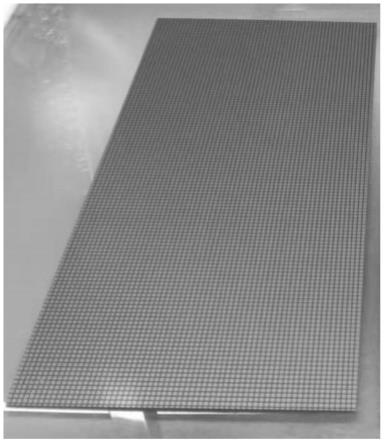
一种清除成品pcb焊盘铜面污渍的osp前处理工艺
技术领域
1.本发明涉及线路板加工领域,特别涉及一种清除成品pcb焊盘铜面污渍的osp前处理工艺。
背景技术:2.osp是印刷电路板(pcb)铜箔表面处理的符合rohs指令要求的一种工艺。osp是organic solderability preservatives的简称,中译为有机保焊膜,又称护铜剂,英文亦称之preflux。简单地说,osp就是在洁净的裸铜表面上,以化学的方法长出一层有机皮膜。这层膜具有防氧化,耐热冲击,耐湿性,用以保护铜表面于常态环境中不再继续生锈(氧化或硫化等);但在后续的焊接高温中,此种保护膜又必须很容易被助焊剂所迅速清除,如此方可使露出的干净铜表面得以在极短的时间内与熔融焊锡立即结合成为牢固的焊点。
3.随着现代科技发展的进步,电子产品对于pcb的要求逐步提高,除要求pcb板保证性能完整可靠外还需保证外观零瑕疵!osp前处理除油的作用,为清除在前制程工序生产过程中残留在pcb焊盘表面的污渍,以露出清洁的铜面,保证成膜效果。而常规的osp工艺,因除油不彻底,焊盘铜面的深度氧化和被挥发性油渍污染的区域无法清洁干净,常造成pcb焊盘铜面颜色差异,形成如白点、杂色、七彩色等外观瑕疵,超出客户对pcb的外观允收标准,无法满足现代工艺要求。
技术实现要素:4.为了解决上述问题,本发明公开了一种清除成品pcb焊盘铜面污渍的osp前处理工艺,包括步骤:一次除油、一次水洗、二次除油、二次水洗、微蚀、三级水洗、酸洗、水洗、成膜风干、di水洗、干燥。
5.优选的,所述二次除油使用除油剂为含有表面活性剂c17h37so4na和助洗剂na2sio3的水溶液。
6.优选的,所述除油剂浓度为5-10%。
7.优选的,所述二次除油方式为循环喷淋方式。
8.优选的,所述循环喷淋时间为5-10s。
9.优选的,所述c17h37so4na和na2sio3的比例为1-30:1。
10.优选的,所述微蚀厚度为1.0-1.5um。
11.优选的,所述di水洗ph为4.0-7.0。
12.优选的,所述成膜风干工艺中膜厚为0.2-0.5um。
13.本发明通过在增加两道除油工艺流程,加强除油效果,所采用特制除油剂,主要针对铜面深度氧化、挥发性油渍对铜面造成的污染进行定向清洁,能够清洁掉99.9%以上的铜面污染物质,从而杜绝pcb焊盘表面杂色、七彩色、白点等外观瑕疵,提高pcb的外观品质,满足了市场对pcb产品的应用需求。
附图说明
14.图1为本发明实施例osp前处理线路板;
15.图2为传统工艺osp前处理线路板。
具体实施方式
16.需要说明的是,在不冲突的情况下,本发明中的实施例及实施例中的特征可以相互组合。
17.在本发明的描述中,需要理解的是,术语“中心”、“纵向”、“横向”、“上”、“下”、“前”、“后”、“左”、“右”、“竖直”、“水平”、“顶”、“底”、“内”、“外”等指示的方位或位置关系为基于附图所示的方位或位置关系,仅是为了便于描述本发明和简化描述,而不是指示或暗示所指的装置或元件必须具有特定的方位、以特定的方位构造和操作,因此不能理解为对本发明的限制。
18.下面结合附图对本发明的具体实施例做详细说明。
19.实施例1
20.清除成品pcb焊盘铜面污渍的osp前处理工艺,步骤为:一次除油、一次水洗、二次除油、二次水洗、微蚀、三级水洗、酸洗、水洗、成膜风干、di水洗、干燥。
21.其中,一次除油和一次水洗为常用传统普通除油水洗方法,二次除油使用除油剂为含有表面活性剂c
17h37
so4na和助洗剂na2sio3的水溶液,除油剂浓度为8%,二次除油方式为循环喷淋方式,循环喷淋时间为7s,c
17h37
so4na和na2sio3的比例为10:1,微蚀厚度为1.2um,di水洗ph为5.0,成膜风干工艺中膜厚为0.3um。其它工艺过程均使用已有技术普通常用工艺进行。
22.实施例2
23.清除成品pcb焊盘铜面污渍的osp前处理工艺,步骤为:一次除油、一次水洗、二次除油、二次水洗、微蚀、三级水洗、酸洗、水洗、成膜风干、di水洗、干燥。
24.其中,一次除油和一次水洗为常用传统普通除油水洗方法,二次除油使用除油剂为含有表面活性剂c
17h37
so4na和助洗剂na2sio3的水溶液,除油剂浓度为5%,二次除油方式为循环喷淋方式,循环喷淋时间为5s,c
17h37
so4na和na2sio3的比例为1:1,微蚀厚度为1um,di水洗ph为4.0,成膜风干工艺中膜厚为0.2um。其它工艺过程均使用已有技术普通常用工艺进行。
25.实施例3
26.清除成品pcb焊盘铜面污渍的osp前处理工艺,步骤为:一次除油、一次水洗、二次除油、二次水洗、微蚀、三级水洗、酸洗、水洗、成膜风干、di水洗、干燥。
27.其中,一次除油和一次水洗为常用传统普通除油水洗方法,二次除油使用除油剂为含有表面活性剂c
17h37
so4na和助洗剂na2sio3的水溶液,除油剂浓度为10%,二次除油方式为循环喷淋方式,循环喷淋时间为10s,c
17h37
so4na和na2sio3的比例为30:1,微蚀厚度为1.5um,di水洗ph为7.0,成膜风干工艺中膜厚为0.5um。其它工艺过程均使用已有技术普通常用工艺进行。
28.实施例4
29.清除成品pcb焊盘铜面污渍的osp前处理工艺,步骤为:一次除油、一次水洗、二次
除油、二次水洗、微蚀、三级水洗、酸洗、水洗、成膜风干、di水洗、干燥。
30.其中,一次除油和一次水洗为常用传统普通除油水洗方法,二次除油使用除油剂为含有表面活性剂c
17h37
so4na和助洗剂na2sio3的水溶液,除油剂浓度为15%,二次除油方式为循环喷淋方式,循环喷淋时间为7s,c
17h37
so4na和na2sio3的比例为20:1,微蚀厚度为1.4um,di水洗ph为6.0,成膜风干工艺中膜厚为0.4um。其它工艺过程均使用已有技术普通常用工艺进行。
31.除油:除油效果的好坏直接影响到成膜质量。除油不良,造成膜厚度不均匀。一方面,可以通过分析溶液,将浓度控制在工艺范围内。另一方面,也要经常检查除油效果是否好,若除油效果不好,则应及时更换除油液。
32.微蚀:微蚀的目的是形成粗糙的铜面,便于成膜。微蚀的厚度直接影响到成膜速率,因此,要形成稳定的膜厚,保持微蚀厚度的稳定是非常重要的。一般将微蚀厚度控制在1.0-1.5um比较合适。每班生产前,可测定微蚀速率,根据微蚀速率来确定微蚀时间。
33.成膜:成膜前的水洗最好采有di水,以防成膜液遭到污染。成膜后的水洗也最好采用di水,且ph值应控制在4.0-7.0之间,以防膜层遭到污染及破坏。osp工艺的关键是控制好防氧化膜的厚度。膜太薄,耐热冲击能力差,在过回流焊时,膜层耐不往高温(190-200℃),最终影响焊接性能,在电子装配线上,膜不能很好的被助焊剂所溶解,影响焊接性能。一般控制膜厚在0.2-0.5um之间比较合适。
34.结合附图1-2,本发明实施例相比常规osp工艺,前处理流程除油后再增加一道除油工艺流程,用于深度处理铜面异物,对减少pcb铜面杂色、七彩色、白点等外观瑕疵,提高pcb表观质量具有更好的效果。
35.上述实施例仅描述现有设备最优使用方式,而运用类似的常用机械手段代替本实施例中的元素,均落入保护范围。