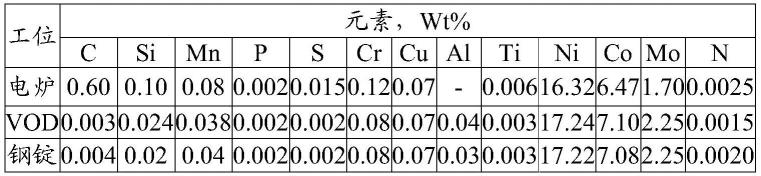
1.本发明属于金属材料技术领域,尤其涉及一种中间合金及其制备方法和应用。
背景技术:2.18ni马氏体时效钢是以无碳或超低碳fe-ni马氏体为基体,经过时效处理使金属间化合物沉淀硬化的一种超高强度钢,具有较高的强度和硬度(超高抗拉强度,表面硬度50~54hrc),兼具良好的韧性和塑性,是制造航空航天和工业装备的一种关键材料,在航空、航天、精密模具等工业领域获得了广泛应用,目前在国内外广泛用作制造火箭发动机壳体、导弹壳体、铀同位素离心分离机高速转筒等高精密承重零件的材料。目前,一般采用真空感应-真空自耗-锻造工艺进行制备,选取纯铁、ni板、j-co、j-mo、j-al、海绵钛为原料,但因真空感应炉吨位小,双真空冶炼成分控制命中率低,成本高,交货周期长。
技术实现要素:3.有鉴于此,本发明的目的在于提供一种中间合金及其制备方法和应用,本发明提供的中间合金具有较好的性能,用于制备18ni马氏体时效钢能够实现成分稳定控制。
4.本发明提供了一种中间合金,成分为:
5.≤0.03wt%的c;≤0.10wt%的mn;≤0.10wt%的si;≤0.05wt%的p;≤ 0.05wt%的s;≤0.15wt%的cr;≤0.10wt%的cu;≤0.05wt%的al;≤0.05wt%的ti;17~19wt%的ni;7~8wt%的co;2~3wt%的mo;≤0.0025wt%的n;余量为fe。
6.优选的,成分为:
7.0.001~0.008wt%的c;
8.0.01~0.05wt%的mn;
9.0.01~0.05wt%的si;
10.0.001~0.004wt%的p;
11.0.001~0.004wt%的s;
12.0.02~0.10wt%的cr;
13.0.02~0.08wt%的cu;
14.0.01~0.04wt%的al;
15.0.001~0.003wt%的ti;
16.17.5~18.5wt%的ni;
17.7.2~7.8wt%的co;
18.2.2~2.8wt%的mo;
19.≤0.0025wt%的n;
20.余量为fe。
21.本发明提供了一种上述技术方案所述的中间合金的制备方法,包括:
22.将合金原料配料后依次进行电弧炉粗炼、vod精炼和浇注,得到中间合金。
23.优选的,所述合金原料配料的成分包括:
24.c:0.08wt%;
25.cu:≤0.05wt%。
26.优选的,所述电弧炉粗炼过程中的终点碳含量为0.40~0.50wt%。
27.优选的,所述电弧炉粗炼过程中的出钢温度为1630~1680℃。
28.优选的,所述vod精炼过程中的出钢温度为1650~1680℃。
29.优选的,所述浇注的温度为1520~1540℃。
30.本发明提供了一种钢材的制备方法,包括:
31.采用中间合金在真空感应炉中熔炼制备得到钢材;
32.所述中间合金为上述技术方案所述的中间合金,或上述技术方案所述的方法制备得到的中间合金。
33.优选的,所述钢材为18ni马氏体时效钢。
34.为了降低18ni马氏体时效钢的生产成本、提高工业化生产效率,本发明通过精选普通废钢及合金,通过电弧炉-vod工艺生产合适成分的中间合金作为真空感应炉原料,降低真空感应炉的原料要求,提高产品成分命中率,实现成分稳定控制,能够实现经济效益约300万元以上。
具体实施方式
35.下面将对本发明实施例中的技术方案进行清楚、完整地描述,显然,所描述的实施例仅仅是本发明一部分实施例,而不是全部的实施例。基于本发明中的实施例,本领域普通技术人员在没有做出创造性劳动前提下所获得的所有其他实施例,都属于本发明保护的范围。
36.本发明提供了一种中间合金,成分为:
37.≤0.03wt%的c;≤0.10wt%的mn;≤0.10wt%的si;≤0.05wt%的p;≤ 0.05wt%的s;≤0.15wt%的cr;≤0.10wt%的cu;≤0.05wt%的al;≤0.05wt%的ti;17~19wt%的ni;7~8wt%的co;2~3wt%的mo;≤0.0025wt%的n;余量为fe。
38.在本发明中,所述中间合金的成分优选为:
39.0.001~0.008wt%的c;
40.0.01~0.05wt%的mn;
41.0.01~0.05wt%的si;
42.0.001~0.004wt%的p;
43.0.001~0.004wt%的s;
44.0.02~0.10wt%的cr;
45.0.02~0.08wt%的cu;
46.0.01~0.04wt%的al;
47.0.001~0.003wt%的ti;
48.17.5~18.5wt%的ni;
49.7.2~7.8wt%的co;
50.2.2~2.8wt%的mo;
51.≤0.0025wt%的n;
52.余量为fe。
53.在本发明中,所述c的质量含量优选为0.001~0.006%,更优选为0.002%;所述mn的质量含量优选为0.01~0.05%,更优选为0.02~0.03%;所述si的质量含量优选为0.01~0.05%,更优选为0.02~0.03%;所述p的质量含量优选为 0.001~0.004,更优选为0.002~0.003%;所述s的质量含量优选为0.001~0.004%,更优选为0.002~0.003%;所述cr的质量含量优选为0.02~0.10%,更优选为 0.03~0.08%,最优选为0.05~0.06%;所述cu的质量含量优选为0.02~0.08%,更优选为0.03~0.06%,最优选为0.04~0.05%;所述al的质量含量优选为 0.01~0.04%,更优选为0.02~0.03%;所述ti的质量含量优选为0.001~0.003%,更优选为0.001~0.002%;所述ni的质量含量优选为17.5~18.5%,更优选为 17.5~18%;所述co的质量含量优选为7.2~7.8%,更优选为7.2~7.6%,最优选为7.2~7.4%;所述mo的质量含量优选为2.2~2.8%,更优选为2.4~2.8%,最优选为2.6~2.8%。
54.本发明提供了一种上述技术方案所述的中间合金的制备方法,包括:
55.将合金原料配料后依次进行电弧炉粗炼、vod精炼和浇注,得到中间合金(钢锭)。
56.本发明对所述合金原料没有特殊的限制,采用本领域人员熟知的合金原料进行合金元素配料即可。在本发明中,所述合金原料优选包括:
57.双相不锈钢或铬镍不锈返回、cr不锈切头废钢、crmo钢切头、高cr钢、 fe-mo。
58.在本发明中,所述合金原料配料的成分优选包括:
59.c:≤0.08wt%;
60.cu:≤0.05wt%。
61.在本发明中,所述合金原料配料后的成分优选为:
62.≤0.03wt%的c;
63.≤0.10wt%的mn;
64.≤0.10wt%的si;
65.≤0.05wt%的p;
66.≤0.05wt%的s;
67.≤0.15wt%的cr;
68.≤0.05wt%的cu;
69.≤0.05wt%的al;
70.≤0.05wt%的ti;
71.17~19wt%的ni;
72.7~8wt%的co;
73.2~3wt%的mo;
74.余量为fe。
75.在本发明中,所述c的质量含量优选为0.0005~0.0025%,更优选为0.002%;所述mn的质量含量优选为0.01~0.05%,更优选为0.02~0.03%;所述si的质量含量优选为0.01~0.05%,更优选为0.02~0.03%;所述p的质量含量优选为0.001~0.004,更优选为0.002~0.003%;所述s的质量含量优选为0.001~0.004%,更优选为0.002~0.003%;所
述cr的质量含量优选为0.02~0.10%,更优选为 0.03~0.08%,最优选为0.05~0.06%;所述cu的质量含量优选为0.02~0.08%,更优选为0.03~0.06%,最优选为0.04~0.05%;所述al的质量含量优选为 0.01~0.04%,更优选为0.02~0.03%;所述ti的质量含量优选为0.01~0.03%,更优选为0.01~0.02%;所述ni的质量含量优选为17.5~18.5%,更优选为17.5~18%;所述co的质量含量优选为7.2~7.8%,更优选为7.2~7.6%,最优选为7.2~7.4%;所述mo的质量含量优选为2.2~2.8%,更优选为2.4~2.8%,最优选为2.6~2.8%。
76.在本发明中,所述电弧炉粗炼过程中的温度优选≥1580℃,更优选为 1610~1630℃,更优选为1615~1625℃,最优选为1620℃。
77.在本发明中,所述电弧炉粗炼过程中优选吹氧脱碳,优选终点碳含量控制在0.40~0.50%,更优选为0.45%。
78.在本发明中,所述电弧炉粗炼过程中优选成分满足下述条件出钢:
79.c:0.5~0.8wt%;
80.p:≤0.001wt%;
81.ti:≤0.01wt%。
82.在本发明中,所述电弧炉粗炼过程中的出钢的温度优选为1630~1680℃,更优选为1640~1670℃,最优选为1650~1660℃;优选扒渣全部出钢。
83.在本发明中,所述电弧炉粗炼过程中优选包括:精选钢铁料,石墨电极块、纯铁、加工余料等;和/或电炉生产前炉衬清洁,设备状态良好。
84.在本发明中,所述电弧炉粗炼的方法优选包括:
85.装料前加石灰600~100kg,通电快速熔化炉料,时间≤90min;
86.熔清取样全分析(包括五害元素),低温去p、si、mn;
87.温度≥1580℃开始吹氧脱碳,终点c控制在0.40~0.50wt%、温度 1650~1680℃出钢。
88.在本发明中,所述石灰的加入量优选为700~900kg,更优选为800kg;所述通电快速熔化炉料的时间优选为60~75min;所述吹氧脱碳的温度优选为 1580~1595℃。
89.在本发明中,所述vod(真空吹氧脱碳)精炼过程中的入罐温度优选≥ 1600℃,更优选为1620~1650℃,最优选为1630~1640℃。
90.在本发明中,所述vod精炼过程中优选控制:
91.si+c的质量含量≤1.0%。
92.在本发明中,所述vod精炼过程中优选脱碳终点c质量含量控制为≤ 0.001%。在本发明中,所述vod精炼过程中优选还原脱s控制为:s的质量含量≤0.002wt%。
93.在本发明中,所述vod精炼过程中优选出钢前分析所有元素成分,成分满足预获得合金成分后再出钢。
94.在本发明中,所述vod精炼过程中的出钢温度优选为1650~1680℃,更优选为1660~1670℃,最优选为1665℃。
95.在本发明中,所述vod精炼的方法优选包括:
96.电炉粗炼钢水进入vod后测温,取样,测量钢包净空自由空间≥800mm,调整氩气流量和初始氧枪高度;
97.冶炼抽真空到25kpa~35kpa开始吹氧脱碳,控制吹氧强度,控制过吹氧量50~200nm3,结束吹氧脱c后,在极限真空度保持时间≥15min,控制终点c ≤0.003%;
98.加还原渣料进行脱s,控制s≤0.003%,出钢温度控制在1530~1550℃。
99.在本发明中,所述氩气流量优选为75~92l/min;所述初始氧枪高度优选为0.8~1.2m;所述抽真空的真空度优选为22~30kpa;所述吹氧强度优选为 500~600nm/h;所述过吹氧量优选为100~150nm3,最优选为120nm3;所述极限真空度的保持时间优选为18~30min。
100.在本发明中,所述浇注过程中优选定型≤3.5t。
101.在本发明中,所述浇注过程中优选采用保护浇注,带模缓冷。
102.在本发明中,所述浇注的方法优选包括:
103.准备足够数量专用钢锭模具,采用下注工艺浇注,浇注温度控制 1520~1540℃,浇注时间控制在250~480秒;钢锭缓冷时间≥90min,进行脱模自然冷却。
104.在本发明中,所述钢锭模具优选为3.5t钢锭模具,所述钢锭模具优选为10~15支。在本发明中,所述浇注温度优选为1530℃;所述浇注时间优选为 300~450秒,更优选为350~400秒,最优选为360~380秒;所述钢锭缓冷的时间优选为100~130min。
105.在本发明中,所述得到浇注完成后优选还包括:
106.钢锭进行精整。
107.在本发明中,所述精整的方法优选包括:
108.冷却后脱模,表面修磨清理,检查无缺陷后使用。
109.本发明提供了一种钢材的制备方法,包括:
110.采用中间合金在真空感应炉中熔炼制备得到钢材。
111.在本发明中,所述中间合金为上述技术方案所述的中间合金,或上述技术方案所述的方法制备得到的中间合金。
112.在本发明中,所述钢材优选为18ni马氏体时效钢。
113.在本发明中,所述钢材的制备方法优选包括:
114.将所述中间合金依次进行真空感应炉熔炼、真空自耗炉熔炼、锻造和热处理,得到钢材。
115.本发明通过设计合适的中间合金原料成分,采用电弧炉-vod工艺生产,合适成分的中间合金作为真空感应炉原料,降低真空感应炉的原料要求,提高产品成分命中率,实现产品成分的稳定控制要求。
116.实施例1
117.电炉生产:选用精选钢铁料、石墨电极块、纯铁、加工余料,总重量43t,配c0.85wt%;装料前加石灰700kg,通电快速熔化炉料,通电时间62min;熔清取样,低温去p,si,mn;测温温度1584℃开始吹氧脱碳;终点c控制在0.60%、温度1663℃出钢到vod。
118.vod生产:电炉粗炼钢水进入vod后测温,取样,测量自由空间850mm,调整氩气流量80l/min和初始氧枪高度1.0m;冶炼抽真空到27kpa开始吹氧脱碳;控制吹氧强度550nm/h,过吹氧量120nm3,结束吹氧脱c后,在极限真空度保持时间21min,加还原渣料进行脱s,出钢温度控制在1539℃。
119.铸锭生产:准备专用3.5t钢锭模11支,采用下注工艺浇注,浇注温度1535℃,浇注
时间324秒。钢锭缓冷时间120min,进行脱模自然冷却,转精整处理,得到中间合金。
120.对本发明实施例1制备的中间合金进行成分检测,取样分析方法执行 gb/t222,分析仪器分别为光谱分析仪(arl3460)、碳硫分析仪(cs844)、气体分析仪(tc600)进行检测,检测结果如下:
[0121][0122]
实施例2
[0123]
电炉生产:选用精选钢铁料、石墨电极块、纯铁、加工余料,总重量45.5t,配c0.72%;装料前加石灰800kg,通电快速熔化炉料,通电时间75min;熔清取样,低温去p,si,mn;测温温度1595℃开始吹氧脱碳,终点c控制在0.58wt%,温度1645℃出钢到vod。
[0124]
vod生产:电炉粗炼钢水进入vod后测温,取样,测量自由空间820mm,调整氩气流量92l/min和初始氧枪高度0.85m;冶炼抽真空到25kpa开始吹氧脱碳。控制吹氧强度530nm/h,过吹氧量150nm3,结束吹氧脱c后,在极限真空度保持时间18min,加还原渣料进行脱s,出钢温度控制在1534℃。
[0125]
铸锭生产:准备专用3.5t钢锭模11支,采用下注工艺浇注,浇注温度 1530℃,浇注时间357秒;钢锭缓冷时间120min,进行脱模自然冷却,转精整处理,得到中间合金。
[0126]
按照实施例1的方法对本发明实施例2制备的中间合金进行成分检测,检测结果如下:
[0127][0128]
实施例3
[0129]
电炉生产:选用精选钢铁料、石墨电极块、纯铁、加工余料,总重量41.8t,配c0.85%;装料前加石灰760kg,通电快速熔化炉料,通电时间65min;熔清取样,低温去p,si,mn;测温温度1584℃开始吹氧脱碳,终点c控制在0.49wt%,温度1655℃出钢到vod。
[0130]
vod生产:电炉粗炼钢水进入vod后测温,取样,测量自由空间950mm,调整氩气流量85l/min和初始氧枪高度0.95m;冶炼抽真空到22kpa开始吹氧脱碳;控制吹氧强度510nm/h,过吹氧量110nm3;结束吹氧脱c后,在极限真空度保持时间19min,加还原渣料进行脱s,出钢温度控制在1540℃。
[0131]
铸锭生产:准备专用3.5t钢锭模11支,采用下注工艺浇注,浇注温度 1536℃,浇注时间353秒;钢锭缓冷时间120min,进行脱模自然冷却,转精整处理,得到中间合金。
[0132]
按照实施例1的方法对本发明实施例3制备的中间合金进行成分检测,检测结果如下:
[0133][0134]
性能检测
[0135]
按照下述方法对本发明实施例制备的中间合金进行性能检测:
[0136]
试验项目检验方法室温拉伸gb/t228.1冲击gb/t229洛氏硬度gb/t230.1室温断裂韧性gb/t4161低倍组织gb/t226非金属夹杂物gb/t10561
[0137]
实施例1制备的中间合金检测结果如下:
[0138]
项目单位测试值要求值rp0.2mpa1374≥1200抗拉强度rmmpa1655≥1500断面收缩率z%61.5≥55冲击功,akvj102.290洛氏硬度hrc41.3≥35断后伸长率%15.5≥9.0
[0139]
项目单位测试值要求值a粗级0≤1.0a细级0≤1.5b粗级0.5≤1.5b细级1.0≤2.0c粗级0≤1.0c细级0≤1.5d粗级0≤1.0d细级0.5≤2.0ds级0.5≤1.0横酸浸合格/一般疏松级1.0≤2.5中心疏松级1.5≤2.5
[0140]
实施例2制备的中间合金检测结果如下:
[0141]
项目单位测试值要求值rp0.2mpa1410≥1200
抗拉强度rmmpa1639≥1500断面收缩率z%62.1≥55冲击功,akvj101.290洛氏硬度hrc42.3≥35断后伸长率%13.6≥9.0
[0142]
项目单位测试值要求值a粗级0≤1.0a细级0≤1.5b粗级1.0≤1.5b细级1.0≤2.0c粗级0≤1.0c细级0≤1.5d粗级0≤1.0d细级1.0≤2.0ds级0.5≤1.0横酸浸合格/一般疏松级1.0≤2.5中心疏松级2.0≤2.5
[0143]
实施例3制备的中间合金检测结果如下:
[0144]
项目单位测试值要求值rp0.2mpa1417≥1200抗拉强度rmmpa1681≥1500断面收缩率z%62.7≥55冲击功,akvj113.490洛氏硬度hrc42.3≥35断后伸长率%14.1≥9.0
[0145]
项目单位测试值要求值a粗级0≤1.0a细级0≤1.5b粗级1.0≤1.5b细级1.0≤2.0c粗级0≤1.0c细级0≤1.5d粗级0≤1.0d细级1.0≤2.0ds级0.5≤1.0横酸浸合格/一般疏松级1.0≤2.5
中心疏松级2.0≤2.5
[0146]
本发明通过设计合适的中间合金原料成分,采用电弧炉-vod工艺生产,合适成分的中间合金作为真空感应炉原料,降低真空感应炉的原料要求,提高产品成分命中率,实现产品成分的稳定控制要求。
[0147]
虽然已参考本发明的特定实施例描述并说明本发明,但是这些描述和说明并不限制本发明。所属领域的技术人员可清晰地理解,在不脱离如由所附权利要求书定义的本发明的真实精神和范围的情况下,可进行各种改变,以使特定情形、材料、物质组成、物质、方法或过程适宜于本技术的目标、精神和范围。所有此类修改都意图在此所附权利要求书的范围内。虽然已参考按特定次序执行的特定操作描述本文中所公开的方法,但应理解,可在不脱离本发明的教示的情况下组合、细分或重新排序这些操作以形成等效方法。因此,除非本文中特别指示,否则操作的次序和分组并非本技术的限制。