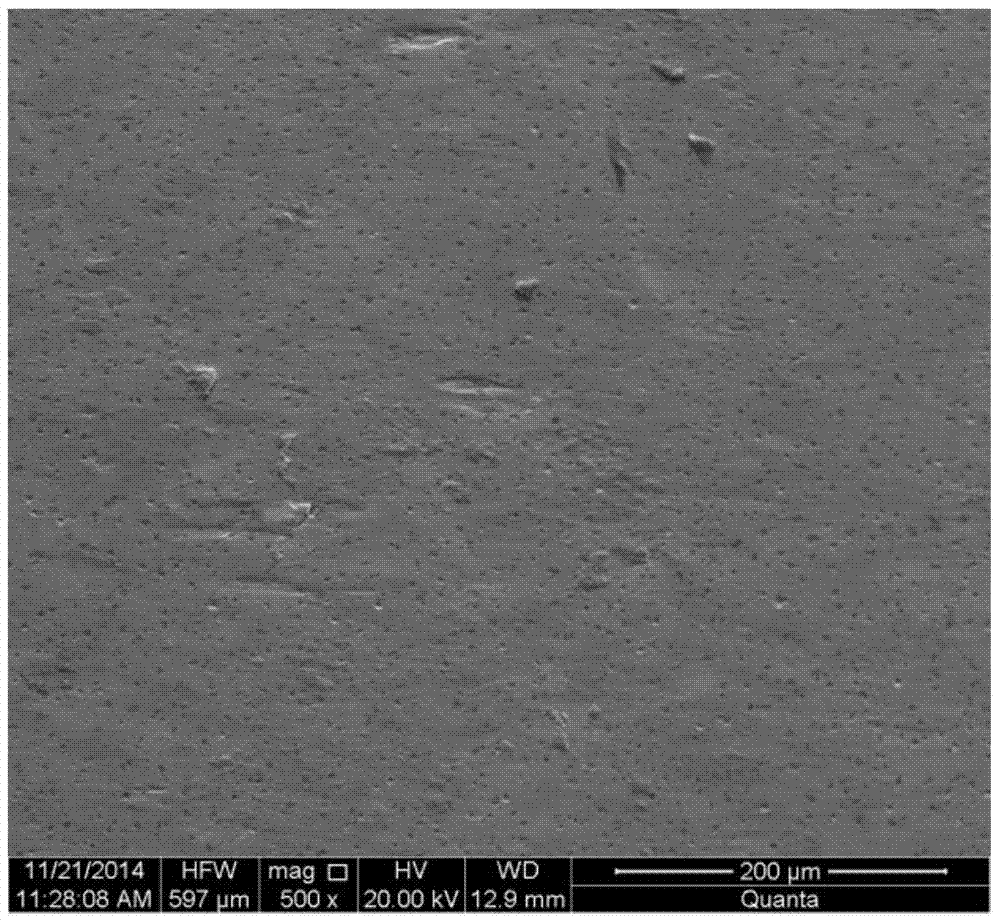
本发明涉及钢轨领域,具体地,涉及一种重载钢轨及其生产方法。
背景技术:铁路运输具有稳定、安全、廉价、高效的特点,是国民经济发展的大动脉。我国自然资源丰富,对铁路运输依赖程度高。进入21世纪以来中国铁路交通运输高速发展。2009年底全国运用铁路总里程达到86000km,中国已成为世界上拥有最长运营铁路的国家之一。预计在2020年中国运营铁路总里程将到达120000km,包括16000km客运专用铁路。我国铁路货运特点是大轴重、专一运输、地理环境复杂等,例如大秦铁路、溯黄铁路,其年运量分别达到了4.4亿吨和2.3亿吨。随着车速及轴重的增加,轮轨承受着前所未有的摩擦力,它们的磨损变得越来越严重。通过对中国部分铁路上轮轨伤损的研究发现,重载线路钢轨伤损以局部磨损为主,尤其是在小半径弯道及道岔处,占到了重载线路伤损总量的80%以上。在轨头出现严重的磨损会导致钢轨压溃,最终酿成严重的事故。所以需要铁路养护人员时刻巡视线路钢轨使用情况,出现问题需及时更换。如果重载线路钢轨耐磨性能差,那么无疑会增加铁路养护人员的劳动强度和钢轨更换的频次,大大提高了的线路运行的人工和经济成本。由于重载线路轴重较大,各国多采用75kg/m以上大断面珠光体钢轨布设线路,由于钢轨断面较大在轧制和热处理过程中容易出现淬透不足、回升温度高等因素引起的硬化层深度不够的问题,导致钢轨硬度不够且耐磨性能差,因此急需研究出一种具有优良耐磨性能的重载钢轨。
技术实现要素:本发明的目的是克服现有的重载钢轨耐磨性能不够好的问题,提供一种具有更好的硬度和更优良的耐磨性能的重载钢轨及其制备方法。本发明提供了一种重载钢轨,以该重载钢轨的总重量为基准,该重载钢轨含有0.8-1.1重量%的C、0.55-0.9重量%的Si、0.5-1重量%的Mn、0.2-0.75重量%的Cr、0.04-0.12重量%的V、≤0.01重量%的P和96.12-97.91重量%的Fe。本发明还提供了一种重载钢轨生产方法,该方法包括以下步骤:(1)转炉冶炼:将铁水预处理后进行转炉冶炼,并将转炉终点控制为:C含量大于0.15重量%,P含量小于0.012重量%,出钢温度为1600-1660℃;(2)脱氧合金化:在转炉出钢的同时进行合金化,并控制该合金化后的成分为:C含量为0.70-0.79重量%、Si含量为0.4-0.5重量%、Mn含量为0.45-0.49重量%、Cr含量为0.15-0.19重量%以及V含量为0.03-0.039重量%,并且在合金化之后向钢液中加入脱氧剂进行脱氧;(3)LF炉精炼:将脱氧合金化所得钢液在LF炉中进行精炼并控制出站钢液中各成分重量含量满足:C含量为0.8-1.1重量%,Si含量为0.55-0.9重量%,Mn含量为0.5-1重量%,Cr含量为0.2-0.75重量%以及V含量为0.04-0.12重量%;(4)RH真空处理:在RH炉中对钢液成分进行微调,使各成分的含量达到目标值。本发明的发明人在研究过程中发现,在经典的mm磨损试验机上开展载荷980N、转速200转/分、循环10万次的磨损试验时,目前铁路主要使用的钢轨磨损量都在0.4g以上,并且磨损表面都有明显挤出脊或沟槽等磨粒磨损特征。由此,本发明的发明人经过深入的研究发现,通过优化合金成分,例如在现有珠光体钢轨含碳量的基础上增加C形成过共析钢,并配合适量的Si、Mn元素及采用V、Cr复合微合金化,可以让钢轨轨头组织细化,硬度提高,淬硬层更深,从而大大提高耐磨性能。更进一步地,优选配合适当的热处理工艺,例如轧制钢轨后利用轧制余热采用不同冷却速度的多阶段热处理方式获得耐磨性能更好的显著优于现有品种的重载钢轨。本发明的其它特征和优点将在随后的具体实施方式部分予以详细说明。附图说明附图是用来提供对本发明的进一步理解,并且构成说明书的一部分,与下面的具体实施方式一起用于解释本发明,但并不构成对本发明的限制。在附图中:图1是实施例1所生产重载钢轨A进行磨损试验之后的SEM电镜照片。图2是实施例2所生产重载钢轨B进行磨损试验之后的SEM电镜照片。图3是实施例3所生产重载钢轨C进行磨损试验之后的SEM电镜照片。图4是对比例1所生产重载钢轨D进行磨损试验之后的SEM电镜照片。图5是对比例2所生产重载钢轨E进行磨损试验之后的SEM电镜照片。具体实施方式以下对本发明的具体实施方式进行详细说明。应当理解的是,此处所描述的具体实施方式仅用于说明和解释本发明,并不用于限制本发明。本发明提供了一种重载钢轨,以该重载钢轨的总重量为基准,该重载钢轨含有0.8-1.1重量%的C、0.55-0.9重量%的Si、0.5-1重量%的Mn、0.2-0.75重量%的Cr、0.04-0.12重量%的V、≤0.01重量%的P和96.12-97.91重量%的Fe。本发明的发明人经过深入的研究发现,通过优化合金成分,使钢轨的成分含量满足上述范围时,可以使钢轨轨头组织细化,硬度提高,淬硬层更深,从而大大提高耐磨性能。进一步优选地,所述重载钢轨的成分含量满足:以该重载钢轨的总重量为基准,该重载钢轨含有0.85-0.95重量%的C、0.55-0.75重量%的Si、0.75-0.85重量%的Mn、0.35-0.50重量%的Cr、0.045-0.095重量%的V、≤0.01重量%的P和96.845-97.455重量%的Fe。在本发明中,所述重载铁路钢轨的金相组织主要为珠光体组织。在本发明中,由于本发明的重载铁路钢轨具有更高的耐磨性能,因此特别适用于75kg/m及以上的大断面钢轨布设线路。本发明还提供了一种重载钢轨生产方法,该方法包括以下步骤:(1)转炉冶炼:将铁水预处理后进行转炉冶炼,并将转炉终点控制为:C含量大于0.15重量%,P含量小于0.012重量%,出钢温度为1600-1660℃;(2)脱氧合金化:在转炉出钢的同时进行合金化,并控制该合金化后的成分为:C含量为0.70-0.79重量%、Si含量为0.4-0.5重量%、Mn含量为0.45-0.49重量%、Cr含量为0.15~0.19重量%以及V含量为0.03-0.039重量%,并且在合金化之后向钢液中加入脱氧剂进行脱氧;(3)LF炉精炼:将脱氧合金化所得钢液在LF炉中进行精炼并控制出站钢液中各成分重量含量满足:C含量为0.8-1.1重量%,Si含量为0.55-0.9重量%,Mn含量为0.5-1重量%,Cr含量为0.2-0.75重量%以及V含量为0.04-0.12重量%;(4)RH真空处理:在RH炉中对钢液成分进行微调,使各成分的含量达到目标值。在步骤(1)中,在进行转炉冶炼之前需要对铁水进行预处理。所述预处理使得进入转炉冶炼的铁水最好能够满足S≤0.014重量%且As≤0.025重量%,优选地,S≤0.010重量%,As≤0.020重量%。在步骤(1)中,所述转炉冶炼使用增碳法进行,所用的增碳剂可以为无烟煤和/或沥青胶,优选为无烟煤。在步骤(1)中,所述转炉冶炼需要对终点进行特别的控制,以使得出钢的温度为1600-1660℃,优选为1640-1660℃;以钢液总重量为基准的C含量大于0.15重量%;以钢液总重量为基准的P含量小于0.012重量%,优选小于0.010重量%。在步骤(2)中,在转炉出钢的同时进行合金化,并控制该合金化后的成分满足以下要求:以钢液总重量为基准,C含量可以为0.70-0.79重量%,Si含量可以为0.4-0.5重量%,Mn含量可以为0.45-0.49重量%,Cr含量可以为0.15-0.19重量%以及V含量可以为0.03-0.039重量%。在步骤(2)中,所述合金化之后向钢液加入脱氧剂进行脱氧,以使得氧含量为0.002重量%以下。为了防止Al的引入,所述脱氧剂为无铝的脱氧剂,例如为Ba-Ca-Si合金。在步骤(3)中,将步骤(2)脱氧合金化以后的钢液在LF炉中进行精炼,向LF炉中加入发泡剂、高碱度精炼渣和碳化硅并加热25-40min。其中,相对于120吨钢液的重量,所述发泡剂的用量为150-220kg,优选为180-200kg,所述高碱度精炼渣的用量为700-800kg,以及所述碳化硅的用量为40-100kg,优选为60-80kg。所述发泡剂可以为本领域常用的各种发泡剂,例如为LFP-III型发泡剂。在步骤(3)中,可以控制LF炉的出站温度为1500-1550℃,优选为1540-1550℃。在步骤(3)中,需要在LF炉进行终点控制,使得出站时钢液中各成分重量含量达到本发明的重载钢轨成分目标含量±0.03重量%。在步骤(4)中,将步骤(3)所得钢液在RH炉中进行真空处理,真空处理的条件没有特别的限定,按照本领域常规的RH炉条件即可,例如,在真空处理前进行定氧,使得真空度≤5mbar,真空时间不得小于10min。在步骤(4)中,可以控制RH炉的出站温度为1480-1490℃。在步骤(4)中,需要对RH炉进行终点控制,即在RH炉中对钢液中的合金成分进行微调,使其达到目标值。根据本发明的方法,通过上述步骤(1)-(4)能够得到合金成分满足本发明的重载钢轨的合金成分的钢液,然后经过本领域常规的铸造和轧制工艺即可得到硬度更高、耐磨性能更好的钢轨。例如,本发明的方法还包括以下步骤:(5)连铸:将所述RH真空处理所得的钢液浇注成预定尺寸的方坯;(6)轧制:将步骤(5)所得方坯加热后轧制成钢轨;在步骤(5)中,将所述RH真空处理所得的钢液进行方坯连铸,其中中间包温度可以控制在1460-1490℃,优选控制在1470-1480℃。所述方坯的尺寸可以为280mm×280mm~450mm×450mm,这是考虑到:若钢坯尺寸小于280mm×280mm,则在后续轧制过程中压缩比过小,成品钢轨组织不够细化,影响钢轨质量;若钢坯尺寸大于450mm×450mm,则在后续轧制过程中,轧机轧制力过大,造成轧制困难,甚至出现劈头废钢。在浇注过程中可以进行全程保护和电磁搅拌,在浇注过程中应当采用轻压下。所述浇注完成以后将方坯进行静置缓冷,缓冷时间为不小于24h。在步骤(6)中,先将缓冷后的方坯进行加热,加热方式可以采用热辐射加热,加热的温度为1200-1300℃,优选为1220-1250℃,加热时间可以为0.8-1.2小时。在方坯加热后轧制前可以进行一段时间的保温,该保温的时间可以为1-1.5h。在步骤(6)中,然后将加热后的方坯进行轧制,例如使用万能轧机对加热方坯进行轧制,具体轧制道次可以根据方坯尺寸进行调整,每个轧制道次记录轧制力大小,根据现场情况调整轧制压下量,保证轧制节奏顺畅,保证断面尺寸符合要求。温度控制没有特别限定,例如,开轧温度可以为1150-1220℃,终轧温度可以为800-900℃。本发明的发明人还发现,使用本发明优化合金成分之后的重载钢轨,如果再配合轧制后热处理的过程,能够细化所述重载钢轨轨头的珠光体组织,从而使得最终所得重载钢轨的硬度和耐磨性得到进一步提高。因此,本发明的方法还包括以下步骤:(7)热处理:对轧制所得钢轨的轨头部位进行多阶段冷却热处理,且冷却速度随阶段逐渐降低。在步骤(7)中,在所述轧制步骤完成后利用轧制的余热对所得钢轨的轨头部位进行多阶段冷却热处理,优选地,进行三个阶段的冷却热处理,且冷却速度随阶段逐渐降低。第一阶段可以称为加速冷却阶段,在该阶段中,开冷温度可以为800-950℃,优选为800-850℃,更优选为80...