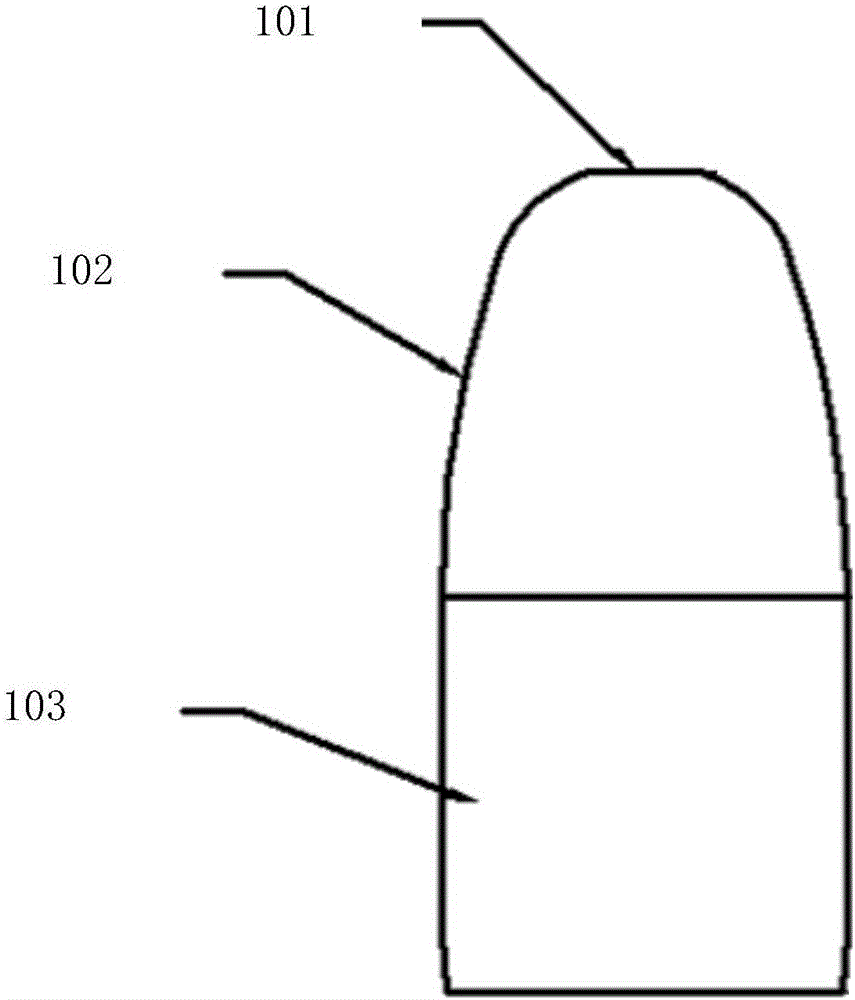
本发明涉及军工
技术领域:
,特别是涉及一种易碎弹芯及其制造方法。
背景技术:
:现在的枪支子弹主要是利用火药爆炸产生推力的原理。在子弹结构中,通过将弹芯装配到装有火药的弹壳中,当枪机扣动板机,弹芯在枪膛内被火药爆炸产生的推力发射出枪管,从而对目标进行杀伤。如今随着世界各国反恐形势越来越严峻,反恐用枪弹的需求越来越紧迫,越来越大。举例来说,在飞机上执行反恐任务时,必须能够避免造成对飞机机体的破坏,从而造成更大的人员伤亡,但也要同时能够确保对恐怖分子起到一定的杀伤作用。并且,在发生人质挟持时,当情况危急至不得不对绑匪进行杀伤时,必须能够保证射向绑匪的弹芯不会穿过绑匪的身体之后对绑匪身后的人群造成二次伤害。传统的弹芯采用钢材做材质,并采用机加工的方法进行加工,钢材比较坚硬,不易碎,其穿透性能较好,在需要降低其穿透性能时,必须将弹芯的口径加大,如此则会增大弹芯的威力(停止作用增大),当误射其他物体(如飞机)或人时,更会造成更大的伤害。因此,现有的钢弹芯不能满足反恐任务的要求,且其加工成本较高,加工难度较大。技术实现要素:有鉴于此,本发明提供了一种易碎弹芯及其制造方法,可在确保具有一定杀伤力的前提下降低弹芯的穿透性能和威力,并能降低制造成本。本发明提供一种易碎弹芯的制造方法,包括以下步骤:将预定重量的混合料和MIM成型剂置于高速混合机中,在预定温度和转速中进行混合以形成喂料,其中混合料包括钨粉和碳化钨粉;将喂料置于双螺杆机中反复挤出预定次数;将挤出的喂料加入注塑机料斗中以进行电加热形成熔融状态,并将熔融状态的喂料注射入模腔,得到预定形状的易碎弹芯。其中,将预定重量的混合料和MIM成型剂置于高速混合机中,在预定温度和转速中进行混合以形成喂料的步骤具体包括:将高速混合机的转速设定为100r/min,在混合料温度升至130~140℃时,将转速设定为300~400r/min,在混合料的温度达到140-150℃时,保持转速不变,直至高速混合机出现剧烈抖动并持续至少3-6分钟后,停机观察是否还存在未熔化的MIM成型剂,若有,则延长混合时间至不再有未熔化的MIM成型剂方可形成喂料。其中,预定次数为2或3次。其中,钨粉在混合料中所占含量为3%~10%,碳化钨粉在混合料中所占含量为90%~97%。其中,MIM成型剂包含石蜡、低密度聚乙烯、聚丙烯、巴西棕榈蜡、硬脂酸,且MIM成型剂的含量调节范围为混合料的6%~8%。本发明进一步提供一种易碎弹芯,易碎弹芯呈柱状,包括由易碎材料一体成型的顶部、弧形连接部以及底座,顶部设置有第一圆形平面,底座设置有与第一圆形平面相对的第二圆形平面,第一圆形平面的直径小于第二圆形平面的直径,第一圆形平面上设置有呈花键型的开孔。其中,易碎弹芯的尺寸设置为适用于口径小于或等于9毫米的枪械。其中,易碎材料包括钨粉、碳化钨粉和MIM成型剂,其中钨粉和碳化钨粉组成混合料,钨粉在混合料中所占含量为3%~10%,碳化钨粉在混合料中所占含量为90%~97%,且MIM成型剂的含量调节范围为混合料的6%~8%。其中,MIM成型剂包括石蜡、低密度聚乙烯、聚丙烯、巴西棕榈蜡、硬脂酸。其中,底座的长度设置为占易碎弹芯总长度的41.7%。区别于现有技术,本发明通过注射成型的方式来生产易碎弹芯,通过对钨粉、碳化钨粉以及MIM成型剂进行高混形成喂料之后,将熔融状态的喂料注射入模腔,从而得到预定形状的易碎弹芯,故相对于传统的机加工的方法进行加工而言,本发明通过注射成型的方式能够准确控制易碎弹芯的尺寸,更有利于大批量生产,且避免了机加工对机床造成磨损,可降低加工成本,更可提高原材料的利用率,而生产出的易碎弹芯相对钢弹芯而言,强度较低,可大幅度降低穿透性能,且可以做成小口径,以降低其威力。附图说明图1是根据本发明实施例的易碎弹芯的制造方法的流程图;图2是本发明的易碎弹芯的侧视图;图3是本发明的易碎弹芯的俯视图。具体实施方式首先请参见图1,图1是根据本发明实施例的易碎弹芯的制造方法的流程图。如图1所示,本发明所揭示的易碎弹芯的制造方法包括以下步骤:步骤S101:将预定重量的混合料和MIM成型剂置于高速混合机中,在预定温度和转速中进行混合以形成喂料。其中混合料包括钨粉和碳化钨粉。其中,钨粉在混合料中所占含量优选为占3%~10%,碳化钨粉在混合料中所占含量优选为占90%~97%。并且,MIM成型剂具体可包含石蜡、低密度聚乙烯、聚丙烯、巴西棕榈蜡、硬脂酸,且MIM成型剂的含量调节范围为混合料的6%~8%。在本步骤中,更可优选将高速混合机的转速设定为100r/min,在混合料温度升至130~140℃时,将转速设定为300~400r/min,在混合料的温度达到140-150℃时,保持转速不变,直至高速混合机出现剧烈抖动并持续至少3-6分钟后,停机观察是否还存在未熔化的MIM成型剂,若有,则延长混合时间至不再有未熔化的MIM成型剂方可形成喂料。步骤S102:将喂料置于双螺杆机中反复挤出预定次数。其中该预定次数可优选为2或3次。步骤S103:将挤出的喂料加入注塑机料斗中以进行电加热形成熔融状态,并将熔融状态的喂料注射入模腔,得到预定形状的易碎弹芯。在本发明中,模腔的形状可根据需要设计,基于易碎弹芯的设计要求,可将模腔的形状设计为呈柱状,并在模腔内进行特定的细节设计,使得生产出来易碎弹芯具有如图2和图3所示的结构,其中图2是本发明的易碎弹芯的侧视图,图3是本发明的易碎弹芯的俯视图。根据图2和图3所示,本发明进一步提供一种易碎弹芯,易碎弹芯呈柱状,包括由易碎材料一体成型的顶部101、弧形连接部102以及底座103,顶部101设置有第一圆形平面,底座103设置有与第一圆形平面相对的第二圆形平面,第一圆形平面的直径小于第二圆形平面的直径,第一圆形平面上设置有呈花键型的开孔104。为降低易碎弹芯的威力,可在模具设计时减小易碎弹芯的尺寸,使得易碎弹芯的尺寸设置为适用于口径小于或等于9毫米的枪械。具体而言,易碎材料包括如以上制造方法所揭示的钨粉、碳化钨粉和MIM成型剂,其中钨粉和碳化钨粉组成混合料,钨粉在混合料中所占含量为3%~10%,碳化钨粉在混合料中所占含量为90%~97%,且MIM成型剂的含量调节范围为混合料的6%~8%。并且,MIM成型剂包括石蜡、低密度聚乙烯、聚丙烯、巴西棕榈蜡、硬脂酸。其中,底座103的长度设置为占易碎弹芯总长度的41.7%。顶部101、弧形连接部102二者设计为占易碎弹芯总长度的58.3%。在本发明中,易碎弹芯在结构设计时将弹芯头部位置设计为花键形的开孔104,可保证易碎弹芯在发射出枪管前后具有一定强度的同时不能击穿靶板(靶板设置为具有飞机机舱同样硬度之材质),开孔104可使得着靶后易碎弹芯易碎裂。花键形孔的形状尺寸在注射成型的时候由模具保证。通过以上制造方法获得的易碎弹芯具有一定的强度,在易碎弹芯出枪膛的过程中可确保其不被膛线划伤,而影响精度,同时在出了枪膛后能够高速旋转保证一定的杀伤能力,能打入凝胶(凝胶用于模拟人体)内部,但又不能击穿靶板。以下可参见表1,表1示出易碎弹芯的性能指标:表1序号检测项目技术要求检测仪器1密度(g/cm3)8.30-8.45分析天平2单重(g)8.05-8.20电子天平在本发明中,所制造的易碎材料相对于普通的钢材,强度要低很多,可以大幅度的降低穿甲能力,在与靶板的撞击过程中能够很快的变形并碎裂,导致不能实现靶板的穿透,并能避免易碎弹芯反弹造成的误伤。且由于易碎弹芯未经过粉末冶金工艺的最终烧结工序,所以它的强度较烧结金属材料低的多,在与靶板的撞击过程中较容易破碎,但其成型后的强度又可以保证对凝胶的穿入深度满足要求,从而满足对敌对目标的杀伤性。且发明人经过大量试验,确定了易碎弹芯的形状结构,使得小口径易碎弹芯兼具良好的破碎性能、出膛强度和杀伤性能。易碎弹芯采用柱体结构,易碎弹芯顶部101设计为有一定面积的第一圆形平面,在第一圆形平面上开有花键形的孔,有利于穿甲过程中降低易碎弹芯的穿甲能力,同时加速易碎弹芯在着靶过程中的变形和破碎,使其形状不完整。易碎弹芯仅设有一个弧形连接部102,在穿甲过程中发生破碎时,弧形连接部102有利于提高穿甲阻力,降低弹芯穿甲率。易碎弹芯的底座103呈圆柱状,可用于压入弹壳内部,便于装弹,底座103具有与第一圆形平面相对的第二圆形平面,第二圆形平面在火药爆炸之后,受力作用从而推动易碎弹头飞出枪管。综上所述,本发明通过注射成型的方式来生产易碎弹芯,通过对钨粉、碳化钨粉以及MIM成型剂进行高混形成喂料之后,将熔融状态的喂料注射入模腔,从而得到预定形状的易碎弹芯,故相对于传统的机加工的方法进行加工而言,本发明通过注射成型的方式能够能够准确控制易碎弹芯的尺寸,更有利于大批量生产,且避免了机加工对机床造成磨损,可降低加工成本,更可提高原材料的利用率,而生产出的易碎弹芯相对钢弹芯而言,强度较低,可大幅度降低穿透性能,且可以做成小口径,以降低其威力。以上所述仅为本发明的实施例,并非因此限制本发明的专利范围,凡是利用本发明说明书及附图内容所作的等效结构或等效流程变换,或直接或间接运用在其他相关的
技术领域:
,均同理包括在本发明的专利保护范围内。当前第1页1 2 3