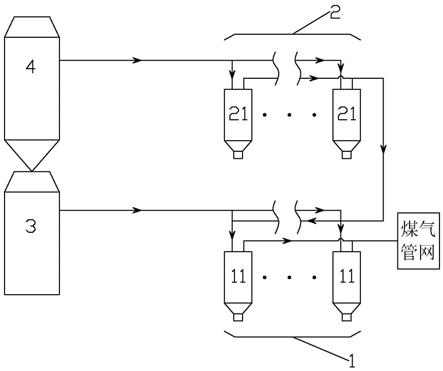
[0001]
本发明涉及高炉工程设备技术领域,具体涉及一种高炉均压放散煤气回收设备。
背景技术:[0002]
高炉是用钢板作炉壳,壳内砌耐火砖内衬。由于高炉炼铁技术经济指标良好,工艺简单,生产量大,劳动生产效率高,能耗低等优点,故这种方法生产的铁占世界铁总产量的绝大部分。高炉生产时从炉顶装入铁矿石、焦炭、造渣用熔剂(石灰石),从位于炉子下部沿炉周的风口吹入经预热的空气。在高温下焦炭(有的高炉也喷吹煤粉、重油、天然气等辅助燃料)中的碳同鼓入空气中的氧燃烧生成的一氧化碳和氢气,在炉内上升过程中除去铁矿石中的氧,从而还原得到铁,炼出的铁水从铁口放出。
[0003]
高炉生产过程中,炉顶均压放散煤气通常会随着每次装料被放散到大气中。这些放散煤气主要有以下三点害处:1、其中含有大量的一氧化碳,一方面一氧化碳作为能源气体被直接排放会造成能源浪费,另一方面一氧化碳的毒性大被大量直接排放存在安全隐患;2、放散煤气排放时的噪音比较大,会对附近居民的日常生活产生影响;3、放散煤气中的粉尘含量比较高,其直接排放到空气中会污染大气环境。
[0004]
长期以来,国内外高炉工作者都试图解决这一问题,但未获得良好效果。现有的虽然通过管路和相关设备的布设,能够实现高炉部分放散煤气的回收,但是由于这些管路和设备的布置复杂,前期投入以及后期维护的成本过高,不利于针对现有高炉设备进行改造;而且在运行过程中需要消耗大量的电和水,对于干式除尘来说还需要额外布设吹气设备,对于现有的企业来说负担较重,限制了钢铁行业的发展。
技术实现要素:[0005]
为了解决现有技术中存在的问题,本发明提供了一种高炉均压放散煤气回收设备,具体方案如下:
[0006]
包括高炉煤气回收组件和料罐煤气回收组件;
[0007]
所述高炉煤气回收组件包括若干第一回收罐,若干所述第一回收罐的入口通过管路与高炉连通,若干所述第一回收罐的出口通过管路与煤气管网连接;
[0008]
所述料罐煤气回收组件包括若干第二回收罐,若干所述第二回收罐的入口通过管路与料罐连接,若干所述第二回收罐的出口通过管路与所述第一回收罐连接;
[0009]
所述第一回收罐和所述第二回收罐内均设有强排装置和过滤装置。
[0010]
进一步地,所述强排装置包括运动板,所述运动板垂直于所述第一回收罐或所述第二回收罐的轴向布置,所述运动板的尺寸与所述第一回收罐或所述第二回收罐的截面尺寸配合;
[0011]
所述第一回收罐和所述第二回收罐内被所述运动板分隔成分别与入口连接的进气腔和与出口连接的出气腔,所述运动板上开设有进气口和出气口,所述进气口和所述出气口内分别设有第一电磁阀和第二电磁阀。
[0012]
进一步地,所述运动板的一侧还设有驱动组件,所述驱动组件用于驱动所述运动板沿所述第一回收罐或所述第二回收罐的轴向运动。
[0013]
进一步地,所述第一回收罐和所述第二回收罐均通过支架竖直布置,所述第一回收罐和所述第二回收罐的入口和出口均设于罐体的顶部,所述出气腔位于所述运动板的上方,所述进气腔位于所述运动板的下方;所述第一回收罐和所述第二回收罐的入口通过软管与所述进气口连通,所述软管布置于所述出气腔内,所述软管的长度大于所述进气腔和所述出气腔的高度之和;
[0014]
所述驱动组件包括设于所述出气腔内的液压装置,所述液压装置沿所述出气腔的轴向布置,所述液压装置固定连接于所述第一回收罐和所述第二回收罐的顶部,所述液压装置输出端的末端连接于所述运动板上。
[0015]
进一步地,所述第一回收罐和所述第二回收罐均为圆柱状罐体,所述出气口设于所述运动板底面的圆心处;所述过滤装置包括设于所述出气口下端的本体,所述本体成型为与所述运动板同轴的圆柱状结构,所述本体内设有可拆卸的过滤网,所述本体内位于所述过滤网的上方还设有振动电机,所述振动电机的输出端与所述过滤网接触;所述第一回收罐和所述第二回收罐的底面成型为锥面,所述第一回收罐和所述第二回收罐的底面开设有与所述本体配合的落灰口,所述落灰口的边沿竖直向下延伸形成落灰腔,所述落灰腔的长度大于所述本体的长度,所述落灰腔的底部设有落灰盖。
[0016]
进一步地,所述运动板的外沿套设有加强环,所述加强环采用耐高温橡胶制成。
[0017]
进一步地,所述料罐顶部设有加料口,所述加料口设有加料盖,所述加料口设有用于检测所述加料盖开合状态的传感器,所述传感器通过单片机与所述第一电磁阀、所述第二电磁阀、所述液压装置和所述振动电机电连接。
[0018]
进一步地,所述第一电磁阀、所述第二电磁阀、所述液压装置和所述振动电机外均设有隔温外壳。
[0019]
进一步地,所述隔温外壳采用导热材料制成,所述导热材料中包括至少一层空腔层,所述空腔层内设有空气或者冷却液。
[0020]
进一步地,所述隔温外壳上开设有与空腔层连通的介质入口和介质出口,所述介质入口和所述介质出口通过管路连接有风扇或者水泵。
[0021]
本发明的有益效果在于,本发明提出的高炉均压放散煤气回收设备,能够同步实现煤气回收,克服了现有技术存在的回收煤气含尘量高,压力波动大,对净煤气管网造成污染等问题,同时避免有毒气体的大量排放和粉尘污染;设备结构简单,减轻消音器负荷,降低噪音,炉顶布置方便,无需消耗大量的水电等能源即可将高炉以及料罐内的均压煤气进行回收,回收成本低。
附图说明
[0022]
图1为本发明结构示意图,
[0023]
图2为本发明第一回收罐的内部结构示意图ⅰ,
[0024]
图3为本发明第一回收罐的内部结构示意图ⅱ,
[0025]
图4为本发明运动板的结构剖视图,
[0026]
图5为本发明再一些实施例中第一回收罐的内部结构示意图ⅰ,
[0027]
图6为本发明再一些实施例中第一回收罐的内部结构示意图ⅱ,
[0028]
图7为本发明再一些实施例中隔温外壳的结构示意图。
[0029]
附图序号及名称:1、高炉煤气回收组件,11、第一回收罐,2、料罐煤气回收组件,21、第二回收罐,3、高炉,4、料罐,5、运动板,51、进气口,52、出气口,53、第一电磁阀,54、第二电磁阀,55、软管,56、液压装置,57、加强环,58、液压装置的输出端,6、进气腔,7、出气腔,8、本体,81、过滤网,82、振动电机,83、落灰口,84、落灰腔,85、落灰盖,9、隔温外壳,91、导热材料,92、空腔层。
具体实施方式
[0030]
为详细说明本发明之技术内容、构造特征、所达成目的及功效,以下兹例举实施例并配合附图详予说明。
[0031]
在本发明的描述中,需要理解的是,后续文中提到的指示方位或位置关系为基于附图所示的方位或位置关系,仅是为了便于描述本发明和简化描述,而不是指示或暗示所指的装置或元件必须具有特定的方位、以特定的方位构造和操作,因此不能理解为对本发明保护范围的限制。
[0032]
如图1所示,一种高炉均压放散煤气回收设备,包括高炉煤气回收组件1 和料罐煤气回收组件2;高炉煤气回收组件1包括若干第一回收罐11,若干第一回收罐11的入口通过管路与高炉3连通,若干第一回收罐11的出口通过管路与煤气管网连接;料罐煤气回收组件2包括若干第二回收罐21,若干第二回收罐21的入口通过管路与料罐4连接,若干第二回收罐21的出口通过管路与第一回收罐11连接;第一回收罐11和第二回收罐21内均设有强排装置和过滤装置。
[0033]
通过强排装置控制第一回收罐和第二回收罐内负压或者高压,从而使第一回收罐和第二回收罐处于吸气状态或出气状态:当第一回收罐处于负压状态时高炉煤气通过管路从高炉进入第一回收罐中,当第一回收罐处于高压状态时通过过滤装置后的高炉煤气通过管路从第一回收罐进入煤气管网进行回收利用;当第二回收罐处于负压状态时料罐煤气通过管路从料罐进入第二回收罐中,当第二回收罐处于高压状态时通过过滤装置后的料罐煤气通过管路从第二回收罐进入第一回收罐进行二次过滤(因为料罐煤气的含尘率大于高炉煤气的含尘率)。
[0034]
煤气管网内回收的煤气可以接入高温超高压发电机组用于发电,以1260m 3
高炉炉顶料罐为例,其均压放散煤气量约50m3/次、17次/时,年排放煤气量为50
×
17
×
24
×
365=7446000m3,按高温超高压发电机组每3m3的煤气能够转换为一度电,年发电量为7446000
÷
3=2482000度电,每度电按0.5元计算,年收益为0.5
×
2482000=1241000元,再加上高炉煤气的回收,能进一步提高回收煤气的收益,减少了污染的同时给炼钢企业带来极大的好处。
[0035]
如图2,以第一回收罐为例,强排装置包括运动板5,运动板5垂直于第一回收罐11的轴向布置,运动板5的尺寸与第一回收罐11的截面尺寸配合;第一回收罐11被运动板5分隔成分别与入口连接的进气腔6和与出口连接的出气腔7,运动板5上开设有进气口51和出气口52,进气口51和出气口52内分别设有第一电磁阀53和第二电磁阀54。
[0036]
结合图1和图2,第一回收罐11和第二回收罐21均通过支架竖直布置,第一回收罐
11和第二回收罐21的入口和出口均设于罐体的顶部,出气腔7位于运动板5的上方,进气腔6位于运动板5的下方;第一回收罐11和第二回收罐21的入口通过软管55与进气口51连通,软管55布置于出气腔7内,软管 55的长度大于进气腔6和出气腔7的高度之和;
[0037]
运动板5位于出气腔7的一侧设有液压装置56,液压装置56沿出气腔7 的轴向布置,液压装置56固定连接于回收罐的顶部,液压装置56的输出端58 的末端连接于运动板5上,通过液压装置驱动运动板沿第一回收罐的轴向运动。
[0038]
通过运动板的运动,配合第一电磁阀和第二电磁阀,实现控制进气腔和出气腔内压力的调整:当第一电磁阀打开,同时第二电磁阀关闭,运动板向图示的上方运动,此时进气腔体积变大,进气腔此时处于负压状态,煤气会通过回收罐的入口被“吸入”进气腔;当第二电磁阀打开,同时第一电磁阀关闭,运动板向图示的下方运动,此时进气腔体积变小,进气腔此时处于高压状态,煤气会通过出气口被“挤入”出气腔,进而通过管道进入煤气管网。
[0039]
结合图2和图3,第一回收罐11和第二回收罐21均为圆柱状罐体,出气口52设于运动板5底面的圆心处;过滤装置包括设于出气口52下端的本体8,本体8成型为与运动板5同轴的圆柱状结构,本体8内设有可拆卸的过滤网81,本体8内位于过滤网81的上方还设有振动电机82,振动电机82的输出端与过滤网81接触;第一回收罐11和第二回收罐21的底面成型为锥面,第一回收罐 11和第二回收罐21的底面开设有与本体8配合的落灰口83,落灰口83的边沿竖直向下延伸形成落灰腔84,落灰腔84的长度大于本体8的长度,落灰腔84 的底部设有落灰盖85。
[0040]
进气腔内的含尘煤气在通过出气口进入出气腔时,会优先通过过滤网,从而将煤气除尘,在重力和振动电机的作用下,除下的尘粒会通过落灰口落进落灰腔中,实际应用中可通过加装重力感应器,当落灰腔中尘粒达到一定量时打开落灰盖,将尘粒由相关设备运走。
[0041]
如图4,运动板5的外沿套设有加强环57,加强环采用耐高温橡胶制成。一方面保证运动板与回收罐内壁的密封性,防止进气腔内的含尘煤气大量进入出气腔;另一方面随着运动板的运动,加强环可以辅助进气腔进行排灰。
[0042]
在本申请的另一些实施例中,料罐4顶部设有加料口,加料口设有加料盖,加料口设有用于检测加料盖开合状态的传感器(如光纤传感器或重力传感器等,附图中未画出)。传感器通过单片机与第一电磁阀53、第二电磁阀54、液压装置56和振动电机82电连接,当单片机检测到加料口打开,则向指定部件发送相应的工作指令,其目的在于需要保证当加料口打开时进气腔必须处于负压状态,使得加料时料罐煤气不会大量溢出料罐。
[0043]
如图5和图6,在本申请的再一些实施例中,第一电磁阀53、第二电磁阀 54、液压装置56和振动电机82外均设有隔温外壳9。
[0044]
如图7,隔温外壳9采用导热材料91制成,导热材料91中包括一层空腔层92,空腔层92内设有空气或者冷却液。隔温外壳9上开设有与空腔层92连通的介质入口和介质出口,介质入口和介质出口通过管路连接有风扇或者水泵。
[0045]
通过风冷或水冷的方式将隔温外壳中的热量快速带走,由于隔温外壳采用导热材料制成,隔温外壳中的热量不仅包括高温含尘煤气的热量,还包括第一电磁阀、第二电磁阀、液压装置和振动电机本身工作时产生的热量,从而降低这些设备工作环境的恶劣程度,延长其使用寿命,进一步地减少整个高炉均压放散煤气回收设备的后期维护成本。
[0046]
综上所述,以上仅为本发明之较佳实施例,不以此限定本发明的保护范围,凡依本发明专利范围及说明书内容所作的等效变化与修饰,皆为本发明专利涵盖的范围之内。