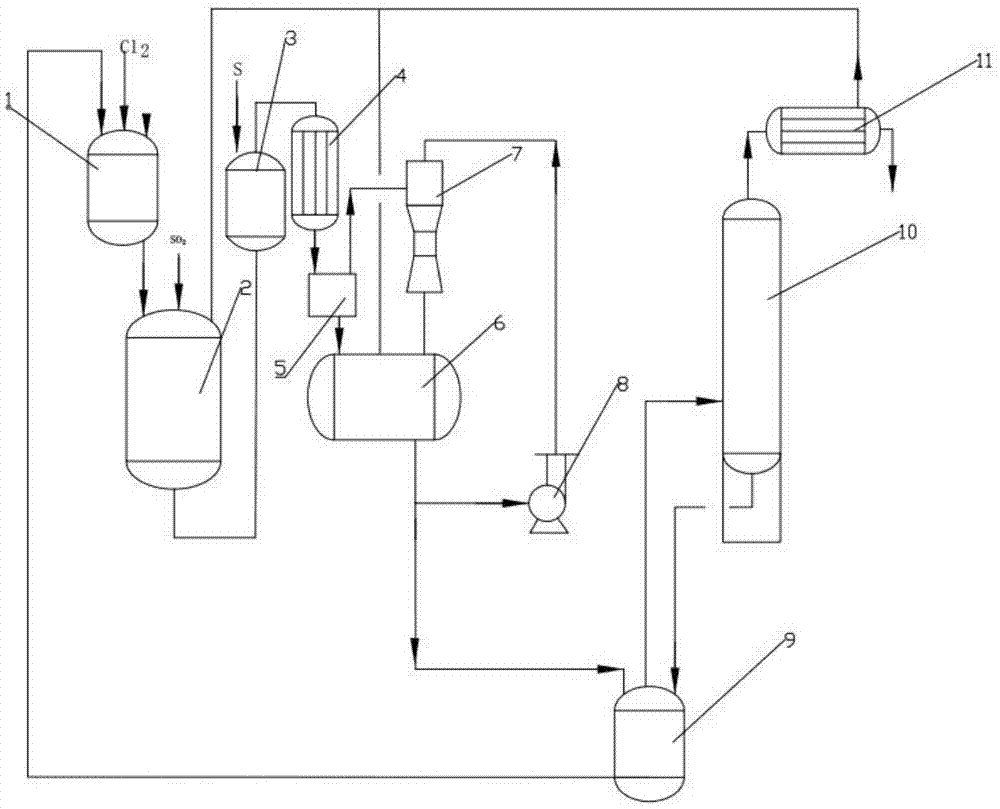
本发明涉及化工工艺领域,尤其涉及一种精制氯化亚砜的方法和设备。
背景技术:
:氯化亚砜溶于苯、氯仿和四氯化碳,在水中分解生成亚硫酸和氯化氢,加热至140度分解生成氯气、二氧化硫和一氯化硫,氯化亚砜的氯原子取代羟基和巯基的能力很强,有时也可取代二氧化硫、氧或氢,能与有羟基的酚或醇等有机化合物反应生成相应的氯化物,与磺酸反应生成磺酰氯,与格利雅试剂反应生成相应的亚砜化合物等。氯化亚砜在有机合成上很重要,它是农药、医药、感光材料和高聚物中间体合成的中间原料。对于不同的用途对氯化亚砜的纯度要求不同,尤其是医药行业需要纯度极高的氯化亚砜,由此对氯化亚砜的精制提纯工艺要求较高。氯化亚砜中含有的常见的杂质为氯气、二氧化硫、二氯化硫、氯化砜以及一氯化硫,氯气和二氧化硫在常温下为气体,很容易与氯化亚砜分开,但是二氯化硫和氯化砜的沸点与氯化亚砜比较接近,在精制氯化亚砜的过程中很难将二氯化硫和氯化砜除去,并且在除杂的同时很容易导致氯化亚砜分解,由此严重降低氯化亚砜的收率。针对以上问题,美国专利us4388290a公开了一种利用氯化铝作催化剂纯化氯化亚砜的改进方法,改进方法为在氯化铝作催化剂的条件下,加入硫进行蒸馏,且在蒸馏前需要先将硫和氯化铝加热到50~60℃,但是该专利提供的方法需要在氯化亚砜粗品加入硫化反应装置之前先溶解在一氯化硫中,而一氯化硫又能抑制配硫反应的进行,除此之外,在硫化反应的过程中,氯化铝又会溶解在氯化亚砜中,后续处理较为麻烦,因此,降低了氯化亚砜的收率的纯化难度。而现有技术cn103172031b公开了一种精制氯化亚砜的方法和设备,采用活性碳作催化剂,在精馏之前将含有杂质的氯化亚砜原料加热为过热气体后,再将其通入到硫化反应装置中进行硫化反应,但是在实际生产过程中,将含有杂质的氯化亚砜气体加热为过热气体时,需要在提纯工艺设备中设置加热装置,对设备要求极高,而且加热过程中易导致氯化亚砜分解。cn101412503a公开了一种利用粗品氯化亚砜为原料合成氯化亚砜的方法,所述的粗品氯化亚砜是将氯化亚砜混合气体进行冷凝以及脱气提纯后产生的,即该现有技术中涉及的氯化亚砜生产工艺为:首先合成原料,再合成氯化亚砜,合成后的氯化亚砜混合气体在冷凝以及脱气提纯后产生粗品氯化亚砜,然后利用粗品氯化亚砜为原料合成氯化亚砜。但是由于该现有技术中精馏提纯过程的不稳定,并且配硫反应不添加任何催化剂,使得所得氯化亚砜的产率和纯度较低,且原料利用率较低。有鉴于此,特提出本发明。技术实现要素:针对以上问题,本发明提供了一种精制氯化亚砜的方法,本发明的目的在于提高氯化亚砜的纯度以及产量,防止精制过程氯化亚砜分解,为实现上述目的,本发明采用如下技术方案:一种精制氯化亚砜的方法,氯化亚砜合成釜产生的混合气体在提纯的过程中经过如下两步配硫反应:首先,从氯化亚砜合成釜排出的混合气体直接通入第一配硫釜中进行硫化,硫化后的混合气体通过冷凝和脱气提纯后形成粗品氯化亚砜;其次,在精馏装置顶部设置二次硫化床,粗品氯化亚砜在进行精馏提纯时进行再次硫化,在二次硫化床内设置催化剂。优选的,第一配硫釜中发生硫化反应的催化剂为活性炭,所述二次硫化床内采用氯化铝为催化剂,所述氯化铝固定在载体铝片上。优选的,向所述第一配硫釜中加入硫的方法为,将选取的硫磺块与干燥剂氯化钙颗粒一起粉碎,再将粉碎后的混合粉末送入到第一配硫釜中进行配硫反应。优选的,所述第一配硫釜采取固定床反应器,在固定床反应器内部设有活性炭床层,从氯化亚砜合成釜中排出的气体直接进入到第一配硫釜中在活性炭作用下进行第一步硫化反应。优选的,氯化亚砜生产过程为:(1)二氯化硫的合成:二氯化硫合成釜内的压力控制为0.01mpa-0.10mpa,二氯化硫合成釜的出气口压力p1为0.01-0.02mpa;(2)氯化亚砜粗品的合成:将二氯化硫合成釜排出的混合气体通入到氯化亚砜合成釜中,同时向氯化亚砜粗品合成釜中通入二氧化硫,氯化亚砜粗品合成釜的出气口压力p2为0.01-0.02mpa;(3)第一配硫反应:将氯化亚砜合成釜产生的混合气体通入到第一配硫釜中进行第一步硫化反应,硫的加入量为完全反应所需硫量的70-80%;(4)氯化亚砜粗品的冷凝:将第一配硫釜产生的混合气体通入到氯化亚砜粗品冷凝器中,不凝性气体通过气体单向输送装置送至氯化亚砜合成釜中;(5)氯化亚砜粗品接收:将氯化亚砜粗品冷凝器中产生的冷凝产物通入到粗品接收槽中进行脱气提纯,利用气体单向输送装置将低沸物抽取到氯化亚砜合成釜中;(6)精馏提纯:将氯化亚砜粗品接收槽输出的脱气提纯产物通入到精馏装置中进行精馏提纯,同时在精馏装置中进行第二步硫化,不凝性气体通过气体单向输送装置输送至氯化亚砜合成釜中。优选的,氯化亚砜粗品冷凝后到达气液分离器,气体单向输送装置抽取气液分离器中的不凝性气体,并将抽取到的不凝性气体再次通入到氯化亚砜粗品接收槽中后,气体单向输送装置再抽取粗品接收槽中的的不凝性气体合并输送至氯化亚砜合成釜中中。优选的,所述气体单向输送装置设置为液体喷射装置,液体喷射装置将抽取的不凝性气体通入到氯化亚砜合成釜中。优选的,所述二氯化硫合成釜的出气口压力p1大于氯化亚砜粗品合成釜的出气口压力p2,所述第一配硫釜的位置要高于氯化亚砜粗品合成釜,且高度差范围为:1.0-3.0m。优选的,第一配硫釜中气相出口的压力p3小于于氯化亚砜粗品接收槽中气相出口的压力p4,所述氯化亚砜粗品接收槽和精馏装置之间存在位差,氯化亚砜粗品接收槽的位置高于精馏装置,且所述位差范围为:2.0-5.0之间。本发明还提供了一种精制氯化亚砜的设备,具体包括反应釜、冷凝装置、脱气提纯装置和精馏装置,在精馏装置的外部设置恒温控制箱,恒温控制箱与成品冷凝器相连接,成品冷凝器中排除的冷凝液体通入到恒温控制箱中,恒温控制箱上还设置加热装置和温度检测器,恒温控制箱上还连接低温储液箱。本发明的有益效果如下:(1)在从氯化亚砜合成釜中合成出来的气体直接为高温气体,在配硫反应之前不需要再加强热,减少设备投入,并且减少了处理加热过程中氯化亚砜的分解,将硫磺和干燥剂混合加入,避免通过加入硫磺引入水分,减小氯化亚砜分解的可能,充分提取生产工艺中的不凝性气体,减轻后续精馏过程中精馏装置的压力,进而提高氯化亚砜的纯度。(2)采用恒温精馏的方式对氯化亚砜进行精馏提纯时,不仅能提高氯化亚砜的纯度,还可以在很大程度上提高高纯度氯化亚砜的产量,硫和氯气对氯化亚砜的转化率接近100%;(3)由于采用全循环全封闭工艺,脱离气体中的so2和cl2混合气体以及各工位产生的氯化亚砜以外的液相产物可以再循环到相应的进料处,使得整套装置基本上无三废液气向外排放,不会造成环境污染;附图说明图1本发明精制氯化亚砜的工艺流程图2本发明精馏装置恒温控制系统示意图1-二氯化硫合成釜,2-氯化亚砜合成釜,3-配硫釜,4-粗品冷凝器,5-气液分离器,6-粗品接收槽,7-液体喷射装置,8-循环泵,9-精馏釜,10-精馏塔,11-成品冷凝器,12-低温储液箱,13-恒温控制箱,14-第一阀门,15-第二阀门,16-第一温度检测器,17-第二温度检测器,18-加热装置,19-出液口具体实施方式下面将结合本发明实施例中的附图,对本发明实施例中的技术方案进行清楚、完整地描述,显然,所描述的实施例仅仅是本发明一部分实施例,而不是全部的实施例。基于本发明中的实施例,本领域普通技术人员在没有付出创造性劳动前提下所获得的所有其他实施例,都属于本发明保护的范围。氯化亚砜粗品在提纯的过程中经过两步硫化反应,从氯化亚砜合成反应器排出的混合型气体通过第一配硫釜进入到粗品冷凝器中,冷凝后的液相组分进入精馏装置中进行精馏提纯,在精馏装置顶部设有二次硫化反应器,在二次硫化反应器内杂质组分在催化剂的作用下与硫反应,精馏后得到高纯度的氯化亚砜。本发明中第一配硫釜中采用活性炭做催化剂,所述二次硫化反应器中采用氯化铝为催化剂。优选的,所述催化剂氯化铝负载在铝片上,降低氯化铝在氯化亚砜产品中的溶解度,进一步提高其催化效果。优选的,在精馏塔顶部设置镂空的铝片,将催化剂氯化铝负载在铝片上。本发明在粗品冷凝后的产物中含有大量的二氯化硫气体,但是二氯化硫的沸点较低(59℃),与氯化亚砜很难分离,由此需要将低沸点的二氯化硫转化为沸点较高的一氯化硫,方便与氯化亚砜分离;在配硫釜内加入硫与二氯化硫反应,能将二氯化硫转化为一氯化硫,但是工业生产用的硫磺中常常包含水分,而氯化亚砜遇水易分解,所以若配硫反应时的硫磺内包含有水分,则容易造成氯化亚砜的分解,影响氯化亚砜的纯度和收率。由此,需要对配硫反应时的硫磺进行干燥处理。本发明配硫釜内硫的加入方法为:将选取的硫磺块与干燥剂氯化钙颗粒一起粉碎,粉碎后的颗粒达到30~50目,再将粉碎后的混合粉末送入到配硫釜中进行配硫反应。本发明中第一配硫釜采取固定床反应器,在固定床反应器内部设有活性炭床层,从氯化亚砜合成釜中排出的气体直接进入到第一配硫釜中在活性炭作用下进行第一步硫化反应。本发明中氯化亚砜生产过程为:(1)二氯化硫的合成:采用液态的一氯化硫与氯气在二氯化硫合成釜内反应,氯气与液态一氯化硫的体积比为150:(0.15-0.25),反应温度控制为60~85℃,二氯化硫合成釜内的压力控制为0.01mpa-0.10mpa,二氯化硫合成釜的出气口压力p1为0.01-0.02mpa;(2)氯化亚砜粗品的合成:将二氯化硫合成釜排出的混合气体通入到氯化亚砜合成釜中,同时向氯化亚砜粗品合成釜中通入计量后的二氧化硫气体,氯化亚砜合成釜温度控制为160-250℃,压力控制为0.10mpa-0.25mpa,氯化亚砜粗品合成釜的出气口压力p2为0.01-0.02mpa;(3)第一配硫反应:将氯化亚砜合成釜产生的混合气体通入到第一配硫釜中,常压状态下进行配硫反应,第一配硫釜内的温度控制为60-80℃,常压状态下进行,硫的加入量为完全反应所需硫量的70-80%;(4)氯化亚砜粗品的冷凝:将第一配硫釜产生的混合气体通入到氯化亚砜粗品冷凝器中,并将冷凝温度设置为≦35℃,得到冷凝产物,其中不凝性气体通过气体单向输送装置送至氯化亚砜合成釜中;(5)氯化亚砜粗品接收:将氯化亚砜粗品冷凝器中产生的冷凝产物通入到粗品接收槽中进行脱气提纯,压力控制为0.10mpa-0.25mpa,提纯后得到粗品氯化亚砜,利用气体单向输送装置将低沸物抽取到氯化亚砜合成釜中;(6)精馏提纯:将氯化亚砜粗品接收的产物通入到精馏装置中进行精馏提纯,同时在精馏装置中进行第二步硫化,不凝性气体通过气体单向输送装置输送至氯化亚砜合成釜中,所述精馏装置采用恒温精馏的方式。其中,氯化亚砜粗品冷凝后到达气液分离器,气体单向输送装置抽取气液分离器中的不凝性气体,气液分离器中的液相组分进入氯化亚砜粗品接收槽,气体单向输送装置将抽取到的不凝性气体通入氯化亚砜粗品接收槽,再由气体单向输送装置或循环泵抽取粗品接收槽中的少量不凝性气体并输送至气体单向输送装置中,气体单向输送装置将内部存储的不凝性气体重新返回到氯化亚砜粗品接收槽中,再进行一次气液传质交换,最后通入到氯化亚砜合成釜中。进一步的,本发明中所述气体单向输送装置设置为液体喷射装置,所述液体喷射装置设置在氯化亚砜粗品冷凝器和精馏装置之间,液体喷射装置将抽取的不凝性气体通入到氯化亚砜合成釜中。本发明中所述二氯化硫合成釜和氯化亚砜合成釜之间存在压差和位差,二氯化硫合成釜的出气口压力p1大于氯化亚砜粗品合成釜的出气口压力p2,二氯化硫合成釜的高度要高于氯化亚砜合成釜的高度,所述位差范围为:1.0-3.0m之间。本发明中第一配硫釜中气相出口的压力p3小于于氯化亚砜粗品接收槽中气相出口的压力p4,所述氯化亚砜粗品接收槽和精馏装置之间存在位差,氯化亚砜粗品接收槽的位置高于精馏装置,且所述位差范围为:2.0-5.0之间。本发明中所述精馏提纯中采用恒温精馏的方式,在精馏装置的外部设置恒温控制箱,恒温控制箱与冷凝器相连接,冷凝器中排除的冷凝液体通入到恒温控制箱中,恒温控制箱上还设置加热装置和温度检测器,恒温控制箱上还连接低温液体装置。以下结合实施例对本发明做进一步描述。实施例1本实施例在氯化亚砜合成釜产生的混合气体进入冷凝之前进行第一步硫化反应,同时在精馏装置中设置二次硫化床,对氯化亚砜粗品进行进一步提纯,实现氯化亚砜的精制。具体方法如下:(1)二氯化硫的合成采用液态的一氯化硫与氯气在二氯化硫合成釜内反应,其中液态一氯化硫一部分来自一氯化硫反应釜内生成的产物,另一部分来自精馏塔脱出的液相高沸物组分,氯气与液态一氯化硫的体积比为150:(0.15-0.25),反应温度控制为60~85℃,生成的scl2和过量cl2的混合气体从出气口排出,控制二氯化硫合成釜内的压力为0.01mpa-0.10mpa,二氯化硫合成釜的出气口压力p1为0.01-0.02mpa;(2)氯化亚砜粗品的合成将二氯化硫合成釜排出的混合原料气体通入到氯化亚砜合成釜中,同时向氯化亚砜粗品合成釜中通入计量后的二氧化硫气体,具体的,其中未发生反应的氯气和生成的二氯化硫以及计量后的二氧化硫按cl2:so2:s2cl2为150:100:0.20的比例加入到氯化亚砜合成釜中,反应温度控制在160~250℃,压力控制为0.01mpa-0.25mpa,氯化亚砜粗品合成釜的出气口压力p2为0.01-0.02mpa;(3)第一配硫反应将氯化亚砜合成釜产生的粗品混合气体不需要经过任何加热过程直接通入到第一配硫釜中,进行第一配硫反应,第一配硫釜内的反应温度为从氯化亚砜合成釜排出的粗品混合气体自身的余温,向其中加入的硫磺,其中所述硫的加入量为完全反应所需硫量的70-80%,最终得到第一配硫产物。(4)氯化亚砜粗品的冷凝将上述反应后的第一配硫产物通入到氯化亚砜粗品冷凝器中,并将冷凝温度设置为≦35℃,冷凝后的粗品进入气液分离器,进而冷凝下来的液相氯化亚砜粗品进入氯化亚砜粗品接收槽,未冷凝下来的不凝性气体通过气体单向输送装置送至氯化亚砜合成釜中。(5)氯化亚砜粗品接收将氯化亚砜粗品冷凝器中产生的冷凝产物通入到粗品接收槽中,粗品接收槽的温度控制在60-80℃,压力控制为0.10mpa-0.25mpa,在粗品接收槽中对氯化亚砜粗品进行脱气提纯,提纯后得到氯化亚砜,利用气体单向输送装置将低沸物抽取到氯化亚砜合成釜中。(6)精馏提纯:在精馏装置的顶部设置二次硫化床,加入足量硫磺,将粗品接收槽脱气提纯的产物通入到精馏装置中进行常压精馏提纯,脱气提纯产物中未在第一配硫釜中硫化的二氯化硫和氯化砜在精馏装置的二次硫化床中与硫进行充分的反应,生成一氯化硫以及少量的二氧化硫,其中一氯化硫回流至塔釜后返回二氯化硫合成釜中,不凝性气体通过气体单向输送装置输送至氯化亚砜合成釜。所述气体单向输送装置为液体喷射装置。液体喷射装置的优点:从设备造价来看,液体喷射装置与隔膜泵相比,液体喷射装置对安装位置要求不高,并且对生产车间占用的体积较小,噪声较低,最重要的是液体喷射装置抽取不凝性气体的效果更好。本实施例提供的精制氯化亚砜的方法将从氯化亚砜合成釜排出的高温混合气体直接通入到第一配硫釜中进行配硫反应,不需要在加强热,而且减少不凝性气体的含量,降低后续气体单向输送装置的压力。实施例2本实施例采用实施例1的工艺,不同之处在于第一配硫釜中添加硫磺时,将硫磺与干燥剂混合进行第一配硫反应的进行,其他工艺同实施例1,具体方法如下:(3)第一配硫反应将氯化亚砜合成釜产生的粗品混合气体不需要经过任何加热过程直接通入到第一配硫釜中,进行第一配硫反应,第一配硫釜内的反应温度为从氯化亚砜合成釜排出的粗品混合气体自身的余温,向其中加入硫磺,硫的加入方法为:将选取的硫磺块与干燥剂氯化钙颗粒一起粉碎,粉碎后的颗粒达到30~50目,再将粉碎后的混合粉末送入到第一配硫釜中进行配硫反应。优选的,所述干燥剂与硫磺块的重量比为(3~5):1,其中所述硫的加入量为完全反应所需硫量的70-80%,最终得到第一配硫产物。之后进行冷凝、脱气提纯以及精馏提纯等,具体其他步骤同实施例1相同。所述气体单向输送装置为液体喷射装置。实施例3本实施例采用实施例2的工艺,不同之处在于第一配硫釜中添加催化剂催化第一配硫反应的进行,其他工艺同实施例2,具体方法如下:(3)将氯化亚砜合成釜产生的粗品混合气体不需要经过任何加热过程直接通入到第一配硫釜中,进行第一配硫反应,第一配硫釜内的反应温度为从氯化亚砜合成釜排出的粗品混合气体自身的余温,其中,第一配硫釜内设置活性炭床层,活性炭作为一次硫化反应的催化剂,向其中加入干燥的硫磺,其中所述硫的加入量为完全反应所需硫量的70-80%,最终得到第一配硫产物。后续步骤同实施例2相同。所述气体单向输送装置为液体喷射装置。实施例4本实施例采用实施例3的工艺,不同之处在于精馏装置顶部的二次硫化床中也添加催化剂催化配硫反应的进行,其他工艺同实施例3,具体方法如下:(6)精馏提纯:在精馏装置的顶部设置二次硫化床,加入足量硫磺,将粗品接收槽脱气提纯的产物通入到精馏装置中进行精馏提纯,具体的,二次硫化反应器在精馏塔顶部的二次硫化床内部设置镂空的铝片,将催化剂氯化铝负载在铝片上,脱气提纯产物中未在第一配硫釜中硫化的二氯化硫和氯化砜在精馏的过程中与硫进行充分的反应,生成一氯化硫以及少量的二氧化硫,其中一氯化硫回流至塔釜后返回二氯化硫合成釜中,不凝性气体通过气体单向输送装置输送至氯化亚砜合成釜,精馏提纯后得到纯度较高的氯化亚砜成品。所述气体单向输送装置为液体喷射装置。其他步骤同实施例3相同。实施例5本实施例采用实施例3相同的工艺,不同之处在于最后精馏提纯的步骤中设置恒温控制装置,对粗品接收槽脱气提纯的产物进行恒温精馏,进而对氯化亚砜实现精制的方法,具体方法如下:(6)精馏提纯:在精馏装置的顶部设置二次硫化床,加入足量硫磺,将粗品接收槽脱气提纯的产物通入到精馏装置中进行精馏提纯,具体的,在精馏装置的外部设置恒温控制箱,恒温控制箱为环状结构,包裹在精馏塔的中部,且恒温控制箱的高度小于精馏塔的高度。脱气提纯产物中未在第一配硫釜中硫化的二氯化硫和氯化砜在精馏的过程中与硫进行充分的反应,生成一氯化硫以及少量的二氧化硫,其中一氯化硫回流至塔釜后返回二氯化硫合成釜中,不凝性气体通过气体单向输送装置输送至氯化亚砜合成釜,精馏提纯后得到高纯度氯化亚砜成品。所述气体单向输送装置为液体喷射装置。其他步骤同实施例3相同。实施例6本实施例描述的是气体单向输送装置从冷凝装置中抽取的不凝性气体再次通入到氯化亚砜粗品接收槽中,再进行一次气液传质,进一步增加分离效果,进而实现对氯化亚砜的精制,其他步骤同实施例5相同,具体方法如下:氯化亚砜混合气体冷凝后进入气液分离器,气体单向输送装置抽取气液分离器中的不凝性气体,并将抽取到的不凝性气体再次通入到氯化亚砜粗品接收槽中后,再由气体单向输送装置或循环泵抽取粗品接收槽中的的不凝性气体合并输送至氯化亚砜粗品合成釜中。这种将气液分离器中的不凝性气体再次进入到粗品接收槽中,对从气液分离器提取的不凝性气体和粗品接收槽中液相又进行了一次气液传质交换的过程,使得气液分离器中抽取的不凝性气体中掺杂的氯化亚砜被粗品接收槽中的液相吸收,而粗品接收槽中的少量的二氧化硫和氯气体能充分的随通入到其中的不凝性气体一并回到氯化亚砜粗品合成釜中。所述气体单向输送装置为液体喷射装置。其他步骤同实施例5相同。由此,利用气体单向输送装置在冷凝装置和氯化亚砜粗品接收槽中间的往复循环,充分提取不凝性气体,有效的减少了精馏前氯化亚砜粗品中的不凝性气体含量,提高精馏效率,不会导致精馏装置内压力的大幅度改变,便于控制精馏压力,进而保证整个精制工艺的稳定性,提高原料利用率和氯化亚砜纯度。实施例7本实施例描述的生产工艺同实施例4相似,不同之处在于:在精馏提纯过程中加入催化剂的方式不同,具体方法如下:在精馏装置的顶部设置二次硫化床,加入足量硫磺,将配硫反应的混合产物通入到精馏装置中进行精馏提纯,具体的,二次硫化床在精馏塔顶部的塔板上投放催化剂氯化铝,混合产物中未在配硫釜中硫化的二氯化硫和氯化砜在精馏的过程中与硫进行充分的反应,生成一氯化硫以及少量的二氧化硫,其中一氯化硫回流至塔釜后返回二氯化硫合成釜中,不凝性气体通过气体单向输送装置输送至氯化亚砜合成釜。所述气体单向输送装置为液体喷射装置。其他步骤同实施例4相同。实施例8如图1和图2所示,本实施例提供了一种精制氯化亚砜的设备,具体包括反应釜、冷凝装置、脱气提纯装置、精馏装置、气体单向输送装置以及循环泵8,所述反应釜包括二氯化硫合成釜1、氯化亚砜合成釜2和第一配硫釜3,所述冷凝装置包括粗品冷凝器4和气液分离器5,所述脱气提纯装置为粗品接收槽6,所述精馏装置包括精馏釜9、精馏塔10和成品冷凝器11。优选的,本发明在精馏塔10的外部设置恒温控制箱13,恒温控制箱13与成品冷凝器相连接,成品冷凝器11中排除的冷凝液体通入到恒温控制箱13中,恒温控制箱13上还设置加热装置18和温度检测器,恒温控制箱13上还连接低温储液箱12。优选的,所述气体单向输送装置设置为液体喷射装置7。优选的,恒温控制箱13为环状结构,包裹在精馏塔10的中部,且恒温控制箱13的高度小于精馏塔10的高度。优选的,恒温控制箱13与冷凝器相连,在连接部位设置有第一阀门14,同时在恒温控制箱13上与成品冷凝器11连接处的附近设置有低温液体入口以及控制低温液体进入恒温控制箱的第二阀门15,使得低温储液箱12与恒温控制箱13相连通,在远离低温液体入口的一侧设置有出液口19,恒温控制箱上设置有温度控制装置。温度控制装置包含有两个温度检测器和加热装置18,其中第一温度检测器16布置在恒温控制箱13中间靠近精馏塔的部位,第二温度检测器17布置在恒温控制箱与冷凝器的连接部位。一般情况下,将精馏塔中间部位的恒温精馏温度范围设置为78~85℃,当第一温度检测器检测到的温度低于78℃时,加热装置开始对恒温控制箱内的液体进行加热。优选的,同时第二检测器也会启动对冷凝液体的温度检测,当检测到冷凝液体的温度高于第一温度检测器检测到的温度时,温度控制装置会控制第一阀门打开,冷凝液体进入恒温控制箱内用于调节恒温控制箱内的液体温度,即恒温控制箱内的温度可以通过高温的冷凝液体来调节升高,也可以通过加热装置控制升高。当第一温度检测器检测到的温度高于85℃时,第二阀门打开,低温液体进入到恒温控制箱中,用于降低恒温控制箱内液体的温度,由此实现恒温控制箱内液体的温度能一直保持在设定的范围内,进而实现氯化亚砜成品的高效精馏。实施例9本实施例描述了一种精制氯化亚砜的装置中精馏装置的恒温控制方法,具体的,该控制方法包括以下步骤:s1:由第一温度检测器检测精馏塔中间部位温度t1,并判断精馏塔中间部位温度t1是否小于预设温度阈值ta,若为是,则执行步骤s21,若为否,则执行步骤s22;s21:若第一温度检测器检测精馏塔中间部位温度t1小于预设温度阈值ta,则恒温控制箱控制加热装置对恒温控制箱内的液体加热,同时启动第二温度检测器;s22:恒温控制箱保持第一状态;s3:由第二温度检测器检测冷凝液体温度t2,并判断冷凝液体温度t2是否大于t1,若为是,则执行步骤s31,若为否,则执行步骤s32;s31:若第二温度检测器检测冷凝液体温度t2大于t1时,恒温控制箱会控制第一阀门打开,冷凝液体进入恒温控制箱内;s32:若第二温度检测器检测冷凝液体温度t2不大于t1时,则第一阀门保持关闭;s4:由第一温度检测器检测精馏塔中间部位温度t1,并判断精馏塔中间部位温度t1是否大于预设温度阈值tb,若为是,则执行步骤s51,若为否,则执行步骤s52;s51:若第一温度检测器检测到精馏塔中间部位温度t1大于预设温度阈值tb,则第二阀门打开,低温液体进入恒温控制箱内部;s52:若第一温度检测器检测到精馏塔中间部位温度t1不大于预设温度阈值tb,恒温控制箱保持第一状态。进一步的,所述第一状态为恒温控制箱内的液体保持不变,加热装置和所有阀门保持关闭。进一步的,所述预设温度阈值ta和tb根据精馏装置需要的控温范围确定,优选的,所述ta的值为78℃,所述tb的值为85℃。比较例1本比较例采用现有技术中cn101412503a的技术方案,由粗品氯化亚砜为原料合成氯化亚砜,且在配硫反应中不添加催化剂,但该现有技术中的粗品氯化亚砜为脱气提纯后得到,具体方法如下:第一配硫反应:将脱气提纯釜产生的提纯产物通入到第一配硫釜中,常压状态下进行第一步配硫反应,配硫釜内的温度控制为60-80℃,硫的加入量为完全反应所需硫量的70-80%。硫化反应后粗品中含有的二氯化硫与硫发生反应生成沸点较高的一氯化硫,硫化后得到第一配硫产物。再将第一配硫产物通入到精馏装置中进行精馏提纯。具体过程同现有技术相同。由于氯化亚砜经过冷凝和脱气提纯后再进行配硫反应,则氯化亚砜为液态性质进入到第一配硫釜中,需要对第一配硫釜进行温度控制,对设备要求较高。比较例2本实施例描述的生产工艺同比较例1相似,不同之处在于,在第一配硫釜内的第一配硫反应中添加催化剂,具体方法如下:第一配硫反应:将脱气提纯釜产生的提纯产物通入到第一配硫釜中,常压状态下进行第一配硫反应,第一配硫釜内的温度控制为60-80℃,其中,第一配硫釜内设置活性炭床层,活性炭作为一次硫化反应的催化剂,向第一配硫釜加入硫磺,其中所述硫的加入量为完全反应所需硫量的70-80%。比较例3本实施例描述的生产工艺同比较例2相似,不同之处在于,精馏装置顶部的二次硫化床中也添加催化剂催化配硫反应的进行,其他工艺同比较例2,具体方法如下:精馏提纯:在精馏装置的顶部设置二次硫化床,加入足量硫磺,将粗品接收槽脱气提纯的产物通入到精馏装置中进行精馏提纯,具体的,二次硫化反应器在精馏塔顶部的二次硫化床内部设置镂空的铝片,将催化剂氯化铝负载在铝片上,脱气提纯产物中未在第一配硫釜中硫化的二氯化硫和氯化砜在精馏的过程中与硫进行充分的反应,生成一氯化硫以及少量的二氧化硫,其中一氯化硫回流至塔釜后返回二氯化硫合成釜中,不凝性气体通过气体单向输送装置输送至氯化亚砜合成釜。所述气体单向输送装置为隔膜泵。实验例1第一配硫工艺顺序的研究检测方法:(1)二氧化硫:其中二氧化硫含量的测定采用国标gb/t16128-1995的方法测定,(2)氯气含量测定:采用液相色谱法,具体步骤为:a.用苯胺水溶液吸收混合气体中的氯气;b.以甲醇、磷酸为流动相,c18柱为分离柱,分离吸收液中的苯胺和1,3-二苯基脲,波长为254nm进行液相色谱分析,1,3-二苯基脲的峰面积与氯气含量成正比;c.利用外标法测量。(3)氯化亚砜含量测定:采用气相色谱法,具体步骤为:a.用苯作溶剂,吸收混合气体中的氯化亚砜;b.取少量溶解后的混合液相,用微量进样器将待测样品注入气相色谱仪里,氯化亚砜的含量与峰面积成正比。(4)氯化砜含量测定:采用液相色谱法,具体步骤为:a.取样,向其中加入过量无水乙醇,使氯化砜完全酯化;b.通入过量氨气中和,离心后,取油酯层进行色谱分析,用面积归一化法计算氯化砜的含量。其中,采用液相色谱仪采用se-30色谱柱。表1为不同实施例各组分的含量其中比较例1为氯化亚砜在经过粗品合成、冷凝和脱气、第一配硫反应后进入精馏装置,实施例1为氯化亚砜在经过粗品合成、第一配硫反应、冷凝和脱气后进入精馏装置,对比两个比较例发现,实施例1在进入精馏装置之前的混合物中氯化亚砜和一氯化硫含量明显较高,杂质组分的含量较低,而氯化亚砜的沸点为78.8℃,一氯化硫的沸点为137℃,两者差距较大,在精馏过程中很容易分离除去。即实施例1的方案在进入精馏塔时不凝性气体含量较低,降低精馏装置的压力,同时提高精馏效率,且得到的氯化亚砜成品纯度较高。由于氯化亚砜合成釜内温度较高,从合成釜排出的混合气体不需要经过加热步骤可直接进入第一配硫釜,省略了加热装置,降低设备投入。而比较例1的方案先将粗品冷凝和脱气再进行加热配硫反应,浪费资源,且对设备要求复杂。实验例2第一配硫反应中硫磺加入方法的研究对比实施例1和实施例2中第一配硫反应后的混合物中各组分的含量发现,实施例2中氯化亚砜的含量明显降低,可见在第一配硫反应时硫磺中的水分会使氯化亚砜分解,导致氯化亚砜的含量降低。而将硫磺与干燥剂混合加入,避免了随着硫磺的加入而引入水分,减小氯化亚砜分解的可能。实验例3催化剂对配硫反应效果的研究氯化砜痕量检测:将混合溶液溶解在水溶液中,使氯化砜和氯化亚砜水解,再采用滴定法间接测定氯化亚砜的含量。另外,将精馏得到的氯化亚砜产品取少量蒸干,观察是否有固体残留,其中的固体残留为溶解在氯化亚砜中的催化剂氯化铝。表2为不同条件下各组分的含量对比通过实施例2和实施例3的对比发现,在第一配硫釜内添加活性炭作催化剂,能降低其中二氯化硫以及以及氯化砜的含量,进而减轻后续精馏过程中精馏装置的压力。通过实施例3、实施例4和实施例7的对比发现,在精馏过程中添加催化剂且将催化剂氯化铝负载在铝片上,有利于氯化亚砜的精制,降低氯化铝在氯化亚砜中的溶解度。实验例4恒温精馏和非恒温精馏对精馏效率的影响研究表3恒温精馏与非恒温精馏效果对比回流比塔顶温度socl2纯度socl2产量实施例41:27899.9467kg/h实施例51:27599.9503kg/h通过以上实施例对比可以看出,采用恒温精馏的方式对氯化亚砜进行精馏提纯时,不仅能提高氯化亚砜的纯度,还可以在很大程度上提高高纯度氯化亚砜的产量。实验例5气体单向输送装置的循环线路研究通过以上对比可以看出,利用气体单向输送装置在冷凝器和氯化亚砜粗品接收槽之间的往复循环,有效的减少了精馏前氯化亚砜粗品中的不凝性气体含量,提高精馏效率,不会导致精馏装置内压力的大幅度改变,便于控制精馏压力,进而保证整个精制工艺的稳定性,提高氯化亚砜的产量。以上所述仅为本发明的优选实施例而已,并不用于限制本发明,对于本领域的技术人员来说,本发明实施例可以有各种更改和变化。凡在本发明的精神和原则之内,所作的任何修改、等同替换、改进等,均应包含在本发明的保护范围之内。当前第1页12