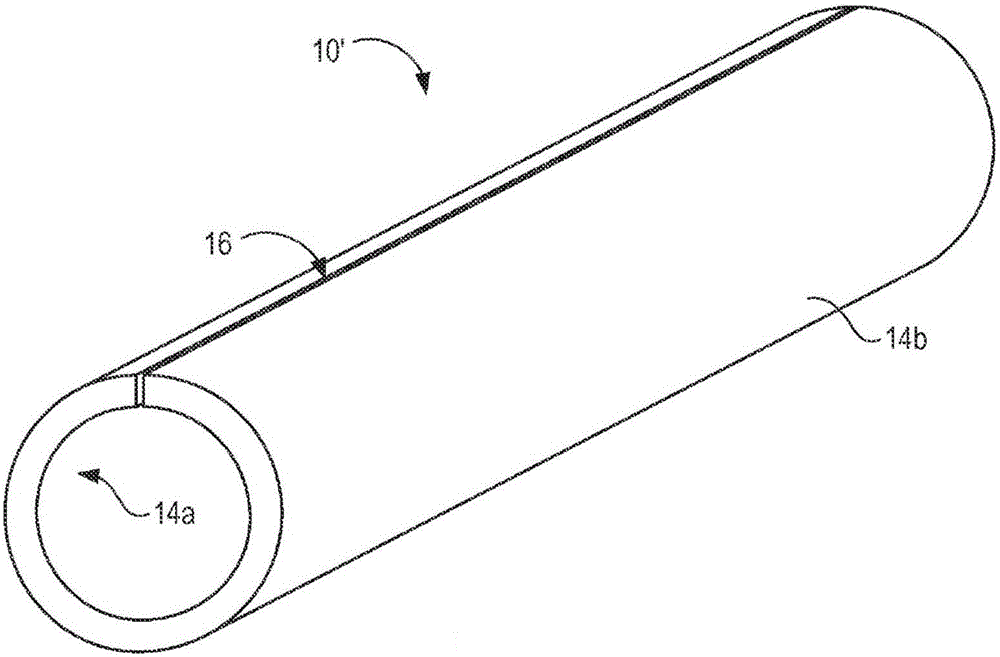
根据PCT第8条和保护工业产权巴黎公约(ParisConventionfortheProtectionofIndustrialProperty)的第4条,这份国际专利申请要求2014年6月27日提交的共同待决的美国临时专利申请号62/018,133的优先权。美国临时专利申请号62/018,133的内容以引用的方式并入本国际专利申请中。发明背景不承认在该
背景技术:
:部分中描述的信息是现有技术。“石油工业专用管材”(OCTG)是石油和天然气工业中使用的管路和管件产品。OCTG包括诸如钻杆、套管和输送管路的产品。钻杆是相对重的测流速管,其在石油和天然气钻井操作中旋转钻头并循环钻井流体。在操作中,钻杆同时经受较高扭矩负载、纵向的压缩和拉伸负载,以及来自于钻井流体的内部压力。另外,可将因非竖直或偏转钻井引起的交替弯曲负载叠加在这些基本负载图案上。套管用于为钻出钻孔加衬里。套管经受纵向拉伸负载、在流体输送期间的内部压力负载,以及来自于周围岩层的外部压力负载。输送管路是用来从井筒输送石油或天然气的管件并经受内部压力负载。在含硫(含硫化氢)、酸性和/或高温度和压力工作条件下的强度和耐腐蚀性是重要OCTG特性。因此,OCTG通常是由高强度耐腐蚀合金(CRA)制成。发明概要本说明书涉及使用流动成型操作来生产耐腐蚀合金管的方法。本说明书还涉及到使用本说明书中描述的方法来制造的耐腐蚀合金管。在一个实例中,一种生产管件的方法包括使耐腐蚀合金板变形以形成中空圆柱形预成型件,所述中空圆柱形预成型件具有位于所述变形的板的两个邻接端部之间的纵向接缝区域。焊接所述纵向接缝区域,以便将所述邻接端部接合在一起。使所述中空圆柱形预成型件流动成型以生产耐腐蚀合金管。在另一实例中,一种生产管件的方法包括使不锈钢板变形以形成中空圆柱形预成型件,所述中空圆柱形预成型件具有位于所述变形的板的两个邻接端部之间的纵向接缝区域。不锈钢包括双相、超级双相或特超级双相不锈钢。激光焊接所述纵向接缝区域,以便将所述邻接端部接合在一起。使所述经激光焊接的预成型件退火。使所述经激光焊接的中空圆柱形预成型件在冷加工温度下流动成型以生产不锈钢管。应当理解,本说明书中描述的本发明不必限于本发明概要中概述的实例。附图简述参考附图,可更好地理解本说明书中描述的本发明的各种特征和特性,其中:图1A是合金板的透视图(未按比例);图1B是由图1A中所示的合金板制成的开缝中空圆柱形预成型件的透视图(未按比例);图1C是由图1B中所示的开缝预成型件制成的闭缝(经焊接的)中空圆柱形预成型件的透视图(未按比例);图2A和图2B是分别示出将合金板变形为开缝中空圆柱形预成型件的三辊弯板设备的示意性透视图和示意性截面图;图3A示出表示在连续辊轧成型操作中的一系列的辊架的一系列示意图;图3B是辊轧成型轧机的示意图,其中一系列的辊架通过漏斗形成型线逐渐将合金条成形为开缝管;图4A是示出将合金板变形为U形中间体的U形压机的示意性透视图;图4B是示出将U形中间体变形为开缝中空圆柱形预成型件的O形压机的示意性透视图;图5是示出使闭缝(经焊接的)中空圆柱形预成型件径向胀大的管件胀大操作的示意性截面图;图6是等温沉淀图,示出在1050℃(1920℉)下退火的第一双相不锈钢(合金2205,其对应于UNS号S31803和S32205)、第二双相不锈钢(合金2304,其对应于UNS号S32304)和超级双相不锈钢(合金2507,其对应于UNS号S32750和S32760)的时间-温度-转变曲线;图7是示出流动成型设备的示意性透视图;图8是示出正向流动成型操作的侧视示意性截面图;图9是示出正反向流动成型操作的侧视示意性截面图;图10是示出流动成型轧辊的示意性透视图;图11是示出流动成型操作中的流动成型轧辊和工件的取向的侧视示意性截面图;图12是示出流动成型操作的示意性透视图,其中闭缝(经焊接的)的中空圆柱形预成型件经变形以生产无缝管;图13是示出流动成型操作的示意性端视图,其中闭缝(经焊接的)的中空圆柱形预成型件使用四辊配置来变形以生产无缝管;图14A是示出流动成型合金625管(右侧)和辊轧且焊接的合金625预成型件(左侧)的照片,辊轧且焊接的合金625预成型件与流动成型成管的预成型件类似;图14B是示出图14A中的流动成型管件的驱动端上的其余焊缝的照片;图15是辊轧且焊接的Ti-15V-3Cr-3Sn-3Al合金预成型件的照片;图16是部分地流动成型的Ti-15V-3Cr-3Sn-3Al合金预成型件/管件的照片;以及图17是辊轧且焊接的超级双相不锈钢(UNSS32760)预成型件的照片。在考虑到根据本说明书的本发明的以下详细描述之后,读者将会理解前述特征和特性,以及其它特征和特性。发明详述油气钻井和提取操作越来越多在涉及更高温度和更高压力、以及更腐蚀性和侵蚀性条件的深井环境中执行。另外,增强回收技术(诸如液压压裂、蒸汽注入、二氧化碳注入、火驱等)在石油和天然气操作中变得常见,并且需要具有更长的使用寿命的可靠设备。操作石油和天然气钻井和提取设备的苛刻的环境条件和操作参数必须抵消重量减小考虑,以及其它经济成本考虑。这些考虑对石油和天然气钻井和提取设备的构造材料设下实际限制。因此,油气钻井和提取设备的OCTG和其它部件可由高强度CRA制成,所述高强度CRA诸如马氏体不锈钢、马氏体/铁素体不锈钢、奥氏体不锈钢、双相(奥氏体(奥氏体/铁素体)不锈钢、超级双相(奥氏体/铁素体)不锈钢、高度双相(奥氏体/铁素体)不锈钢、奥氏体镍基合金、奥氏体镍基超合金和钛基合金。这些CRA使材料强度、韧度、耐腐蚀性、可成型性和成本效益平衡,以使合金适于OCTG。大直径管(例如,具有至少6.625英寸(168.3mm)的外径的管件)占据大部的OCTG市场。然而,用于大直径管的生产的现有方法存在许多缺点。例如,现有的无缝管生产方法(诸如刺穿和皮尔格式辊轧(Mannesmann)方法、刺穿和芯棒辊轧(Stiefel)方法、刺穿和心轴辊轧方法、推台方法、刺穿和拉伸方法,以及热挤方法)通常不能生产足够大小的CRA管材以生产具有适于OCTG的大外径、壁厚和长度的组合的成品管件。现有焊接管件生产方法在CRA管生产的上下文中也有许多缺点,包括无法有效形成和焊接相对大且厚的CRA板材(例如,至少8英尺(2.4米)的长度,至少6.5英寸(165.1mm)的宽度,以及至少0.75英寸(19.1mm)的厚度)。将相对大且厚的CRA板材形成和焊接到中空圆柱形预成型件中的能力对于在冷加工(冷硬化)条件下生产大直径CRA管是重要的,这需要下游冷成型操作以实现OCTG规范所需强度性质。通常需要OCTG满足各种行业标准规范,包括美国国家标准协会/美国石油协会规范5CRA,第一版,2010年2月(用作套管、管道和耦接器材的无缝耐腐蚀合金管的规范(SpecificationforCorrosionResistantAlloySeamlesstubesforUseasCasing,TubingandCouplingStock))(“ANSI/API规范5CRA”)。ANSI/API规范5CRA等效于ISO13680:2008(修改)。ANSI/API规范5CRA以引用的方式并入本说明书。除其它要求外,ANSI/API规范5CRA规定由CRA制成的OCTG的许多微结构、机械和组成要求,所述CRA包括马氏体不锈钢、马氏体/铁素体不锈钢、双相(奥氏体/铁素体)不锈钢、超级双相(奥氏体/铁素体)不锈钢、奥氏体不锈钢和奥氏体镍基合金。例如,除其它要求外,ANSI/API规范5CRA规定在适用于特定CRA的各种条件下对OCTG的室温屈服强度(0.2%补偿屈服点)、极限抗拉强度、伸长率和HRC硬度数的要求(例如,热精制、淬火和回火、固溶退火或冷硬化)。已经发现,利用现有焊接管件生产方法生产满足ANSI/API规范5CRA的要求的CRA管(尤其大直径冷硬化CRA管)是在商业上不切实际的。然而,本说明书中描述的方法可解决和克服这种在商业上的不切实际性,并且生产可满足ANSI/API规范5CRA的要求的焊接且无缝的冷加工(冷硬化)CRA管(包括但不限于大直径管)。一种生产管件的方法包括使合金板变形以形成中空圆柱形预成型件。中空圆柱形预成型件初始是具有位于圆柱形变形板的两个邻接端部之间的纵向接缝区域的开缝预成型件。焊接纵向接缝区域,以便将邻接端部接合在一起,并且形成闭缝预成型件。可使闭缝(经焊接的)中空圆柱形预成型件径向胀大。使闭缝(任选地胀大的)中空圆柱形预成型件流动成型以提供无缝冷加工(冷硬化)合金管。如本文所使用,术语“管件”是指任何中空圆柱形管状制品。因此,不管尺寸如何,术语“管件”均涵盖并包括管路和包括环形截面的其它导管。参考图1A,矩形的合金板10具有相对纵向端部12a和12b,以及相对的主表面14a和14b。合金板10被变形为中空圆柱形预成型件10',如图1B所示。中空圆柱形预成型件10’是具有位于两个邻接纵向端部12a和12b之间的纵向接缝区域16的开缝预成型件。如本文所使用,术语“开缝”是指位于圆柱形变形板的邻接纵向端部之间的纵向区域的初始未焊接状态,术语“闭缝”是指该纵向区域的随后已焊接状态。开缝预成型件可以具有进行物理接触或在邻接纵向端部之间具有小间隙的邻接纵向端部。为了说明目的,纵向接缝区域16在图1B中示为在邻接纵向端部12a和12b之间具有间隙。应当理解,在实践中,在邻接纵向端部之间的任何间隙应当小至足以允许随后将邻接纵向端部焊接在一起。因此,如本文所使用,术语“邻接”是指直接物理接触或相面对的取向,其中在相面对的纵向端部之间的间隙小至足以允许随后将邻接纵向端部焊接在一起。接缝区域中的邻接纵向端部之间的任何间隙的大小可由用于将纵向端部接合在一起的焊接技术来指定。纵向接缝区域16被焊接以将邻接端部12a和12b接合在一起,并且形成闭缝预成型件10”,如图1C所示。闭缝中空圆柱形预成型件10”包括将端部12a和12b接合在一起的焊缝18。使合金板变形以形成开缝中空圆柱形预成型件可使用辊弯成形操作来执行。如本文所使用,术语“辊弯成形”是指使用例如三辊弯曲设备或类似设备在间歇操作中弯曲单个的合金板(一次就一个板)。例如,图2A和图2B示意性地示出在包括轧辊25a、25b和25c的三辊弯曲设备中形成开缝中空圆柱形预成型件20',所述开缝中空圆柱形预成型件具有位于变形的板20的邻接端部22a和22b之间的纵向接缝区域26。如本文所使用,“辊弯成形”不同于辊轧成型,在辊轧成型中,连续的合金条进给通过辊轧成型轧机,其中一系列的辊架通过漏斗形成型线(参见图3A和图3B)逐渐将该条成形为开缝管。在各种实施方案中,辊轧成型操作(例如,包括连续和/或高速辊轧成型操作,诸如在Gandy的美国专利号6,880,220中描述的那些)可能并不适于生产预成型件,因为辊轧成型轧机无法使大且厚的板材(例如,至少0.75英寸(19.1mm)的厚度)塑性变形为中空圆柱形预成型件。使合金板变形以形成开缝中空圆柱形预成型件可使用U-O压制操作来执行。如本文所使用,术语“U-O压制”是指在U形压机中顺序压制板材以形成U形截面中间体,接着在O形压机中压制U形中间体以形成O形截面开缝中空圆柱形预成型件。例如,图4A示意性地示出在U形压机中压制板以形成具有纵向端部42a和42b的U形中间体40,并且图4B示意性地示出在O形压机中随后压制U形中间体以形成具有位于邻接纵向端部42a和42b之间的纵向接缝区域46的开缝中空圆柱形预成型件40'。在U形压制操作中,圆形半径工具通常在单个压制行程中,将板在两个支撑件之间向下推动。随着操作趋于结束,可使在两个支撑件之间的距离减小,以施加小程度的过度弯曲来抵抗任何回弹效应。在随后O形压制操作中,U形中间体通常在单个压制行程中,被形成为O形预成型件。在U-O压制操作中执行的变形操作被协调以确保有效抵消回弹效应,并且开缝预成型件是尽可能圆的,而邻接纵向端部是尽可能齐平的。在各种实施方案中,在U-O压制操作前可以进行C形压制操作,其中矩形板首先在C形压机中被压制成C形截面中间体,C形中间体在U形压机中被压制成U形截面中间体,并且U形中间体在O形压机中被压制成O形截面开缝中空圆柱形预成型件。上述辊弯成形和U-O压制操作是用于将合金板变形为开缝中空圆柱形预成型件的示例性技术。变形也可使用具有使相对较厚的合金板变形为开缝中空圆柱形预成型件的能力的其它压制成型操作执行。使合金板变形以形成开缝中空圆柱形预成型件可以在冷加工温度下执行。如本文所使用,术语“冷加工温度”是指小于合金的重新结晶温度的温度。在各种实施方案中,可以使合金板在小于500℃、小于400℃、小于300℃、小于200℃或小于100℃的冷加工温度下变形为开缝中空圆柱形预成型件。在各种实施方案中,可以使合金板在室温(即,在变形操作开始时而不考虑塑性变形期间的绝热加热的温度)下变形为开缝中空圆柱形预成型件。在各种实施方案中,开缝中空圆柱形预成型件由板形成,使得合金材料晶粒基本上沿预成型件的纵向方向来取向。这可例如通过提供具有基本上沿板的长度(纵向边缘方向)取向的晶粒的矩形的合金板实现,所述长度可由温轧或热轧的板件或中间板提供达到最终板厚,其中辊轧方向与板的长度(长尺寸)一致。如本文所使用,术语“基本上取向的”是指合金织构条件,其中组成颗粒长轴的大部分是朝三个基本方向(长度、宽度、厚度)中的一者倾斜。给定合金样品晶粒是否是沿特定方向“基本上取向的”可使用显微图像来金相学地确定。使合金材料的晶粒基本上取向于预成型件的纵向方向上可以提供更高效且更有效的流动成型操作。变形为开缝中空圆柱形预成型件的合金板可通过热轧操作来提供。可熔融合金原料材料以提供预定合金化学物质,并且熔融材料在冶金操作中铸造成铸锭或板件。适于提供铸造CRA的冶金操作的实例包括例如连续板件铸造、真空感应熔融(VIM)和铸锭铸造,以及电弧熔融和铸锭铸造。还可采用中间精炼操作,包括例如氩氧脱碳(AOD)、真空氧脱碳(VOD)、电渣精炼/重熔(ESR)和/或真空电弧重熔(VAR)。可将铸造的合金锭热锻造(即,在高于合金的重新结晶温度的温度下锻造)成适于辊轧的板件或其它辊轧产品形式。可直接对铸造板件进行辊轧。铸造或热锻造的合金板(通常为6-12英寸(152.4-308.4mm)厚)可加热到高于合金的重新结晶温度的温度,并辊轧成诸如0.5英寸至1.75英寸(12.7-44.5mm)的板厚。辊轧板件在辊轧方向上伸长,其通常与在热轧操作中形成的板的长度(长尺寸)一致,因此在合金板中的晶粒基本上沿板的长度(纵向边缘方向)取向。热轧的板可切割成适当矩形尺寸,诸如至少8英尺(2.4米)的长度和至少6.5英寸(165.1mm)的宽度。接着,热轧的板可直接在辊弯成形、U-O压制或其它合适成型操作中变形为开缝中空圆柱形预成型件。用于形成开缝中空圆柱形预成型件的板可以在热加工条件(其通常类似于软化退火条件)下使用,因为随后流动成型操作可以使合金材料的晶粒结构改进。在合金板变形为开缝中空圆柱形预成型件前,可磨削或机械加工合金板。可磨削或机械加工板的主顶表面和底表面,以便增大板平整度。例如,可磨削或机械加工板的主顶表面和底表面,以便确保板呈现出至少±0.020英寸(±0.508mm)的平整度。矩形板的纵向端部和/或横向端部也可在变形前被磨削或机械加工,以便确保相对端部是平行的,并且确保纵向端部垂直于横向端部。板的相对纵向端部也可在变形前机械加工,以便在端部上提供适当焊接倒角。在合金板变形为开缝中空圆柱形预成型件前,可使合金板的纵向端部在边缘弯曲(卷曲)压机中预先弯曲。在弯曲(卷曲)压机中形成在板中的边缘弯曲半径通常可对应于随后形成的开缝中空圆柱形预成型件的预定直径。在形成开缝中空圆柱形预成型件后并且在焊接纵向接缝区域以便将邻接端部接合在一起前,纵向接缝区域可沿该接缝区域的长度在离散位置处进行点焊。例如,可将邻接端部在点焊定点处压在一起形成物理接触,并且在沿该接缝区域的长度的离散位置处点焊以将在邻接端部之间的任何间隙闭合。然后,经点焊的中空圆柱形预成型件随后可经历焊接操作以完全焊接纵向接缝区域。可使用焊接技术(诸如钨极惰性气体保护焊接(TIG)、金属惰性气体保护焊接(MIG)、等离子弧焊接、摩擦搅拌焊接、电子束焊接或激光焊接)来焊接开缝中空圆柱形预成型件的纵向接缝区域。在各种实施方案中,使用无填料焊接技术(诸如激光焊接的)焊接纵向接缝区域,这不会在接缝区域沉积任何额外焊接合金。焊接纵向接缝区域可以包括两个道次:沿预成型件的外表面上的接缝区域的外侧道次;以及沿预成型件的内表面上的接缝区域的内侧道次。在包括使用填料材料的焊接技术的实施方案中,焊接合金组分可与板/预成型件的组成合金相同或类似。例如,TIG或MIG焊接操作可以使用由与板/预成型件的组成合金相同或类似的焊接合金组分制成的填料焊丝或自耗电极。在一些实施方案中,焊接合金可与至少一种奥氏体稳定化元素(例如,镍、锰、铜、氮和/或碳)过合金化。可设计或选择焊接合金中的过合金化水平,以便确保预成型件中的焊缝的化学组分和微结构保持板/预成型件的组成合金的规格。例如,在包括双相或超级双相不锈钢预成型件的实施方案中,双相或超级双相不锈钢焊接合金可用于TIG、MIG或等离子弧焊接操作以闭合纵向接缝。该双相或超级双相不锈钢焊接合金的化学组分可例如与镍或锰略微过合金化,但仍在预成型件的双相或超级双相不锈钢的规格内。可任选地在氮气气氛中执行对纵向接缝区域的焊接。例如,可由在中空圆柱形预成型件的焊接道次期间流自指向纵向接缝区域的喷嘴的氮气保护气体提供氮气气氛。例如,激光焊接操作产生很有限的受热影响的区,并使经焊接的纵向接缝区域快速冷却,这减少或防止金属间相形成。然而,与激光焊接关联的较高冷却速率可能导致当激光焊接双相、超级双相或特超级双相不锈钢时,在焊接区中形成过量的铁素体。氮是奥氏体稳定化元素,并且因此,在包括双相、超级双相或特超级双相不锈钢CRA的实施方案中,在氮气气氛中激光焊接可有助于维持焊接区中的奥氏体和铁素体的相对比例。在纵向接缝区域的焊接期间,焊痕(也称焊道)可沿焊缝形成。可使用例如磨光操作、刮削(切割)操作、机械加工操作、磨削操作或平整操作来去除焊痕/焊道。焊痕/焊道也可使用例如在美国专利号6,375,059中描述的辊轧操作而变平滑,所述美国专利以引用的方式并入本说明书。闭缝(经焊接的)中空圆柱形预成型件可任选地在流动成型前径向胀大。经焊接的中空圆柱形预成型件径向胀大可使用液压或机械胀管器来执行。图5示意性地示出包括纵向焊缝58的闭缝中空圆柱形预成型件50的径向胀大。径向胀大闭合(焊接)中空圆柱形预成型件会使合金材料塑性变形,并且增大预成型件的截面圆度和纵向直度,这可利于随后流动成型操作。闭缝(经焊接的)中空圆柱形预成型件可以使预成型件的初始内径径向胀大至少0.5%。例如,预成型件可以使预成型件的初始内径胀大至少1%、至少1.5%或至少2%。闭缝(经焊接的)中空圆柱形预成型件可胀大不超过预成型件的初始内径的6%。例如,预成型件可胀大不超过预成型件的初始内径的5%、4%或3%。通常,该径向胀大量(若有的话)可为实现足够的圆度和直度以满足流动成型公差必需的最小值。该胀大量应避免使焊缝分裂,并且避免冷加工/冷硬化合金材料。闭合(焊接)中空圆柱形预成型件可以在小于500℃的温度下执行任选胀大。例如,径向胀大可以在小于500℃、小于400℃、小于300℃、小于200℃或小于100℃的温度下执行。径向胀大可以在室温下执行。在焊接操作后并在流动成型操作前,可以任选地对闭缝(经焊接的)中空圆柱形预成型件进行退火。在包括任选胀大操作的实施方案中,可在焊接操作之后并在胀大操作之前、或者在胀大操作与流动成型操作之间执行任选退火操作。可基于预成型件的合金材料的类型来选择合适退火温度。例如,双相不锈钢预成型件可以在875℃至1200℃(1607-2192℉)或其中涵盖的任何子范围(诸如1010℃-1177℃(1850-2150℉)、982℃至1149℃(1800-2100℉)、950℃至1150℃(1742-2102℉)或1000℃至1100℃(1832-2012℃))内的温度下退火。例如,超级双相不锈钢预成型件和特超级双相不锈钢预成型件可以在950℃至1200℃(1742-2192℉)的温度范围或其中涵盖的任何子范围(诸如1010℃-1177℃(1850-2150℉)、982℃至1149℃(1800-2100℉)、1050℃至1150℃(1922-2102℉)或1075℃至1100℃(1967-2012℉))内的温度下退火。通常,对于双相、超级双相和特超级双相不锈钢,相较在合适较低温度下退火,在合适较高温度下退火可能增加铁素体的含量。如本文所使用,将预成型件加热成“处于”指定温度或温度范围达指定时间段或时间范围(即,处于某温度的时间)表示将预成型件加热达从预成型件表面温度(例如,使用热电偶、高温计等测量到的)达到指定温度或温度范围的±14℃(±25℉)时的点起测量的指定时间或时间范围。如本文所使用,指定处于某温度的时间并不包括使预成型件表面温度达到指定温度或温度范围的±25℉(±14℃)的预热时间。如本文所使用,术语“炉内时间(furnacetime)”指示工件维持在温度受控环境(诸如预热的炉)内的时间量,并且并不包括使温度受控环境达到指定温度或温度范围需要的时间。退火处理可以在高于合金(包括变形的板的合金和可用于闭合变形的板的纵向接缝的任何焊接合金)的重新结晶温度的温度下执行。退火处理可以使经焊接的预成型件的至少受热影响的区重新结晶,可以使经焊接的预成型件的更大部分重新结晶,或可以使整个经焊接的预成型件重新结晶。退火处理可以通过在退火温度范围内将预成型件加热到表面温度并接着在冷却预成型件前将预成型件维持达预定处于某温度的时间(例如,通过将预成型件从退火炉去除)来执行。例如,可以在退火温度范围内将预成型件加热到指定表面温度,并且接着维持该温度达至少5分钟、至少10分钟、至少15分钟、至少20分钟、至少25分钟或至少30分钟(处于某温度的时间)。或者,可通过将预成型件放置于在一定温度下操作的退火炉(或其它温度受控环境)中,并且接着在冷却预成型件前将预成型件维持在炉中达预定炉内时间来执行退火处理(例如,通过将预成型件从退火炉去除)。例如,可将预成型件放置于在退火温度范围内在指定温度下操作的退火炉中,并且接着将管件维持在炉中达至少5分钟、至少10分钟、至少15分钟、至少20分钟、至少25分钟或至少30分钟(炉内时间)。可将预成型件维持在一定温度下或在正在操作的炉中达不超过例如60分钟、45分钟、30分钟或15分钟的时间(处于某温度的时间或炉内时间,视情况定)的时间段。在包括任选退火操作的实施方案中,可以在指定处于某温度或处于炉的时间后,将经退火的预成型件从退火温度淬火。例如,可以在不超过30分钟、不超过25分钟、不超过20分钟或不超过15分钟(处于某温度的时间或炉内时间,视情况定)后,将预成型件从退火温度淬火。淬火可以在冷却期间防止有害相沉淀的冷却速率来执行。此类冷却速率可例如使用水淬操作来实现。在双相、超级双相和特超级双相不锈钢中,例如,在某些温度下,可在几分钟内快速形成有害σ相、χ相、α’相、碳化物和/或氮化物。例如,在双相(UNSS31803和S32205)和超级双相(UNSS32750和S32760)不锈钢中的沉淀反应和其它特征性反应的典型温度在表1中示出。表1图6是等温沉淀图,示出在1050℃(1920℉)下退火的第一双相不锈钢(合金2205,其对应于UNS号S31803和S32205)、第二双相不锈钢(合金2304,其对应于UNS号S32304)和超级双相不锈钢(合金2507,其对应于UNS号S32750和S32760)的时间-温度-转变曲线。图6示出有害相形成的温度范围和动力学。碳化物和氮化物沉淀可以在温度下快至1-2分钟开始σ相和χ相沉淀在较高温度下发生,但与碳化物和氮化物沉淀在大致相同时间上。在铬、钼和镍中更高度合金化的双相和超级双相不锈钢将会具有比较低度合金化的双相不锈钢更快的σ相和χ相形成动力学。在较低温度下形成α’沉淀物可能会不利地硬化并使双相和超级双相不锈钢中的铁素体脆化。在以上所指出的温度范围内几分钟的暴露可能导致对耐腐蚀性和韧性有害的相的形成。允许预成型件在相对快速淬火(例如,通过水淬前从退火温度冷却到700-980℃(1300-1800℉)温度范围还可导致有害相的形成。因此,在各种实施方案中,可以足以防止形成有害相的冷却速率将预成型件从退火温度淬火(使用例如水淬操作)。使闭缝(经焊接的)中空圆柱形预成型件流动成型以提供无缝冷加工(冷硬化)合金管。流动成型是用于生产精确圆柱形部件的金属成型操作。流动成型通常通过使用来自两个或更多个轧辊的轴向力、径向力和切向力的组合在内部旋转心轴上压缩圆柱形工件的外径来执行。材料被压缩成高于它的屈服强度,从而导致材料塑性变形。因此,工件的外径和壁厚减小,而其长度增大,直到实现该部件的期望几何形状。流动成型通常是在冷加工温度下执行的冷成型操作。虽然绝热是由塑性变形产生,但是工件、心轴和轧辊通常充满冷冻的冷却剂以将热量耗散。这确保了材料在其重新结晶温度以下加工良好。作为冷成型方法,流动成型增大工件材料的强度和硬度,赋予材料纹理,并且通常实现比利用任何温热或热成型制造方法实现的更接近要求的机械性能和尺寸精度。流动成型操作的两个实例是正向流动成型和反向流动成型。通常,正向流动成型可用于形成具有至少一个闭合或半闭合端部的管件或部件(例如,闭合圆筒)。反向流动成型通常可用于形成具有两个打开端部的管件或部件(例如,有两个打开端部的圆筒)。在一些情况下,可利用正向流动成型和反向流动成型的组合来成功实现期望几何形状。通常,可通过改变必要工具来在相同流动成型机器上执行正向流动成型和反向流动成型。图7示意性地示出流动成型装置100。流动成型装置100被配置成用于正向流动成型。流动成型装置100包括用于保持圆柱形工件118的心轴112、将工件118固定到心轴112的尾座114、用于向工件118的外表面施力的两个或多个轧辊116,以及可耦接到轧辊116的移动托架119。如图7所示,轧辊116可相对于工件118的中心轴彼此成相等的角度。轧辊116可为液压驱动和计算机数控的(CNC)。图8示出进行正向流动成型操作的工件118的侧视示意性截面图。在此操作期间,工件118可放置在心轴112上方,其闭合或半闭合端部朝心轴112的端部(如图7所示,朝心轴的右侧)。工件118可例如借助来自尾座114的液压力通过尾座114来固定在心轴118的端部上。接着,心轴112和工件118可绕轴线120旋转,同时轧辊116在沿其长度的期望位置处移动到与工件118的外表面接触的位置。头座134旋转或驱动心轴112,并且尾座114提供额外支撑以使心轴112旋转,使得较长心轴112适当自旋。接着,托架119可沿工件118(通常在124处指示的方向上)移动轧辊116(从右向左行进,如图7所示)。轧辊116可向工件118的外表面施加一个或多个力,以例如使用受控的径向力、轴向力和切向力的组合来减小其壁厚126和其外径。可使用一个或两个喷射器136将冷却剂喷涂在轧辊116、工件118和心轴112上,但是可使用更多的喷射器来耗散工件118最初例如在室温下经历大量塑性变形时产生的绝热。甚至可将心轴112浸没在冷却剂(未示出)中,例如浸没在槽型装置中,使得冷却剂收集并聚集在心轴112上以保持工件118冷却。轧辊116可用足够的力压缩工件118的外表面,使得材料塑性变形,并且在122处指出的方向(大体上平行于纵向轴线120)上移动或流动。可将轧辊116定位在距心轴112的外径或工件118的内壁的任何期望距离处,以便产生沿工件118的长度恒定或变化(如图8和图9所示)的壁厚126。长度128表示工件118已经历流动成型操作的部分,而长度130是未变形的部分。图8中示出的操作称为“正向流动成型”,因为经变形的材料在与轧辊正移动的方向124相同的方向122上流动。在反向流动成型中,流动成型装置可以与图7所示类似的方式配置,但是驱动环132而非尾座114将工件118固定到心轴112。如图7和图9所示,驱动环132位于心轴112的非自由端处的头座134附近。图9示出经历反向流动成型操作的工件118的侧视图。在此操作期间,可将工件118放置在心轴112上,并且在心轴112的非自由端(如图9所示的左侧)一直推压在驱动环132上。可将轧辊116移动到在沿其长度的期望位置处与工件118的外表面接触的位置。然后,托架119可朝驱动环132移动(在从右到左方向上,如图7所示)以向工件118施力。轧辊116施加的力可将工件118推入到驱动环132中,在那,工件可被驱动环132的表面上的一系列细齿或其它固定特征夹住或固定。这允许了心轴112和工件118围绕纵向轴线120旋转,同时轧辊116可向工件118的外表面施加一个或多个力。工件材料塑性变形,并且在大体上平行于轴线120的方向122上移动或流动。类似于正向流动成型,可将轧辊116定位在距心轴112的外径或工件118的内壁的任何期望距离处,以便产生沿工件118的长度恒定或变化的壁厚126。长度128表示工件118已经历流动成型操作的部分,而长度130则表示未变形的部分。当工件118变形时,它沿心轴112的长度向下延伸远离驱动环132。这个操作称为“反向流动成型”,因为经变形的材料在与轧辊正移动的方向124相反的方向122上流动。除了使各个部分在平滑心轴上方流动成型以形成流动成型管件的平滑内径之外,可将细齿、膛线或其它纹理形成到流动成型管件的孔中。这可通过使用具有表面纹理(诸如膛线、凹槽、凹口或其它构造)的心轴来实现,这些表面纹理在工件流动成型时压入工件的内表面。例如,心轴可以在其表面上构造有螺旋、笔直、周期性的或其它期望的隆脊。这些隆脊在完成最终流动成型道次后,在工件的内表面中留下膛线、凹槽、凹口和/或其它构造。当工件材料在一组旋转轧辊下塑性变形并被压缩到心轴上时,可以在单道中实现大程度的壁厚减小。对于圆柱形合金预成型件,如果每流动成型道次使用的壁厚减小小于20%,那么该工件的最外部分就会塑性变形,但是最靠近内心轴的材料可能不会经历足够塑性变形。如果在单道(例如,大于75%)中执行太大程度壁厚减小,那么工件可能不被可接受地处理,因为流动成型操作可能无法塑性变形并且一次移动所有材料。在一些实施方案中,在必要时,可以在第一道次上执行一定量的壁厚减小,在第二或是随后道次上执行较小量的减小。通常,当在流动成型操作中执行至少20%的壁厚减小时,穿过整个壁厚的材料的塑性变形足以均匀地将预成型件伸长到流动成型管件中。如本文所使用,术语“壁厚减小”表示在流动成型操作(即,面积缩小)期间预成型件的壁的环形截面面积的缩小百分比。流动成型方法均匀“精炼”变形的材料的晶粒尺寸,并且在基本上平行于流动成型管件的中心线的纵向方向上以相对均匀的方式重对准微结构。流动成型方法可以在一个或多个流动成型道次中进行。当使用两个或更多个道次时,在第一道次中实现的壁厚减小可以大于在随后道次中实现的壁厚减小,并且可为至少25%的壁厚减小。例如,对于使用多于一个道次的35%的总壁厚减小,第一道次可为至少25%的壁厚减小,第二道次可为10%的壁厚减小。在另一实例中,对于使用多于一个道次的50%的总壁厚减小,第一道次可为至少25%的壁厚减小,第二道次可为15%的壁厚减小,并且第三道次可为10%的壁厚减小。随着由流动成型操作施加的冷加工的程度,材料的硬度和抗拉强度增大,同时可延展性和冲击韧度值减小。经由流动成型的冷加工通常还降低了流动成型材料晶粒尺寸。通常,当材料被冷加工时,微小缺陷在整个变形区域上成核。当缺陷通过变形累积时,就会变得越来越难出现缺陷的滑移或移动。这导致了材料硬化。如果材料经受过多的冷加工,那么硬化材料可能断裂。因此,对于每个流动成型道次,经变形的材料变得更硬并且具有更低可延展性,因此可在第一道次之后使用一系列越来越小的减小。除了流动成型材料的双轴强度和硬度增大之外,实施方案还可在流动成型部件内径处的近表面的材料中提供由自紧方法引起的残余压缩应力。自紧是指在管状部件上使用以通过在孔处产生残余压缩应力来提高管件的强度和疲劳寿命的金属制造技术。在典型自紧方法中,在管孔内施加压力,从而导致近内表面材料塑性变形,同时近外表面材料发生弹性变形。因此,在去除压力后,存在残余应力分布,从而在管件的内表面上提供残余压缩应力。在各种实施方案中,在最终流动成型道次中,轧辊可配置为使用轴向力和径向力的组合压缩工件外径,这使工件内径处的材料将利用足够的力来压缩到心轴112上,以使内径处的材料塑性变形,由此以类似于自紧的方式对内径施加压缩应力。这可例如通过将轧辊彼此充分拉开而实现。接着,流动成型操作使工件压靠在心轴上并夹紧心轴,而非刚好正从心轴释放或从心轴弹回工件,这通常是在标准流动成型操作期间出现的情况。以此方式将内径压缩到心轴上对流动成型部件内径施加压缩环向应力。图10和图11分别示出三辊流动成型配置的示意性透视图和示意性侧视图。图10示出容纳有三个流动成型轧辊116(在图11中示为X、Y和Z)的托架,三个流动成型轧辊可沿着三个轴线(在图10中示为X、Y和Z轴)移动,并且围绕主轴线径向定位,例如彼此间隔120°。虽然附图示出三个轧辊,但是流动成型操作可以使用两个或更多个轧辊。例如,在可能必需大变形力并可将负载分布在更多轧辊上的实施方案中,可以使用四辊配置。可独立编程的X、Y和Z轧辊提供必要的径向力,同时W轴的从右至左可编程的进给运动施加了轴向力。每个轧辊可具有特定几何形状以支持其在流动成型操作中的特定作用。轧辊116的位置可相对于彼此纵向和/或径向交错。交错的量可以变化,并且可以基于工件初始壁厚和给定流动成型道次中期望的壁减小量。例如,如图11所示,S0表示在流动成型道次之前的工件壁厚,并且S1表示在利用沿v方向移动的轧辊116进行流动成型操作之后的工件壁厚。轧辊116可沿工件118的纵向方向(在图10中示为W轴)纵向交错,并且可相对于该工件的中心线或内径(沿X、Y和Z轴)径向交错,以将相对均匀的压缩力施加到工件118的外部。例如,如图11所示,轧辊X可与轧辊Y分离位移或距离A1,并且轧辊X可沿工件118的纵向方向与轧辊Z分离距离A2。类似地,轧辊X可从工件内径径向移位距离S1,距离S1是工件118在流动成型道次之后的期望壁厚,轧辊Y可从工件内径径向位移距离R1,并且轧辊Z可从工件内径径向位移距离R2。如图所示,在已经建立轴向交错图案后,可使用角度K;凹确定径向交错的量。轧辊X、Y和Z彼此分离越大,施加到工件材料颗粒结构的螺旋扭曲越大。以此方式施加到部件的压缩环向应力(自紧)可以减小开裂的可能性并且降低可能在部件内径上引发的任何裂纹的生长速率,从而有效提高流动成型管件疲劳寿命。流动成型的另一益处是,施加到内径的压缩应力的量可根据轧辊配置沿管件长度变化。例如,轧辊可配置成使得压缩应力仅施加到管件的一部分,例如,施加在管件的一端或中间部分上。在流动成型操作中,可在工件和心轴的内径之间使用润滑剂,以便减少工件粘附或卡在心轴上的可能性。使闭缝(经焊接的)中空圆柱形预成型件流动成型以减小外径、增大长度并且去除焊缝,由此提供无缝冷加工(冷硬化)合金管。图12示意性地示出包括焊缝218的闭缝(经焊接的)中空圆柱形预成型件210的反向流动成型。预成型件210放置在心轴(未示出)上,并且固定在驱动环(未示出)上。驱动环在如222处的可旋转的箭头指示的旋转方向上旋转预成型件210。该流动成型设备的轧辊216在如箭头224处的箭头指示的纵向方向上旋转和移动,从而接合预成型件210并且使其塑性变形(虽然示出两个轧辊216,但是也可存在第三轧辊,并且其被流动成型管件290遮挡)。预成型件210的塑性变形合金材料出现在轧辊的相对侧上作为流动成型管件290,并沿由222处的线性箭头指示的纵向方向流动。预成型件210与管件290之间的转变区域250在轧辊216沿纵向方向来轴向接合工件的地方出现。如图12所示,由闭缝(经焊接的)中空圆柱形预成型件210生产的流动成型管件290没有可看到的焊缝,因此它是焊接且无缝的管件。图13示意性地示出包括焊缝318的闭缝(经焊接的)中空圆柱形预成型件310的反向流动成型。预成型件310放置在心轴312上,并且固定在驱动环(未示出)上。驱动环在如322处的可旋转的箭头指示的旋转方向上旋转预成型件310。流动成型设备的轧辊316旋转并沿进入页面平面中的纵向方向移动,从而接合预成型件310并且使其塑性变形。四辊配置在图13中示出。如上指出,在可能必需大变形力并可将负载分布在更多轧辊上的实施方案中,可以使用四辊配置。预成型件310的塑性变形合金材料出现在轧辊的相对侧上作为流动成型管件390,并沿指向页面平面外的纵向方向流动。预成型件310与管件390之间的转变区域350在轧辊316沿纵向方向来轴向接合工件的地方出现。如图13所示,由闭缝(经焊接的)中空圆柱形预成型件310生产的流动成型管件390没有可看到的焊缝,因此它是焊接且无缝的管件。闭缝(经焊接的)中空圆柱形预成型件(包括但不一定限于经扩展和/或退火的预成型件)的流动成型可以在冷加工的(冷硬化的)条件下来生产无缝管。例如,使得预成型件变形为管件的流动成型操作可以在室温和/或利用冷冻的冷却剂执行,以便确保变形在冷加工温度下发生。使得预成型件变形为管件的流动成型操作可将合金材料冷加工为具有在20%至80%的范围内(包括端点)或其中涵盖的任何子范围(诸如25%至75%、50%至75%、50%至70%、25%至65%、30%至65%、30%至60%、大于30%至小于60%、35%至55%或40%至50%)内的面积缩小率。使得预成型件变形为管件的流动成型操作可以在单道或多道中执行。使预成型件流动成型以生产管件提供控制在管件中实现预定目标材料性质必需的冷加工的精确水平(其量化为面积缩小率)的能力。例如,流动成型允许精确控制在冷加工的(冷硬化的)条件下实现管件中的室温屈服强度、极限抗拉强度、伸长率和硬度的预定平衡所需要的面积缩小率(例如,在30%至60%的范围内,这取决于特定合金)。这提供了有效且高效地生产遵循ANSI/API规范5CRA的化学组分、尺寸、机械和微结构要求的管件的能力。使得预成型件变形为管件的流动成型操作可以提供在冷加工的(冷硬化的)条件下有室温性质的管件,所述室温性质包括至少110ksi(758MPa)的屈服强度、至少125ksi(862MPa)的极限抗拉强度、至少9%的伸长率和/或不大于38的HRC硬度数。如本文所使用,术语“屈服强度”是指0.2%补偿屈服点。通过本说明书中描述的方法生产出的管件可表征为具有至少110ksi(758MPa)且不大于160ksi(1,103MPa)的屈服强度。通过本说明书中描述的方法生产出的管件可以具有比管件屈服强度大至少10ksi(70MPa)的极限抗拉强度。通过本说明书中描述的方法生产出的管件可以具有至少125ksi(862MPa)的屈服强度、至少130ksi(896MPa)的极限抗拉强度、至少10%的伸长率和/或不大于37的HRC硬度数。通过本说明书中描述的方法生产出的管件可以具有至少140ksi(965MPa)的屈服强度和/或至少145ksi(1000MPa)的极限抗拉强度。通过本说明书中描述的方法生产出的管件可以具有至少12%的伸长率和/或不大于36的HRC硬度数。使得预成型件变形为管件的流动成型操作可以提供具有至少1.0英寸(25.4mm)的外径和至少0.015英寸(0.381mm)的壁厚的管件。使得预成型件变形为管件的流动成型操作可以提供具有至少1.5英寸(81.1mm)的外径和至少0.020英寸(0.508mm)的壁厚的管件。使得预成型件变形为管件的流动成型操作可以提供具有至少2.0英寸(50.8mm)的外径和至少0.025英寸(0.635mm)的壁厚的管件。使得预成型件变形为管件的流动成型操作可以提供具有至少6.5英寸(165.1mm)的外径、至少0.231英寸(5.87mm)的壁厚和/或至少28.0英尺(8.5米)的长度的管件。使得预成型件变形为管件的流动成型操作可以提供具有至少7.0英寸(177.8mm)的外径、至少0.231英寸(5.87mm)的壁厚和/或至少34.0英尺(10.4米)的长度的管件。使得预成型件变形为管件的流动成型操作可以提供具有至少9.625英寸(244.5mm)的外径、至少0.312英寸(7.92mm)的壁厚和/或至少36.0英尺(11.0米)的长度的管件。使得预成型件变形为管件的流动成型操作可以提供具有至少9.875英寸(250.8mm)的外径、至少0.625英寸(15.9mm)的壁厚和/或至少36.0英尺(11.0米)的长度的管件。在流动成型操作后,管件可任选地退火。可基于流动成型管件的合金材料的类型来选择合适退火温度。例如,双相不锈钢管可以在875℃至1200℃(1607-2192℉)或其中涵盖的任何子范围(诸如1010℃-1177℃(1850-2150℉)、982℃至1149℃(1800-2100℉)、950℃至1150℃(1742-2102℉)或1000℃至1100℃(1832-2012℃))内的温度下退火。例如,超级双相不锈钢管和特超级双相不锈钢管可以在950℃至1200℃(1742-2192℉)的温度范围或其中涵盖的任何子范围(诸如1010℃-1177℃(1850-2150℉)、982℃至1149℃(1800-2100℉)、1050℃至1150℃(1922-2102℉)或1075℃至1100℃(1967-2012℉))内的温度下退火。通常,对于双相、超级双相和特超级双相不锈钢,相较在合适较低温度下退火,在合适较高温度下退火可能增加铁素体的含量。退火处理可以在高于流动成型管件的合金的重新结晶温度的温度下执行。退火处理可以使流动成型管件的冷加工微结构重新结晶。退火处理可以通过在退火温度范围内将管件加热到表面温度并接着在冷却管件前将管件维持达预定处于某温度的时间(例如,通过将预成型件从退火炉去除)来执行。例如,可以在退火温度范围内将管件加热到指定表面温度,并且接着维持该温度达至少5分钟、至少10分钟、至少15分钟、至少20分钟、至少25分钟或至少30分钟(处于某温度的时间)。或者,可通过将管件放置于在一定温度下操作的退火炉(或其它温度受控环境)中,并且接着在冷却管件前将管件维持在炉中达预定炉内时间来执行退火处理(例如,通过将管件从退火炉去除)。例如,可将管件放置于在退火温度范围内在指定温度下操作的退火炉中,并且接着将管件维持在炉中达至少5分钟、至少10分钟、至少15分钟、至少20分钟、至少25分钟或至少30分钟(炉内时间)。可将管件维持在一定温度下或在正在操作的炉中达不超过例如60分钟、45分钟、30分钟或15分钟的时间(处于某温度的时间或炉内时间,视情况定)的时间段。在包括任选退火操作的实施方案中,可以在指定处于某温度或处于炉的时间后,将经退火的管件从退火温度淬火。例如,可以在不超过30分钟、不超过25分钟、不超过20分钟或不超过15分钟(处于某温度的时间或炉内时间,视情况定)后,将管件从退火温度淬火。淬火可以在冷却期间防止有害相沉淀的冷却速率来执行。此类冷却速率可例如使用水淬操作来实现。本说明书中描述的方法可用于从合金板形成无缝的合金管,合金板包含例如CRA,CRA包括但不限于马氏体不锈钢、马氏体/铁素体不锈钢、奥氏体不锈钢、双相(奥氏体(奥氏体/铁素体)不锈钢、超级双相(奥氏体/铁素体)不锈钢、特超级双相(奥氏体/铁素体)不锈钢、奥氏体镍基合金、奥氏体镍基超合金和钛基合金。例如,可根据本说明书中描述的方法使用包含双相、超级双相或特超级双相不锈钢的不锈钢板来生产不锈钢管。双相不锈钢具有奥氏体和铁素体的混合的微结构。双相、超级双相和特超级双相之间通常基于耐点蚀当量数(PREN=%Cr+3.3*(%Mo+0.5*%W)+16*%N)进行区分,其中双相不锈钢具有至少35的PREN,超级双相不锈钢具有至少40的PREN,并且特超级双相不锈钢具有至少45的PREN。适于根据本说明书中描述的方法生产管件的双相、超级双相和特超级双相不锈钢的实例包括但不限于分别在表2-4中列出的不锈钢(以基于总合金质量的质量百分比指定的组分)。表2:双相不锈钢表3:超级双相不锈钢表4:特超级双相不锈钢UNS号CrNiMoNMnCCuFeS3270726.0-29.05.5-9.54.0-5.00.30-0.50≤1.5≤0.03≤1.0余量S3320729.0-33.06.0-9.03.0-5.00.40-0.60≤1.5≤0.03≤1.0余量以上表2-4中列出的不锈钢可以包含组成元素,基本上由组成元素组成,或者由组成元素和伴生杂质组成。例如,本说明书中描述的方法可以生产不锈钢管,所述不锈钢管包含超级双相不锈钢,所述超级双相不锈钢包含(以质量百分比计):24.0-26.0%铬;6.0-8.0%镍;3.0-5.0%钼;0.20-0.32%氮;至多0.04%碳;任选地,0.5-1.0%铜;任选地,0.5-1.0%钨;以及铁和伴生杂质。在各种实施方案中,本说明书中描述的方法可以生产具有铁素体积分数为40%至60%的范围的双相不锈钢管。在各种实施方案中,本说明书中描述的方法可以生产具有铁素体积分数为35%至55%的范围的超级双相不锈钢管。可适于根据本说明书中描述的方法生产管件的CRA的其它实例包括但不限于合金2205(UNSS31803)双相不锈钢、合金2507超级双相不锈钢(UNSS32750、S32760、S39274)、合金028(UNSN08028)Ni-Cr-Fe奥氏体不锈钢、合金825(UNSN08825)Ni-Fe-Cr合金、合金G-3(UNSN06985)Ni-Cr-Fe合金、合金050(UNSN06950)镍基合金、合金C-276(UNSN10276)镍基合金、合金600(UNSN06600)镍基合金、合金617(UNSN06617)镍基合金、合金625(UNSN06625)镍基合金、合金690(UNSN06690)镍基合金、合金718(UNSN07718)镍基合金、Ti-15V-3Cr-3Sn-3Al合金(UNSR58153)、Ti-4Al-2.5V-1.5Fe-0.25O合金(UNSR54250)、Ti-3Al-2.5V合金(UNSR56320)、Ti-3Al-8V-6Cr-4Mo-4Zr合金(UNSR58640)、Ti-4.5Al-3V-2Mo-2Fe合金(SP-700;UNS:无),以及可商购的纯钛(UNSR50250、R50400、R50550、R50700;ASTM等级1-4)。适于根据本说明书中描述的方法生产管件的某些镍基合金和钛基合金的化学组分列于以下表5和表6中(组分以基于总合金的质量百分比指定,并且可以包含组成元素,基本上由组成元素组成,或者由组成元素和伴生杂质组成)。表5:镍基合金表6:钛基合金本说明书中描述的方法可以生产管件,这种管件遵循ANSI/API规范5CRA,第一版,2010年2月。本说明书中描述的方法提供对生产的管的化学组分、尺寸、机械性质和微结构的精确控制。ANSI/API规范5CRA针对OCTG的这些性质和其它性质规定要求。因此,可将本说明书中描述的方法用于生产遵循标准的OCTG。ANSI/API规范5CRA针对OCTG规定标准长度范围:范围1(16.0-25.0英尺;4.88-7.62米);范围2(25.0-34.0英尺;7.62-10.36米);以及范围3(34.0-48.0英尺;10.36-14.63米)。ANSI/API规范5CRA还规定了OCTG的标准外径(OD)和壁厚(WT),它们范围为1.050-13.375英寸(26.67-339.72mm)OD和0.113-0.797英寸(2.87-20.24mm)WT。现有管件生产方法无法在商业规模上经济性地生产落在这些尺寸范围的上限内并还满足由ANSI/API规范5CRA设定的机械性质要求(例如,最小的屈服强度和抗拉强度、最小的伸长率和最大硬度水平)的管件。本说明书中描述的方法可以允许在冷加工的(冷硬化的)条件下有效生产较长(例如,范围3)且较大的外径(例如,大于7英寸/177.8mm)和较大壁厚(例如,大于0.5英寸/12.7mm)的无缝CRA管,其可满足由ANSI/API规范5CRA设定的机械性质要求。虽然已结合OCTG描述了本说明书中描述的方法的各种实施方案,但应理解,生产方法和生产出的管件并不限于油气应用。例如,通过本说明书中描述的方法生产出的管件可适于其中高强度和韧度以及耐腐蚀/侵蚀性重要的任何应用,诸如化学处理、石油化学处理、发电、采矿、废物处理和航空/飞机应用。实例实例1:机械加工合金625板(UNSN06625;20.0%-23.0%铬、8.0%-10.0%钼、3.15%-4.15%铌和/或钽、至多5.0%铁、至多1.0%钴、至多0.50%锰、至多0.5%硅、至多0.4%钛、至多0.4%铝、至多0.10%碳、余量镍和伴生杂质(以质量百分比计))以提高板平整度。机械加工板具有约8英寸(203.2mm)宽和0.750英寸(19.05mm)厚度的尺寸。板辊弯成形成中空圆柱形预成型件,所述中空圆柱形预成型件具有位于变形的板的两个邻接端部之间的纵向接缝区域。在氮气气氛下激光焊接辊弯成形的板,从而将邻接端部接合在一起。将焊痕从经激光焊接的纵向接缝区域去除。在环境温度下,使闭缝(经焊接的)预成型件反向流动成型为具有约50%的面积缩小率。所述方法生产具有8.625英寸(219.8mm)的外径和0.375英寸(9.53mm)的壁厚的合金625管。图14A示出流动成型的合金625管(右侧)和辊轧且焊接的合金625预成型件(左侧),所述辊轧且焊接的合金625预成型件与流动成型成管件的预成型件类似。如图14A所示,激光焊缝在预成型件中清楚可见,但是在流动成型管件中并不可见。图14B示出接合流动成型设备中的驱动环的流动成型管件的驱动端上的其余激光焊缝。实例2:将Ti-15V-3Cr-3Sn-3Al合金板(UNSR58153;14.0%-16.0%钒、2.5%-3.5%铬、2.5%-3.5%锡、2.5%-3.5%铝、余量钛和伴生杂质(以质量百分比计))辊弯成形成中空圆柱形预成型件,所述中空圆柱形预成型件具有位于变形的板的两个邻接端部之间的纵向接缝区域。这样的板具有约22-23英寸(559-584mm)长、17英寸(432mm)宽和0.050英寸(1.27mm)厚的尺寸。在氮气气氛下激光焊接辊弯成形的板,从而将邻接端部接合在一起。将焊痕从经激光焊接的纵向接缝区域去除。闭缝(经焊接的)预成型件具有约5.418英寸(138mm)的内径、约0.050英寸(1.27mm)的壁厚和约22-23英寸(559-584mm)的长度。闭缝(经焊接的)预成型件在图15中示出。大致将闭缝(经焊接的)预成型件对半切割成两个部分,并且每个部分在环境温度下反向流动成型。经流动成型的样品冷加工为具有约51%、53%、57%、61%和67%的面积缩小率,并且所生产的Ti-15V-3Cr-3Sn-3Al合金管具有约0.017英寸(0.43mm)、0.020英寸(0.51mm)、0.022英寸(0.56mm)、0.024英寸(0.61mm)和0.025英寸(0.64mm)的壁厚。图16示出在部分地流动成型的条件(与图12中的示意图相比)下的Ti-15V-3Cr-3Sn-3Al合金样品中的一个。部分地流动成型的样品包括闭缝(经焊接的)预成型件部分、流动成型的无缝管件部分和预成型件部分与管件部分之间的转变区域。焊缝在预成型件部分中是可见的,但是在转变区域中消失,而且不存在于无缝管件部分中。实例3:将超级双相不锈钢板(UNSS32760;24.0%-26.0%铬、6.0%-8.0%镍、3.0%-4.0%钼、0.20%-0.30%氮、至多1.0%锰、至多0.04%碳、0.5%-1.0%铜、0.5%-1.0%钨,以及余量铁和伴生杂质(以质量百分比计))辊弯成形成中空圆柱形预成型件,所述中空圆柱形预成型件具有位于变形的板的两个邻接端部之间的纵向接缝区域。板为约1.20英寸(30.5mm)厚。在氮气气氛下激光焊接辊弯成形的板,从而将邻接端部接合在一起。将焊痕从经激光焊接的纵向接缝区域去除。闭缝(经焊接的)预成型件具有约1.20英寸(30.5mm)的壁厚。闭缝(经焊接的)预成型件在图17中示出。在环境温度下,使得闭缝(经焊接的)预成型件反向流动成型。经流动成型的样品冷加工为具有约75%的面积缩小率,并且所生产的超级双相不锈钢管具有约0.30英寸(7.6mm)的壁厚。实例4:提供CRA板,所述CRA板具有长度18.0英尺(5.5米)、宽度9.125英寸(231.8mm)和厚度1.2英寸(30.5mm)的尺寸。磨削或机械加工板的主顶表面和底表面,以便确保板呈现出至少±0.020英寸(±0.508mm)的平整度。机械加工相对纵向端部(18.0英尺/5.5米)以确保它们是平行的,并且在必要时,提供适当焊接倒角。板辊弯成形成开缝中空圆柱形预成型件,所述开缝中空圆柱形预成型件具有位于变形的板的两个邻接端部之间的纵向接缝区域。焊接开缝中空圆柱形预成型件,以便将邻接端部接合在一起并将接缝闭合。经焊接的中空圆柱形预成型件具有长度18.0英尺(5.5米)、内径9.25英寸(235.0mm)和外径10.375英寸(263.5mm)的尺寸。在室温下,使得经焊接的中空圆柱形预成型件反向流动成型,以便将外径减小到9.875英寸(250.8mm),并且将长度增大到36英尺(11.0米)(约50%面积缩小率)。所得CRA管具有长度36英尺(11.0米)、外径9.875英寸(250.8mm)和壁厚0.625英寸(15.9mm)的尺寸。CRA管具有至少110ksi(758MPa)和不大于160ksi(1,103MPa)的屈服强度、至少125ksi(862MPa)的极限抗拉强度、至少9%的伸长率和不大于38的HRC硬度数。CRA管遵循ANSI/API规范5CRA,第一版,2010年2月。实例5:提供合金2507超级双相不锈钢板(UNSS32750;标称地是25.0%铬、7.0%镍、3.8%钼、0.27%氮、余量铁和伴生杂质)),所述合金2507超级双相不锈钢板具有长度18.0英尺(5.5米)、宽度9.125英寸(231.8mm)和厚度1.2英寸(30.5mm)的尺寸。磨削或机械加工板的主顶表面和底表面,以便确保板呈现出至少±0.020英寸(±0.508mm)的平整度。机械加工相对纵向端部(18.0英尺/5.5米)以确保它们是平行的,并且在必要时,提供适当焊接倒角。板辊弯成形成开缝中空圆柱形预成型件,所述开缝中空圆柱形预成型件具有位于变形的板的两个邻接端部之间的纵向接缝区域。激光焊接开缝中空圆柱形预成型件,以便将邻接端部接合在一起并将接缝闭合。在氮气气氛下,执行激光焊接,所述氮气气氛是由在焊道期间从指向纵向接缝区域的喷嘴流出的氮气保护气体提供。将焊痕从经激光焊接的纵向接缝区域磨光或刮削。闭缝(经焊接的)中空圆柱形预成型件在胀管器中径向胀大约1%(基于内径),以便确保预成型件是纵向笔直且周向成圆的。焊接且扩展的中空圆柱形预成型件具有长度18.0英尺(5.5米)、内径9.25英寸(235.0mm)和外径10.375英寸(263.5mm)的尺寸。在室温下,使得焊接且扩展的中空圆柱形预成型件反向流动成型,以便将外径减小到9.875英寸(250.8mm),并且将长度增大到36英尺(11.0米)(约50%面积缩小率)。所得合金2507超级双相不锈钢管具有长度36英尺(11.0米)、外径9.875英寸(250.8mm)和壁厚0.625英寸(15.9mm)的尺寸。合金2507超级双相不锈钢管具有至少110ksi(758MPa)和不大于160ksi(1,103MPa)的屈服强度、至少125ksi(862MPa)的极限抗拉强度、至少9%的伸长率和不大于38的HRC硬度数。合金2507超级双相不锈钢管遵循ANSI/API规范5CRA,第一版,2010年2月。****在本说明书中描述本发明的各种特征和特性,以便提供对所公开的方法和产品的全面理解。应当理解,本说明书中描述的各种特征和特性可以任何合适方式组合,不管此类特征和特性是否在本说明书中以组合的方式明确描述。申请人明确地意图将此类特征和特性的组合包括在本说明书范围内。因此,权利要求可修正为以任何组合来陈述在本说明书中明确或固有地描述或以其它方式由本说明书明确或固有地支持的任何特征和特性。此外,申请人保留了修正权利要求以肯定地放弃可出现在现有技术中的特征和特性的权利,即使那些特征和特性在本说明书中并未明确描述。因此,任何此类修正都将遵循描述的撰写和充分性要求(例如,欧洲专利公约第123(2)条),并且将不会向本说明书或权利要求中增加新的内容。本说明书中公开的方法和产品可以包括本说明书中描述的各种特征和特性、由它们组成或基本上由它们组成。此外,本说明书中陈述的任何数值范围均描述了包含在所陈述的范围内的相同数值精度(即,具有相同数目指定数位)的所有的子范围。例如,所陈述的“1.0至10.0”的范围描述在陈述的最小值1.0与陈述的最大值10.0之间(并且包括该最小值和最大值)的所有的子范围,例如“2.4至7.6”,即使在本说明书文本中没有明确陈述“2.4至7.6”的范围也是如此。因此,申请人保留了修正本说明书(包括权利要求)以明确陈述包含在本说明书中明确陈述的范围内的相同数值精度的任何的子范围的权利。在本说明书中固有地描述了所有此类范围,使得明确陈述任何的子范围而做出的任何修正都将遵循描述的撰写和充分性要求(例如,欧洲专利公约第123(2)条),并且将不会向本说明书或权利要求中增加新的内容。另外,本说明书中描述的数值参数应根据所报道的有效数位的数量、数字数值精度并且通过应用普通舍入技术来理解。还应理解,本说明书中描述的数值参数将会必然具有用于确定参数数值的基础测量技术的固有可变特性。除非另有说明,否则本说明书中标明的任何专利、出版物或其它公开材料全文以引用方式并入本说明书中,但仅限于所并入的材料不与本说明书中明确阐述的现有描述、定义、陈述或其它公开材料冲突的程度。因此,并且在必要程度上,本说明书中阐述的明确公开内容取代以引用方式并入的任何冲突材料。以引用方式并入本说明书中但与本文中阐述的现有定义、陈述或其它公开材料冲突的任何材料或其部分仅限于在所并入的材料与现有公开材料之间无冲突产生的情况下并入。申请人保留了修改本说明书以明确陈述以引用方式并入的任何主题或其部分的权利。除非另有说明,否则本说明书中使用的语法冠词“一者”、“一种”、“一个”和“所述”旨在包括“至少一个”或“一个或多个”。因此,在本说明书中使用冠词指示一个或多于一个(即,“至少一个”)该冠词的语法对象。举例来说,“组分”表示一种或多种组分,并且因此,可能的是,构想出了多于一种组分,并且在所述方法、组合物和产品的实现方式中可采用或使用这些组分。另外,除非使用的上下文另有要求,否则使用单数名词包括复数,并且使用复数名词包括单数。当前第1页1 2 3