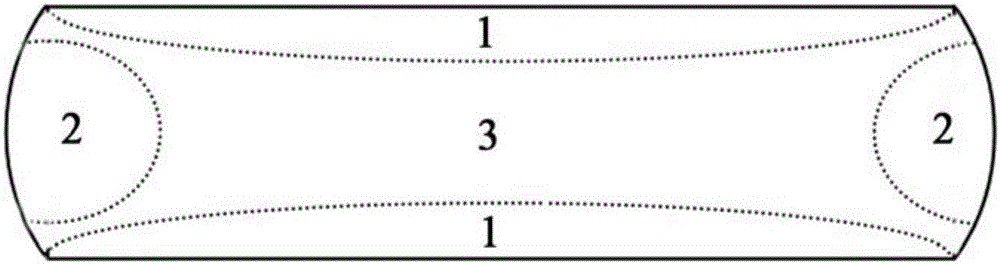
本发明涉及镁合金锻件的制备方法,特指系一种组织均匀的大尺寸镁合金锻件的制备方法;属于镁合金材料压力加工技术领域。
背景技术:镁合金以其低密度、高比强度的显著优点,在航空航天、汽车工业以及电子工业等领域得到广泛应用,特别是在航空工业领域,随着航空航天产业的迅速发展,对镁合金的需求也越来越大。目前镁合金零件的制备主要通过以下几种形式:(1)铸造成形,通过重力铸造、低压铸造等方式直接制备所需零件毛坯,然后进行后续机械加工及热处理来满足使用要求,缺点在于铸造合金的力学性能比较低,不适合有高强度需求的零件制造。(2)挤压成型,通过热挤压的方式制备出型材,后续经过焊接或铆接制备零件,很难制备整体大型零部件。(3)轧制成型,主要制备板材,且零件的承载能力有限。(4)锻造成型,尤其是结合模锻成型的工艺,可制备大尺寸的零部件,并且所制备零件具有较好的力学性能,并且各向的性能均匀。目前航天航空工业对大尺寸高强镁合金零部件的需求越来越多,大尺寸镁合金的锻件制备技术则显得更加重要。在进行镁合金模锻件制备时,一般需要先对锭坯进行热变形开坯,开坯方式主要有挤压和自由锻造,挤压开坯适合制备尺寸较小的模锻件,对于大尺寸模锻件,一般采用锻造开坯的方式制备模锻坯料。对于大尺寸模锻坯料制备而言则存在以下技术难点:(1)成型困难,由于镁合金本身的塑性变形能力较差,加上大尺寸坯料变形时温度分布不均匀,应力分布不均等难点,锻造时很容易开裂失效,目前通过各种工艺制度的优化和控制,已经能够制备出直径达到800mm的大型镁合金锻坯。(2)组织不均匀导致的性能不均匀,由于镁合金单向压缩锻造时,不可避免的存在“难变形区、易变形区和自由变形区”,这三个区域由于变形量不同,锻造后在晶粒大小、形态上存在非常大的区别,导致其力学性能也差异较大。特别是难变形区,由于锻造时砧板和坯料间的摩擦作用,该区域金属流动非常困难,即使整体变形量达到80%,但该区域仍然保持不变形。为了解决锻造组织的不均匀性,目前常采用的方法有:(1)多向锻造,通过改变锻造方向来实现组织的均匀,该方法主要适用于方形坯料锻造,不适用于直径较大,厚度较小的饼状坯料。(2)墩粗+小变形横向碾压,可以避免自由变形区开裂的问题,以及保证自由变形区和易变形区组织均匀性。但是以上两种方法都无法避免砧板和坯料接触区域难变形区组织不均匀性问题。虽然难变形区可以通过对锻饼的后续机加工车削去除,但是这样导致车削加工量大,材料利用率低,而且需要预先制备尺寸更大的饼坯,才能满足切削后模锻坯料的尺寸要求。本发明通过二次翻边组合锻造的方式,将难变形区变为易变形区,消除了锻造后由于难变形区引起的晶粒尺寸、形态不均匀,提高了锻饼整体组织和性能的均匀性,同时减少后续的车削加工,提高了材料的利用率。另外组合锻造的方式时高径比增加,降低了锻造时的变形抗力,提高了设备的加工能力。
技术实现要素:本发明的目的在于克服现有技术之不足而提供一种工艺简单,加工技术合理,能够大幅度提高大尺寸镁合金锻饼各区域组织均匀性的锻造方法。本发明一种提高大尺寸镁合金锻饼组织均匀性的锻造方法,包括下述步骤:取两块镁合金预锻饼坯作为一组,将两块镁合金预锻饼坯分别加热到400℃~420℃,保温2~3小时后,将两块镁合金预锻饼坯叠置,构成第一组坯料,对第一组坯料进行一级热锻;或将两块镁合金预锻饼坯叠置,构成第一组坯料后,加热到400℃~420℃,保温2~3小时,对第一组坯料进行一级热锻;一级热锻结束后,将第一组坯料中的两块镁合金分开,并将每一块镁合金翻转180度,重新叠置,使第一组坯料中与锻锤及锻墩接触的镁合金预锻饼坯表面相互接触,构成第二组坯料,对第二组坯料进行二级热锻,然后,将第二组坯料中的两块镁合金分开,得到两个镁合金锻饼,锻饼直径达到600-1200mm。本发明一种提高大尺寸镁合金锻饼组织均匀性的锻造方法,进行二级热锻前,先将第二组坯料加热到400℃~420℃,保温20~30分钟。本发明一种提高大尺寸镁合金锻饼组织均匀性的锻造方法,一级热锻或二级热锻的锻造速度均为10~15mm/s,变形量均为15%~20%。本发明一种提高大尺寸镁合金锻饼组织均匀性的锻造方法,两块镁合金预锻饼坯的直径相近、厚度相当,且两块镁合金预锻饼坯的直径差≤20mm,厚度差≤10mm。本发明一种提高大尺寸镁合金锻饼组织均匀性的锻造方法,两块镁合金预锻饼坯的直径均为500~800mm,厚度均为150~180mm。本发明一种提高大尺寸镁合金锻饼组织均匀性的锻造方法,两块镁合金预锻饼坯采用常规单向热压缩锻造的方法制备,锻造温度为400℃~420℃,锻造速度为15~20mm/s,变形量为60%~75%。本发明一种提高大尺寸镁合金锻饼组织均匀性的锻造方法,两次组合锻造后的锻坯的各位置晶粒形态和晶粒大小均匀一致,不存在难变形与自由变形区晶粒不均匀的现象。本发明由于采用上述工艺方法,可制备组织均匀的大尺寸镁合金锻饼,可直接用于机加工制备零件,也可为后续模锻提供组织均匀的优良坯料。在一级热锻过程中,将两块预锻饼坯叠置,使两块预锻饼坯之间的接触面由采用现有技术锻造时的难变形区,变为易变形区,使其发生变形,细化晶粒,翻面后的二级热锻,将一级热锻过程中与锻锤及锻墩接触的面相互接触,其接触面转变为易变形区,而一级热锻过程中相互接触叠置、已经发生变形的面,在二级热锻时则与锻锤及锻墩接触,变成难变形区,在二级热锻时不继续发生变形,两次热锻后的锻坯的各位置晶粒形态和晶粒大小均匀一致,不存在难变形与自由变形区晶粒不均匀的现象,最终使整体保持组织均匀,两次热锻过程如附图1所示。本发明利用塑性加工原理中单向压缩过程中金属的流动规律,将传统锻造过程中产生的难变形区转变为易变形区,组合后的整体变形过程符合塑性加工的基本原理。根据塑性加工原理中影响锻造时变形力的因素可以发现,单块坯料锻造时,由于饼状锻件的直径远大于其厚度(约8~10倍),那么锻件和砧板的摩擦力增大,坯料的易变形区域减小,锻造使需要的变形力迅速增加,当两块坯料组合锻造,使整体锻件的高径比增加,也就相当于增加了易变形区域的大小,锻造时的变形力降低,变形更容易进行。本发明的优点是:解决了大尺寸镁合金锻饼在锻造过程中由于难变形区的存在而导致的饼坯整体组织不均匀性,减小了后续的切削加工量,提高了材料的利用率,同时降低了锻造时的变形力,提高了设备的生产效率。锻造过程中工艺简单,无需对现有设备进行任何改造,得到的锻饼组织和性能均匀,并且可实现大批量生产。综上所述,本发明为提高大尺寸镁合金锻饼组织均匀性提供了一条简单高效的有效途径。附图说明:附图1为常规方式锻造后根据组织不均匀性的三个分区示意图。附图2为两次组合锻造过程示意图。附图3为实施例3合金锻造后的宏观形貌。附图4为实施例3合金锻造后锻饼表面附近的金相组织。附图5为实施例3合金锻造后锻饼中心部位的金相组织。附图6为采用现有技术对实施例3的合金锻造后锻饼表面附近的金相组织。附图7为采用现有技术对实施例3合金锻造后锻饼中心部位的金相组织。图1中,1表示难变形区,2表示自有变形区,3表示易变形区;图2中,第一次锻造时,两个预锻饼坯的“1反”和“2正”两个区域本来为难变形区,组合后变为组合体的易变形区,“1正”和“2反”区域仍然为难变形区,一次锻造过程,消除了“1反”和“2正”区域的难变形组织,使其变为易变形区组织;第一次组合锻造结束后,分别转180度后进行第二次组合锻造,“1正”和“2反”两个区域本来为难变形区,组合后变为组合体的易变形区,二次锻造过程,消除了“1正”和“2反”区域的难变形组织,经过两次组合锻造,两块坯料中的难变形区均消失;图3中,实施例3合金锻造后,锻坯直径为1000mm,厚度为115mm;从图4、图5可见,采用本方法锻造的锻饼,由于在工艺上避免了表面附近和中心部位变形的均匀的情况,最终锻饼各部位的晶粒大小均匀。从图6、图7可见由于传统锻造方法难变形区在锻造过程中基本不发生变形,保持变形前组织特征,而变形更集中于易变性区,导致传统方法锻造的锻饼表面附近的难变形区与心部易变形区晶粒大小不均匀的现象。具体实施方式:实施例1采用常规单向热压缩锻造的方法,在410℃±10℃温度条件下,以速度为20mm/s的条件对直径为300mm,高度为500mm的AZ80镁合金圆柱铸锭,经2火锻造至直径为500mm,厚度为180mm的锻饼,变形量为64%。锻造前在410℃±10℃的电阻炉中保温12小时。锻造过程为避免鼓肚开裂,第一火和第二火锻造结束时,采取小变形压边锻造的方法对锻饼鼓肚部分进行压缩变形,变形量为15%~18%。按照相同的工艺条件锻造同样尺寸的锻饼共两块。分别标记为1号和2号,并对两个锻饼的正反面分别标记“1正”、“1反”、“2正”、“2反”。将2块经过标记的锻饼放入410±10℃的电阻炉中保温2小时。保温结束,将两块坯料从电阻炉中取出,按照“1正1反2正2反”叠放后在油压机上进行整体压缩变形,压缩速度为15mm/s,共压缩60mm,变形为16.6%。第一次组合锻造后两块锻饼的直径为550mm,厚度为150mm。将第一次组合锻造的两块饼坯放入410±10℃的电阻炉中保温20分钟后取出,按照“1反1正2反2正”的顺序叠放后进行二次整体组合锻造,压缩速度为12mm/s,共压缩50mm,变形为16.6%。第二次组合锻造后两块锻饼的直径为600mm,厚度为125mm,二次锻造后空冷。实施例2采用常规单向热压缩锻造的方法,在410℃±10℃温度条件下,以速度为18mm/s的条件对直径为350mm,高度为640mm的AZ80镁合金圆柱铸锭,经2火锻造至直径为700mm,厚度为160mm的锻饼,变形量为75%。锻造前在410℃±10℃的电阻炉中保温18小时。锻造过程为避免鼓肚开裂,第一火和第二火锻造结束时,采取小变形压边锻造的方法对锻饼鼓肚部分进行压缩变形,变形量为15%~18%。按照相同的工艺条件锻造同样尺寸的锻饼共两块。分别标记为1号和2号,并对两个锻饼的正反面分别标记“1正”、“1反”、“2正”、“2反”。将2块经过标记的锻饼放入410±10℃的电阻炉中保温2.5小时。保温结束,将两块坯料从电阻炉中取出,按照“1正1反2正2反”叠放后在油压机上进行整体压缩变形,压缩速度为12mm/s,共压缩50mm,变形为15.6%。第一次组合锻造后两块锻饼的直径为760mm,厚度为135mm。将第一次组合锻造的两块饼坯放入410±10℃的电阻炉中保温25分钟后取出,按照“1反1正2反2正”的顺序叠放后进行二次整体组合锻造,压缩速度为15mm/s,共压缩50mm,变形为18.5%。第二次组合锻造后两块锻饼的直径为845mm,厚度为110mm,二次锻造后空冷。实施例3采用常规单向热压缩锻造的方法,在410℃±10℃温度条件下,以速度为15mm/s的条件对直径为400mm,高度为720mm的AZ80镁合金圆柱铸锭,经2火锻造至直径为800mm,厚度为180mm的锻饼,变形量为75%。锻造前在410℃±10℃的电阻炉中保温18小时。锻造过程为避免鼓肚开裂,第一火和第二火锻造结束时,采取小变形压边锻造的方法对锻饼鼓肚部分进行压缩变形,变形量为15%~18%。按照相同的工艺条件锻造同样尺寸的锻饼共两块。分别标记为1号和2号,并对两个锻饼的正反面分别标记“1正”、“1反”、“2正”、“2反”。将2块经过标记的锻饼放入410±10℃的电阻炉中保温2.5小时。保温结束,将两块坯料从电阻炉中取出,按照“1正1反2正2反”叠放后在油压机上进行整体压缩变形,压缩速度为15mm/s,共压缩70mm,变形为19.5%。第一次组合锻造后两块锻饼的直径为890mm,厚度为145mm。将第一次组合锻造的两块饼坯放入410±10℃的电阻炉中保温30分钟后取出,按照“1反1正2反2正”的顺序叠放后进行二次整体组合锻造,压缩速度为15mm/s,共压缩60mm,变形为20%。第二次组合锻造后两块锻饼的直径为1000mm,厚度为115mm,二次锻造后空冷。附表1为实施例3合金锻造后锻饼表面附近和中心部位的力学性能。表1取样位置抗拉强度(MPa)屈服强度(MPa)伸长率(%)表面位置3091797.68心部位置3041837.39从表1的数据并结合附图4、5,可以看出:由于采用本发明制备的锻饼表面位置和心部位置晶粒大小均匀,使得这两个位置的强度和伸长率基本一致,避免了传统工艺制备的锻饼各位置性能差异较大的缺点。