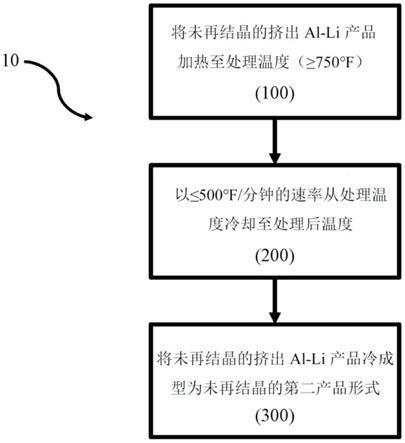
1.本公开涉及冷成型铝锂合金的方法和由其制得的未再结晶的产品。
背景技术:2.众所周知,铝
‑
锂合金通过热加工,随后进行固溶热处理和自然或人工老化而作为锻造产品生产。在不破坏微观结构的情况下将此类铝
‑
锂产品成型为最终产品形式(例如,航空航天部件)是有问题的。
技术实现要素:3.广泛地,本专利申请涉及生产冷成型、未再结晶、挤出铝
‑
锂合金产品的方法。本文公开的新方法可促进例如具有改进的冷成型特性的产品的生产,例如通过促进在高应变区域中具有主要未再结晶的微结构的挤出铝锂合金产品的保留和/或生产。新方法还可以例如通过促进受限数目的冷成型操作和/或热处理操作来促进此类产品的更高效生产。因此,可以生产更具成本效益的产品,并且此类产品可以实现改进的特性。
4.在图1中示出用于生产冷成型、未再结晶、挤出铝
‑
锂合金产品的方法的一个实施例。在所说明的实施例中,方法(10)包括将未再结晶的挤出铝
‑
锂产品加热至处理温度(100),将未再结晶的挤出铝
‑
锂产品从处理温度冷却至处理后温度(200),且接着将未再结晶的挤出铝
‑
锂产品冷成型为第二未再结晶的产品形式(300)。冷成型(300)通常如下地使未再结晶的挤出铝
‑
锂产品塑性变形:通过(a)使未再结晶的挤出铝
‑
锂产品非均匀变形(例如,使得在冷成型产品中实现可变应变),或(b)对未再结晶的挤出铝
‑
锂产品施加曲率,从而实现具有至少一个弓形表面的第二产品形式,或(a)和(b)两者。冷成型类型的非限制性实例包括冷拉伸成型、非均匀冷轧和凸块成型,仅举几例。下文提供涉及这些步骤中的每一个的更特定实施例。同样如下文所述,可按需要多次重复步骤(100)
‑
(300),直至实现产品的最终型式。在一个实施例中,利用至少两个序列(即,采用步骤(100)
‑
(300)的至少两个序列)。在一个实施例中,最终序列包括最终加热步骤(100f)、最终冷却步骤(200f)和最终冷成型步骤(300f)。作为一个非限制性实例,可重复步骤(100)
‑
(300)至多六次,其中在最终冷成型步骤(300f)之后获得最终产品。冷成型、未再结晶、挤出铝
‑
锂最终产品的非限制性实例包括机身框架、机身纵梁、机身蒙皮、机翼纵梁、翼梁、小翼、弦杆和龙骨梁等。
5.i.未再结晶的挤出铝
‑
锂产品
6.现参看图2a,如上所述,加热步骤(100)可包括加热未再结晶的挤出铝
‑
锂产品。在加热(100)之前,产生未再结晶的挤出物(挤出产品)。未再结晶的挤出铝
‑
锂产品可经由任何合适的直接或间接挤出技术制成挤出物(110)。在一个实施例中,未再结晶的挤出铝
‑
锂产品通过间接挤出产生。在另一实施例中,未再结晶的挤出铝
‑
锂产品通过直接挤出产生。一般来说,在加热(100)之前,未再结晶的挤出铝
‑
锂产品主要为未再结晶的,即含有大于50%未再结晶的晶粒。在一个实施例中,在加热(100)之前,未再结晶的挤出铝
‑
锂产品为至少60%未再结晶的。在另一实施例中,在加热(100)之前,未再结晶的挤出铝
‑
锂产品为至少
70%未再结晶的。在另一实施例中,在加热(100)之前,未再结晶的挤出铝
‑
锂产品为至少80%未再结晶的。在另一实施例中,在加热(100)之前,未再结晶的挤出铝
‑
锂产品为至少90%未再结晶的。在另一实施例中,在加热(100)之前,未再结晶的挤出铝
‑
锂产品为至少95%未再结晶的,或更多。可通过对适当光学显微照片的目视检查或经由ebsd分析来确定产品是否为未再结晶的,如下文进一步详细描述。
7.未再结晶的挤出铝
‑
锂产品可由具有锂的任何合适的铝合金制成。在一个实施例中,铝
‑
锂合金包含0.2至5.0重量%li(120)。在一个实施例中,铝
‑
锂合金为具有锂的2xxx、5xxx、7xxx或8xxx铝合金(130)之一。2xxx、5xxx、7xxx和8xxx铝合金产品的定义是根据铝业协会(aluminum association)在2015年1月公布的文献“international alloy designations and chemical composition limits for wrought aluminum and wrought aluminum alloys”,也称为“青绿色板材(teal sheets)”。在一个实施例中,铝
‑
锂合金为2xxx
‑
合金,即具有锂的2xxx铝合金。在另一实施例中,铝
‑
锂合金为5xxx
‑
li合金,即具有锂的5xxx铝合金。在另一实施例中,铝
‑
锂合金为8xxx
‑
li合金,即具有锂的8xxx铝合金。
8.在一个实施例中,未再结晶的挤出铝
‑
锂产品为2xxx
‑
li产品。在一个实施例中,2xxx
‑
li产品包含2.0
‑
5.0重量%cu、0.2
‑
2.0重量%li、至多1.5重量%mg、至多1.0重量%ag、至多1.0重量%mn、至多1.5重量%zn、各为至多0.25重量%的zr、ti、sc和hf,其余为铝,任选的附带元素和杂质。在一个实施例中,2xxx
‑
li产品为2x55型铝合金产品,其具有3.2
‑
4.2重量%cu、0.10
‑
0.50重量%mn、0.20
‑
0.6重量%mg、0.30
‑
0.7重量%zn、0.20
‑
0.7重量%ag、1.0
‑
1.3重量%li、0.05
‑
0.15重量%zr、至多0.10重量%ti、至多0.10重量%fe、和至多0.07重量%si,其余为铝、任选的附带元素和杂质。
9.ii.加热步骤
10.现参看图2b,如上所述,加热步骤(100)可包括将未再结晶的挤出铝
‑
锂产品加热至处理温度(100)。一般来说,此处理温度为至少750℉。所使用的特定处理温度可取决于合金组成,但处理温度通常低于所采用的特定铝
‑
锂合金的固相线温度。在一个实施例中,处理温度为低于未再结晶的挤出铝
‑
锂产品的固相线温度85℉至低于未再结晶的挤出铝
‑
锂产品的固相线温度15℉(140)。如下文所示的本文包括的数据所示,使用高热处理温度与适当冷却步骤(200)和适当冷成型步骤(300)的组合可促进冷成型未再结晶的挤出铝
‑
锂产品的生产。在一个实施例中,热处理温度为至少800℉。在另一实施例中,热处理温度为至少850℉。在另一实施例中,热处理温度为至少900℉。在另一实施例中,热处理温度为至少925℉。可使用其它处理温度。
11.为达到处理温度,产品加热速率应适当高。产品加热速率是产品(作为整体)在处理温度的10℉内所需的时间量。热电偶可用于确定产品何时达到处理温度。举例来说,如果产品(作为整体)从75℉的温度变为925℉的处理温度需要43分钟,则加热速率将为19.76℉/分钟((925℉
‑
75℉)/43分钟=19.76℉/分钟)。
12.在一个实施例中,加热速率为至少1℉/分钟(150)。在另一实施例中,加热速率为至少3℉/分钟。在另一实施例中,加热速率为至少5℉/分钟。在另一实施例中,加热速率为至少8℉/分钟。在另一实施例中,加热速率为至少10℉/分钟。在另一实施例中,加热速率为至少15℉/分钟。在另一实施例中,加热速率为至少20℉/分钟。在另一实施例中,加热速率为至少25℉/分钟。在另一实施例中,加热速率为至少35℉/分钟。在另一实施例中,加热速
率为至少45℉/分钟。在另一实施例中,加热速率为至少55℉/分钟。在另一实施例中,加热速率为至少65℉/分钟。在另一实施例中,加热速率为至少75℉/分钟。在另一实施例中,加热速率为至少85℉/分钟。在一个实施例中,加热速率为不超过100℉/分钟(155)。
13.一旦产品已达到处理温度,其便可在处理温度下保持任何合适的时间量。在一个实施例中,使产品保持足以溶解至少一些沉淀相粒子的时间。在另一实施例中,使产品保持足以溶解大部分或几乎所有沉淀相粒子的时间。可溶解于铝
‑
锂合金产品中的沉淀相粒子的非限制性实例尤其包括al2culi(t1)、al3li(δ')、al2cu(θ')、alli(δ)、al2cumg(s')和al2cu(ω)。在一个实施例中,在处理温度下的保持时间为至少5分钟。在另一实施例中,保持时间为至少30分钟。在一个实施例中,保持时间不超过10小时。在另一实施例中,保持时间不超过5小时。在另一实施例中,保持时间不超过3小时。在另一实施例中,保持时间不超过2小时。在一个特定实施例中,保持时间为约1小时。因此,加热步骤(100)可包含持续足以溶解主要量的沉淀相粒子但不使未再结晶的挤出铝
‑
锂产品再结晶的时间段将未再结晶的挤出铝
‑
锂产品保持在处理温度下。
14.现参看图2c,最终加热步骤(100f)可采用此部分中所描述的加热条件/参数中的任一个。在一些情况下,最终加热步骤(100f)被视为固溶热处理步骤,如图2c中所示。
15.iii.冷却步骤
16.现参看图3,如上所述,冷却步骤(200)可包括将未再结晶的挤出铝
‑
锂产品从处理温度冷却至处理后温度。对于非最终冷却步骤,从处理温度至处理后温度的冷却速率通常不大于500℉/分钟。通过使用适当冷却速率,可在未再结晶的挤出铝
‑
锂产品中形成适当量和/或适当分布的沉淀物。此分布可促进例如较高浓度的较小沉淀相粒子,如下文进一步详细解释。较高浓度的较小沉淀相粒子(例如,在以下章节iv中所描述的d10、d50和d90量内)可促进晶界固定,同时还减少冷成型操作期间存在的溶质的量。晶界固定可限制/防止再结晶。进一步具有相对较低量的纳米级沉淀相(例如<20纳米),其通常充当强化相,可促进材料的加工。较大粒子还可充当用于再结晶的成核位点。因此,本文所述的方法可限制/避免大规模和纳米级粒子的产生,同时具有适当量的小沉淀相粒子。
17.如上所述,在一个实施例中,从处理温度至处理后温度的冷却速率不大于500℉/分钟。举例来说,如果材料在118分钟内从965℉的处理温度冷却至75℉的处理后温度,则冷却速率将为每分钟7.5℃。在一个实施例中,冷却速率不大于400℉/分钟。在另一实施例中,冷却速率不大于300℉/分钟。在另一实施例中,冷却速率不大于200℉/分钟。在另一实施例中,冷却速率不大于100℉/分钟。在另一实施例中,冷却速率不大于50℉/分钟,或更小。
18.冷却速率还应该足够快以限制大沉淀相粒子的产生。因此,在一个实施例中,冷却速率为至少1℉/分钟。因此,一个可接受的冷却速率范围可以是至少1℉/分钟至不超过500℉/分钟的冷却速率(210)。在一个实施例中,冷却速率为至少5℉/分钟。在另一实施例中,冷却速率为至少10℉/分钟。
19.在一个实施例中,冷却步骤(200)包含空气冷却(215)。在一个实施例中,空气冷却(215)包含从炉(或其它加热设备)中移出产品并且使产品自然地冷却至室温。在另一实施例中,空气冷却包含强制空气冷却,其中从炉(或其它加热设备)中移出产品,且迫使空气(或另一气体)围绕产品的外表面,从而促进对流冷却。
20.在冷却步骤(200)结束之后,未再结晶的挤出铝
‑
锂产品可完全或部分维持其未再
结晶的微观结构(220),且至少部分归因于本文所述的加工条件的使用。一般来说,在冷却步骤(200)结束之后,未再结晶的挤出铝
‑
锂产品主要为未再结晶的。在一个实施例中,在冷却步骤(200)结束之后,未再结晶的挤出铝
‑
锂产品为至少60%未再结晶的。在另一实施例中,在冷却步骤(200)结束之后,未再结晶的挤出铝
‑
锂产品为至少70%未再结晶的。在另一实施例中,在冷却步骤(200)结束之后,未再结晶的挤出铝
‑
锂产品为至少80%未再结晶的。在另一实施例中,在冷却步骤(200)结束之后,未再结晶的挤出铝
‑
锂产品为至少90%未再结晶的。在另一实施例中,在冷却步骤(200)结束之后,未再结晶的挤出铝
‑
锂产品为至少95%未再结晶的,或更多。
21.现参看图2c,最终冷却步骤(200f)在最终加热步骤(100f)之后。对于最终冷却步骤(200f),冷却速率通常不同。具体地,最终冷却步骤可采用快速淬灭以形成过饱和状态(例如,用于后续自然或人工老化)。在一些实施例中,最终冷却步骤(200f)被视为相对于固溶热处理的快速淬灭步骤,如图2c中所示。因此,在一些实施例中,最终冷却步骤(200f)的冷却速率可为1000℉/分钟,或更高。一些合适的快速淬灭方法包括液体浸没和液体喷雾,尤其如冷水浸没或冷水喷雾。在一个实施例中,最终冷却步骤(200f)的冷却速率为至少100℉/秒。在另一实施例中,最终冷却步骤(200f)的冷却速率为至少200℉/秒。在另一实施例中,最终冷却步骤(200f)的冷却速率为至少400℉/秒。在另一实施例中,最终冷却步骤(200f)的冷却速率为至少800℉/秒。在另一实施例中,最终冷却步骤(200f)的冷却速率为至少1600℉/秒,或更高。
22.iv.冷成型步骤
23.现参看图4a,如上所述,冷成型步骤(300)可包括将未再结晶的挤出铝
‑
锂产品冷成型为第二未再结晶的产品形式(300)。冷成型(300)通常如下地使未再结晶的挤出铝
‑
锂产品塑性变形:通过(a)使未再结晶的挤出铝
‑
锂产品非均匀变形(例如,使得在冷成型产品中实现可变应变)(320),或(b)对未再结晶的挤出铝
‑
锂产品施加曲率(330),从而实现具有至少一个弓形表面的第二产品形式,或(a)和(b)两者。冷成型类型的非限制性实例包括冷拉伸成型、非均匀冷轧和凸块成型,仅举几例。出于本专利申请的目的,非最终冷成型步骤(300)不包括通常对产品进行均匀应变,例如片材或板材的常规冷轧。
24.在一个实施例中,非最终冷成型步骤在产品的至少部分中诱导3
‑
20%应变(310)。较高应变量可促进较少的冷成型循环。然而,过多应变可导致产品的小部分或甚至相当大的部分再结晶。因此,应控制诱导应变。在一个实施例中,非最终冷成型步骤的最大诱导应变不大于18%。在另一实施例中,非最终冷成型步骤的最大诱导应变不大于15%。在另一实施例中,非最终冷成型步骤的最大诱导应变不大于12%。在另一实施例中,非最终冷成型步骤的最大诱导应变不大于10%。在另一实施例中,非最终冷成型步骤的最大诱导应变不大于8%,或更小。在一个实施例中,非最终冷成型步骤的最大诱导应变为至少3.5%。在另一实施例中,非最终冷成型步骤的最大诱导应变为至少4%。在另一实施例中,非最终冷成型步骤的最大诱导应变为至少4.5%。在另一实施例中,非最终冷成型步骤的最大诱导应变为至少5%。在另一实施例中,非最终冷成型步骤的最大诱导应变为至少5.5%,或更大。
25.如上所述,冷成型(300)可包含使未再结晶的挤出铝
‑
锂产品非均匀变形(320)。在一个实施例中,冷成型(300)产生实现第一应变量的第二产品形式的第一部分(322)和实现第二应变量的第二产品形式的第二部分(324),其中第一应变量与第二应变量相差至少1%
(326)。在一个实施例中,应变差为至少2%。在另一实施例中,应变差为至少3%。在另一实施例中,应变差为至少5%。在另一实施例中,应变差为至少6%,或更高。
26.冷成型(300)可在任何合适的冷成型温度下开始。通常,冷成型是在产品应变硬化时开始的,主要通过位错滑移过程和位错相互作用,导致位错倍增和金属中位错密度的总体增加。因此,在一个实施例中,当未再结晶的挤出铝
‑
锂产品具有不大于400℉的温度时,开始冷成型步骤(300)。在另一实施例中,当未再结晶的挤出铝
‑
锂产品具有不大于300℉的温度时,开始冷成型步骤(300)。在另一实施例中,当未再结晶的挤出铝
‑
锂产品具有不大于200℉的温度时,开始冷成型步骤(300)。在另一实施例中,当未再结晶的挤出铝
‑
锂产品具有不大于150℉的温度时,开始冷成型步骤(300)。在另一实施例中,当未再结晶的挤出铝
‑
锂产品具有不大于125℉的温度时,开始冷成型步骤(300)。在另一实施例中,当未再结晶的挤出铝
‑
锂产品具有不大于100℉的温度时,开始冷成型步骤(300)。在另一实施例中,当未再结晶的挤出铝
‑
锂产品具有不大于90℉或更小的温度时,开始冷成型步骤(300)。在一个实施例中,当未再结晶的挤出铝
‑
锂产品在环境温度下时,开始冷成型步骤(300)。
27.在冷成型步骤(300)结束之后,第二产品形式可完全或部分维持先前未再结晶的挤出铝
‑
锂产品的未再结晶的微观结构(340),且至少部分归因于本文所述的加工条件的使用。通常,在冷成型步骤(300)结束之后,第二产品主要为未再结晶的。在一个实施例中,在冷成型步骤(300)结束之后,第二产品形式为至少60%未再结晶的。在另一实施例中,在冷成型步骤(300)结束之后,第二产品形式为至少70%未再结晶的。在另一实施例中,在冷成型步骤(300)结束之后,第二产品形式为至少80%未再结晶的。在另一实施例中,在冷成型步骤(300)结束之后,第二产品形式为至少90%未再结晶的。在另一实施例中,在冷成型步骤(300)结束之后,第二产品形式为至少95%未再结晶的,或更多。
28.现参看图4b,如上所述,归因于本文所公开的加工条件,可实现沉淀相粒子的独特分布。此分布可促进例如较高浓度的较小沉淀相粒子(350),如以上章节iii中所解释。在一个实施例中,第二产品形式包含沉淀相粒子并且这些沉淀相粒子的d50不大于0.50微米。在另一实施例中,这些沉淀相粒子的d50不大于0.25微米。在另一实施例中,这些沉淀相粒子的d50不大于0.10微米。在另一实施例中,这些沉淀相粒子的d50不大于0.08微米,或更小。将根据下文的粒度计算机分析程序测量和计算粒度和其分布。初始未再结晶挤出铝
‑
锂产品还可实现这些沉淀相粒度和粒度分布中的任一个。
29.在一个实施例中,第二产品形式包含沉淀相粒子并且这些沉淀相粒子的d90不大于2.0微米。在另一实施例中,这些沉淀相粒子的d90不大于1.5微米。在另一实施例中,这些沉淀相粒子的d90不大于1.25微米。在另一实施例中,这些沉淀相粒子的d90不大于1.10微米,或更小。初始未再结晶挤出铝
‑
锂产品还可实现这些沉淀相粒度和粒度分布中的任一个。
30.在一个实施例中,第二产品形式包含沉淀相粒子并且这些沉淀相粒子的d10不大于0.125微米。在另一实施例中,这些沉淀相粒子的d10不大于0.10微米。在另一实施例中,这些沉淀相粒子的d10不大于0.075微米。在另一实施例中,这些沉淀相粒子的d10不大于0.050微米。在另一实施例中,这些沉淀相粒子的d10不大于0.025微米,或更小。初始未再结晶挤出铝
‑
锂产品还可实现这些沉淀相粒度和粒度分布中的任一个。
31.现参看图2c,最终冷成型步骤(300f)在最终冷却步骤(200f)之后。最终冷成型步
骤可在产品的至少部分中诱导0.5至20%或0.5至10%应变。在一个实施例中,最终冷成型步骤的最大诱导应变不大于8%。在另一实施例中,最终冷成型步骤的最大诱导应变不大于6%。在另一实施例中,最终冷成型步骤的最大诱导应变不大于5%,或更小。在一个实施例中,最终冷成型步骤的最大诱导应变为至少1.0%。在另一实施例中,最终冷成型步骤的最大诱导应变为至少1.5%。在另一实施例中,最终冷成型步骤的最大诱导应变为至少2.0%。在另一实施例中,最终冷成型步骤的最大诱导应变为至少2.5%。在另一实施例中,最终冷成型步骤的最大诱导应变为至少3.5%,或更大。在一个实施例中,最终冷成型步骤(300f)可采用上文所述的任何冷成型操作。在另一实施例中,最终冷成型步骤(300f)是冷加工步骤,其包含拉伸和轧制等中的一个或多个。在一个实施例中,最终冷成型步骤(300f)是拉伸。在另一实施例中,最终冷成型步骤(300f)是轧制。不同于非最终冷成型操作,在一些情况下,最终冷成型步骤(300f)可包括均匀应变和/或非弓状应变(例如,一般均匀拉伸)。在一个实施例中,最终冷成型步骤包含将产品拉伸约1
‑
5%。
32.v.重复步骤
33.仍参看图2c,如上所述,可按需要多次重复步骤(100)
‑
(300),直至实现产品的最终型式。在一个实施例中,采用至少两个循环,初始循环(100
i
)
‑
(300
i
)和最终循环(100
f
)
‑
(300
f
)。可采用任何数目个中间循环。因此,第二产品形式可能不是最终产品形式,即,第二产品形式可能是中间产品形式。在这些实施例中,第二产品形式可以根据步骤(100)
‑
(300)加工以产生另一产品形式。当第二产品形式将被加工成另一中间产品形式时,采用加热(100)、冷却(200)和冷成型(300)步骤的非最终型式。当第二产品形式将被加工成最终产品形式时,采用加热(100f)、冷却(200f)和冷成型(300f)步骤的最终型式。因此,所述方法可按需要重复加热、冷却和冷成型步骤,直至实现最终产品形式。在一个实施例中,重复步骤(100)
‑
(300)六次。在另一实施例中,重复步骤(100)
‑
(300)五次。在另一实施例中,重复步骤(100)
‑
(300)四次。在另一实施例中,重复步骤(100)
‑
(300)三次。在另一实施例中,仅重复步骤(100)
‑
(300)两次,例如,进行步骤(100i)
‑
(300i),随后进行步骤(100f)
‑
(300f)。
34.与进行步骤(100)
‑
(300)的次数无关,最终产品形式可实现主要未再结晶的微观结构。在一个实施例中,最终产品形式为至少60%未再结晶的。在另一实施例中,最终产品形式为至少70%未再结晶的。在另一实施例中,最终产品形式为至少80%未再结晶的。在另一实施例中,最终产品形式为至少90%未再结晶的。在另一实施例中,最终产品形式为至少95%未再结晶的,或更多。
35.如上所述,最终产品可用于多种航空航天和其它应用。可用于航空航天应用的冷成型、未再结晶、挤出铝
‑
锂最终产品的非限制性实例包括机身框架、机身纵梁、机身蒙皮、机翼纵梁、翼梁、小翼、弦杆和龙骨梁等。最终产品还可用于其它应用,例如汽车、地面运输和工业应用。
36.最后,应注意,步骤(100)、(200)和(300)本身具有创造性。例如,相信步骤(100)是新颖和创造性的,并且可以独立地获得专利。相信步骤(200)是新颖和创造性的,并且可以独立地获得专利。相信步骤(300)是新颖和创造性的,并且可以独立地获得专利。这同样适用于最终步骤(100f)、(200f)和(300f)。
37.vi.最终产品的任选的额外加工
38.现参看图5a,在最终冷成型步骤(300f)之后,最终产品可任选地经受一个或多个
额外加工操作。举例来说,最终产品可经老化(410)或机械加工(420)。老化步骤(410)可包括自然(412)和/或人工(414)老化。因此,最终产品通常处于t3、t4、t6、t7或t8回火之一。如果使用其它加工,则最终产品可处于其它回火,如t1、t2、t5、t9或t10回火中的任一个。最终产品还可以w回火形式供应。本文所用的回火名称是根据ansi h35.1(2009)。
39.现参看图5b,在任何任选的额外加工(400)之后,加工后的最终产品形式可完全或部分维持未再结晶的微观结构(460)。因此,加工后的最终产品形式可实现主要未再结晶的微观结构。在一个实施例中,最终产品形式为至少60%未再结晶的。在另一实施例中,最终产品形式为至少70%未再结晶的。在另一实施例中,最终产品形式为至少80%未再结晶的。在另一实施例中,最终产品形式为至少90%未再结晶的。在另一实施例中,最终产品形式为至少95%未再结晶的,或更多。
40.如上所述,最终产品可用于多种航空航天和其它应用。可用于航空航天应用的冷成型、未再结晶、挤出铝
‑
锂最终产品的非限制性实例包括机身框架、机身纵梁、机身蒙皮、机翼纵梁、翼梁、小翼、弦杆和龙骨梁等。
41.vii.应用于其它合金和产品形式
42.尽管相对于铝
‑
锂合金产品(例如,2xxx
‑
li产品;5xxx
‑
li产品;8xxx
‑
li产品)描述前述章节中所述的方法,但本文中所述的方法还可用于其它可热处理的铝合金,如用于2xxx、6xxx、7xxx和可热处理的8xxx铝合金的无锂型式中的任一种,且明确预期本文所述的本发明方法可用于此类铝合金。此外,尽管相对于挤出铝合金产品描述前述章节中所述的方法,但本文所述的方法还可用于其它锻造产品形式,例如未再结晶的轧制铝合金产品和未再结晶的锻造铝合金产品,且明确预期本文所述的本发明方法可用于此类未再结晶的轧制铝合金产品和此类未再结晶的锻造铝合金产品。
43.viii.程序
44.a.微观结构测定程序
45.以下程序用于确定根据本专利申请制得的挤出铝合金产品的一个或多个冷成型部分是再结晶的还是未再结晶的。可进行类似分析以确定产品的再结晶程度。
46.步骤1
‑
从具有最高冷成型应变的区域获得三个样本
47.来自挤出产品的三个样本将取自挤出产品中由于冷成型所致的最高应变的区域。冷成型应变是通过冷成型(如上文所定义)诱导的应变。例如,如果冷成型使得产品的部分因冷成型而具有8%、6%和4%的应变,则将从因冷成型而具有8%应变的部分中获取三个样本。将忽略挤出产品内的其它应变(例如,由挤出过程诱导的应变)。仅考虑冷成型应变。可使用例如但不限于以下的各种已知方法测量应变:量规标记、应变计和数字散斑图样相关性。
48.步骤2
‑
制备三个样本的光学显微照片
49.将获得在步骤1中获得的三个样本的光学显微照片。首先,将通过标准金相样品制备方法制备样品。例如,样品可用buehler si
‑‑
c纸手动抛光3分钟,然后用平均粒度为约3微米的buehler金刚石液体抛光剂手动抛光。然后可将样品在氟酸硼水溶液中阳极化30
‑
45秒。然后可使用含有三氧化铬的磷酸水溶液汽提样品,且接着冲洗并干燥。这些程序符合astm e3,金相样本制备标准指南。
50.制备后,将在lt
‑
st平面上以50x或100x放大率获得三个样品中的每一个的光学显
微照片。光学显微照片将展示样品的整个厚度。本发明合金的合适的光学显微照片的一个实例展示于图15a中。非本发明合金的合适的光学显微照片的一个实例展示于图15b中。如所示出,本发明合金通常在内部区域1020中未再结晶,在这种特定情况下,所述区域通常从表面以下约10%到刚好在产品的中间部分(t/2)外部。相反,非本发明合金在此相同区域(1040)中再结晶。此外,本发明产品几乎完全未再结晶,仅在产品的中间厚度部分处实现几个大晶粒。因此,在一个实施例中,光学显微照片的目视检查将指示挤出铝合金产品的冷成型部分是未再结晶的(根据图15a)还是再结晶的(根据图15b)。如可能了解的,如果挤出铝合金产品的高应变部分保持未再结晶,则未再结晶的挤出铝合金产品的其它部分也将通常由于热力学而保持未再结晶。
51.步骤3(任选的)
‑
制备ebsd图像并获得晶粒度数据
52.在一些实施例中,ebsd成像和对应计算机分析可用于确定产品的冷成型部分是否未再结晶。在这些实施例中,将使用在步骤1中获得的样本和来自步骤2的光学显微照片。使用来自步骤2的光学显微照片,将鉴别具有大晶粒的区域。举例来说,在图15a中,一些大晶粒似乎位于产品的中间厚度(t/2)处。随后,使用将大晶粒区域放大1000x的三个sem图像对来自样本的特定大晶粒区域进行ebsd(电子反向散射衍射)。因此,如果将对图15a的产品进行ebsd分析(这将是不必要的,因为产品是未再结晶的),则将通过在图15a的产品的大晶粒区域的1000x放大率下获得三个sem图像来进行ebsd分析。
53.将对获得的sem进行计算机化分析,其中根据下文展示的晶粒度计算机分析程序计算粒度。来自三个sem的数值晶粒度数据将在适当的数据分析程序(例如microsoft excel)中校对且经由直方图分析进行分析。直方图应将小于7.5微米的晶粒分配到第一分格,其中后续分格以10微米晶粒度递增,至多67.4微米。最后一个分格应用于粒度为至少67.5微米的晶粒。分析应计算每一分格的晶粒数目并确定那些分格的面积分数(%)。实例展示于图13f中。
54.b.晶粒度计算机分析程序
55.电子反向散射衍射(ebsd)映射测量将使用配备有ebsd相机、edax hikari super相机或等效物的thermo fisher scientific apreo s扫描电子显微镜(sem)或等效物进行。应使用利用16(或等效值)的光斑尺寸、20kv的加速电压与65
°
的样品倾斜角和17mm的工作距离的sem成像条件进行测量。ebsd将使用edax oim数据收集软件版本7.3.1与edax hikari super相机或等效物一起执行。ebsd图案将使用4
×
4分格和增强型图像处理收集,包括静态背景减与后续标准化强度直方图)或等效方法。使用步长为0.5μm的方形网格扫描模式,以500μm
×
500μm的尺寸进行ebsd扫描。
56.用于分析所获取的数据的软件应为edax tsl oim
tm
8数据分析程序包或类似者。数据分析将包括2步清理程序。第一步为应用于具有0.1的最小置信指数(confidence index,ci)和5度的晶粒容差角度的数据的相邻取向相关性2级清理。第二步为晶粒扩张,对于单次迭代,使用5度的晶粒容差角和每晶粒5个点的最小值。
57.晶粒被定义成每晶粒具有5个点的最小值以及5度的晶粒容差角。使用软件通过面积加权平均晶粒度确定晶粒度。软件首先通过对每个晶粒内的点数进行计数且乘以每个点的大小(步长平方)来计算个别晶粒面积。接着通过对个别晶粒度乘以其面积除以总面积求和来确定面积加权平均值。在所有情况下,如果晶粒在平面视图中是完美的圆,则晶粒度结
果表示等效直径(以微米为单位)。接着将晶粒度直径分格,并相对于面积分数绘制。
58.c.粒度计算机分析程序
59.反向散射电子(bse)成像应该用扫描电子显微镜feg
‑
sem,如thermo
‑
scientific apreo s或等效物进行。sem成像条件是光斑尺寸为10(或等效值)、加速电压为2kv且工作距离为3mm。将使用透镜内t1反向散射检测器或等效物以1000
×
(水平场宽127微米)的放大率获取图像。将应用1.5的伽马校正(gamma correction)以帮助粒子从较亮晶粒的通道对比度中脱颖而出。
60.使用所获得的1000
×
图像中的三个使用适当软件程序,例如由美国国立卫生研究院提供的imagej软件,https://imagej.nih.gov/ij/来进行图像分析。软件将根据用户输入0.0413μm/像素、6个定义粒子的最小像素以及在0至255(或等效值)范围内的80
‑
100(通常为91)(或等效值)的最小亮度阈值来计算粒子的数目、大小和面积百分比。使用80
‑
100(通常为91)(或等效值)的阈值将有助于检测图像中的小粒子和大粒子以确定其数量,且因此确定材料的d10、d50和d90。(参见章节iv)。80
‑
100(通常为91)(或等效值)的阈值也将避免检测纳米级粒子,这会不恰当地歪曲小粒子和大粒子结果。
61.ix.代表性条项
62.下文是定义一个或多个发明的一些非限制性、代表性条项。这些条项是非限制性实例,且并不打算将本文所公开的本发明限制于所述的事项,且并不将本发明限制于所述的事项。实际上,本说明书中所述的主题中的任一个都可用于定义一个或多个发明。
63.条项1.一种方法,其包含:
64.将未再结晶的挤出铝
‑
锂产品冷成型为第二产品形式;
65.(i)其中所述未再结晶的挤出铝
‑
锂合金包含0.2
‑
5.0重量%的li;
66.(ii)其中所述未再结晶的挤出铝
‑
锂产品主要为未再结晶的;
67.(iii)其中所述冷成型包含当所述未再结晶的挤出铝
‑
锂产品具有不大于400℉的温度时开始所述冷成型;
68.(iv)其中所述冷成型包含使所述未再结晶的挤出铝
‑
锂产品塑性变形,其中所述塑性变形包含以下中的至少一个:
69.(a)使所述未再结晶的挤出铝
‑
锂产品非均匀变形,其中由于所述非均匀变形,所述第二产品形式的第一部分实现第一应变量,且所述第二产品形式的第二部分实现第二应变量,其中所述第一应变量与所述第二应变量相差至少1%;以及
70.(b)对所述未再结晶的挤出铝
‑
锂产品施加曲率,其中所述第二产品形式包含至少一个弓形表面。
71.(v)其中所述第二产品形式主要为未再结晶的。
72.条项2.根据条项1所述的方法,其中在冷成型步骤之前,所述方法包含:
73.将所述未再结晶的挤出铝
‑
锂产品加热至处理温度,其中所述处理温度为至少750℉;且接着
74.将所述未再结晶的挤出铝
‑
锂产品从所述处理温度冷却至处理后温度,并且以不大于500℉/分钟的冷却速率冷却。
75.条项3.根据前述条项中任一项所述的方法,其包含:
76.将所述第二产品形式第二次加热至第二处理温度,其中所述第二处理温度为至少
750℉;
77.将所述第二产品形式从所述第二处理温度第二次冷却至第二处理后温度;
78.将所述第二产品形式第二次冷成型为另一产品形式,其中所述另一产品形式主要为未再结晶的。
79.条项4.根据前述条项中任一项所述的方法,其中第二产品形式为中间产品形式,其中另一产品形式为最终产品形式,且其中第二冷却包含以至少1000℉/分钟的速率将第二产品形式从第二处理温度冷却至第二处理后温度。
80.条项5.根据前述条项中任一项所述的方法,其中所述未再结晶的挤出铝
‑
锂产品为2xxx
‑
li产品,且其中所述2xxx
‑
li产品包含2.0
‑
5.0重量%cu、0.2
‑
2.0重量%li、至多1.5重量%mg、至多1.0重量%ag、至多1.0重量%mn、至多1.5重量%zn、各为至多0.25重量%的zr、ti、sc和hf,其余为铝,任选的附带元素和杂质。
81.条项6.根据条项5所述的方法,其中所述2xxx
‑
li产品为2x55铝合金产品。
82.条项7.根据前述条项中任一项所述的方法,其中所述未再结晶的挤出铝
‑
锂产品为至少60%未再结晶的,或至少70%未再结晶的,或至少80%未再结晶的,或至少90%未再结晶的,或至少95%未再结晶的。
83.条项8.根据条项1所述的方法,其中所述处理温度为至少800℉,或至少850℉,或至少900℉,或至少925℉。
84.条项9.根据前述条项中任一项所述的方法,其中所述处理温度低于未再结晶的挤出铝
‑
锂产品的固相线温度。
85.条项10.根据前述条项中任一项所述的方法,其中所述处理温度为低于未再结晶的挤出铝
‑
锂产品的固相线温度85℉至低于未再结晶的挤出铝
‑
锂产品的固相线温度15℉。
86.条项11.根据前述条项中任一项所述的方法,其中加热包含以如下的加热速率将未再结晶的挤出铝
‑
锂产品从处理前温度加热至处理温度:至少1℉/分钟,或至少3℉/分钟,或至少5℉/分钟,或至少8℉/分钟,或至少10℉/分钟,或至少15℉/分钟,或至少20℉/分钟,或至少25℉/分钟,或至少35℉/分钟,或至少45℉/分钟,或至少55℉/分钟,或至少65℉/分钟,或至少75℉/分钟,或至少85℉/分钟。
87.条项12.根据前述条项中任一项所述的方法,其中加热包含以不大于100℉/分钟的加热速率将未再结晶的挤出铝
‑
锂产品从处理前温度加热至处理温度。
88.条项13.根据前述条项中任一项所述的方法,其中加热包含持续足以溶解主要量的沉淀相粒子但不使未再结晶的挤出铝
‑
锂产品再结晶的时间段将未再结晶的挤出铝
‑
锂产品保持在处理温度下。
89.条项14.根据前述条项中任一项所述的方法,其中冷却包含以如下的冷却速率将未再结晶的挤出铝
‑
锂产品从处理温度冷却至处理后温度:不大于400℉/分钟的冷却速率,或不大于300℉/分钟的冷却速率,或不大于200℉/分钟的冷却速率,或不大于100℉/分钟的冷却速率,或不大于50℉/分钟。
90.条项15.根据前述条项中任一项所述的方法,其中所述冷成型包含在第二产品形式中包括3%至20%应变。
91.条项16.根据条项15所述的方法,其中所述冷成型包含在第二产品形式中包括不大于18%应变,或不大于15%应变,或不大于12%应变,或不大于10%应变,或不大于8%应
变。
92.条项17.根据条项15至16中任一项所述的方法,其中所述冷成型包含在第二产品形式中诱导至少3.5%应变,或至少4%应变,或至少4.5%应变,或至少5%应变,或至少5.5%应变。
93.条项18.根据前述条项中任一项所述的方法,其中所述冷成型包含当未再结晶的挤出铝
‑
锂产品具有不大于300℉,或不大于200℉,或不大于150℉,或不大于125℉,或不大于100℉的温度时开始所述冷成型。
94.条项19.根据前述条项中任一项所述的方法,其中所述冷成型包含当未再结晶的挤出铝
‑
锂产品处于环境温度下时开始所述冷成型。
95.条项20.根据前述条项中任一项所述的方法,其中第二产品形式主要为未再结晶的,或至少60%未再结晶的,或至少70%未再结晶的,或至少80%未再结晶的,或至少90%未再结晶的,或至少95%未再结晶的。
96.条项21.根据前述条项中任一项所述的方法,其中所述冷成型为拉伸成型。
97.x.其它
98.在以下描述中部分阐述此新技术的这些和其它方面、优点和新颖特征,且本领域的技术人员在检查以下描述和附图后将变得显而易见,或可以通过实践本公开所提供的技术的一个或多个实施例而习得。
99.附图构成本说明书的一部分并包括本公开的示意性实施方案,并且示意了其各种目的和特征。另外,附图中示出的任何测量结果、规格等旨在示意而非限制。因此,本文公开的具体结构和功能细节不应被解释为限制性的,而仅仅作为用于教导本领域的技术人员以各种方式采用本发明的代表性基础。
100.在已经公开的那些益处和改进当中,根据结合附图进行的以下描述,本发明的其他目的和优点将变得显而易见。在本文中公开了本发明的详细实施例;然而,应当理解,所公开的实施例仅仅说明可以通过各种形式体现的本发明。另外,连同本发明的各种实施方案一起给出的每一个实例均旨在示意而非限制。
101.在通篇说明书和权利要求书中,除非上下文另有明确规定,否则以下术语采取本文明确相关的含义。如本文所用,短语“在一个实施例中”和“在一些实施例中”不一定指相同实施例(虽然它们可以是)。另外,如本文所用,短语“在另一个实施例中”和“在一些其它实施例中”不一定指不同实施例(虽然它们可以是)。因此,可以容易地将本发明的各种实施例组合,而不偏离本发明的范围或精神。
102.此外,除非上下文另外明确规定,否则如本文所用,术语“或”是一种包括性的“或”运算符,且相当于术语“和/或”。除非上下文另外明确规定,否则术语“基于”不具有排他性且允许基于未描述的其它因素。此外,在本说明书全篇中,除非上下文另外明确规定,否则“一个”、“一种”和“所述”的含义包括复数指代物。除非上下文另外明确规定,否则“在...中”的含义包括“在...中”和“在...上”。
103.虽然已经描述了本发明的多个实施例,但应了解这些实施例仅具说明性且无限制性,且多种润饰对于所属领域的技术人员而言可为显而易见的。更进一步,除非上下文另外明确要求,否则各种步骤可以按任何期望的顺序进行,并且可以添加和/或消除任何适用的步骤。
附图说明
104.图1是说明用于生产未再结晶挤出产品的本发明方法的一个实施例的流程图。
105.图2a说明与铝合金组合物和挤出产品类型有关的图1的步骤(100)的额外实施例。
106.图2b说明与热处理实践有关的图1的步骤(100)的额外实施例。
107.图2c是说明加热(100)、冷却(200)和冷成型(300)步骤的周期,包括初始(100i
‑
300i)和最终(100f
‑
300f)周期的流程图。
108.图3说明与冷却速率有关的图1的步骤(200)的额外实施例。
109.图4a说明与变形和相关项目有关的图1的步骤(300)的额外实施例。
110.图4b说明与由方法所致的粒度分布有关的图1的额外实施例。
111.图5a说明与方法有关的任选的额外加工(400)。
112.图5b说明图5a的额外实施例。
113.图6a
‑
6b是展示实例1的典型产品的微观结构的显微照片。
114.图7是展示实例2的产品的微观结构的显微照片。
115.图8是展示实例3的产品的微观结构的显微照片。
116.图9a
‑
9f是展示实例4的产品的微观结构的显微照片。
117.图10是展示实例5的产品的微观结构的显微照片。
118.图11是展示实例7的产品的微观结构的显微照片。
119.图12是展示实例8的产品的微观结构的显微照片。
120.图13a
‑
13e是来自实例9的sem图像。
121.图13f是展示基于实例9的sem图像的晶粒度分布的图。
122.图13g
‑
13h是展示非发明(13g)和本发明(13h)材料内的粒子的显微照片。
123.图14是展示非本发明实践和各种本发明实践的粒度分布结果的图。
124.图15a
‑
15b是展示本发明微观结构(图15a)相对于非本发明微观结构(图15b)的光学显微照片。
具体实施方式
125.实例1
‑
常规挤出、冷成型和固溶热处理产生再结晶的产品
126.将2055型铝合金挤出为z形挤出物,产生未再结晶的铝
‑
锂挤出物。材料通过拉伸成型而冷成型为最终产品形状。然后对材料进行固溶热处理和冷水淬灭。最终材料再结晶,如图6所示。
127.实例2
‑
中间加工导致大量再结晶
128.鉴于常规加工(实例1)产生再结晶产品,开发了中间热处理实践以停止/限制未再结晶的挤出产品转变为再结晶的产品。具体来说,将2055型铝合金挤出为矩形条,产生未再结晶的铝
‑
锂挤出物。接着通过在炉中快速加热至720℉处理温度对矩形条进行热处理。材料在720℉处理温度(+/
‑
10℉)下保持1小时(当材料达到690℉的温度时开始均热时间)。接着通过将炉的温度改变到450℉来缓慢冷却材料。以50℉/小时的速率将材料从720℉处理温度冷却至450℉处理温度。材料在450℉处理温度(+/
‑
10℉)下保持4小时(当材料达到465℉的温度时开始均热时间)。接着从炉中移出材料并使其空气冷却。接着通过对材料进行单轴拉伸来对材料进行冷成型,以产生8%永久应变。接着对材料进行固溶热处理,且接着在
冷水中淬灭。尽管有中间热实践,但最终材料仍再结晶,如图7所示。
129.实例3
‑
回复退火导致大量再结晶
130.产生最终未再结晶的产品的额外努力围绕使用冷成型后回复退火。具体来说,将2055型铝合金挤出为矩形条,产生未再结晶的铝
‑
锂挤出物。矩形条接着根据实例2进行热处理,即在720℉和450℉下进行处理,且接着使其空气冷却。接着通过对材料进行单轴拉伸来对材料进行冷成型,以产生6%永久应变。接着通过加热至215℉(3小时),且接着加热至400℉(2小时),且接着加热至500℉(3小时),且接着加热至600℉(4小时)来对材料进行热处理。根据实例2,接着对材料进行固溶热处理,且接着在冷水中淬灭。最终材料也再结晶,如图8所示。
131.实例4
‑
额外回复退火导致大量再结晶
132.在实例3的努力的基础上,完成了额外回复退火测试。具体来说,根据实例3,制备2055型铝合金且在冷成型之前进行热处理。接着通过单轴应变来对材料进行冷成型,以产生7%拉伸。接着将此材料的各种样品快速加热至各种退火温度(525℉、575℉、675℉、725℉、775℉和875℉)。根据实例2,接着对材料进行固溶热处理,且接着在冷水中淬灭。所有最终材料均再结晶,如图9a
‑
9f中所示。
133.实例5
‑
无冷成型的回复退火导致大量再结晶
134.在实例5中,根据实例2制备2055型铝合金且进行热处理,除了将材料挤出为z形。此时,重复热处理循环三次(即,根据实例2,在720℃和450℃下3次)。在此实例5中不采用冷成型操作。替代地,在三次热循环操作之后,根据实例2,材料经固溶热处理且接着在冷水中淬灭。尽管未接受冷成型,但最终材料仍再结晶,如图10所示。
135.实例6
‑
高温热处理产生未再结晶的产品
136.在实例6中,将2055型铝合金挤出为矩形条,产生未再结晶的铝
‑
锂挤出物。接着通过在炉中快速加热至945℉处理温度对矩形条进行热处理。材料在945℉处理温度(+/
‑
10℉)下保持1小时(当材料达到935℉的温度时开始均热时间)。均热结束后,从炉中移出材料并使其空气冷却至环境温度。此冷却步骤的冷却速率为约25℉/分钟。接着通过单轴应变对材料进行冷成型,以产生6%永久应变。根据实例2,接着对材料进行固溶热处理,且在冷水中淬灭。这一次,最终材料保持未再结晶。
137.实例7
‑
多个高温和多个应变操作产生未再结晶的产品
138.为了测试此过程的稳健性,对未再结晶的2055挤出产品执行与实例6相同的方法,但在945℉下进行4个热处理循环且在每个热处理循环后进行4个对应的应变操作,每个应变操作对先前产品施加6%永久应变。在第4个应变操作之后,根据实例2,材料经固溶热处理且在冷水中淬灭。即使在四个应变操作之后,最终材料仍保持未再结晶,如图11所示,指示所述过程的稳健性。
139.实例8
‑
多个高温和多个应变操作产生未再结晶的产品
140.在实例8中,根据实例2对未再结晶的2055挤出产品进行热处理,即,在720℉和450℉下进行处理,且接着使其空气冷却。在此热处理之后,材料未经冷成型。替代地,根据实例6采用额外热处理循环,即,通过在炉中快速加热至945℉处理温度,在945℉处理温度(+/
‑
10℉)下保持1小时(当材料达到935℉的温度时开始均热时间),且接着从炉中移出材料并使其空气冷却至环境温度来处理。接着通过单轴应变对材料进行冷成型,以产生8%永久应
变。根据实例2,接着对材料进行固溶热处理,且在冷水中淬灭。再次,最终材料保持未再结晶,如图12中所示。
141.实例9
‑
晶粒度分析
142.根据微结构测定程序获得通过本发明方法制备的若干合金和通过非本发明方法制备的一种合金的sem。根据晶粒度计算机分析程序计算这些sem的晶粒度。sem提供于图13a
‑
13e中。如所示出,本发明合金全部实现小得多的晶粒。计算机化分析证实了这一点。如图13f中所示,非本发明合金实现比本发明合金大得多的晶粒。这也可在图13g
‑
13h中看出,所述图为展示非本发明(13g)和本发明(13h)材料内的粒子的显微照片。(附注:图13g使用10微米尺度;图13h使用5微米尺度)。
143.鉴于前述实例,且不受任何特定理论束缚,相信高温热处理实践与合理量的应变组合允许产生保留未再结晶的晶粒的冷成型铝
‑
锂挤出产品。实际上,最终产品一般含有大量未再结晶的晶粒,并且相对于处于挤出态条件下的起始产品。
144.因此,在一些实施例中,“再结晶的”冷成型产品为如下产品:基于上文收集的ebsd数据和sem实现面积分数为大晶粒(≥67.5微米(即,大于或等于67.5微米))的至少0.20%的微观结构(根据sem),且在所获得的样品中的任一个中。也就是说,即使样品中的一个实现这些标准,材料也被分类为再结晶。在一个实施例中,再结晶的冷成型产品实现面积分数为大晶粒的至少25%的微观结构。在另一实施例中,再结晶的冷成型产品实现面积分数为大晶粒的至少30%的微观结构。在另一实施例中,再结晶的冷成型产品实现面积分数为大晶粒的至少35%的微观结构。在另一实施例中,再结晶的冷成型产品实现面积分数为大晶粒的至少40%的微观结构。在另一实施例中,再结晶的冷成型产品实现面积分数为大晶粒的至少45%或更高的微观结构。
145.在一些实施例中,未再结晶的冷成型产品是超出“再结晶的”冷成型产品的以上定义的任何产品。在一个实施例中,未再结晶的冷成型产品还实现或替代地实现面积分数为≥57.5至67.4微米的粒度的晶粒的不大于0.2%的微观结构(根据sem和ebsd数据)。在另一实施例中,未再结晶的冷成型产品还实现或替代地实现面积分数为≥57.5至67.4微米的粒度的晶粒的不大于0.15%的微观结构。在另一实施例中,未再结晶的冷成型产品还实现或替代地实现面积分数为≥57.5至67.4微米的粒度的晶粒的不大于0.10%的微观结构。
146.在一个实施例中,未再结晶的冷成型产品还实现或替代地实现面积分数为≥47.5至57.4微米的粒度的晶粒的不大于0.2%的微观结构。在另一实施例中,未再结晶的冷成型产品还实现或替代地实现面积分数为≥47.5至57.4微米的粒度的晶粒的不大于0.15%的微观结构。在另一实施例中,未再结晶的冷成型产品还实现或替代地实现面积分数为≥47.5至57.4微米的粒度的晶粒的不大于0.10%的微观结构。
147.在一个实施例中,未再结晶的冷成型产品还实现或替代地实现面积分数为≥37.5至47.4微米的粒度的晶粒的不大于0.22%的微观结构。在另一实施例中,未再结晶的冷成型产品还实现或替代地实现面积分数为≥37.5至47.4微米的粒度的晶粒的不大于0.17%的微观结构。在另一实施例中,未再结晶的冷成型产品还实现或替代地实现面积分数为≥37.5至47.4微米的粒度的晶粒的不大于0.12%的微观结构。
148.实例10
‑
粒度分析
149.从根据实例2(非本发明)和实例6
‑
8(本发明)的实践加工的材料获得各种样品。所
有样品经热处理,且接着根据或类似于这些实例进行空气淬灭。获得样品的反向散射sem图像,且接着对图像进行计算机分析以根据粒度计算机分析程序确定各种材料的粒子分布/粒度。
150.各种样品的粒度分布展示于图14中。如所示出,本发明实践(由实心条展示)通常具有高得多体积的小粒子,且分布更均匀。实例2的非本发明实践(由具有阴影线的条展示)实现大得多的粒子且分布更紧凑。图14的数据的特定d10、d50和d90值提供于以下表1中。
151.表1
‑
实例10的粒度数据
[0152][0153]
鉴于前述实例,且不受任何特定理论束缚,相信高温热处理实践与热处理后冷却速率以及适当量的冷却后应变组合产生具有小沉淀相粒子分布的独特未再结晶的产品。如上文章节iii中所解释,较高浓度的较小沉淀相粒子(例如,在章节iv中所描述的d10、d50和d90量内)可促进晶界固定,同时还减少冷成型操作期间存在的溶质的量。晶界固定可限制/防止再结晶。进一步具有相对较低量的纳米级沉淀相(例如<20纳米)可促进材料的加工。较大粒子还可充当用于再结晶的成核位点。因此,本文所述的方法试图限制/避免大规模和纳米级粒子的产生,同时具有适当量的小沉淀相粒子。因此,形状成型可在少量循环内完成以实现最终部件几何形状,且在未再结晶的条件下完成,接着进行适当的冷成型后操作(例如,固溶热处理、sht后拉伸以促进老化沉淀物的成核、老化(自然和/或人工)和机械加工,仅列举数例)。可因此实现大幅成本降低。
[0154]
虽然已详细描述了本公开内容的各种实施例,但显而易见,本领域技术人员将想到那些实施例的修改和适应。然而,应明确地理解,这些修改和适应在本公开内容的精神和范围内。