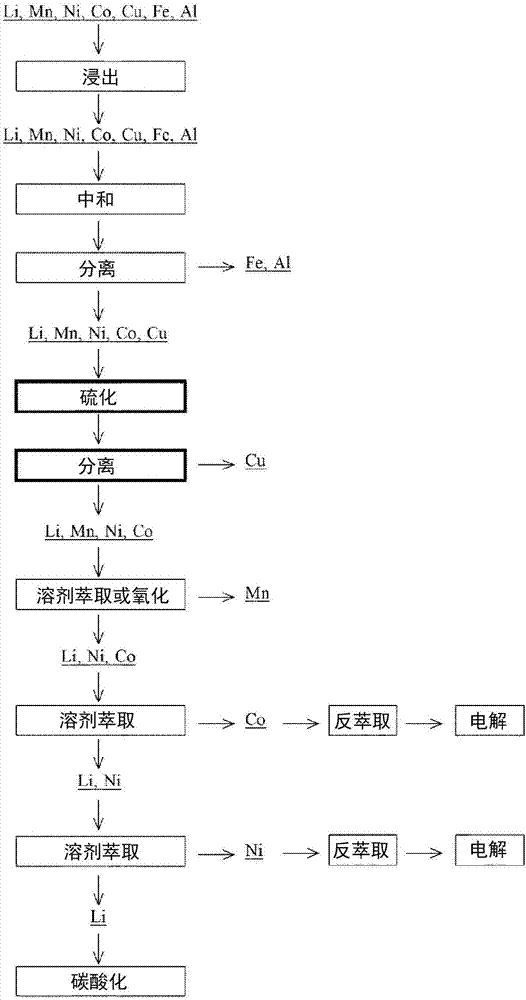
本发明涉及从含有铜的锂离子电池废料除去铜的方法以及回收金属的方法,特别提及能够有效且容易地进行锂离子电池废料中所含的铜的除去、能够有助于处理效率的提高和成本的降低的技术。
背景技术:
:在以各种电子器件为首的大多产业领域中使用的锂离子电池使用含有锰、镍和钴的锂金属盐作为正极活性物质,近年来,随着其使用量的增加和使用范围的扩大,目前的状况是因电池的制品寿命、制造过程中的不良而导致废弃的量不断增大。在该状况下,为了对上述的镍和钴等昂贵的元素进行再利用,期望从大量废弃的锂离子电池废料以较低成本容易地回收上述元素。在为了回收有用金属而对锂离子电池废料进行处理时,首先,例如将根据需要经过焙烧、破碎和筛分等各工序得到的粉状或粒状的锂离子电池废料用过氧化氢进行酸浸出,使可能包含在该废料中的锂、镍、钴、锰、铁、铜、铝等溶解于溶液中而得到浸出后液。接着,对该浸出后液实施溶剂萃取法,分离各金属元素。在此,为了使浸出至浸出后液的各金属分离,对浸出后液依次实施与所分离的金属对应的多个阶段的溶剂萃取或中和等,再对各阶段中所得的各溶液实施反萃取、电解、碳酸化等处理。具体而言,首先,回收铁和铝,接下来回收锰和铜,然后回收钴,之后回收镍,最后在水相中残留锂,由此可以回收各有用金属。技术实现要素:发明要解决的课题如上述所示,为了从浸出锂离子电池废料而得到的浸出后液分离回收各金属,需要进行多种处理。因此,若可以从浸出后液中所含的金属中预先以固体形式分离除去特定的金属,则在之后的回收工序中可以简化或省略为了分离回收各金属而对浸出后液实施的多种处理中已被除去的金属的回收所需的处理,因此从处理的效率和成本的观点出发是有效的。并且,特别是在浸出后液中以高浓度包含铜离子时,例如在以溶剂萃取钴并进行反萃取后的电解工序中有时会导致发生电沉积异常,因此需要使浸出后液中的铜离子浓度充分低。本发明是以解决这种问题为课题的发明,其目的在于提供能够有效且容易地进行锂离子电池废料中所含的铜的除去、并且能够有助于处理效率的提高和成本的降低的从锂离子电池废料除去铜的方法和回收金属的方法。用于解决课题的手段发明人进行深入研究的结果发现:在将锂离子电池废料进行酸浸出时,若在添加了包含铜的锂离子电池废料的酸性溶液中包含铝的固体,则在酸性溶液中存在铝的固体的状况下,可以将铜的浸出率维持为极小。而且认为:通过利用这种特性,从而可以在直至浸出工序结束为止的期间抑制铜的溶解或使溶解的铜析出,之后以固体形式容易地分离/除去铜。在这种见解下,本发明的从锂离子电池废料除去铜的方法为从含有铜的锂离子电池废料除去铜的方法,包括:浸出工序,将上述锂离子电池废料添加到酸性溶液中,在酸性溶液中存在铝的固体的状况下,使该锂离子电池废料浸出;和铜分离工序,在浸出工序后从酸性溶液分离以固体形式包含于该酸性溶液中的铜。在此,在上述浸出工序中,上述铝的固体优选为锂离子电池废料中所含的铝粉末。而且,在此,在上述浸出工序中,优选在铜开始溶解之前将上述铝的固体添加到酸性溶液中。在本发明的铜的除去方法中,在酸性溶液中的铝的固体全部溶解且锂离子电池废料中所含的铜开始溶解之前结束上述浸出工序是合适的。另外,上述锂离子电池废料可以含有镍和/或钴。此时,优选:在上述浸出工序中,将存在于酸性溶液中的上述铝的固体的量设为在上述锂离子电池废料中的镍和/或钴全部溶解后铝仍以固体形式残留的量。另外,此时优选:在上述浸出工序中,使上述锂离子电池废料中的镍和/或钴溶解时的酸性溶液的ph为0~2.0,在上述铜分离工序中,使从酸性溶液分离铜的固体时的酸性溶液的ph为2.0~3.0。本发明的从锂离子电池废料回收金属的方法为使用上述任一种从锂离子电池废料除去铜的方法来回收锂离子电池废料中所含的金属的方法,包括:回收工序,在铜分离工序后从使锂离子电池废料浸出而得的浸出后液回收其所含的金属。发明效果根据本发明,在酸性溶液中存在铝的固体的状况下使锂离子电池废料浸出,由此在浸出工序中可以将铜的浸出率抑制得充分小,因此在之后的铜分离工序中可以有效且容易地分离除去以固体形式包含于酸性溶液中的铜。其结果是可以有助于之后的工序等中的处理效率的提高和成本的降低。附图说明图1为表示本发明的金属的回收方法的一个实施方式的流程图。图2为表示以往的回收方法的流程图。图3为表示本发明的金属的回收方法的另一实施方式的流程图。图4为表示以往的其他回收方法的流程图。图5为分别表示实施例1的ph和orp的变化、以及各金属成分的浓度变化的图表。图6为分别表示实施例2的ph和orp的变化、以及各金属成分的浓度变化的图表。图7为分别表示比较例1的ph和orp的变化、以及各金属成分的浓度变化的图表。图8为分别表示比较例2的ph和orp的变化、以及各金属成分的浓度变化的图表。图9为分别表示比较例3的ph和orp的变化、以及金属成分的浓度变化的图表。具体实施方式以下,详细说明本发明的实施方式。本发明的一个实施方式的从锂离子电池废料除去铜的方法为从含有铜的锂离子电池废料除去铜的方法,包括:浸出工序,将上述锂离子电池废料添加到酸性溶液中,在酸性溶液中存在铝的固体的状况下使该锂离子电池废料浸出;和铜分离工序,在浸出工序后从酸性溶液分离以固体形式包含于该酸性溶液中的铜。(锂离子电池废料)锂离子电池废料可以以如下物质为对象:因电池制品的寿命、制造不良或其他理由而废弃的所谓电池渣、带铝箔的正极材料或正极活性物质、或者它们中的至少一种;或者例如将电池渣等根据需要进行焙烧、化学处理、破碎和/或筛分后的物质等。但是,根据锂离子电池废料的种类等的不同,未必需要这种焙烧、化学处理、破碎、筛分。需要说明的是,在此,例如在锂离子电池废料为电池渣的情况下,在该锂离子电池废料中通常除包含由构成正极活性物质的锂、镍、钴、锰中的一种元素形成的单独金属氧化物和/或由两种以上元素形成的复合金属氧化物外,还会包含铝、铜、铁等。或者,在锂离子电池废料为正极活性物质的情况下,该废料中通常可以包含上述的单独金属氧化物和/或复合金属氧化物。另外,在锂离子电池废料为带铝箔的正极材料的情况下,有时除该单独金属氧化物和/或复合金属氧化物外还包含铝。在本发明的铜的除去方法中作为对象的锂离子电池废料只要是至少包含铜的锂离子电池废料即可。在实施后述的回收工序的情况下,锂离子电池废料优选还包含作为有用金属的钴和/或镍,更优选还包含钴和镍。(浸出工序)在浸出工序中,将上述的锂离子电池废料添加到硫酸等酸性溶液并使其浸出。在此,通过使锂离子电池废料最初包含铝的固体,或者在酸性溶液中另行添加铝的固体,从而在酸性溶液中存在铝的固体的状况下使锂离子电池废料浸出。据此,在酸性溶液中从存在铝的固体时起,便有效地抑制铜的浸出率的增加。认为这是由于:铝是比铜更低腐蚀电位的金属(卑な金属)、即铝比铜标准氧化还原电位小,因此与锂离子电池废料中所含的铜相比,铝的溶解反应先行进行,并且已经溶解于酸性溶液中的铜析出。但是并不限定于这种理论。需要说明的是,可以在浸出工序的开始到结束的整个期间在酸性溶液中存在铝的固体,但是,只要在至少浸出工序的某个时期在酸性溶液中存在铝的固体即可。在存在铝的固体的期间,铜的溶解被抑制。在该浸出工序中,可以存在于酸性溶液中的铝的固体为锂离子电池废料中最初所含有的铝粉末的方式,在酸性溶液中仅添加包含铝粉末的锂离子电池废料,也可以除锂离子电池废料之外另行将铝的固体也添加到酸性溶液中。在除锂离子电池废料之外另行将铝的固体添加于酸性溶液中的情况下,该铝的固体优选为在其他的锂离子电池废料的处理中所得的铝粉末。这是因为:在从废弃等的锂离子电池废料回收镍、钴等有用金属的情况下,有时从附着有正极材料的正极活性物质的铝箔剥离包含有用金属的正极活性物质,此时,产生大量的铝粉末,因此期望有效地活用这种铝粉末。需要说明的是,在从锂离子电池废料得到添加于酸性溶液的铝粉末时,例如根据需要对锂离子电池废料的正极材料进行裁切,接着,使用单轴剪切式破碎机等破碎机,将正极材料破碎至小于规定大小为止。通过这种使正极材料成为粒状的过程,可以从正极活性物质中以铝粉末形式分离作为正极材料的集电体的铝箔的至少一部分。之后,再将该破碎物用规定大小的筛进行筛分,在筛上侧残留铝粉末,使正极活性物质转移至筛下侧。由此可以得到铝粉末。另外,在该浸出工序中,在酸性溶液中添加铝的固体而使其存在的情况下,优选在酸性溶液中的锂离子电池废料中所含的铜开始溶解之前将铝的固体添加到酸性溶液中。由此,可以不使更多的铜溶解而将其在后述的铜除去工序中以固体形式进行分离。而且,若铝的固体全部溶解,则之后铜开始溶解,因此在更有效地抑制铜的溶解的方面,在酸性溶液中的铝的固体全部溶解且锂离子电池废料中所含的铜开始溶解之前结束该浸出工序是合适的。在锂离子电池废料中包含钴、镍且在后续的回收工序中回收这些金属的情况下,可以根据钴、镍的浸出率和铝的浸出率来结束浸出工序。即,从提高钴等的回收率的观点出发,优选尽可能地使铜不溶解,而另一方面使钴、镍充分溶解。因此,在锂离子电池废料含有钴和/或镍的情况下,有效的是:按照在酸性溶液中的锂离子电池废料所含的钴和/或镍全部溶解后铝仍以固体形式残留的程度的量,使铝的固体存在于酸性溶液中。这种情况下,钴和/或镍完全溶解,但是此时铝的固体残留,从而使更多的铜以固体形式存在于酸性溶液中,可以容易地将其除去。在这种浸出工序中,以使钴和/或镍与铝的固体一起溶解但不使铜溶解的方式使酸性溶液的ph逐渐上升。具体而言,使钴和/或镍溶解时的酸性溶液的ph可以为0~2.0。这是因为:若此时的ph过大,则存在钴和镍的浸出速度不充分的可能性,另一方面,若ph过小,则浸出急速进行,导致铜浸出,另外,在后续工序中需要提升ph时,为了调整ph而存在成本增加的可能性。另外,在浸出工序中,从将锂离子电池废料添加到酸性溶液时起到浸出结束为止的浸出时间优选设为0.5小时~10小时。这是因为:若反应时间过短,则有时期望溶解的钴、镍没有充分地溶解。另一方面,若浸出时间过长,则存在铝的固体的溶解结束且铜开始溶解的风险。浸出时间的更优选的范围为1小时~5小时、进一步优选为1小时~3小时。(铜分离工序)上述的浸出工序后,除铜以外的金属特别是钴、镍基本溶解,对于铜以固体形式残留的酸性溶液,可以在铜分离工序中利用固液分离等公知的方法分离浸出残渣和浸出后液。在浸出工序中铝的固体存在于酸性溶液中,由此铜以固体形式残留、析出至酸性溶液中,由此在该铜分离工序得到的浸出残渣中包含大量铜的固体,另一方面,在浸出后液中几乎不包含铜。在此,使铜的固体分离时的酸性溶液的ph可以设为2.0~3.0。即,若铜分离工序中的酸性溶液的ph过大,则产生氢氧化物沉淀,金属成分的分离性变差。另外,后续工序中的ph调节成本增大。若ph过小,则存在进行铝浸出的风险。(金属的回收方法)在利用如以上所述的铜的除去方法浸出锂离子电池废料而得的铜除去后的浸出后液中镍、钴等有用金属溶解并存在的情况下,为了从该浸出后液回收有用金属,可以实施金属的回收方法。在该回收方法中,对如上述那样得到的浸出后液,例如使用通常的溶剂萃取或中和等来回收包含溶解于其中的有用金属的各金属。在该回收方法的一个实施方式中,如图1所例示那样,例如对包含锂、锰、镍、钴、铜、铁和铝的锂离子电池废料进行如上述所示的浸出工序和铜分离工序。分离铜而得的浸出后液是铜被除去从而几乎不含铜的液体。接着,对浸出后液实施用于除去铁和铝的中和/分离。之后,从由此得到的溶液中利用溶剂萃取或氧化来除去锰,然后利用基于与各金属对应的萃取剂的溶剂萃取来依次回收钴和镍,之后在水相中残留锂。溶剂中的钴可以通过反萃取而移动至水相,并通过电解沉积(電解探取)来回收。另外,溶剂中的镍也同样可以通过反萃取和电解沉积来回收。锂可以以被碳酸化成碳酸锂的形式来回收。根据图1所示的实施方式,在浸出后液中不包含铜,因此不需要在图2所示的以往的方法中为了在除去铁和铝后除去铜而进行的硫化/分离,可以大大提高用于回收这种有用金属的锂离子电池废料的处理工艺的处理效率,并且可以有效地降低进行硫化/分离所需的成本。另外,若因回收钴时的电解而使溶液中大量含有铜,则导致电沉积异常,因此需要直至此时为止而使铜离子浓度降低至例如0.5mg/l以下左右的规定的低值。在该实施方式中,可以利用在先的铜分离工序充分地除去铜,因此可以可靠地防止这种电沉积异常的发生。图3中示出本发明的金属的回收方法的另一实施方式。在图3所示的实施方式中,使锂离子电池废料浸出而得到浸出后液的情况与图1所示的实施方式相同,但是从浸出后液通过溶剂萃取除去铁和铝的一部分,之后,再进行溶剂萃取,除去锰和残留的铝。之后残留于溶液中的锂、镍和钴的回收与图1所示的实施方式相同。在该实施方式中,与图4所示的以往的方法相比可知:能够减轻溶剂萃取锰时的铜除去的负荷。实施例接下来,试验性地实施本发明的方法,并确认其效果,在以下进行说明。但是,在此的说明的目的仅在于例示,其意图并不在于限定本发明。按照表1所示的量准备包含各金属的电池粉和正极活性物质(lco)。[表1](实施例1)在实施例1中,在300ml的纯水中添加30g上述的电池粉,并且添加使金属成分全部浸出所需量的1倍的硫酸,在液温60℃、搅拌速度250rpm下,使各金属成分浸出,随着时间的推移,对ph、orp的变化以及钴、铝和铜的浓度变化进行了调查。在此,金属成分浸出率通过与将相同样品利用王水完全溶出金属成分的情况相比较来进行计算。其结果如表2和图5所示。由表2和图5所示可知:铝的浸出率从浸出开始时起增加,另一方面,铜的浸出率大致维持在零的状态。另外,钴较多地浸出。[表2](实施例2)在实施例2中,在300ml的纯水中添加上述的正极活性物质,并且添加使金属成分全部浸出所需量的1倍的硫酸,再添加铜箔和铝箔的粉末,与实施例1同样地操作,使各金属成分浸出,随着时间的推移,对ph、orp的变化以及钴、铝和铜的浓度变化进行了调查。其结果如表3和图6所示。在此,正极活性物质的添加量为17.35g,以使所添加的正极活性物质中的钴的量与30g电池粉中的钴的量相等。另外,所添加的铜箔和铝箔的各自的添加量为铜箔1.5g、铝箔2.37g,以使与30g电池粉中的铜和铝的各自的量相等。由表3和图6所示的结果可知:从浸出开始时起铝和钴的浸出率增加,另一方面,铜的浸出率维持在低水平,然而铝大部分浸出后,铜的浸出率也增加。另外,直至铝大部分浸出为止,钴的浸出率维持在高水平。[表3]反应时间(h)cocual0.545%2%8%154%2%20%272%0%43%3.584%1%67%5103%3%94%699%3%92%995%5%94%2486%15%82%(比较例1)在比较例1中,不添加铝箔而添加铜箔,除此以外,与实施例2同样地进行试验,随着时间的推移,对ph、orp的变化以及钴和铜的浓度变化进行了调查。其结果如表4和图7所示。由表4和图7所示的结果可知:由于未添加铝箔,从而从浸出开始时起铜的浸出率增大,由此大量的铜浸出,此外,钴没有浸出太多。[表4]反应时间(h)cocu0.573%39%183%46%289%54%3.588%55%589%60%686%59%979%62%2479%71%(比较例2)在比较例2中,不添加铜箔而添加铝箔,除此以外,与实施例2同样地进行试验,随着时间的推移,对ph、orp的变化以及钴和铝的浓度变化进行了调查。其结果如表5和图8所示。在表5和图8所示的结果中,铝的浸出率提高,但是钴的浸出率并不太增加。[表5]反应时间(h)coal0.536%6%144%16%250%42%354%61%666%97%1270%102%2454%81%(比较例3)在比较例3中,铜箔和铝箔均未添加,除此以外,与实施例2同样地进行试验,随着时间的推移,对ph、orp的变化以及钴的浓度变化进行了调查。其结果如表6和图9所示。此时,钴的浸出率在整个反应时间内维持在低水平。[表6]反应时间(h)co0.539%137%236%333%634%1234%2427%由以上的试验可知:根据本发明的方法,在酸性溶液中存在铝的固体的状况下,使包含铜的锂离子电池废料浸出,由此将铜的浸出率抑制得充分小,可以从酸性溶液有效地分离除去铜。当前第1页12