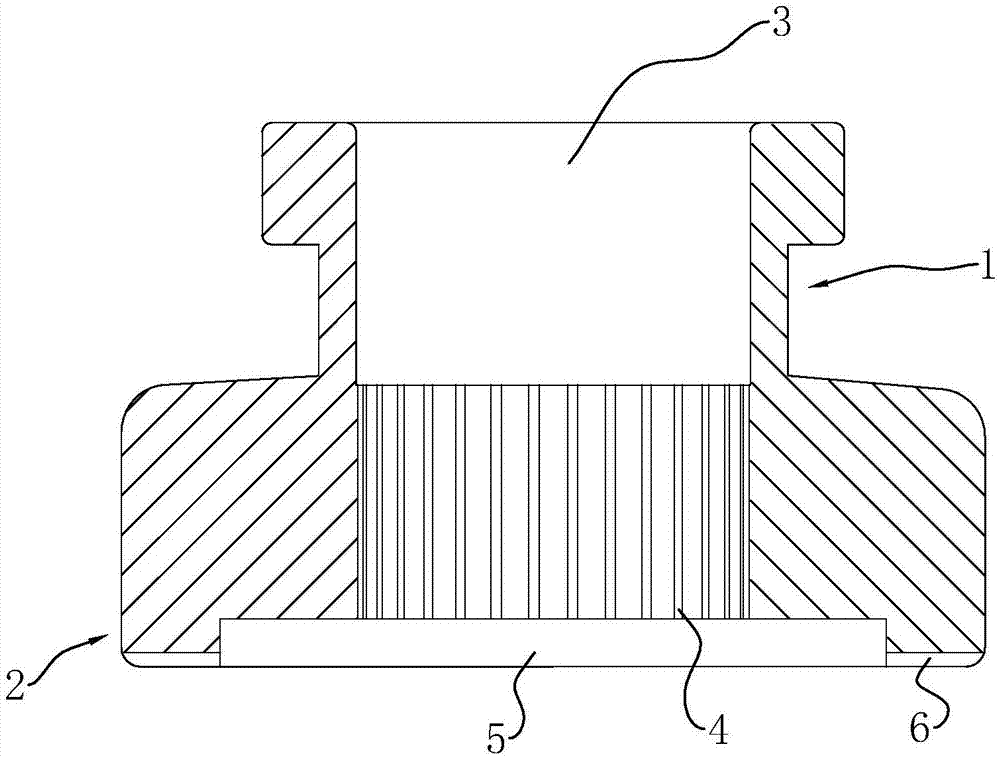
本发明涉及玻璃瓶生产配件
技术领域:
,更具体地说,它涉及一种玻璃瓶吹气头及其生产工艺。
背景技术:
:玻璃瓶在生产过程中,最为传统的方式是采用手工吹制工艺,即:手执一根长的空心管子,把管子插进具有一定流动性的玻璃液体里。在玻璃还未冷却时用嘴在管子另一头吹气,从而形成玻璃瓶的造型,若所需的玻璃瓶的造型较为复杂时,还需要一边进行高温加热一边进行吹塑,以保持玻璃液体的可塑性。然而,采用手工吹气工艺时,由于吹气是由人为控制的,容易造成吹出的玻璃瓶的规则程度不够好。随着现代化水平越来越高,全自动生产线的推广程度也在不断提高,因此,在生产玻璃瓶时,通常采用制瓶机进行连续生产玻璃瓶,以实现制造出的玻璃瓶具有较好的规则程度、合格率较高的优点,且玻璃瓶的产量也得到大幅度的提高。然而,制瓶机上的吹气头上开设有一个直径较大的出气孔,在吹气时,吹出的气体较为集中,对吹出的玻璃瓶的底部的作用力不同,容易导致吹出的玻璃瓶内的成型效果不稳定,最终出现瓶内凹凸不一致的现象,尤其是针对不同类型的玻璃瓶而言,获得的合格率较低。技术实现要素:针对现有技术存在的不足,本发明的第一个目的在于提供一种玻璃瓶吹气头,使吹出的玻璃瓶的底部光滑、平整,不易出现瓶内凹凸不一致的现象。在吹制玻璃瓶的过程中,不仅使吹出的气流分布均匀,使吹制获得的玻璃的瓶内均匀、光滑,不易出现瓶内凹凸不一致的现象,提高玻璃瓶的合格率;还能有效提高生产过程中的散热效果。本发明的第二个目的在于提供一种玻璃瓶吹气头的生产工艺,有助于提高玻璃瓶吹气头的均匀散热效果,从而有助于减缓吹气头的老化并延长其使用寿命。为实现上述第一个目的,本发明提供了如下技术方案:一种玻璃瓶吹气头,所述吹气头包括一体成型设置的进气件、出气件,所述进气件上设置有进气孔,所述出气件上靠近进气件的一侧面设置有出气区域,所述出气区域由若干个均匀排列的出气通孔组成,且所述出气件的另一端开设有卡槽,所述出气通孔与进气孔、卡槽连通;所述出气件上还开设有排气通孔,所述排气通孔与卡槽连通。通过采用上述技术方案,本发明中的玻璃瓶吹气头可用于行列式制瓶机中。用于吹制的适量的熔融玻璃置于卡槽内,想进气孔中通入气体,气体从进气孔进入出气区域,即从若干个均匀排列的出气通孔中均匀通入到卡槽内,进而对熔融玻璃进行吹气,使玻璃瓶逐渐形成。在吹制过程中,不断有气体进入进气孔中,为了维持气体吹入的稳定性,部分气体会从排气通孔中排出,进而使吹制获得的玻璃瓶的底部光滑平整,薄厚均匀,不易出现凹凸不平的现象。熔融玻璃的热量会从卡槽向进气孔方向传递,而出气通孔数量较多且均匀排列,有助于使热量快速传递,不易造成卡槽部位的温度过高而引起吹气头的使用寿命缩短。与此同时,热量也会被从排气通孔中排出的气体带走,进而起到散热效果,进一步减少卡槽部分以及其周围部位温度过高的情况,从而提高吹气头的使用寿命。进一步优选为:所述出气通孔沿出气件的中心线对称设置。通过采用上述技术方案,出气通孔可均匀排列从而围绕形成圆圈、方形等,这可根据瓶身的形状或尺寸来适配对应的出气通孔排列形成的形状。对称设置的出气通孔,可使吹制玻璃瓶时吹出的气体具有更加均匀的分布。进一步优选为:所述排气通孔等间距设置于出气件上。通过采用上述技术方案,有助于使吹制过程中吹出的气体的稳定性更好。进一步优选为:所述卡槽的长度大于出气区域的长度。通过采用上述技术方案,在吹制过程中,可有效地向熔融玻璃吹出气体,不易出现吹制出的玻璃瓶的瓶口有残缺的现象,有助于提高玻璃瓶的合格率。为实现上述第二个目的,本发明提供了如下技术方案:一种玻璃瓶吹气头的生产工艺,包括如下步骤:熔融合金;铸造成型获得吹气头初成品;正火处理;淬火处理;回火处理;所述淬火处理时,先将经过正火处理的吹气头初成品浸入第一保护混合物中,浸泡5-10min,然后在1000-1050℃的温度下加热30-50min,再在880-950℃的温度下加热60-85min;所述回火处理时,先将经过淬火处理后的吹气头初成品浸入第二保护混合物中,浸泡3-5min;再在500-650℃的温度下保温处理12-15h;所述淬火处理中使用的第一保护混合物包括如下重量份数的组分:传热油100份;导热材料10-15份;氯化钠2-3份;所述回火处理时使用的第二保护混合物包括如下重量份数的组分:传热油100份;导热材料3-6份;所述第一保护混合物、第二保护混合物中的导热材料包括纳米氮化硅镁、纳米碳化硅、纳米氮化铝、纳米氮化硼、高球形度氧化铝、金红石型纳米二氧化钛、纳米氮化硅中的至少三种。通过采用上述技术方案,合金具有较好的耐高温效果,铸造成型后获得的吹气头具有较好的耐高温性能,能承受吹制过程中的高温。淬火处理时,经过正火处理的吹气头初成品浸入第一保护混合物中时,处于高温状态的经过正火处理的吹气头初成品的表层在一定程度上被降温,而其内部的温度较高。经第一保护混合物浸泡后的初成品再进行两次加热,使表面被稍降下温度的初成品又被迅速加热,进而使初成品的组织结构发生新的变化,有助于使经淬火处理的初成品获得光洁的表面,以及更高的硬度、耐磨性和疲劳强度,但同时,也会容易使脆性有所提升。与此同时,淬火处理过程中,前后采用了2次加热处理过程,第一次在1000-1050℃的温度下加热30-50min,第二次在880-950℃的温度下加热60-85min。第一次加热的温度较高,但加热持续的时间较短,有助于使第一保护层快速形成,并且使导热材料与初成品之间形成较为充分的连接;第二次加热的温度相对较低,但加热持续的时间较长,可使形成的第一保护层中的导热材料能与初成品之间得到充分的连接,进而实现均匀且优异的导热效果。在经过淬火处理的初成品,继续进行回火处理,且回火处理时,需要将经过淬火处理后的吹气头初成品浸入第二保护混合物中一段时间,起到适当的降温作用,再在较高温度下加热并保温较长的时间,这段时间的加热,温度相对于淬火处理时的加热温度而言更低,时间更长,可充分调整经过淬火处理后的吹气头初成品的硬度,并起到减小脆性的作用。且在较长时间的加热、保温作用后,可使初成品表面的保护物质将其表面包覆地更加全面,从而起到更好的保护作用。导热材料中,纳米氮化硅镁、纳米碳化硅、纳米氮化铝、纳米氮化硼、高球形度氧化铝、金红石型纳米二氧化钛、纳米氮化硅这几种材料的耐高温效果非常优异,能在经过淬火处理的吹气头初成品的表面形成第一保护层,能使吹气头在吹制玻璃瓶时具有更好且更均匀的导热作用,结合吹气头的形状,其具有较大的比表面积以及排气通孔,有助于提高散热的效果,从而减少高温对吹气头的损伤,进而有助于延长吹气头的使用寿命。且导热材料均采用纳米级材料,纳米级的材料具有较大的比表面积,可与传热油形成充分接触,并且有助于充分分散于传热油中。此外,纳米级的导热材料与传热油、氯化钠相互配合形成的第一保护混合物,在经过正火处理的吹气头初成品浸入其中后,可在初成品的表面形成第一保护层,分别在1000-1050℃、880-950℃的温度下加热时,有助于使该第一保护层与初成品之间形成紧密连接,充分发挥对初成品的保护作用。或者纳米级的导热材料与传热油相互配合后形成的第二保护混合物,在经过淬火处理后、并形成第一保护层的吹气头初成品的表面再形成第二保护层,且第二保护混合物中的导热材料能充分弥补第一保护层存在的缺陷,使初成品得到进一步的保护。进一步优选为:所述导热材料的粒径为20-25nm。通过采用上述技术方案,粒径小、质地细腻,在经过正火处理的吹气头初成品表面能形成轻薄的保护层。进一步优选为:所述经过正火处理的吹气头初成品与第一保护混合物的体积比为1∶(150-265);所述经过淬火处理的吹气头初成品与第二保护混合物的体积比为1∶(105-162)。通过采用上述技术方案,第一保护混合物、第二保护混合物的体积较大,在将经过正火处理的吹气头初成品、经过淬火处理的吹气头初成品分别加入其中时,一方面,能将初成品的温度降低,另一方面,能使第一保护混合物、第二保护混合物与初成品形成结合。进一步优选为:所述淬火处理中使用的第一保护混合物或第二保护混合物采用如下步骤制备获得:步骤一,将传热油加热至100℃,按照重量份数,加入导热材料,在150-200rpm的转速下充分混合,再按照重量份数,加入氯化钠,在350-600rpm的转速下充分混合,获得初混物;步骤二,将步骤一中获得的初混物采用超声波分散处理,超声波频率为20khz,充分混合物,获得第一保护混合物或第二保护混合物。通过采用上述技术方案,传热有加热至100℃时,其粘度降低,加入导热材料后,较易被分散。而氯化钠的加入,容易增大整个流动体系的粘稠感,继而需要增大转速,才能实现充分的混合。加入的导热材料的粒径较小,较易出现团聚等现象。而超声波处理后,有助于提高导热材料在传热油中的分散、悬浮效果,不易使导热材料、氯化钠出现沉淀、团聚等现象。且经过搅拌后的初混物再经过超声波处理,有助于使导热材料、氯化钠与传热油形成充分混合。进一步优选为:所述第一保护混合物、第二保护混合物中的传热油为mobiltherm603热导油、mobiltherm605热导油、mobilithshc220高温高速黄油中的一种。通过采用上述技术方案,mobiltherm603热导油、mobiltherm605热导油、mobilithshc220高温高速黄油均购自深圳灏鸿科技有限公司。其中,mobiltherm603热导油、mobiltherm605热导油具有优异的传热作用,同时也有助于加速散热;两者还具有抗热裂化性能、抗化学氧化性能。mobilithshc220高温高速黄油具有优异的化学稳定性、抗磨性、防锈性、防腐蚀能力。进一步优选为:所述合金为310s不锈钢、ra330合金、ra333合金中的一种。通过采用上述技术方案,310s不锈钢是奥氏体铬镍不锈钢,具有很好的抗氧化性、耐腐蚀性、耐高温性能,其中含有较高百分比的铬和镍,使其具有优异的蠕变强度,可适用于较高温度下进行的吹制玻璃瓶的工序。ra330合金为镍铁铬系耐热合金,ra333合金为高铬镍基特种合金,在高温下能保持优异的机械性能、耐氧化性能、耐蚀性能。综上所述,本发明具有以下有益效果:第一、本发明中的铸造成型过程中,获得的吹气头初成品上开设有出气区域、卡槽、排气通孔,且出气区域与卡槽相连通,卡槽与排气通孔相连通,在吹气过程中,当吹气量达到所需要求后,多余的气体可从排气通孔中被排出,在一定程度上提高了散热的效率。第二、本发明中采用了淬火处理和回火处理相结合的工艺,其中,淬火处理中,先浸泡了第一保护混合物,再前后采用了一高、一低的加热方式进行淬火;后采用回火处理,先浸泡了第二保护混合物,再采用了比淬火处理更低的加热温度进行加热和较长时间的保温,有助于使经过回火处理的初成品具有较低的脆性、更高的硬度、耐磨性和疲劳强度;且与初成品的表面充分连接的第一保护层和第二保护层共同作用,实现整个初成品具有均匀且优异的导热效果。第三、吹气头的制备工艺与成型的结构相结合,有助于提高在吹制玻璃瓶的过程中的热传导并且加快散热速度,进而延长吹气头的使用寿命。第四、吹气头上的出气区域中设置有若干个均匀排列的出气通孔,在吹制玻璃瓶时,可根据要求的瓶身大小放置不同出气通孔排列方式的吹气头,进而使吹出的气体分布均匀,有助于使获得的玻璃瓶底部具有均匀的质地,不易出现凹凸不平的现象。附图说明图1是本发明的实施例1的结构示意图。图2是本发明的实施例1的仰视图。图3是本发明的实施例13的结构示意图。图4是本发明的实施例13的横截面图。图中,1、进气件;2、出气件;3、进气孔;4、出气通孔;5、卡槽;6、排气通孔;7、水平转动调节件;71、底座;72、固定槽;73、连通孔;8、第一凹槽;9、第二凹槽;10、弹性固定件;101、弹簧;102、固定球。具体实施方式以下结合附图和实施例对本发明作进一步详细说明。实施例1:一种玻璃瓶吹气头,参照图1,包括一体成型设置且柱状的进气件1、出气件2,且进气件1上设置有进气孔3;在出气件2靠近进气孔3的一端开设有若干个出气通孔4,这些出气通孔4沿出气件2的中心线对称设置并等间距排列成圆圈状的出气区域,该出气区域有三个,呈同心圆的方式排布。在出气件2远离进气孔3的一端开设有卡槽5,且进气孔3、出气通孔4、卡槽5连通。参照图2,在出气件2上还对称开设有4个排气通孔6,且排气通孔6沿水平方向与卡槽5连通,而卡槽5的水平长度大于出气区域的直径。本实施例的实施原理为:在吹制玻璃瓶的过程中,气体从进气孔3中通入,通过出气通孔4进行分散,使气体较为均匀且分散地吹出,使玻璃瓶内部的底部被充分吹出成型,达到均匀、平整的效果。玻璃瓶吹气头通过如下步骤生产获得:熔融合金;铸造成型获得吹气头初成品;正火处理;淬火处理;回火处理。其中,合金为310s不锈钢、ra330合金、ra333合金。淬火处理时,先将经过正火处理的吹气头初成品浸入第一保护混合物中,且经过正火处理的吹气头初成品与第一保护混合物的体积比为1∶150,浸泡10min;然后在1000℃的温度下加热35min,再在900℃的温度下加热70min;回火处理时,先将经过淬火处理后的吹气头初成品浸入第二保护混合物中,且经过淬火处理的吹气头初成品与第二保护混合物的体积比为1∶105,浸泡5min;再在500℃的温度下保温处理15h。其中,第一保护混合物中所包括的组分及其质量如表1所示;第二保护混合物中所包括的组分及其质量如表2所示。表1实施例1-3中第一保护混合物中所包括的组分及其质量表2实施例1-3中第二保护混合物中所包括的组分及其质量其中,传热油为mobiltherm603热导油;导热材料为质量比为1∶1∶1∶1∶1∶1∶2的纳米氮化硅镁、纳米碳化硅、纳米氮化铝、纳米氮化硼、高球形度氧化铝、金红石型纳米二氧化钛、纳米氮化硅,且导热材料的粒径为20nm。第一保护混合物采用如下步骤制备获得:步骤一,将传热油加热至100℃,加入导热材料,在150-200rpm的转速下充分混合,再加入氯化钠,在350-600rpm的转速下充分混合,获得初混物;步骤二,将步骤一中获得的初混物采用超声波分散处理,超声波频率为20khz,充分混合物,获得第一保护混合物或第二保护混合物。第二保护混合物采用上述与第一保护混合物相同的制备方法制备获得。实施例4:一种玻璃瓶吹气头,与实施例1的区别在于,合金为ra330合金。实施例5:一种玻璃瓶吹气头,与实施例1的区别在于,合金为ra333合金。实施例6:一种玻璃瓶吹气头,与实施例1的区别在于,传热油为mobiltherm605热导油。实施例7:一种玻璃瓶吹气头,与实施例1的区别在于,传热油为mobilithshc220高温高速黄油。实施例8:一种玻璃瓶吹气头,与实施例1的区别在于,导热材料为质量比为1∶2∶1∶1的纳米碳化硅、纳米氮化硼、金红石型纳米二氧化钛、纳米氮化硅,且导热材料的粒径为23nm。实施例9:一种玻璃瓶吹气头,与实施例1的区别在于,导热材料为质量比为1∶1∶2∶1的纳米氮化硅镁、纳米氮化铝、金红石型纳米二氧化钛、纳米氮化硅,且导热材料的粒径为25nm。实施例10:一种玻璃瓶吹气头,与实施例1的区别在于,导热材料为质量比为1∶1∶1∶1∶1∶2的纳米氮化硅镁、纳米碳化硅、纳米氮化铝、纳米氮化硼、高球形度氧化铝、纳米氮化硅,且导热材料的粒径为20nm。实施例11:一种玻璃瓶吹气头,与实施例1的区别在于,淬火处理时,先将经过正火处理的吹气头初成品浸入第一保护混合物中,且经过正火处理的吹气头初成品与第一保护混合物的体积比为1∶265,浸泡10min;然后在1050℃的温度下加热30min,再在950℃的温度下加热60min;回火处理时,先将经过淬火处理后的吹气头初成品浸入第二保护混合物中,且经过淬火处理的吹气头初成品与第二保护混合物的体积比为1∶150,浸泡4min;再在600℃的温度下保温处理13h。实施例12:一种玻璃瓶吹气头,与实施例1的区别在于,淬火处理时,先将经过正火处理的吹气头初成品浸入第一保护混合物中,且经过正火处理的吹气头初成品与第一保护混合物的体积比为1∶200,浸泡8min;然后在1000℃的温度下加热50min,再在880℃的温度下加热85min;回火处理时,先将经过淬火处理后的吹气头初成品浸入第二保护混合物中,且经过淬火处理的吹气头初成品与第二保护混合物的体积比为1∶162,浸泡3min;再在650℃的温度下保温处理12h。其中,实施例中采用的mobiltherm603热导油、mobiltherm605热导油、mobilithshc220均购自深圳灏鸿科技有限公司。实施例13:一种玻璃瓶吹气头,与实施例1的区别在于,参照图3,在出气件2的端头处,连接有一个柱状的水平转动调节件7。参照图4,该水平转动调节件7包括底座71、柱状的固定槽72、开设于固定槽72上的若干个连通孔73,出气件2的端头处可较为紧固地插于固定槽72内,且连通孔73的孔径、数量、排列方式,分别与出气通孔4的孔径、数量、排列方式相同。在固定槽72的侧面沿水平方向开设有一个柱状的第一凹槽8,在第一凹槽8内固定有一个弹簧101,并且在朝向第一凹槽8的开口处的弹簧101的一端焊接有一个固定球102。在弹簧101处于正常伸缩状态时,固定球102部分突出于第一凹槽8的开口处。在吹气件的侧壁上沿水平方向均匀开设有两个第二凹槽9,该第二凹槽9的开口孔径比固定球102的直径稍大。本实施例的实施原理为:在需要调节出气通孔4时,旋转水平转动调节件7,在合适的位置,使固定球102进入第二凹槽9内,使水平转动调节件7与出气件2形成连接,从而将出气通孔4与连通孔73之间的连通程度得到固定,在吹制玻璃瓶时,不易出现水平转动调节件7与出气件2之间发生相对偏移而导致连通程度发生变化的现象,进而可使吹制时吹出的气体保持平稳,从而有助于使适用于该出气通孔4大小进行吹制的玻璃瓶的瓶身内部的底部具有光滑、均匀的效果。对比例1:一种玻璃瓶吹气头,与实施例1的区别在于,吹气头上只开设有一个柱状的进气孔,而不存在出气通孔和排气通孔。对比例2:一种玻璃瓶吹气头,与实施例1的区别在于,导热材料的质量为6kg,且为质量比为1∶1的纳米碳化硅与纳米氮化铝。对比例3:一种玻璃瓶吹气头,与实施例1的区别在于,导热材料的质量为3kg,且为质量比为2∶1的纳米氮化硼与纳米氮化硅。对比例4:一种玻璃瓶吹气头,与实施例1的区别在于,淬火处理过程中,采用体积相等的水替换第一保护混合物。对比例5:一种玻璃瓶吹气头,与实施例1的区别在于,淬火处理过程中,采用体积相等的、质量百分含量为15%的氯化钠水溶液,替换第一保护混合物。对比例6:一种玻璃瓶吹气头,与对比例4的区别在于,回火处理过程中,采用体积相等的水替换第二保护混合物。对比例7:一种玻璃瓶吹气头,与对比例5的区别在于,回火处理过程中,采用体积相等的、质量百分含量为15%的氯化钠水溶液,替换第一保护混合物。对比例8:一种玻璃瓶吹气头,与实施例1的区别在于,采用等质量的钡基润滑脂代替传热油。试验一:吹制获得的玻璃瓶观察试验试验方法:分别将实施例1-13、对比例1安装在13台h9s-3/4/6组单滴回转式行列制瓶机中,每台制瓶机上均安装相同款的吹气头。将13台制瓶机同时投入生产,采用的熔融玻璃相同,每台制瓶机在生产1000只同类型的玻璃瓶后停止生产。观察采用不同吹气头生产出的玻璃瓶瓶身底部的情况,将出现的大多数情况进行记录。将每台制瓶机生产出的、瓶身底部为光滑、平整、均匀的玻璃瓶的数量进行记录,计算出合格率。试验结果:采用实施例1-13、对比例1生产出的玻璃瓶的瓶身底部情况及合格率如表3所示。表3采用实施例1-13、对比例1生产出的玻璃瓶的瓶身底部情况及合格率由表3可知,采用实施例1-13所吹制出来的玻璃瓶,其瓶身底部绝大多数出现光滑、平整、均匀的现象,且合格率高于99%;而采用对比例1所吹制出来的玻璃瓶,其瓶身底部绝大多数出现凹凸不平等不均匀的现象,合格率低至55%。上述情况说明,在吹气头上进开设一个吹气孔,在吹制玻璃瓶时,吹出的气体过于集中,不能有效地将熔融玻璃吹散,从而也难以使玻璃瓶的底部分布均匀,最终导致了瓶身底部成型凹凸不平的现象。试验二:吹气头使用寿命试验试验方法:分别将实施例1-12、对比例1-8安装在20台h9s-3/4/6组单滴回转式行列制瓶机中,每台制瓶机上均安装相同款的吹气头。将20台制瓶机同时投入生产,采用的熔融玻璃相同,一天24小时进行生产,记录其中一个吹气头出现损坏而无法吹制玻璃瓶时记录该时间,以此时间作为该类吹气头的使用寿命。试验结果:实施例1-12、对比例1-8的使用寿命如表4所示。表4实施例1-12、对比例1-8的使用寿命吹气头使用寿命/天吹气头使用寿命/天实施例11503实施例111518实施例21525实施例121523实施例31561对比例11460实施例41493对比例2516实施例51520对比例3508实施例61575对比例4472实施例71566对比例5477实施例81543对比例6388实施例91469对比例7379实施例101553对比例8362由表4可知,实施例1-12的使用寿命远远高于对比例2-8的使用寿命。对比例2-3中,由于导热材料的选取以及配比不够合理,导致了对比例2-3的导热、散热效果不够好,缩短了其使用寿命;对比例4-5中,由于淬火过程中,吹气头浸入的液体选择不够合理,导致了对比例4-5外部没有保护层,在导热、散热方面不具备优势,最终导致缩短了其使用寿命;对比例6-7中,由于回火过程中,吹气头浸入的液体选择不够合理,导致了对比例6-7外部没有保护层,在导热、散热方面不具备优势,最终导致缩短了其使用寿命;对比例8中,采用的是钡基润滑脂,无法承受高温,因此,导致了无法在吹气头的外部形成保护层,进而导致了获得的对比例8在导热、散热方面不具备优势,最终导致缩短了其使用寿命。本具体实施例仅仅是对本发明的解释,其并不是对本发明的限制,本领域技术人员在阅读完本说明书后可以根据需要对本实施例做出没有创造性贡献的修改,但只要在本发明的权利要求范围内都受到专利法的保护。当前第1页12