。
[0076]
如上所述,在一些实施方式中,复合涂层30可以仅设置于正极活性涂层22上,或者仅设置于负极活性涂层12;在另一些实施方式中,复合涂层30也可以一部分设置于正极活性涂层22上,另一部分设置于负极活性涂层12上(位于正极活性涂层22上的一部分复合涂层30和位于负极活性涂层12上的另一部分复合涂层30相对)。
[0077]
复合涂层30设置于正极活性涂层22的情况可理解为:
[0078]
变阻子层31平铺设置于正极活性涂层22上,绝缘子层32平铺设置于变阻子层31远离正极活性涂层22的一侧;
[0079]
或者,
[0080]
绝缘子层32平铺设置于正极活性涂层22上,变阻子层31平铺设置于绝缘子层32远离正极活性涂层22的一侧。
[0081]
复合涂层30设置于负极活性涂层12的情况可理解为:
[0082]
变阻子层31平铺设置于负极活性涂层12上,绝缘子层32平铺设置于变阻子层31远离负极活性涂层12的一侧;
[0083]
或者,
[0084]
绝缘子层32平铺设置于负极活性涂层12上,变阻子层31平铺设置于绝缘子层32远离负极活性涂层12的一侧。
[0085]
复合涂层30一部分设置于正极活性涂层22上,另一部分设置于负极活性涂层12上的情况可理解为:
[0086]
变阻子层31平铺设置于负极活性涂层12上,绝缘子层32平铺设置于正极活性涂层22上;
[0087]
或者,
[0088]
变阻子层31平铺设置于正极活性涂层22上,绝缘子层32平铺设置于负极活性涂层12上;
[0089]
或者,
[0090]
变阻子层31的一部分设置于负极活性涂层12上,变阻子层31的另一部分设置于正极活性涂层22上,绝缘子层32设置于变阻子层31远离负极活性涂层12/正极活性涂层22的一侧;
[0091]
或者,
[0092]
绝缘子层32的一部分设置于负极活性涂层12上,绝缘子层32的另一部分设置于正极活性涂层22上,变阻子层31设置于绝缘子层32远离负极活性涂层12/正极活性涂层22的一侧。
[0093]
可选的,所述正极活性涂层22和/或所述负极活性涂层12上设置有凹槽,所述复合涂层30位于所述凹槽内。
[0094]
进一步的,所述正极活性涂层22的厚度、所述负极活性涂层12的厚度以及所述隔膜40的厚度之和为第一厚度值,所述复合涂层30的厚度为第二厚度值,所述第二厚度值小于所述第一厚度值。
[0095]
在复合涂层30设置于正极活性涂层22和/或负极活性涂层12的情况下,通过限制第二厚度值小于所述第一厚度值,以避免复合涂层30过厚的情况出现,使电芯能具备较好的平整性。
[0096]
为满足第二厚度值小于第一厚度值的条件,会对复合涂层30在正极活性涂层22和/或负极活性涂层12的设置位置进行减薄处理(如通过机械清洗等方式削减涂层厚度),进行减薄处理后的正极活性涂层22和/或负极活性涂层12处即形成前述凹槽。
[0097]
需要说明的是,实际应用中,复合涂层30也可以一部分设置于正极集流体21和/或负极集流体11上,另一部分设置于正极活性涂层22和/或负极活性涂层12上。
[0098]
可选的,所述复合涂层30位于所述电芯的尾部。
[0099]
通过设置复合涂层30位于电芯的尾部,以在电芯实际温度超过电芯使用温度范围时,使复合涂层30因电芯正负极短路而产生的热量能向外充分传导,抑制电芯在短路过程中的温升,进一步提升电芯的安全性。
[0100]
其中,电芯的尾部应理解为,电芯在卷绕过程中的收尾区域,也即正极片20和负极片10远离电芯中心的一侧端部。
[0101]
可选的,所述电芯的尾部的长度大于或等于0.5厘米,且小于或等于10厘米。
[0102]
如上所述,通过限制电芯的尾部的长度,一方面能避免复合涂层30占用电芯较多空间的情况,以此确保电芯内正极活性涂层22和负极活性涂层12能获得较为充足的设置空间,进而保障电芯能拥有较高的能量密度;另一方面也能对电芯正负极通过变阻子层31进行短路放电的倍率电流进行控制,使电芯正负极在短路放电过程中产生的热量始终处于可控范围。
[0103]
可选的,所述变阻子层31的厚度大于或等于5微米,且小于或等于100微米;
[0104]
所述绝缘子层32的厚度大于或等于1微米,且小于或等于50微米。
[0105]
通过上述设置,使得用户可根据实际需求在[5微米,100微米]范围内适应性调整变阻子层31的厚度,以满足电芯的正负极短路需求,同时避免变阻子层31过厚的情况出现,
同理,用户也可根据实际需求在[1微米,50微米]范围内适应性调整绝缘子层32的厚度,以满足电芯的正负极的绝缘需求,避免微短路现象的出现,同时规避绝缘子层32过厚的情况出现。
[0106]
本技术实施例还提供一种电池,所述电池包括电池外壳、电解液以及前述实施例提供的电芯,所述电解液浸润所述电芯。
[0107]
为方便理解,示例说明如下:
[0108]
设置实验组的电芯通过下述方式进行制备:
[0109]
1、负极片制备:按重量比96:0.5:1.5:2.0的质量配比,称取石墨、导电剂炭黑、粘结剂丁苯橡胶、增稠剂羧甲基纤维素钠,将粉料混合均匀后加入适量的去离子水中,充分搅拌形成均匀的浆状,将浆料涂覆在铜箔上,然后经烘干,辊压,裁切,得到负极极片。在负极片末端的空箔区,熔融涂覆50μm厚的ntc材料层(即前述变阻子层31),冷却后再涂上5μm厚的常温绝缘层(即前述绝缘子层32)。
[0110]
2、正极片制备:称取钴酸锂、聚偏二氟乙烯、导电炭黑按95:2.5:2.5的质量比混合,再加入适量的n-甲基吡咯烷酮充分搅拌形成均匀的浆料,将浆料涂覆在正极集流体涂炭铝箔上,然后经烘干,辊压,分切,得到正极片。
[0111]
3、隔膜30制备:选择9μm湿法聚乙烯隔膜作为基材,先在基材的一个表面涂2μm厚的氧化铝陶瓷涂层,然后再在隔膜两侧分别涂厚度为1μm的绝缘胶层,得到总厚度为13μm的隔膜,分切为所需宽度备用。
[0112]
4、电解液制备:在含水量《1ppm的充有氩气的手套箱中,将碳酸乙烯酯、碳酸甲乙酯、碳酸二乙酯按照质量比0.5:1.5:1.5混合,加入浓度为1.0mol/l的六氟磷酸锂,搅拌均匀,继续充分搅拌均匀后得到电解液。
[0113]
5、电芯制备:将上述负极片、隔膜和正极片按顺序叠好,使隔膜处于正极片和负极片中间,然后经过卷绕得到卷芯,然后将卷芯置于铝塑膜包装袋中,最后注入上述电解液并经过真空密封、静置、化成、整形等工序,即可完成电芯制备。
[0114]
设置对照组一的电芯仍沿用实验组的制备方式制备,不同的是,对照组一的电芯的负极片上未设置常温绝缘层。
[0115]
设置对照组二的电芯仍沿用实验组的制备方式制备,不同的是,对照组二的电芯的正负极片的末端均未设置ntc材料层和常温绝缘层,且对照组二的电芯的正负极片被隔膜充分分隔。
[0116]
对实验组、对照组一和对照组二的电池均进行安全性测试,所述安全性测试包括常温存储测试、中温存储测试以及高温热存储测试。
[0117]
其中,常温存储测试具体为,将电芯充电至满电状态(4.45v),然后在常温下存储30天,每间隔72小时对电芯电压进行测试,同时记录电芯在30天后的电压。
[0118]
中温存储测试具体为,将电芯充电至满电状态(4.45v),然后在50℃下存储30天,每间隔72小时对电芯电压进行测试,同时记录电芯在30天后的电压。
[0119]
高温热存储测试具体为,将电芯充电至满电状态(4.45v),然后将电芯放置于烘箱内,设置烘箱以2℃/min的加热速率升温至150℃,并保持60min。
[0120]
在常温存储测试中,实验组对应电芯在30天后的电压为4.43v,对照组一对应电芯在30天后的电压为4.4v,对照组二对应电芯在30天后的4.44v。
[0121]
在中温存储测试中,实验组对应电芯在30天后的电压为4.38v,对照组一对应电芯在30天后的电压为3.8v,对照组二对应电芯在30天后的4.4v。
[0122]
在高温热存储测试中,实验组对应电芯在温度升到100℃时电压出现明显降低,在120℃-130℃电压接近0v,未出现热失控现象;对照组一对应电芯也未出现热失控现象;对照组二对应电芯在140℃时电压骤减至0v,严重胀气,随后冒烟起。
[0123]
由上述示例可知,利用电芯尾部的ntc材料层和常温绝缘层的设置,不仅可以避免电芯在常温下出现微短路现象,还可以在电芯温度过高时,实现电芯正负极的短路,降低正负极电势差,避免电芯热失控问题的出现,提高电芯的安全性。
[0124]
上面结合附图对本技术的实施例进行了描述,但是本技术并不局限于上述的具体实施方式,上述的具体实施方式仅仅是示意性的,而不是限制性的,本领域的普通技术人员在本技术的启示下,在不脱离本技术宗旨和权利要求所保护的范围情况下,还可做出很多形式,均属于本技术的保护之内。