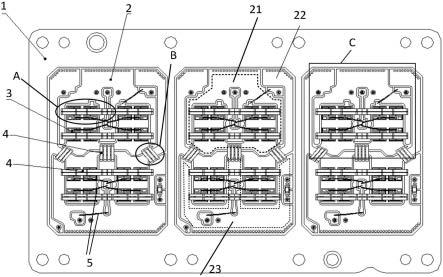
1.本实用新型涉及电力电子技术领域,尤其涉及一种铜带键合的碳化硅车用功率模块封装结构。
背景技术:2.随着功率器件封装技术的不断发展,由于功率器件封装热阻较大,而封装热阻又决定了器件的最大功率损耗,若能减少封装热阻及寄生电阻,则有利于降低功率器件的导通损耗,降低功率器件的使用温升,从而提升功率器件整体效率。
3.由于传统的功率器件封装中,一般采用金线、铝线、铜线等金属材料作为引线将芯片与引脚焊接,实现电气连接。而这些金属线焊接存在一些问题,铝线单根通流能力虽然大于金线和铜线,但铝线在焊接过程中,与被焊区的铝金属化层表面快速摩擦,使得铝线与芯片电极表面产生塑性变形以达到焊接效果,因而会在多次楔焊后对芯片造成较大冲击,增加芯片内部出现暗裂和弹坑的风险,且升降温连接层的耐应力差和抗功率循环性能差。金线和铜线单根通流能力有限,过大的电流会将它烧断,因此功率器件一般需要采用多根金线或铜线的工艺以实现大电流通过能力,但是多根金线或铜线会产生较大的寄生电阻,从而导致电源效率降低,功率损耗增大。
技术实现要素:4.针对现有技术中存在的问题,本实用新型提供一种铜带键合的碳化硅车用功率模块封装结构,包括:
5.基板,所述基板上焊接有至少一块覆铜陶瓷基板,各所述覆铜陶瓷基板的上半部分设有第一沟槽区,各所述覆铜陶瓷基板的下半部分设有第三沟槽区,所述第一沟槽区和所述第三沟槽区之间间隔设有第二沟槽区;
6.多个车用功率芯片,各所述车用功率芯片分别呈阵列分布于所述第一沟槽区和所述第二沟槽区;
7.同一行的各所述车用功率芯片之间以及各所述车用功率芯片与所述覆铜陶瓷基板的表面之间均通过铜带键合连接;
8.所述第一沟槽区和所述第三沟槽区之间通过多根铜带键合连接。
9.优选的,所述车用功率芯片包括:硅基mosfet芯片、硅基igbt芯片、sic芯片和gan芯片中的至少一种。
10.优选的,每个所述车用功率芯片上至少有两个芯片键合点,所述铜带的中段和两端上分别有多个铜带键合点;
11.所述铜带和各所述车用功率芯片通过所述铜带的中段的各所述铜带键合点和各所述芯片键合点对应键合,实现电气连接;
12.所述铜带和所述覆铜陶瓷基板的表面通过所述铜带两端的各所述铜带键合点和所述覆铜陶瓷基板的表面键合,实现电气连接。
13.优选的,各所述车用功率芯片的门极之间以及各所述车用功率芯片的门极与所述覆铜陶瓷基板的门极之间均通过铝线连接。
14.优选的,各所述铜带键合点形状为正方形,或长方形,或不规则形。
15.优选的,各所述铜带键合点高度为20μm到5mm。
16.优选的,各所述铜带的键合尺寸范围为500μm*500μm到1500μm*500μm。
17.优选的,连接各所述车用功率芯片和所述覆铜陶瓷基板的表面的各所述铜带之间并排均匀分布。
18.优选的,所述第三沟槽区为“山”字型,连接所述第三沟槽区和所述第一沟槽区的各所述铜带的一端键合在所述第三沟槽区的“山”字型的峰顶,另一端键合在所述第一沟槽区的底部。
19.上述技术方案具有如下优点或有益效果:
20.1)通过铜带作为引线,连接覆铜陶瓷基板表面的沟槽,提升通流能力、耐应力、抗功率循环能力,使模块可靠性能提升;
21.2)通过铜带键合在车用功率芯片及覆铜陶瓷基板的表面上,实现芯片及覆铜陶瓷基板的表面的连接,减少车用功率芯片单位面积上所受到的压力,也就减少了车用功率芯片损伤的可能性;
22.3)采用铜带键合,铜带引线具有自身电阻小,寄生电阻小,电性能优的特点,可获得更小的导通电阻,且耐应力强,过流能力提升及功率循环性能强,从而提高功率模块可靠性能。
附图说明
23.图1为本实用新型的较佳的实施例中,铜带键合的碳化硅车用功率模块封装结构的结构示意图;
24.图2为图1中的a区的局部放大图;
25.图3为图1中的b区的局部放大图;
26.图4为图1中的c区的局部放大图。
具体实施方式
27.下面结合附图和具体实施例对本实用新型进行详细说明。本实用新型并不限定于该实施方式,只要符合本实用新型的主旨,则其他实施方式也可以属于本实用新型的范畴。
28.本实用新型的较佳的实施例中,基于现有技术中存在的上述问题,现提供一种铜带键合的碳化硅车用功率模块封装结构,如图1和图4所示,包括:
29.基板1,基板1上焊接有至少一块覆铜陶瓷基板2,各覆铜陶瓷基板2的上半部分设有第一沟槽区21,各覆铜陶瓷基板2的下半部分设有第三沟槽区23,第一沟槽21区和第三沟槽区23之间间隔设有第二沟槽区22;
30.多个车用功率芯片3,各车用功率芯片3分别呈阵列分布于第一沟槽区21和第二沟槽区22;
31.同一行的各车用功率芯片3之间以及各车用功率芯片3与覆铜陶瓷基板2的表面之间均通过铜带4键合连接;
32.第一沟槽区21和第三沟槽区23之间通过多根铜带4键合连接。
33.本实用新型的较佳的实施例中,如图1所示,第三沟槽区23为“山”字型,连接第三沟槽区23和第一沟槽区21的各铜带4的一端键合在第三沟槽区23的“山”字型的峰顶,另一端键合在第一沟槽区21的底部。
34.具体的,本实施例中,在图示中由虚线框选的两部分分别为第一沟槽区21和第三沟槽区23,位于第一沟槽区和第三沟槽区之间的沟槽区为第二沟槽区22,可以看出第二沟槽区22向上延伸将第一沟槽区21半包围,且第三沟槽区23为“山”字型,第三沟槽“山”字形的峰顶距离第一沟槽区的底部最近,各铜带4的一端键合在第三沟槽区23的“山”字型的峰顶,另一端键合在第一沟槽区21的底部,可以缩短铜带4距离,提高传输效率,也可节省成本,实现第三沟槽区23和第一沟槽区21的电气连接。
35.如图4所示,在第一沟槽区21中还包括第一子沟槽区211和第二子沟槽区212,第二子沟槽区212位于第一沟槽区21的底部,第一子沟槽区21在位于第一沟槽区21的顶部;在第一沟槽区21中,通过铜带4将第一子沟槽区211的表面和第二子沟槽区中的各车用功率芯片3键合连接,实现第一子沟槽区211和第二子沟槽区212的电气连接。
36.通过铜带4将第二沟槽区22中的车用功率芯片与第三沟槽23的表面键合,实现将第二沟槽区22和第三沟槽区23的电气连接。
37.可以看出,通过铜带键合,使覆铜陶瓷基板2表面的所有沟槽区之间实现电气连接,提升通流能力、耐应力、抗功率循环能力,使功率模块的可靠性能提升。
38.本实用新型的较佳的实施例中,车用功率芯片3包括:硅基mosfet芯片、硅基igbt芯片、sic芯片和gan芯片中的至少一种。
39.本实用新型的较佳的实施例中,每个车用功率芯片3上至少有两个芯片键合点,铜带4的中段和两端上分别有多个铜带键合点;
40.铜带4和各车用功率芯片3通过铜带的中段的各铜带键合点和各芯片键合点对应键合,实现电气连接;
41.铜带4和覆铜陶瓷基板2的表面通过铜带4两端的各铜带键合点和覆铜陶瓷基板2的表面键合,实现电气连接。
42.具体的,本实施例中,通过多个铜带键合点分别与多个芯片键合点以及覆铜陶瓷基板2的表面键合连接,实现车用功率芯片3及覆铜陶瓷基板2的表面的连接,减少车用功率芯片3单位面积上所受到的压力,也就减少了车用功率芯片3损伤的可能性。
43.本实用新型的较佳的实施例中,如图1所示,各车用功率芯片3的门极以及各车用功率芯片3的门极与覆铜陶瓷基板2的门极之间均通过铝线5连接。
44.具体的,本实施例中,将各车用功率芯片3的门极与各车用功率芯片3的门极之间以及各车用功率芯片3的门极与覆铜陶瓷基板2的门极之间均通过铝线5连接,进一步实现车用功率芯片3和覆铜陶瓷基板2的电气连接,增大电流导通能力。
45.本实用新型的较佳的实施例中,各铜带键合点形状为正方形,或长方形,或不规则形。
46.本实用新型的较佳的实施例中,各铜带键合点高度为20μm到5mm。
47.本实用新型的较佳的实施例中,各铜带4的键合尺寸范围为500μm*500μm到1500μm*500μm。
48.具体的,本实施例中,铜带键合点的形状、高度和尺寸范围可根据不同的车用功率芯片和键合的需求选择。
49.本实用新型的较佳的实施例中,如图1所示,连接各车用功率芯片3和覆铜陶瓷基板2的表面的各铜带4之间并排均匀分布。
50.具体的,本实施例中,各铜带4间并排均匀分布,可减小铜带4单位面积受的压力,增强电流导通能力。
51.以上仅为本实用新型较佳的实施例,并非因此限制本实用新型的实施方式及保护范围,对于本领域技术人员而言,应当能够意识到凡运用本说明书及图示内容所作出的等同替换和显而易见的变化所得到的方案,均应当包含在本实用新型的保护范围内。