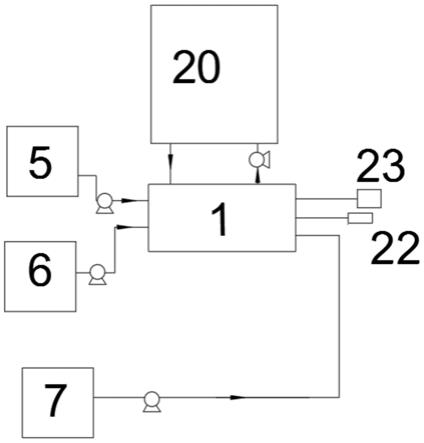
一种cof卷带精准蚀刻管控方法
技术领域
1.本发明涉及cof film生产领域,特别涉及一种cof卷带精准蚀刻管控方法、管控系统。
背景技术:2.柔性薄膜(flexiblefilm)经过许多工程移送的曝光、显影及蚀刻等阶段在薄膜表面形成预定线路图案,如cof(chip on film),覆晶薄膜。柔性薄膜由于容易弯曲的性质,一般以卷对卷(roll to roll)的方式从一侧轮上转出,再收卷至另外一侧轮。
3.在cof film生产工艺中,为了对金属形成微细线路,需要使用蚀刻液对cof film进行微蚀,微蚀是在cof film的电路形成中,选择性地只留下电路,而去除铜及铜合金的工艺。
4.在高价cu离子+酸+添加剂的蚀刻体系中,高价cu离子具有氧化性,可以将cu氧化成cu
+
,蚀刻反应为:
5.高价cu离子+cu
→
低价cu离子
6.随着蚀刻工艺的进行,副产物cu
+
不断增加,蚀刻能力随之下降,而cof蚀刻需要实现蚀刻精细管控,因此蚀刻液的各组分需要稳定在一定范围内才能使蚀刻实现精细管控(否则产品不符合生产要求),随着生产反应的进行,浓度逐渐偏离有效范围,当偏出目标范围后,原有蚀刻液不符合蚀刻要求。
7.现有的方式之一是当蚀刻液偏出目标范围后,将旧蚀刻液整体排走,重新加入新蚀刻液生产,排走的药液进行后续废液处理,虽然废液可以通过再生后再使用,但是,整个蚀刻工序长时期不能连续生产(连续生产只能在同一次蚀刻液时进行)。而重新药液配置,耗费大量药液,同时排走的药液后期处理也需浪费大量资源。
8.为了能够保持蚀刻能力,现有的另外一种方式如图1,蚀刻槽1上设置有酸添加口2、强氧化剂添加口3、添加剂加口4,生产前,先在蚀刻槽1中配好蚀刻液,生产时,当蚀刻液偏出目标范围后(根据高效色谱分析、滴定分析等化学分析方法分析浓度),直接在蚀刻液中定量补充酸液、强氧化剂及添加剂,对蚀刻液进行再生,使低价cu离子重新转变为高价cu离子,蚀刻液恢复正常蚀刻能力,现有通过添加双氧水等强氧化剂的方式使蚀刻液进行再生,反应为:
9.低价cu离子+酸+强氧化剂
→
高价cu离子+h2o
10.但是,这种添加的方式在生产时常常出现蚀刻线路形成如图2所示的倒梯(图2中,cu线路的底部11与cof的基体连接,顶部宽度h1与底部宽度h2),因此造成短路缺陷率高、线路不直等产品缺陷,即使增加分析和补充频率也无法解决该问题。
技术实现要素:11.针对上述缺陷,本发明提供一种cof卷带精准蚀刻管控方法,该方法通过在管控中加入电位分析法,解决了蚀刻过程中出现的蚀刻线路形成倒梯、线路不直的缺陷。
12.本发明发明人通过长期研究发现,产生上述缺陷的原因是在蚀刻液再生中,当强氧化剂的体积分数超过一定数值时,会使添加剂的浓度降低,从而无法使添加剂与生成的cu+反应生成保护膜,确保蚀刻速度均匀,导致线路蚀刻形成倒梯型,造成线路短路。而蚀刻液中强氧化剂如h2o2的浓度较低,通过hplc高效色谱分析、滴定分析等化学方法无法分析蚀刻液中强氧化剂的是否存在。
13.本发明发明人进一步研究发现,蚀刻液在无双氧水的情况下,电位处于低位,蚀刻液在双氧水存在情况下,电位处于高位。
14.本发明提供一种cof卷带精准蚀刻管控方法,该方法通过蚀刻液的电位分析控制强氧化剂的添加量。本发明通过监测蚀刻液的电位,判断出蚀刻液中是否存在强氧化剂,从而控制蚀刻液中cu+的浓度,确保蚀刻液的蚀刻效果,从而确保药液稳定,提高产品良率。
15.当蚀刻液电位处于高位时(蚀刻液中有强氧化剂存在),通过每隔一定时间化学分析添加剂的浓度,当相邻两次分析结果的绝对差值在目标范围外(如2%),添加铜粉至电位处于低位。
16.本发明人进一步研究还发现,当强氧化剂过量、添加剂与酸同时添加在蚀刻液时,一部分的添加剂与过量的强氧化剂发生了反应,影响添加剂的使用效果。
17.进一步地,本发明中,所述cof卷带精准蚀刻管控方法还包括强氧化剂单独添加到蚀刻槽的蚀刻液中,酸与添加剂按照配比形成蚀刻液,然后再添加至蚀刻槽中。
18.本发明还提供一种cof卷带精准蚀刻管控系统,包括蚀刻上单元、蚀刻下单元、添加剂原液单元、酸原液单元和强氧化剂原液单元,蚀刻上单元与蚀刻下单元通过管道连接,添加剂原液单元、酸原液单元和强氧化剂原液单元分别与蚀刻下单元连接,cof卷带精准蚀刻管控系统还分别设置有化学分析仪和电位测量仪,化学分析仪分析蚀刻下单元的蚀刻液中添加剂的成分,电位测量仪监测蚀刻下单元的蚀刻液的电位。
19.本发明还提供一种cof卷带精准蚀刻管控系统,包括蚀刻上单元、蚀刻下单元、回收单元、第一造液单元、添加剂原液单元、酸原液单元、第一送液单元、第二送液单元、第二造液单元和强氧化剂原液单元,蚀刻上单元与蚀刻下单元通过管道连接,回收单元分别与蚀刻下单元和第一造液单元通过管道连接,第一造液单元还分别与添加剂原液单元、酸原液单元和第一送液单元通过管道相连,第一送液单元还与蚀刻下单元通过管道相连,第二送液单元分别与第二造液单元和蚀刻下单元通过管道相连,第二造液单元还与强氧化剂原液单元相连,cof卷带精准蚀刻管控系统还分别设置有用于检测蚀刻下单元中的蚀刻液添加剂浓度的化学分析仪和用于监测蚀刻下单元中的蚀刻液电位的电位测量仪。
20.本发明还提供一种cof卷带精准蚀刻管控系统,包括蚀刻上单元、蚀刻下单元、平衡单元、回收单元、第一造液单元、添加剂原液单元、酸原液单元、第一送液单元、第二送液单元、第二造液单元和强氧化剂原液单元,蚀刻上单元与蚀刻下单元通过管道连接,蚀刻下单元与平衡单元之间通过管道水平连通,平衡单元还与蚀刻上单元相连,回收单元分别与蚀刻下单元和第一造液单元通过管道连接,第一造液单元还分别与添加剂原液单元、酸原液单元和第一送液单元通过管道相连,第一送液单元还与蚀刻下单元通过管道相连,第二送液单元分别与第二造液单元和蚀刻下单元通过管道相连,第二造液单元还与强氧化剂原液单元相连,cof卷带精准蚀刻管控系统还分别设置有用于检测蚀刻下单元中的蚀刻液添加剂浓度的化学分析仪和用于监测蚀刻下单元中的蚀刻液电位的电位测量仪。
21.本发明大大减少了高成本的蚀刻添加剂的使用,控制了药液成本,同时减少了对环境的影响和废液处理的成本,本发明将溢出的药液进行回收,并在供给侧重新调整药液至蚀刻液里,通过定量补充消耗的hcl,cu2+和添加剂,在生产的同时给蚀刻液进行再生补充,从而实现对蚀刻液浓度的精细管控,确保铜线路的完美形状,达到蚀刻液稳定生产的目的。
22.本发明通过高效液相色谱对蚀刻液中添加剂含量进行分析,精准控制添加剂添加量,同时通过测量电位蚀刻液的电位,确保蚀刻液中不存在未反应的强氧化剂,杜绝了强氧化剂对添加剂的影响。
附图说明
23.图1是本发明背景技术蚀刻管控系统结构示意图;
24.图2是本发明背景技术cu线路截面图示意图
25.图3是本发明实施例1卷带精准蚀刻管控系统流程示意图;
26.图4是本发明实施例2cof卷带精准蚀刻管控系统流程示意图;
27.图5是本发明实施例3蚀刻液自主回收系统流程示意图;
28.图6是本发明蚀刻液不同浓度双氧水中添加剂随时间变化的趋势图。
具体实施方式
29.下面将结合附图对本发明作进一步说明。
30.在本发明的描述中,需要说明的是,术语“上”、“下”、“底”、“顶”、“长度方向”、“宽度方向”等指示的方位或位置关系为基于附图所示的方位或位置关系,或者是该发明产品使用时惯常摆放的方位或位置关系,仅是为了便于描述本发明和简化描述,而不是指示或暗示所指的装置或元件必须具有特定的方位、以特定的方位构造和操作,因此不能理解为对本发明的限制。此外,术语“第一”、“第二”、“第三”等仅用于区分描述,而不能理解为指示或暗示相对重要性。
31.在本发明的描述中,还需要说明的是,除非另有明确的规定和限定,术语“贴合”、“连接”应做广义理解,例如,“连接”可以是固定连接,也可以是可拆卸连接,或一体地连接;可以是机械连接,也可以是电连接;可以是直接相连,也可以通过中间媒介间接相连,可以是焊接,也可以是封装连接等,对于本领域的普通技术人员而言,可以具体情况理解上述术语在本发明中的具体含义。
32.一种cof卷带精准蚀刻管控方法,该方法通过蚀刻液的电位分析控制强氧化剂的添加量,通过监测蚀刻液的电位,判断出蚀刻液中是否存在强氧化剂。
33.本发明中,通过电位分析,可判断出蚀刻液中是否有双氧水,控制蚀刻液中cu+的浓度,确保蚀刻液的蚀刻效果确保药液稳定,提高产品良率。
34.进一步地,该cof卷带精准蚀刻管控方法还包括化学分析添加液的浓度,当蚀刻液电位处于高位时,每隔一定时间化学分析添加液的浓度,当相邻两次分析结果的绝对差值在目标范围外,添加铜粉至电位处于低位。
35.本发明中,蚀刻生产时,使用高效液相色谱,每隔12小时重复分析一次蚀刻液的添加剂浓度,根据前后两次分析结果,判断蚀刻液中强氧化剂如h2o2浓度(双氧水量不同,添加
剂衰减速率不同,根据前期实验得到的不同浓度双氧水中添加剂随时间变化的趋势图
‑
如图6,反推h2o2的浓度),两次结果偏差在
±
2%,在误差范围内,不进行任何操作,若超过,则反推h2o2浓度,通过添加铜粉的方式将强氧化剂如双氧水降至管控范围以内。
36.本发明中,电位测试测试原理如下:
37.能斯特方程:e=e0+(0.059/n)log([cu2+]/[cu+])
[0038]
e:是特定浓度下的电位
[0039]
e0:标准电位
[0040]
n:得失电子数
[0041]
[cu2+]:二价铜离子浓度
[0042]
[cu+]:一价铜离子浓度
[0043]
进一步地,为预防强氧化剂与一部分添加剂反应,cof卷带精准蚀刻管控方法还包括强氧化剂单独添加到蚀刻槽的蚀刻液中,酸与添加剂按照配比形成蚀刻液后加入蚀刻槽中。
[0044]
基于上述的cof卷带精准蚀刻管控方法,下面的实施例1
‑
3提供一种卷带精准蚀刻管控系统。
[0045]
实施例1
[0046]
参考图3,图3为一种cof卷带精准蚀刻管控系统示意图。
[0047]
如图3,一种cof卷带精准蚀刻管控系统,包括蚀刻上单元20、蚀刻下单元1、添加剂原液单元5、酸原液单元6和强氧化剂原液单元7,蚀刻上单元20与蚀刻下单元1通过管道连接,添加剂原液单元5、酸原液单元6和强氧化剂原液单元7分别与蚀刻下单元1连接。
[0048]
本发明中,蚀刻下单元1接收从蚀刻上单元20蚀刻后的蚀刻液(蚀刻液在与cof蚀刻反应后流入蚀刻上单元20底部并立即从蚀刻上单元20底部的出口流出),防止了蚀刻上单元20中由于蚀刻液的积液而导致cof的过度蚀刻而造成的产品质量缺陷。
[0049]
本发明中,cof卷带精准蚀刻管控系统还分别设置有高效液相色谱仪22和电位测量仪23,高效液相色谱仪22分析蚀刻下单元1的蚀刻液中的成分,电位测量仪23测量蚀刻下单元1的蚀刻液的电位。
[0050]
将本实施例的cof卷带精准蚀刻管控系统用于cof蚀刻生产,并对蚀刻后的产品的cu线路的顶部宽度h1与底部宽度h2进行检测,检测结果见下表一。
[0051]
对比实施例1
[0052]
本实施例1与实施例1相比,除cof卷带精准蚀刻管控系统不含有电位测量仪23外,其余均相同,也就是说,本实施例在进行cof蚀刻生产时,仅没有进行电位检测,无法根据电位进行相应调整,而关于蚀刻的生产参数及工艺条件等,与实施例1完全相同。对蚀刻后的产品的cu线路的顶部宽度h1与底部宽度h2进行检测,检测结果见下表一。
[0053]
表一cu线路h2
‑
h1的差值
[0054][0055][0056]
实施例2
[0057]
参考图4,图4为一种cof卷带精准蚀刻管控系统示意图。
[0058]
如图4,一种cof卷带精准蚀刻管控系统,包括蚀刻上单元20、蚀刻下单元1、回收单元2、第一造液单元3、添加剂原液单元5、酸原液单元6、第一送液单元10、第二送液单元9、第二造液单元8和强氧化剂原液单元7,蚀刻上单元20与蚀刻下单元1通过管道连接,回收单元2分别与蚀刻下单元1和第一造液单元3通过管道连接,第一造液单元3还分别添加剂原液单元5、酸原液单元6和第一送液单元10通过管道相连,第一送液单元10还与蚀刻下单元1通过管道相连,第二送液单元9分别与第二造液单元8和蚀刻下单元1通过管道相连,第二造液单元8还与强氧化剂原液单元7相连。
[0059]
本发明中,cof卷带精准蚀刻管控系统还分别设置有高效液相色谱仪22和电位测量仪23,高效液相色谱仪22分析蚀刻下单元1的蚀刻液中的成分,电位测量仪23测量蚀刻下单元1的蚀刻液的电位。
[0060]
本发明中,蚀刻下单元1接收从蚀刻上单元20蚀刻后的蚀刻液(蚀刻液在与cof蚀刻反应后流入蚀刻上单元20底部并立即从蚀刻上单元20底部的出口流出),防止了蚀刻上
单元20中由于蚀刻液的积液而导致cof的过度蚀刻而造成的产品质量缺陷。
[0061]
本发明中,回收单元2接收蚀刻下单元1溢流出的蚀刻液并将该蚀刻液经管道送到第一造液单元3,回收单元2的设置是由于生产过程中随着生产的不断进行,补充液(即补充添加的氧化液、酸、添加剂)的量有可能大于实际消耗的量,而蚀刻下单元1中的液体将逐渐增多,不利于精确管控。通过回收单元2的设置,保证了蚀刻上单元20中蚀刻液量的稳定。
[0062]
本发明中,第一造液单元3接收从回收单元2而来的蚀刻液,并根据从蚀刻下单元1取样分析的结果经定量泵从添加剂原液单元5、酸原液单元6中接收添加剂和酸,混合后将混合后的液体经泵送到第一送液单元10,第一送液单元10再送到蚀刻下单元1中。
[0063]
本发明中,第二造液单元8将从强氧化剂原液单元7而来的市售原液浓缩或稀释到符合蚀刻液正常生产要求的浓度,浓缩或稀释的方法是现有的,在此不做特别的限定。第二造液单元8造好的符合蚀刻液正常生产要求的浓度的氧化液通过泵送到第二送液单元9,第二送液单元9再根据取样分析的结果通过定量泵补充氧化液量到蚀刻下单元1中。
[0064]
本发明中,氧化液直接添加到蚀刻下单元1中,而酸、添加剂先通过第一造液单元3与从回收单元2的蚀刻液先混合,混合后在经第一送液单元10添加到蚀刻下单元1中,一方面是因为同时添加会增加管控的难度,另一方面是防止强氧化剂与酸、添加剂反应,从而影响蚀刻液的再生。
[0065]
蚀刻生产时,蚀刻液从蚀刻下单元1送到蚀刻上单元20内腔的喷淋管并经安装在喷淋管上的喷头喷到经过蚀刻上单元20内腔的cof上,在cof经过蚀刻上单元20时对cof进行蚀刻,蚀刻后的液体流到蚀刻上单元20的底部并经出口流入蚀刻下单元1进入蚀刻液自主回收系统再生回到蚀刻下单元1后重新送入蚀刻上单元20蚀刻,周而复始,连续稳定生产。
[0066]
实施例3
[0067]
参考图5,图5为另一种cof卷带精准蚀刻管控系统示意图。
[0068]
如图5,一种cof卷带精准蚀刻管控系统,包括蚀刻上单元20、蚀刻下单元1、平衡单元21、回收单元2、第一造液单元3、添加剂原液单元5、酸原液单元6、第一送液单元10、第二送液单元9、第二造液单元8和强氧化剂原液单元7,蚀刻上单元20与蚀刻下单元1通过管道连接,蚀刻下单元1与平衡单元21之间通过管道水平连通,平衡单元21还与蚀刻上单元20单元相连,回收单元2分别与蚀刻下单元1和第一造液单元3通过管道连接,第一造液单元3还分别添加剂原液单元5、酸原液单元6和第一送液单元10通过管道相连,第一送液单元10还与蚀刻下单元1通过管道相连,第二送液单元9分别与第二造液单元8和蚀刻下单元1通过管道相连,第二造液单元8还与强氧化剂原液单元7相连。
[0069]
本发明中,cof卷带精准蚀刻管控系统还分别设置有高效液相色谱仪22和电位测量仪23,高效液相色谱仪22分析蚀刻下单元1的蚀刻液中的成分,电位测量仪23测量蚀刻下单元1的蚀刻液的电位。
[0070]
本发明中,蚀刻下单元1接收从蚀刻上单元20蚀刻后的蚀刻液(蚀刻液在与cof蚀刻反应后流入蚀刻上单元20底部并立即从蚀刻上单元20底部的出口流出),防止了蚀刻上单元20中由于蚀刻液的积液而导致cof的过度蚀刻而造成的产品质量缺陷。
[0071]
本发明中,回收单元2接收蚀刻下单元1溢流出的蚀刻液并将该蚀刻液经管道送到第一造液单元3,回收单元2的设置是由于生产过程中随着生产的不断进行,补充液(即补充
添加的氧化液、酸、添加剂)的量有可能大于实际消耗的量,而蚀刻下单元1中的液体将逐渐增多,不利于精确管控。通过回收单元2的设置,保证了蚀刻上单元20中蚀刻液量的稳定。
[0072]
本发明中,第一造液单元3接收从回收单元2而来的蚀刻液,并根据从蚀刻下单元1取样分析的结果经定量泵从添加剂原液单元5、酸原液单元6中接收添加剂和酸,混合后将混合后的液体经泵送到第一送液单元10,第一送液单元10再送到蚀刻下单元1中。
[0073]
本发明中,第二造液单元8将从强氧化剂原液单元7而来的市售原液浓缩或稀释到符合蚀刻液正常生产要求的浓度,浓缩或稀释的方法是现有的,在此不做特别的限定。第二造液单元8造好的符合蚀刻液正常生产要求的浓度的氧化液通过泵送到第二送液单元9,第二送液单元9再根据从取样分析的结果通过定量泵补充氧化液量到蚀刻下单元1中。
[0074]
本发明中,氧化液直接添加到蚀刻下单元1中,而酸、第一添加剂、第二添加剂先通过第一造液单元3与从回收单元2的蚀刻液先混合,混合后在经第一送液单元10添加到蚀刻下单元1中,一方面是因为同时添加会增加管控的难度,另一方面是防止强氧化剂与酸、第一添加剂、第二添加剂反应,从而影响蚀刻液的再生。
[0075]
本发明中,平衡单元21的设置使得经蚀刻的原蚀刻液中的大部分先进入回收单元2进行再生,补充的氧化液先在蚀刻下单元1中与补充了添加剂和酸的蚀刻液混合,从而使得从平衡单元21中送入蚀刻上单元20进入蚀刻的含补充液的液体混合更均匀,提高cof蚀刻制成能力,形成铜线路的完美形状。
[0076]
蚀刻生产时,蚀刻液从平衡单元21送到蚀刻上单元20内腔的喷淋管并经安装在喷淋管上的喷头喷到经过蚀刻上单元20内腔的cof上,在cof经过蚀刻上单元20时对cof进行蚀刻,蚀刻后的液体流到蚀刻上单元20的底部并经出口流入蚀刻下单元1进入蚀刻液自主回收系统再生回到蚀刻下单元1,然后蚀刻下单元1流入平衡单元21后重新送入蚀刻上单元20蚀刻,周而复始,连续稳定生产。