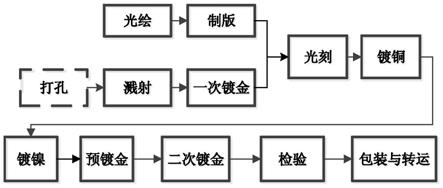
1.本发明属于微波集成电路技术领域,特别涉及一种适用于固放产品的微波集成电路薄膜加厚工艺。
背景技术:2.常规薄膜电路通过溅射、图形转移以及镀金进行制作,膜层厚度受到手工焊接、湿法刻蚀质量控制等各方面限制,目前微波集成电路微带产品主要以薄膜工艺为主,微带电路图形表层au膜层厚度最厚仅4μm~6μm,难以满足大功率部件应用需求。为了达到使用要求,通常采用在au层表面键合金带的方式,以提高电路功率耐受能力。但是这种方法可靠性低,工艺流程长,不能满足高可靠型号任务的需求。
3.随着卫星发射成本的提高和卫星功能密度的不断增加,原有基于氧化铝陶瓷基板的固放制造模式已经无法满足需求,迫切需要找到一种能显著提高大功率固放电路可靠性的途径。
4.为了满足大功率电路的需求,产品制作过程中可将au层加厚至10~15μm,但是由于产品装配过程中涉及到snpb焊接,过厚的au层无法通过多次搪锡彻底去金,残余金的存在使焊点的长期可靠性存在隐患。
5.当前,在公开发表的文献以及刊物中,较少有提到薄膜加厚相关工艺、规范以及产品应用的实例。中国专利“印刷电路板的局部图形铜厚加厚的制作方法”,公开号cn108617104a,提供了一种印刷电路板的局部图形铜厚加厚的制作方法,包括以下步骤:来料步骤;钻孔和沉孔步骤;第一次板电步骤;第一次贴干膜步骤;第一次曝光和第一次显影步骤;局部电镀步骤;第一次退膜步骤;第二次板电步骤;喷印抗蚀刻油墨步骤;第二次贴干膜步骤;第二次曝光和第二次显影步骤;蚀刻步骤;第二次退膜步骤。该专利采用“带胶电镀”实现铜层加厚,利用“胶膜”控制铜层侧向生长,然而,“带胶电镀”难以控制铜层在高度方向上的生长,同时“胶膜”可能作为污染源对电镀溶液体系造成污染,影响镀层纯度,最终导致印刷电路板产品性能不合格。
6.中国专利“一种pcb板面单区局部加厚镀铜的生产工艺”,公开号 cn106061127a,提供了一种pcb板面单区局部加厚镀铜的生产工艺,工艺流程主要包括:(1)对铜材进行清洗,清洗液为松香油污清洗液;(2)微蚀,利用 naps将底铜微蚀;(3)化学沉铜,将pcb板一次浸入到化学镀液中进行镀铜; (4)图形电镀;(5)掩体,选用抗镀材料加工后得到掩体层;(6)局部加厚镀铜,运用掩体层,进行局部加厚镀铜;(7)喷砂,对铜面喷砂以得到磨砂面;(8)喷锡,喷砂处理后进行喷锡;(9)水洗,水洗时控制温度,并且伴有空气搅拌;(10)镀后用开水烫熔掩体层蜡层回收,再用水溶性清洗剂清洗即可。该专利利用掩体阻挡线条在镀铜过程中侧向生长。然而,掩体同样难以控制铜层在高度方向上的生长,且存在制作复杂,电镀完成后去除工序繁琐的问题。
7.中国专利“一种氮化铝基薄膜电路制作方法”,公开号cn104037115a,提供了一种具备锡焊功能表面镀层结构和异形状特征的氮化铝基薄膜电路制作方法,包括以下步骤:
步骤101:清洗氮化铝基片。步骤102:将氮化铝基片设置形成正面和反面具有金属种子层薄膜。步骤103:在正面的金属种子层薄膜上使用光刻刻蚀工艺制备形成含异形状特征的电路图形。步骤104:激光加工氮化铝基薄膜电路的内部矩形通孔、或内部矩形通孔与外形异常部分。步骤105:稀盐酸处理。步骤106:制备锡焊功能表面镀层。步骤107:使用砂轮划片机划切氮化铝基薄膜电路的外形常规部分。该专利针对基于氮化铝陶瓷基板的薄膜微波电路板制作,采用物理沉积方式制作金属种子层,再通过图形转移和电镀加厚获得成品,不涉及薄膜加厚工艺。
8.中国专利“氧化铝陶瓷电路板制作方法”,公开号cn109195338a,提供了一种氧化铝陶瓷电路板制作方法,包括:步骤1,紫外激光刻蚀:采用紫外激光机对氧化铝陶瓷板依电路图形进行刻蚀,以形成与所述电路图形中的导电部分形状匹配的凹槽;步骤2,填充导电铜浆:用印刷方式将导电铜浆均匀地填充进所述凹槽中,并烘烤;步骤3,磨板:用磨板机将非电路图形的陶瓷面上残留的导电铜浆磨掉;步骤4,表面刷镀:用高速电刷镀笔在电路图形上刷镀铜镍金,即成高可靠精细陶瓷电路板。该专利是使用激光在陶瓷基板上刻蚀出与走线一致的凹槽,然后通过印刷金属浆料与烧结工序制作电路基层,最后在印刷金属膜上方刷镀金属层,不涉及薄膜加厚工艺。
9.对国内外论文和期刊文献进行了检索,尚未发现适用于固放产品的微波集成电路薄膜加厚工艺。
技术实现要素:10.为了克服现有技术中的不足,本发明人进行了锐意研究,提供了一种适用于固放产品的微波集成电路薄膜加厚工艺,通过特有的膜层结构设计,基于薄膜陶瓷电路板制作工艺,采用“四镀一刻”(四次长时间电镀,一次光刻)的方式,解决了较厚膜层电路的制作问题,达到较高的图形精度与膜层附着力,实现多种功能(焊接功能器件、键合金丝/金带/功能器件),满足大功率电路的需求,从而完成本发明。
11.本发明提供的技术方案如下:
12.第一方面,一种适用于固放产品的微波集成电路薄膜加厚工艺,包括如下步骤:
13.在带有附着层的陶瓷基片上实施一次镀金,形成的金镀层的厚度为2~3μm;
14.将掩膜版紧密贴合在一次镀金后涂覆有光敏胶的基片表面,曝光后进行显影、定影以及金属层的腐蚀,完成在金镀层上的光刻;
15.在光刻后的金镀层上镀铜,形成的铜镀层的厚度为3~5μm;
16.在铜镀层上镀镍,形成的镍镀层的厚度为0.5~1μm;
17.在镍镀层上实施二次镀金,形成的金镀层的厚度为2~3μm。
18.第二方面,一种薄膜加厚微波集成电路板,如图5所示,由下至上依次包括陶瓷基片、附着层、2~3μm的au镀层、3~5μm的cu镀层、0.5~1μm的ni 镀层以及2~3μm的au镀层。
19.根据本发明提供的一种适用于固放产品的微波集成电路薄膜加厚工艺,具有以下有益效果:
20.(1)根据本发明提供的一种适用于固放产品的微波集成电路薄膜加厚工艺,基于常规陶瓷薄膜电路的“二次叠加式”复合膜层技术路线,创新地解决固放电路产品难以耐受较大电流能力问题;其中“四镀一刻”的工艺流程中,通过镀液和电镀工艺的参数选择,可以
达到复合膜层结构镀层厚度与结晶颗粒的高质量控制;
21.(2)根据本发明提供的一种适用于固放产品的微波集成电路薄膜加厚工艺,确定了优化后的膜层结构,在现有薄膜电路结构基础上,增加电镀3~5μm 的cu层,以保证电路性能的正常实现;同时,为避免cu层向表面扩散氧化,同时满足后续组装金丝、金带键合要求,在电镀厚cu的基础上依次电镀 0.5~1μm的ni、2~3μm的au,以符合航天可靠性要求;表面金层厚度控制在 2~3μm,可以通过常规的搪锡实现去金,保证铅锡焊接的可靠性;
22.(3)根据本发明提供的一种适用于固放产品的微波集成电路薄膜加厚工艺,根据确定的膜层结构,对工序进行优化设计,将加厚工艺流程进行优化:将光刻工序放在一次镀金之后,使得微带侧向生长时长显著缩短,从而获得侧面较为整齐的微带,同时提高产品性能稳定性;本发明采用无掩膜、掩体状态下控制微带边缘侧向生长,避免了掩膜、掩体带来的污染或工序繁杂问题。
23.(4)根据本发明提供的一种适用于固放产品的微波集成电路薄膜加厚工艺,制得的“准厚膜”电路产品,膜层附着力提高到2kg/mm2以上,金丝键合强度高,线宽/间距精度好,电路膜层厚度可调,电路膜层电阻精度高,电路膜层耐受锡铅焊料次数多,耐电流能力强。
附图说明
24.图1为一种适用于固放产品的微波集成电路薄膜加厚工艺的流程图;
25.图2为先光刻后镀膜时微波集成电路薄膜加厚工艺的流程图;
26.图3.1和图3.2为采用图2中工艺流程电镀后微带突出部分尺度示意图;图 3.3和图3.4为采用图1中工艺流程电镀后微带侧面图;
27.图4为采用图1中工艺流程电镀后微带侧面尺寸图;
28.图5左为现有微波集成电路结构示意图;图5右为本发明中微波集成电路结构示意图;
29.图6为本发明中微波集成电路结构的sem图;
30.图7为固放产品应用场景。
具体实施方式
31.下面通过对本发明进行详细说明,本发明的特点和优点将随着这些说明而变得更为清楚、明确。
32.在这里专用的词“示例性”意为“用作例子、实施例或说明性”。这里作为“示例性”所说明的任何实施例不必解释为优于或好于其它实施例。尽管在附图中示出了实施例的各种方面,但是除非特别指出,不必按比例绘制附图。
33.如图1所示,本发明提供了一种适用于固放产品的微波集成电路薄膜加厚工艺,薄膜加厚工艺具体阐述如下。
34.(1)光绘
35.利用光绘设备将电子图形制作为放大若干倍数的底片。采用激光直写工艺时,则可忽略本工序。
36.(2)制版
37.采用缩微照相,将放大的电子图形成像在玻璃掩膜版上。采用激光直写制版时,可直接在掩膜版上刻蚀图形。
38.(3)打孔
39.根据设计需要,决定是否在陶瓷基片上实施打孔工序。目前,通常使用二氧化碳、皮秒或光纤激光加工的方式在陶瓷基片上制孔。
40.(4)溅射
41.根据选择附着层的差异,采用不同的通气速率、真空度、功率参数在基片表面实施溅射镀膜,得到附着层。
42.薄膜加厚微波集成电路产品,正反面溅射膜层结构与常规薄膜微波集成电路产品一致。溅射得到的附着层是后续膜层沉积的种子层,其附着力将决定最终薄膜加厚产品的附着力。
43.(5)一次镀金
44.镀金采用中性微氰镀覆体系,溶液ph=5.9~6.1,金含量为8~15g/l,体系温度为50
±
5℃,电流密度为1~2.3ma/cm2,阳极:阴极(面积比)=2:1。一次镀金厚度为2~3μm。
45.在溅射层上直接进行镀铜、镍等后续操作,由于晶格等微观结构差异,会导致铜层与底部溅射层剥离,一次镀金的金层的作用是附着层与其上方镀层的过渡。
46.一次镀金中,中性微氰镀液中金以au(cn)
2-的形式存在,具有较强的阴极极化作用、分散能力和覆盖能力,镀层细致光亮,因此选用为薄膜加厚的镀金体系。
47.(6)光刻
48.将步骤(2)中制作的掩膜版紧密贴合在一次镀金后涂覆有光敏胶的基片表面,曝光后进行显影、定影以及金属层的腐蚀,完成图形的转移。
49.传统的蚀刻理念中,一般为先光刻后镀膜,对应至本发明中工艺,则步骤 (6)应在步骤(5)前,流程图如图2所示。
50.图1和图2工艺流程中均显示,薄膜加厚主要有4次电镀(预镀工序过程时长极短、镀层厚度极小,此处不做讨论):然而,值得注意的是,每增加一次电镀工序,微带(图形)都会进一步侧向生长,进一步放大底层缺陷,甚至超出微带公差要求,使微带边缘呈“锯齿状”。采用图2中工艺流程,四次电镀后,以100μm线宽为标准,突出部分尺度可高达20μm(见图3.1、图3.2)。
51.本发明为减少电镀对微带外观的影响,将加厚工艺流程进行优化:将光刻工序放在一次镀金之后。这一操作使得微带侧向生长的机会从四次减少为三次,微带侧向生长时长显著缩短,从而获得侧面较为整齐的微带(见图3.3、图3.4),线条宽度精度可控制在
±
15μm(以100μm线宽为标准,见图4)。因而,将工艺流程由图2所示的“先刻后镀”改进为图1所示的“先镀后刻”。
52.(7)镀铜
53.(7.1)镀前准备
54.对于表面污迹较多的电路半成品,应使用有机溶剂对基片表面除油。
55.含不导电孤立图形的电路半成品,应先进行金丝互连,使电孤立图形在电镀时与电极连通。金丝作为工艺线,首先应保证所有孤立图形均导通,同时应避开较细线条、输入输出端等关键功能性区域。
56.同时可知,本发明中上述先镀后刻的方式,实现了将工艺线键合点“缺陷”电镀放大次数从4次减少到3次的作用,在一定意义上进一步改善了薄膜加厚电路产品的外观。
57.镀铜前应对产品表面状态、金丝互联情况进行检查,核对数量、工艺文件齐套性。明确工艺要求、计算施镀面积并清洗挂具。
58.(7.2)上挂
59.将基片固定在夹具上,夹点应选择在空白处或检验点上,要求夹持牢靠,不脱落。
60.(7.3)除油
61.在碱性除油液中浸泡除油,严禁使用超声波除油。
62.(7.4)氰化镀铜
63.将待镀基片零件挂镀槽中,并在阴极杆上固定好,基片的顶端距镀液液面约5~10cm。每槽电镀最小面积不低于2dm2;如果基片面积不足,用“陪片”(可采用铝合金或铜合金作为电镀配片)使总面积达到2dm2。
64.氰化镀铜电镀,溶液组分及工艺参数见表1。
65.表1氰化镀铜溶液配方及操作条件
[0066][0067]
下槽后,先使用2
±
0.5a/dm2的电流密度“冲击镀”1
±
0.5min,然后降低电流至1.1
±
0.1a/dm2,继续镀铜,总电镀时间3
±
1min。
[0068]
(7.5)酸性光亮镀铜
[0069]
镀铜注意事项与前文相同。
[0070]
酸性光亮镀铜电镀液中,溶液组分及工艺参数见表2。
[0071]
表2光亮镀铜溶液配方及操作条件
[0072][0073]
下槽后,先用2
±
0.5a/dm2的电流密度“冲击镀”1
±
0.5min,然后将电流降至 1.4
±
0.1a/dm2,继续镀铜,总电镀时间40
±
5min。铜层厚度为3~5μm。
[0074]
化学镀铜体系始终处于非稳态,状态一致性差;氰化镀铜结晶颗粒粗大,难以保证线条侧边的笔直度,但与一次镀金后界面结合力强,因此作为预镀铜工序。而酸性光亮镀铜的镀层光亮、孔隙率低且整平性好,故选用其作为正式镀铜工序。
[0075]
(8)镀镍
[0076]
镀镍体系的选用必须考虑内应力对膜层与基片、膜层与膜层之间附着力的影响。经大量研发试验后,确定选择氨基磺酸盐镀镍溶液体系。该体系应力低、镀液沉积速度快,且分散能力优于使用硫酸主盐的镀镍溶液。
[0077]
氨基磺酸盐镀镍溶液体系,溶液组分及工艺参数见表3。
[0078]
表3电镀镍溶液配方及操作条件
[0079][0080]
镍层厚度过小无法阻止下层铜层扩散,存在电路失效风险;而厚度过大则会导致膜层内应力失控,造成电路膜层脱落。为确定这一厚度,对选用不同镍层厚度的薄膜加厚电路片进行了高温储存试验,见表4。
[0081]
表4镍层厚度确定试验
[0082][0083][0084]
三组试片金层均为发生颜色变化,即未发生肉眼可见的铜层扩散。进一步采用“序号1”试验样片进行金丝、金带压焊试验。金丝、金带的破坏性拉力测试数值均满足微波集成电路相关检验要求,且断裂方式均为“颈缩处断裂”,可判定金层性能达标,纯度可靠,考虑应力因素,选择镍层厚度为0.5-1μm。
[0085]
(9)二次镀金
[0086]
(9.1)预镀金
[0087]
预镀金前,对镀镍后微波集成电路产品水洗,再采用10wt%~15wt%的柠檬酸溶液进行活化处理,活化温度为室温,活化时间20s~60s。
[0088]
活化后的微波集成电路产品,采用柠檬酸盐镀金液,在柠檬酸盐镀金槽中,预镀金3~5min。其中,柠檬酸盐镀金液,溶液组分及工艺参数见表5。
[0089]
表5预镀金(1)溶液配方及操作条件
[0090][0091]
(9.2)镀金
[0092]
二次镀金厚度为2-3微米。具体操作方法和参数与5)电镀中相同,即:采用中性微氰镀覆体系,溶液ph=5.9~6.1,金含量为8~15g/l,体系温度为50
±
5℃,电流密度为1~2.3ma/cm2,阳极:阴极面积比=2:1。
[0093]
至此已经确定了具体的膜层结构。即在现有薄膜电路结构基础上(基片+ 附着层+2~3μm的au镀层),增加电镀3~5μm的cu镀层、0.5~1μm的ni镀层以及2~3μm的au镀层,如图5所示和图6。
[0094]
3~5μm cu镀层的设置可以保证电路性能的正常实现,cu的选择考量了其优良的导热、导电性能,可以在满足电性能实现的前提下,兼顾散热等需求。 0.5~1μm厚度ni镀层避免cu层向表面扩散氧化,同时满足后续组装金丝、金带键合要求,若镍层厚度过小无法阻止下层铜层扩散,存在电路失效风险,而厚度过大则会导致膜层内应力失控,造成电路膜层脱落。表面金层厚度控制在 2~3μm,可以通过常规的搪锡实现去金,保证铅锡焊接的可靠性。采取该工艺条件的模样产品已进行多次试验,能够满足产品性能需求。
[0095]
本发明中薄膜加厚工艺制得的薄膜加厚微波集成电路,可达到的技术指标如下:
[0096]
a.电路膜层附着力>2kg/mm2,直径25微米金丝键合强度≥4.5g;250*25 微米金带键合强度≥50g;
[0097]
b.线宽/间距精度
±
15μm;
[0098]
c.电路膜层厚度:10-15μm;
[0099]
d.电路膜层电阻精度
±
2%;
[0100]
e.电路膜层耐受锡铅焊料次数:至少20次,每次3秒;
[0101]
f.耐电流能力:0.4mm线宽/5a
[0102]
综上,本发明在薄膜微波集成电路制备工艺的基础之上,结合焊接与键合等多种使用需求与金属材料的物理特性,从确定薄膜加厚的复合膜层结构出发、通过试验确认各个膜层部分的厚度、利用流程优化改善产品质量,最终获得了性能指标均满足航天星载产品要求的薄膜加厚的微波电路产品,达到国内外先进水平。该工艺方法目前已率先在风云2号l频段220w固放、风云3号c频段100w固放、天通s频段20w固放、天链s频段43w固放等多型号、多频段的大功率固放产品得到成功应用,解决了常规工艺膜层耐返修差、耐电流能力不足问题,应用效果良好,见图7。
[0103]
根据本发明的第二方面,提供了一种薄膜加厚微波集成电路板,采用第一方面所述的加厚工艺制备得到,如图5所示,由下至上依次包括陶瓷基片、附着层、2~3μm的au镀层、3~5μm的cu镀层、0.5~1μm的ni镀层以及2~3μm 的au镀层。
[0104]
以上结合具体实施方式和范例性实例对本发明进行了详细说明,不过这些说明并不能理解为对本发明的限制。本领域技术人员理解,在不偏离本发明精神和范围的情况下,可以对本发明技术方案及其实施方式进行多种等价替换、修饰或改进,这些均落入本发明的范围内。本发明的保护范围以所附权利要求为准。
[0105]
本发明说明书中未作详细描述的内容属本领域技术人员的公知技术。