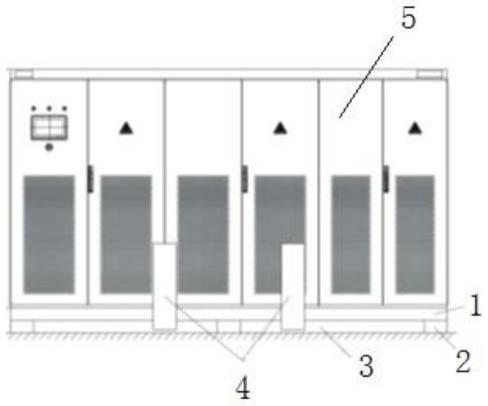
1.本实用新型涉及机柜,具体涉及一种用于叉车搬运的支撑结构及机柜。
背景技术:2.在传统机柜底部托梁设计中,有一种情况是机柜需要使用叉车来实现搬运,因此要求机柜的底部有足够的空隙,便于插入货叉,传统的做法是将底部托梁设计成如图1与图2的形式,包括第一支撑板1以及三个均匀连接在第一支撑板1一侧的第二支撑板2,三个第二支撑板2之间形成两个供叉车4的货叉穿过的通道,第一支撑板1另一侧与机柜本体5下端连接,但是这种结构,需要占用两层空间,其中最下面一层的功能是与地面接触以及实现货叉的插入,第二层是提供足够的刚度承载机柜的荷载,由于两层都属于机柜可用容积以外的空间,所以导致机柜可用容积减少。
技术实现要素:3.本实用新型的目的是解决现有的底部托梁占用的空间大,导致机柜可用容积减少的技术问题,而提供一种用于叉车搬运的支撑结构及机柜。
4.为实现上述目的,本实用新型所采用的技术方案为:
5.一种用于叉车搬运的支撑结构,其特殊之处在于:
6.包括搬运支撑件与支撑组件;
7.所述搬运支撑件的数量为一个,且其内部设置有空腔;所述搬运支撑件上沿水平方向设置有用于叉车上的货叉穿过的两个叉车孔;两个所述叉车孔之间的距离与叉车上的两个货叉之间的距离相等;
8.所述空腔高度大于所述叉车孔的高度;
9.所述支撑组件的数量为两个,位于所述空腔内部且分别设置在两个所述叉车孔处,通过将叉车孔直接开设在一层设置的搬运支撑件,较原先两层的结构,减少了高度尺寸,并且通过将搬运支撑件内部设置为空腔,可以节省材料。
10.进一步地,所述支撑组件包括第一加强柱;
11.所述第一加强柱为矩形结构;
12.所述第一加强柱设置在所述叉车孔内,且第一加强柱前端面的上下两端与后端面的上下两端均与搬运支撑件的内壁连接,位于前端面与后端面之间的第一加强柱与搬运支撑件的内壁之间存在间隙;
13.所述矩形结构设置有供货叉穿过的通孔,所述通孔的长度和高度尺寸大于等于所述叉车孔的长度和高度尺寸,通过设置的第一加强柱,可以保证叉车孔处的刚度、强度与抗弯性能,从而保证搬运支撑件在使用时的安全性。
14.进一步地,所述支撑组件还包括设置在所述间隙内的第二支撑件;
15.所述第二支撑件包括第二加强板与第三加强板;
16.所述第二加强板包括第一横板、两个一端连接在第一横板两侧的斜板以及通过两
个斜板另一端分别沿左右两端向外水平延伸而成的第二横板;两个斜板另一端通过第三加强板连接,且所述第三加强板的长度尺寸大于所述横板的长度尺寸,从而使得第一横板、第三加强板以及两个斜板形成正梯形结构,所述第一加强柱设置在所述正梯形结构内;
17.所述第一横板、斜板、第二横板与第三加强板前后的宽度尺寸均小于第一加强柱的宽度尺寸;
18.所述第一横板的左右两端以及第三加强板左右两端均与搬运支撑件内壁连接;所述第一横板、第三加强板均与所述第一加强柱的上下端外侧壁贴合。
19.进一步地,所述搬运支撑件包括第一槽钢、第二槽钢、第一封闭板、第二封闭板、第三封闭板和第四封闭板;
20.所述第一槽钢与第二槽钢均为u型且相对设置,第一槽钢与第二槽钢沿其长度方向的两端分别通过第一封闭板、第二封闭板连接,第一槽钢与第二槽钢上下两端分别通过第三封闭板、第四封闭板连接,从而在第一槽钢、第二槽钢、第一封闭板、第二封闭板、第三封闭板与第四封闭板之间形成所述空腔;所述第三封闭板与第四封闭板之间的距离、第一槽钢上下两端之间的距离以及第二槽钢上下两端之间的距离均大于叉车孔纵向截面的高度;
21.所述叉车孔贯穿所述第一槽钢的底面与第二槽钢的底面;
22.所述第一加强柱前端面的上下两端与后端面的上下两端分别与第二槽钢和第一槽钢连接;所述第三加强板和第一横板左右两端的前后两边分别与第二槽钢和第一槽钢连接。
23.进一步地,所述第一槽钢与第一封闭板、第二封闭板、第三封闭板和第四封闭板焊接;所述第二槽钢与第一封闭板、第二封闭板、第三封闭板和第四封闭板焊接;
24.所述第一加强柱前端面的上下两端与后端面的上下两端分别与第二槽钢和第一槽钢焊接;所述第三加强板和第一横板的左右两端分别与第一槽钢和第二槽钢焊接,采用焊接工艺,可以进一步增加强度与刚度,保证安全性与稳定性。
25.本实用新型还提出一种柜机,其特殊之处在于:包括柜子本体与设置在柜子本体下方的多个支撑结构;
26.所述支撑结构采用上述提出的用于叉车搬运的支撑结构。
27.本实用新型的有益效果是:
28.1、本实用新型提出的一种用于叉车搬运的支撑结构,采用单层的搬运支撑件,并且在搬运支撑件上设置叉车孔,为叉车上的货叉提供活动通道,相比原先采用的双层结构,减少了支撑结构占用的体积,从而在不增加机柜总高度的前提下,提高机柜可用容积。
29.2、本实用新型提出的一种用于叉车搬运的支撑结构,通过将搬运支撑件内部设置为空腔,既减轻了重量,有节省了材料。
30.3、本实用新型提出的一种用于叉车搬运的支撑结构,通过在叉车孔处设置支撑组件,保证了叉车孔处的强度、刚度与抗弯性能,提高搬运的安全性。
31.4、本实用新型提出的一种用于叉车搬运的支撑结构,通过设置的第二支撑件,进一步保证了搬运支撑件的强度,具体的,将第二支撑件设置为正梯形结构,可以将搬运支撑件上端的受力通过第二支撑件传递到搬运支撑件下端,实现力的过渡,保证了叉车孔处的强度、刚度与抗弯性能,提高搬运的安全性,并且可以防止受力集中而导致搬运支撑件的损
坏。
附图说明
32.图1是现有技术的主视结构示意图;
33.图2是图1的左视图;
34.图3是本实用新型实施例的主视图;
35.图4是图3的左视图;
36.图5是本实用新型搬运支撑件主视图;
37.图6是图5中b-b处的剖视图;
38.图7是图5中a-a处的剖视图;
39.图8是本实用新型实施例中搬运支撑件未开孔前的抗弯截面的惯性矩示意图;
40.图9是图8开孔后的抗弯截面的惯性矩示意图;
41.图10是在图9基础上焊接支撑组件后的抗弯截面的惯性矩示意图。
42.图中;1、第一支撑板;2、第二支撑板;3、通道;4、货叉;5、机柜本体;6、搬运支撑件;7、叉车孔;8、第一槽钢;9、第二槽钢;10、第一封闭板;12、第三封闭板;13、第四封闭板;14、第一加强柱;15、第二加强板;16、第三加强板。
具体实施方式
43.为使本实用新型的目的、优点和特征更加清楚,以下结合附图和具体实施例作进一步详细说明。
44.文中所述的“前、后、上、下、左、右、长度、宽度以及高度”均以图5为基准,左右为长度方向,上下为高度方向,前后为宽度方向。
45.本实用新型提出一种机柜,如图3-图10所示,包括机柜本体5、两个搬运支撑件6、四个支撑组件;
46.各部件的组成如下:
47.如图6所示,搬运支撑件6包括第一槽钢8、第二槽钢9、第一封闭板10、第二封闭板、第三封闭板12和第四封闭板13;第一槽钢8与第二槽钢9结构相同,且均为u型,第一槽钢8与第二槽钢9相对设置,第一槽钢8与第二槽钢9沿其长度方向的两端分别通过第一封闭板10、第二封闭板焊接连接,第一槽钢8与第二槽钢9上下两端分别通过第三封闭板12、第四封闭板13焊接连接;从而在第一槽钢8、第二槽钢9、第一封闭板10、第二封闭板、第三封闭板12和第四封闭板13之间形成空腔;如图3、图4与图5所示,第一槽钢8、第二槽钢9沿长度方向上设置有供叉车4上的货叉穿过的两个叉车孔7。
48.如图7所示,为了保证叉车孔7处的强度、刚度与抗弯性能,在两个叉车孔7的处分别设置一个支撑组件。
49.支撑组件包括第一加强柱14与第二支撑件,第二支撑件包括第二加强板15与第三加强板16,第二加强板15包括第一横板、两个一端连接在第一横板两侧的斜板以及通过两个斜板另一端分别向外水平延伸而成的第二横板;两个斜板另一端通过第三加强板16连接,并且第三加强板16的长度尺寸大于第一横板的长度尺寸,从而使得第二加强板15与第三加强板16形成正梯形结构,第一加强柱14设置在正梯形结构内,第一加强柱14为矩形筒
状结构,且其内部的高度等于叉车孔7的高度。
50.第一加强柱14前端面的上下两端与后端面的上下两端分别与第二槽钢9和第一槽钢8焊接;第三加强板16和第一横板左右两端的前后两边分别与第二槽钢9和第一槽钢8连接。
51.为了保证第一加强柱14上端的受力可以传递到搬运支撑件6下端,实现力的分摊,第一横板、第三加强板16均与第一加强柱14贴合。
52.本实用新型的工作原理是通过焊接支撑组件来弥补因开叉车孔7而导致的抗弯截面的不足:
53.在没有开叉车孔7之前,搬运支撑件6的抗弯截面的惯性矩ia如图8所示。开了叉车孔7后,但是又没有焊接支撑组件的情况下,抗弯截面的惯性矩ib如图9所示。由于截面s
b2
被切除,导致惯性矩只能由s
b1
来提供,因此ib≤ia。惯性矩是描述截面抵抗弯曲的性质的物理量,说明开了叉车孔7后的搬运支撑件6抗弯性能被削弱了,并且从截面sa到s
b1
可知惯性矩ib被削弱的非常严重。
54.为了弥补这一抗弯截面的损失,该方案采用焊接支撑组件的方法,在图9的基础上增加焊接第一加强柱14、第二加强板15和第三加强板16,此时托梁抗弯截面的惯性矩ic如图10所示,由于抗弯截面增加了s
c1
部分,为削弱了的抗弯截面弥补了一部分抗弯性能,当弥补的面积s
c1
足够多时,惯性矩ic将恢复到原来的惯性矩ia。这样就保证了搬运支撑件的抗弯性能。