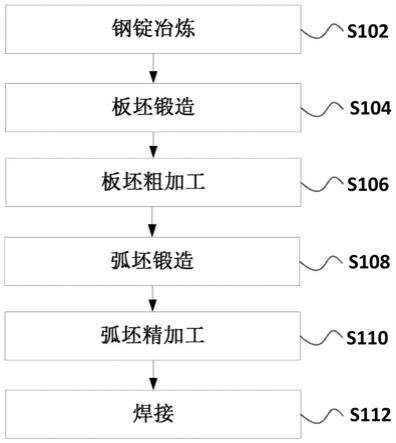
1.本技术涉及不锈钢材料制造领域,更具体地涉及一种大型环形锻件及其制造方法以及反应堆支承环。
背景技术:2.大型环形锻件广泛应用于航空航天、石油、化工及反应堆等大型容器中,其制造技术直接决定着重大装备的制造水平。
3.反应堆内的大型环形锻件包括反应堆支承环,其为示范快堆堆容器内承载最重的结构件。反应堆支承环承载超过6800t,可称之为反应堆的脊梁,因此对支承环的力学性能要求十分严格。如何改进支承环的制造工艺,确保支承环材料整体均匀性好、缺陷少,减小服役风险就显得尤为重要。
技术实现要素:4.鉴于上述问题,提出了一种克服上述问题或者至少部分地解决上述问题的一种大型环形锻件及其制造方法以及反应堆支承环。
5.根据本技术的第一个方面,提供了一种大型环形锻件的制造方法,包括:
6.钢锭冶炼步骤:冶炼多个钢锭坯料;
7.板坯锻造步骤:对每个所述钢锭坯料进行锻造处理,形成板状锻件毛坯;
8.板坯粗加工步骤:对所述板状锻件毛坯进行粗加工处理;
9.弧坯锻造步骤:利用锻造工艺对粗加工处理后的板状锻件毛坯进行热弯曲成形处理,形成圆弧锻件毛坯;
10.弧坯精加工步骤:对所述圆弧锻件毛坯进行精加工处理,形成横断面具有预设形状的圆弧锻件;以及
11.焊接步骤:对精加工处理后的多个圆弧锻件进行焊接处理,形成所述环形锻件。
12.根据本技术的第二个方面,提供了一种大型环形锻件,其利用本技术第一方面的制造方法制造。
13.根据本技术的第三个方面,提供了一种反应堆支承环,其利用本技术第一方面的制造方法制造。
附图说明
14.通过下文中参照附图对本技术所作的描述,本技术的其它目的和优点将显而易见,并可帮助对本技术有全面的理解。其中:
15.图1是根据本技术实施例的支承环的俯视结构图;
16.图2是沿图1中a
‑
a方向的剖面图;
17.图3是图2中b区域的局部放大图;
18.图4是根据本技术一个实施例的大型环形锻件的制造方法流程图;以及
19.图5是根据本技术另一个实施例的大型环形锻件的制造方法流程图。
20.应该注意的是,附图只是为了便于描述优选实施例,而不是本技术本身。附图没有示出所描述的实施例的每个方面,并且不限制本技术的范围。
具体实施方式
21.下面详细描述本技术的实施方式,实施方式的示例在附图中示出,其中自始至终相同或类似的标号表示相同或类似的元件或具有相同或类似功能的元件。下面通过参考附图描述的实施方式是示例性的,仅用于解释本技术,而不能理解为对本技术的限制。
22.下文的公开提供了多个不同的实施方式或例子用来实现本技术。为了简化本技术的公开,下文中对特定例子的部件和方法进行描述。当然,它们仅仅为示例,并且目的不在于限制本技术。
23.图1至图3示出了根据本技术一个实施例的反应堆支承环10的结构图。参见图1至图3,从支承环10的横断面101可以看出,支承环10的内侧102设有接口1011和接口1012,外侧103设有接口1013和接口1014。支承环10的四个接口1011、1012、1013、1014,分别与反应堆内的堆内支承支承筒、主容器底封头、主容器筒体、主容器支承筒焊接。堆内支承支承筒与堆内支承相焊接,将堆内支承及堆内支承承载的设备载荷传递至主容器;主容器支承筒与保护容器支承环焊接,主容器支承筒将主容器的重量载荷传递至保护容器;支承环10内侧焊接有2个导向块(图中未示出),用于堆内支承现场安装时导向定位。
24.支承环主体材料为316h不锈钢,所受工况复杂,截面尺寸大,规格为643
×
285mm,外径达到15450mm。对于这种规格的环形件,制造工艺难度大,制成后材料均匀性差,缺陷多,对于堆内支承环而言,服役风险较高。
25.由此,本技术提供了一种大型环形锻件的制造方法,制成的环形锻件材料整体均匀性好、缺陷少。
26.图4是根据本技术一个实施例的大型环形锻件的制造方法流程图。参见图4,在本技术一些实施例中,一种大型环形锻件的制造方法包括钢锭冶炼步骤s102至焊接步骤s112。
27.钢锭冶炼步骤s102,冶炼多个钢锭坯料;
28.板坯锻造步骤s104,对每个钢锭坯料进行锻造处理,形成板状锻件毛坯;
29.板坯粗加工步骤s106,对板状锻件毛坯进行粗加工处理;
30.弧坯锻造步骤s108,利用锻造工艺对粗加工处理后的板状锻件毛坯进行热弯曲成形处理,形成圆弧锻件毛坯;
31.弧坯精加工步骤s110,对圆弧锻件毛坯进行精加工处理,形成横断面具有预设形状的圆弧锻件;
32.焊接步骤s112,对精加工处理后的多个圆弧锻件进行焊接处理,形成环形锻件。
33.本技术实施例先利用锻造工艺制造板状锻件毛坯,接着对板状锻件毛坯进行粗加工处理,之后进行弧坯锻造处理,然后再进行弧坯精加工处理,之后再进行焊接处理。相比相关技术中在模锻成型后进行煨弯处理相比,本技术实施例先利用锻造工艺使板状锻件毛坯弯曲成形,之后再进行精加工,制成的环形锻件材料整体均匀性好、缺陷少。
34.在本技术实施例的制造方法中,从锻件材质角度考虑,圆弧锻件的制造难度在于
钢锭的冶金质量要求高。
35.因此,在一些实施例中,在钢锭冶炼步骤s102中,钢锭坯料可以采用电炉粗炼、vod精炼炉精炼以及电渣重熔的冶炼方式生产。
36.具体地,将生产钢锭坯料的原料依次在电炉中进行粗炼,在vod精炼炉中进行精炼,之后进行氩气保护浇注形成钢锭,将钢锭根据要求选用锻制或轧制工艺制成电极棒,然后将电极棒进行电渣重熔,制得钢锭坯料。
37.对于支承环而言,其锻件材质为316h奥氏体不锈钢。316h奥氏体不锈钢中cr、mo元素含量较高,大规格钢锭凝固过程中极易产生组织缺陷。为确保316h锻件的冶金质量,采用电弧炉、炉外精炼、电渣重熔工艺制造不锈钢钢锭。利用电渣重熔凝固速度快的特点,抑制有害相的析出,进而提高合金组织均匀性,同时对电渣钢锭进行高温均匀化处理,使钢锭组织均匀。
38.针对合金易出现的as、sn、pb、se杂质微量元素超标问题,在电极棒熔炼阶段主要通过精选原材料的办法进行解决。从源头上避免了杂质微量元素超标问题的发生。
39.h含量控制方面,利用炉外精炼vod真空环境对氢元素予以脱除,并在精炼阶段通过精选渣料,高温烘烤等办法减少增氢。
40.由于利用电弧炉和炉外精炼工艺制备的电极经电渣重熔后形成的钢锭坯料直接用于锻造,为减少锻造产生表面开裂,需提高电渣重熔锭表面质量,采用适当的重熔速度冶炼抑制钢锭表面渣沟的产生。重熔速度一般可以选为15~30kg/min,在此范围内,钢锭表面渣沟较少表面质量较好。
41.针对大规格钢锭非金属夹杂物含量超标等问题,在电渣重熔工艺中,可采取优选渣料和液渣起弧的办法进行解决。
42.在本技术实施例的制造方法中,从锻件形状角度考虑,圆弧锻件的制造难度在于超大壁厚奥氏体不锈钢锻件成形。
43.奥氏体不锈钢由于锻造区间窄,锻造过程中由于析出有害相极易造成锻造开裂,与此同时由于不能通过热处理来调整晶粒尺寸,因此锻造过程必须保证具有较大的变形量,才能确保发生完全动态再结晶细化晶粒,但自由锻由于锻造时间长,锻造过程中的降温以及不均匀步锤等因素造成各位置变形量及变形条件不同,从而常造成混晶问题,这是大型不锈钢锻造的一大难点。
44.因此,在本技术一些实施例中,在板坯锻造步骤s104中,锻造处理可以包括依次进行的镦粗处理(使坯料高度减小,横截面增大的成形工序)和多次拔长处理(使坯料横截面减小,长度增加的成形工序)以及一次拔扁方处理,形成矩形板状锻件毛坯。
45.具体地,可以在第一预设温度下进行镦粗处理,之后在第一预设温度下进行三次拔长处理,最后在第一预设温度下进行拔扁方处理。
46.在具体的实施例中,可在锻造处理开始之前,先切除钢锭坯料的水冒口弃料。之后,按照锻比1.2对钢锭进行一次墩粗处理,锻造温度为1250℃~850℃;之后,按照锻比1.8对墩粗后的钢锭进行一次拔长处理,锻造温度为1250℃~850℃;之后,按照锻比1.8对拔长后的钢锭再进行一次拔长处理,锻造温度为1250℃~850℃;之后,按照锻比1.7对拔长后的钢锭又进行一次拔长处理,锻造温度为1250℃~850℃;之后,按照锻比1.4对拔长后的钢锭进行一次拔扁方处理形成板状锻件毛坯,锻造温度为1050℃~900℃。锻造后的板状锻件毛
坯重48.3t。
47.在一些实施例中,在上述拔长处理和拔扁方处理中均采用热挤压成形工艺。
48.本技术实施例针对支承环的特点,在板状锻件毛坯的制造中,开创性地采用了热挤压成形的制造工艺,热挤压过程中,锻坯经受三向压应力,有效抑制了锻坯的开裂,同时进行热挤压成形能够保证锻件具有较大的变形量,此外,热挤压过程为连续变形过程,其成形速率较快,近似可视为等温变形,且各位置变形量及变形条件较一致,从而进一步保证了变形后各位置晶粒尺寸的均匀性。
49.在上述板坯锻造步骤s104中,还可以采用胎模锻的工艺。胎模锻是介于自由锻与模锻之间的一种锻造方法。采用热挤压成形复合胎模锻工艺实现了锻件的近净成形(即锻件成型后,仅需要少量加工或不再加工),提高了生产效率,降低了制造成本。
50.此外,通过应力分析评定,支承环10与主容器底封头连接处(对应接口1012)的设计裕量最小。由此导致支承环10制造过程中,会出现以下技术问题:一是留给设计人员进行结构设计的空间、裕量有限,结构设计会受到限制;二是对制造、焊接工艺要求严格,即使出现较小尺寸偏差也会导致结构设计裕量降低,结构安全性降低。而本技术通过在板坯锻造步骤s104利用热挤压成形工艺制作板坯,使得板坯成型质量好,便于后续加工时进行尺寸控制,确保设计裕量不会降低。
51.在弧坯锻造步骤s108中,热弯曲成形处理可以采用整体加热分段弯曲的锻造成形方式。即,将锻件毛坯整体加热到预设温度,然后采用分段弯曲的锻造方式使锻件毛坯形成具有圆弧形状的圆弧锻件毛坯。
52.在一些实施例中,在弧坯锻造步骤s108中,加热温度范围可选为950℃~1050℃。整个锻造过程拟压三锤,一火次完成。
53.在一些实施例中,弧坯锻造步骤s108包括:将板状锻件毛坯整体送至加热炉加热至预设温度;将板状锻件毛坯沿长度方向划分为第一部分、第二部分、以及连接第一部分和第二部分的中间部分;其中中间部分的长度小于等于第一部分和第二部分的长度;对第一部分进行一次锤压以使第一部分形成弧形;之后对第二部分进行一次锤压以使第二部分形成弧形;最后对中间部分进行一次锤压,以使中间部分形成弧形,从而使板状锻件毛坯整体形成圆弧锻件毛坯。
54.在一些实施例中,对中间部分进行一次锤压时的压下行程小于对第一部分和第二部分进行一次锤压时的压下行程,从而使得整个圆弧锻件毛坯内部组织更加均匀。
55.在具体的实施例中,可提供锻造机,其包括锤头、弧形的上砧座和下砧座,其中上砧座设置于锤头的下端面。
56.预先在板状锻件毛坯上焊接4支吊耳,利用天车挂吊耳将板状锻件毛坯的第一部分放置于下砧座;利用上砧座对板状锻件毛坯位于下砧座内的第一部分进行第一次锤压,上砧座将坯料完全压至下砧座内弧面后保压一段时间抬锤,压下形程大致为640mm,以使第一部分形成弧形;将板状锻件毛坯的第二部分吊至锻锤下方的下砧座;利用上砧座对板状锻件毛坯位于下砧座内的第二部分进行第二次锤压,压下形程大致为640mm,以使第二部分形成弧形;将板状锻件毛坯的中间部分吊至锻锤下方的下砧座;利用上砧座对板状锻件毛坯位于下砧座内的中间部分进行第三次锤压,压下形程大致为500mm,以使中间部分形成弧形,从而使板状锻件毛坯整体形成圆弧锻件毛坯。
57.在一些实施例中,锻造机为压水机。
58.在一些实施例中,圆弧锻件毛坯对应的圆心角可以在30度至150度之间,进一步优选为60度至120度之间。在一些实施例中,圆弧锻件毛坯的对应的圆心角可以为90度或者大致为90度。这样,通过四个相同的圆弧锻件毛坯即可焊接组成一个完整的环形结构。
59.在弧坯精加工步骤s110中,对圆弧锻件毛坯进行精加工处理。精加工处理可以利用机械加工的方式对圆弧锻件毛坯进行加工,使圆弧锻件毛坯的横断面具有目标产品横断面的预设形状。如前所述,对于反应堆支承环而言,其具有四个接口,在精加工处理时,使圆弧锻件毛坯的内外两侧表面的相应位置形成上述四个接口。
60.在焊接步骤s112中,可以采用埋弧焊焊接方法对多个圆弧锻件进行焊接。例如,对于圆心角为90
°
的圆弧锻件,可将四个圆弧锻件焊接为一整体圆环。
61.图5是根据本技术另一个实施例的大型环形锻件的制造方法流程图。
62.参见图5,在本技术一些实施例中,所述制造方法在板坯粗加工步骤s106与弧坯锻造步骤s108之间,还包括:
63.板坯探伤检测步骤s107,对板坯粗加工处理之后的板状锻件毛坯进行探伤检测,在满足预设条件后进行弧坯锻造步骤s108。
64.探伤检测通常利用超声波进行探伤。超声波探伤时钢板内部严重的缺陷阻碍超声波的行进形成伤波,被判为超声波探伤不合格。超声波探伤发现的缺陷在钢板上呈片状、点状、线状等多种形式。如果超声波探伤不合格(即不满足预设条件),则重复钢锭冶炼步骤s102至板坯探伤检测步骤s107,直至探伤检测结合(即满足预设条件),接着进行弧坯锻造步骤s108。
65.参见图5,在本技术一些实施例中,所述制造方法在弧坯锻造步骤s108与弧坯精加工步骤s110之间,还包括:
66.弧坯粗加工步骤s1091,对圆弧锻件毛坯进行粗加工处理。弧坯粗加工步骤s1091是为弧坯精加工步骤s110做铺垫,由于粗加工和精加工使用的加工方式、加工仪器等均有区别,在精加工之前进行粗加工有利于提高加工效率。
67.参见图5,在本技术一些实施例中,所述制造方法在弧坯粗加工步骤s1091与弧坯精加工步骤s110之间,还包括:
68.弧坯固溶热处理步骤s1092,对粗加工处理后的圆弧锻件毛坯进行固溶热处理。
69.固溶热处理用于保证合金元素及碳化合物等完全固定在晶粒中得到奥氏体组织状态。固溶热处理的加热温度可为1050℃
±
10℃,每100mm截面至少保温1h,圆弧锻件毛坯出炉到入水时间不超过12min。
70.在一些实施例中,所述制造方法在弧坯固溶热处理步骤s1092与弧坯精加工步骤s110之间,还包括:
71.弧坯性能检测步骤s1093,对固溶热处理后的圆弧锻件毛坯的性能进行检测,在满足预设条件后进行弧坯精加工步骤s110。
72.性能试验可以包括熔敷金属拉伸试验、焊接接头拉伸试验、冲击试验、侧弯试验、晶间腐蚀试验、金相检验、焊缝化学成分检测、硬度试验等。
73.在一些实施例中,弧坯性能检测步骤s1093包括:从圆弧锻件毛坯上切取多个试验块,对所述多个试验块的性能进行检测。
74.在弧坯性能检测步骤s1093中,可在圆弧锻件毛坯圆周方向和轴线方向设置取样位置,且每处位置均需要截取周向、轴向和径向共3个方向的试样。每处取样位置的3个方向分别取1个室温拉伸试样、2个高温拉伸试样、3个(1组)冲击试样。每处取样位置还分别截取1个化学、1个金相试样和1个晶间腐蚀试样。
75.经过测试,性能符合技术条件要求后进行弧坯精加工步骤s110。
76.在一些实施例中,在焊接步骤s112之前,所述制造方法还可包括试焊接步骤s1112,对从圆弧锻件毛坯上切取的至少两个实验块进行试焊接处理,以获得焊接步骤s112的焊接参数。
77.试焊接步骤s1112可具体包括:将至少两个实验块进行焊接,并检测实验块在焊接过程中的内圆弧角变形量和弧长收缩量,根据圆弧角变形量和弧长收缩量调节焊接参数,以获得实验焊接参数作为焊接步骤s112中的焊接参数。换言之,在焊接步骤s112中,根据实验焊接参数进行焊接处理。焊接参数可以包括电流、电压、焊速、坡口宽度等数据。
78.实验块可以为弧坯性能检测步骤s1093中使用的实验块,也可以重新切取新的实验块进行试焊接处理。容易理解,这些实验块的切取并不影响精加工处理之后形成的圆弧锻件的结构。
79.在焊接步骤s112中,在进行焊接之前,提前设计焊接接头,提出焊材要求,最后完成相应装配,采用埋弧焊焊接方法进行焊接。焊接过程中记录每层每道工艺参数,包括电流、电压、焊速、坡口宽度等数据。
80.在焊接步骤s112中,检测内圆弧角变形、弧长收缩量,并根据圆弧角变形量和弧长收缩量调整两侧焊接顺序,以使环形锻件的椭圆度在预设范围内。在一些实施例中,椭圆度应小于7mm。
81.焊接完成后,可以采用铝基无铁砂轮对验证件进行两侧焊缝的打磨,满足pt和rt检测要求。
82.在一些实施例中,在焊接步骤s112之前,所述制造方法还可包括:
83.弧形探伤检测步骤s1111,对弧坯精加工步骤s110之后的圆弧锻件进行弧坯探伤检测,在满足预设条件后进行焊接步骤s112。弧形探伤检测步骤s1111中可以采用ut、pt、dt或vt探伤检测。
84.在一些实施例中,所述制造方法可以在弧形探伤检测步骤s1111之后,再进行试焊接步骤s1112,即,在探伤检测合格之后再进行试焊接处理。
85.在一些实施例中,所述制造方法在焊接步骤s112之后,还可包括:
86.稳定化热处理步骤s114,对环形锻件进行稳定化热处理。
87.对于环形锻件,在实际产品焊接完成后由于结构尺寸太大,无法进行整体热处理,为模拟实际产品制造,采取局部电加热方式进行局部稳定化热处理。为避免奥氏体不锈钢加热过程中出现敏化现象,制定焊后稳定化热处理的温度为400℃
±
15℃,保温时间15h
±
0.5h。
88.在一些实施例中,考虑焊后变形,在弧坯精加工步骤s110中,圆弧锻件内外壁均预留20mm加工量,高度方向预留42mm加工量,焊接时内弧处焊接拉筋等辅具控制焊接变形;焊接坡口选用双面焊接坡口,保证焊后应力分布均匀。在这样的实施例中,在稳定化热处理步骤s114之后,还可进行一次精加工步骤,以对焊接后的环形锻件进行最后的整体精加工。
89.在一些实施例中,所述制造方法在步骤稳定化热处理s114之后,还可包括:
90.环形锻件探伤检测步骤s116,对环形锻件进行pt和验证性rt检测。即,对焊接接头按照asme第iii卷nb
‑
5000进行pt和验证性rt检测及验收。
91.在一些实施例中,在焊接步骤s112之后(即焊接步骤s112与稳定化处理步骤s114之间)及稳定化处理步骤s114之后,均对环形锻件进行pt和验证性rt检测。
92.对于支承环而言,支承环组焊后直径接近16m。在环形锻件探伤检测步骤s116中,由于支承环直径远大于射线探伤室大门宽度,无法进入射线室内进行检测,且焊缝焊后厚度约为320mm,焊缝材质为不锈钢,超出了超声检测的能力上限。
93.为解决上述问题,在焊接步骤s112中,先将圆弧锻件焊接成两个半圆锻件。将半圆锻件放入探伤室内采用9mev加速器进行射线检测。之后,将两个半圆锻件焊接为整体环形锻件,对于最终合口的2条焊缝,将9mev加速器拆装至室外进行透照。
94.射线检测时可将加速器机头拆下,线缆加长,放置在探伤室外的台车上,并研制工装,使加速器机头能在台车上平稳升降及对中,射线室门打开,将支承环放置在台车上,透照时尽量使支承环焊缝靠近射线室,距离加速器出束方向约1.5m,减少射线的辐射和散射范围。
95.将9mev加速器开关按钮外接,采用9mev加速器的延时出束功能,操作人员进入射线室迷宫进行射线防护,或者使用距离防护和屏蔽防护进行射线屏蔽。
96.在一些实施例中,在环形锻件探伤检测步骤s116之后,还可进行破坏性试验。
97.本技术实施例的制造方法解决了大型锻件大断面钢锭凝固过程存在明显尺寸效应的问题,克服了钢锭偏析、疏松、粗晶现象。采用本技术实施例的制造方法,可确保大型奥氏体不锈钢环锻件满足性能试验要求,本技术为制造大厚度奥氏体不锈钢环锻件提供了新的发展方向。
98.采用本技术实施例的制造方法,制造的支承环材料整体均匀性好、缺陷少,满足示范快堆内支承环的力学要求。
99.本技术实施例的制造方法由于不采用锻模成型处理工艺,节约了原材料,缩短了制造周期,大大提高了示范快堆项目主容器支承环制造的可靠性。
100.基于上述制造方法,本技术还提供了一种大型环形锻件和反应堆支承环,利用如前任一实施例的制造方法制造。
101.对于本技术的实施例,还需要说明的是,在不冲突的情况下,本技术的实施例及实施例中的特征可以相互组合以得到新的实施例。
102.以上所述仅为本技术的优选实施例而已,并不用于限制本技术,对于本领域的技术人员来说,本技术可以有各种更改和变化。凡在本技术的精神和原则之内,所作的任何修改、等同替换、改进等,均应包含在本技术的保护范围之内。