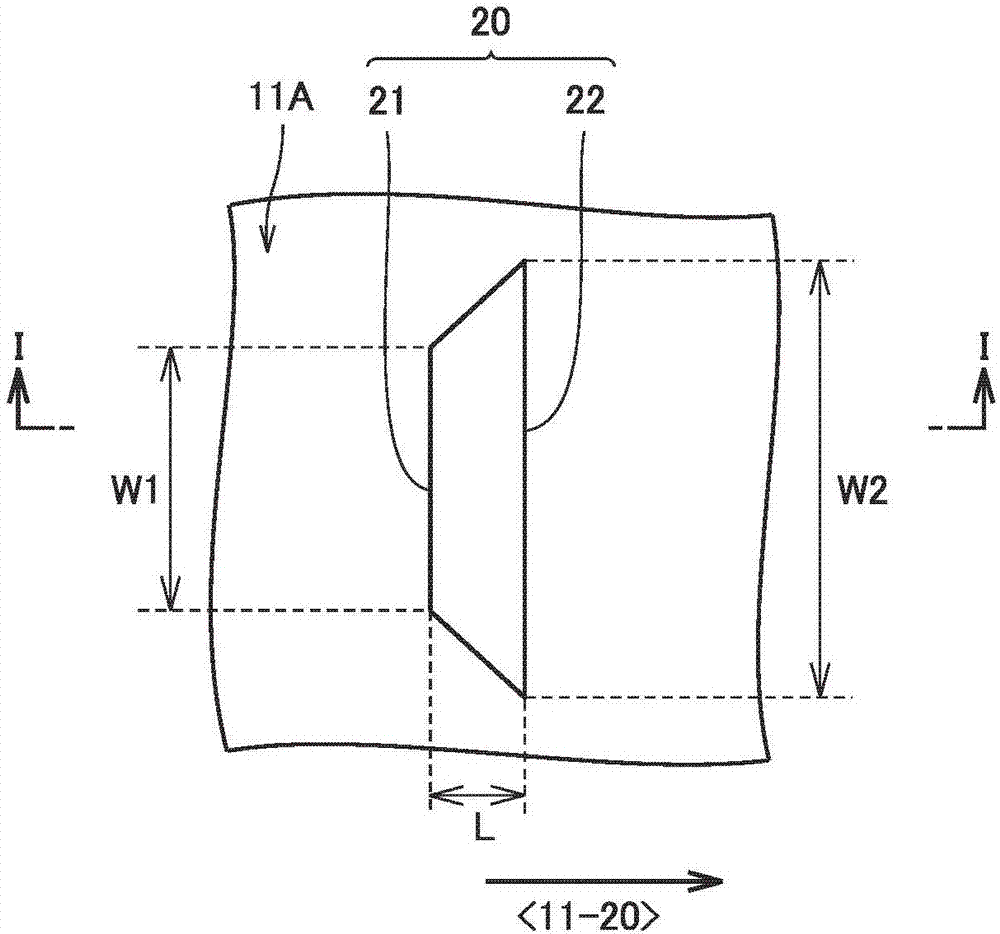
本公开涉及碳化硅外延基板的制造方法和碳化硅外延基板。
背景技术:
:日本特开2013-34007号公报(专利文献1)记载了碳化硅(sic)外延片,其具有在以0.4°至5°的偏角倾斜的sic单晶基板上生长的sic外延层,特征在于没有短台阶聚并。现有技术文献专利文献专利文献1:日本特开2013-34007号公报技术实现要素:发明要解决的技术问题本公开的目的是提供减少了梯形平面形状的缺陷(以下称为“梯形缺陷”)的碳化硅外延基板。解决技术问题的技术手段本公开一个方面的碳化硅外延基板的制造方法包括:准备碳化硅单晶基板的步骤;将所述碳化硅单晶基板放置在成膜装置的腔室内并降低所述腔室内的压力的步骤;将所述腔室内的温度升高到第一温度的步骤;将氢气引入到所述腔室内而调节所述腔室内的压力的步骤;将烃气体引入到所述腔室内的步骤;在保持所述腔室内的所述调节后的压力和所述氢气的流量并引入所述烃气体的状态下,将所述腔室内的温度升高到第二温度并将温度在所述第二温度下保持预定时间的基板改性步骤;和通过在保持所述第二温度的状态下将硅烷气体引入到所述腔室内而在所述碳化硅单晶基板上生长外延层的步骤。本公开一个方面的碳化硅外延基板包含具有1°以上且8°以下的偏角的碳化硅单晶基板、和在所述碳化硅单晶基板上形成的外延层。在所述外延层的表面中,作为梯形凹陷的梯形缺陷的缺陷密度为1个/cm2以下。当在俯视图中观察时,所述梯形缺陷各自包含与<11-20>方向相交的上底部和下底部。所述上底部的宽度为0.1μm以上且100μm以下。所述下底部的宽度为50μm以上且5000μm以下。所述上底部包含突起部。所述下底部包含多个台阶聚并。发明的效果根据以上说明,提供了梯形缺陷的缺陷密度降低的碳化硅外延基板。附图说明图1为显示本公开一个方面的碳化硅外延基板的构造的一个例子的示意局部剖视图。图2为显示梯形缺陷的一个例子的示意俯视图。图3为显示成膜装置的构造的一个例子的示意侧视图。图4为沿图3中的iv-iv线取的示意剖视图。图5为概略显示本公开一个方面的碳化硅外延基板的制造方法的流程图。图6为显示成膜装置内的温度控制和气体流量控制的一个例子的时序图。图7为显示图6的时序图的第一种变体的部分时序图。图8为显示图6的时序图的第二种变体的部分时序图。图9为显示梯形缺陷的另一个例子的示意俯视图。图10为沿图9中的x-x线取的示意剖视图。图11为沿图9中的xi-xi线取的示意剖视图。图12为图9中区域a的放大图。具体实施方式[本公开的实施方式的说明]首先,将列出并说明本公开的实施方式。在以下说明中,相同或相应的要素将以相同的参考符号标明,并且将不重复对其的相同说明。此外,关于本说明书中的结晶学表述,个别取向由[]表示,集合取向由<>表示,个别面由()表示,且集合面由{}表示。通常,结晶学上的负指数应该将“-”(线棒)放在数字上方来表示,但在本说明书中将负号放在数字之前来表示。另外,“俯视图”是指当从外延层的表面的法线方向观察时的视野。[1]本公开一个方面的碳化硅外延基板的制造方法包括:准备碳化硅单晶基板的步骤;将所述碳化硅单晶基板放置在成膜装置的腔室内并降低所述腔室内的压力的步骤;将所述腔室内的温度升高到第一温度的步骤;将氢气引入到所述腔室内而调节所述腔室内的压力的步骤;将烃气体引入到所述腔室内的步骤;在保持所述腔室内的所述调节后的压力和所述氢气的流量并引入所述烃气体的状态下,将所述腔室内的温度升高到第二温度并将温度在所述第二温度下保持预定时间的基板改性步骤;和通过在保持所述第二温度的状态下将硅烷气体引入到所述腔室内而在所述碳化硅单晶基板上生长外延层的步骤。根据本发明人的研究,梯形缺陷可能在碳化硅单晶基板与外延层之间的生长界面附近有起点,并随着外延层生长从该起点向外延层的表面延伸。以往,一般在即将进行外延生长之前在碳化硅单晶基板的主面上使用氢气进行蚀刻。这是基于清洁所述主面以抑制缺陷生成的想法。然而,本发明人认为,使用氢气的蚀刻不能充分抑制上述梯形缺陷的起点的生成,并且本发明人对代替常规蚀刻的加工条件进行了研究,最终完成了上述制造方法。因此,上述制造方法包括在碳化硅单晶基板上生长外延层的步骤之前的基板改性步骤。基板改性步骤使碳化硅单晶基板与烃气体在特定条件下接触。也就是说,在基板改性步骤中,通过将氢气引入到成膜装置的腔室内而调节压力以及引入烃气体、并在保持氢气的流量和腔室内的压力的状态下将温度升高到生长温度(第二温度),对碳化硅单晶基板的主面进行改性。根据这种制造方法,可以将外延层的表面中的梯形缺陷的缺陷密度控制到例如1个/cm2以下。[2]优选地,烃气体包括选自由甲烷气体、乙烷气体、丙烷气体、丁烷气体和乙炔气体构成的组中的一种或多种,因为在这些烃气体的单种气体或混合气体中可预期大的改性效果。[3]优选地,在所述引入步骤中的所述烃气体的流量为5sccm以上且30sccm以下。在此,流量的单位“sccm(标准立方厘米/分钟)”表示标准状态(0℃,101.3kpa)下的“ml/分钟”。[4]优选地,在所述调节步骤中的所述氢气的流量为50slm以上且200slm以下。在此,流量的单位“slm(标准升/分钟)”表示在上述标准状态下的“l/分钟”。[5]优选地,所述第一温度为1300℃以上且低于1500℃,并且所述第二温度为1500℃以上且1700℃以下。[6]优选地,在所述基板改性步骤中的所述腔室内的压力为5kpa以上且40kpa以下(50毫巴以上且400毫巴以下)。[7]本公开一个方面的碳化硅外延基板的制造方法包括:准备碳化硅单晶基板的步骤;将所述碳化硅单晶基板放置在成膜装置的腔室内并降低所述腔室内的压力的步骤;将所述腔室内的温度升高到1300℃以上且低于1500℃的第一温度的步骤;将流量为50slm以上且200slm以下的氢气引入到所述腔室内而将所述腔室内的压力调节到5kpa以上且40kpa以下的步骤;将流量为5sccm以上且30sccm以下的丙烷气体引入到所述腔室内的步骤;在保持所述腔室内的所述调节后的压力和所述氢气的流量并引入丙烷气体的状态下,将所述腔室内的温度升高到1500℃以上且1700℃以下的第二温度并将温度在所述第二温度下保持预定时间的基板改性步骤;和通过在保持所述第二温度的状态下将硅烷气体引入到所述腔室内而在所述碳化硅单晶基板上生长外延层的步骤。根据这种制造方法,能够减少梯形缺陷。本公开一个方面的碳化硅外延基板包含具有1°以上且8°以下的偏角的碳化硅单晶基板、和在所述碳化硅单晶基板上形成的外延层。在所述外延层的表面中,梯形缺陷的缺陷密度为1个/cm2以下。当在俯视图中观察时,所述梯形缺陷各自包含与<11-20>方向相交的上底部和下底部。所述上底部的宽度为0.1μm以上且100μm以下,所述下底部的宽度为50μm以上且5000μm以下。例如,通过使用上述[1]至[7]中的制造方法将梯形缺陷的缺陷密度控制到1个/cm2以下,可以改善使用所述碳化硅外延基板制造的半导体装置中的氧化膜的可靠性。在此,可以通过使用nomarski型光学显微镜(例如,由olympus公司制造的“mx-51”)在50倍至400倍的放大倍数下分析外延层的整个表面,并将检测出的梯形缺陷数量除以外延层的表面面积,来算出“梯形缺陷的缺陷密度”。需要说明的是,通常,在此所使用的整个表面不包括未被半导体装置利用的区域。在此,未被半导体装置利用的区域是指例如从基板的边缘起算3mm的区域。[8]此外,当从另一个观点来看时,上述碳化硅外延基板包含以下构造。即,碳化硅外延基板包含具有1°以上且8°以下的偏角的碳化硅单晶基板、和在所述碳化硅单晶基板上形成的外延层。在所述外延层的表面中,作为梯形凹陷的梯形缺陷的缺陷密度为1个/cm2以下。当在俯视图中观察时,所述梯形缺陷各自包含与<11-20>方向相交的上底部和下底部。所述上底部的宽度为0.1μm以上且100μm以下。所述下底部的宽度为50μm以上且5000μm以下。所述上底部包含突起部。所述下底部包含多个台阶聚并。[9]优选地,碳化硅单晶基板的主面为相对于{0001}面倾斜所述偏角的面。当碳化硅单晶基板的主面为相对于(0001)面或(000-1)面倾斜1°以上且8°以下的面时,可以获得不同多型体的混合少的外延层。[10]优选地,碳化硅单晶基板的直径为100mm以上,因为这可以有助于减少半导体装置的制造成本。[11]外延层的厚度可以为5μm以上且30μm以下。本公开一个方面的碳化硅外延基板包含具有相对于{0001}面倾斜1°以上且8°以下的主面并且直径为100mm以上的碳化硅单晶基板、和在所述碳化硅单晶基板上形成并且厚度为5μm以上且30μm以下的外延层。在所述外延层的表面中,梯形缺陷的缺陷密度为1个/cm2以下。当在俯视图中观察时,所述梯形缺陷各自包含与<11-20>方向相交的上底部和下底部。所述上底部的宽度为0.1μm以上且100μm以下,所述下底部的宽度为50μm以上且5000μm以下。[12]此外,当从另一个观点来看时,上述碳化硅外延基板包含以下构造。即,碳化硅外延基板包含具有相对于{0001}面倾斜1°以上且8°以下的主面并且直径为100mm以上的碳化硅单晶基板、和在所述碳化硅单晶基板上形成并且厚度为5μm以上且30μm以下的外延层。在所述外延层的表面中,作为梯形凹陷的梯形缺陷的缺陷密度为1个/cm2以下。当在俯视图中观察时,所述梯形缺陷各自包含与<11-20>方向相交的上底部和下底部。所述上底部的宽度为0.1μm以上且100μm以下。所述下底部的宽度为50μm以上且5000μm以下。所述上底部包含突起部。所述下底部包含多个台阶聚并。在使用本公开的碳化硅外延基板制造的半导体装置中,预期可改善氧化膜的可靠性。[本公开实施方式的详情]下文中,将对本公开的一个实施方式(以下称为“本实施方式”)进行详细说明,但本实施方式不限于以下说明。[碳化硅外延基板的制造方法]图5为概略显示本实施方式中的碳化硅外延基板的制造方法的流程图。如图5所示,制造方法包括准备步骤(s101)、减压步骤(s102)、升温步骤(s103)、氢气引入步骤(s104)、烃气体引入步骤(s105)、基板改性步骤(s106)和外延生长步骤(s107)。在本实施方式中,在外延生长步骤(s107)之前进行基板改性步骤(s106)。由此减少碳化硅单晶基板10中的梯形缺陷20的起点23。结果,减少了外延层11的表面11a中的梯形缺陷20的缺陷密度。下文中,将对各步骤进行说明。[准备步骤(s101)]在准备步骤(s101)中,准备了图1中显示的碳化硅单晶基板10。例如,通过对由碳化硅单晶制成的晶锭进行切割,准备碳化硅单晶基板10。例如,使用线锯进行切割。期望碳化硅具有4h的多型体,因为该多型体在电子迁移率、介电强度(絶縁破壊電界強度)等方面比其他多型体更优异。碳化硅单晶基板10的直径优选为100mm以上(例如,4英寸以上),更优选为150mm以上(例如,6英寸以上)。具有较大的直径可以有助于降低半导体装置的制造成本。碳化硅单晶基板10具有后面将在其上生长外延层11的主面10a。碳化硅单晶基板10具有1°以上且8°以下的偏角θ。也就是说,主面10a是相对于预定晶面以1°以上且8°以下的偏角θ倾斜的面。通过对碳化硅单晶基板10设置偏角θ,当通过cvd法生长外延层11时,引起从主面10a露出的原子台阶开始的横向生长,即“台阶流动生长”。由此,在保持碳化硅单晶基板10的多型体的状态下生长单晶,并抑制不同多型体的混入。在此,预定的晶面优选为(0001)面或(000-1)面。也就是说,预定的晶面优选为{0001}面。期望偏角所设置的方向为<11-20>方向。偏角θ更优选为2°以上且7°以下,特别优选为3°以上且6°以下,最优选为3°以上且5°以下,因为通过将偏角设定在这样的范围内,保持了不同多型体的抑制与生长速度之间的平衡。[成膜装置]在成膜装置内进行准备步骤(s101)以后的步骤。因此,首先将对成膜装置的构造进行说明。图3为显示成膜装置的构造的一个例子的示意侧视图。图4为沿图3中的iv-iv线取的示意剖视图。图3和4中显示的成膜装置1为卧式热壁cvd装置(横型ホットウォールcvd装置)。如图3所示,成膜装置1包括加热元件6、绝热材料5、石英管4和感应加热线圈3。加热元件6由例如碳制成。如图4所示,成膜装置1设有两个加热元件6,并且各加热元件6具有包括曲面部分6a和平坦部分6b的半圆柱形中空结构。两个平坦部分6b被布置成彼此面对,并且由两个平坦部分6b包围的空间作为在其中放置碳化硅单晶基板10的腔室1a。腔室1a也称为“气体流动通道”。绝热材料5被布置成包围加热元件6的外周部分。腔室1a通过绝热材料5与成膜装置1的外部绝热。石英管4被布置成包围绝热材料5的外周部分。感应加热线圈3沿着石英管4的外周部分缠绕。成膜装置1以通过向感应加热线圈3供给交流电而对加热元件6进行感应加热、从而可以控制腔室1a内的温度的方式构成。在这种情况下,因绝热材料5的作用,石英管4几乎不被加热。[减压步骤(s102)]在减压步骤(s102)中,如图3和4所示,碳化硅单晶基板10放置在成膜装置1的腔室1a内,并降低腔室1a内的压力。碳化硅单晶基板10放置在腔室1a内未显示的基座上。可以对基座进行sic涂布等。图6为显示在减压步骤(s102)之中和之后的腔室1a内的温度和气体流量控制的时序图。在图6中,减压步骤(s102)对应于从碳化硅单晶基板10放置在腔室1a内的时间点t1开始、经过开始腔室1a内的减压的时间点t2到腔室1a内的压力达到目标值(压力p1)的时间点t3的时间。例如,压力p1为约1×10-6pa。[升温步骤(s103)]在升温步骤(s103)中,成膜装置1的腔室1a内的温度被加热到第一温度t1。如图6所示,腔室1a内的升温从时间点t3开始,并且腔室1a内的温度在时间点t6达到第一温度t1。升温至第一温度t1可以在单个步骤中进行,或者例如可以在升温过程中通过设置保持预定温度t0的时间(图6中从时间点t4到时间点t5)以逐步的方式进行。在温度t0处的保持时间例如为约10分钟。第一温度t1优选为1300℃以上且低于1500℃。如果第一温度t1低于1300℃,则碳化硅单晶基板10将在后面进行的基板改性步骤(s106)中在低于1300℃的温度下与氢气和烃气体接触,并且可能促进梯形缺陷以外的缺陷的生成。另一方面,如果第一温度t1为1500℃以上,则在第一温度t1与第二温度t2之间只有小的温差,可能降低改性效果。第一温度t1更优选为1320℃以上且1480℃以下,特别优选为1350℃以上且1450℃以下。此外,考虑到与后述的第二温度t2的关系,期望第一温度t1比第二温度t2低约100℃至约200℃。升温时间(从时间点t3到时间点t6的时间)例如为约30分钟至约2小时。[氢气引入步骤(s104)]如图6所示,从腔室1a内的温度达到第一温度t1的时间点t6开始,将氢气(h2)引入腔室1a而将腔室1a内的压力调节到压力p2。在氢气引入步骤(s104)中,腔室1a内的压力p2优选被调节到5kpa以上且40kpa以下,因为在这样的范围内的压力下,可以预期大的改性效果。在氢气引入步骤(s104)中,腔室1a内的压力p2更优选被调节到5kpa以上且15kpa以下(50毫巴以上且150毫巴以下),并且特别优选被调节到7.5kpa以上且12.5kpa以下(75毫巴以上且125毫巴以下)。氢气的流量(图6中的fh)优选为50slm以上且200slm以下。如果氢气的流量小于50slm,则烃气体的流量对总气体流量的比率变得过高,可能促进梯形缺陷以外的缺陷的生成。另一方面,如果氢气的流量大于200slm,则烃气体的流量对总气体流量的比率变得过低,可能降低改性效果。氢气的流量更优选为75slm以上且175slm以下,特别优选为100slm以上且150slm以下。[烃气体引入步骤(s105)]如图6所示,在时间点t6处,烃气体引入步骤(s105)与氢气引入步骤(s104)并行开始。然而,氢气引入步骤(s104)和烃气体引入步骤(s105)不一定必须同时开始,这些步骤可以在稍微偏差的时间点下开始。例如,可以在完成使用氢气进行的压力调节后开始烃气体的引入。作为烃气体,可以使用甲烷(ch4)气体、乙烷(c2h6)气体、丙烷(c3h8)气体、丁烷(c4h10)气体和乙炔(c2h2)气体等。这些烃气体可以单独使用,或者可以两种以上混合使用。也就是说,烃气体优选包括选自由甲烷气体、乙烷气体、丙烷气体、丁烷气体和乙炔气体构成的组中的一种或多种。在烃气体引入步骤(s105)中的烃气体的流量(图6中的fc)优选为5sccm以上且30sccm以下,因为在这样的范围内可以预期大的改性效果。烃气体的流量更优选为10sccm以上且25sccm以下,特别优选为15sccm以上且20sccm以下。此外,烃气体流量与氢气流量之比(烃气体流量÷氢气流量)优选为2.5×10-5以上且6.0×10-4以下,更优选为5.7×10-5以上且3.3×10-4以下,特别优选为1.0×10-4以上且2.0×10-4以下。[基板改性步骤(s106)]基板改性步骤(s106)通过从经由引入氢气将腔室1a内的压力调节到压力p2并引入烃气体的时间点t6起升高腔室1a内的温度开始。根据本发明人的研究,通过从略低于作为生长温度的第二温度t2的温度起使碳化硅单晶基板10与烃气体接触,可以减少梯形缺陷的起点。如图6所示,在基板改性步骤(s106)中,从时间点t6起升高腔室1a内的温度,在时间点t7处达到第二温度t2,并进一步保持在第二温度t2下直到时间点t8(即将全面生长(本成長)之前)。在这种情况下,当开始升温时(时间点t6时),就认为碳化硅单晶基板10的改性开始。在基板改性步骤(s106)中的处理时间,即从时间点t6到时间点t8的时间优选为大于1分钟,以便获得大的改性效果。从时间点t6到时间点t8的时间更优选为5分钟以上,特别优选为10分钟以上,最优选为15分钟以上。在这种情况下,从时间点t6到时间点t7的时间(升温时间)优选为10秒以上且2分钟以下,更优选为20秒以上且1分30秒以下,特别优选为30秒以上且1分钟以下。此外,从时间点t7到时间点t8的时间(保持时间)优选为1分钟以上且60分钟以下,更优选为5分钟以上且40分钟以下,特别优选为10分钟以上且30分钟以下。在此,第二温度t2优选为1500℃以上且1700℃以下。如果第二温度t2低于1500℃,则可能难以在后面进行的外延生长步骤(s107)中均一地生长单晶,并且可能降低生长速度。此外,如果第二温度t2高于1700℃,则使用氢气的蚀刻作用增强,可能会相反地降低生长速度。第二温度t2更优选为1520℃以上且1680℃以下,特别优选为1550℃以上且1650℃以下。在基板改性步骤(s106)中,氢气流量和腔室1a内的压力被保持不变,而从第一温度t1到第二温度t2的升温速度不一定是不变的。此外,烃气体的流量也不一定是不变的。[第一种变体]图7为显示基板改性步骤(s106)中的升温方法的第一种变体的部分时序图。如图7所示,可以以升温速度逐渐降低的方式进行从第一温度t1到第二温度t2的升温。例如,温度在图7中的时间点t6与t7之间的各时间点(例如时间点t61)处可以升高50℃,同时逐渐增加时间点之间的间隔。在这种情况下,可以根据升温速度的降低逐渐增加烃气体的流量。时间点之间的时间(例如,时间点t61与t62之间的时间)例如为约1秒以上且约30秒以下。[第二种变体]图8为显示基板改性步骤(s106)中的升温方法的第二种变体的部分时序图。如图8所示,从第一温度t1到第二温度t2的升温可以以阶梯状方式进行。例如,温度在图8中的时间点t6与t8之间的各时间点(例如时间点t61)处可以升高50℃,并且可以设定为在升温后恒定并保持预定的时间。此外,在这种情况下,保持时间可以被设定为逐渐加长。此外,配合升温,烃气体的流量在各时间点处可以以阶梯状的方式增大。各阶梯中的保持时间例如为约1秒以上且约30秒以下。[外延生长步骤(s107)]在外延生长步骤(s107)中,除了已经被引入腔室1a的氢气和烃气体之外,还在保持第二温度t2的状态下,引入硅烷(sih4)气体。由此可以在碳化硅单晶基板10的主面10a上生长外延层11。虽然在外延生长步骤(s107)中硅烷气体的流量(图6中的fs)没有特别限制,但期望以烃气体中含有的碳(c)原子数与硅烷气体中含有的硅(si)原子数之比(c/si)为0.5以上且2.0以下的方式调节硅烷气体的流量,以外延生长化学计量比适当的sic。在外延生长步骤(s107)中,可以引入氮气(n2)等作为掺杂剂。在这种情况下,可以在生长的初期阶段(时间点t8与时间点t9之间)形成大量含有掺杂剂的区域。这样的区域也称为“缓冲层”。缓冲层具有例如约1×10-18cm-3的掺杂浓度。缓冲层具有例如约0.1μm至约1.0μm的厚度。根据外延层11的目标厚度,持续进行外延生长直到时间点t10。在生长完成后,腔室1a内的温度向着时间点t11降低。此外,在时间点t11处及以后,腔室1a的内部向大气开放,并且将腔室1a内的压力恢复到大气压(时间点t12)。由此,制造碳化硅外延基板100。[碳化硅外延基板]下文中,将对通过本实施方式的制造方法得到的碳化硅外延基板100进行说明。图1为显示碳化硅外延基板100的构造的一个例子的示意剖视图。如图1所示,碳化硅外延基板100包含具有相对于预定晶面倾斜偏角θ的主面10a的碳化硅单晶基板10,和在碳化硅单晶基板10的主面10a上形成的外延层11。如上所述,预定晶面优选为(0001)面或(000-1)面。[梯形缺陷]在碳化硅外延基板100中,外延层11的表面11a中的梯形缺陷20的缺陷密度为1个/cm2以下。考虑到半导体装置中的氧化膜的可靠性,期望梯形缺陷20具有较低的缺陷密度,理想地,缺陷密度为0(零)。梯形缺陷20的缺陷密度优选为0.5个/cm2以下,更优选为0.1个/cm2以下。如图1所示,梯形缺陷20在碳化硅单晶基板10与外延层11之间的界面处具有起点23,并延伸到外延层11的表面11a。然而,梯形缺陷20不一定具有起点23。也就是说,本实施方式的梯形缺陷包括没有起点的缺陷,只要缺陷包含上底和下底即可,因为本发明人的研究已经证实存在不能确认起点的梯形缺陷。图2为显示梯形缺陷的平面形状的示意俯视图。如图2所示,梯形缺陷20包含与<11-20>方向相交的上底21和下底22。在梯形缺陷20中,上底21的宽度w1为0.1μm以上且100μm以下,而下底22的宽度w2为50μm以上且5000μm以下。外延层11的厚度h优选为5μm以上且30μm以下。包含这样的厚度的外延层11的碳化硅外延基板100作为用于例如高击穿电压mosfet的基板特别有用。图9为显示梯形缺陷的另一个例子的示意俯视图。梯形缺陷120为在外延层11的表面中形成的凹陷,并具有梯形平面形状。梯形缺陷120包含与<11-20>方向相交的上底部121和下底部122。上底部121的宽度w1为0.1μm以上且100μm以下,而下底部122的宽度w2为50μm以上且5000μm以下。图10为沿图9中的x-x线取的示意剖视图。如图10所示,上底部121包含突起部121a。突起部121a可以基本上位于上底部121的中央。在上底部121中,突起部121a相对于突起部121a以外的部分突起约5nm至约20nm。突起部121a的高度可以用白光干涉显微镜(例如,由nikon公司制造的“bw-d507”)进行测定。将汞灯用作白光干涉显微镜的光源,并且将白光干涉显微镜的视野设定为250μm×250μm。图11为沿图9中的xi-xi线取的示意剖视图。梯形缺陷120内部,也就是在上底部121与下底部122之间的区域中,外延层11的表面向着碳化硅单晶基板10稍微缩进。梯形缺陷120在碳化硅单晶基板10与外延层11之间的界面处具有起点123。起点123可以与突起部121a连接。然而,突起部121a没有与贯通位错连接。图12为图9中的区域a的放大图。如图12所示,下底部122包含多个台阶聚并122b。“台阶聚并”是指多个原子台阶形成束并产生1nm以上的水平差的线性缺陷。台阶聚并中的水平差的大小可以例如为约1nm至约5nm。台阶聚并中的水平差的大小可以用例如原子力显微镜(afm)进行测定。下底部122中包含的台阶聚并的数量可以例如为约2个至约100个,或约2个至约50个。下底部122中包含的台阶聚并的数量也可以通过用afm观察下底部122来计数。作为afm,例如可以使用由veeco制造的“dimension300”等。作为afm的微悬臂(探针),由bruker制造的“nchv-10v”等是合适的。如下设定afm的测定条件。将afm的测定模式设定为敲击模式,在敲击模式中,将测定区域设定为边长为20μm的正方形并且将测定深度设定为1.0μm。敲击模式中的取样在如下条件下进行:测定区域内的扫描速度设定为5秒一个周期,各扫描行的数据的数目设定为512点,并且扫描行的数目设定为512。将微悬臂的位移控制设定为15.50nm。实施例下文中,将使用实施例对本实施方式进行更具体地说明,但本实施方式不限于此。如下制造样品1、2和3的碳化硅外延基板以研究梯形缺陷的缺陷密度。[样品1至3的制造]准备具有相对于(0001)面倾斜4°的主面10a的碳化硅单晶基板10。碳化硅单晶基板10放置在成膜装置1的腔室1a内,并根据图6的时序图在其上生长厚度为15μm的外延层11。为了制造样品1至3,如下设定图6中显示的参数。腔室内的压力p1:1×10-6pa腔室内的压力p2:10kpa氢气流量fh:120slm硅烷气体流量fs:46sccm烃气体流量fc:17sccm烃气体种类:丙烷气体温度t0:1100℃第一温度t1:1400℃第二温度t2:1590℃。对于样品1,将丙烷的流量在图6中从时间点t1到时间点t8设定为0,并且从时间点t8到时间点t10设定为fc。如图6所示设定温度曲线。也就是说,对于样品1,没有在引入烃气体的状态下进行升温到生长温度(第二温度t2),并且没有进行基板改性步骤(s106)。样品1相当于只进行使用氢气蚀刻的例子,如常规方法中一样。对于样品2,从图6中的时间点t6起(也就是说,在温度升高到生长温度的过程中)引入丙烷气体。将时间点t6与开始引入硅烷气体的时间点t8之间的时间(基板改性步骤中的处理时间)设定为5分钟。对于样品3,从图6中的时间点t6起引入丙烷气体。将时间点t6与开始引入硅烷气体的时间点t8之间的时间设定为15分钟。使用nomarski型光学显微镜,根据上述方法测定样品1至3的外延层中的梯形缺陷的缺陷密度。表1显示了结果。[表1]样品1样品2样品3基板改性步骤无5分钟15分钟梯形缺陷3.7个/cm20.1个/cm2以下0个/cm2从表1能够看出,在进行了基板改性步骤的样品2和3中,当与没有进行基板改性步骤的样品1相比较时,梯形缺陷的缺陷密度显著降低。特别是,在基板改性步骤中的处理时间被设定为15分钟的样品3中,梯形缺陷的缺陷密度降低到实质上不能确认梯形缺陷存在的状态。应该理解,在此公开的实施方式和实施例在各方面都是例示性的而非限制性的。本发明的范围由权利要求的范围而不是上述实施方式和实施例限定,并且意图包括与权利要求的范围等价的范围和含义内的任何变更。标号说明1:成膜装置;1a:腔室;3:感应加热线圈;4:石英管;5:绝热材料;6:加热元件;6a:曲面部分;6b:平坦部分;10:单晶基板;10a:主面;11:外延层;11a:表面;20,120:梯形缺陷;21:上底;22:下底;23,123:起点;100:碳化硅外延基板;121:上底部;121a:突起部;122:下底部;122b:台阶聚并;h:高度;a:区域;fc,fh,fs:流量;h:厚度;l:间隔;p1,p2:压力;t0:温度;t1:第一温度;t2:第二温度;w1,w2:宽度;t1,t2,t3,t4,t5,t6,t7,t8,t9,t10,t11,t12,t61,t62,t63,t64:时间点。当前第1页12