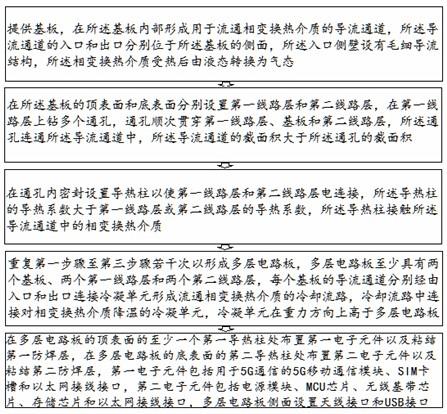
用于5g终端网卡的多层电路板制备方法及其5g网卡
技术领域
1.本发明涉及5g通信电路板技术领域,特别是一种用于5g终端网卡的多层电路板制备方法及其5g网卡。
背景技术:2.第五代移动通信技术(5g)具有更高的速率、更宽的带宽,其电子元件的功能越来越多,封装体积越来越小,表面贴装技术使电子元件的安装密度增大,有效散热面积减小,处理能力却越来越强,5g网卡在工作过程中会产生热量,热量积累容易导致5g网卡烧毁,这就要求电路板具有较高的导热性以及散热能力,另外,5g网卡需要高速多层板以支持更高的速率、更宽的带宽。
3.pcb板材是覆铜/环氧玻璃布基材或酚醛树脂玻璃布基材,这些基材虽然具有优良的电气性能和加工性能,但散热性差,一般采用从元件的表面向周围空气中散热,电路板零件常用散热方式向外辐射和周围空气流动,也有带有其它方式的,比如水冷,风扇等等。现有技术中,热接面添加到pcb的一面来改善散热,例如大的重铜块,这阻止了使用板的特定面来增加组件以增加pcb的复杂性和功能性,从而限制了5g网卡的设计和使用。而且,铜和类似的金属块是重的,这对于对有效载荷敏感的操作可能是不希望的,并且它们在粗糙的运输或其它使用条件下可能会发生脱离,从而阻止了多余热量的有效输送。现有技术通过与产生过热的部件热连通的散热器,使得热量不通过pcb基板被传送走。但这仅从pcb的单面进行散热,例如风扇、水冷设备,需要使用越来越大和越来越重的散热器,以使与过量热源热连通的表面积最大化,从而促进更好的散热。由于pcb基板的导热性差和用于安装散热器的可用空间有限,仍然难以散发多余的热量。
4.随着5g的到来,进入了小型化、高密度安装、高发热化组装时代,由于表面安装元件的大量使用,5g电子元器件产生的热量大量地传给pcb板,pcb基板的低热导率值会使从电子系统中移除多余的热量变得相当困难。因此,目前现有技术中从pcb去除多余热量的方法越来越不那么有效,从而妨碍了5g网卡的使用寿命及稳定性。
5.在背景技术部分中公开的上述信息仅仅用于增强对本发明背景的理解,因此可能包含不构成在本国中本领域普通技术人员公知的现有技术的信息。
技术实现要素:6.本发明人等为了达成上述目的而进行了深入研究,具体而言,一种用于5g终端网卡的多层电路板制备方法步骤包括:第一步骤,提供基板,在所述基板内部形成用于流通相变换热介质的导流通道,所述导流通道的入口和出口分别位于所述基板的侧面,所述入口侧壁设有毛细导流结构,所述相变换热介质受热后由液态转换为气态,第二步骤,在所述基板的顶表面和底表面分别设置第一线路层和第二线路层,在第一线路层上钻多个通孔,通孔顺次贯穿第一线路层、基板和第二线路层,所述通孔连通所
述导流通道中,所述导流通道的截面积大于所述通孔的截面积,第三步骤,在通孔内密封设置导热柱以使第一线路层和第二线路层电连接,所述导热柱的导热系数大于第一线路层或第二线路层的导热系数,所述导热柱接触所述导流通道中的相变换热介质,第四步骤,重复第一步骤至第三步骤若干次以形成多层电路板,所述多层电路板至少具有两个基板、两个第一线路层和两个第二线路层,每个基板的所述导流通道分别经由入口和出口连接冷凝单元形成流通相变换热介质的冷却流路,所述冷却流路中连接对相变换热介质降温的冷凝单元,所述冷凝单元在重力方向上高于所述多层电路板,第五步骤,在多层电路板的顶表面的至少一个第一导热柱处布置第一电子元件以及粘结第一防焊层,在多层电路板的底表面的不同于第一导热柱的第二导热柱处布置第二电子元件以及粘结第二防焊层,所述第一电子元件包括用于5g通信的5g移动通信模块、sim卡槽和以太网接线接口,第二电子元件包括电源模块、mcu芯片、无线基带芯片、存储芯片和以太网接线接口,所述多层电路板侧面设置天线接口和usb接口。
7.所述的用于5g终端网卡的多层电路板制备方法中,第一步骤中,提供下半基板,在所述下半基板上表面形成用于流通相变换热介质的第一导流槽,第一导流槽的入口的内壁上设有毛细导流结构,提供上半基板,在所述上半基板的下表面形成用于流通相变换热介质的第二导流槽,第二导流槽的入口的内壁上设有毛细导流结构,层合第一基板和第二基板,其中,所述第一导流槽和第二导流槽重合以构成导流通道。
8.所述的用于5g终端网卡的多层电路板制备方法中,所述第一导流槽上铺设导热管,所述第一导流槽和第二导流槽重合以包裹所述导热管,所述导热管构成用于流通相变换热介质的导流通道,所述导热管于毛细导流结构处连接入口。
9.所述的用于5g终端网卡的多层电路板制备方法中,第二步骤中,在第一线路层粘贴绝缘层,脉冲二氧化碳激光烧蚀掉待钻通孔处的绝缘层以露出第一线路层的铜箔,所述铜箔电镀形成第一金属增强层,同样地,第二线路层粘贴绝缘层,脉冲二氧化碳激光烧蚀掉待钻通孔处的绝缘层以露出第二线路层的铜箔,然后电镀形成第二金属增强层,脉冲二氧化碳激光在锡层的位置钻孔以顺次贯穿第一金属增强层、第一线路层、基板、第二线路层和第二金属增强层,最后经由乙醇清洗通孔。
10.所述的用于5g终端网卡的多层电路板制备方法中,第三步骤,所述导热柱为实心银柱,在通孔内热封所述实心银柱以使所述实心银柱与第一线路层和第二线路层电连接,所述实心银柱分别与第一线路层及其第一金属增强层和第二线路层及其第二金属增强层密封。
11.所述的用于5g终端网卡的多层电路板制备方法中,每个基板的所述导流通道的入口经由第一总管连接冷凝单元,每个基板的所述导流通道的出口经由第二总管连接冷凝单元。
12.所述的用于5g终端网卡的多层电路板制备方法中,冷凝单元为蛇形冷凝管,所述蛇形冷凝管设有散热翅片。
13.所述的用于5g终端网卡的多层电路板制备方法中,多层电路板中,偶数层或奇数层的基板设有导流通道。
14.所述的用于5g终端网卡的多层电路板制备方法中,基板包括有机绝缘介质层和半固化片层,所述导流通道为均匀分布于基板内部的交错的槽壁形成的s形通道。
15.根据本发明的另一方面,一种5g网卡包括多层电路板,所述多层电路板经由所述的用于5g终端网卡的多层电路板制备方法制成。
16.发明的效果本发明的用于5g终端网卡的多层电路板制备方法通过在基板内部设置用于流通相变换热介质的导流通道,不用占据多层电路板的上下表面宝贵的使用空间,进一步把所述导流通道的入口和出口分别位于所述基板的侧面,进一步有利于高密度安装,所述入口侧壁设有毛细导流结构,增强了液态的相变换热介质流入导流通道的流动性,在第一线路层上钻多个通孔,通孔顺次贯穿第一线路层、基板和第二线路层,所述通孔连通所述导流通道中,在通孔内密封设置导热柱以使第一线路层和第二线路层电连接,所述导热柱接触所述导流通道中的相变换热介质,这将上下表面的电子元件产生的热量传递到相变换热介质中以被迅速冷却,所述导流通道的截面积大于所述通孔的截面积,保障了导热柱浸没在相变换热介质中,所述导热柱的导热系数大于第一线路层或第二线路层的导热系数,提高了导热效率,每个基板的所述导流通道分别经由入口和出口连接冷凝单元形成流通相变换热介质的冷却流路,将吸收了热量的相变换热介质经由冷却流路流出,以及新的相变换热介质经由入口重新进入导流通道,冷凝单元把气态的相变换热介质降温转换成液态相变换热介质,所述冷凝单元在重力方向上高于所述多层电路板,有利于气态的相变换热介质升入冷凝单元进行降温,本公开可以同时冷却上下表面的第一电子元件和第二电子元件,显著提高了5g通信的多层电路板的散热效果,且避免妨碍电路板的上下表面空间位置,不会限制pcb的设计和使用,本公开不会增加多层电路板的重量,对有效载荷敏感的操作不会造成任何影响,提升了多层电路板的应用性,另外,可以理解的,多层电路板的各个基板的导流通道共用一个冷却流路,进一步提高了散热效能。
17.上述说明仅是本发明技术方案的概述,为了能够使得本发明的技术手段更加清楚明白,达到本领域技术人员可依照说明书的内容予以实施的程度,并且为了能够让本发明的上述和其它目的、特征和优点能够更明显易懂,下面以本发明的具体实施方式进行举例说明。
附图说明
18.[图1] 示出了本发明的用于5g终端网卡的多层电路板制备方法的步骤示意图。
[0019]
[图2] 示出了本发明的用于5g通信的多层电路板一个实施例的结构示意图。
[0020]
[图3] 示出了本发明的用于5g通信的多层电路板的导流通道的一个实施例的结构示意图。
[0021]
[图4] 示出了本发明的用于5g通信的多层电路板的冷凝单元的一个实施例的结构示意图。
具体实施方式
[0022]
下面将参照附图更详细地描述本发明的具体实施例。虽然附图中显示了本发明的具体实施例,然而应当理解,可以以各种形式实现本发明而不应被这里阐述的实施例所限
制。相反,提供这些实施例是为了能够更透彻地理解本发明,并且能够将本发明的范围完整的传达给本领域的技术人员。
[0023]
需要说明的是,在说明书及权利要求当中使用了某些词汇来指称特定组件。本领域技术人员应可以理解,技术人员可能会用不同名词来称呼同一个组件。本说明书及权利要求并不以名词的差异来作为区分组件的方式,而是以组件在功能上的差异来作为区分的准则。如在通篇说明书及权利要求当中所提及的“包含”或“包括”为一开放式用语,故应解释成“包含但不限定于”。说明书后续描述为实施本发明的较佳实施方式,然所述描述乃以说明书的一般原则为目的,并非用以限定本发明的范围。本发明的保护范围当视所附权利要求所界定者为准。
[0024]
为便于对本发明实施例的理解,下面将结合附图以几个具体实施例为例做进一步的解释说明,且各个附图并不构成对本发明实施例的限定。
[0025]
具体而言,如图1所示的本发明的用于5g终端网卡的多层电路板制备方法的步骤示意图,一种用于5g终端网卡的多层电路板制备方法步骤包括:第一步骤,提供基板1,在所述基板1内部形成用于流通相变换热介质的导流通道2,所述导流通道2的入口11和出口12分别位于所述基板1的侧面,所述入口11侧壁设有毛细导流结构,所述相变换热介质受热后由液态转换为气态,可选地,所述相变换热介质包括一氯二氟甲烷、三氟甲烷(ch2f2)、四氟乙烷(cf3ch2f)、五氟丙烷(chf2cf2ch2f)、八氟环丁烷(cyclo
‑
c4f8)、二氯四氟乙烷(cclf2cclf2)、四氟一氯乙烷(chclfcf3)、五氟乙烷(chf2cf3)、反式一氯三氟丙烯(cf3ch=chcl)、异丁烷(ch(ch3)3)及其组合。
[0026]
第二步骤,在所述基板1的顶表面和底表面分别设置第一线路层3和第二线路层4,在第一线路层3上钻多个通孔5,通孔5顺次贯穿第一线路层3、基板1和第二线路层4,所述通孔5连通所述导流通道2中,所述导流通道2的截面积大于所述通孔5的截面积,第三步骤,在通孔5内密封设置导热柱6以使第一线路层3和第二线路层4电连接,所述导热柱6的导热系数大于第一线路层3或第二线路层4的导热系数,所述导热柱6接触所述导流通道2中的相变换热介质,第四步骤,重复第一步骤至第三步骤若干次以形成多层电路板,所述多层电路板至少具有两个基板1、两个第一线路层3和两个第二线路层4,每个基板1的所述导流通道2分别经由入口11和出口12连接冷凝单元形成流通相变换热介质的冷却流路,所述冷凝单元在重力方向上高于所述多层电路板,第五步骤,在多层电路板的顶表面的至少一个第一导热柱6处布置第一电子元件7以及粘结第一防焊层,在多层电路板的底表面的不同于第一导热柱6的第二导热柱6处布置第二电子元件8以及粘结第二防焊层,所述第一电子元件7包括用于5g通信的5g移动通信模块、sim卡槽和以太网接线接口,第二电子元件8包括电源模块、mcu芯片、无线基带芯片、存储芯片和以太网接线接口,所述多层电路板侧面设置天线接口和usb接口。
[0027]
所述的用于5g终端网卡的多层电路板制备方法的优选实施方式中,第一步骤中,提供下半基板1,在所述下半基板1上表面形成用于流通相变换热介质的第一导流槽,第一导流槽的入口11的内壁上设有毛细导流结构。
[0028]
提供上半基板1,在所述上半基板1的下表面形成用于流通相变换热介质的第二导流槽,第二导流槽的入口11的内壁上设有毛细导流结构,层合第一基板1和第二基板1,其
中,所述第一导流槽和第二导流槽重合以构成导流通道2。
[0029]
所述的用于5g终端网卡的多层电路板制备方法的优选实施方式中,所述第一导流槽上铺设导热管,所述第一导流槽和第二导流槽重合以包裹所述导热管,所述导热管构成用于流通相变换热介质的导流通道2,所述导热管于毛细导流结构处连接入口11。
[0030]
所述的用于5g终端网卡的多层电路板制备方法的优选实施方式中,第二步骤中,在第一线路层3粘贴绝缘层,脉冲二氧化碳激光烧蚀掉待钻通孔5处的绝缘层以露出第一线路层3的铜箔,所述铜箔电镀形成第一金属增强层9,同样地,第二线路层4粘贴绝缘层,脉冲二氧化碳激光烧蚀掉待钻通孔5处的绝缘层以露出第二线路层4的铜箔,然后电镀形成第二金属增强层10,脉冲二氧化碳激光在锡层的位置钻孔以顺次贯穿第一金属增强层9、第一线路层3、基板1、第二线路层4和第二金属增强层10,最后经由乙醇清洗通孔5。
[0031]
所述的用于5g终端网卡的多层电路板制备方法的优选实施方式中,第三步骤,所述导热柱6为实心银柱,在通孔5内热封所述实心银柱以使所述实心银柱与第一线路层3和第二线路层4电连接,所述实心银柱分别与第一线路层3及其第一金属增强层9和第二线路层4及其第二金属增强层10密封。
[0032]
所述的用于5g终端网卡的多层电路板制备方法的优选实施方式中,每个基板1的所述导流通道2的入口11经由第一总管连接冷凝单元,每个基板1的所述导流通道2的出口12经由第二总管连接冷凝单元。
[0033]
所述的用于5g终端网卡的多层电路板制备方法的优选实施方式中,所述冷却流路中连接冷凝单元,其为蛇形冷凝管,所述蛇形冷凝管设有散热翅片。
[0034]
所述的用于5g终端网卡的多层电路板制备方法的优选实施方式中,多层电路板中,偶数层或奇数层的基板1设有导流通道2。
[0035]
所述的用于5g终端网卡的多层电路板制备方法的优选实施方式中,基板1包括有机绝缘介质层和半固化片层,所述导流通道2为均匀分布于基板1内部的交错的槽壁形成的s形通道。
[0036]
为了进一步理解本发明,如图2所示,在一个实施例中,一种用于5g终端网卡的多层电路板制备方法步骤包括:第一步骤,如图3所示,提供基板1,在所述基板1内部形成用于流通相变换热介质的导流通道2,所述导流通道2的入口11和出口12分别位于所述基板1的侧面,所述入口11侧壁设有毛细导流结构,可选地,在所述基板1内部形成用于流通相变换热介质的导流通道2中,提供下半基板1,在所述下半基板1上表面形成用于流通相变换热介质的第一导流槽,第一导流槽的入口11的内壁上设有毛细导流结构,提供上半基板1,在所述上半基板1的下表面形成用于流通相变换热介质的第二导流槽,第二导流槽的入口11的内壁上设有毛细导流结构,层合第一基板1和第二基板1,其中,所述第一导流槽和第二导流槽重合以构成导流通道2。进一步地,为了提高散热效果,特别是对于没有布置通孔5的区域,所述第一导流槽上铺设导热管,所述第一导流槽和第二导流槽重合以包裹所述导热管,所述导热管构成用于流通相变换热介质的导流通道2,所述导热管于毛细导流结构处连接入口11。导热管的导热系数大于基板1的导热系数,有利于将基板1的热量导入导流通道2。可以理解的是,相变换热介质为不导电的相变换热介质,可选地,所述相变换热介质包括一氯二氟甲烷。可选地,基板1可由环氧树脂,铋酰亚胺
‑
三嗪树脂,聚酰亚胺树脂,聚苯醚树脂等有机树脂形成,也
可以混合两种以上的有机树脂。进一步地,基板1中包括玻璃纤维、玻璃无纺布、芳族聚酰胺的增强材料。
[0037]
第二步骤,在所述基板1的顶表面和底表面分别设置第一线路层3和第二线路层4,第一线路层3和第二线路层4经由例如导电树脂或金属电镀等形成导体电路,但从蚀刻等加工的便利性来看,特别优选镀铜的铜电镀,可以是化学铜电镀。在第一线路层3上钻多个通孔5,通孔5顺次贯穿第一线路层3、基板1和第二线路层4,所述通孔5连通所述导流通道2中,所述导流通道2的截面积大于所述通孔5的截面积,可选地,所述导流通道2、通孔5截面为圆形、矩形、圆角矩形、椭圆或其他几何形状。可选地,在第一线路层3上钻多个通孔5中,在第一线路层3粘贴绝缘层,脉冲二氧化碳激光烧蚀掉待钻通孔5处的绝缘层以露出第一线路层3的铜箔,所述铜箔电镀锡层形成铜锡层,同样地,第二线路层4粘贴绝缘层,脉冲二氧化碳激光烧蚀掉待钻通孔5处的绝缘层以露出第二线路层4的铜箔,然后电镀锡层形成铜锡层,脉冲二氧化碳激光在锡层的位置钻孔以顺次贯穿铜锡层的第一金属增强层9、第一线路层3、基板1、第二线路层4和铜锡层的第二金属增强层10,最后经由乙醇清洗通孔5。通过形成铜锡层的第一和第二金属增强层10,不但提高了导热柱6密封效果,增强了导电性,且有利于5g的高频信号高速稳定性。
[0038]
第三步骤,在通孔5内密封设置导热柱6以使第一线路层3和第二线路层4电连接,导热柱6分别与第一线路层3及其第一金属增强层9和第二线路层4及其第二金属增强层10密封,所述导热柱6的导热系数大于第一线路层3或第二线路层4的导热系数,所述导热柱6接触所述导流通道2中的相变换热介质。可选地,为进一步增加密封性,通孔5内壁设有内螺纹,相应地导热柱6外表面设有对应的外螺纹。可选地,导热柱6可以与导电迹线或限定印刷电路的其它部件电连通或不电连通。因此,导热柱6相对于多层电路板的操作可以是功能性的,非功能性的,或它们的任意组合。
[0039]
第四步骤,重复第一步骤至第三步骤若干次以形成多层电路板,所述多层电路板具有多个基板1、多个第一线路层3和多个第二线路层4,每个基板1的所述导流通道2分别经由入口11和出口12连接冷凝单元形成流通冷却介质的冷却流路,可选地,同一根导热柱6从多层电路板的上表面贯穿至下表面,或者,同一根导热柱6仅从贯穿其所在的基板1,或者一部分所述导热柱6从多层电路板的上表面贯穿至下表面,另一部分导热柱6仅从贯穿其所在基板1。进一步地,所述冷凝单元13包括蛇形盘管,如图4所示。
[0040]
第五步骤,在多层电路板的顶表面的至少一个第一导热柱6处布置第一电子元件7以及粘结第一防焊层,在多层电路板的底表面的不同于第一导热柱6的第二导热柱6处布置第二电子元件8以及粘结第二防焊层,所述第一电子元件7包括用于5g通信的5g移动通信模块、sim卡槽和以太网接线接口,第二电子元件8包括电源模块、mcu芯片、无线基带芯片、存储芯片和以太网接线接口,所述多层电路板侧面设置天线接口和usb接口。
[0041]
5g网卡包括多层电路板,其经由所述的用于5g终端网卡的多层电路板制备方法制成。
[0042]
工业实用性本发明的用于5g终端网卡的多层电路板制备方法及其5g网卡可以在5g通信电路板领域使用。
[0043]
尽管以上结合附图对本发明的实施方案进行了描述,但本发明并不局限于上述的
具体实施方案和应用领域,上述的具体实施方案仅仅是示意性的、指导性的,而不是限制性的。本领域的普通技术人员在本说明书的启示下和在不脱离本发明权利要求所保护的范围的情况下,还可以做出很多种的形式,这些均属于本发明保护之列。