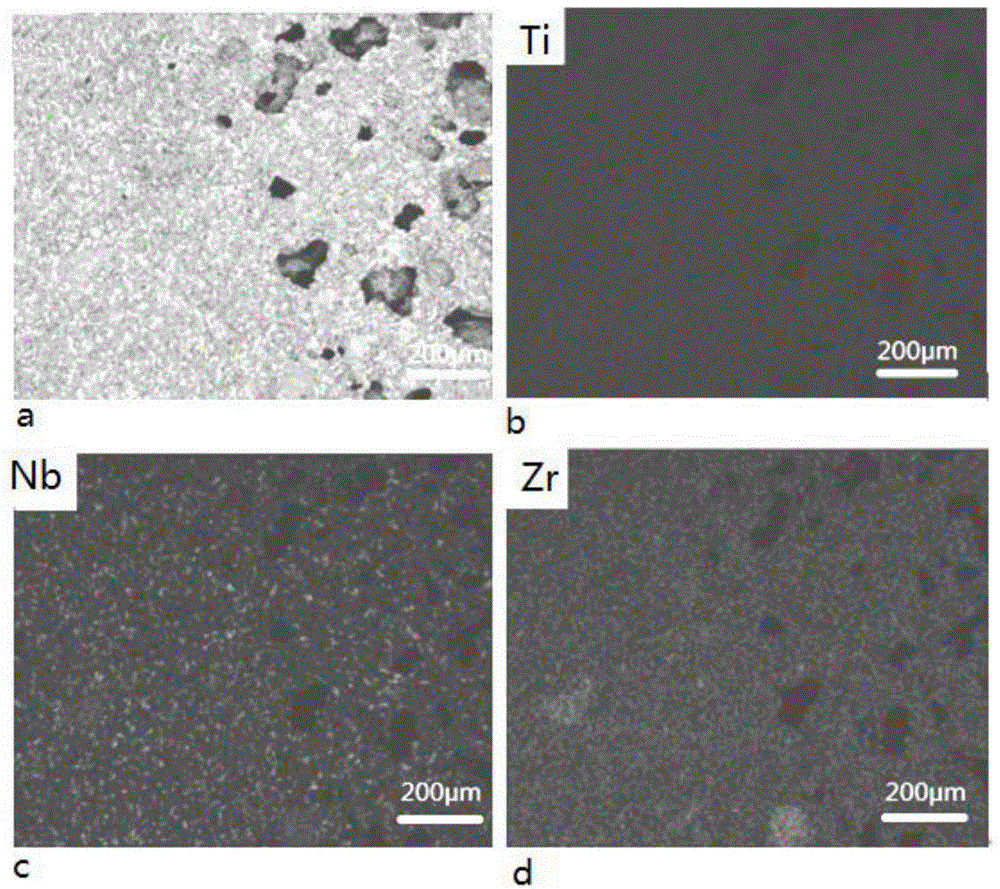
本发明涉及骨植入材料制备
技术领域:
,尤其涉及一种多孔ti-nb-zr复合人造骨植入材料及其制备方法和应用。
背景技术:
:生物医用钛合金因其良好的力学性能、耐生物腐蚀性能、高疲劳强度和低弹性模量以及良好的生物相容性等优点,在临床骨替换和骨修复材料中得到广泛应用。但是钛合金的惰性天然属性,使其在植入人体后无法主动适应自然的骨组织和生理环境,两者之间只是简单的锁合。而且钛合金较高的弹性模量与自然原生骨呈现出生物力学不相容会造成应力屏蔽,引起自然骨组织功能的退化或吸收。因此钛合金不能与骨组织形成有效骨结合、骨整合的能力,并且在长期服役状态下容易造成植入体松动,甚至导致植入失败,从而制约了钛合金在医用领域的广泛应用。而孔隙结构的引入可以降低生物材料的弹性模量,使其符合自然骨组织要求,并且增加了材料表面与植入体内组织、骨细胞和组织体液之间的接触面积,可诱导骨组织的向内生长。例如据文献报道,通过粉末冶金方式制备的多孔ti合金、多孔ti-mg合金和多孔ti-ha复合材料等多孔材料,在生物性能学方面都取得了较好的结果,此类多孔材料的弹性模量和抗弯强度都与人体骨密质较为接近。但材料中孔隙结构的引入将导致材料的力学性能、腐蚀性能的下降,并且随着孔隙特征的变化(孔隙率增加,孔隙尺寸增大)而急剧降低。申请号为cn201510836735.2的中国专利公开了一种ti-39nb-6zr生物医用多孔钛合金及其制备方法,该合金由铌,锆和钛组成,其中铌39w%,锆6w%,余量为钛;钛合金的孔隙率为19.4%-42.1%。采用真空自耗熔炼方法制备ti-39nb-6zr合金铸锭,利用旋转电极雾化法获得球形粉末颗粒;选用100-150目的合金粉末,添加粘结剂,或碳酸氢铵造孔剂和粘结剂,充分混合,压制成压坯;在通氩管式烧结炉中进行压坯烧结,彻底清除粘结剂,或造孔剂和粘结剂,获得多孔合金。该合金弹性模量为3.6gpa~12.4gpa,抗拉强度为123.8mpa~347.5mpa,虽然该专利制备的圆柱体多孔合金具有弹性模量低的优点,但是该多孔合金在制备前期需要对合金进行多次熔炼和雾化成粒,且合金中铌的成分比例较高,造成成本大大增加,限制其推广应用;制备过程中烧结温度较高,升温加热速度较慢,烧结时间较长;材料在制备过程使用粘接剂聚乙二醇,低分子量聚乙二醇具有一定毒性,且烧结温度在300℃才会发生分解,增加了作为人体植入材料的风险。技术实现要素:针对现有技术的不足,本发明的目的在于提供一种径向成分一致,结构变化的外层多孔ti-nb-zr骨硬植入材料及其制备方法和应用。本发明提供的多孔骨硬植入材料使用具有良好生物相容性和高强度、高耐腐蚀性能的ti-nb-zr合金作为基体材料,在外层ti-nb-zr合金材料中适当引入孔隙特性(孔隙率和孔隙直径),不但降低了骨与植入件的弹性模量差异,还促进了两者的结合性和整合性。并且采用脉冲直流活化烧结技术,较常规粉末冶金烧结具有升温降温速率快、保温时间短、制备过程洁净等优点。本发明第一方面,提供一种多孔ti-nb-zr复合人造骨植入材料制备方法,所述制备方法包括以下步骤:步骤(1)将钛(ti)、铌(nb)和锆(zr)混合金属粉末在氩气气氛下放入球磨罐中,将氩气气氛球磨罐放入高能球磨机上进行球磨混粉,然后在真空干燥箱中烘干后得到复合金属粉末a;步骤(2)复合金属粉末a和造孔剂碳酸氢铵粉末在v型混料机中混合得到复合粉末b;步骤(3)利用硬质钢内管与模具固定器外管组合固定于硬质钢模具中,采用两步成型获得压坯材料:先将模具固定器外管取出填入复合粉末b后预压成型获得环状柱体压坯,再将硬质钢内管取出填入复合金属粉末a进行预压获得圆柱体压坯;步骤(4)预压成型的圆柱体压坯在轴向压力下压实后置于脉冲直流活化烧结炉石墨模具中,抽取真空进行活化烧结,并在烧结过程中持续抽真空使得压坯外层的碳酸氢铵完全分解产生的气体排出;(5)烧结完成后随炉冷却至室温,脱模即可得到径向成分一致,结构变化的外层多孔ti-nb-zr复合人造骨植入材料。进一步地,步骤(1)所述复合金属粉末a中铌(nb)质量百分比为8~15%、锆(zr)质量百分比为8~15%、余量为钛(ti)。进一步地,步骤(1)机械球磨过程中不锈球与混合金属粉末质量比为3:1~10:1,加入无水乙醇作为分散剂,在氩气气氛保护下进行球磨,转速为200~700r/min,时间为2~15小时;无水乙醇的加入量足够淹没粉末和球磨球即可。进一步地,所述钛(ti)、铌(nb)和锆(zr)的平均粒径均小于100μm,纯度均≥99.95%;所述造孔剂碳酸氢铵粉末平均粒径为80~450μm。进一步地,步骤(2)在复合粉末b中复合金属粉末a的质量百分比为50~90%、造孔剂碳酸氢铵粉末的质量百分比为10~50%;步骤(2)混料过程在氩气环境下进行,混料机转速为50~150r/min,时间为10~40min。进一步地,步骤(3)复合粉末b预压成型的环状柱体压坯直径范围为由复合金属粉末a预压成型的芯部材料直径范围为整体圆柱压坯的直径与环状柱体压坯直径一致,压坯高度h≤50mm。进一步地,步骤(4)对圆柱体压坯施加的轴向压实压力为50~400mpa,烧结过程中持续抽真空使得炉内真空度保持在10pa以下,脉冲直流活化烧结的目标温度为850~1250℃,烧结时间为5~15min,目标温度的升温速率为50~150℃/min;升温过程中,当温度上升至150℃时,保温1~2分钟使得造孔剂完全分解,再以60~200℃/min升温速率加热至烧结目标温度。作为优选,脉冲直流活化烧结的目标温度为1000~1150℃。进一步地,步骤(5)烧结结束后,烧结炉以20~100℃/min的降温速率冷却至室温。本发明第二方面,提供所述制备方法得到的多孔ti-nb-zr复合人造骨植入材料。本发明第三方面,提供所述多孔ti-nb-zr复合人造骨植入材料的应用。本发明提供的成分纯净、组织均匀、弹性模量低、强度适宜、生物相容性和成骨活性好的径向成分一致,结构变化的外层多孔骨硬植入材料可作为良好的医用植入或者替换材料,适用于制备牙种植体、人工关节、骨创伤产品等材料,其在结构设计与制备方法上均为临床应用提供了相应的研究基础。本发明的特点如下:本发明将硬质钢内管与模具固定器外管组合固定于硬质钢模具中,先取出模具固定器外管,填入定量配比的ti、nb、zr、nh4hco3复合粉末后预压成型,获得环状柱体压坯,按照同样步骤取出硬质钢内管,填入定量配比的ti、nb、zr复合粉末后预压获得柱体压坯,再将两步成型的柱体坯料在一定轴向压力下压实后置于石墨模具中进行脉冲直流活化烧结,最终获得径向成分一致,结构变化的外层多孔骨硬植入材料。采用本发明方法制备的骨植入材料不仅因为其外层的多孔结构具有良好生物活性和适合与人体骨骼相匹配的低弹性模量,还因其芯部致密的结构而具有优异的抗压性能,因此可作为理想的人造骨组织植入材料,适用于制备牙种植体、人工关节、骨创伤产品等材料。采用脉冲直流活化烧结法制备ti-nb-zr复合人造骨组织替换材料,烧结时间短,节能高效,不需要粘结剂,绿色环保。另外,本发明通过控制ti、nb、zr三种成分的配比以及烧结条件,使得最终得到的骨材料内外层结合面无明显的裂纹缺陷,呈现冶金式结合,并且兼具良好力学性能及适宜孔隙结构特征(孔隙尺寸和孔隙率)。与现有技术相比,本发明具有以下有益效果:(1)本发明所述方法制备获得的生物材料组织均匀、径向外层多孔部分弹性模量低、径向芯部致密部分强度适宜、生物相容性良好;径向多孔部分的孔隙特征为细胞粘附、增殖和分化提供了空间,促进材料在植入过程中形成良好的生物骨结合及骨整合能力;并且制备过程中的造孔剂为无毒无害的碳酸氢铵,其在较低温度下就能完全分解,通过烧结炉的真空系统完全挥发,由此获得的多孔部分无任何杂质残留,为材料的洁净性提供了保障;并且本发明所采用的制备方法操作方便、成本低廉,容易实现产业化。(2)本发明制备获得的骨科硬植入材料力学性能和弹性模量与自然原生骨组织匹配度较高,其抗压强度可达180~490mpa、弹性模量为18~48gpa,与骨(弹性模量≤30gpa,抗压强度100~230mpa)匹配度较高,减轻或消除因生物力学不相容从而造成应力屏蔽,引起自然骨组织功能的退化或吸收,从而避免了在长期服役状态中植入体松动,甚至是植入失败的风险。(3)本发明制备获得的骨科硬植入材料以ti-nb-zr作为基体材料,材料中的元素zr相对于传统医用合金中的cr、ni、mn、al和v具有更好的生物相容性和适应性;而且nb和zr在人体环境中容易在材料表面形成一层致密的金红石结构钝化膜,有利于提高材料的耐腐蚀性能。附图说明图1是本发明实施例1中预制坯体流程图;(a)压制环状柱体坯,(b)压制芯部,(c)压制柱体坯,(d)脱模;图2是本发明实施例1中脉冲直流活化烧结后复合材料的x射线衍射图谱;图3是本发明实施例1制备的径向成分一致,结构变化的外层多孔骨硬植入ti-nb-zr复合材料sem图。具体实施方式下面结合实施例对本发明的技术方案进一步详细说明,具体描述仅用于解释本发明而不是限定本发明。实施例1本实施例提供一种径向成分一致,结构变化的外层多孔ti-15nb-15zr骨硬植入材料的制备方法,具体包括以下步骤:(1)将平均粒径为30μm、纯度为99.95%的钛、铌和锆金属粉末按照名义质量百分比钛70%、铌15%和锆15%进行称量放入球磨罐体内,加入无水乙醇和球料质量比为5:1的不锈钢球并密封罐体,该步骤全程在手套箱中操作;机械球磨转速为280r/min,时间为8小时;球磨完成后在真空干燥箱中60℃烘干获得复合金属粉末a。(2)将复合金属粉末a和平均粒径为80~450μm分析纯度的造孔剂碳酸氢铵(nh4hco3)粉末在v型混料机中以转速150r/min混合30min得到复合粉末b;在复合粉末b中,复合金属粉末a的质量百分比为80%、造孔剂碳酸氢铵粉末的质量百分比为20%;(3)利用硬质钢内管与模具固定器外管组合固定于硬质钢模具中,然后将模具固定器外管取出填入复合粉末b,手工压实后取出模具固定器外管得到环状柱体压坯,再将硬质钢内管取出填入粉末a手工压实后获得圆柱体压坯,对预压成型的圆柱体压坯整体施加50mpa的轴向压力后脱模(如图1所示);(4)将脱模后的圆柱体压坯置于脉冲直流活化烧结炉的石墨模具中,然后对炉内抽取真空达10pa,烧结目标温度设定为1050℃,保温时间6min;目标温度升温过程以50℃/min升温速率加热至150℃时,保温1分钟,再以100℃/min升温速率加热至烧结目标温度1050℃。烧结结束后以50℃/min的降温速率冷却至室温。在活化烧结过程中持续抽真空保持真空度在10pa左右,烧结完成随炉快速冷却至室温后脱模即可得到径向成分一致,结构变化的外层多孔ti-15nb-15zr骨植入材料。图2为实施例1所制备材料的x射线衍射(xrd)分析。通过检测可知:制备材料相组成单一,没有出现造孔剂及污染物杂相,可保证其作为骨植入材料的生物安全性。利用gb/t7314-2017《金属材料室温压缩试验方法》对制备材料的力学性能进行检测。结果表明:其抗压强度为368mpa、弹性模量为29gpa,与自然骨的(弹性模量≤30gpa,抗压强度100~230mpa)匹配度较高。图3为实施例1所制备材料的横向截面扫描电子显微镜形貌图(sem)及化学成分eds能谱图。图3(a)的结果表明:ti-15nb-15zr合金材料芯部的致密度高达93.8%,外层由于造孔剂碳酸氢铵的分解产生了均匀、贯通的孔隙,形成了孔隙率为32%的多孔结构ti-15nb-15zr合金外层,并且复合材料内外层结合面无明显的裂纹缺陷,呈现冶金式结合,为该材料的力学协同性能提供保证。图3(b-d)的eds分析表明:复合材料中钛、铌、锆元素分布均匀,无明显的成分偏析,保证了材料的组织均匀性。对该材料采用iso-2738标准检测可知,其多孔层的孔隙平均直径为320μm,有利于骨细胞粘附、生长及增值,并且孔间呈现外贯通相连的生物网状结构,不仅能方便骨细胞向内生长和毛细血管的形成,还能在材料承受外力时协同变形吸收更多的能量。实施例2本实施例提供一种径向成分一致,结构变化的外层多孔ti-18nb-15zr骨硬植入材料的制备方法,具体包括以下步骤:(1)将平均粒径为30μm、纯度为99.95%的钛、铌和锆金属粉末按照名义质量百分比钛67%、铌18%和锆15%进行称量放入球磨罐体内,加入无水乙醇和球料质量比为5:1的不锈钢球并密封罐体,该步骤全程在手套箱中操作;机械球磨转速为400r/min,时间7小时;球磨完成后在真空干燥箱中60℃烘干获得复合金属粉末a。(2)将复合金属粉末a和平均粒径为80~450μm、分析纯度的造孔剂碳酸氢铵(nh4hco3)粉末在v型混料机中以转速50r/min混合20min得到复合粉末b;在复合粉末b中,复合金属粉末a的质量百分比为80%、造孔剂碳酸氢铵粉末的质量百分比为10%;(3)利用硬质钢内管与模具固定器外管组合固定于硬质钢模具中,然后将模具固定器外管取出填入复合粉末b,手工压实后取出模具固定器外管得到环状柱体压坯,再将硬质钢内管取出填入粉末a手工压实后获得圆柱体压坯,对预压成型的圆柱体压坯整体施加100mpa的轴向压力后脱模;(4)将脱模后的圆柱体压坯置于脉冲直流活化烧结炉的石墨模具中,然后对炉内抽取真空达10pa,烧结目标温度分别设定为850℃、900℃、950℃和1000℃,保温时间10min;目标温度升温过程以100℃/min升温速率加热至150℃时,保温2分钟,再以100℃/min升温速率加热至烧结目标温度。烧结结束后以50℃/min的降温速率冷却至室温。在活化烧结过程中持续抽真空保持真空度在10pa左右,烧结完成随炉快速冷却至室温后脱模即可得到径向成分一致,结构变化的外层多孔ti-18nb-15zr骨植入材料。将本例中不同烧结目标温度所制备的样品进行gb/t7314-2017《金属材料室温压缩试验方法》力学性能检测,结果如表1所示。表1不同烧结温度对复合材料力学性能的影响烧结温度(℃)弹性模量(gpa)抗压强度(mpa)85020.4212.590018.6267.995019.7329.2100022.3341.7由测试结果可知,本实施例所制备的材料抗压强度为212~342mpa、弹性模量为19~22gpa,与自然骨(弹性模量≤30gpa,抗压强度100~230mpa)匹配度较高。其中,材料的力学性能与烧结温度有着密切关系:随着烧结温度的提高,复合材料的弹性模量呈现先降低后升高的趋势,而抗压强度随着烧结温度的升高而提高。当前第1页12