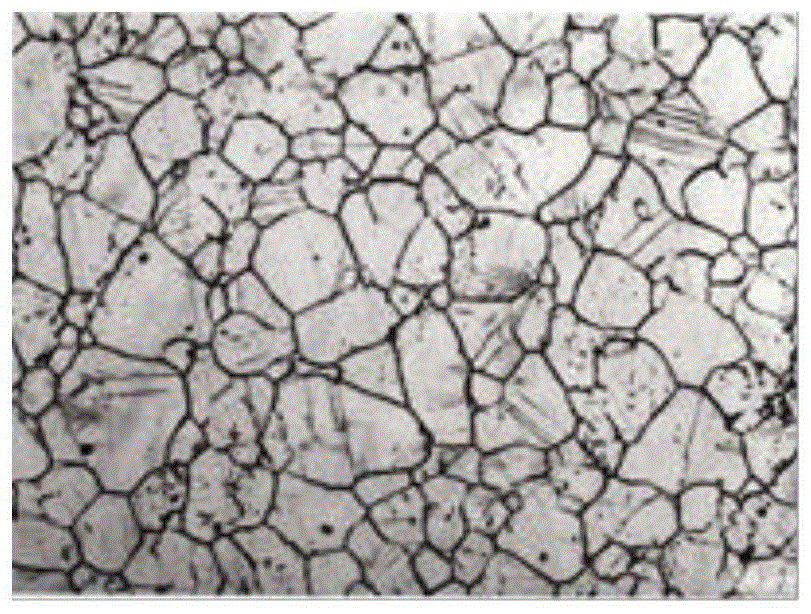
本发明属于材料
技术领域:
,尤其涉及一种镍铜合金及其制备方法。
背景技术:
:在航空航天、核工业以及海洋工程的应用设备往往对部分零部件提出了苛刻的综合性能要求,如海水泵的泵轴不仅需要很强的耐海水腐蚀、耐硫化氢腐蚀性能、较高的强度以及硬度等。而在海水环境中具有此类性能要求的材料大多是镍铜合金类材料。镍铜合金具有优良的抗海水腐蚀性能,是理想的海洋用材,被广泛的应用于海洋设备、设施中,如船用设备、管道系统的重要部件:泵和阀的零部件(如泵轴、阀杆、阀盘等)。但现有的镍铜合金会受到在海上原油开采和输运过程中原油中的硫化氢的严重腐蚀,另外,其在潜油电泵泵轴和密封管之间的应用也存在较高的摩擦系数,使得镍铜合金的使用大大受到限制。由此可见,现有的镍铜合金存在耐硫化氢腐蚀能力差,并且自润滑性差、与其他金属间的摩擦系数较高,无法满足特殊作业环境的质量需求问题。技术实现要素:本发明实施例提供一种镍铜合金,旨在解决现有的镍铜合金存在耐硫化氢腐蚀能力差,并且自润滑性差、与其他金属间的摩擦系数较高,无法满足特殊作业环境的质量需求问题。本发明实施例是这样实现的,一种镍铜合金,包括以下重量百分比的合金元素:碳0.08~0.3%;铜26.5~34%;铁1.5~2.5%;锰1.5~2.0%;硅0.1~0.5%;硫0.025~0.05%;余量为镍。本发明实施例还提供一种镍铜合金的制备方法,包括:将碳、铜、铁、锰、硅、硫以及镍按比例加入中频真空感应炉内进行熔炼,得到合金熔炼液;将所述合金熔炼液浇注到铸铁模具中成型,得到铸锭;将所述铸锭放置于电驴内加热至1100~1200℃,保温3.5~4.5小时后进行第一次锻造处理,控制其锻造变形量35%~45%,得到锻造合金;将所述锻造合金进行冷却处理,并将冷却后的锻造合金重新置于电驴内加热至1100~1200℃,保温3.5~4.5小时后进行第二次锻造处理,得到合金棒;将所述合金棒置于580~620℃下保温2.5~3.5小时,即得。本发明实施例提供的镍铜合金,一方面,具有较佳力学性能,抗拉强度达到540mpa以上,屈服强度达到230mpa以上,硬度达到hrc18以上,延伸率为25%以上,面缩31%以上;另一方面,具有很高的自润滑特性,其摩擦系数是传统镍铜合金的1/3~1/2,且其在潮湿硫化氢环境中的腐蚀速率约在0.065mm/a左右,耐硫化氢腐蚀性能非常优异,可满足某些特殊作业环境的质量需求。附图说明图1为本发明实施例提供的镍铜合金成品组织的金相图谱。具体实施方式为了使本发明的目的、技术方案及优点更加清楚明白,以下结合附图及实施例,对本发明进行进一步详细说明。应当理解,此处所描述的具体实施例仅仅用以解释本发明,并不用于限定本发明。本发明实施例提供的镍铜合金以镍为基体,还添加有碳、铜、硅、铁、硫和锰元素,其中,硫元素含量控制在0.025~0.05%范围内,有利显著提高自润滑性能;该镍铜合金,一方面,具有较佳力学性能,抗拉强度达到540mpa以上,屈服强度达到230mpa以上,硬度达到hrc18以上,延伸率为25%以上,面缩31%以上;另一方面,具有很高的自润滑特性,其摩擦系数是传统镍铜合金的1/3~1/2,且其在潮湿硫化氢环境中的腐蚀速率约在0.065mm/a左右,耐硫化氢腐蚀性能非常优异,可满足某些特殊作业环境的质量需求。本发明实施例提供了一种镍铜合金,包括以下重量百分比的合金元素:碳0.08~0.3%;铜26.5~34%;铁1.5~2.5%;锰1.5~2.0%;硅0.1~0.5%;硫0.025~0.05%;余量为镍。在本发明实施例中,硫元素的添加对所得镍铜合金获得较佳且稳定的锻造、自润滑以及腐蚀性能具有直接影响,但其不得超过0.05%,否则合金几乎没有锻造性能。作为本发明的一个优选实施例,镍铜合金包括以下重量百分比的合金元素:碳0.08~0.18%;铜27.6~30%;铁1.85~2.35%;锰1.7~1.9%;硅0.3~0.5%;硫0.025~0.03%;余量为镍。作为本发明的另一个优选实施例,镍铜合金包括以下重量百分比的合金元素:碳0.08%;铜29.5%;铁2.35%;锰1.9%;硅0.5%;硫0.025%;镍65.645%。本发明实施例还提供了一种镍铜合金的制备方法,包括以下步骤:将碳、铜、铁、锰、硅、硫以及镍按比例加入中频真空感应炉内进行熔炼,得到合金熔炼液;将所述合金熔炼液浇注到铸铁模具中成型,得到铸锭;将所述铸锭放置于电驴内加热至1100~1200℃,保温3.5~4.5小时后进行第一次锻造处理,控制其锻造变形量35%~45%,得到锻造合金;将所述锻造合金进行冷却处理,并将冷却后的锻造合金重新置于电驴内加热至1100~1200℃,保温3.5~4.5小时后进行第二次锻造处理,得到合金棒;将所述合金棒置于580~620℃下保温2.5~3.5小时,即得。在本发明实施例中,需要将碳置于直径20mm、壁厚2mm的纯铁管内,管的上面圆面用厚2mm的纯铁板焊接,并在一圆面上钻出直径2mm的小孔3个。将碳置于纯铁管内是考虑到工业化连续生产时,如果将碳直接加入到温度很高的熔炼容器内时一方面会造成碳的烧损;另一方面当真空炉启动抽真空时会吸出碳,从而会影响到最终合金中碳的含量。因此,将碳置于纯铁管内可以很好地防止碳因高温和抽真空而产生的损失,从而保证合金化学配方的准确。在本发明实施例中,镍铜合金中添加的铁的含量要考虑到装碳纯铁管的量。即添加的原料铁的含量应包括用于装碳的纯铁管的重量和配方中需要补足添加的铁的重量。在本发明的一个优选实施例中,上述将碳、铜、铁、锰、硅、硫以及镍按比例加入中频真空感应炉内进行熔炼,得到合金熔炼液的步骤,具体包括:将碳、铜、铁、锰、硅、硫以及镍按比例加入中频真空感应炉内,并加入除气剂,升温至1550~1650℃熔炼110~130分钟,再降温至1350~1450℃并保持35~45分钟,得到熔炼液;将所述熔炼液升温至1550~1650℃继续熔炼25~35分钟,再降温至1350~1450℃,并保持35~45分钟,得到合金熔炼液。在本发明实施例中,除气剂为含镁量为20%的镍镁合金或铜镁合金。其中,除气剂的加入量为合金材料总重量的0.08~0.16wt%;即除气剂中的镁、铜元素的加入量需要控制在每100公斤熔炼料加入100克~200克,高于200克/100公斤则会将镁元素引入熔炼合金而引起合金污染。由于加入的除气剂的量很少,在精炼过程中加入后绝大部分镁都会与氧结合而消耗掉,真正进入熔炼合金中的量小于ppm级,可以忽略不计,故由其引入到合金熔炼液引入镁元素杂质可以忽略不计,另外,以下具体实施例中所用除气剂均选为铜镁合金,用量控制为:每100公斤熔炼合金中加入的铜镁除气剂为100克。在本发明的一个优选实施例中,上述步骤将所述铸锭放置于电驴内加热至1100~1200℃,保温3.5~4.5小时后进行第一次锻造处理,控制其锻造变形量35%~45%,得到锻造合金的步骤,具体为:将所述铸锭放置于电驴内加热至1150℃,保温4小时后进行第一次锻造处理,控制其锻造变形量40%,得到锻造合金。在本发明的一个优选实施例中,上述步骤将所述锻造合金进行冷却处理,并将冷却后的锻造合金重新置于电驴内加热至1100~1200℃,保温3.5~4.5小时后进行第二次锻造处理,得到合金棒的步骤,具体为:将所述锻造合金进行冷却处理,并将冷却后的锻造合金重新置于电驴内加热至1150℃,保温4小时后进行第二次锻造处理,得到合金棒。以下通过具体实施例对本发明的镍铜合金的技术效果做进一步的说明。实施例1:首先将重量百分比为:0.28%的碳,67.185%的ni,28%的cu,0.5%的si,2.0%的mn,0.035%s(s的含量以fes的形式加入),2.0%的fe(铁含量要考虑到装碳纯铁管的量)于中频真空感应炉内熔炼。其中,0.28%的碳置于直径20mm、壁厚2mm的纯铁管内,管的上面圆面用厚2mm的纯铁板焊接,并在一圆面上钻出直径2mm的小孔3个。含镁量为20%的铜镁合金作为除气剂,1650℃下熔炼100分钟,然后将熔液降至1450℃并保持40分钟,再次将温度升高到1650℃下继续熔炼30分钟,然后降温到1450℃并保持30分钟后,将合金熔液浇入直径180mm的铸铁模中,30分钟后将真空炉炉盖打开,将铸铁模具吊出后直接投入到水中,1小时后将合金铸锭从模具中取出。然后铸锭在电炉内加热到1100℃并保温3.5小时,进行锻造处理,首先将铸锭进行开坯处理,控制其锻造变形量在30%左右,锻成方形后进行空冷,至室温后将开坯件表面裂纹用铣床铣掉,然后将铣后的锻件重新放入电炉内从室温重新加热至1150℃,并保温3小时,然后再用2吨空气锤进行自由锻造,将其锻造成直径为60mm的棒。对锻造所得合金棒在580℃下保温3小时进行去应力退火,即得。实施例2首先将重量百分比为:0.2%的碳,64.75%的ni,30%的cu,0.5%的si,2.0%的mn,0.05%s(s的含量以fes的形式加入),2.5%的fe(铁含量要考虑到装碳纯铁管的量)于中频真空感应炉内熔炼。其中,0.2%的碳置于直径20mm、壁厚2mm的纯铁管内,管的上面圆面用厚2mm的纯铁板焊接,并在一圆面上钻出直径2mm的小孔3个。含镁量为20%的铜镁合金作为除气剂,1650℃下熔炼120分钟,然后将熔液降至1350℃并保持45分钟,再次将温度升高到1650℃下继续熔炼30分钟,然后降温到1350℃并保持35分钟后,将合金熔液浇入直径180mm的铸铁模中,30分钟后将真空炉炉盖打开,将铸铁模具吊出后直接投入到水中,1小时后将合金铸锭从模具中取出。然后铸锭在电炉内加热到1100℃并保温4.5小时,进行锻造处理,首先将铸锭进行开坯处理,控制其锻造变形量在35%左右,锻成方形后进行空冷,至室温后将开坯件表面裂纹用铣床铣掉,然后将铣后的锻件重新放入电炉内从室温重新加热至1100℃,并保温4小时,然后再用2吨空气锤进行自由锻造,将其锻造成直径为50mm的棒。对锻造所得合金棒在580℃下保温3小时进行去应力退火,即得。实施例3首先将重量百分比为:0.1%的碳,68.47%的ni,27.6%的cu,0.3%的si,1.5%的mn,0.03%s(s的含量以fes的形式加入),2.0%的fe(铁含量要考虑到装碳纯铁管的量)于中频真空感应炉内熔炼。其中,0.1%的碳置于直径20mm、壁厚2mm的纯铁管内,管的上面圆面用厚2mm的纯铁板焊接,并在一圆面上钻出直径2mm的小孔3个。含镁量为20%的铜镁合金作为除气剂,1550℃下熔炼110分钟,然后将熔液降至1400℃并保持35分钟,再次将温度升高到1550℃下继续熔炼30分钟,然后降温到1400℃并保持35分钟后,将合金熔液浇入直径180mm的铸铁模中,35分钟后将真空炉炉盖打开,将铸铁模具吊出后直接投入到水中,1小时后将合金铸锭从模具中取出。然后铸锭在电炉内加热到1150℃并进行锻造处理,首先将铸锭进行开坯处理,控制其锻造变形量在40%左右,锻成方形后进行空冷,至室温后将开坯件表面裂纹用铣床铣掉,然后将铣后的锻件重新放入电炉内从室温重新加热至1200℃,并保温3.5小时,然后再用2吨空气锤进行自由锻造,将其锻造成直径为50mm的棒。对锻造所得合金棒在600℃下保温3小时进行去应力退火,即得。实施例4首先将重量百分比为:0.08%的碳,65.645%的ni,29.5%的cu,0.5%的si,1.9%的mn,0.0025%s(s的含量以fes的形式加入),2.35%的fe(铁含量要考虑到装碳纯铁管的量)于中频真空感应炉内熔炼。其中,0.08%的碳置于直径20mm、壁厚2mm的纯铁管内,管的上面圆面用厚2mm的纯铁板焊接,并在一圆面上钻出直径2mm的小孔3个。含镁量为20%的铜镁合金作为除气剂,1600℃下熔炼120分钟,然后将熔液降至1450℃并保持40分钟,再次将温度升高到1600℃下继续熔炼30分钟,然后降温到1450℃并保持30分钟后,将合金熔液浇入直径180mm的铸铁模中,30分钟后将真空炉炉盖打开,将铸铁模具吊出后直接投入到水中,1小时后将合金铸锭从模具中取出。然后铸锭在电炉内加热到1150℃并进行锻造处理,首先将铸锭进行开坯处理,控制其锻造变形量在40%左右,锻成方形后进行空冷,至室温后将开坯件表面裂纹用铣床铣掉,然后将铣后的锻件重新放入电炉内从室温重新加热至1200℃,并保温4小时,然后再用2吨空气锤进行自由锻造,将其锻造成直径为50mm的棒。对锻造所得合金棒在580℃下保温3小时进行去应力退火,即得。实施例5首先将重量百分比为:0.3%的碳,62.15%的ni,34%的cu,0.1%的si,1.9%的mn,0.05%s(s的含量以fes的形式加入),1.5%的fe(铁含量要考虑到装碳纯铁管的量)于中频真空感应炉内熔炼。其中,0.3%的碳置于直径20mm、壁厚2mm的纯铁管内,管的上面圆面用厚2mm的纯铁板焊接,并在一圆面上钻出直径2mm的小孔3个。含镁量为20%的铜镁合金作为除气剂,1600℃下熔炼120分钟,然后将熔液降至1400℃并保持40分钟,再次将温度升高到1600℃下继续熔炼30分钟,然后降温到1400℃并保持30分钟后,将合金熔液浇入直径180mm的铸铁模中,30分钟后将真空炉炉盖打开,将铸铁模具吊出后直接投入到水中,1小时后将400合金铸锭从模具中取出。然后铸锭在电炉内加热到1150℃并进行锻造处理,首先将铸锭进行开坯处理,控制其锻造变形量在40%左右,锻成方形后进行空冷,至室温后将开坯件表面裂纹用铣床铣掉,然后将铣后的锻件重新放入电炉内从室温重新加热至1150℃,并保温4小时,然后再用2吨空气锤进行自由锻造,将其锻造成直径为50mm的棒。对锻造所得合金棒在580℃下保温3小时进行去应力退火,即得。对本发明实施例1-5所制得的镍铜合金进行力学性能测试,测得的抗拉强度、屈服强度、硬度、延伸率、面缩率结果见下表1所示。表1抗拉强度屈服强度硬度延伸率面缩率实施例1580mpa270mpahrc2225%31%实施例2550mpa260mpahrc2030%38%实施例3540mpa230mpahrc1835%40%实施例4550mpa240mpahrc2335%35%实施例5560mpa270mpahrc2125%37%综上,从表1的实验结果可看出,本发明实施例1-5所制得的镍铜合金具有较佳力学性能,抗拉强度达到540mpa以上,屈服强度达到230mpa以上,硬度达到hrc18以上,延伸率为25%以上,面缩31%以上;上述实施例1-5所制备得到的镍铜合金的金相图谱均如图1所示,组织为栾晶奥氏体以及少量析出物。进一步,对本发明实施例1-5所制备得到的镍铜合金进行摩擦系数以及抗硫化氢腐蚀试验测试;所得结果表示本发明实施例1-5所制备得到的镍铜合金均具有很高的自润滑特性,其摩擦系数是同等条件下传统镍铜合金的1/3~1/2,且其在潮湿硫化氢环境中的腐蚀速率约在0.065mm/a左右,耐硫化氢腐蚀性能非常优异。其中,摩擦系数是通过利用美国bruker公司生产的umt-tribolab摩擦磨损试验机进行测试,实验采用球盘实验进行,上试样为4mm轴承钢(上海轴承钢厂制造,国标gb308,材质gcr15),下试样为自润滑材料,在1n的载荷下,进行往复实验(参数条件:往复行程5mm,频率2hz,速度为20mm/s);抗硫化氢腐蚀实验是利用英国solartron公司生产的si1287+si1260电化学工作站,利用电化学阻抗谱的测试方法进行测试。电化学阻抗谱是一种近似的原位测试技术,其原理是对测量体系施加一微小电位扰动(通常为5mv或10mv),对扰动后测得的电阻、电容、电感等物理元件进行模型分析,从而得到与腐蚀相关的信息。电化学阻抗谱最大的优点在于测试过程不会破坏腐蚀膜原有的形态和组织,近似于原位分析。实验方法为,首先将材料加工成规格为φ10mm×5mm的圆柱,其中一个圆面用铜线引出,次面及侧面用环氧树脂密封,露出背面作为工作面,工作面用水磨砂纸逐级打磨至7000号,酒精清洗;其次将工作电极浸泡入含有一定浓度h2s的容颜中,与sce参比电极(标准甘汞电极,饱和kcl),铂金对电极形成三电极系统,进行电化学交流阻抗谱测试;最后根据实验结果对抗硫化氢腐蚀能力进行研判。进一步,为研究硫元素对镍铜合金的自润滑特性的影响,进行了对比例1-3的设计实验:对比例1除未添加硫元素外,其余制备工艺与实施例1一致。对比例2除未添加硫元素外,其余制备工艺与实施例2一致。对比例3除未添加硫元素外,其余制备工艺与实施例3一致。将本发明实施例1-3所制备含硫镍铜合金以及对比例1-3所制备的不含硫镍铜合金分别与gcr15摩擦副对磨(干摩擦)2小时以及1n载荷下测得平均摩擦系数,如下表2所示。表2摩擦系数摩擦系数实施例10.15对比例10.64实施例20.12对比例20.69实施例30.09对比例30.63从表2中可看出,利用实施例1、2、3制备的含硫和不含硫的镍铜合金与gcr15摩擦副对磨(干摩擦)2小时以及1n载荷下测得摩擦系数,在硫元素加入后,摩擦系数显著降低,表明硫元素直接影响着镍铜合金的自润滑性能。本发明实施例提供的镍铜合金,一方面,具有较佳力学性能,抗拉强度达到540mpa以上,屈服强度达到230mpa以上,硬度达到hrc18以上,延伸率为25%以上,面缩31%以上;另一方面,具有很高的自润滑特性,其摩擦系数是传统镍铜合金的1/3~1/2,且其在潮湿硫化氢环境中的腐蚀速率约在0.065mm/a左右,耐硫化氢腐蚀性能非常优异,可满足某些特殊作业环境的质量需求。以上所述实施例仅表达了本发明的几种实施方式,其描述较为具体和详细,但并不能因此而理解为对本发明专利范围的限制。应当指出的是,对于本领域的普通技术人员来说,在不脱离本发明构思的前提下,还可以做出若干变形和改进,这些都属于本发明的保护范围。因此,本发明专利的保护范围应以所附权利要求为准。以上所述仅为本发明的较佳实施例而已,并不用以限制本发明,凡在本发明的精神和原则之内所作的任何修改、等同替换和改进等,均应包含在本发明的保护范围之内。当前第1页12