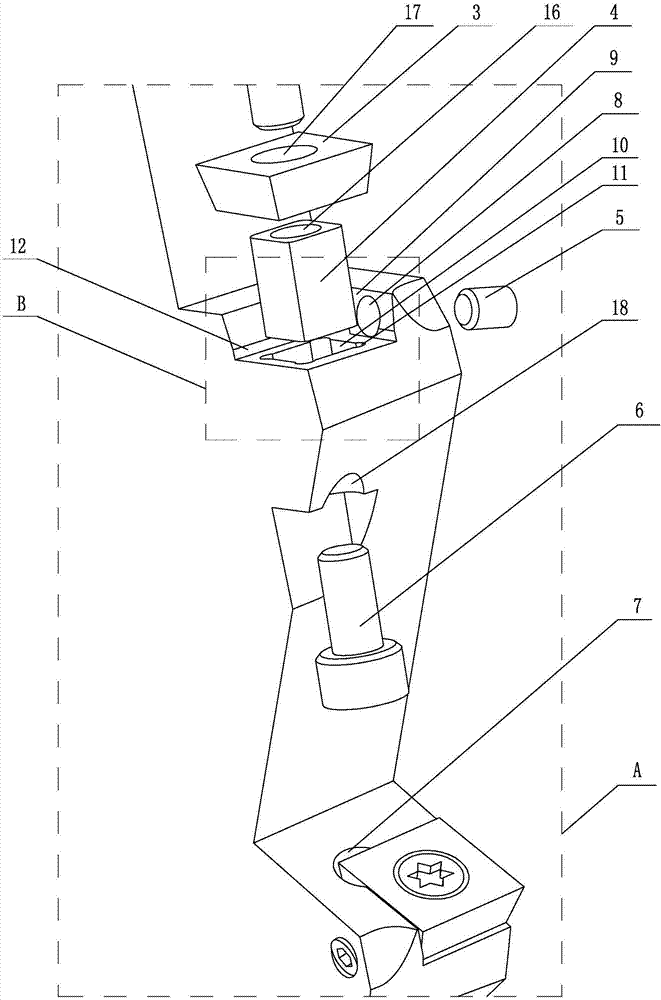
本发明涉及一种盘铣刀具,属于切削加工刀具技术领域。
背景技术:整体叶盘作为航空发动机重要核心结构部件,其结构复杂、叶片扭曲度大、流道开敞性差,毛坯多选用钛合金等难加工材料,给整体叶盘的制造带来很大的难度。对整体叶盘进行开粗加工时材料去除量在60%左右,因此粗加工刀具的性能对整体叶盘的加工效率影响显著。传统的整体叶盘开槽粗加工工艺主要采用球头铣刀对槽型进行行切或使用插刀进行插铣加工,加工过程中刀具磨损较为严重,当刀具径向切入时所受切削力较大,刀具易折断,不得不进行刀具的更换,不仅影响了整体叶盘的加工效率而且使其制造成本增加,采用盘铣刀对整体叶盘进行开粗加工,可以有效解决上述问题。而现有的盘铣刀具多为直齿结构,切削宽度固定,同一切削时间内参与切削的刀片承受的切削力大,刀具刚切入时振动明显,刀片磨损严重,当整体叶盘流道尺寸发生变化时,为了保证加工效率,不得不重新进行盘铣刀具的设计以满足切宽要求,增加了刀具研发成本,并且重新换刀又增加了整体叶盘的加工周期。针对整体叶盘流道的开槽粗加工,对现有的盘铣刀结构进行设计优化,以求满足整体叶盘的高效加工要求。
技术实现要素:本发明的目的是为解决现有的整体叶盘开槽存在加工效率低、刀具易磨损、排屑差、切削宽度固定、成本高的问题,提出了一种整体叶盘流道开粗平装错齿变切宽盘铣刀具。本发明的刀具主要应用于对整体叶盘的开槽粗加工过程,改善整体叶盘加工过程中加工效率低、刀具受力大、刀具磨损严重、切削宽度不可调等问题。通过平装错齿结构的刀具设计,可以实现刀具轻快加工,切削性能、刀具寿命得到明显提高;通过可调结构的设计,实现在一定的切宽范围内,同一把刀具对不同槽宽的加工,且刀片调整方便、定位准确。拉紧螺钉、紧固螺钉等采用标准件设计,利于刀具的标准化设计及规模化生产,实现刀具的制备到工件的整个加工周期成本的降低,提高整体叶盘的加工效率。实现上述目的,本发明采取的技术方案如下:整体叶盘流道开粗平装错齿变切宽盘铣刀具,其组成包括刀体、中心衬套、多个定位螺钉及多个刀片,所述的刀体的中心加工有中心通孔,所述的中心衬套固定安装在刀体的中心通孔内,中心衬套内壁沿轴向加工有键槽,刀体的外圆周面上均布加工有多个L形排屑槽,且所述的多个L形排屑槽均贯穿刀体的厚度设置,每个L形排屑槽的短槽侧面上均加工有一个刀槽,每个所述的刀槽由槽底面和两个相交的槽侧壁构成,所述的整体叶盘流道开粗平装错齿变切宽盘铣刀具还包括切宽调整机构,所述的切宽调整机构包括多个滑块、多个紧定螺钉和多个拉紧螺钉;所述的多个刀槽的每相邻两个刀槽沿刀体的轴向交错设置,每个刀槽的底面上加工有一个滑块槽,每个所述的滑块上加工有螺纹孔一,每个所述的滑块槽内设置有一个滑块,每个刀槽内设置有一个刀片,每个刀片与滑块可拆卸固定连接,每个L形排屑槽的长槽侧面上加工有一个与滑块的螺纹孔一同轴的通孔二,每个滑块槽与滑块之间沿轴向设有间隙,每个滑块槽的通孔二内穿入一个拉紧螺钉,所述的拉紧螺钉与滑块的螺纹孔一紧固连接,每个刀槽垂直于轴向的所述的槽侧壁上加工有一个螺纹孔二,每个所述的螺纹孔二内旋紧有一个紧定螺钉,每个所述的紧定螺钉沿轴向顶靠在相对应的刀片上。本发明相对于现有技术的有益效果是:1、由于加工整体叶盘的盘铣刀具尺寸较大,刀具制备成本较高,在保证刀体强度的前提下,综合考虑刀具材料的适应条件,将刀体材料确定为42CrMo,本发明刀具可实现切宽的可变切削,即在切宽允许调整范围内,能够在单侧0.1-1mm内实现切宽的简便实用调整,考虑到盘铣刀具采用错齿结构设计,即两侧刀片同时参与切削,可以实现刀具的切削宽度在19mm-21mm范围内自由调整,同时采用可转位结构对刀体进行设计,使刀片的装配、更换过程方便,而采用滑块、拉紧螺钉及紧定螺钉的调整结构在调整刀具切宽时减少调整时间,滑块制备简单,精度容易保证,加工误差小。2、本发明所述的刀具采用平装错齿可转位结构,切削过程中两个刀齿(也是刀片)交互参与切削,采用平装结构相比于立装结构,切削过程中刀具切削更加轻快,切削过程中排屑顺畅,提高刀具加工效率。切削过程中刀具同时有两个共同承担切削力的作用,能够有效减少单一刀齿受力集中状态,有效延长刀具使用寿命;通过键槽对刀具进行轴向定位,提高定位精度,减小加工过程中刀具旋转时因扭矩过大而损坏刀具。3、刀具中的L形排屑槽采用立铣刀90°直开方式,即通过φ16的合金立铣刀垂直于刀片矢量对排屑空间进行加工,这种敞开式的排屑空间设计可有效增加刀具容屑、排屑空间,使切屑更易卷曲、折断、快速排出,不会堆积在刀具表面,并且能带走刀具加工过程中产生的大部分切削热,有效提高刀具的切削效率及使用寿命。4、刀槽设计有整体叶盘钛合金材料加工常用的预装角度,可使用前角0°的刀片直接安装,并可根据不同材料刃磨前角,使得盘铣刀使用更加灵活,降低加工的成本;切宽调整机构与刀槽组合刀片及滑块即能定位,又能保护刀尖,避免安装后刀具与刀槽的干涉以及加工过程中刀尖与刀体的摩擦,避免刀片的二次破坏。5、刀具采用径向前角为6°~8°轴向前角为4°~6°,更好地保证切削过程中的刀具的切削性能,同时增加修正角度,有效避免刀具的径向角和轴向角在制备过程中对刀槽底面造成不光顺的影响,可使加工后的刀槽底面更加平整,提高刀片的定位安装精度。6、所述的刀具的定位螺钉、拉紧螺钉、紧定螺钉均采用标准件设计,可以有效降低刀具的制造成本,便于刀具的批量化生产。综上,本发明主要用于整体叶盘流道开槽粗加工,改善了刀具加工过程中存在的问题,而且可以在不更换刀具的前提下,进行刀具切削宽度的调整,使加工效率提高25%左右,延长刀具使用寿命30%左右,降低加工成本20%左右。附图说明图1为本发明的整体叶盘流道开粗平装错齿变切宽盘铣刀具的轴测图;图2为图1的A处局部放大图;图3为图2的B处局部放大图。上述附图中部件名称及标号汇总如下:刀体1、定位螺钉2、刀片3、滑块4、紧定螺钉5、拉紧螺钉6、退刀槽一7、螺纹孔二8、刀槽9、滑块槽10、退刀槽二11、直棱12、L形排屑槽13、中心衬套14、键槽15、螺纹孔一16、通孔一17、通孔二18。具体实施方式具体实施方式一:如图1~图3所示,整体叶盘流道开粗平装错齿变切宽盘铣刀具,其组成包括刀体1、中心衬套14、多个定位螺钉2及多个刀片3(优选刀片3的数量为12个),所述的刀体1的中心加工有中心通孔,所述的中心衬套14固定安装在刀体1的中心通孔内,中心衬套14内壁沿轴向加工有键槽15,刀体1的外圆周面上均布加工有多个L形排屑槽13,且所述的多个L形排屑槽13均贯穿刀体1的厚度设置,每个L形排屑槽13的短槽侧面上均加工有一个刀槽9(优选刀槽9的数量为12个),每个所述的刀槽9由槽底面和两个相交的槽侧壁构成,所述的整体叶盘流道开粗平装错齿变切宽盘铣刀具还包括切宽调整机构,所述的切宽调整机构包括多个滑块4、多个紧定螺钉5和多个拉紧螺钉6;所述的多个刀槽9的每相邻两个刀槽9沿刀体1的轴向交错设置,每个刀槽9的底面上加工有一个滑块槽10,每个所述的滑块4上加工有螺纹孔一16,每个所述的滑块槽10内设置有一个滑块4,每个刀槽9内设置有一个刀片3,每个刀片3与滑块4可拆卸固定连接(即刀片3上加工有通孔一17,定位螺钉2穿过刀片3上的通孔一17与滑块4的螺纹孔一16可拆卸固定连接),每个L形排屑槽13的长槽侧面上加工有一个与滑块4的螺纹孔一16同轴的通孔二18,每个滑块槽10与滑块4之间沿轴向设有间隙,每个滑块槽10的通孔二18内穿入一个拉紧螺钉6,所述的拉紧螺钉6与滑块4的螺纹孔一16紧固连接,每个刀槽9垂直于轴向的所述的槽侧壁上加工有一个螺纹孔二8,每个所述的螺纹孔二8内旋紧有一个紧定螺钉5,每个所述的紧定螺钉5沿轴向顶靠在相对应的刀片3上(使用紧定螺钉5可以改变滑块10的轴向位置,进而实现刀片3切削宽度的改变)。当刀片3位于初始位置时,刀具切宽最小,此时紧定螺钉5不参与滑块4的轴向运动,通过刀槽9的侧壁对刀片3起到支撑作用,并使用拉紧螺钉6对滑块4起到夹紧作用。当刀片3偏移1.0mm时,即单侧刀具切宽增加1mm,调整过程中先将拉紧螺钉6松开,将滑块4和刀片3所构成的整体沿刀槽9外侧即切宽增大方向移动,直至达到切宽的有效长度,此时使用拉紧螺钉6对滑块4进行预固定,通过千分表辅助紧定螺钉5对滑块4与刀片3的整体进行精确的调整,实现每个刀片3切削的一致性,使每个刀片3径向跳动控制在0.05mm以内,保证刀片3在刀槽9中定位的一致性,最后将拉紧螺钉6旋紧,使刀片3与刀槽9的槽侧壁完成贴合。通过使用拉紧螺钉6将滑块4顶部固定,在刀片3宽度方向通过使用紧定螺钉5调整滑块4的轴向尺寸进而实现刀片3切宽的顺畅改变。本实施方式采用可转位平装错齿结构,使刀具对流道进行开槽加工中能够实现轻快切削,有利于减少加工过程中刀具受到的切削力,刀具寿命得到明显提高。其中紧定螺钉5与拉紧螺钉6分别采用型号为GB/T77-2000M5×10与GB/T70.1-2000M4×6的螺钉标准件。具体实施方式二:如图1~图3所示,具体实施方式一所述的整体叶盘流道开粗平装错齿变切宽盘铣刀具,每个所述的刀槽9均设计有预安装角度:即轴向前角为4°~6°,径向前角为6°~8°,轴向后角为13°~15°,径向后角为10°~12°。具体实施方式三:如图1及图2所示,具体实施方式一所述的整体叶盘流道开粗平装错齿变切宽盘铣刀具,每个所述的刀槽9槽底面的顶角处均加工有退刀槽一7。具体实施方式四:如图1~图3所示,具体实施方式一所述的整体叶盘流道开粗平装错齿变切宽盘铣刀具,每个所述的刀槽9的两个槽侧壁下端均加工有直棱12。具体实施方式五:如图2及图3所示,具体实施方式一所述的整体叶盘流道开粗平装错齿变切宽盘铣刀具,每个所述的滑块槽10的每个角部均加工有一个退刀槽二11。具体实施方式六:如图1所示,具体实施方式一、二、三或四所述的整体叶盘流道开粗平装错齿变切宽盘铣刀具,所述的L形排屑槽13的长槽侧面和短槽侧面之间的夹角为90°。具体实施方式七:如图1所示,具体实施方式一所述的整体叶盘流道开粗平装错齿变切宽盘铣刀具,所述的刀体1的材料为42CrMo。具体实施方式八:如图2及图3所示,具体实施方式一所述的整体叶盘流道开粗平装错齿变切宽盘铣刀具,每个所述的滑块槽10与设置在其内的滑块4之间的轴向间隙均为0.1-1mm。实施例1:结合图1说明,在本实施例中,所述的刀片3采用88°菱形结构设计,其四边上均可作为刀具的有效切削刃,可以进行多次重复换刀,刀片3采用5°的前角,12°的后角,保证刀具流道开粗过程中既保证切削刃有一定的锋利程度又能保证切削刃有足够的强度,刀片3材料选用TiAlN硬质合金涂层材料,减少切削整体叶盘钛合金材料时对刀片3的磨损,提高刀具的使用寿命,加工过程中刀体1材料为42CrMo,增加刀体1的强度,刀体直径为250mm,所述刀体1中心加工有中心通孔,中心通孔直径为40mm,中心通孔中固定安装有中心衬套14,主要用于将铣刀具连接到刀柄上,并且能够增加刀具强度;中心衬套14内设计有轴向键槽15进行轴向定位,提高定位精度,减小刀具旋转过程中因扭矩过大而损坏刀具。实施例2:结合图1~图3说明,在本实施例中,L形排屑槽13的长槽侧面和短槽侧面之间的夹角为90°,较大的排屑开敞空间有利于切屑快速排出,不会堆积,并且能带走刀具切削产生的大部分热量,增加刀具使用寿命,提高切削效率。每个L形排屑槽13的短槽侧面上加工有一个刀槽9,考虑到对刀槽9制备加工过程中走刀方式,清根过程等因素;刀槽9槽底面的顶角处加工有退刀槽一7,为刀片3与刀槽9预留一定量的间隙空间,防止当切削力过大时刀片3与刀槽9直接接触,使刀片3过早的发生挤压变形,影响刀具的切削性能,同时刀槽9设计有直棱12,起到空刀作用,采用刀片3与刀槽9底面紧密贴合,可以提高刀片3与刀槽9间定位配合精度,进而提高刀片3的安装定位精度,此外在每个刀槽9垂直于轴向的槽侧壁上加工有一个螺纹孔二8,紧定螺钉5通过在螺纹孔二8中的旋调,对刀片3的切宽进行调整。实施例3:结合图1~图3说明,在本实施例中,每个滑块4上设有螺纹孔一16,滑块4在滑块槽10内通过拉紧螺钉6将其沿径向方向固定,使用紧定螺钉5可以改变滑块10的轴向位置,进而实现刀片3切削宽度的改变。当刀片3不做调整,即刀具加工的最小切宽,此时紧定螺钉5不参与滑块4的轴向运动,通过刀槽9的侧壁对刀片3起到支撑作用,并使用拉紧螺钉6对滑块4起到夹紧作用。当刀片3偏移1.0mm时,即单侧刀具切宽增加1mm,调整过程中先将拉紧螺钉6松开,将滑块4和刀片3所构成的整体沿刀槽9外侧即切宽增大方向移动,直至达到切宽的有效长度,此时使用拉紧螺钉6对滑块4进行预固定,通过调整紧定螺钉5,对滑块4与刀片3的整体进行调整,直至刀片3与刀槽9侧壁完全贴合。实施例4:结合图1~图3说明,在本实施例中,所述的刀槽4设计有预安装角度:即轴向前角为4°~6°,径向前角为6°~8°,轴向后角为13°~15°径向后角为10°~12°;可用前角0°的刀片直接安装,并可根据不同材料刃磨刀具前角,使得盘铣刀具使用更加灵活,降低加工的成本。实施例5:结合图1-图3说明,在本实施例中,所述在刀槽9底面设计有滑块槽10,考虑到滑块槽10的尺寸决定了滑块4的移动位置,进而决定了刀具的可变切宽尺寸,为了保证刀具的定位加工精度及刀具可调切宽尺寸范围,设计的滑块槽10在槽宽方向尺寸应大于滑块4,且二者之间的间隙在0.1~1mm之间,便于滑块4在滑块槽10内滑动,从而实现槽宽的改变;同时考虑到滑块槽10的加工工艺,在不影响刀具制备过程中的进刀及清根等操作的情况下,在滑块槽10内设计有退刀槽二11,从而避免了滑块4与滑块槽10发生过盈配合,发生过早磨损,影响刀具切宽调整时的定位安装精度。