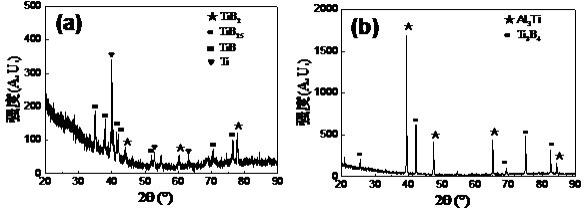
[0001]
本发明涉及一种化学热处理技术,尤其是一种通过硼铝共渗的工艺方法来提高钛合金硬度、耐磨损、抗高温氧化和抗高温腐蚀的技术,具体地说是一种钛合金表面硼铝共渗剂及共渗工艺。
背景技术:[0002]
钛合金因其具有良好的比强度高和比刚度高等一系列性能,而被广泛的使用在海洋以及电子领域,但其硬度、耐磨损、抗高温氧化和耐热腐蚀性上还不能满足航空航天及武器装备领域的要求,限制了其在航天、交通运输及武器装备的广泛应用。表面改性技术能够提高其硬度、耐磨损、抗高温氧化和耐热腐蚀性。钛合金表面渗硼技术能够获得硬度高和耐磨性高的钛合金,但其抗高温氧化和耐热腐蚀性较差;而钛合金表面硼铝共渗技术能够获得抗高温氧化好和耐热腐蚀性好的钛合金,但其硬度和耐磨性高较差。以上两种方法都难以兼顾硬度、耐磨损、抗高温氧化和耐热腐蚀性等问题。而硼铝共渗有望突破同时获得硬度高、耐磨损好、抗高温氧化好和耐热腐蚀性好的钛合金的难题。
[0003]
迄今为止,尚未有一种具有自主知识产权的能同时兼顾硬度、耐磨损和抗高温性的钛合金表面硼铝共渗工艺方法可供使用,这一定程度上制约了我国航空航天、武器装备等工业的发展。
技术实现要素:[0004]
本发明的目的是针对目前钛合金的硬度、耐磨损和抗高温性能难以兼顾的问题,发明一种钛合金表面硼铝共渗剂及共渗工艺,希望能通过硼铝共渗获得表面质量好的硼铝共渗层,来提高钛合金硬度、耐磨损、抗高温氧化性和耐热腐蚀性。
[0005]
本发明的技术方案之一是:一种钛合金表面硼铝共渗剂,其特征是:其主要由铝、碳化硼、氯化铵和碳化硅组成,其中按质量百分比为:铝20%,碳化硼20%,氯化铵5%,碳化硅55%,称取各组分并进行混合,即获得钛合金表面硼铝共渗剂。
[0006]
本发明的技术方案之二是:一种基于钛合金表面硼铝共渗剂的钛合金表面硼铝共渗工艺,其特征是:首先,对钛合金进行磨抛和清洗,获得清洁表面;然后,将钛合金放入硼铝共渗剂填充一半的坩埚中,随后再将坩埚填充满、密封并在100
±
5℃下干燥箱内保温至少1h;最后,将坩埚放入到箱式电阻炉内在950
±
10℃的硼铝共渗温度下,保温20
ꢀ-
25h,当渗层制备完成后取出空冷,即可在钛合金表面制得硬度高、耐磨性好、抗高温氧化性好和耐热腐蚀性好的硼铝共渗层。
[0007]
本发明的有益效果是:(1)渗硼涂层的硬度为1996 hv是基体(tc4)硬度(328 hv)的6.1倍,硼铝共渗涂层
(tc4)的硬度为1221 hv,大约是基体(tc4)硬度的3.72倍。
[0008]
(2)渗硼涂层(tc4)的表面划痕宽度为845μm比基体(tc4)表面划痕宽度(1108 μm)的降低了32.65%,硼铝共渗涂层的表面划痕宽度为910 μm,比tc4的表面划痕宽度(1108 μm)降低了18.82%。
[0009]
(3)在相同氧化时间(60 h)的条件下,在900℃的抗高温氧化性比700℃更好,硼铝共渗涂层的氧化质量增益为1.3 mg/cm2,达到完全抗氧化级别,比基体(tc4)氧化质量增益(69.69 mg/cm2)的降低了98.1 %,氧化层的厚度为10 μm,比基体(tc4)氧化层的厚度(590 μm)的降低了98.3 %;(4)在相同腐蚀时间(60 h)的条件下,在900℃的抗热腐蚀性比700℃更好,基体(tc4)的腐蚀质量增益为157.1 mg/cm2是硼铝共渗涂层腐蚀质量增益(0.3 mg/cm2)的5000倍,硼铝共渗涂层的腐蚀后的氧化层的厚度为8μm,基体(tc4)腐蚀后的氧化层的厚度(1400 μm)是其174倍。
附图说明
[0010]
图1是本发明渗硼层和硼铝共渗层表面xrd图谱:(a) 渗硼涂层; (b)硼铝共渗涂层;图2是本发明基体(tc4),渗硼和硼铝共渗涂层的表面硬度图;图3是本发明摩擦磨损后各样品sem图:(a) 基体(tc4); (b) 渗硼涂层; (c) 硼铝共渗涂层;图4是本发明700℃下60h内基体(tc4)、渗硼钛涂层和硼铝共渗涂层的氧化动力学曲线;图5是本发明700 ℃氧化60 h后截面形貌分析图:(a)基体(tc4); (b) 渗硼涂层; (c) 硼铝共渗涂层;图6是本发明900℃下60h内基体(tc4)、渗硼涂层和硼铝共渗涂层的氧化动力学曲线:;图7是本发明900 ℃氧化60 h后截面形貌分析图:(a)基体(tc4); (b) 渗硼涂层; (c) 硼铝共渗涂层;图8是本发明700℃下60h内基体(tc4)、渗硼涂层和硼铝共渗涂层的腐蚀动力学曲线;图9是本发明700 ℃腐蚀60 h后截面形貌分析图:(a)基体; (b) 渗硼涂层; (c) 硼铝共渗涂层;图10是本发明900℃下60h内基体(tc4)、渗硼涂层和硼铝共渗涂层的腐蚀动力学曲线;图11是本发明900 ℃腐蚀60 h后截面形貌分析图:(a)基体(tc4); (b) 渗硼涂层; (c) 硼铝共渗涂层。
具体实施方式
[0011]
下面结合附图和实施例对本发明作进一步的说明,但本发明不仅限于实施例。
[0012]
实施例一。
[0013]
如图1-11所示一种钛合金表面硼铝共渗工艺,步骤如下:首先,按质量百分比为:碳化硼20%,氯化铵5%,碳化硅75%,称取重量并进行混合,获得
钛合金表面渗硼剂;然后,对钛合金(tc4)进行磨抛和清洗,获得清洁表面;随后,将表面预处理后的基体(tc4)放入硼铝共渗剂填充一半的坩埚中,随后再将坩埚填充满,密封并在100
±
5℃下干燥箱内保温1~1.5h;最后,将坩埚放入到箱式电阻炉内在950
±
10℃的硼铝共渗温度下,保温20
ꢀ-
24h,当渗层制备完成后取出空冷,即可在钛合金表面制得硬度高、耐磨性好、抗高温氧化性好和耐热腐蚀性好的渗硼层。
[0014]
本实施例渗硼涂层硬度为1996 hv(如图2所示),表面划痕宽度为845μm(如图3所示);在700℃氧化60 h的条件下,渗硼涂层的氧化质量增益为13.0 mg/cm2(如图4所示),达到抗氧化级别,氧化层的厚度为28 μm(如图5所示);在900℃氧化60 h的条件下,渗硼涂层的氧化质量增益为61.0 mg/cm2(如图6所示),为不抗氧化级别,氧化层的厚度为580 μm(如图7所示);在700℃腐蚀60 h的条件下,渗硼涂层的腐蚀质量增益为3.5 mg/cm2(如图8所示),腐蚀后的氧化层的厚度为32 μm(如图9所示);在900℃腐蚀60 h的条件下,渗硼涂层的腐蚀质量增益为97.0 mg/cm2(如图10所示),腐蚀后的氧化层的厚度为680 μm(如图11所示)。
[0015]
实施例二。
[0016]
如图1-11所示本实施例与实施例一类同,不同之处在于将渗硼剂(b4c、sic 、nh4cl)换成硼铝共渗剂(b4c、al、sic 、nh4cl),按质量百分比为:铝20%,碳化硼20%,氯化铵5%,碳化硅55%,称取重量并进行混合,获得硼铝共渗剂;然后,对基体(tc4)进行磨抛和清洗,获得清洁表面;随后,将表面预处理后的钛合金(tc4)放入硼铝共渗剂填充一半的坩埚中,随后再将坩埚填充满,密封并在100
±
5℃下干燥箱内保温1h;最后,将坩埚放入到箱式电阻炉内在950
±
10℃的渗硼温度下,保温20 h,当渗层制备完成后取出空冷,即可在钛合金表面制得硬度高、耐磨性好、抗高温氧化性好和耐热腐蚀性好的硼铝共渗层。
[0017]
本实施例硼铝共渗涂层硬度为1221 hv(如图2所示),表面划痕宽度为910 μm(如图3所示);在700℃氧化60 h的条件下,硼铝共渗涂层的氧化质量增益为-0.2 mg/cm2(如图4所示),达到完全抗氧化级别,氧化层的厚度为7 μm(如图5所示);在900℃氧化60 h的条件下,硼铝共渗涂层的氧化质量增益为1.3 mg/cm2(如图6所示),为抗氧化级别,氧化层的厚度为10 μm(如图7所示);在700℃腐蚀60 h的条件下,硼铝共渗涂层的腐蚀质量增益为0.3 mg/cm2(如图8所示),腐蚀后的氧化层的厚度为5 μm(如图9所示);在900℃腐蚀60 h的条件下,硼铝共渗涂层的腐蚀质量增益为0.3 mg/cm2如图10所示),腐蚀后的氧化层的厚度为8 μm(如图11所示)。
[0018]
对比例。
[0019]
基体(tc4)本对比例基体(tc4)硬度为328 hv(如图2所示),表面划痕宽度为1108 μm(如图3所示);在700℃氧化60 h的条件下,钛合金(tc4)的氧化质量增益为13.5 mg/cm2(如图4所示),氧化层的厚度为240 μm(如图5所示);在900 ℃氧化60 h的条件下,钛合金(tc4)的氧
化质量增益为69.7 mg/cm2(如图6所示),为抗氧化级别,氧化层的厚度为590 μm(如图7所示);在700℃腐蚀60 h的条件下,钛合金(tc4)的腐蚀质量增益为14.1 mg/cm2(如图8所示),腐蚀后的氧化层的厚度为230 μm(如图9所示);在900℃腐蚀60 h的条件下,钛合金(tc4)的腐蚀质量增益为157.1 mg/cm2(如图10所示),腐蚀后的氧化层的厚度为1400 μm(如图11所示)。
[0020]
将两个实施例与对比例对比发现,(1)渗硼涂层的硬度为1996 hv是基体(tc4)硬度(328 hv)的6.1倍,硼铝共渗钛合金(tc4)的硬度为1221 hv,大约是基体(tc4)硬度的3.72倍(如图2所示)。
[0021]
(2)渗硼涂层的表面划痕宽度为845μm比基体表面划痕宽度(1108 μm)的降低了32.65%,硼铝共渗涂层的表面划痕宽度为910 μm,比基体(tc4)的表面划痕宽度(1108 μm)降低了18.82 %(如图3所示)。
[0022]
(3)在700℃氧化60 h的条件下,渗硼涂层的氧化质量增益为13.0 mg/cm2,达到抗氧化级别,且比基体(tc4)氧化质量增益(13.5 mg/cm2)的降低了0.037%,硼铝共渗涂层(tc4)的氧化质量增益为-0.2 mg/cm2,达到完全抗氧化级别,且抗氧化性有大幅度明显的增加(如图4所示);渗硼涂层(tc4)的氧化层的厚度为28 μm,比基体(tc4)氧化层的厚度(240 μm)的降低了88.3%,硼铝共渗涂层(tc4)的氧化层的厚度为7 μm,比基体(tc4)氧化层的厚度(240 μm)的降低了97.0%(如图5所示);在900℃氧化60 h的条件下,渗硼涂层的氧化质量增益为61.0 mg/cm2,为不抗氧化级别,比基体(tc4)氧化质量增益(69.69 mg/cm2)的降低了12.5 %,硼铝共渗涂层的氧化质量增益为1.3 mg/cm2,达到抗氧化级别,比基体(tc4)氧化质量增益(69.69 mg/cm2)的降低了98.1 %(如图6所示);渗硼涂层(tc4)的氧化层的厚度为580 μm,比基体(tc4)氧化层的厚度(590 μm)的降低了1.7 %,硼铝共渗涂层的氧化层的厚度为10 μm,比基体(tc4)氧化层的厚度(590 μm)的降低了98.3 %(如图7所示)。
[0023]
(4)在700℃腐蚀60 h的条件下,渗硼涂层的腐蚀质量增益为3.5 mg/cm2,比基体(tc4)腐蚀质量增益(14.1 mg/cm2)的降低了75.2 %,硼铝共渗涂层的腐蚀质量增益为0.3 mg/cm2,比基体(tc4)腐蚀质量增益(14.1 mg/cm2)的降低了97.9 %(如图8所示);渗硼涂层的腐蚀后的氧化层的厚度为32 μm,比基体(tc4)氧化层的厚度(230 μm)的降低了86.1 %,硼铝共渗涂层的腐蚀后的氧化层的厚度为5 μm,比基体(tc4)氧化层的厚度(230 μm)的降低了97.8 %(如图9所示);在900℃腐蚀60 h的条件下,基体(tc4)的腐蚀质量增益为157.1 mg/cm2是硼铝共渗涂层(tc4)腐蚀质量增益(0.3 mg/cm2)的5000倍,渗硼涂层的腐蚀质量增益为97.0 mg/cm2是硼铝共渗涂层腐蚀质量增益(0.3 mg/cm2)的3000倍(如图10所示),渗硼涂层腐蚀后的氧化层的厚度为680 μm,比基体(tc4)腐蚀后的氧化层的厚度(1400 μm)降低了51.4%,硼铝共渗涂层腐蚀后的氧化层的厚度为8 μm,基体(tc4)腐蚀后的氧化层的厚度(1400 μm)是其174倍(如图11所示)。
[0024]
本发明未涉及部分均与现有技术相同或可采用现有技术加以实现。