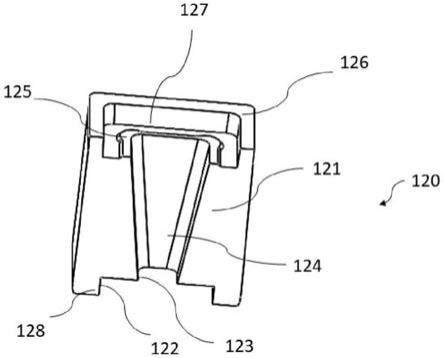
1.本实用新型涉及结构光投射应用领域,更具体地,涉及投射模组壳体。本实用新型还涉及投射模组及包括其的移动终端。
背景技术:2.随着人脸3d解锁技术在手机上的应用,基于结构光的3d深度感知技术已经成为技术开发的热点方向。其中,激光散斑投射模组是结构光深度感知技术的关键设备之一,投射模组的结构性能将直接影响投射模组的使用寿命、使用性能以及投射的结构光的稳定性及图案质量,最终会影响到移动终端的使用性能及客户感受。
3.由于投射模组通常用于例如手机等移动终端内,尺寸相对较小,因此投射模组的壳体侧壁通常较薄,而且由于内部包括发光发热的光源组件或电路,因此会在受到外力或温度变化的情况下,发生结构开裂、损坏或变形等问题,也会由于壳体侧壁较薄,与相应的投射光学元件或壳体基板的接合面较小,而发生脱离接合等问题。
4.为了解决上述问题,需要对投射模组壳体进行改进,从而进一步获得改进的投射模组及移动终端。
技术实现要素:5.本实用新型的目的是通过对投射模组的壳体进行结构改进,从而解决上述问题,提供具有更高强度、稳定性、性能优良的投射模组壳体和投射模组,从而提供客户感受优良的移动终端。
6.根据本实用新型的技术方案的一个方面,提供一种投射模组壳体,包括:
7.主体,限定纵向轴线,包括第一端、第二端、主体侧壁和由主体侧壁围绕的沿所述纵向轴线贯穿主体的中空腔体,所述第一端用于接合投射光学元件;
8.基板,与所述主体的第二端接合,以与所述主体侧壁、所述投射光学元件一起形成内部腔室,所述基板用于设置光源组件;
9.其中,所述主体侧壁的壁厚形成为从第一端朝向第二端逐渐增大并且不影响所述光源组件发射的光束的传播,以减小所述内部腔室。
10.通过对投射模组壳体侧壁壁厚进行的改进,可增强投射模组侧壁的强度,增大投射模组壳体主体与各部件、元件的接合面积,提高接合强度,缩小投射模组壳体内部腔室的体积,从而减小内部腔室内的空气由于内部空腔内的光源组件或电路发热造成的受热膨胀的影响,提高了结构稳定性。在对投射模组壳体侧壁壁厚改进的同时,应注意避免对投射的光路造成阻挡,避免影响光源组件发射的光束的传播。
11.优选地,所述主体侧壁的内表面从所述第一端朝向所述第二端形成锥面。
12.优选地,所述锥面为四棱锥面。
13.投射模组壳体侧壁壁厚增大的方式可以包括多种方式,例如台阶式逐渐增厚,或曲线形式的连续增厚,本实用新型不受投射模组壳体侧壁壁厚增大方式的限制。
14.优选地,所述锥面与所述纵向轴线的夹角大于等于所述光源组件的半角发散角。
15.优选地,所述壳体还包括逃气孔,所述逃气孔的一端开口在所述主体的第二端处的主体侧壁外表面上,另一端开口通到所述内部腔室。
16.壳体主体的第二端处的侧壁壁厚较第一端处的侧壁壁厚更厚,在第二端处设置逃气孔,对壁强度的影响更小,尤其对第一端与投射光学元件的接合面积的影响减小,增大第一端与投射光学元件的接合强度。
17.优选地,在所述第一端在轴向端面上还包括下沉凹部,用于以嵌入方式接合所述衍射光学元件。
18.优选地,所述基板的朝向所述内部腔室的表面上还包括用于所述光源组件的电路,以及用于与所述主体的第二端的轴向端面接合的台阶部,所述台阶部与所述电路在同一工序中通过相同的工艺设置,以确保其具有相同的水平高度。
19.通常台阶部和电路在相同的工艺下同时形成,由此能够控制为具有相同的高度,从而通过壳体主体的第二端的轴向端面与台阶部接合,第一端与投射光学元件接合,确保与电路接合的光源组件到投射光学元件的距离由壳体主体的结构确定,从而使得不同批次造成的电路的水平高度差异不会对光源组件到投射光学元件的距离造成影响,确保了光学投影的质量。
20.优选地,所述台阶部形成在所述基板上的与所述主体第二端的轴向端面接合的至少三个位置处。
21.本实用新型不受台阶部的形式的限制,只要能够确保台阶部与壳体主体第二端轴向端面接合,并且与电路具有相同的水平高度,任何形式的台阶部都可包括在本实用新型的范围内。
22.根据本实用新型的技术方案的另一方面,提供一种投射模组,其特征在于,用于投射衍射光学图案,包括前面所述的壳体、安装在壳体一端的衍射光学元件以及安装在壳体内部腔室中的光源组件。
23.根据本实用新型的又一方面,提供一种移动终端设备,包括前面所述的投射模组。
24.通过本实用新型的技术方案,能够进一步改善投射模组的结构性能,提供具有更高强度、稳定性、性能优良的投射模组壳体和投射模组,从而提供客户感受优良的移动终端。
附图说明
25.通过阅读参照以下附图所作的对非限制性实施例所作的详细描述,本发明的其它特征、目的和优点将会变得更明显:
26.图1是根据本实用新型的第一实施例的投射模组的立体视图;
27.图2是图1中的投射模组的分解立体视图;
28.图3是图1中的投射模组的壳体主体的立体视图;
29.图4是图3中的投射模组的壳体主体的剖切立体视图;
30.图5是图3中的投射模组的壳体主体的仰视图;
31.图6是图1中的投射模组的基板的立体视图;
32.图7是图6中的投射模组的基板的俯视图;
33.图8是图1中的投射模组的侧视剖切视图;
34.图9是根据本实用新型的第二实施例的投射模组壳体主体的仰视图;
35.图10是根据本实用新型的第三实施例的投射模组基板的俯视图;
36.图11是根据本实用新型的第四实施例的投射模组的侧视剖切视图;
37.图12是根据本实用新型的第五实施例的投射模组的侧视剖切视图。
具体实施方式
38.下面结合附图和实施例对本申请作进一步的详细说明。可以理解的是,此处所描述的具体实施例仅仅用于解释相关实用新型,而非对该实用新型的限定。另外还需要说明的是,为了便于描述,附图中仅示出了与实用新型相关的部分。
39.图1是根据本实用新型的第一实施例的投射模组的立体视图,图2是图1中的投射模组的分解立体视图。同时参照图1和图2,投射模组总体用100标示,投射模组100包括壳体、安装到壳体上的投射光学元件110和安装在壳体内的光源组件140。壳体包括主体120和基板130。投射光学元件110可以为doe匀光片或者散斑结构光doe。
40.图3是图1中的投射模组100的壳体主体120的立体视图,参照图3,可看到,主体120沿纵向轴线延伸,包括第一端126、第二端128、主体侧壁121和由主体侧壁121围绕的沿所述纵向轴线贯穿主体120的中空腔体124,第一端126包括第一凹部127,用于以嵌入方式接合投射光学元件110(参见图1和图2)。中空腔体124的在第一端126处的开口为125。
41.图4是图3中的投射模组壳体主体120的剖切立体视图,通过沿平行于图3中所示的壳体主体120的主体侧壁121的前后表面的平面剖切,去除剖切平面前面的部分获得,由此可看到壳体主体120的中空腔体124、中空腔体124在第一端126处的开口125和在第二端128处的开口123、第一端126处的第一凹部127、第二端128处的第二凹部122以及主体侧壁121的截面。从图4可看到,主体侧壁121的壁厚形成为从第一端126朝向第二端128逐渐增大,中空腔体124的在第一端126的第一凹部127处的开口125大于中空腔体124的在第二端128的第二凹部122处的开口123。但是主体侧壁121的壁厚形成为并不影响光源组件发射的光束的传播,即不会遮挡照射到投射光学元件110上用来形成投射图案的光束。第二端128处的第二凹部122形成用于接纳光源组件140(参见图2)和电路132(参见图6,图7)的空间,另一方面也可避开光束传播的光路,不会遮挡光束。
42.由于主体侧壁121的增大的壁厚,能够减小中空腔体124的体积,由此减小由基板130、主体侧壁121以及接合到主体120的第一端126的第一凹部127中的光学元件110形成的内部腔室的体积,从而减小内部腔室内的空气由于内部腔室内的光源组件140或电路132发热造成的受热膨胀的影响,提高了结构稳定性。
43.图5是图3中的投射模组的壳体主体120的仰视图。图5更清楚地显示了图3中所示的中空腔体124在第二端128处的开口123的形状、第二端128处的第二凹部122的形状以及主体侧壁121在第二端128的端面的形状。同时参照图5和图3,进一步显示了主体120上还包括逃气孔150,逃气孔150的一端开口在主体120的第二端128处的主体侧壁121外表面上,另一端开口在主体侧壁121的第二端128处通到内部腔室中,用于内部腔室中的空气由于受到光源组件140和电路132发出的热膨胀时从逃气孔150逸出,避免由于膨胀造成投射模组壳体损坏。
44.结合图4,从中空腔体124可看出,本实施例中,主体侧壁121的内表面从所述第一端126朝向所述第二端128形成为四棱锥面。为了不影响光源组件140发射的光束的传播,所述锥面与纵向轴线的夹角应大于等于光源组件的半角发散角。
45.图6是图1中的投射模组100的基板130的立体视图,图7是图6中的投射模组100的基板130的俯视图。同时参照图6和图7,基板130包括板体131,和在板体131的朝向内部腔室的表面上的电路132,所述电路132和光源组件140连接,用于为光源组件140供电并且对光源组件140进行控制。电路132为铜层,从图6和图7还可看到,在板体131的朝向内部腔室的表面上还包括台阶部133,台阶部133与电路132为同一工序中通过相同的工艺设置,因此能够制备为具有相同的水平高度。例如,可以在基板130上蒸镀覆盖整个基板表面的铜层,然后通过化学或刻蚀方法去除多余的铜层部分,形成台阶部133和电路132。台阶部133形成在基板130的板体131的朝向内部腔室的表面上,位于与主体120的第二端128的轴向端面接合的至少三个位置处,图中显示为在四个位置处设置台阶部133。
46.图8是图1中的投射模组的侧视剖切视图。图8中可以清楚看出,投射模组壳体主体120的第二端128搁置在基板130的台阶部133上。通过在第二端128和基板130的台阶部133处的朝向内部腔室的表面之间的间隙中注入粘接剂,将投射模组壳体的主体120与基板130粘接在一起。图8中还可看到,光源组件140贴合在基板130的电路132上。光源组件140可通过导电粘接剂粘接在电路132,也可通过焊接与电路132固定连接。由于在设计投射光学元件时,工作距离,即光源至衍射光学元件的距离,是一个重要的设计参数,因此在装配投射模组时需要确保实际的工作距离与设计时的工作距离差异在容许的误差范围之内,以保证投射图案质量。以往的投射模组结构中,由于不同批次制造的基板的电路的厚度会有一些偏差,通常为几微米至十几微米甚至是数十微米,因此会造成不同批次的投射模组的工作距离出现相应的偏差,无法保证投射模组的投射图案质量的一致性。根据本实用新型的技术方案,由于台阶部133和电路132具有相同的水平高度,因此光源组件140与投射光学元件110之间的距离,即工作距离,完全由投射模组壳体主体120的长度决定,由此能够确保投射模组的投射图案质量。
47.图1到图8所示的实施例是本实用新型的优选实施例,可以基于该优选实施例获得多种变型。
48.本实施例中所示的一些结构特征不一定是必需的,比如第一端126处的第一凹部127,可以不包括该凹部,投射光学元件110可直接粘接在第一端126的轴向端面上,同样第二端128处的第二凹部122,在台阶部133足够高或中空腔体124在第二端128处的开口125足够大能够容纳电路132的情况下,也可以不包括在投射模组的壳体中。
49.本实施例中的台阶部133以离散方式设置,其也可以实施为形成与主体121的第二端128的环状轴向端面位置对应的整个台阶部环。或者,不同于本实施例中的台阶部133以离散方式设置在与第二端128的轴向端面的拐角对应的位置处,台阶部133也可以设置与第二端128的轴向端面的边对应的位置处。
50.本实施例中的主体120的外形为四棱柱的形状,但是本实用新型不限于该四棱柱的形状,能够实现投射模组功能的任何形状都在本实用新型范围内。
51.下面描述基于该优选实施例的一些变型实施例,所述变型实施例仅为示例,并非穷举。
52.图9是根据本实用新型的第二实施例的投射模组壳体主体220的仰视图。图9中显示了投射模组壳体主体220的主体侧壁221、第二端处的第二凹部222、逃气孔250以及中空腔体在第二端处的开口225。从图9中可以看出,投射模组的该第二实施例与第一实施例的区别,中空腔体224的在第二端处的开口225为圆形,由此可见中空腔体224的内表面为圆锥面,而第一实施例中则为四棱锥面。
53.本实用新型的中空腔体内表面不限于第一和第二实施例中的锥面形式,也可以以主体侧壁阶梯式增厚的方式、平滑曲线式增厚的方式实现,只要能减小中空腔体的内部体积,由此减小内部腔室的体积,同时又不影响所述光源组件发射的光束的传播的任何主体侧壁增厚方式,都在本实用新型的保护范围内。
54.图10是根据本实用新型的第三实施例的投射模组基板330的俯视图。图10示出了基板330的板体331、在板体331的朝向中空腔体的表面上的台阶部333和电路332。对比图7,图10中第三实施例的基板330与第一实施例的基板130的区别在于,电路332上还设置了散热孔334。散热孔334可以是通孔,也可以在其中设置具有良好导热性能的芯体,例如铜芯或陶瓷芯体,用于将电路332产生的热量快速消散。
55.图11是根据本实用新型的第四实施例的投射模组400的侧视剖切视图。图11中显示了投射模组400的光学元件410、壳体主体侧壁421、基板430、光源组件440和基板430上的电路432和台阶部433。对比图8,图11中第四实施例的投射模组400与第一实施例的投射模组100的区别在于,投射模组100的主体侧壁421并没有采用壁厚形成为从第一端朝向第二端逐渐增大的结构,但是由于仍采用了具有台阶部433的基板430的结构,第四实施例的投射模组400由于台阶部433和电路432具有相同的水平高度,因此光源组件440与投射光学元件410之间的距离,即工作距离,完全由投射模组壳体主体420的长度决定,由此能够确保投射模组的投射图案质量。
56.图12是根据本实用新型的第五实施例的投射模组500的侧视剖切视图。图12中显示了投射模组500的光学元件510、壳体主体侧壁521、基板530、光源组件540和基板530上的电路532。对比图8,图12中第五实施例的投射模组500与第一实施例的投射模组100的区别在于,其基板530没有设置台阶部,但是由于仍采用了主体侧壁521壁厚形成为从第一端朝向第二端逐渐增大的结构,能够减小中空腔体524的体积,由此减小由基板530、壳体主体520以及接合到壳体主体520的第一端的投射光学元件510形成的内部腔室的体积,从而减小内部腔室内的空气由于内部腔室内的光源组件540或电路532发热造成的受热膨胀的影响,提高了结构稳定性。
57.以上描述仅为本申请的较佳实施例以及对所运用技术原理的说明。本领域技术人员应当理解,本申请中所涉及的实用新型范围,并不限于上述技术特征的特定组合而成的技术方案,同时也应涵盖在不脱离所述实用新型构思的情况下,由上述不同实施例中的技术特征或其等同特征进行任意组合而形成的其它技术方案。例如上述特征与本申请中公开的(但不限于)具有类似功能的技术特征进行互相替换而形成的技术方案。