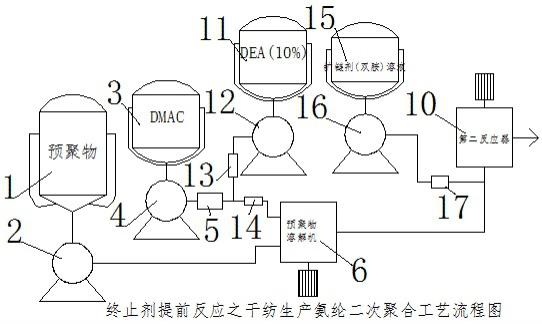
1.本发明属于高分子聚合技术领域,涉及干纺氨纶聚合生产工艺等方面。
背景技术:2.目前干纺工艺生产氨纶,主要分为聚合工序和纺丝工序,其中聚合工序分为预聚合和二次聚合。
3.预聚合由mdi(二苯基甲烷二异氰酸酯)和ptmg(聚四亚甲基醚二醇)按一定比例混合均匀后升温到70℃~90℃发生化学反应,生成异氰酸酯基
‑
n=c=o封端的预聚物(一般mdi摩尔数与ptmg摩尔数之比在mdi:ptmg=1.55~1.75左右),用于生产氨纶的ptmg之平均分子量一般在1600~2000左右,预聚合原料配比中,mdi占质量百分比一般在18%~20%左右。
4.二次聚合是将预聚物溶液和混合胺溶液混合进行进一步的扩链反应,混合胺溶液由扩链剂双胺基有机胺与终止剂单胺基有机胺按一定的比例溶解于溶剂dmac中调配而成(质量浓度一般在4%~10%间),胺基与异氰酸酯基发生化学反应生成含有脲键的高分子量聚合物(以下简称高聚物),形成高聚物溶液;扩链剂有乙二胺、丙二胺、戊二胺等,本说明书中扩链剂以仅使用乙二胺的工艺进行说明(乙二胺eda,分子式:h2n
‑
ch2‑
ch2‑
nh2,以下称eda);终止剂一般使用二乙胺,本说明书中终止剂以仅使用二乙胺的工艺进行说明(二乙胺dea,分子式:ch3‑
ch2‑
nh
‑
ch2‑
ch3以下称dea);一般氨纶聚合工艺之二次聚合,胺基的摩尔数略超过异氰酸酯基nco,因此二次聚合生成的高聚物,其分子由dea与nco结合封端外,还包括相当一部份的来自扩链剂的胺基也起到封端作用(即1个eda分子只有1个胺基反应到高聚物中、另一个胺基因为nco已经消耗完了没有机会反应而连接在高聚物上);二次聚合中混合胺之胺基摩尔数超过nco基团的摩尔数的量、称为过量胺;高聚物中结合的胺基摩尔数占总过量胺的摩尔数百分比在本说明书中称为过量胺附着率;过量胺附着率与二次聚合反应均匀度密切相关,涉及到设备、工艺(如预聚物溶液粘度)等多个方面,过量胺附着率低会导致二次聚合出来之高聚物溶液粘度上升、胶体增多、而生产出来的氨纶纤维中高聚物的特性粘度会下降、氨纶纤维的断裂强度和耐热性均会相应下降。
5.二次聚合生产出来的高聚物溶液添加一定量的功能性助剂(包括抗氧剂、防粘剂、助染剂、消光剂等)后形成纺丝原液,纺丝原液经过计量泵从喷丝孔中挤出进入纺丝甬道,在纺丝甬道的高温(230℃~260℃左右)热风作用下溶剂dmac闪蒸脱除后纺丝原液固化形成氨纶纤维,同时在高温热量作用下,高聚物的特性粘度进一步上升,由原液中的0.7~0.9dl/g上升到1.0~2.0dl/g左右,其本质原因是在甬道高温作用下,二次聚合中dea与nco反应封端生成的脲键分解、释出nco、使得部份高聚物分子的封端基团变成了nco,此部份nco与高聚物中过量胺封端部分的胺基反应结合,使得部份高聚物的分子量进一步上升(此即干纺氨纶生产工艺中的后聚合或三次聚合,以下称三次聚合)。
6.当前常规氨纶生产中,一般使用ptmg分子量约1800左右,而耐热型常规氨纶,为了
提高纤维的耐热性,nco%值控制得比较高(一般达到2.5~2.7%)、而纺丝甬道的进风温度高达260℃以上。nco%值偏高(即mdi使用比例偏大,占预聚物原料质量百分比d在19%~20%左右)会导致氨纶丝的模量偏大、伸长率偏低(断裂伸长率只有450%~550%左右),不利于人体的舒适感,而纺丝甬道温度过高(260℃以上)不仅导致生产氨纶的能耗偏高、也增加了溶剂dmac的热分解量导致dmac酸值偏高,即增加了精制的运行成本也增加了溶剂dmac的消耗量;另外、mdi使用比例上升增加了高聚物间氢键形成量也导致纺丝原液的动态粘度偏高、所以纺丝原液的固含量只能偏低一点(34%~35%左右),这也导致生产能耗偏高;普通非耐热型氨纶,使用的mdi比例稍偏小,占预聚物原料百分比18.5%左右,其伸长率比普通耐热型氨纶要高,断裂伸长率约600%左右,但是因为纤维特性粘度偏低、耐热性差。
技术实现要素:7.本发明的第一项内容是,使用分子量2300~2800的ptmg代替分子量1800左右的ptmg,预聚物mdi使用百分比由常规工艺的18~20%下降到16~17%左右,mdi与ptmg的摩尔比由1.55~1.75调整到2.0;二次聚合工艺中,dea与高聚物中的过量胺之摩尔比按接近1:1来设计(0.99~1.05之间控制);本发明以预聚中mdi使用质量百分比为16%的配比,分子量为2630的ptmg来生产改良型高伸长率耐热氨纶纤维为例进行说明,以使用分子量为1790的ptmg及mdi使用质量百分比为16%的高伸长率耐热氨纶纤维配方工艺、普通非耐热型氨纶配方工艺、普通耐热型氨纶配方工艺为参照对比进行说明,具体配比工艺见表1、表2:表1:不同ptmg分子量及不同mdi使用百分比之预聚合配方工艺对比表1中:mdi分子量为250.26,预聚物分子封端nco量(mol)=2
×
mdi(mol)
‑2×
ptmg(mol)预聚物平均分子量=预聚物量(g)
÷
[预聚物分子封端nco量(mol)
×
0.5];从表1可知,如果使用分子量为1790的ptmg来生产高伸长率耐热型氨纶纤维,当mdi使用质量百分比为16%时,预聚物的分子量高达5886,远远超过普通氨纶工艺的预聚物分子量,意味着其粘度会上升,不利于后继的预聚物溶解及二次聚合的均一性,容易产生胶体、导致高聚物分子量分布过宽等一系列不利状态出现,而使用分子量为2630的ptmg,在mdi使用质量比为16%时,其预聚物的分子量仅有3131,略低于常规氨纶工艺之预聚物的分子量,这有利于后继工序的预聚物溶解均匀、也有利于二次聚合预聚物与扩链剂有机胺的
均匀混合与反应、有利于降低二次聚合生成的高聚物的分子量分布、提高二次聚合过量胺的附着率进而提高甬道内的三次聚合比例以提高氨纶纤维中高聚物的特性粘度;显然,使用分子量为1800左右的ptmg来生产高伸长率的氨纶纤维并不是最合适的选择;此外,改良型高伸长率配方工艺之预聚物中, mdi的摩尔数是ptmg摩尔数的2.0倍,因此预聚物中主要的分子结构是1个ptmg与2个mdi结合而成,预聚物的分子量分布非常均匀(预聚的工艺是低温45℃条件下先混合均匀,此时几乎不反应,混合均匀后再升温到80℃~90℃进行预聚物应,因此反应会非常均匀);以m代表mdi、p代表ptmg,那么预聚物的分子可以用m
‑
p
‑
m来表示,改良型高伸长率配方工艺中之预聚物主要是这种分子形式,因此其分子量分布非常窄而均匀、也不容易产生胶体;普通型耐热配方预聚工艺之摩尔比mdi:ptmg=1.7(见表1),17mol mdi与10mol ptmg反应,可先生成8.5mol的m
‑
p
‑
m预聚物加上1.5mol的ptmg,这1.5mol的ptmg再与1.5~3.0mol的预聚物m
‑
p
‑
m反应,生成各种分子量的分子,均一性不及mdi与ptmg之摩尔比为2:1的配方生成的预聚物好、超高分子量的胶体含量也会更高;另外,普通型氨纶因为mdi使用百分比含量相对偏低、加上氨纶纤维中高聚物的特性粘度也更低,所以其具有较高的伸长率,但是耐热性相对较差,而普通耐热型氨纶,因为mdi使用百分比含量相对偏高(达到19.2%)且氨纶纤维中高聚物特性粘度相对较高,虽然其耐热性还可以、但是伸长率偏低。
[0008]
表2:不同ptmg分子量及不同mdi使用百分比之二次聚合及三次聚合之配方工艺对比表2中:
dea分子量为73.13,eda分子量为60.1;二次聚合合成的高聚物之理论分子量均按36700左右设计;二次聚合高聚物中过量胺附着率均按90%计算;甬道中三次聚合之过量胺反应率是指高聚物中的过量胺再次与nco结合的摩尔数占高聚物中总过量胺摩尔数的百分比;二次聚合高聚物生成量(g) =预聚物量(g)+dea量(g)+eda量(g)过量胺量(mol)=dea量(mol) + 2
×
eda量(mol) —预聚物分子封端nco量(mol)高聚物中过量胺量(mol)=过量胺量(mol)
×
高聚物过量胺附着率二次聚合高聚物封端基团摩尔数(mol)=dea量(mol)+高聚物中过量胺量(mol)二次聚合高聚物理论平均分子量:=二次聚合高聚物生成量(g)
÷
[二次聚合高聚物封端基团摩尔数(mol)
×
0.5];氨纶纤维中高聚物封端基团数量(mol) := 二次聚合高聚物封端基团摩尔数(mol) —高聚物中过量胺量(mol)
×
甬道中三次聚合之过量胺反应率
×
2氨纶纤维中高聚物理论平均分子量:=二次聚合高聚物生成量(g)
ꢀ÷
[氨纶纤维中高聚物封端基团数量( mol)
×
0.5]表2中,dea摩尔数与二次聚合高聚物中过量胺摩尔数之比越接近1,则氨纶纤维中高聚物的分子量越大;甬道中三次聚合之过量胺反应率越大则氨纶纤维中高聚物的分子量越大,此反应率与甬道热风温度、纺丝速度等因素均有一定的关系。
[0009]
从表2可以看出,普通非耐热型配方生产的氨纶,其氨纶纤维中高聚物的理论平均分子量比较低,大约在6.6~9万左右,mdi占主料的18.5%左右;普通耐热型配方生产的氨纶,其氨纶纤维中高聚物的理论平均分子量相对要高,约8.2~14万左右,但mdi占主料的19.2%左右;因为普通耐热型配方生产的氨纶具有更高的氨纶纤维高聚物分子量、因此其耐热性更好,但是因为纤维中高聚物分子量更大加上mdi使用的比例增大,所以其纤维的伸长率不及普通非耐热型氨纶;改良型高伸长率耐热配方1,其设计的二次聚合高聚物理论分子量与普通耐热型配方相同在36700左右,但mdi占预聚物中的质量百分比降到16%以提高氨纶纤维的伸长率,dea与二次聚合高聚物中过量胺的摩尔量之比接近1:1,以提高氨纶纤维中高聚物的理论分子量(或特性粘度),甬道中三次聚合之过量胺反应率达到60%的情况下,其氨纶纤维中高聚物的理论平均分子量即可达到9万左右,而如果该反应率能达到80%的话,则氨纶纤维中的高聚物理论平均分子量可达到18万左右;考虑到改良型高伸长率耐热配方1预聚物中mdi用量只占16%左右,相对于普通耐热型和普通非耐热型配方而言,纺丝原液中的氢键将会大量下降,会导致纺丝原液的动态粘度有较大幅度的下降,为了防止纺丝原液动态粘度有大幅度的下降,改良型高伸长率耐热配方1可使用比普通耐热型配方工艺高一点的原液固含量,或者按表2中改良型高伸长率耐热配方2来设计生产:二次聚合高聚物理论平均分子量由36700上调到40200左右,这样纺丝原液的动态粘度可以适当上升,弥补因为mdi使用比例下降导致的原液中氢键减少带来的原液动态粘度下降,相应的,其氨纶纤维中的高聚物平均分子量可达到10~20万左右。
[0010]
由于本发明设计的改良型高伸长率耐热配方工艺中,dea与高聚物中过量胺的摩尔比接近1:1,因此甬道中三次聚合发生的几率更大、这也就意味着与普通型配方相比要得到相同的氨纶纤维特性粘度的话,可以使用更低的纺丝甬道热风温度或更快的纺丝速度、降低生产成本。
[0011]
本发明的第二项内容是:由常规工艺中eda与dea混合后一起进入第二反应器(见附图1),改为先将终止剂dea与溶解预聚物的溶剂dmac混合后再进入溶解机与预聚物混合溶解均匀,此阶段是nco过量,dea欠量,因此dea能全部反应完成(见附图2),加上dea的浓度非常低(与溶解预聚物的dmac混合后其质量浓度不到0.5%)因此能确保反应均匀;使用此工艺路线,dea对高聚物的封端比常规工艺中在第二反应器中反应封端更均匀,有利于缩小二次聚合生成的高聚物的分子量分布,也有利于二次聚合提高过量胺的附着率(反应越均匀则过量胺附着率越高)、进而提高氨纶高聚物在甬道内的三次聚合比例、提高氨纶纤维的耐热性;从另一个方面来说,二次聚合合成的高聚物,其分子封端有胺基、也有由dea与nco反应生成脲键基团,而三次聚合的基础就是dea与nco生成的脲键在高温下分解释出nco,使得高聚物在甬道内有机会进行三次聚合,如果按常规的工艺,在二次聚合的时候,由于胺是过量的,加上仲胺的反应速度比伯胺的反应速度低(eda是伯胺、dea是仲胺),相当一部份的dea可能没有机会与nco反应而形成原液中的游离胺,这样就会导致甬道内的三次聚合比例下降(能参与三次聚合反应的基团量下降)。
[0012]
附图说明:图1为常规干纺生产氨纶之聚合工序的二次聚合工艺流程图,图2为终止剂在预聚物溶解工序中加入反应之流程图,其中:1为预聚物供应罐、2为预聚物输送计量泵、3为溶剂dmac供应罐、4为dmac供应泵、5为dmac流量计、6为预聚物溶解机、7为混合胺溶液供应罐、8为混合胺供应泵、9为混合胺流量计、10为第二反应器、11为dea溶液供应罐、12为dea溶液供应泵、13为dea溶液流量计、14为管道静态混合器、15为扩链剂(双胺如eda、pda等)溶液供应罐、16为扩链剂溶液供应泵、17为扩链剂溶液流量计。
[0013]
实施方案:首先是dea调配成质量浓度为1%的dmac溶液,经过计量与溶解预聚物的dmac在管道混合器(14)内混合均匀后dea质量浓度下降到0.15%左右,然后质量溶度为0.15%的dea溶液直接进入溶解机(6),将定量计量进入溶解机的预聚物溶解均匀,之后将被dea部份封端的预聚物之溶液输入第二反应器(10)、同时质量浓度为5%的eda溶液经计量后被输送进入第二反应器,在高速搅拌下迅速与部份封端的预聚物溶液混合均匀;检测二次聚合生成之高聚物的特性粘度,达到目标值(即常规工艺时高聚物理论分子量为36700时的特性粘度),此时二次聚合出来的高聚物溶液动态粘度相对于常规工艺会偏低,加上因为mdi使用比例有较大幅度的下降、其在储存过程中的增粘速度也会下降,可考虑适当提高高聚物溶液的浓度来提高其动态粘度以适应纺丝工艺需要,其浓度可由常规耐热型使用的34%~35%上调到36%~37%左右;因为“改良型高伸长率耐热配方”中,dea与高聚物中之过量胺基摩尔比接近1:1,所以达到相同的氨纶纤维中高聚物之特性粘度,需要的纺丝温度低于普通耐热型配方工艺,检测氨纶纤维的特性粘度,如果过高可适当降低甬道进风温度(如由普通耐热型氨纶的
纺丝进风温度260℃下调到255℃),使其氨纶纤维中高聚物之特性粘度与普通耐热型氨纶纤维的接近或略微高一点;因为mdi使用比例由常规耐热配方的19.2%左右下降到16%,远低于普通耐热型氨纶纤维中mdi的使用比例(mdi使用比例下降了3.2
÷
19=16.7%左右),而氨纶纤维中的高聚物之特性粘度与普通型耐热型氨纶的相近或略高,因此按“改良型高伸长率耐热配方”生产的氨纶纤维,其断裂伸长率要高于普通耐热型氨纶纤维、而其耐热性则高于普通非耐热型配方工艺生产的氨纶纤维。