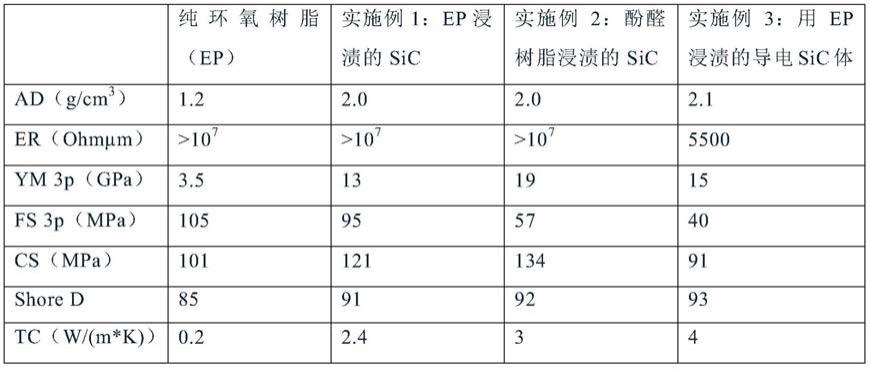
[0001]
本发明涉及一种由含有至少一种硬质材料和塑料的复合材料制造陶瓷组件的方法、通过该方法制造的组件以及使用该组件的方法。
背景技术:[0002]
陶瓷组件通常以即使在高温下仍然高硬度、高耐磨性、高化学稳定性和高强度为特征。由于这些性质,陶瓷组件用在暴露于高机械和/或化学负荷、侵蚀性或腐蚀性介质的任何地方,例如用于泵、管道或喷嘴中。
[0003]
de 10327494 b1描述了包含金属部件和混合铸件的复合泵组件,所述混合铸件是充当粘合剂的塑料与细晶粒的耐磨和耐腐蚀材料的固化混合物。环氧树脂、乙烯基酯树脂或聚甲基丙烯酸酯被列为塑料,而碳化硅(sic)、金刚砂、石英砂、玻璃或这些材料的混合物被列为耐磨和耐腐蚀材料。在这些复合部件的制造中,金属部件用作混合铸件的铸模。制造这些泵组件的缺点是需要铸模,通常只可用数量有限的铸模。因此,由于需要使用铸模,因此该过程昂贵而冗长。此外,混合铸件的形状由铸模的形状决定。
技术实现要素:[0004]
因此,本发明的目的是提供一种不需要铸模的陶瓷组件制造方法,该方法具有较短的加工时间(因此成本较低)并允许以简单的方式制造任何形状的陶瓷组件。
[0005]
在本发明的情形下,通过提供一种由含有至少一种硬质材料和塑料的复合材料制造陶瓷组件的方法来实现该目的,所述方法包括以下步骤:
[0006]
a)提供通过3d打印方法制造的包含至少一种硬质材料的生坯,
[0007]
b)用至少一种液体树脂体系浸渍所述生坯,以及
[0008]
c)使所述浸渍的生坯固化以形成合成树脂基质。
[0009]
根据本发明,已经发现,当通过3d打印来制造所述包含至少一种硬质材料的生坯时,制造陶瓷组件的工艺时间显著减少,也导致工艺的成本更低。另外,因为不需要铸模,可以在更短的时间内制造数量更大的陶瓷组件。
[0010]
在本发明的情形下,硬质材料应理解为莫氏硬度大于/等于(≥)8.5、优选≥9.0、特别优选≥9.3的材料。莫氏硬度以1到10的尺度表示相对硬度值。莫氏硬度为1到2的材料表示软质材料;中等硬度材料的莫氏硬度为3到5,而硬质材料的莫氏硬度为6到10。莫氏硬度通过查明是否材料a能划伤材料b但材料b不会划伤材料a来确定。结果,较硬的材料划伤较软的材料。
[0011]
用于本发明方法的优选的硬质材料是碳化硅(sic)、碳化硼(b4c)或sic和b4c的任何混合物,优选sic。如果将sic或b4c用作唯一的硬质材料,则这些材料作为纯硬质材料使用,即没有与其它材料混合。通过在生坯的制造中使用b4c代替sic,用其制造的陶瓷组件的硬度增加并且该组件的重量降低。如果使用sic和b4c的任何混合物,则所使用的sic与b4c比率取决于陶瓷组件的性质。
[0012]
步骤a)中的生坯通过3d打印方法制造。该方法提供了一种粒度(d50)在10μm和500μm之间、优选在60μm和350μm之间、更优选在70μm和300μm之间、特别优选在75μm和200μm之间的硬质材料粉末,和一种液体粘结剂。这之后在表面上沉积所述粉末的层,然后将液体粘结剂的液滴局部沉积到该层上。重复这些步骤,直到制造出期望的组件形状为止,每个单个步骤针对期望的组件形状进行调适。然后,将所述粘结剂至少部分固化或干燥,产生具有期望的组件形状的生坯。术语“d50”是指50%的粒子小于给定值。d50值借助于激光粒度测定法(iso 13320)、使用sympatec gmbh的测量装置与相关评价软件来确定。
[0013]
为了制造包含多于一种硬质材料的生坯,将硬质材料sic和b4c的混合物用于表面沉积步骤。单个硬质材料的粉末具有上述粒度。
[0014]
获得具有期望的组件形状的生坯具有以下含义。粘结剂固化或干燥后即刻,生坯仍被松散的粉状组合物粒子的粉末覆盖物包围。因此,必须将生坯从粉末覆盖物中取出或与松散的未压实粒子分开。在3d打印文献中,这也被称为将所打印部件“解封”。生坯解封之后,可以对生坯进行(细致的)清洁以除去粘附的粒子残留物。例如,可以用功能强大的抽吸装置真空吸去松散的粒子,从而实现解封。然而,解封的类型没有特别限定,可以使用所有已知的方法。
[0015]
在生坯的制造期间,向所述至少一种硬质材料添加液体活化剂、例如液体硫酸活化剂会是有利的。通过使用这样的活化剂,一方面可以减少固化所述粘结剂的固化时间和所需温度,另一方面减少粉状组合物的粉尘形成。有利地,基于所述至少一种硬质材料和活化剂的总重量,活化剂的量为0.05重量%至0.2重量%。如果使用基于活化剂和所述至少一种硬质材料的总重量的大于0.2重量%,则所述粉状组合物会粘在一起并且流动性会降低;如果使用基于活化剂和所述至少一种硬质材料的总重量的少于0.05重量%,则可以与粘结剂、更确切地说是与粘结剂的树脂组分起反应的活化剂的量将太少而无法实现期望的上述优点。
[0016]
用于制造所述3d打印生坯的粘结剂的选择没有特别限制。合适的粘结剂是例如酚醛树脂、呋喃树脂、水玻璃或这些的任何混合物。在此也包括所提到的粘结剂的溶液。这些粘结剂的优点在于它们只需要硬化或干燥,这使制造过程更具成本效益。优选呋喃树脂和酚醛树脂,因为相应的生坯具有特别高的稳定性,并且这些粘结剂在可能碳化的情况下只形成碳。
[0017]
优选地,基于生坯的总重量,所述生坯中粘结剂的比例为1.0至10.0重量%,最优选1.5至6.0重量%。
[0018]
在本发明的范围内,根据步骤b),用至少一种液体树脂体系浸渍所述生坯。在此,液体树脂体系包含至少一种树脂、至少一种溶剂和至少一种硬化剂,其中所述至少一种树脂和所述至少一种溶剂可以是相同的。
[0019]
优选的液体树脂体系是通过缩聚反应或加聚反应转化为合成树脂基质的树脂体系。缩聚反应是通过稳定但仍具有反应性的中间产物分阶段进行的缩合反应,其中大分子例如聚合物或共聚物是由许多低分子物质(单体)通过裂解掉构造简单的分子、通常是水而形成的。这些大分子也称为缩聚物。为了单体参与反应,单体必须具有至少两个特别具有反应性的官能团,例如-oh。该过程接连进行数次,直到形成大分子。加聚反应应理解为代表一种聚合物形成形式的反应,其根据单体亲核加成到聚加合物的机制而发生。在该过程中,通
过转移质子、即从一个基团转移到另一个基团,将不同类型的分子连接到至少两个官能团上。对此的前提是分子类型的官能团含有双键。与缩聚相似,加聚也分阶段进行,但不形成低分子副产物,例如水。使用通过加聚反应转化为合成树脂基质的液态树脂体系导致具有高强度的比较致密的陶瓷组件,而使用通过缩聚反应转化为合成树脂基质的液体树脂体系导致具有高化学稳定性和特别高的温度稳定性的陶瓷组件。
[0020]
优选地,所述至少一种通过加聚反应转化为合成树脂基质的液体树脂体系表示环氧树脂、聚氨酯树脂或苯并嗪树脂,而所述至少一种通过缩聚反应转化为合成树脂基质的液体树脂体系表示酚醛树脂或呋喃树脂。环氧树脂或聚氨酯树脂的特征在于它们的机械稳定性特别高,即抗弯强度高,而酚醛树脂或呋喃树脂的特征在于它们的化学稳定性特别高,即使在特别高的温度下也是如此,并且温度稳定性高。苯并嗪树脂的特征在于,它们兼有已通过加聚反应或缩聚反应转化为树脂基质的树脂的有利性质。当固化形成合成树脂基质时,苯并嗪树脂不会裂解出副产物,例如水,并且该基质的温度稳定性高。该至少一种液体树脂体系也可以是已通过加聚反应转化为合成树脂基质的树脂体系和已通过缩聚反应转化为合成树脂基质的树脂体系的任何混合物。例如,因此可以使用环氧树脂与呋喃树脂或酚醛树脂的混合物,或聚氨酯树脂与呋喃树脂或酚醛树脂的混合物,或苯并嗪树脂与呋喃树脂或酚醛树脂的混合物。
[0021]
根据步骤b)的用至少一种液体树脂体系浸渍可以通过喷涂、沉浸、刷涂、真空浸渍或通过真空压力浸渍来进行。对于真空浸渍,所用的真空取决于所述至少一种液体树脂体系的溶剂的沸点。在真空压力浸渍的情况下,所使用的压力取决于用于真空压力浸渍的设备。取决于所述体系,可以使用通常最高16巴的压力。
[0022]
根据本发明方法的步骤c)的固化应理解为是指完全固化。该固化优选在室温下或通过施加60℃至250℃、更优选120℃至200℃的温度来进行。
[0023]
根据本发明的另一个优选实施方式,将步骤b)的用至少一种通过缩聚转化为合成树脂基质的液体树脂体系浸渍和步骤c)的固化的步骤重复至少一次。通过本发明方法的步骤b)和c)的这种重复,增加了陶瓷组件的抗弯强度。在缩聚期间,裂解掉的分子(通常是水)逸出,从而在组件中生成孔隙。固化后,这些孔在用上述至少一种液体树脂体系进行下一次浸渍期间被填充。
[0024]
根据本发明的另一个优选实施方式,在步骤b)中进行用至少一种通过缩聚反应转化为合成树脂基质的液体树脂体系浸渍,并且在步骤c)的固化之后,进行步骤d)的碳化所述固化组件,随后是步骤e)用通过加聚反应或缩聚反应转化为合成树脂基质的液体树脂体系浸渍所述碳化体和f)使所述浸渍体固化以形成合成树脂基质。当sic用作硬质材料时,优选使用该实施方式。
[0025]
上述步骤d)的术语“碳化”应理解为是指生坯所含的树脂体系热转化为碳。碳化可以通过在惰性气体气氛(例如氩气或氮气气氛)中加热到在500℃-1100℃范围内、优选从800℃至1000℃的温度以及随后的保持时间来进行。
[0026]
步骤b)的液体树脂体系中通过缩聚反应转化为合成树脂基质的树脂,在碳化过程期间转化为碳,其结果是在硬质材料晶粒之间形成了导电粘结剂桥。这显著增加了相应陶瓷组件的电导率,尤其是当使用sic作为硬质材料时。作为缩聚树脂的替代品,也可以使用苯并嗪树脂,因为这类树脂在碳化步骤期间也显示出与典型的缩聚树脂、例如酚醛树脂
或呋喃树脂一样的碳得率。通过在步骤e)的浸渍所述碳化体时使用液体树脂体系,该体系通过加聚反应转化为合成树脂基质,实现了陶瓷组件的抗渗性和强度增加。
[0027]
本发明还涉及由含有至少一种硬质材料和塑料的复合材料制成的陶瓷组件,该组件可以根据本发明的上述方法来制造。
[0028]
优选地,本发明的组件的比电阻小于10,000μohm*m,优选小于7,000μohm*m。本发明的组件还优选具有大于/等于90的肖氏硬度d。肖氏硬度代表塑料的特征值。在确定肖氏硬度时,使用由硬化钢制成的弹簧加荷钉,该钉在待测材料中的穿透深度是肖氏硬度的量度。肖氏硬度在0肖氏(2.5毫米穿透深度)到100肖氏(0毫米穿透深度)的尺度上测量。因此,数字高意味着硬度大。
[0029]
另外,本发明的组件优选热导率为至少2.0w/(m
·
k),更优选至少3.0w/(m
·
k)。
[0030]
本发明的组件的强度取决于用来浸渍生坯的所述至少一种液体树脂体系。如果用至少一种通过加聚反应进行反应的液体树脂体系进行浸渍,则达到至少80mpa的强度;另一方面,如果用至少一种通过缩聚反应进行反应的液体树脂体系进行浸渍,则相应的组件的强度为至少40mpa。
[0031]
本发明的组件征在于比较高的电导率和热导率。另外,这些组件的热膨胀低,即,即使在超过1,000℃的高温下,它们在一定时间内仍然是尺寸稳定的。含有sic作为硬质材料的本发明组件尤其如此。如果将sic用作硬质材料并且如果将通过缩聚反应转化为合成树脂基质的树脂体系、例如呋喃树脂或酚醛树脂用作至少一种液体树脂体系,也可以实现高温下的稳定性。当施加超过1,000℃的温度时,发生原位碳化。然而,也可以在上述浸渍步骤之后施行碳化步骤。该碳化步骤之后可以进行用相同液体树脂体系的进一步浸渍步骤;在此再次发生原位碳化。这些实施方式在用作高温模制工具领域中的材料时特别重要。
[0032]
由于前述的有利特性,本发明的组件可以用于各种应用中。在最高220℃的温度下,本发明的组件,取决于所使用的液体树脂体系,适合作为泵和压缩机中的叶轮和截止或旋转阀、作为泵壳、作为分级轮、作为塔的内部构件、作为静态混合元件、作为湍流器、作为喷雾嘴、以及作为用于防护磨损和在腐蚀性应用中的衬里元件。如果本发明的该组件要具有高不可渗透性和高强度,例如当用作泵和压缩机中的叶轮和截止阀或旋转阀或用作泵壳时,可以使用环氧树脂作为液体树脂体系。在本发明的组件要具有高化学和温度稳定性的情况下,例如当用作塔的内部构件、用作静态混合元件或用于腐蚀性应用时,可以使用酚醛树脂或呋喃树脂。在高于220℃的温度下,本发明的组件可以用作电热元件或用作氧化稳定性高温模具用于浇铸、烧结或压制。例如,这样的高温模具可用于制造钻头。这些高温模具优选通过所述方法的变体制造,所述方法变体具有用至少一种通过缩聚反应转化为合成树脂基质的液体树脂体系的中间浸渍、并具有碳化步骤。
具体实施方式
[0033]
下面,通过示例性而非限制性的实施例描述本发明。
[0034]
实施例:
[0035]
可以如下所述进行使用碳化硅作为本发明我们的方法的步骤a)的硬质材料来制造生坯。
[0036]
使用粒度为f80(根据fepa标准的粒度)的碳化硅。将其首先与基于碳化硅和活化
剂的总重量为0.1重量%的酚醛树脂用硫酸液体活化剂混合,并用3d打印粉末床机器加工。刮刀单元在平坦的粉末床上放置碳化硅粉末薄层(高约0.3mm),喷墨打印单元根据期望的组件几何形状将酚醛树脂醇溶液印刷到碳化硅粉末床上。然后将打印台下降所述层的厚度,施加另一层碳化硅并再次局部印刷酚醛树脂。通过重复该程序,构建了尺寸为例如120mm(长)
×
20mm(宽)
×
20mm(高)的立方形试样。一旦打印了完整的“组件”,就将所述粉末床放入预热至160℃的烘箱中,并在此保持约20小时,在此期间,酚醛树脂完全固化并形成尺寸稳定的生坯。然后在冷却后,真空吸去多余的碳化硅粉末,并取出生坯。确定试样的几何密度为1.45g/cm3,
[0037]
本发明的实施例1:
[0038]
将通过3d打印方法制造的碳化硅基生坯用液体环氧树脂体系真空浸渍。来自ebalta的环氧树脂由100份室温(rt)粘度为约800mpas的树脂和30份rt粘度为约55mpas的相应的快速固化硬化剂组成。环氧树脂体系的适用期根据制造商的说明书陈述为50-60分钟。将试样完全浸入所述液体树脂体系中,并抽空至约100毫巴。试样在真空下在所述树脂体系中再浸渍30分钟,该时间之后,使其达到环境压力,从容器中取出并从表面清洁粘附的树脂。在室温下保存并随后在60℃下固化后,从该棒材通过机械做出用于物理测试的相应试样几何形状。试样的密度为2.0g/cm3。最终可得到得研磨品质的试样表面。
[0039]
本发明的实施例2:
[0040]
将通过3d打印方法制造的碳化硅基生坯进行真空压力浸渍,用20℃下的粘度为700mpas并且根据karl fischer(iso 760)的含水量为约15%的酚醛树脂(hexion)进行,而不是用环氧树脂浸渍。程序如下:将所述碳体放置在浸渍容器中。施加树脂后,将容器中的压力降至10毫巴并升至11巴。10小时的停留时间后,将碳试样从浸渍容器中取出,并在11巴的压力下加热至160℃以固化树脂。加热时间约为2小时,在160℃的停留时间约为10小时。缩聚固化后,冷却的试样的密度为2.0g/cm3。
[0041]
本发明的实施例3:
[0042]
将使用3d打印方法制造的碳化硅基生坯首先用呋喃树脂进行沉浸式浸渍。呋喃树脂浸渍的优点是呋喃树脂体系的粘度极低,小于100mpas,这意味着无需真空或压力即可实现完全的浸渍。使用以下程序:将样本放置在玻璃容器中,并将预先制备的一份马来酸酐(aug.hedinger gmbh&co.kg)和10份糠醇(international furan chemicals b.v.)的溶液倒在其上。将试样完全浸没在所述溶液中,完全渗透时间为2小时(在室温下)。糠醇/马来酸酐溶液渗透后,将样本移出并用网格布表面清洁。用树脂浸泡的样本然后在干燥箱中固化。温度从50℃逐渐增至150℃。实际的固化程序如下:50℃下19小时,70℃下3小时,100℃下3小时,最后150℃下1.5小时。固化后测得呋喃树脂浸渍的试样的平均密度为1.70-1.75g/cm3。固化后,将浸渍的sic生坯在氮气气氛中于900℃碳化。对于碳化处理,选择在900℃下经过3天的缓慢加热曲线,以确保生坯不会由于溶剂、即水的突然蒸发而破裂。在碳化处理期间,呋喃树脂转化为碳,并由此在sic晶粒之间形成导电的粘结剂桥。最后,用实施例1的环氧树脂浸渍所述碳化体并进一步加工。
[0043]
对实施例1-3的所有试样进行材料表征。这些测试的结果显示在下表中,其中包括纯环氧树脂的测量结果作为比较:
[0044][0045]
ad(g/cm3):密度(几何密度),根据iso 12985-1
[0046]
er(ohmμm):电阻,根据din 51911
[0047]
ym 3p(gpa):弹性模量(刚度),由根据en iso 178的三点弯曲试验确定
[0048]
fs 3p(mpa):三点抗弯强度,根据en iso 178
[0049]
cs(mpa):抗压强度,根据en iso 604
[0050]
shore d:肖氏硬度,根据din iso 7619-1
[0051]
tc(w/(m*k)):室温下的热导率,根据din 51908
[0052]
具有环氧树脂基质的sic复合材料(实施例1和3)显示出比具有酚醛树脂基质的sic复合材料更高的强度,但是后者更加温度稳定并且更加化学稳定。关于浸渍所需的努力,sic生坯可以用呋喃树脂简单通过浸没法浸渍(实施例3中的部分方法步骤),而酚醛树脂和环氧树脂则由于通常粘度较高而必须通过真空浸渍法或真空压力浸渍法来浸渍。环氧树脂的固化机理是加聚,其导致复合材料相对致密。缩聚树脂例如苯酚树脂或呋喃树脂通常具有致密度低得多的结构。
[0053]
在实施例3中,通过用供碳树脂(在此为呋喃树脂)中间浸渍并随后碳化处理,形成了具有碳粘结剂桥的导电sic网络。通过随后的环氧树脂浸渍填充孔隙,产生具有良好的机械性质和良好的电导率的渗透复合材料。
[0054]
与纯环氧树脂相比,添加硬质材料显著降低热膨胀,热膨胀可以根据din 51909确定。与实施例2的具有酚醛树脂基质的sic复合材料相比,实施例1的具有环氧树脂基质的sic复合材料显示出高的热膨胀。因此,如果需要尺寸稳定性高并由此需要热膨胀低的话,则单独具有酚醛树脂基质或呋喃树脂基质或随后进行碳化步骤并用酚醛树脂或呋喃树脂再浸渍的sic复合材料是优选的。