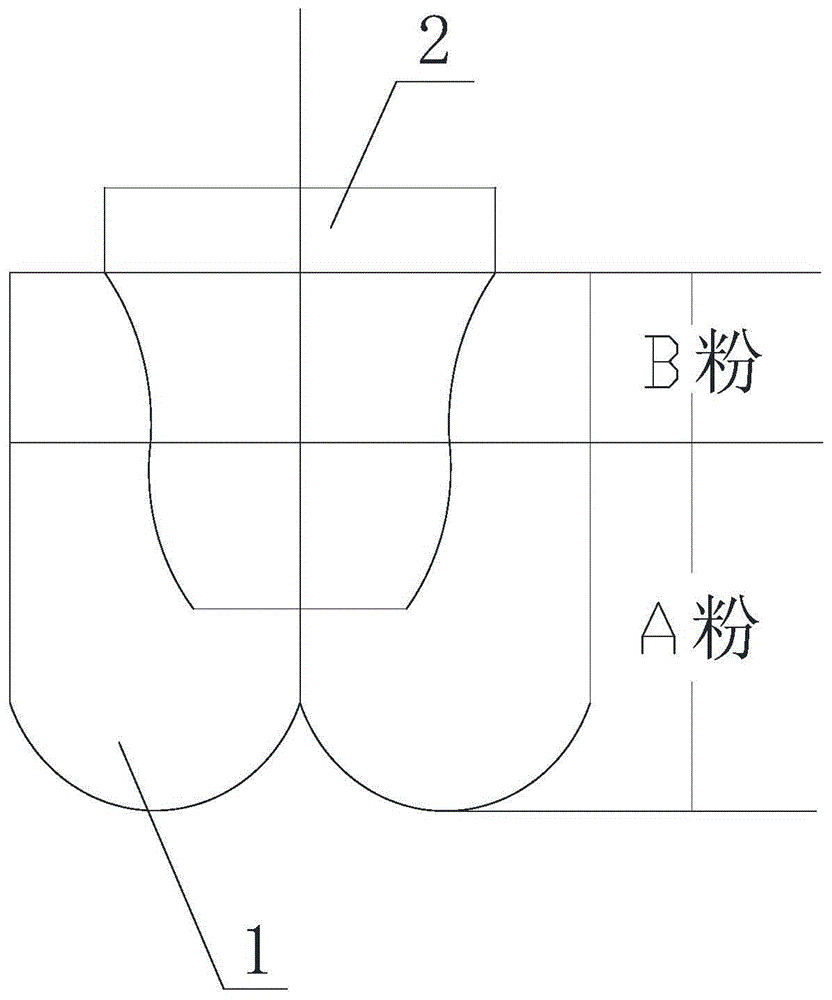
本发明型涉及油气钻头
技术领域:
,具体涉及一种pdc胎体钻头粉料配方。
背景技术:
:pdc钻头是聚晶金刚石复合片钻头的简称。是地质钻探行业常用的一种钻井工具。分为胎体式pdc钻头和钢体式pdc钻头,胎体式pdc钻头是将金刚石复合片通过钎焊方式焊接在钻头胎体上的一种切削型钻头。钻头胎体用碳化钨粉末烧结而成,用人造聚晶金刚石复合片钎焊在碳化钨胎体上,用天然金刚石保径;钢体pdc钻头,是用镍、铬、钼合金钢调质处理及起样后,按三维的计算机械加工成形。表面堆焊耐磨材料后,将人造聚晶金刚石复合片压入(紧配合)钻头体内,用柱状碳化钨保径。在石油地质钻探工程中使用的耐磨胎体钻头,其烧结胎体的主要成分是碳化钨,而在生产过程中,为满足工艺过程的要求,又将胎体粉料分为两种,一种是高强度不可切削加工的a粉,另一种是相对强度较低的可切削加工的b粉。图1即是完成烧结后的钻头体,其钻头冠部要求耐磨强度高,就采用a粉,而接近接头部分需按机械加工,则采用b粉。a、b粉末自下而上自然过渡,在烧结浸渍过程中,低熔点铜合金可顺利通过a.b粉界面区,均匀自上而下浸渍不在界面区形成任何烧结缺陷,保证钻头胎体强度整体的完整性。当进行下一道工序配接头时,钻头体的b粉部分就和配接头钢芯一起被切削程45°圆锥形(如图2所示),由此可见,可切削胎体粉料b粉在胎体钻头制造中是必不可少的。目前,b粉的配方组成是结晶坞粉占80%以上,而结晶坞粉价格很高,这样造成胎体钻头制造成本高,为了保证钻头胎体加工工艺和整体钻头性能,又不得不用昂贵的b粉。发明型内容本发明型所要解决的技术问题是现有pdc胎体钻头制造中为了保证钻头胎体加工工艺和整体钻头性能,只能选用价格昂贵的b粉,使得企业的生产成本高,其目的在于提供一种pdc胎体钻头粉料配方,通过该配方制造出胎体钻头既保证了钻头胎体加工工艺和整体钻头性能,又降低了企业的生产成本,满足企业发展需求。本发明型通过下述技术方案实现:pdc胎体钻头粉料配方,由下述重量比的组分构成:结晶坞粉为32%~40%,铁-镍粉为45%~55%,其余的13%~15%采用镍粉。目前在石油地质钻探工程中使用的耐磨胎体钻头,其烧结胎体的主要成分是碳化钨,而在生产过程中,为满足工艺过程的要求,又将胎体粉料分为两种,一种是高强度不可切削加工的a粉,另一种是相对强度较低的可切削加工的b粉。由于在烧结后的钻头体的钻头冠部要求耐磨强度高,就采用a粉,而接近接头部分由于不会与岩石产生较大接触,其耐磨强度要求不高,则这部分的材料采用b粉。虽然b粉没有与岩石直接接触,但是作为钻头的构成部分,在进行钻探时其仍然需要具备相应的要求,所以可切削胎体粉料b粉在胎体钻头制造中是必不可少的,也不能随意地替代。目前整个钻头制造行业,人们为了满足钻头胎体加工工艺和整体钻头性能满足钻探要求,将b粉的配方组成是结晶坞粉占80%以上,结晶钨粉属于钨粉中最粗的一种规格。结晶钨粉呈亮灰色粉末,有较好的流动性,结晶钨粉主要应用于表面喷涂,石油射孔,硬面材料,耐高温涂层,燃烧室喷涂高温涂层和其它耐磨、耐高温部件涂层,中频炉钨钳锅喷涂。通过将结晶钨粉采用大比重组成,烧结后满足了钻头胎体加工工艺和整体钻头性能满足钻探要求,但是市面上结晶坞粉价格很高,如此大比例的使用结晶钨粉,就会造成胎体钻头制造成本高,为了保证钻头胎体加工工艺和整体钻头性能,又不得不用昂贵的b粉。这也是目前钻头生产厂家所遇到的困难,针对可切削胎体粉料成本高的问题,经多年的探索研究,以不降低胎体物理性能(主要是可切削性和耐磨性)的前提下,采用多种合理的配方试验,进行比较筛选,最终选定一种新的配方,采用降低结晶坞粉比重,用大量铁-镍粉替代结晶坞粉,铁-镍粉是指铁镍合金粉,铁镍合金是一种在弱磁场中具有高磁导率和低矫顽力的低频软磁材料。所谓的铁镍合金,顾名思义其主要成分之一就是镍,一般情况下铁镍合金的含镍量在30%-90%范围内。铁镍合金的性能优势在于磁导率高,在弱、中磁场下尤其明显。除此之外,由于加入了贵重金属镍,所以铁镍合金拥有极小的矫顽力,加工性能非常好,相比较其他的合金而言它拥有更优异的防锈性能。除此之外,铁镍合金如果经过特定的加工,还可以获得非常不错的磁性能。铁-镍粉的相对价格较结晶坞粉低很多,而本发明将结晶坞粉为32%~40%,铁-镍粉为45%~55%,其余的13%~15%采用镍粉。所使用的组分材料都是现有材料,按照这个组分进行配制后,在保证可加工型和良好的烧结性能的前提下,使可切削胎体粉的成本下降65%,整个钻头体的成本降低35%,在不改变制造工艺的参考前提下,取得良好效果,满足企业发展需求,大大增强了企业的竞争力。进一步地,结晶坞粉为34%~38%,铁-镍粉为49%~51%,其余的13%~15%采用镍粉。按照这个组分配比形成的pdc胎体粉料,在烧结成型后可切削胎体的可切削性能略好于原可切削胎体,其烧结工艺与原可切削胎体相同,生产制造没有困难,而继续性格与原可切削胎体基本一致。作为优选的,结晶坞粉为36%,铁-镍粉为50%,其余的14%采用镍粉。采用这种固定比例的组分,其效果是最佳的,根据在厂区和钻探时的多次试验,钻头可切削胎体的可切削性能略好于原可切削胎体,其烧结工艺与原可切削胎体相同,生产制造没有困难,而继续性格与原可切削胎体基本一致,在多次钻探工程试验过程中没有出现过质量问题,显著降低了制造成本,取得明显的经济效益。本发明型与现有技术相比,具有如下的优点和有益效果:本发明通过对钻头的组分构成进行改变,制造出胎体钻头既保证了钻头胎体加工工艺和整体钻头性能满足钻探要求,同时又降低了企业的生产成本,取得明显的经济效益,满足企业发展需求,大大增强了企业的竞争力。附图说明此处所说明的附图用来提供对本发明型实施例的进一步理解,构成本申请的一部分,并不构成对本发明型实施例的限定。在附图中:图1是完成烧结后的钻头体结构示意图;图2是配接头后的钻头体结构示意图。附图中标记及对应的零部件名称:1-钻头冠部,2-配接头钢芯,3-接头,4-焊缝。具体实施方式为使本发明型的目的、技术方案和优点更加清楚明白,下面结合实施例和附图,对本发明型作进一步的详细说明,本发明型的示意性实施方式及其说明仅用于解释本发明型,并不作为对本发明型的限定。实施例1:图1是完成烧结后的钻头体,其钻头冠部1要求耐磨强度高,采用a粉,而接近接头部分,则采用本实施例的b粉。a、b粉末自下而上自然过渡,在烧结浸渍过程中,低熔点铜合金可顺利通过a.b粉界面区,均匀自上而下浸渍不在界面区形成任何烧结缺陷,保证钻头胎体强度整体的完整性。当进行下一道工序配接头时,钻头体的b粉部分就和配接头钢芯2一起被切削程45°圆锥形(如图2所示),配接头钢芯2顶面上设置有接头3,接头3底部通过焊接产生焊缝在配接头钢芯2顶面上,由此可见,可切削胎体粉料b粉在胎体钻头制造中是必不可少的。针对可切削胎体粉料成本高的问题,经多年的探索研究,以不降低胎体物理性能(主要是可切削性和耐磨性)的前提下,采用多种合理的配方试验,进行比较筛选,最终选定一种新的配方,本实施例中pdc胎体钻头粉料配方,由下述重量比的组分构成:结晶坞粉为32%,铁-镍粉为55%,其余的13%为镍粉。按照本实施例的组分进行烧结后,得到的新配方可切削胎体与原可切削胎体性能比较:抗弯强度抗冲强度硬度可切削性烧结温度原配方胎体600mpa4j30hrc良好1170℃新配方胎体630mpa4j28hrc良好1170℃从上表中可以看出,新配方可切削胎体的可切削性能和原可切削胎体的可切削性能一致,硬度基本没有影响,还是能够满足钻探需求,同时抗弯强度还略有增强,其抗冲强度和烧结温度都和原工艺相同,即其烧结工艺与原可切削胎体相同,生产制造没有困难,而继续性格与原可切削胎体基本一致,经过在多次钻探工程试验过程中没有出现过质量问题,显著降低了制造成本,取得明显的经济效益。实施例2:如图1和图2所示,本实施例与实施例1基本相同,不同之处在于:pdc胎体钻头粉料配方,由下述重量比的组分构成:结晶坞粉为40%,铁-镍粉为45%,其余的15%为镍粉。按照本实施例的组分进行烧结后测定,得到的新配方可切削胎体与原可切削胎体性能比较:抗弯强度抗冲强度硬度可切削性烧结温度原配方胎体600mpa4j30hrc良好1170℃新配方胎体632mpa4j29hrc良好1170℃从上表中可以看出,新配方可切削胎体的可切削性能和原可切削胎体的可切削性能一致,硬度基本没有影响,还是能够满足钻探需求,同时抗弯强度还略有增强,其抗冲强度和烧结温度都和原工艺相同,即其烧结工艺与原可切削胎体相同,生产制造没有困难,而继续性格与原可切削胎体基本一致,经过在多次钻探工程试验过程中没有出现过质量问题,显著降低了制造成本,取得明显的经济效益。实施例3:如图1和图2所示,本实施例与实施例1基本相同,不同之处在于:pdc胎体钻头粉料配方,由下述重量比的组分构成:结晶坞粉为34%,铁-镍粉为51%,其余的15%为镍粉。按照本实施例的组分进行烧结后测定,得到的新配方可切削胎体与原可切削胎体性能比较:抗弯强度抗冲强度硬度可切削性烧结温度原配方胎体600mpa4j30hrc良好1170℃新配方胎体635mpa4j30hrc良好1170℃从上表中可以看出,新配方可切削胎体的可切削性能和原可切削胎体的可切削性能一致,硬度基本没有影响,还是能够满足钻探需求,同时抗弯强度还略有增强,其抗冲强度和烧结温度都和原工艺相同,即其烧结工艺与原可切削胎体相同,生产制造没有困难,而继续性格与原可切削胎体基本一致,经过在多次钻探工程试验过程中没有出现过质量问题,显著降低了制造成本,取得明显的经济效益。实施例4:如图1和图2所示,本实施例与实施例1基本相同,不同之处在于:pdc胎体钻头粉料配方,由下述重量比的组分构成:结晶坞粉为38%,铁-镍粉为49%,其余的13%为镍粉。按照本实施例的组分进行烧结后测定,得到的新配方可切削胎体与原可切削胎体性能比较:抗弯强度抗冲强度硬度可切削性烧结温度原配方胎体600mpa4j30hrc良好1170℃新配方胎体632mpa4j29hrc良好1170℃从上表中可以看出,新配方可切削胎体的可切削性能和原可切削胎体的可切削性能一致,硬度基本没有影响,还是能够满足钻探需求,同时抗弯强度还略有增强,其抗冲强度和烧结温度都和原工艺相同,即其烧结工艺与原可切削胎体相同,生产制造没有困难,而继续性格与原可切削胎体基本一致,经过在多次钻探工程试验过程中没有出现过质量问题,显著降低了制造成本,取得明显的经济效益。实施例5:如图1和图2所示,本实施例与实施例1基本相同,不同之处在于:pdc胎体钻头粉料配方,由下述重量比的组分构成:结晶坞粉为36%,铁-镍粉为50%,其余的14%为镍粉。按照本实施例的组分进行烧结后测定,得到的新配方可切削胎体与原可切削胎体性能比较:抗弯强度抗冲强度硬度可切削性烧结温度原配方胎体600mpa4j30hrc良好1170℃新配方胎体638mpa4j31hrc良好1170℃从上表中可以看出,新配方可切削胎体的可切削性能和原可切削胎体的可切削性能一致,硬度还略有增强,还是能够满足钻探需求,同时抗弯强度还略有增强,其抗冲强度和烧结温度都和原工艺相同,即其烧结工艺与原可切削胎体相同,生产制造没有困难,而继续性格与原可切削胎体基本一致,经过在多次钻探工程试验过程中没有出现过质量问题,显著降低了制造成本,取得明显的经济效益。以上所述的具体实施方式,对本发明型的目的、技术方案和有益效果进行了进一步详细说明,所应理解的是,以上所述仅为本发明型的具体实施方式而已,并不用于限定本发明型的保护范围,凡在本发明型的精神和原则之内,所做的任何修改、等同替换、改进等,均应包含在本发明型的保护范围之内。当前第1页12