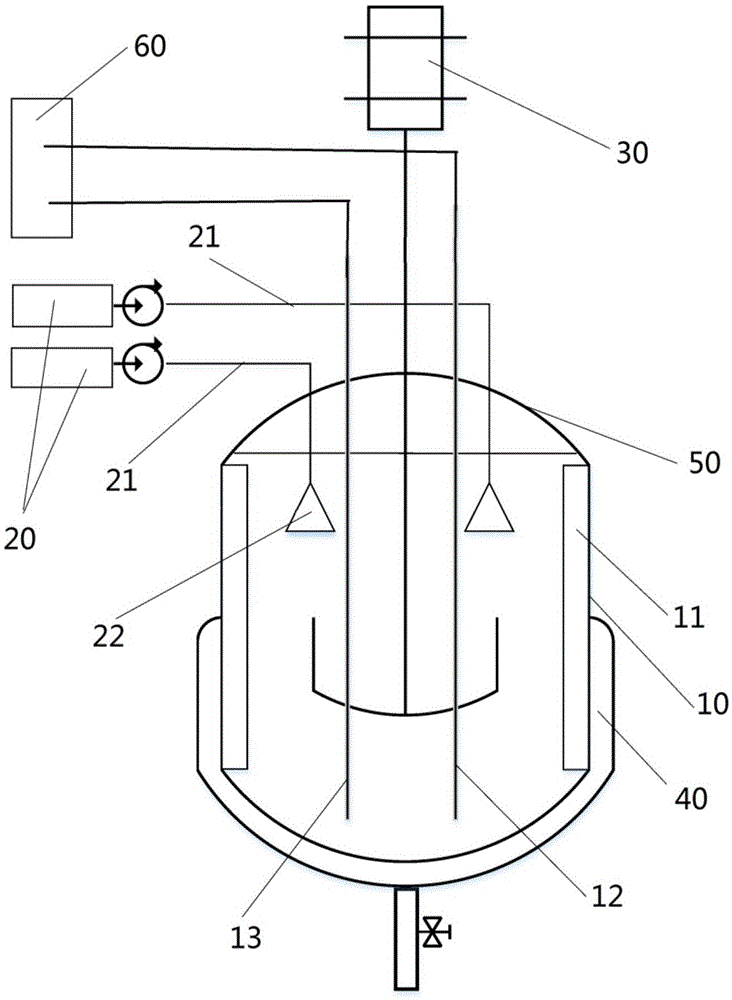
本发明涉及稀土生产领域,具体而言,涉及一种稀土沉淀装置。
背景技术:
:稀土矿经过浸出和萃取步骤生产过程后期,还需将稀土料液进行沉淀净化。沉淀工艺中有正序加料、共同加料和反序加料。不同加料方式对沉淀物的晶型、晶体大小、分布都有影响。正序加料中将稀土沉淀剂加入到稀土料液或反序加料将稀土料液加入到稀土沉淀剂中都会由于局部某反应物浓度过高而影响稀土沉淀晶体沉淀质量,进而影响后续过滤和洗涤步骤的进行。比如,目前存在的稀土沉淀装置中,大多数都将沉淀剂向稀土草酸盐或氯化盐等稀土料液中通过加入或滴入,导致溶液初期不能混匀问题;而且稀土草酸盐或氯化盐在沉淀过程中,由于原料和沉淀剂混合不均会导致局部区域的ph或料浓度过小或过大,致使稀土沉淀雏晶颗粒大小不一;现有的共同加料方式中稀土料液与沉淀剂的接触面同样较小。另外,稀土沉淀过程通常是放热反应,沉淀过程中的热量积聚导致温度上升在一方面会极大影响稀土沉淀结晶的形状和生长速率,致使稀土结晶沉淀最终产品质量不够稳定。技术实现要素:本发明的主要目的在于提供一种稀土沉淀装置,以解决现有技术中的稀土沉淀装置得到的稀土结晶质量不稳定的问题。为了实现上述目的,根据本发明的一个方面,提供了一种稀土沉淀装置,包括:沉淀容器,具有本体和本体围成的容纳腔;供料器,向的沉淀容器的容纳腔提供稀土料液和沉淀剂;搅拌器,具有搅拌桨,搅拌桨设置在容纳腔中;以及温度控制器,与沉淀容器相连,控制沉淀容器内物料的温度。进一步地,上述温度控制器为控温夹套,控温夹套套设在本体的外表面。进一步地,上述供料器包括相互独立设置的:稀土料液供料器,向沉淀容器的容纳腔提供稀土料液;沉淀剂供料器,向沉淀容器的容纳腔提供沉淀剂。进一步地,上述稀土料液供料器和沉淀剂供料器各自独立地包括:供料管;喷淋头,与供料管相连,喷淋头的喷嘴朝向容纳腔设置。进一步地,上述喷淋头与容纳腔底部的距离为容纳腔深度的2/3以上。进一步地,上述稀土沉淀装置还包括气体收集器,气体收集器为溢流罩或空气冷凝罩,气体收集器设置在本体的顶部将容纳腔密封。进一步地,上述沉淀容器内还设置有挡板,挡板设置在本体的内壁上,优选挡板靠近喷淋头所在位置设置。进一步地,上述挡板为可拆卸的矩形挡板,且挡板的顶端所在位置高于喷淋头所在位置,底端所在位置低于容纳腔的1/3深度。进一步地,上述稀土沉淀装置还包括自动控制设备,温度控制器与自动控制设备电连接,沉淀容器还设置有:热电偶,热电偶用于检测沉淀容器内物料的温度,热电偶与自动控制设备电连接,自动控制设备接收热电偶检测的温度并根据温度向温度控制器发送指令来对沉淀容器内物料的温度进行调节。进一步地,上述沉淀容器还设置有:ph计,ph计用于检测沉淀容器内物料的ph值,ph计与自动控制设备电连接,自动控制设备接收ph计检测的ph值并根据ph值向供料器发送指令调整供料速度来对沉淀容器内物料的ph值进行调节。应用本发明的技术方案,利用该温度控制器控制沉淀容器内物料的温度,使得稀土沉淀过程放热反应导致的温度变化得到补偿,同时在容纳腔中设置搅拌桨使得稀土料液和沉淀剂的接触更均匀,且促进了放热反应产生的热量的向外传递,从而温度控制器能够更准确、及时地对沉淀容器内物料的温度进行调整,进而能够控制稀土沉淀反应在温度稳定的条件下进行,避免了放热反应的热量积聚导致温度上升进而导致稀土结晶质量不稳定的问题出现。附图说明构成本申请的一部分的说明书附图用来提供对本发明的进一步理解,本发明的示意性实施例及其说明用于解释本发明,并不构成对本发明的不当限定。在附图中:图1示出了根据本发明的一种实施方式提供的稀土沉淀装置的结构示意图;以及图2示出了根据本发明实施例3以及对比例1的沉淀样品的x射线衍射谱图。其中,上述附图包括以下附图标记:10、沉淀容器;11、挡板;12、热电偶;13、ph计;20、供料器;21、供料管;22、喷淋头;30、搅拌器;40、温度控制器;50、气体收集器;60、自动控制设备。具体实施方式需要说明的是,在不冲突的情况下,本申请中的实施例及实施例中的特征可以相互组合。下面将参考附图并结合实施例来详细说明本发明。如本申请
背景技术:
所分析的,利用现有技术的稀土沉淀装置进行稀土沉淀时,由于稀土沉淀过程通常是放热反应,沉淀过程中的热量积聚导致温度上升在一方面会极大影响稀土沉淀结晶的形状和生长速率,致使稀土结晶沉淀最终产品质量不够稳定。为了解决该问题,本申请提供了一种稀土沉淀装置。如图1所示,该稀土沉淀装置包括沉淀容器10、供料器20、搅拌器30和温度控制器40,沉淀容器10具有本体和本体围成的容纳腔;供料器20向的沉淀容器10的容纳腔提供稀土料液和沉淀剂;搅拌器30具有搅拌桨,搅拌桨设置在容纳腔中;温度控制器40与沉淀容器10相连,控制沉淀容器10内物料的温度。本申请的稀土沉淀装置设置有温度控制器40,利用该温度控制器40控制沉淀容器10内物料的温度,使得稀土沉淀过程放热反应导致的温度变化得到补偿,同时在容纳腔中设置搅拌桨使得稀土料液和沉淀剂的接触更均匀,且促进了放热反应产生的热量的向外传递,从而温度控制器40能够更准确、及时地对沉淀容器10内物料的温度进行调整,进而能够控制稀土沉淀反应在温度稳定的条件下进行,避免了放热反应的热量积聚导致温度上升进而导致稀土结晶质量不稳定的问题出现。上述温度控制器40的可以为多种形式,比如盘管式换热器,优选上述温度控制器40为控温夹套,控温夹套套设在本体的外表面。将温度控制器40设置为控温夹套,从而能够以包裹的形式设置在本体的外表面,从而实现对整个沉淀容器10内物料温度的调整。在一种实施例中,如图1所示,上述供料器20包括相互独立设置的稀土料液供料器和沉淀剂供料器,稀土料液供料器向沉淀容器10的容纳腔提供稀土料液;沉淀剂供料器向沉淀容器10的容纳腔提供沉淀剂。上述供料器20的具体形式可以为供料管21,进料管的末端可以设置在容纳腔的上部或下部,具体设置可以参考现有技术。通过控制稀土料液供料器和沉淀剂供料器各自的供料速度,来调节沉淀容器中物料的ph值,进而进行高效率沉淀。为了增加稀土料液和沉淀剂的混合均匀性,优选如图1所示,上述稀土料液供料器和沉淀剂供料器各自独立地包括供料管21和喷淋头22,喷淋头22与供料管21相连,喷淋头22的喷嘴朝向容纳腔设置。利用喷淋头22以喷淋的方式将稀土料液和沉淀剂喷入容纳腔中,使得二者的接触面积增大,因此改善了二者的混合均匀性,进而避免了混合不均匀导致的局部区域ph值或物料浓度过大或过小导致的稀土沉淀雏晶颗粒大小不一的问题出现。为了增加喷淋头22的分散效果,优选上述喷淋头22与容纳腔底部的距离为容纳腔深度的2/3以上。上述距离的设置使得喷淋液有足够的距离实现分散,进而进一步优化了物料的混合均匀性。在本申请一种实施例中,如图1所示,上述稀土沉淀装置还包括气体收集器50,气体收集器50为溢流罩或空气冷凝罩,气体收集器50设置在本体的顶部将容纳腔密封。由于在稀土沉淀过程中,随着反应的进行部分氨气、水蒸汽会从容纳腔中逸出,导致环境污染以及工作环境恶化,上述气体收集器50的设置能够将氨气、水蒸汽进行收集,避免了上述问题的产生。另外,为了避免喷淋液对沉淀容器10本体的物理损伤,优选如图1所示,上述沉淀容器10内还设置有挡板11,挡板11设置在本体的内壁上,优选挡板11靠近喷淋头22所在位置设置。利用挡板11对喷淋头22喷出的物料进行承接阻挡其直接溅射至本体内壁上,进而避免了其对本体内壁的物理损伤,延长了本体的使用寿命。优选地,上述挡板11为可拆卸的矩形挡板11,且挡板11的顶端所在位置高于喷淋头22所在位置,底端所在位置低于容纳腔的1/3深度。以保证容纳腔足够的反应容积且利用挡板11对本体实现足够的保护作用。在本申请另一种实施例中,如图1所示,上述稀土沉淀装置还包括自动控制设备60,温度控制器40与自动控制设备60电连接,沉淀容器10还设置有热电偶12,热电偶12用于检测沉淀容器10内物料的温度,热电偶12与自动控制设备60电连接,自动控制设备60接收热电偶12检测的温度并根据温度向温度控制器40发送指令来对沉淀容器10内物料的温度进行调节。通过设置自动控制设备60和热电偶12,并且利用自动控制设备60接收热电偶12检测的温度并根据温度向温度控制器40发送指令来对沉淀容器10内物料的温度进行调节,实现了对温度的实时、自动监控,提高了稀土沉淀装置工作自动化程度和可控性。进一步地,优选如图1所示,上述沉淀容器10还设置有ph计13,ph计13用于检测沉淀容器10内物料的ph值,ph计13与自动控制设备60电连接,自动控制设备60接收ph计13检测的ph值并根据ph值向供料器20发送指令来对沉淀容器10内物料的ph值进行调节。自动控制设备60接收ph计13检测的ph值并根据ph值向供料器20发送指令调整供料速度来对沉淀容器10内物料的ph值进行调节。以下将结合实施例和对比例进行说明本申请的有益效果。实施例1采用图1所示的稀土沉淀装置进行如下过程。将稀土溶液(具体成分如表1所示)与稀土沉淀剂(浓度为12~14wt%的氨水)分别通过进料器按10ml/min和9ml/min的速率打入到沉淀槽中(其中上述速率在满足ph值前提下进行调整),沉淀温度设定在50℃,并且利用温度控制器进行温度的实时调节;经沉淀完成后,继续保温30min。沉淀过程中沉淀槽利用空气冷凝罩密闭。沉淀过程中物料的ph值由ph计进行监测,并控制ph值在7~8之间,沉淀过程通过电机驱动搅拌桨转动,转速为20~300rpm。利用xrf分析的沉淀样品化学组成如表2结果所示。表3为采用激光粒度分析仪对样品的粒度的分析结果。实验结果表明在50℃密闭条件下沉淀,所得样品的沉淀粒径中位径(d50)较大。表1(ppm)reesalfecucocrmgmnniti17035.0100.040.0100.045.0840.0150.090.025.0110.0表2(wt%)oreesscrcafealthsi其他42.50642.02612.5882.0200.3450.1670.0850.0580.0510.154表3实施例2将稀土溶液(具体成分如表1所示)与稀土沉淀剂(浓度为12~14wt%的铵水溶液)分别通过进料器按10ml/min和9ml/min的速率打入到沉淀槽中(其中上述速率在满足ph值前提下进行调整),沉淀温度设定在90℃,并且利用温度控制器进行温度的实时调节沉淀;经沉淀完成后,继续保温30min。沉淀过程中沉淀槽利用空气冷凝罩密闭。沉淀过程中物料的ph值由ph计进行监测,并控制ph值在7~8之间,沉淀过程通过电机驱动搅拌桨转动,转速为20~300rpm。利用xrf分析的沉淀样品化学组成如表4结果所示。样品粒度分析方法同上,其测试结果如表5及其粒径累积分布图所示。测试结果表明,在密闭环境90℃下沉淀的样品中,中位径为8.079μm,样品粒径偏小。表4(%)表5实施例3与实施例1不同之处在于沉淀温度设定在60℃。稀土沉淀剂为浓度为0.25~0.35mol/l的草酸。利用xrf分析的沉淀样品化学组成如表7结果所示。粒度分析方法同上,粒径分布信息如表6所示。表6对比例1与实施例3的不同之处在于,沉淀过程没有密闭。利用xrf分析的沉淀样品化学组成如表7结果所示。由表7数据对比可以看出,非密闭样品中杂质元素含量较密闭样品中杂质元素含量高,其原因可能是非密闭样品粒径生长较快物理包裹了溶液中的较多杂质物质。粒度分析方法同上,粒径分布信息如表8所示。由表6和表8的数据对比可以发现,实施例3密封条件下得到的样品相比对比例1非密闭沉淀所得样品粒径相对较小。表7(%)表8中位径(d50):16.06μm体积平均径:29.47μm面积平均径:4.027μm遮光率:13.16%跨度:4.738长度平均径:0.918μm比表面积:551.7m2/kg拟合残差:0.346%对比例2与实施例1不同之处在于,将喷淋头替换为管路,且管路延伸至容纳强深度的1/2处。利用xrf分析的沉淀样品化学组成如表9结果所示。采用管路延伸至容纳强深度的1/2处沉淀样品中杂质元素含量较实施例1中杂质元素高。表9(wt%)oreesscrcafealthsi其他40.50141.23414.2352.3710.3380.1280.1080.0550.062余量另外,采用x射线衍射仪对实施例3和对比例1的沉淀样品的结构进行检测,检测结果见图2。对比例3与实施例的区别在于,没有设置温度控制器,因此实际温度随着反应的进行增大,最高温度可达62℃。由于其温度波动导致样品粒径特征中的跨度值较实施例1大,样品粒度均一性较差。利用xrf分析的沉淀样品化学组成如表10结果所示。表11为采用激光粒度分析仪对样品的粒度的分析结果。表10(wt%)oreesscrcafealthsi其他42.57241.67612.0842.540.2420.2860.0840.0920.042余量表11上述实验结果表明,进料方式以及沉淀槽打开和密闭对实验样品成分不仅有影响,而且对实验沉淀结晶的形态也产生了影响,其中沉淀槽密闭的实验样品晶化率较沉淀槽打开的实验样品低。这是因为密闭操作时,便于控制反应空间内的压强,如增大或减小。在本实验中,通过增加反应空间内的压强,首先在一定程度上增强了沉淀反应正向进行,促进了雏晶的形成,但同时却减慢了沉淀晶体生长速度,使沉淀样品粒径相对较小、晶化率较低,沉淀样品中杂质包含较少;其次,密闭操作不仅可改善操作环境,同时可提高稀土沉淀剂如草酸、碳酸沉淀剂的使用效率;最后,密闭操作中可增强搅拌强度,稀土料液与沉淀剂混合接触时间更短,液相ph分布均匀,促使晶体粒径生长更加均一。从以上的描述中,可以看出,本发明上述的实施例实现了如下技术效果:本申请的稀土沉淀装置设置有温度控制器,利用该温度控制器控制沉淀容器内物料的温度,使得稀土沉淀过程放热反应导致的温度变化得到补偿,同时在容纳腔中设置搅拌桨使得稀土料液和沉淀剂的接触更均匀,且促进了放热反应产生的热量的向外传递,从而温度控制器能够更准确、及时地对沉淀容器内物料的温度进行调整,进而能够控制稀土沉淀反应在温度稳定的条件下进行,避免了放热反应的热量积聚导致温度上升进而导致稀土结晶质量不稳定的问题出现。以上所述仅为本发明的优选实施例而已,并不用于限制本发明,对于本领域的技术人员来说,本发明可以有各种更改和变化。凡在本发明的精神和原则之内,所作的任何修改、等同替换、改进等,均应包含在本发明的保护范围之内。当前第1页12