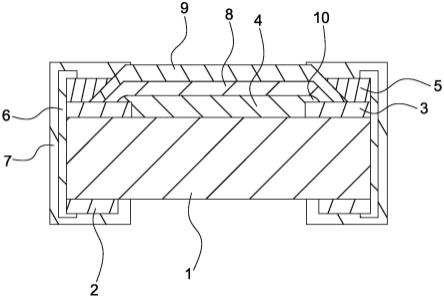
1.本实用新型涉及一种电阻,尤其涉及一种耐高温电阻。
背景技术:2.常规晶片电阻使用环境温度-55℃~155℃。环境温度不超过70℃满载功率使用,当温度超出70℃,负载依照降低额定功率曲线使用(降额曲线如图 1所示)。如果晶片电阻不降低额定功率,在高温下仍然满载使用,则使用一段时间后,电阻值变化率变大而不稳定,难以达成高温稳定负载寿命的要求。取常规0603型别,life满载功率(0.125w)临界值45k3的晶片电阻晶片80pcs,经过三次回流焊前处理,把晶片电阻焊接在耐高温在pcb板上。而后在180℃的环境温度下,加75v工作电压,持续通电。分别对各时间节点尺寸监控,可以发现随时间推移,电阻值变化率不断离散。待持续通电h 后,量测电阻值变化率已超出2%。
技术实现要素:3.本实用新型目的是提供一种耐高温电阻,通过使用该结构,能够制作出在高温环境下高功率、稳定性强的高温电阻,提高使用稳定性,延长使用寿命。
4.为达到上述目的,本实用新型采用的技术方案是:一种耐高温电阻,包括:
5.基板;
6.两组背面电极,其分别对称设置于所述基板的底面两侧;
7.两组正面电极,其分别对称设置于所述基板的顶面两侧;
8.电阻层,其设置于两组所述正面电极之间的所述基板的顶面上;
9.保护层,所述保护层覆盖于所述电阻层的外部,且所述电阻层的两端分别覆盖于两侧所述正面电极的部分顶面上;
10.两组侧部端电极,两组所述侧部端电极分别密封于所述基板的两侧,
11.所述电阻层的两端分别与两侧所述正面电极的内侧相连,所述电阻层的两端分别朝外延伸,分别覆盖于两组所述正面电极的部分顶面上;所述电阻层的长度为所述正面电极长度的2.5倍~5倍,所述电阻层的厚度为所述正面电极厚度的1.2倍~2倍;
12.每组所述正面电极的顶面外端分别设有一辅助电极层,所述辅助电极层的内侧与所述保护层的外侧面相连。
13.上述技术方案中,所述侧部端电极包括真空镀膜层及包覆于所述真空镀膜层外部的电镀层;所述真空镀膜层的中部覆盖于所述基板的侧壁上,所述真空镀膜层的上方覆盖于所述正面电极以及所述辅助电极层的外壁,且所述真空镀膜层的上方覆盖于所述辅助电极层的部分顶面上;所述真空镀膜层的下方覆盖于所述背面电极的外壁,且所述真空镀膜层的下方覆盖于所述背面电极的部分底面上;
14.所述电镀层完全覆盖于所述真空镀膜层的外部,所述电镀层的上方覆盖于所述辅助电极层的外部顶面上,且所述电镀层的上方覆盖于所述保护层的外壁上;所述电镀层的下方完全覆盖于所述背面电极的外部,且所述电镀层的下方覆盖于部分所述基板的底面。
15.上述技术方案中,所述保护层包括第一保护层及第二保护层,所述第一保护层包覆于所述电阻层的外部,所述第二保护层包覆于所述第一保护层的外部,且所述第一保护层及第二保护层的两端底部分别包覆于两组所述正面电极的部分正面上。
16.上述技术方案中,所述基板为陶瓷基板,所述第一保护层为玻璃保护层,所述第二保护层为树脂保护层。
17.上述技术方案中,所述电阻层的中部为方形结构,所述电阻层的顶部两端分别设有朝外延伸的延伸部,每组所述延伸部的底面与一组所述正面电极的部分顶面相连;所述延伸部的宽度大于所述电阻层的中部宽度以及所述正面电极的顶部宽度,所述延伸部在宽度方向将所述正面电极完全覆盖包裹,所述电阻层与两侧所述延伸部之间构成两端大、中间小的哑铃结构。
18.上述技术方案中,所述电阻层前侧及后侧分别设有前侧雷切定位凹槽及后侧雷切定位凹槽,所述前侧雷切定位凹槽靠近左侧所述延伸部设置,所述后侧雷切定位凹槽靠近右侧所述延伸部设置。
19.为达到上述目的,本实用新型采用了一种耐高温电阻的制作方法,其步骤为:
20.①
在基板的底面印刷制作背面电极,然后在基板的顶面印刷正面电极,再进行烧结固化,使背面电极以及正面电极固化在基板上;
21.②
在基板的顶面进行电阻层的印刷,然后进行烧结固化;在电阻层印刷的过程中,会预留有雷切定位凹槽;
22.③
在第一电阻层上面进行第一保护层的印刷,第一保护层印刷完成之后,进行烧结固化;
23.④
根据雷切定位凹槽,通过镭射激光调阻机对电阻层进行切割调阻;
24.⑤
在第一保护层上面印刷第二保护层,然后在第二保护层的两侧外部,以及每组正面电极上方印刷辅助电极层;
25.⑥
然后在第二保护层外部进行字码印刷,再进行固化,使第二保护层、辅助电极层以及字码进行固化,固化完成之后,进行外观检查;
26.⑦
将上述基板折成条状半成品;
27.⑧
在步骤
⑦
的条状半成品的两侧进行真空镀膜,使条状半成品的两侧实现真空镀膜层;
28.⑨
将步骤
⑧
中的条状半成品折成粒状半成品;
29.⑩
将步骤
⑨
中的粒状半成品设置有真空镀膜层的两端头制作电镀层,完成耐高温电阻的制作。
30.上述技术方案中,所述正面电极、背面电极以及电阻层采用850℃进行烧结固化;所述第一保护层采用620℃进行烧结固化;所述第二保护层、辅助电极层及字码采用200℃进行烧结固化。
31.由于上述技术方案运用,本实用新型与现有技术相比具有下列优点:
32.1.本实用新型中通过对电阻层以及正面电极尺寸的设置,能够拓展电流通路长度及宽度,提升电阻使用功率,削弱导体扩散的影响,增强电阻在高温功率下的稳定性,使得在180℃全功率情况下运行的时候,电阻阻值的变化率小于0.1%,提高电阻在高温情况下使用的稳定性;
33.2.本实用新型中能够减少热点聚集,增强电阻的散热及耐高温能力,提高电阻的高温使用性能及稳定性;
34.3.本实用新型中电阻层为哑铃结构的流线型,能够增加电阻层与正面电极的搭接,加强电阻层对正面电极边缘的覆盖保护,削弱尖端效应等导致的导体边缘银向电阻层扩散;其次有效增加散热面积的同时,又避免了雷切阻值修正区域因电阻过宽而导致内切现象发生;
35.4.本实用新型汇总通过多个雷切定位凹槽的设置,既便于雷割定位,降低切割批间的波动,同时能够增加电流路径的有效长度,减少因为雷切切割道口过长对电阻层的伤害;
36.5.本实用新型中电阻层厚度的设置,比以往结构中电阻层的厚度更厚,免因电阻层印刷导致的缺陷而形成的热点,降低电阻层局部温度;其二拓宽电流通路提升功率及寿命稳定性;
37.6.本实用新型中增加辅助电极层,解决因正面电极缩短、电阻层延长而带来的正面端子不足问题,增加电阻的散热能力及耐侵蚀能力。
附图说明
38.图1是背景技术中晶片电阻降额曲线图;
39.图2是本实用新型实施例一中的结构示意图;
40.图3是本实用新型实施例一中电阻层状态下的俯视图(电阻批量生产过程中,正面电极、电阻层印刷之后的状态图)。
41.其中:1、基板;2、背面电极;3、正面电极;4、电阻层;5、辅助电极层;6、真空镀膜层;7、电镀层;8、第一保护层;9、第二保护层;10、延伸部;11、前侧雷切定位凹槽;12、后侧雷切定位凹槽。
具体实施方式
42.下面结合附图及实施例对本实用新型作进一步描述:
43.实施例一:参见图2、3所示,一种耐高温电阻,包括:
44.基板1;其中基板的顶面为正面,基板的底面为背面。
45.两组背面电极2,其分别对称设置于所述基板的底面两侧;
46.两组正面电极3,其分别对称设置于所述基板的顶面两侧;
47.电阻层4,其设置于两组所述正面电极之间的所述基板的顶面上;
48.保护层,所述保护层覆盖于所述电阻层的外部,且所述电阻层的两端分别覆盖于两侧所述正面电极的部分顶面上;
49.两组侧部端电极,两组所述侧部端电极分别密封于所述基板的两侧,其特征在于:
50.所述电阻层的两端分别与两侧所述正面电极的内侧相连,所述电阻层的两端分别朝外延伸,分别覆盖于两组所述正面电极的部分顶面上;所述电阻层的长度为所述正面电极长度的2.5倍~5倍,所述电阻层的厚度为所述正面电极厚度的1.2倍~2倍;
51.每组所述正面电极的顶面外端分别设有一辅助电极层5,所述辅助电极层的内侧与所述保护层的外侧面相连。
52.在本实施例中,电阻层进行延长,对正面电极进行缩短,这样能够延长电阻层的长度,在保证电阻层与正面电极搭接稳定性的基础上,延长有效电阻,从而提升电阻使用率,增加电阻散热面积,提高高温情况下的使用稳定性。并且,由于正面电极缩短、电阻层延长会带来正面端子不足的问题,通过两侧辅助电极层的设置,解决上述正面端子不足的问题,还能够增加电阻的散热能力以及耐侵蚀能力。增加电阻层的厚度,能够避免因为电阻层印刷导致的缺陷而形成的热点,能够降低电阻层局部温度,同时,拓宽电流通路,提升功率和寿命的稳定性。
53.同时,增加电阻层长度及厚度,其一减少因电阻层过薄导致的局部缺陷,高温负载易形成热点造成局部导电机制发生变化或破坏而导致阻值不稳定,也就是提高使用的稳定性。其二增加电阻层厚度及长度,拓宽电流通路,提升电阻使用功率。
54.参见图2所示,所述侧部端电极包括真空镀膜层6及包覆于所述真空镀膜层外部的电镀层7;所述真空镀膜层的中部覆盖于所述基板的侧壁上,所述真空镀膜层的上方覆盖于所述正面电极以及所述辅助电极层的外壁,且所述真空镀膜层的上方覆盖于所述辅助电极层的部分顶面上;所述真空镀膜层的下方覆盖于所述背面电极的外壁,且所述真空镀膜层的下方覆盖于所述背面电极的部分底面上。
55.所述电镀层完全覆盖于所述真空镀膜层的外部,所述电镀层的上方覆盖于所述辅助电极层的外部顶面上,且所述电镀层的上方覆盖于所述保护层的外壁上;所述电镀层的下方完全覆盖于所述背面电极的外部,且所述电镀层的下方覆盖于部分所述基板的底面。其中,真空镀膜层的设置,用以将正面电极与背面电极进行连接。
56.在本实施例中,由于辅助电极层的设置,因此,真空镀膜层及电镀层的上方会覆盖于辅助电极层的外部,起到连通导电的作用。
57.参见图2所示,所述保护层包括第一保护层8及第二保护层9,所述第一保护层包覆于所述电阻层的外部,所述第二保护层包覆于所述第一保护层的外部,且所述第一保护层及第二保护层的两端底部分别包覆于两组所述正面电极的部分正面上。
58.所述基板为陶瓷基板,所述第一保护层为玻璃保护层,所述第二保护层为树脂保护层。
59.其中,第一保护层及第二保护层用于将电阻层进行保护以及绝缘,同时,树脂保护层采用的是耐高温、散热性强的树脂,用以增强电阻耐高温和散热能力,增加电阻在高温情况下的稳定性。树脂保护层一般会选用膨胀系数较小的树脂材料。
60.参见图2、3所示,所述电阻层的中部为方形结构,所述电阻层的顶部两端分别设有朝外延伸的延伸部10,每组所述延伸部的底面与一组所述正面电极的部分顶面相连;所述延伸部的宽度大于所述电阻层的中部宽度以及所述正面电极的顶部宽度,所述延伸部在宽度方向将所述正面电极完全覆盖包裹,所述电阻层与两侧所述延伸部之间构成两端大、中间小的哑铃结构。
61.在本实施例中,电阻层的宽度会略大于正面电极的宽度,因此,延伸部的宽度也会大于正面电极的宽度,这样电阻层就构成一个哑铃结构,延伸部的内侧与电阻层侧壁连接处为弧形面连接,哑铃结构的电阻层设计,能够增加电阻层与正面电极的搭接,首先加强电阻层对正面电极内侧边缘的覆盖及保护,削弱尖端效应等导致的导体边缘银向电阻层扩散;其次有效增加散热面积的同时,又避免了雷切阻值修正区域因电阻过宽而导致内切现
象发生。
62.其中,电阻层的左右为电阻层的长度方向,前后为电阻层的宽度方向,延伸部的长度大于正面电极与电阻层的搭接长度,宽度方向超出正面电极宽度的50微米~100微米。
63.参见图3所示,所述电阻层前侧及后侧分别设有前侧雷切定位凹槽11 及后侧雷切定位凹槽12,所述前侧雷切定位凹槽靠近左侧所述延伸部设置,所述后侧雷切定位凹槽靠近右侧所述延伸部设置。
64.其中,前侧雷切定位凹槽及后侧雷切定位凹槽会处在电阻层的雷切区域,通过对应雷切定位凹槽的设置,既能够便于雷切切割定位,降低切割批间波动,同时,增加电流路径的有效长度,并且减少雷切切割道口过长对电阻层的伤害,用以保证电阻效果。
65.并且,通过雷切定位凹槽的设置,将其设置在电阻层需要雷切起始位置,将雷切的起始位置设计为镂空区,在使用对应设计的电阻网版印刷呈电阻层所需厚度之后,需要雷切的起始部位就呈现凹槽基板裸露,方便雷切定位,并且减少切割长度,减少切割过程中对电阻层的伤害,用以保证电阻效果。
66.为达到上述目的,本实用新型采用了一种耐高温电阻的制作方法,其步骤为:
67.①
在基板的底面印刷制作背面电极,然后在基板的顶面印刷正面电极,再进行烧结固化,使背面电极以及正面电极固化在基板上;
68.②
在基板的顶面进行电阻层的印刷,电阻层的中部设置在两组正面电极之间,电阻层的两侧则会分别搭接覆盖在两侧正面电极内端的上方,然后进行烧结固化;在电阻层印刷的过程中,会预留有雷切定位凹槽;
69.③
在第一电阻层上面进行第一保护层的印刷,第一保护层印刷完成之后,进行烧结固化;
70.④
根据雷切定位凹槽,通过镭射激光调阻机对电阻层进行切割调阻;
71.⑤
在第一保护层上面印刷第二保护层,然后在第二保护层的两侧外部,以及每组正面电极上方印刷辅助电极层;
72.⑥
然后在第二保护层外部进行字码印刷,再进行固化,使第二保护层、辅助电极层以及字码进行固化,固化完成之后,进行外观检查;
73.⑦
将上述基板折成条状半成品;
74.⑧
在步骤
⑦
的条状半成品的两侧进行真空镀膜,使条状半成品的两侧实现真空镀膜层;
75.⑨
将步骤
⑧
中的条状半成品折成粒状半成品;
76.⑩
将步骤
⑨
中的粒状半成品设置有真空镀膜层的两端头制作电镀层,完成耐高温电阻的制作。
77.所述正面电极、背面电极以及电阻层采用850℃进行烧结固化;所述第一保护层采用620℃进行烧结固化;所述第二保护层、辅助电极层及字码采用200℃进行烧结固化。
78.其中,辅助电极层采用能够导电、可以被电镀的材料,其能够增强散热,阻隔硫化物等侵袭,同时和第二保护层、正面电极的结合力也比较好。
79.在本实用新型中,无需引入新材料,即可使得电阻能够在高温环境下进行高功率、高稳定性的正常运行以及使用,延长使用寿命,保证使用的稳定性,提高适用范围。