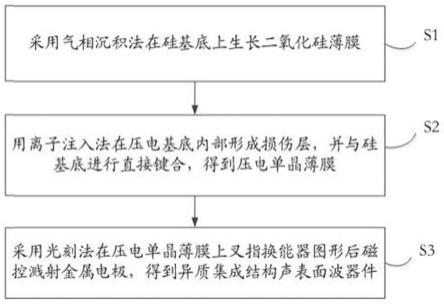
1.本技术属于半导体制造技术领域,尤其涉及一种异质集成结构声表面波器件及其制备方法。
背景技术:2.声表面波器件(surfaceacousticwave,saw)是利用叉指换能器在压电材料层上完成电信号-声信号-电信号的信号处理和转换的一类固态电子元器件。由于声表面波器件具有体积小、灵敏度高、稳定可靠等优点而被广泛应用,而随着技术的不断发展,对更高品质的声表面波器件提出了新的要求。
3.铌酸锂等铁电单晶具有诸多优异的性能,这些材料具有良好的光电、声光、压电、双折射、非线性等物理特性以及耐高温、抗腐蚀、机械性能稳定的特性,因此被广泛应用于制备谐振器、滤波器、光电调制器等。
4.目前,声光器件对器件的性能、体积、功耗、可靠性等不断提出了新的指标。然而,当前的声表面波器件通常是在完成器件封装以后,以分立元器件的形式和信息处理电路模块封装于声光模块中。这种结构的声光器件还难以实现声光与电学分立器件的集成,无法满足当前对声光器件的指标要求。
技术实现要素:5.有鉴于此,本技术提供了一种异质集成结构声表面波器件及其制备方法,以此来解决压电晶体与硅晶体失配问题,该结构的saw器件可以满足高频和高机电耦合系数领域的应用要求。
6.本技术的具体技术方案如下:
7.本技术提供一种异质集成结构声表面波器件的制备方法,包括如下步骤:
8.步骤一:采用气相沉积法在硅基底上生长二氧化硅薄膜;
9.步骤二:用离子注入法在压电基底内部形成损伤层,并与硅基底进行直接键合,得到压电单晶薄膜;
10.步骤三:采用光刻法在压电单晶薄膜上叉指换能器图形后磁控溅射金属电极,得到异质集成结构声表面波器件。
11.优选地,所述二氧化硅薄膜的厚度为300-800nm,粗糙度为5-10nm。
12.优选地,所述键合的压力为8000~12000n,键合温度80~120℃。
13.优选地,所述压电基底的材料选自铌酸锂、钽酸锂、铌镁酸铅-钛酸铅、磷酸钛氧钾以及镐钛酸铅中的一种或多种。
14.优选地,所述压电单晶薄膜的厚度为300nm-5μm,粗糙度为1-10nm。
15.优选地,生长二氧化硅薄膜之后以及硅基底进行直接键合之后还包括:依次进行机械化学抛光、氧等离子体活化和rac清洗。
16.优选地,所述金属电极选自al、au/ti或pt/ti,所述金属电极的厚度为50-300nm。
17.优选地,所述光刻法为紫外线曝光或电子束曝光。
18.本技术还提供一种异质集成结构声表面波器件,由下至上依次包括硅基底、二氧化硅薄膜、压电单晶薄膜以及叉指换能器,是由所述制备方法制备得到。
19.优选地,所述压电单晶薄膜的厚度为300nm-5μm,粗糙度1-10nm;所述叉指换能器的厚度为50-300nm;所述二氧化硅薄膜的厚度300nm-800nm,粗糙度为5-10nm。
20.本技术提供了一种异质集成结构声表面波器件及其制备方法,通过采用气相沉积法在硅基底上生长二氧化硅薄膜;用离子注入法在压电基底内部形成损伤层,并与硅基底进行直接键合,得到压电单晶薄膜;采用光刻法在压电单晶薄膜上叉指换能器图形后磁控溅射金属电极,得到异质集成结构声表面波器件。本技术通过改进的直接晶圆键合技术将压电材料与硅材料进行混合集成,可兼容cmos工艺,制得的基片可用作压电层和衬底的声表面波器件,从而实现大规模集成电路与声表面波器件的高效集成,以此来解决压电晶体与硅晶体失配问题。本技术制得的异质集成结构声表面波器件可以与传统cmos硅基集成电路进行混合集成,进一步提升了声光模块的性能、体积、功耗、可靠性等指标,降低了声光器件的成本,可应用于高频和高机电耦合系数领域,满足新一代声光通信技术发展对声光器件与信息处理模块集成化要求。
附图说明
21.为了更清楚地说明本技术实施例或现有技术中的技术方案,下面将对实施例或现有技术描述中所需要使用的附图作简单地介绍,显而易见地,下面描述中的附图仅仅是本技术的一些实施例,对于本领域普通技术人员来讲,在不付出创造性劳动性的前提下,还可以根据这些附图获得其它的附图。
22.图1为本技术实施例中异质集成结构声表面波器件的制备方法流程图;
23.图2为本技术实施例中异质集成结构声表面波器件的结构示意图;
24.图3为本技术实施例中异质集成结构声表面波器件的截面sem图;
25.图4为本技术实施例中异质集成结构声表面波器件的exd测试曲线图;
26.图示说明:1、硅基底;2、二氧化硅薄膜;3、压电单晶薄膜;4、叉指换能器。
具体实施方式
27.参照图1,图1为本技术实施例中异质集成结构声表面波器件的制备方法流程图。
28.本技术实施例提供一种异质集成结构声表面波器件的制备方法,包括如下步骤:
29.s1:采用气相沉积法在硅基底上生长二氧化硅薄膜;
30.s2:用离子注入法在压电基底内部形成损伤层,并与硅基底进行直接键合,得到压电单晶薄膜;
31.s3:采用光刻法在压电单晶薄膜上叉指换能器图形后磁控溅射金属电极,得到异质集成结构声表面波器件。
32.需要说明的是,本技术实施例首先在硅基底表面生长一层二氧化硅薄膜,并利用离子注入法在压电基底内注入损伤层后与带有二氧化硅薄膜的硅基底键合,制备得到压电单晶薄膜。接着用光刻法在压电单晶薄膜表面旋涂光刻胶刻蚀图形,在图形表面磁控溅射金属电极形成叉指换能器,最终得到异质集成结构声表面波器件。本技术实施例通过改进
的直接晶圆键合技术将压电材料与硅材料进行混合集成,可兼容cmos工艺,制得的基片可用作压电层和衬底的声表面波器件,从而实现大规模集成电路与声表面波器件的高效集成,以此来解决压电晶体与硅晶体失配问题。
33.根据本技术实施例,所述二氧化硅薄膜的厚度为300-800nm,粗糙度为5-10nm。
34.根据本技术实施例,所述键合的压力为8000~12000n,键合温度80~120℃。
35.根据本技术实施例,所述压电基底的材料选自铌酸锂、钽酸锂、铌镁酸铅-钛酸铅、磷酸钛氧钾以及镐钛酸铅中的一种或多种。
36.根据本技术实施例,所述压电单晶薄膜的厚度为300nm-5μm,粗糙度为1-10nm。
37.根据本技术实施例,生长二氧化硅薄膜之后以及硅基底进行直接键合之后还包括:依次进行机械化学抛光、氧等离子体活化和rac清洗。
38.根据本技术实施例,所述金属电极选自al、au/ti或pt/ti,所述金属电极的厚度为50-300nm。
39.根据本技术实施例,所述光刻法为紫外线曝光或电子束曝光。
40.参照图2,图2为本技术实施例中异质集成结构声表面波器件的结构示意图。
41.本技术实施例还提供一种异质集成结构声表面波器件,由下至上依次包括硅基底1,二氧化硅薄膜2,压电单晶薄膜3以及叉指换能器4,是由所述制备方法制备得到。
42.需要说明的是,本技术实施例通过改进的直接晶圆键合技术将压电材料与硅材料进行混合集成,进一步提升了声光模块的性能、体积、功耗、可靠性等指标,降低了声光器件的成本,满足新一代声光通信技术发展对声光器件与信息处理模块集成化要求。
43.根据本技术实施例,所述压电单晶薄膜的厚度为300nm-5μm,粗糙度1-10nm;所述叉指换能器的厚度为50-300nm;所述二氧化硅薄膜的厚度300nm-800nm,粗糙度为5-10nm。
44.为使得本技术的目的、特征、优点能够更加的明显和易懂,对本技术实施例中的技术方案进行清楚、完整地描述,显然,下面所描述的实施例仅仅是本技术一部分实施例,而非全部的实施例。基于本技术中的实施例,本领域普通技术人员在没有做出创造性劳动前提下所获得的所有其它实施例,都属于本技术保护的范围。
45.本技术实施例所使用的试剂和原料均为市售或自制。
46.实施例1
47.1、在硅基底上利用气相沉积法生长一层二氧化硅薄膜,二氧化硅薄膜的厚度为300nm(300-800nm)。利用logitech lp50抛光系统对其进行抛光处理,使其粗糙度为10nm(5-10nm),然后用pva tepla ion40等氧离子体系统进行活化处理,满足直接键合工艺的工艺面,最后rac清洗得到sio2/si基片。
48.2、对压电基片和步骤1中的sio2/si基片进行清洗,并用氮气吹干备用。用一定剂量的高能h/he离子注入铌酸锂压电单晶基片,形成一个非晶层,之后将注入h/he离子的压电基片和sio2/si基片在evg510键合机中进行键合,键合压力为10000n(8000~12000n),键合温度为100℃(80~120℃)。键合之后进行3h高温退火处理,剥离出sio2/si基压电单晶薄膜。对sio2/si基压电单晶薄膜进行减薄和化学机械抛光,减薄为离子铣削或机械减薄,制得光滑的sio2/si基压电单晶薄膜,粗糙度为10nm(1-10nm),厚度为5μm(300nm-5μm),满足光刻工艺的工艺面。
49.3、用匀胶机在sio2/si基压电单晶薄膜上旋涂一层光刻胶,利用光刻技术在sio2/
si基压电单晶薄膜制作指宽为2μm的叉指换能图形。
50.4、采用磁控溅射制备一层50nm(50-300nm)的铝膜,最后去胶剥离,制得异质集成结构声表面波器件。
51.本实施例制得的linbo3/sio2/si异质集成结构声表面波器件的截面sem图和exd测试曲线如图3和图4所示。
52.图3测试结果表明直接键合界面的每一层都清晰可见,厚度均匀,从上到下依次为linbo3层、sio2层和si衬底。图4测试结果表明,c、si、nb元素之间发生互扩散,原子扩散并迁移,在界面处形成原子级连接,这说明本实施例通过改进的直接晶圆键合技术将压电材料与硅材料进行混合集成解决了晶格失配问题,而这一进步将有效进一步提升了声光模块的性能、体积、功耗、可靠性等指标。
53.实施例2
54.1、在硅基底上利用气相沉积法生长一层二氧化硅薄膜,二氧化硅薄膜的厚度为800nm。利用logitech lp50抛光系统对其进行抛光处理,使其粗糙度为5nm,然后用pva tepla ion40等氧离子体系统进行活化处理,满足直接键合工艺的工艺面,最后rac清洗得到sio2/si基片。
55.2、对压电基片和步骤1中的sio2/si基片进行清洗,并用氮气吹干备用。用一定剂量的高能h/he离子注入铌酸锂压电单晶基片,形成一个非晶层,之后将注入h/he离子的压电基片和sio2/si基片在evg510键合机中进行键合,键合压力为12000n,键合温度为120℃。键合之后进行3h高温退火处理,剥离出sio2/si基压电单晶薄膜。对sio2/si基压电单晶薄膜进行减薄和化学机械抛光,减薄为离子铣削或机械减薄,制得光滑的sio2/si基压电单晶薄膜,粗糙度为10nm,厚度为5μm,满足光刻工艺的工艺面。
56.3、用匀胶机在sio2/si基压电单晶薄膜上旋涂一层光刻胶,利用光刻技术在sio2/si基压电单晶薄膜制作指宽为2μm的叉指换能图形。
57.4、采用磁控溅射制备一层50nm的铝膜,最后去胶剥离,制得异质集成结构声表面波器件。
58.实施例3
59.1、在硅基底上利用气相沉积法生长一层二氧化硅薄膜,二氧化硅薄膜的厚度为300nm。利用logitech lp50抛光系统对其进行抛光处理,使其粗糙度为10nm,然后用pva teplaion40等氧离子体系统进行活化处理,满足直接键合工艺的工艺面,最后rac清洗得到sio2/si基片。
60.2、对压电基片和步骤1中的sio2/si基片进行清洗,并用氮气吹干备用。用一定剂量的高能h/he离子注入铌酸锂压电单晶基片,形成一个非晶层,之后将注入h/he离子的压电基片和sio2/si基片在evg510键合机中进行键合,键合压力为8000n,键合温度为80℃。键合之后进行3h高温退火处理,剥离出sio2/si基压电单晶薄膜。对sio2/si基压电单晶薄膜进行减薄和化学机械抛光,减薄为离子铣削或机械减薄,制得光滑的sio2/si基压电单晶薄膜,粗糙度为1nm,厚度为300nm,满足光刻工艺的工艺面。
61.3、用匀胶机在sio2/si基压电单晶薄膜上旋涂一层光刻胶,利用光刻技术在sio2/si基压电单晶薄膜制作指宽为2μm的叉指换能图形。
62.4、采用磁控溅射制备一层50nm的铝膜,最后去胶剥离,制得异质集成结构声表面
波器件。
63.实施例4
64.1、在硅基底上利用气相沉积法生长一层二氧化硅薄膜,二氧化硅薄膜的厚度为300nm。利用logitech lp50抛光系统对其进行抛光处理,使其粗糙度为10nm,然后用pva tepla ion40等氧离子体系统进行活化处理,满足直接键合工艺的工艺面,最后rac清洗得到sio2/si基片。
65.2、对压电基片和步骤1中的sio2/si基片进行清洗,并用氮气吹干备用。用一定剂量的高能h/he离子注入铌酸锂压电单晶基片,形成一个非晶层,之后将注入h/he离子的压电基片和sio2/si基片在evg510键合机中进行键合,键合压力为10000n,键合温度为100℃。键合之后进行3h高温退火处理,剥离出sio2/si基压电单晶薄膜。对sio2/si基压电单晶薄膜进行减薄和化学机械抛光,减薄为离子铣削或机械减薄,制得光滑的sio2/si基压电单晶薄膜,粗糙度为10nm,厚度为5μm,满足光刻工艺的工艺面。
66.3、用匀胶机在sio2/si基压电单晶薄膜上旋涂一层光刻胶,利用光刻技术在sio2/si基压电单晶薄膜制作指宽为2μm的叉指换能图形。
67.4、采用磁控溅射制备一层300nm的铝膜,最后去胶剥离,制得异质集成结构声表面波器件。
68.实施例5
69.1、在硅基底上利用气相沉积法生长一层二氧化硅薄膜,二氧化硅薄膜的厚度为500nm。利用logitech lp50抛光系统对其进行抛光处理,使其粗糙度为8nm,然后用pva tepla ion40等氧离子体系统进行活化处理,满足直接键合工艺的工艺面,最后rac清洗得到sio2/si基片。
70.2、对压电基片和步骤1中的sio2/si基片进行清洗,并用氮气吹干备用。用一定剂量的高能h/he离子注入钽酸锂压电单晶基片,形成一个非晶层,之后将注入h/he离子的压电基片和sio2/si基片在evg510键合机中进行键合,键合压力为10000n,键合温度为100℃。键合之后进行3h高温退火处理,剥离出sio2/si基压电单晶薄膜。对sio2/si基压电单晶薄膜进行减薄和化学机械抛光,减薄为离子铣削或机械减薄,制得光滑的sio2/si基压电单晶薄膜,粗糙度为10nm,厚度为5μm,满足光刻工艺的工艺面。
71.3、用匀胶机在sio2/si基压电单晶薄膜上旋涂一层光刻胶,利用光刻技术在sio2/si基压电单晶薄膜制作指宽为2μm的叉指换能图形。
72.4、采用磁控溅射制备一层100nm的au/ti膜,最后去胶剥离,制得异质集成结构声表面波器件。
73.实施例6
74.1、在硅基底上利用气相沉积法生长一层二氧化硅薄膜,二氧化硅薄膜的厚度为500nm。利用logitech lp50抛光系统对其进行抛光处理,使其粗糙度为8nm,然后用pva tepla ion40等氧离子体系统进行活化处理,满足直接键合工艺的工艺面,最后rac清洗得到sio2/si基片。
75.2、对压电基片和步骤1中的sio2/si基片进行清洗,并用氮气吹干备用。用一定剂量的高能h/he离子注入铌镁酸铅-钛酸铅压电单晶基片,形成一个非晶层,之后将注入h/he离子的压电基片和sio2/si基片在evg510键合机中进行键合,键合压力为10000n,键合温度
为100℃。键合之后进行3h高温退火处理,剥离出sio2/si基压电单晶薄膜。对sio2/si基压电单晶薄膜进行减薄和化学机械抛光,减薄为离子铣削或机械减薄,制得光滑的sio2/si基压电单晶薄膜,粗糙度为5nm,厚度为1μm,满足光刻工艺的工艺面。
76.3、用匀胶机在sio2/si基压电单晶薄膜上旋涂一层光刻胶,利用光刻技术在sio2/si基压电单晶薄膜制作指宽为2μm的叉指换能图形。
77.4、采用磁控溅射制备一层100nm的pt/ti膜,最后去胶剥离,制得异质集成结构声表面波器件。
78.实施例7
79.1、在硅基底上利用气相沉积法生长一层二氧化硅薄膜,二氧化硅薄膜的厚度为500nm。利用logitech lp50抛光系统对其进行抛光处理,使其粗糙度为8nm,然后用pva tepla ion40等氧离子体系统进行活化处理,满足直接键合工艺的工艺面,最后rac清洗得到sio2/si基片。
80.2、对压电基片和步骤1中的sio2/si基片进行清洗,并用氮气吹干备用。用一定剂量的高能h/he离子注入磷酸钛氧钾压电单晶基片,形成一个非晶层,之后将注入h/he离子的压电基片和sio2/si基片在evg510键合机中进行键合,键合压力为10000n,键合温度为100℃。键合之后进行3h高温退火处理,剥离出sio2/si基压电单晶薄膜。对sio2/si基压电单晶薄膜进行减薄和化学机械抛光,减薄为离子铣削或机械减薄,制得光滑的sio2/si基压电单晶薄膜,粗糙度为5nm,厚度为1μm,满足光刻工艺的工艺面。
81.3、用匀胶机在sio2/si基压电单晶薄膜上旋涂一层光刻胶,利用光刻技术在sio2/si基压电单晶薄膜制作指宽为2μm的叉指换能图形。
82.4、采用磁控溅射制备一层100nm的铝膜,最后去胶剥离,制得异质集成结构声表面波器件。
83.实施例8
84.1、在硅基底上利用气相沉积法生长一层二氧化硅薄膜,二氧化硅薄膜的厚度为500nm。利用logitech lp50抛光系统对其进行抛光处理,使其粗糙度为8nm,然后用pva tepla ion40等氧离子体系统进行活化处理,满足直接键合工艺的工艺面,最后rac清洗得到sio2/si基片。
85.2、对压电基片和步骤1中的sio2/si基片进行清洗,并用氮气吹干备用。用一定剂量的高能h/he离子注入镐钛酸铅压电单晶基片,形成一个非晶层,之后将注入h/he离子的压电基片和sio2/si基片在evg510键合机中进行键合,键合压力为10000n,键合温度为100℃。键合之后进行3h高温退火处理,剥离出sio2/si基压电单晶薄膜。对sio2/si基压电单晶薄膜进行减薄和化学机械抛光,减薄为离子铣削或机械减薄,制得光滑的sio2/si基压电单晶薄膜,粗糙度为5nm,厚度为1μm,满足光刻工艺的工艺面。
86.3、用匀胶机在sio2/si基压电单晶薄膜上旋涂一层光刻胶,利用光刻技术在sio2/si基压电单晶薄膜制作指宽为2μm的叉指换能图形。
87.4、采用磁控溅射制备一层100nm的au/ti膜,最后去胶剥离,制得异质集成结构声表面波器件。
88.综上所述,本技术实施例的制备方法通过改进的直接晶圆键合技术将压电材料与硅材料进行混合集成,可兼容cmos工艺,制得的基片可用作压电层和衬底的声表面波器件,
从而实现大规模集成电路与声表面波器件的高效集成,以此来解决压电晶体与硅晶体失配问题。本技术实施例制得的异质集成结构声表面波器件可以与传统cmos硅基集成电路进行混合集成,进一步提升了声光模块的性能、体积、功耗、可靠性等指标,降低了声光器件的成本,可应用于高频和高机电耦合系数领域。
89.以上所述,以上实施例仅用以说明本技术的技术方案,而非对其限制;尽管参照前述实施例对本技术进行了详细的说明,本领域的普通技术人员应当理解:其依然可以对前述各实施例所记载的技术方案进行修改,或者对其中部分技术特征进行等同替换;而这些修改或者替换,并不使相应技术方案的本质脱离本技术各实施例技术方案的精神和范围。