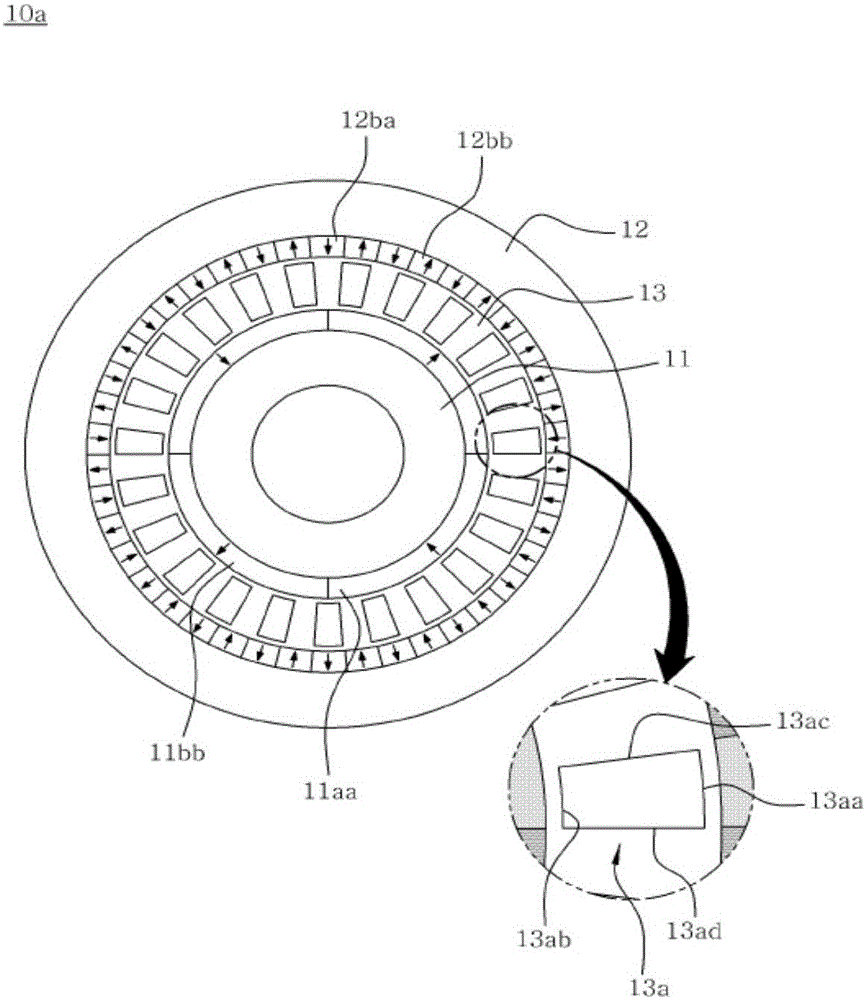
本发明涉及一种凸极式磁齿轮,更为具体地,涉及一种使用叠层铁芯的凸极替代内转子或者外转子、内转子和外转子的磁双极中的一个极的磁铁,由此能够减少稀土永磁铁的使用,并通过改善极片的形状将磁束集中在空隙中,从而能够提高传递转矩且降低转矩脉动的凸极式磁齿轮。
背景技术:
:磁齿轮是利用磁力以非接触的形式来传递动力的非接触式齿轮装置,相比通过物理接触传递动力的齿轮,其噪音和振动小,且无需注入润滑油或进行维修检验,不存在机械摩擦,稳定性和耐久性高,因此近年来正积极开展研究。而且,由于磁齿轮能够减少能量损失,因此可实现高效率驱动,并且能够传递可靠度及准确度高的最大转矩。而且,近年来努力在风力轮机、电动汽车、变速器等多种产业全面适用磁齿轮。图1是示出普通磁齿轮的图,图2是示出普通磁齿轮的垂直剖面的图。参照图1及图2,现有的磁齿轮10大致包括内转子11,外转子12、在内转子11和外转子之间与各转子11、12隔开设置的极片模块13。而且,所述内转子11包括内侧回转子11b和磁铁11a,所述磁铁11a以旋转轴为中心并以放射状粘贴在内侧回转子11b的外部,所述外转子12包括外侧回转子12a和磁铁12b,所述磁铁12b以旋转轴为中心并以放射状粘贴在外侧回转子12a的内部,所述极片模块13包括相对于旋转轴以放射状设置并等距离隔开的多个极片13a。而且,所述内转子11和所述外转子12的磁铁是具有反向(朝向旋转轴的方向和朝向旋转轴反方向的方向)磁力的磁铁相互交替设置的磁铁,且具有反向磁力的两个磁铁形成双极。如上所述,当在所述转子11、12上以双极形式配置磁铁时,能够制造出可实现高转矩输出和高速旋转的齿轮,但是随着稀土永磁铁的使用量增加,存在制造成本高的缺点。而且,当所述极片模块13处于固定状态时,所述内转子11和所述外转子12相互以反方向旋转,根据哪一个转子成为输入轴,将其用作减速器或加速器。而且,所述外转子12以低速旋转,所述内转子11以高速旋转,如以下数学式a所示,所述外转子12的极对数和所述内转子11的极对数决定极片13a的数量。[数学式a]Ns=p1+p2在此,NS为极片13a的数量,p1为外转子12的极对数,p2为内转子11的极对数。而且,如图2,外转子12的磁铁的极数为42极,极对数为21极,内转子11的磁铁的极数为4极,极对数为2极,因此,极片13a的数量为将各转子的极对数21极和2极相加得出的23个。而且,如以下数学式b所示,磁齿轮10的齿轮比由转子的极对数的比值所决定。[数学式b]Gr=p1p2]]>而且,磁齿轮10的转子的速度比如下数学式c。[数学式c]w2=-Grw1另外,现有的磁齿轮1的极片13a具有垂直剖面由圆心角相同而直径不同的外侧弧13aa、内侧弧13ab、连接外侧弧13aa和内侧弧13ab的各一端的直线13ac以及连接各另一端的直线13ad围绕的图形的形状。但是,现有的磁齿轮10因所述极片13a的形状的局限性,而无法将磁束集中在外转子12与极片模块13之间、内转子11与极片模块13之间的空隙中,因此存在转矩传递低且转矩脉动大的问题。现有技术文献专利文献1.韩国公开专利第10-2013-0042564号,磁齿轮装置及保持构件2.韩国公开专利第10-2014-0013087号,磁齿轮装置技术实现要素:(一)要解决的技术问题本发明是为了解决上述问题而提出的,本发明的目的在于提供一种磁齿轮,所述磁齿轮能够通过减少稀土永磁铁的使用来降低生产成本。而且,本发明的目的在于提供一种磁齿轮,所述磁齿轮能够通过优化极片的形状将磁束集中在空隙中,从而提高转矩的传递,降低转矩脉动,由此提高动力传递率和可靠性。本发明的目的并不限定于以上所提及的目的,本领域的普通技术人员可通过以下的记载内容明确地理解未被提及的其他的目的。(二)技术方案本发明为达到上述目的提供一种磁齿轮,其包括:内转子(innerrotor);外转子(outerroter),与所述内转子隔开设置;极片模块,其位于所述内转子与所述外转子之间,并且包括多个隔开设置的极片(polepiece),所述极片将磁束从所述内转子传递至所述外转子或者从所述外转子传递至所述内转子,其特征在于,所述内转子和所述外转子中,至少一个转子是磁铁和凸极(salientpole)相对于旋转轴以放射状交替叠层在其表面上。根据优选实施例,所述外转子是凸极式转子,所述外转子包括:圆筒形外侧回转子;多个磁铁(以下简称为‘外侧磁铁’),以旋转轴为中心并以放射状隔开粘贴在所述外侧回转子的内侧面,并且具有朝向所述旋转轴的磁力;以及凸极(以下简称为‘外侧凸极’),其通过铁芯叠层在所述外侧回转子的内侧面而形成,且分别设置在所述外侧磁铁之间。根据优选实施例,所述内转子是凸极式转子,所述内转子包括:圆筒形内侧回转子;多个磁铁(以下简称为‘内侧磁铁’),以旋转轴为中心并以放射状隔开粘贴在所述内侧回转子的外侧面,并且具有朝向所述旋转轴的反方向的磁力;以及凸极(以下简称为‘内侧凸极’),其通过铁芯叠层在所述内侧回转子的外侧面而形成,且分别设置在所述内侧磁铁之间。而且,所述外转子和所述内转子分别可由凸极式转子构成。根据优选实施例,所述各极片的剖面具有由第一图形和第二图形接合的形状,其中,所述第一图形是由第一弧(arc)、具有与所述第一弧相同的中心位置和圆心角且内径小于所述第一弧的内径的第二弧以及连接所述第一弧和所述第二弧的各一端和各另一端的线围绕而形成,所述第二图形是由具有与所述第二弧相同的中心位置和内径且圆心角大于所述第二弧的圆心角的第三弧、具有与所述第三弧相同的中心位置和圆心角且内径小于所述第三弧的内径的第四弧以及连接所述第三弧和所述第四弧的各一端和各另一端的线围绕而形成,并且,具有以所述第二弧的二等分位置和所述第三弧的二等分位置相互重叠的方式接合的形状。根据优选实施例,如以下的数学式1所示,所述第四弧与所述第三弧的垂直距离(以下简称为‘第一垂直距离’)大于所述第四弧与所述第一弧的垂直距离(以下简称为‘第二垂直距离’)的13.5%,小于所述第四弧与所述第一弧的垂直距离的23.5%,[数学式1]Lpr×0.135≤α≤Lpr×0.235其中,α为所述第一垂直距离,Lpr为所述第二垂直距离。根据优选实施例,如以下数学式2所示,所述第四弧的圆心角大于连接中间夹有一个极片的两个极片的第一弧的虚拟弧的圆心角(以下简称为‘参考角’)的40%,而小于所述参考角的50%,[数学式2]0.4≤Np360×23×β≤0.5]]>其中,β为所述第四弧的圆心角,Np为所述极片的数量。根据优选实施例,在所述第一图形中,连接所述第一弧和第二弧的线为向所述第一图形的中心部凹陷的曲线(以下简称为‘凹曲线’)。根据优选实施例,凹陷长度大于从第二虚拟线段的二等分位置沿垂直方向到第三虚拟线段的长度的30%,并小于所述长度的40%,其中,所述凹陷长度是指从第一虚拟线段的二等分位置沿垂直方向到所述凹曲线的长度,第一虚拟线段为连接所述凹曲线两端的虚拟线段,第二虚拟线段是指从所述凹曲线的所述第一弧侧的一端沿垂直方向连接到所述第四弧的虚拟线段,第三虚拟线段是指连接所述第一弧的二等分位置和所述第四弧的二等分位置的虚拟线段。根据优选实施例,所述凹陷长度是通过以下数学式3来计算,[数学式3]0.3≤γ14(Dpi+Dpo)tan(90Np)≤0.4]]>其中,Dpi为所述第四弧的内径,Dpo为所述第一弧的内径,Np为所述极片的数量。而且,本发明还提供一种多类型的磁齿轮,其特征在于,所述多类型的磁齿轮至少包括两个所述磁齿轮,所述磁齿轮中,第一磁齿轮的输出侧转子与第二磁齿轮的输入侧转子直接连接。而且,本发明还提供一种多层型的磁齿轮,其特征在于,所述多层型磁齿轮包括:所述磁齿轮;至少一个内部极片模块,其在所述磁齿轮的内转子的外侧隔开设置,且包括多个极片;以及至少一个中间转子,其设置在所述内部极片模块与所述磁齿轮的极片模块之间。(三)有益效果本发明具有如下优异效果。首先,根据本发明的磁齿轮,具有以下优点:通过将外转子或者内转子、外转子和内转子构成为凸极式转子来减少稀土永磁铁的使用,从而能够降低生产成本。而且,根据本发明的磁齿轮,具有以下优点:即使将转子以凸极式构成,也能够通过调节磁铁和凸极的大小来补偿转矩的减小。而且,根据本发明的磁齿轮,具有以下效果:能够通过限定极片的剖面形状的相关变数α、β、γ,将磁束集中在空隙中,因此能够提高转矩的传递,降低转矩脉动,从而提高动力传递率和可靠性。而且,根据本发明的多类型的磁齿轮,具有以下效果:通过将两个磁齿轮直接连接,以小的体积也能够提供大的转矩比。而且,根据本发明的多类型磁齿轮,具有以下效果:在外转子与内转子之间插入中间转子,从而能够利用较少的磁铁来提供大的转矩比。附图说明图1是示出普通的磁齿轮的图。图2是示出普通的磁齿轮的垂直剖面的图。图3是用于说明本发明的第一实施例的磁齿轮的图。图4是用于说明本发明的第二实施例的磁齿轮的图。图5是用于说明本发明的第三实施例的磁齿轮的图。图6是用于说明本发明的实施例的磁齿轮的极片形状的图。图7至图9是用于说明决定本发明的实施例的磁齿轮的极片形状的变数的图。图10是用于说明本发明的另一实施例的多类型的磁齿轮的图。图11是用于说明本发明的另一实施例的多层型的磁齿轮的图。最佳实施方式在本发明中所使用的术语尽可能选择了当前广泛使用的普通术语,在特定的情况下也存在申请人任意选定的术语,这种情况下应考虑记载或者使用在详细的说明内容部分的含义而理解其含义,而不是仅仅掌握其术语名称。下面,参照在附图中所示出的优选实施例对本发明的技术结构进行详细说明。但是,本发明并不限定于将在此说明的实施例,可通过其他形式来具体实施。整个说明书中的相同的附图标记表示相同的组件。参照附图3,本发明的第一实施例的磁齿轮100包括:外转子110;内转子120,其在所述外转子110的内侧与所述外转子110隔开设置;以及极片模块130,其在所述外转子110与所述内转子120之间分别与所述外转子110和所述内转子120隔开设置。而且,当所述极片模块130处于固定状态时,所述外转子110和所述内转子120相互以反方向旋转,并且从所述外转子110向所述内转子120传递旋转力,或者从所述内转子120向所述外转子110传递旋转力。但是,在所述外转子110和所述内转子120中的一个转子被固定时,所述极片模块130和未被固定的另一个转子旋转的同时可传递动力。在这种情况下,所述极片模块130与旋转的转子的旋转方向相同。而且,在图3中虽示出本发明的磁齿轮100为圆筒旋转型磁齿轮,但还可以制造成圆板旋转型、平板式直线型、圆筒式直线型。(例如,可参照专利文献1的圆板旋转型、平板式直线型、圆筒式直线型的形状。)而且,所述外转子110是其内侧面有相对于旋转轴c以放射状设置的磁铁112和在磁铁112之间形成的凸极(salientpole)的凸极式转子。具体地,所述外转子110包括:圆筒形外侧回转子111;多个磁铁112(以下简称为‘外侧磁铁’),以旋转轴c为中心并以放射状隔开粘贴在所述外侧回转子111的内侧面上,并且具有朝向所述旋转轴c的磁力;以及凸极111a(以下简称为‘外侧凸极’),分别设置在所述外侧磁铁112之间。而且,所述外侧凸极111a是在所述外侧回转子111的内侧面上将铁芯叠层而形成的,因此又称为铁极。而且,在本发明中虽说明了所述外侧凸极111a是在所述外侧回转子111上叠层形成的,但所述外侧凸极111a和所述外侧回转子111可以以一体形式制造。即,本发明的第一实施例的磁齿轮100与现有的磁齿轮10相比,外转子110不具有双极磁铁,而只设置有朝向旋转轴c的方向被磁化的磁铁,因此能够减少永磁铁的使用量,具有制造成本低的优点。而且,所述内转子120包括内侧回转子121和多个磁铁122,所述多个磁铁122形成双极且粘贴在所述内侧回转子121的外侧。而且,所述极片模块130包括多个极片131,所述极片131相对于旋转轴c以放射状相互隔开设置。而且,所述极片131又称为磁极片,其作为磁体,起到从所述外转子110向所述内转子120传递磁束,或者从所述内转子120向所述外转子110传递磁束的作用。而且,虽未示出,所述极片模块130可包括支撑部件,所述支撑部件使所述极片131之间以及极片131与所述转子110、120的磁铁之间保持相互隔开的状态。而且,所述极片131的数量由上述数学式a决定,齿轮比如上述的数学式b所示。而且,所述极片131与所述外转子110之间存在外侧空隙(outerairgap),所述极片131与所述内转子120之间存在内侧空隙(innerairgap),这些空隙110a、120a在磁路中充当抗阻,以使磁束集中。另外,本发明的第一实施例的磁齿轮100与磁铁减少量成比例地减小转矩。这种转矩的减小可通过调节所述外侧磁铁112和所述外侧凸极111a的大小来补偿,具体如以下表1所示,可通过调节所述外侧磁铁112的圆心角θ和所述外侧凸极111a的叠层宽度L来补偿。[表1]具体实施方式参照图4,本发明的第二实施例的磁齿轮100a的内转子110包括:圆筒形内侧回转子121;多个磁铁123(以下简称为‘内侧磁铁’),以旋转轴c为中心并以放射状隔开粘贴在所述内侧回转子121的外侧面,并且具有朝向旋转轴c的反方向的磁力;以及凸极121a(以下简称为‘内侧凸极’),分别设置在所述内侧磁铁123之间。而且,如图4所示,当由两个所述内侧磁铁123构成时,所述内侧磁铁123相对于旋转轴c以彼此相对的方向配置。而且,本发明中虽说明了所述内侧凸极121a叠层形成在所述内侧转子121上,但所述内侧凸极121a和所述内侧回转子121还可以以一体形式制造。即,本发明的第二实施例的磁齿轮100a与现有的磁齿轮10相比,能够减少包括在内转子120中的永磁铁的使用量,因此具有制造成本低的优点。参照图5,本发明的第三实施例的磁齿轮100b与本发明的第一实施例的磁齿轮100和第二实施例的磁齿轮100a相比,所述外转子110和所述内转子120分别由凸极式转子构成。而且,本发明的第三实施例的磁齿轮100b的外转子110与所述第一实施例的磁齿轮100的外转子实质相同,其内转子120与所述第二实施例的磁齿轮100a的内转子实质相同,因此省略其具体说明。即,本发明的第三实施例的磁齿轮100b与本发明的第一实施例及第二实施例的磁齿轮100、100a相比,其具有能够进一步减少永磁铁的使用量的优点。以下表2是比较现有的磁齿轮10和本发明实施例的磁齿轮100、100a、100b的永磁铁面积及牵出转矩(pull-outtorque,外转子的转矩)的表。[表2]永磁铁面积[mm2]牵出转矩[Nm]现有的磁齿轮6283(100%)192.8(100%)本发明的第一实施例4373(69.6%)131.3(68.1%)本发明的第二实施例5051(80.4%)125.7(65.1%)本发明的第三实施例3141(50%)96.3(49.9%)参照表2,本发明的第三实施例的磁齿轮100b的永磁铁的面积最小,但转矩低,本发明的第二实施例的磁齿轮100a的磁铁的面积减小量最少,但其转矩比本发明的第一实施例的磁齿轮100低。因此,本发明的第一实施例的磁齿轮100a的转矩减小量相对于面积减小量最少,因此可以确认适合用作传动装置。而且,本发明的第一实施例的磁齿轮100的内转子的转矩脉动为6.15%,相对来说比较低,而本发明的第二实施例的磁齿轮100a和第三实施例的磁齿轮的内转子的转矩脉动分别为11.95%、56.24%,比较高,因此本发明第一实施例的磁齿轮100的可靠性最高。图6是用于说明本发明的实施例的磁齿轮100、100a、100b的极片131的一个例子的图,本发明的实施例的磁齿轮100、100a、100b的极片131能够制造成可将磁束集中在空隙中的形状。参照图6对所述极片131的形状进行详细的说明,所述极片131具有与旋转轴c并排的杆状形状,其垂直剖面具有第一图形131a和第二图形131b在平面上接合的形状。而且,所述第一图形131a是由曲线第一弧131aa(arc)、第二弧131ab、线131ac及线131ad围绕而形成的平面图形,所述第二弧131ab与所述第一弧131aa的中心c的位置及圆心角θ1相同,其内径d2小于第一弧131aa的内径d1,所述线131ac连接所述第一弧131aa和所述第二弧131ab的各一端,所述线131ad连接所述第一弧131aa和所述第二弧131ab的各另一端。换句话说,所述第二弧131ab的内半径(d2/2)小于所述第一弧131aa的内半径(d1/2),曲率相同且中心c位置与旋转轴c的位置相互一致。而且,优选地,连接所述第一弧131aa和所述第二弧131ab的线131ac、131ad为向所述第一图形131a的中心部凹陷的曲线(以下称‘凹曲线’)。而且,所述第二图形131b是由第三弧131ba、第四弧131bb、线131bd及线131bc围绕而形成的平面图形,所述第三弧131ba与所述第二弧131ab的中心c的位置及内径d2相同,其圆心角θ2大于所述第二弧131ab的圆心角θ1,所述第四弧131bb与所述第三弧131ba的中心c的位置及圆心角θ2的大小相同,其内径d3小于所述第三弧131ba的内径d2,所述线131bd连接所述第三弧131ba和所述第四弧131bb的各一端,所述线131bc连接所述第三弧131ba和所述第四弧131bb的各另一端。换句话说,所述第二弧131ab和所述第三弧131ba的内半径(d2/2)相同,所述第三弧131ba的内半径(d2/2)大于所述第四弧131bb的内半径(d3/2)。而且,优选地,连接所述第三弧131ba和所述第四弧131bb的各端的线131bc、131bd为直线。而且,所述第一图形131a和所述第二图形131b以所述第二弧131ab的二等分位置c1和所述第三弧131ba的二等分位置c1相互重叠的方式在平面上接合,从而形成所述极片131的剖面形状。图7至图9是用于说明决定本发明的实施例的所述极片131形状的变数的图,决定所述极片131形状的变数大致分为三种。首先,参照图7,第一个变数是分别垂直于所述第三弧131ba和所述第四弧131bb的直线的距离α(以下简称为‘第一垂直距离’)。而且,Lpr′为分别垂直于所述第四弧131bb和所述第一弧131aa的直线的距离(以下简称为‘第二垂直距离’),所述第一垂直距离α大于Lpr′的13.5%,而小于Lpr′的23.5%。即,所述第一垂直距离α被设为满足以下数学式1。数学式1[式1]Lpr×0.135≤α≤Lpr×0.235下面,参照图8,第二个变数是所述第四弧131bb的圆心角β。而且,β′(以下简称为‘参考角’)为连接中间置有一个极片131的两个极片131′、131″的第一弧131′aa、131″aa的相对的末端的虚拟弧的圆心角,所述第四弧131bb的圆心角β大于β′的40%,而小于β′的50%。即,如以下数学式2所示,所述第四弧131bb的圆心角β被设为参考角β′的40%至50%的范围内的角度。数学式2[式2]0.4≤Np360×23×β≤0.5]]>在此,Np为所述极片的数量。然后,参照图9,第三个变数是从连接一个凹曲线131ac两端的虚拟线段l1(以下简称为‘第一虚拟线段’)的二等分位置c2至所述一个凹曲线131ac的垂直长度γ(以下简称为‘凹陷长度’)。而且,长度γ′(以下简称为‘参考长度’)为从虚拟线段l2(以下简称为第二虚拟线段)的二等分位置c3到虚拟线段l3(以下简称为第三虚拟线段)的垂直长度,其中,虚拟线段l2为从所述一个凹曲线131ac的所述第一弧131aa侧一端131ac′垂直连接到所述第四弧131bb的虚拟线段,所述虚拟线段l3为连接所述第一弧131aa的二等分位置c4和所述第四弧131bb的二等分位置c5的虚拟线段,所述凹陷长度γ大于所述γ′的30%,而小于所述γ′的40%。即,如以下数学式3所示,所述凹陷长度γ被设为参考长度γ′的30%至40%的范围内的长度。数学式3[式3]0.3≤γ14(Dpi+Dpo)tan(90Np)≤0.4]]>在此,Dpi为所述第四弧131bb的内径d3,Dpo为所述第一弧131aa的内径d1,Np为所述极片131的数量。而且,在数学式3中,分母表示所述参考长度γ′,所述数学式是用于在以圆点c为中心的直角坐标系上,将所述第一虚拟线段l3作为X轴,计算经过c5和c4的直线与经过c3和c6的直线的交点的y轴坐标值的式子。然而,所述参考长度γ′可利用多种方式计算。以下表3是将本发明第一实施例的磁齿轮100的极片131形状与将极片13a制成如现有的磁齿轮100的极片13a一样的普通形状的情况和制成如图6所示的磁束集中型极片131的情况进行比较的表。[表3]通过表3可知,若将极片131制成磁束集中型极片,则转矩会上升。图10是用于说明本发明实施例的多类型的磁齿轮的图。参照图10,本发明的另一实施例的多类型的磁齿轮200为由多个本发明的一个实施例的磁齿轮100直接连接的形状。而且,在图10中虽示出了由两个磁齿轮100、100′直接连接的双磁齿轮型,然而还可由三个以上的磁齿轮直接连接形成。而且,当为双磁齿轮型时,第一磁齿轮100的输出侧110a将与第二磁齿轮110′的输入侧130′a连接。而且,当动力从所述第一磁齿轮100传递至所述第二磁齿轮100′时,则用作减速器,而当动力从所述第二磁齿轮100′传递至所述第一磁齿轮100时,则用作加速器。而且,当所述第一磁齿轮100的内转子130与外转子110的齿轮比为1:10,所述第二磁齿轮100′的内转子130′与外转子110′的齿轮比为1:10时,整个齿轮比成为1:100,转矩比也成为1:100。即,当要将现有的磁齿轮10设计成具有1:100的转矩比时,外转子的极对数应比内转子的极对数多出100倍,因此不可避免大型化的设计,但本发明的多类型的磁齿轮200具有可利用两个磁齿轮来实现小型化且高转矩比的优点。图11是用于说明本发明另一实施例的多层型的磁齿轮的图。参照图11,本发明另一实施例的多层型的磁齿轮300是在本发明的一个实施例的磁齿轮100中包括内部极片模块310和中间转子320而构成。而且,对于所述内部极片模块310和所述中间转子320的数量不做限定,设计人员可根据所需的齿轮比以任意数量构成。只是,所述内部极片模块310和所述中间转子320应成对构成。而且,所述内部极片模块310在所述磁齿轮100的内转子120的外侧上隔开设置,并具有多个内部极片311。而且,所述内部极片311的形状也可与磁束集中型极片的形状相同地,以限定变数α、β、γ的形式设计。而且,所述中间转子320在所述内部极片模块310与所述极片模块130之间分别与所述内部极片模块310和所述极片模块130隔开设置。即,本发明的另一实施例的多层型的磁齿轮300具有以下结构:当所述内转子120旋转时,所述内部极片模块311向所述中间转子320传递磁束,而所述中间转子320的磁束是通过所述极片模块130向所述外转子110传递而旋转。而且,虽在图11中示出所述中间转子320是磁铁以双极形式粘贴在内侧面和外侧面的转子,但还可以是将磁铁和凸极交替叠层的凸极式转子,这时可减少永磁铁的使用量。而且,当驱动力从所述内转子120传递至所述外转子110时,则用作减速器,而当驱动力从所述外转子110传递至所述内转子120时,则用作加速器。因此,根据本发明的多层型的磁齿轮300,由其外转子110、中间转子320及内转子120分担现有的磁齿轮10所要实现的齿轮比,因此与现有的磁齿轮10相比,具有减少了磁铁的极数比的同时能够实现所需的齿轮比的优点。如上所述,本发明通过优选实施例进行了说明,但并不限定于所述实施例,本领域所属技术人员在不脱离本发明的范围内可进行多种变更和修改。工业实用性本发明的磁齿轮可适用于车辆、机床、工厂设施等需要非接触式旋转动力的各种领域。当前第1页1 2 3