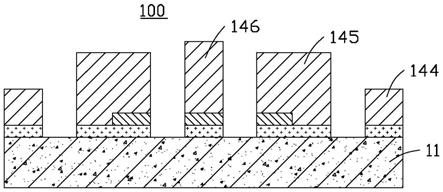
1.本发明涉及一种电路板及其制作方法。
背景技术:2.近年来,电子产品被广泛应用在日常工作和生活中,其中,摄像头更是起到越来越重要的作用,对摄像头性能的要求也越来越高。为实现这种需求,摄像头内部的各种零件需要相应的优化。目前摄像头采用的微型马达由于采用漆包铜丝做线圈,需进行打件到电路板上,再绕折呈方形结构以适配摄像头。漆包铜线绝缘层一般较厚,不利于实现微型化,线距大,导致线圈层数多产品厚,一般线圈的厚度》0.4mm,且生产流程需电路板的制作及线圈的制作打件,流程较长,生产效率较低。
技术实现要素:3.有鉴于此,有必要提供一种能解决上述问题的电路板的制作方法。
4.还提供一种上述制作方法制作的电路板。
5.本技术的实施例提供一种电路板的制作方法,包括以下步骤:
6.在基板的基层表面的第一金属层及种子层上进行压膜,所述种子层位于所述第一金属层表面;
7.在所述基板上进行曝光、显影及电镀,分别露出所述第一金属层、部分所述第一金属层与所述种子层及所述种子层,并在其上分别形成信号层、连接柱及线圈;
8.进行去膜;
9.将所述信号层与所述连接柱之间的所述第一金属层及所述连接柱与所述线圈之间的所述种子层蚀刻,暴露出底部的所述基层,使所述信号层形成第一线路层,使所述连接柱形成第二线路层,使所述线圈形成第三线路层。
10.进一步地,在本技术的一些实施例中,在基板的第一金属层及种子层上进行压膜的步骤之前还包括,对所述基板进行压膜,所述基板包括所述基层、形成于所述基层表面的所述第一金属层及形成于所述第一金属层表面的第二金属层;
11.对所述基板进行曝光、显影及蚀刻制程,将所述第二金属层蚀刻形成所述种子层;
12.进行去膜。
13.进一步地,在本技术的一些实施例中,将所述信号层与所述连接柱之间的所述第一金属层及所述连接柱与所述线圈之间的所述种子层蚀刻的步骤包括,对所述连接柱与所述线圈之间的所述种子层进行蚀刻制程,暴露出所述种子层底部的所述第一金属层;对所述基层上暴露的所述第一金属层进行蚀刻制程,暴露出底部的所述基层。
14.进一步地,在本技术的一些实施例中,在基板的第一金属层及种子层上进行压膜的步骤之前还包括,对所述基板进行压膜;
15.对所述基板进行曝光、显影及喷涂,在所述基板上形成所述第一金属层;
16.进行去膜,在所述第一金属层中形成凹槽并对所述基板再进行压膜;
17.对所述基板进行曝光、显影及喷涂,在所述凹槽中形成所述种子层;
18.进行去膜。
19.进一步地,在本技术的一些实施例中,所述第一金属层的方阻大于所述种子层的方阻。
20.本技术的实施例还提供一种电路板,包括:
21.一基板,所述基板包括基层及形成于其上的第一金属层及形成于所述第一金属层上的种子层;
22.位于所述基板表面的第一线路层,所述第一线路层包括所述第一金属层、形成于所述第一金属层表面的信号层;
23.与所述第一线路层连接的第二线路层,所述第二线路层包括所述第一金属层、所述种子层及形成于所述第一金属层与所述种子层表面的连接柱;及
24.与所述第二线路层连接的第三线路层,所述第三线路层包括所述种子层及形成于所述种子层表面的线圈。
25.进一步地,在本技术的一些实施例中,所述种子层形成于所述第一金属层表面。
26.进一步地,在本技术的一些实施例中,所述第一金属层中有凹槽,所述凹槽中形成所述种子层。
27.进一步地,在本技术的一些实施例中,所述第一金属层的方阻大于所述种子层的方阻。
28.进一步地,在本技术的一些实施例中,所述电路板能够在所述第一线路层处绕折,形成包括四个所述线圈的矩形结构,四个所述线圈两两相对。
29.本发明提供的电路板,通过电路板的制作工艺将线圈直接通过电镀形成在电路板上,可实现线圈的小型化,且线圈及电路板基板集成一体成型,无需线圈的单独制作及打件,生产效率提高。
附图说明
30.图1是本发明第一实施方式的基板的剖视示意图。
31.图2是对图1所示的基板进行压膜的剖视示意图。
32.图3是对图2所示的基板进行曝光、显影及蚀刻的示意图。
33.图4是对图3所示基板进行去膜的示意图。
34.图5是对图4所示的基板进行压膜的示意图。
35.图6是对图5所示基板进行曝光、显影及电镀的剖视示意图。
36.图7是对图6所示基板进行去膜的剖视示意图。
37.图8是对图7所示基板上的种子层进行蚀刻的剖视示意图。
38.图9是对图8所示基板上的第一金属层进行蚀刻的剖视示意图。
39.图10是本发明第一实施方式的线圈的示意图。
40.图11是本发明第一实施方式的电路板的应用示意图。
41.图12是本发明第二实施方式的基板的剖视示意图。
42.图13是对图12所示基板进行曝光、显影及喷涂制程的剖视示意图。
43.图14是对图13所示基板进行去膜制程并再进行压膜的剖视示意图。
44.图15是对图14所示基板进行曝光、显影及喷涂制程的剖视示意图。
45.图16是对图15所示基板进行去膜的剖视示意图。
46.图17是对图16所示基板进行压膜的剖视示意图。
47.图18是对图17所示基板进行曝光、显影及电镀的剖视示意图。
48.图19是对图18所示基板进行去膜的剖视示意图。
49.图20是对图19所示基板上的第一金属层及种子层进行蚀刻的剖视示意图。
50.主要元件符号说明
51.电路板
ꢀꢀꢀꢀꢀꢀꢀꢀꢀꢀꢀꢀꢀꢀꢀꢀꢀꢀꢀꢀꢀꢀꢀꢀ
100、100a
52.基板
ꢀꢀꢀꢀꢀꢀꢀꢀꢀꢀꢀꢀꢀꢀꢀꢀꢀꢀꢀꢀꢀꢀꢀꢀꢀꢀ
10、10a
53.基层
ꢀꢀꢀꢀꢀꢀꢀꢀꢀꢀꢀꢀꢀꢀꢀꢀꢀꢀꢀꢀꢀꢀꢀꢀꢀꢀ
11、11a
54.第一金属层
ꢀꢀꢀꢀꢀꢀꢀꢀꢀꢀꢀꢀꢀꢀꢀꢀꢀꢀꢀꢀ
12、12a
55.凹槽
ꢀꢀꢀꢀꢀꢀꢀꢀꢀꢀꢀꢀꢀꢀꢀꢀꢀꢀꢀꢀꢀꢀꢀꢀꢀꢀ
121
56.第二金属层
ꢀꢀꢀꢀꢀꢀꢀꢀꢀꢀꢀꢀꢀꢀꢀꢀꢀꢀꢀꢀ
13
57.种子层
ꢀꢀꢀꢀꢀꢀꢀꢀꢀꢀꢀꢀꢀꢀꢀꢀꢀꢀꢀꢀꢀꢀꢀꢀ
131、13a
58.信号层
ꢀꢀꢀꢀꢀꢀꢀꢀꢀꢀꢀꢀꢀꢀꢀꢀꢀꢀꢀꢀꢀꢀꢀꢀ
141、141a
59.连接柱
ꢀꢀꢀꢀꢀꢀꢀꢀꢀꢀꢀꢀꢀꢀꢀꢀꢀꢀꢀꢀꢀꢀꢀꢀ
142、142a
60.线圈
ꢀꢀꢀꢀꢀꢀꢀꢀꢀꢀꢀꢀꢀꢀꢀꢀꢀꢀꢀꢀꢀꢀꢀꢀꢀꢀ
143、143a
61.第一线路层
ꢀꢀꢀꢀꢀꢀꢀꢀꢀꢀꢀꢀꢀꢀꢀꢀꢀꢀꢀꢀ
144、144a
62.第二线路层
ꢀꢀꢀꢀꢀꢀꢀꢀꢀꢀꢀꢀꢀꢀꢀꢀꢀꢀꢀꢀ
145、145a
63.第三线路层
ꢀꢀꢀꢀꢀꢀꢀꢀꢀꢀꢀꢀꢀꢀꢀꢀꢀꢀꢀꢀ
146、146a
64.干膜
ꢀꢀꢀꢀꢀꢀꢀꢀꢀꢀꢀꢀꢀꢀꢀꢀꢀꢀꢀꢀ
20、30、20a、30a、40
65.如下具体实施方式将结合上述附图进一步说明本发明。
具体实施方式
66.下面将结合本发明实施例中的附图,对本发明实施例中的技术方案进行清楚、完整地描述,显然,所描述的实施例仅仅是本发明一部分实施例,而不是全部的实施例。基于本发明中的实施例,本领域普通技术人员在没有做出创造性劳动前提下所获得的所有其他实施例,都属于本发明保护的范围。
67.除非另有定义,本文所使用的所有的技术和科学术语与属于本发明的技术领域的技术人员通常理解的含义相同。本文中在本发明的说明书中所使用的术语只是为了描述具体的实施例的目的,不是旨在于限制本发明。
68.下面结合附图,对本发明的一些实施方式作详细说明。在不冲突的情况下,下述的实施例及实施例中的特征可以相互组合。
69.本技术的实施例提供一种电路板的制作方法,包括以下步骤:
70.在基板的基层表面的第一金属层及种子层上进行压膜,所述种子层位于所述第一金属层表面;
71.在所述基板上进行曝光、显影及电镀,分别露出所述第一金属层、部分所述第一金属层与所述种子层及所述种子层,并在其上分别形成信号层、连接柱及线圈;
72.进行去膜;
73.将所述信号层与所述连接柱之间的所述第一金属层及所述连接柱与所述线圈之间的所述种子层蚀刻,暴露出底部的所述基层,使所述信号层形成第一线路层,使所述连接柱形成第二线路层,使所述线圈形成第三线路层。
74.本技术的实施例还提供一种电路板,包括:
75.一基板,所述基板包括基层及形成于其上的第一金属层及形成于所述第一金属层上的种子层;
76.位于所述基板表面的第一线路层,所述第一线路层包括所述第一金属层、形成于所述第一金属层表面的信号层;
77.与所述第一线路层连接的第二线路层,所述第二线路层包括所述第一金属层、所述种子层及形成于所述第一金属层与所述种子层表面的连接柱;及
78.与所述第二线路层连接的第三线路层,所述第三线路层包括所述种子层及形成于所述种子层表面的线圈。
79.上述电路板,通过电路板的制作工艺将线圈直接通过电镀形成在电路板上,可实现线圈的小型化,且线圈及电路板基板集成一体成型,无需线圈的单独制作及打件,生产效率提高。
80.下面结合附图,对本技术的实施例作进一步的说明。
81.请参阅图1至图9,本发明的第一实施方式中电路板100的制作方法,其包括以下步骤:
82.步骤s101,请参阅图1,提供一基板10。所述基板10包括一可挠性的绝缘的基层11、形成于所述基层11表面的第一金属层12及形成于所述第一金属层12表面的第二金属层13。
83.所述基层11的材质可选自聚酰亚胺(polyimide,pi)、液晶聚合物(liquid crystal polymer,lcp)、聚对苯二甲酸乙二醇酯(polyethylene terephthalate,pet)以及聚萘二甲酸乙二醇酯(polyethylene naphthalate,pen)等材料中的一种。
84.所述第一金属层12与第二金属层13的材质不同,所述第一金属层12的方阻较大,所述第二金属层13的方阻较小。
85.在一些实施例中,所述第一金属层12的材质为ni-p或nicr氧化物等的组合,可通过p、o的掺杂含量以及金属层的厚度控制所述第一金属层12的方阻。所述第二金属层13的材质可以是cu。由于第一金属层12与第二金属层13的方阻存在差异,通过控制阶梯电流的大小,可实现在其上电镀效率的不同,从而实现电镀层厚度的差异。
86.在一些实施例中,所述第一金属层12的厚度小于0.1μm。所述第二金属层13的厚度在0.1μm~4μm。
87.步骤s102,请参阅图2,对基板10进行压膜,在所述第一金属层12上覆盖一层干膜20。
88.步骤s103,请参阅图3,对基板10进行曝光、显影及蚀刻制程,将基板10的所述第二金属层13蚀刻形成种子层131。
89.具体地,通过曝光、显影将未曝光的干膜20去掉,露出部分第二金属层13,随后通过蚀刻,将干膜20暴露的所述第二金属层13蚀刻掉,在曝光的干膜20下形成种子层131。
90.步骤s104,请参阅图4,对基板10进行去膜制程,将所述干膜20去除。
91.步骤s105,请参阅图5,对基板10进行压膜,在所述第一金属层12及种子层131上覆
盖一层干膜30。
92.步骤s106,请参阅图6,对基板10进行曝光、显影及电镀制程,去掉未曝光的干膜30,分别露出第一金属层12、部分第一金属层12与种子层131及种子层131,并在其上分别形成信号层141、连接柱142及线圈143。所述连接柱142位于所述信号层141与所述线圈143之间。
93.具体地,由于第一金属层12和种子层131的方阻存在差异,通过控制阶梯电流大小可实现第一金属层12和种子层131上不同的电镀效率(可采用先小电流后大电流的阶梯电镀方案),从而使得第一金属层12上的信号层141铜厚最薄,种子层131上的线圈143铜厚最厚,部分第一金属层12与种子层131上的连接柱142铜厚则适中。
94.步骤s107,请参阅图7,对基板10进行去膜制程,将所述干膜30去除,使得信号层141与连接柱142之间的第一金属层12暴露,连接柱142与线圈143之间的种子层131暴露。
95.步骤s108,请参阅图8,对连接柱142与线圈143之间的种子层131进行蚀刻制程,暴露出种子层131底部的第一金属层12。
96.步骤s109,请参阅图9,对基层11上暴露的第一金属层12进行蚀刻制程,暴露出底部的基层11,形成电路板100。
97.具体地,通过蚀刻,使信号层141与第一金属层12形成第一线路层144,使连接柱142、种子层131与第一金属层12形成第二线路层145,使线圈143、种子层131与第一金属层12形成第三线路层146。其中,第三线路层146为线圈功能区,当电路板100用于微型马达中时,所述第三线路层146在通电后产生磁场,以此来实现驱动。第二线路层145可以是用于连接第三线路层146与电源之间的连接线。第一线路层144可以是供电源和信号走线的线路层。
98.具体地,请参阅图10,由于采用电路板工艺制得线圈143,因此线圈143的线宽及线距可设计的更细。具体地,线圈143形成的第三线路层146中线路的线宽l≤30μm,线距s≤20μm,所述线圈143的厚度大于50μm。产品总厚度可小于等于0.3mm。
99.可以理解的,在一些实施例中,所述电路板100还可设计成双面板或多层板。
100.在一些实施例中,步骤s108和s109还可以合并,可在一次蚀刻中将信号层141与连接柱142之间的第一金属层12,连接柱142与线圈143之间的种子层131及第一金属层12蚀刻掉。
101.请参阅图9,本发明的第一实施方式还提供一种电路板100,其包括一基板10、位于基板10表面的第一线路层144、与第一线路层144连接的第二线路层145及与第二线路层145连接的第三线路层146。
102.所述基板10为一可挠性的绝缘的基层11。
103.所述基层11的材质可选自聚酰亚胺(polyimide,pi)、液晶聚合物(liquid crystal polymer,lcp)、聚对苯二甲酸乙二醇酯(polyethylene terephthalate,pet)以及聚萘二甲酸乙二醇酯(polyethylene naphthalate,pen)等材料中的一种。
104.所述第一线路层144包括形成于所述基层11表面的第一金属层12、形成于第一金属层12表面的信号层141。
105.所述第二线路层145包括形成于所述基层11表面的第一金属层12、形成于部分第一金属层12表面的种子层131及形成于第一金属层12与种子层131表面的连接柱142。
106.所述第三线路层146包括形成于所述基层11表面的第一金属层12、形成于第一金属层12表面的种子层131及形成于种子层131表面的线圈143。
107.所述线圈143的数量及匝数均可根据实际的驱动需求进行相应的设置。
108.所述第一线路层144的信号层141厚度小于所述第二线路层145的连接柱142的厚度,所述第二线路层145的连接柱142厚度小于所述第三线路层146中的线圈143的厚度。
109.所述线圈143的厚度大于50μm。
110.所述第一金属层12与种子层131的材质不同,所述第一金属层12的方阻较大,所述种子层131的方阻较小。
111.在一些实施例中,所述第一金属层12的材质为ni-p或nicr氧化物等的组合,可通过p、o的掺杂含量以及金属层的厚度控制所述第一金属层12的方阻。所述种子层131的材质可以是cu。
112.其中,第一线路层144可以是供电源和信号走线的线路层。所述第三线路层146为线圈功能区,第二线路层145可以是用于连接第三线路层146与电源之间的连接线。
113.参阅图11,电路板100可在第一线路层144处进行绕折,形成包括四个所述线圈功能区的矩形结构,四个所述第三线路层146的线圈143两两相对,从而形成用于驱动的磁场,得到的产品可应用于微型马达,如摄像头中。由于其线圈及电路板基板集成一体成型,使其更适于制作微型产品,且效率较高。
114.请参阅图12至图20,本发明的第二实施方式中电路板100a的制作方法,其包括以下步骤:
115.步骤s201,请参阅图12,提供一基板10a,并在所述基板10a覆盖一层干膜20a。所述基板10a包括一可挠性的绝缘的基层11a。
116.所述基层11a的材质可选自聚酰亚胺(polyimide,pi)、液晶聚合物(liquid crystal polymer,lcp)、聚对苯二甲酸乙二醇酯(polyethylene terephthalate,pet)以及聚萘二甲酸乙二醇酯(polyethylene naphthalate,pen)等材料中的一种。
117.步骤s202,请参阅图13,对基板10a进行曝光、显影及喷涂制程,在基层11a上形成第一金属层12a。
118.具体地,通过曝光、显影将未曝光的干膜20a去掉,露出基层11a,随后通过喷涂制程,在干膜20a暴露的基层11a上形成第一金属层12a。所述干膜20a外侧同样形成第一金属层12a。
119.形成所述第一金属层12a的方法不局限于喷涂方法,在一些实施例中,所述第一金属层12a也可通过涂层(coating)、磁控溅射、化镀等其他方式形成。
120.步骤s203,请参阅图14,对基板10a进行去膜制程,将所述干膜20a去除,在所述第一金属层12a中形成凹槽121,然后对基板10a再进行压膜,在所述第一金属层12a及基层11a上覆盖一层干膜30a。
121.步骤s204,请参阅图15,对基板10a进行曝光、显影及喷涂制程,在所述凹槽121中形成种子层13a。
122.具体地,通过曝光、显影将未曝光的干膜30a去掉,露出凹槽121,随后通过喷涂制程,在干膜30a暴露的凹槽121中形成种子层13a。
123.形成所述种子层13a的方法不局限于喷涂方法,在一些实施例中,所述种子层13a
也可通过涂层(coating)、磁控溅射、化镀等其他方式形成。
124.所述第一金属层12a与种子层13a的材质不同,所述第一金属层12a的方阻较大,所述种子层13a的方阻较小。
125.在一些实施例中,所述第一金属层12a的材质为ni-p或nicr氧化物等的组合,可通过p、o的掺杂含量以及金属层的厚度控制所述第一金属层12a的方阻。所述种子层13a的材质可以是cu。由于第一金属层12a与种子层13a的方阻存在差异,通过控制阶梯电流的大小,可实现在其上电镀效率的不同,从而实现电镀层厚度的差异。
126.在一些实施例中,所述第一金属层12a与种子层13a的厚度大致相同。
127.步骤s205,请参阅图16,对基板10a进行去膜制程,将所述干膜30a去除。
128.步骤s206,请参阅图17,对基板10a进行压膜,在所述第一金属层12a及种子层13a上覆盖一层干膜40。
129.步骤s207,请参阅图18,对基板10a进行曝光、显影及电镀制程,去掉未曝光的干膜40,分别露出第一金属层12a、部分第一金属层12a与种子层13a及种子层13a,并在其上分别形成信号层141a、连接柱142a及线圈143a。所述连接柱142a位于所述信号层141a与所述线圈143a之间。
130.具体地,由于第一金属层12a和种子层13a的方阻存在差异,通过控制阶梯电流大小可实现第一金属层12a和种子层13a上不同的电镀效率,从而使得第一金属层12a上的信号层141a铜厚最薄,种子层13a上的线圈143a铜厚最厚,部分第一金属层12a与种子层13a上的连接柱142a铜厚则适中。
131.步骤s208,请参阅图19,对基板10a进行去膜制程,将所述干膜40去除,使得信号层141a与连接柱142a之间的第一金属层12a暴露,连接柱142a与线圈143a之间的种子层13a暴露。
132.步骤s209,请参阅图20,对信号层141a与连接柱142a之间的第一金属层12a、连接柱142a与线圈143a之间的种子层13a进行蚀刻制程,暴露出第一金属层12a及种子层13a底部的基层11a,形成电路板100a。
133.具体地,通过蚀刻,使信号层141a与第一金属层12a形成第一线路层144a,使连接柱142a、种子层13a与第一金属层12a形成第二线路层145a,使线圈143a及种子层13a形成第三线路层146a。其中,第三线路层146a为线圈功能区。第二线路层145a可以是用于连接第三线路层146a与电源之间的连接线。第一线路层144a可以是供电源和信号走线的线路层。
134.可以理解的,在一些实施例中,所述电路板100a还可设计成双面板或多层板。
135.请参阅图20,本发明的第二实施方式还提供一种电路板100a,其包括一基板10a、位于基板10a表面的第一线路层144a、与第一线路层144a连接的第二线路层145a及与第二线路层145a连接的第三线路层146a。
136.所述基板10a为一可挠性的绝缘的基层11a。
137.所述基层11a的材质可选自聚酰亚胺(polyimide,pi)、液晶聚合物(liquid crystal polymer,lcp)、聚对苯二甲酸乙二醇酯(polyethylene terephthalate,pet)以及聚萘二甲酸乙二醇酯(polyethylene naphthalate,pen)等材料中的一种。
138.所述第一线路层144a包括形成于所述基层11a表面的第一金属层12a、形成于第一金属层12a表面的信号层141a。
139.所述第二线路层145a包括形成于所述基层11a表面的第一金属层12a及种子层13a、形成于第一金属层12a与种子层13a表面的连接柱142a。
140.所述第三线路层146a包括形成于所述基层11a表面的种子层13a及形成于种子层13a表面的线圈143a。
141.所述第一线路层144a的信号层141a厚度小于所述第二线路层145a的连接柱142a的厚度,所述第二线路层145a的连接柱142a厚度小于所述第三线路层146a中的线圈143a的厚度。
142.所述线圈143a的厚度大于50μm。
143.所述第一金属层12a与种子层13a的材质不同,所述第一金属层12a的方阻较大,所述种子层13a的方阻较小。
144.在一些实施例中,所述第一金属层12a的材质为ni-p或nicr氧化物等的组合,可通过p、o的掺杂含量以及金属层的厚度控制所述第一金属层12a的方阻。所述种子层13a的材质可以是cu。
145.其中,第一线路层144a可以是供电源和信号走线的线路层。所述第三线路层146a为线圈功能区,第二线路层145a可以是用于连接第三线路层146a与电源之间的连接线。
146.本发明提供的电路板100,通过电路板的制作工艺将线圈直接通过电镀形成在电路板上,可实现线圈的小型化,且线圈及电路板基板集成一体成型,无需线圈的单独制作及打件,生产效率提高。
147.以上所述,仅是本发明的较佳实施方式而已,并非对本发明任何形式上的限制,虽然本发明已是较佳实施方式揭露如上,并非用以限定本发明,任何熟悉本专业的技术人员,在不脱离本发明技术方案范围内,当可利用上述揭示的技术内容做出些许更动或修饰为等同变化的等效实施方式,但凡是未脱离本发明技术方案内容,依据本发明的技术实质对以上实施方式所做的任何简单修改、等同变化与修饰,均仍属于本发明技术方案的范围内。