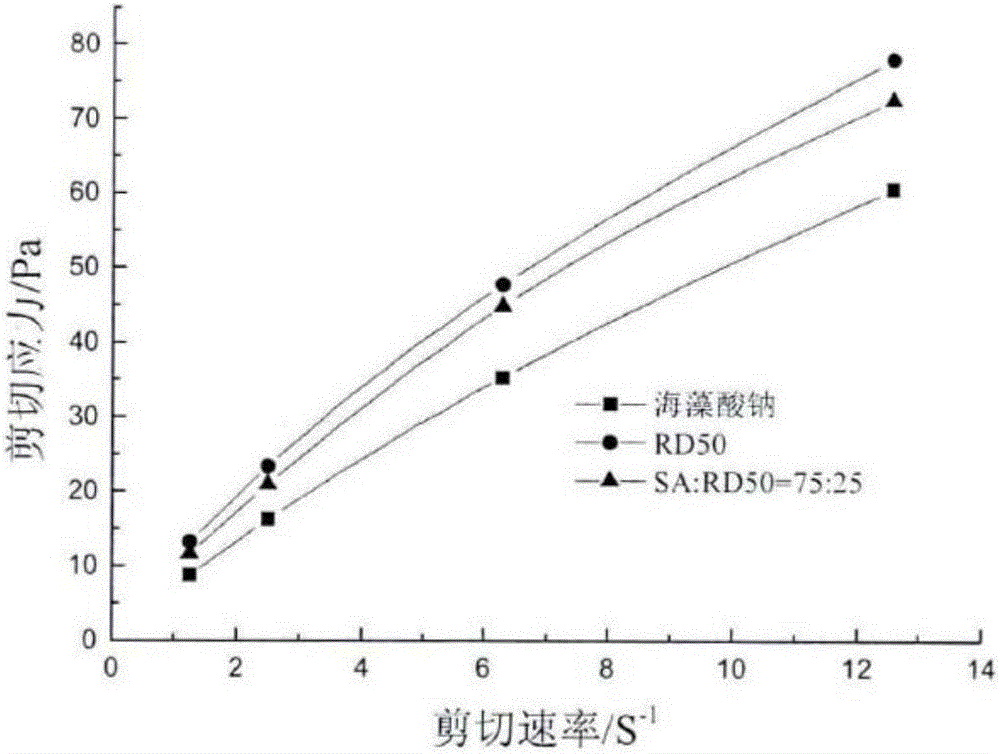
本发明涉及印染
技术领域:
,特别涉及一种涤、棉布的分散、活性染料二相法印花方法。
背景技术:
::涤、棉织物是用涤纶纤维和棉纤维混纺纱线织成的各种织物,具有外观挺刮、耐穿、耐用、尺寸稳定、易洗快干等优点,适宜制作各种衣服。目前市场上绝大部分的涤、棉都是采用涂料印花,这对于大面积印花的手感及印花部分的刷洗牢度都不能达到客户要求。为改善这种工艺,出现了分散/活性染料的印花工艺,分散/活性染料的印花工艺根据染料的不同,可分为两大类,一相法和二相法。一相法也称全料法,顾名思义,就是把分散染料、活性染料、碱剂及其他助剂全部放在一起制成色浆进行印花、固色、水洗的工艺。此法是目前应用最广泛的方法,工艺比较简单:一相法工艺流程:半成品—印花—烘干—固色一水洗—皂煮—水洗―烘干。常用的色浆处方如下:此工艺最需要注意的地方是由于色浆中含有碱剂,所以色浆不是很稳定,而且高温焙烘时部分碳酸氢钠会分解,色浆中pH值升高,某些分散染料对碱不稳定,容易发生色变,固色率低,甚至结构发生变化,因此要选择耐碱性良好的分散染料。此外,在碱剂的存在条件下涤棉织物经高温焙烘后,织物容易泛黄(主要是棉纤维),因此碱剂的用量要严格控制,且活性染料要选用热稳定好、固色率高的染料。二相法印花是色浆中不加碱剂,一般也不加尿素,先对分散染料进行高温焙烘固色,活性染料则在印后经轧碱液进行短蒸固色。两相法印花适用于反应性高的活性染料(如乙稀砜型、双活性基型活性染料),借助浓碱的作用,在短时间内高温汽蒸的条件下进行固色。常用的色浆处方如下:快速蒸化轧碱剂处方如下:两相法印花的最主要优点是色浆中不含碱剂,色浆稳定,大大扩大分散染料的选择,色泽鲜艳,色光纯正,白地沾污和织物泛黄都较好。同时大幅度降低尿素用量,减少污染。为防止印花后白地沾污的问题,还可以选用不耐碱的分散染料,后处理采用热碱水洗工艺,破坏分散染料的浮色,防止沾污。两相法的主要缺点是工艺流程长,色泽难以控制;同时后轧碱液容易引起花纹渗化。传统法的轧液率为70—80%,活性染料固色不充分;带液率太高,易造成花型渗化、不清晰。印染效果还受糊料和蒸化设备影响:印花原糊的作用是使色浆具有一定的粘度和流变性。它由亲水性高分子物糊料调制而成,常用的糊料有淀粉、淀粉降解产物(白糊精与黄糊精)、淀粉醚衍生物、海藻酸钠(或铵)、羟乙基皂荚胶、龙胶、纤维素醚、合成高分子化合物等。用水、火油与乳化剂制成的乳化糊,有时也用作印花原糊。印花原糊对色浆中的化学药剂应具有良好的稳定性,不与染料发生作用,对纤维有一定的粘附力并易于从织物上洗去。印花色浆的粘度决定于原糊的性质,印花时如果色浆粘度下降太多则难以印得精细的线条,粘度太大则色浆不易通过筛网的细孔。蒸化亦称汽蒸。印上色浆的织物经烘干后进行蒸化。蒸汽在织物上冷凝,使织物温度升高、纤维和糊料溶胀、染料溶解并上染,有些染料在蒸化过程中还发生化学反应。印花染料由于糊料的存在,上染过程较为复杂,蒸化时间要比轧染的蒸化时间长。蒸化设备有三种:①高压汽蒸箱:将织物悬挂在支架上,推入箱体进行蒸化;②连续蒸化机:把织物成环状悬挂在长环上,长环缓缓前进,连续蒸化;③各种快速蒸化机。汽蒸箱和悬挂式连续蒸化机适用于蚕丝织物、针织物和合成纤维织物。汽蒸箱在密闭条件下进行蒸化,但不能连续生产。蒸化条件随染料和纤维性质而异。对还原染料的印花织物蒸化时,应将蒸化室中的空气驱除。分散染料的涤纶印花织物,可在密闭汽蒸箱中以130℃左右进行蒸化,或在常压下用175℃左右的过热蒸汽蒸化,也可在200℃左右过热空气焙烘固色。对于上述任一技术条件进行改善创新,均可对印花效果造成较大影响,现有技术中。《印染》(2006No.7)作者:贾景文,王玉民:涤棉织物分散/活性两相法印花工艺,此文章公开了分散/活性两相法印花工艺条件,优选了染料和固色碱剂,与全料法印花工艺相比,前者固色率高,色牢度可提高0.5~1级,生产易控制;提出两相法印花中轧碱高温快速蒸化的技术关键是设备,并给出两次皂洗的工艺条件,以解决白地沾污问题。其工艺条件:白布预定形(温度190℃、车速45m/min)→印花→焙烘(195℃、60s)→轧碱快速蒸化→皂洗(第一次)→皂洗(第二次)→拉幅上软(温度170℃,车速45m/min)→预缩。工艺处方如下:(1)印花处方/g·kg-1与变性淀粉混合糊适量(2)快速蒸化轧碱剂处方/g·L-1轧液率50%~60%,蒸化130~135℃×50s。再如,现有技术中,中国专利公开号CN104562800A(2015.04.29)公开涤棉织物印花工艺,工艺流程如下:预定形:白布预定形温度190℃,车速45m/min。印花:印花处方:分散染料30-40g/kg、雷玛素活性染料40-45g/kg、防染盐S10-15g/kg、柠檬酸10-15g/kg,将上述配方与变性淀粉混合糊混合组成印花色浆印花。烘焙:烘培温度195℃,时间1min。轧碱快速蒸化:轧碱剂处方:纯碱150g/L、食盐100g/L、碳酸钾100g/L、36波美度烧碱100mL/L,轧液率50%-60%,蒸化温度130-135℃,蒸化时间50s。皂洗:先用冷水洗,再用3-5g/L的硫酸溶液酸洗,接着用含皂洗剂MR3g/L的溶液进行第一次皂洗,皂洗温度90℃,最后用含烧碱3g/L、皂洗剂MR3g/L的溶液进行第二次皂洗;热水洗:用40-50℃的热水清洗织物。烘干。又如,现有技术中,中国专利公开号CN105113296A(2015.12.02)公开了一种印花糊料及其制备方法,印花糊料,包括以下组分且100g印花糊料中各组分的质量为:羟乙基皂荚胶:5-10g;乳化剂:2-3g;火油:70-75g;尿素:5-6g;水:余量。再如、现有技术中,中国专利公开号CN105696379A(2016.06.22)公开了一种活性染料印花糊料及其制备方法和应用,按照质量百分比由以下组分构成:海泡石10%-20%,煤油6%-12%,乳化剂0.8%-1.6%,尿素8%-12%,防染盐S2%-4%,纯碱2%-4%,余量为水,以上组分含量总量为100%。现有技术中的涤棉分散活性染料全相法印花,由于碱剂的加入,使得分散与活性染料的利用率较低,且稳定性较差。为解决这种技术问题,需要出现一种使用方便,通过刮印含有碱剂与尿素的糊料,经过二次印花涂布再进行常温常压汽蒸的方式,从而达到对活性染料的固色,提高染料的适应性、固色率,以及防沾污性均显著提高的一种涤、棉布的分散、活性染料二相法印花方法。技术实现要素::本发明的目的在于克服现有技术中存在的缺点,提供一种使用方便,通过刮印含有碱剂与尿素的糊料,经过二次印花涂布再进行常温常压汽蒸的方式,从而达到对活性染料的固色,提高染料的适应性、固色率,以及防沾污性均显著提高的一种涤、棉布的分散、活性染料二相法印花方法。为了实现上述目的,本发明提供了一种涤、棉布的分散、活性染料二相法印花方法,其中,包括如下步骤:A、色浆与原糊的制备B、印花C、高温蒸化D、第二次刮印涂布E、常温蒸化F、二次水洗定型。进一步的,色浆制备包括预配软水和增稠剂的步骤:配制增稠剂时用电机搅拌至透明状,然后静置过夜使其充分膨化,配制色浆时,染料先用水溶解,然后再加增稠剂,配置软水:100g六偏磷酸钠1.2g水98.8g;配置增稠剂:100g尿素Xg防染盐S1.3gNaHCO3Yg海藻酸钠8g软水Zg;配置色浆:100g增稠剂78g活性染料xg分散染料yg冷水zg。进一步的,原糊的制备:将海藻酸钠、RD50分别加入到52-65摄氏度蒸馏水,搅拌至透明状,静置过夜,使这两种基本糊料充分膨化,两种基本原糊按质量比混合得海藻混合糊,海藻酸钠:RD50为100-0:0-100进行混合。进一步的,印花处方g/L如下,其中,分散染料为双酯型的分散染料,不耐碱;活性染料为一氯均三嗪型染料。进一步的,第二次刮印的处方g/L如下:进一步的,第二次刮印(含有尿素与碱剂的原糊),①第二次刮印基本原糊采用全海藻。②第二次刮印浆的粘度控制在3000-4000dpa.s.③第二次刮印时进布不能起皱,反面罗纹辊开幅及控制好工艺车速。④控制好活性基本糊涂布时磁棒及刮刀压力。进一步的,两次蒸化条件如下,高温蒸化180℃,8min,常温蒸化102℃,8min。进一步的,二次水洗为皂洗:第一次皂洗工序:轧酸,条件:5g/L醋酸,PH值5.5-6;→多格水洗→皂洗,皂洗剂ALX2g/L,温度90℃,整体车速为35-40m/min;第二次皂洗:三格碱洗,烧碱2g/L,皂洗剂ALX2g/L,→皂洗→三格热水洗→烘干。进一步的,二相法印花后的水洗必须先进行轧酸清洗,然后再进行轧碱皂洗与皂蒸。经试验,在第一次水洗时进行轧酸水洗,可以减少活性染料的沾色,而第二次水洗时,在2g/l烧碱溶液中加入2g/l皂洗剂,95℃洗涤2min白地的白度会大大提高。而对于全相法印花,由于染料的选择问题,首先分散染料不能采用不耐碱的分散染料,所以对于分散染料的棉相沾色不能很好的洗除。从而造成涤棉织物的色泽萎暗、陈旧,浮色可达30%到50%,湿摩擦牢度显著下降。所以对于涤棉织物中棉相沾色来说,浮色越容易去除干净,则其织物的印花鲜艳度则越高。本发明的优点为:使用方便,通过刮印含有碱剂与尿素的糊料,经过二次印花涂布再进行常温常压汽蒸的方式,从而达到对活性染料的固色,提高染料的适应性、固色率,以及防沾污性均显著提高,本发明与印花方法与国内外的对比如下:本发明二相法印花的工艺流程为:印花(制浆是分散与活性染料同浆配制,其中不加尿素与碱剂色浆中只含有软水剂与防还原剂)→高温焙烘(180℃X8min分散染料发色)→第二次刮印(含有尿素与碱剂的色浆,其色浆中不含任何染料)→常温常压汽蒸(102℃X8min)→加酸、冷流水洗、碱洗或皂洗→后整理→成品欧洲国家的传统二相印花为:印花(制浆是分散与活性染料同浆配制,其中不加尿素与碱剂色浆中只含有软水剂与防还原剂)→高温焙烘(195℃X60S,分散染料发色)→轧碱快速蒸化(轧余率50%-60%,蒸化130℃-135℃X50S,快速轧碱处方为36Be.烧碱100ml/l,纯碱150g/l,食盐100g/l,碳酸钾100g/l)→第一次皂洗→第二次皂洗→后整理→成品。我国现在一相法印花为:印花(制浆时分散与活性染料同浆配制,加入适量的尿素与适量的碱剂。软水剂与防还原剂一并加入)→先焙烘,后汽蒸(焙烘180℃X4min,蒸化为102℃X5-6min。)→水洗及皂洗→后整理→成品。可以发现:1、本发明通过刮印含有碱剂与尿素的糊料,通过二次印花涂布再进行常温常压汽蒸的方式,从而达到对活性染料的固色。2,对于全相法印花,此二相法印花对于染料的适应性、分散染料的固色率都在很大的提高,并且工艺操作简便。3,通过采用双酯型分散染料,对于涤棉印花的沾污性要比全相法印花好得多,对于活性染料,此方法可以采用目前工厂使用的染料,而不需要另外采用乙烯砜结构的染料。附图说明:图1为本发明原糊的随剪切速率变化的粘度曲线图2为本发明原糊的流变曲线。具体实施方式:下面结合附图,对本发明进行说明。本发明的整体工艺为:印花(制浆是分散与活性染料同浆配制,其中不加尿素与碱剂色浆中只含有软水剂与防还原剂)→高温焙烘(180℃X8min分散染料发色)→第二次刮印(含有尿素与碱剂的色浆,其色浆中不含任何染料)→常温常压汽蒸(102℃X8min)→加酸、冷流水洗、碱洗或皂洗→后整理→成品。其具体的关键部分如下,包括如下步骤:A、色浆与原糊的制备B、印花C、高温蒸化D、第二次刮印涂布E、常温蒸化F、二次水洗定型。进一步的,色浆制备包括预配软水和增稠剂的步骤:配制增稠剂时用电机搅拌至透明状,然后静置过夜使其充分膨化,配制色浆时,染料先用水溶解,然后再加增稠剂,配置软水:100g六偏磷酸钠1.2g水98.8g;配置增稠剂:100g尿素Xg防染盐S1.3gNaHCO3Yg海藻酸钠8g软水Zg;配置色浆:100g增稠剂78g活性染料xg分散染料yg冷水zg。进一步的,原糊的制备:将海藻酸钠、SP980分别加入到52-65摄氏度软水,搅拌至透明状,静置过夜,使这两种基本糊料充分膨化,两种基本原糊按质量比混合得海藻混合糊,海藻酸钠:RD50为100-0:0-100进行混合。进一步的,印花处方g/L如下,其中,分散染料为双酯型的分散染料,不耐碱;活性染料为一氯均三嗪型染料。进一步的,第二次刮印的处方g/L如下:进一步的,第二次刮印(含有尿素与碱剂的原糊),①第二次刮印基本原糊采用全海藻。②第二次刮印浆的粘度控制在3000-4000dpa.s.③第二次刮印时进布不能起皱,反面罗纹辊开幅及控制好工艺车速。④控制好活性基本糊涂布时磁棒及刮刀压力。进一步的,两次蒸化条件如下,高温蒸化180℃,8min,常温蒸化102℃,8min。进一步的,二次水洗为皂洗:第一次皂洗工序:轧酸,条件:5g/L醋酸,PH值5.5-6;→多格水洗→皂洗,皂洗剂ALX2g/L,温度90℃,整体车速为35-40m/min;第二次皂洗:三格碱洗,烧碱2g/L,皂洗剂ALX2g/L,→皂洗→三格热水洗→烘干。进一步的,二相法印花后的水洗必须先进行轧酸清洗,然后再进行轧碱皂洗与皂蒸。经试验,在第一次水洗时进行轧酸水洗,可以减少活性染料的沾色,而第二次水洗时,在2g/l烧碱溶液中加入2g/l皂洗剂,95℃洗涤2min白地的白度会大大提高。而对于全相法印花,由于染料的选择问题,首先分散染料不能采用不耐碱的分散染料,所以对于分散染料的棉相沾色不能很好的洗除。从而造成涤棉织物的色泽萎暗、陈旧,浮色可达30%到50%,湿摩擦牢度显著下降。所以对于涤棉织物中棉相沾色来说,浮色越容易去除干净,则其织物的印花鲜艳度则越高。试验1:配置4%海藻酸钠、4%RD50原糊和混合原糊(4%海藻酸钠:4%RD50=75:25)随着剪切速率变化的粘度曲线如图1所示,流变曲线如图2所示。海藻酸钠、RD50原糊及拼混原糊均属于假塑性流体,拼混原糊的流变性与RD50的流变性相近。这表明在海藻酸钠糊中加入少量的RD50糊就能很好的改善海藻酸钠糊的流变性。RD50随着剪切速度的增加,粘度急剧降低,与SA相比假塑性更强,结构粘度更大。海藻酸钠随着剪切速率的增大,粘度下降程度不大,与RD50相比,更接近牛顿流体。海藻酸钠的剪切应力与剪切速率基本呈线性关系,接近牛顿流体,粘弹性比RD50糊差。故本发明优选在海藻酸钠与RD50的比例为75:25或者70:30或者80:20,或者85:15。海藻酸钠为SA。试验2:糊料的抱水性就是糊料的水合能力,是指该糊料的膨润性、吸水性及耐稀释性。糊料的抱水性强弱与否,对于活性染料汽蒸固色过程有很大的影响。汽蒸过程中,水在抱水性差的糊料中可自由移动,产生渗化现象;而抱水性太强的糊料,汽蒸过程中会吸收过量的水分,同样可能产生渗化现象。海藻酸钠为SA。如下表各原糊的抱水性由大到小依次为,RD50>混合糊>SA。半小时的上升高度均在0.1-0.2cm之间,各原糊均能满足生产要求。试验3:采用活性RedPB-BR、YellowPB-6G活性染料用不同糊料对棉织物进行印花,印花织物正、反面的K/S值和渗透率如下表织物表面K/S值和渗透率变化趋势是一致的:RD50糊的表面得色量最高,混合糊次之,SA表面得色量最差;RD50糊的渗透性最好,SA次之,混合糊的渗透率最差。试验4:SA、RD50和混合糊料配制的色裝印花后织物的耐摩擦色牢度和耐洗色牢度等级。试验5:SA、RD50和混合糊印花皂洗后的印花织物在50%DMF水溶液中处理前后的K/S值及固色率情况。可以发现三个印花体系的固色率都大于97%,比较试验一:本发明的二相法分散/活性工艺印花,因色浆中不含碱剂与尿素,在印花时,只是在色浆中加入了相应的活性与分散染料,然后对分散染料进行高温焙烘,蒸化温度为180℃,时间为8-10分钟,由于色浆中没有尿素、碱剂,所以在高温焙烘时,对分散染料的染深性没有影响。表一,分散染料在碱性条件下色变与上染率的比较+表示不发生色变,-表示发生色变;√表示上色率正常,X表示上色率下降。对于二相法印花则不产生上述分散染料的色变与上染率变化的问题。二相法能提高染料的固着上染率,其色牢度可较全相法提高0.5-1级。表二,二相法印花与全相法印花活性染料上染率的比较活性染料全相法上染率二相法上染率活性黄PX-6GN70%90%活性黄P-2RN72%91%雅可素红P-4B70%90%活性红K-3B65%85%活性橙K-7R66%86%英彩克隆翠蓝P-GR55%70.5%活性蓝K-GRS60%78%雅可素艳蓝P-3R58%76%雅可素藏青P-2R60%78%英彩克隆黑P-SG60%78%活性黑KN-B55%70%二相法印花时活性染料的上染率基本上与全棉活性印花时活性染料的上染率相同,而涤棉布全相法印花时,由于分散染料与活性染料同浆,色浆中含有1%-1.5%的碱剂,这就造成了分散染料的色变与分散染料上染率下降的。而二相法印花时,色浆中只含有染料及间硝基苯磺酸钠。分散染料的上染基本上不受影响。表三,全相法印花与二相法印花织物的各项牢度比较试验二,本发明二相法印花的工艺流程为:印花(制浆是分散与活性染料同浆配制,其中不加尿素与碱剂色浆中只含有软水剂与防还原剂)→高温焙烘(180℃X8min分散染料发色)→第二次刮印(含有尿素与碱剂的色浆,其色浆中不含任何染料)→常温常压汽蒸(102℃X8min)→冷流水洗、碱洗或皂洗→后整理→成品。而欧洲国家的传统二相印花为:印花(制浆是分散与活性染料同浆配制,其中不加尿素与碱剂色浆中只含有软水剂与防还原剂)→高温焙烘(195℃X60S,分散染料发色)→轧碱快速蒸化(轧余率50%-60%,蒸化130℃-135℃X50S,快速轧碱处方为36Be.烧碱100ml/l,纯碱150g/l,食盐100g/l,碳酸钾100g/l)→第一次皂洗→第二次皂洗→后整理→成品。我国现在一相法印花为:印花(制浆时分散与活性染料同浆配制,加入适量的尿素与适量的碱剂。软水剂与防还原剂一并加入)→先焙烘,后汽蒸(焙烘180℃X4min,蒸化为102℃X5-6min。)→水洗及皂洗→后整理→成品。分散/活性全相法与二相法印花的区别:综上,本发明使用方便,通过刮印含有碱剂与尿素的糊料,经过二次印花涂布再进行常温常压汽蒸的方式,从而达到对活性染料的固色,提高染料的适应性、固色率,以及防沾污性均显著提高,具体为,1、本发明通过刮印含有碱剂与尿素的糊料,通过二次印花涂布再进行常温常压汽蒸的方式,从而达到对活性染料的固色。2,对于全相法印花,此二相法印花对于染料的适应性、分散染料的固色率都在很大的提高,并且工艺操作简便。3,通过采用双酯型分散染料,对于涤棉印花的沾污性要比全相法印花好得多,对于活性染料,此方法可以采用目前工厂使用的染料,而不需要另外采用乙烯砜结构的染料。当前第1页1 2 3