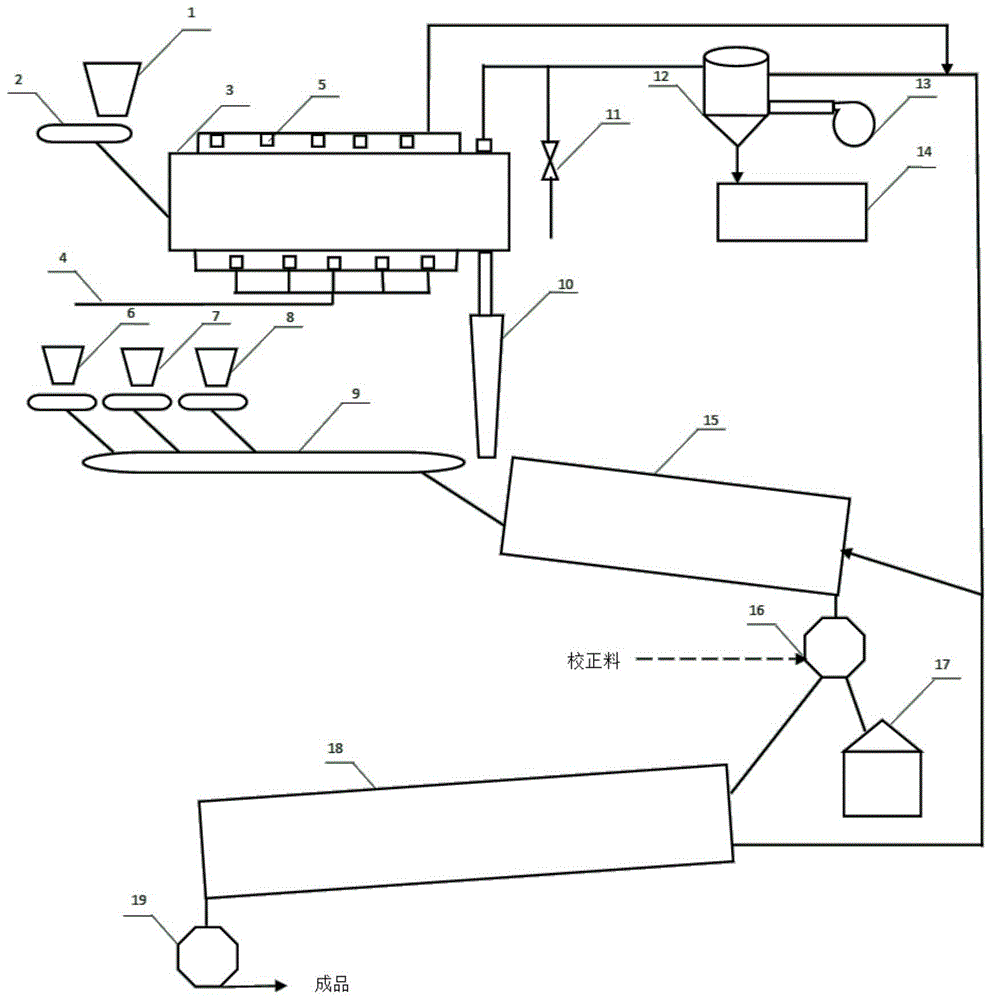
本发明涉及铝加工、建材技术及大宗工业固废的资源综合利用和环境保护治理领域,涉及一种铝灰预处理的全固废制备硫铝酸盐水泥的方法及系统。
背景技术:
:公开该
背景技术:
部分的信息仅仅旨在增加对本发明的总体背景的理解,而不必然被视为承认或以任何形式暗示该信息构成已经成为本领域一般技术人员所公知的现有技术。工业固废是工业生产过程中排入环境的各种废渣、粉尘及其他废物,可分为一般工业废物(如高炉渣、钢渣、赤泥、尾矿、粉煤灰、脱硫灰、电石渣、盐泥等)和工业有害固体废物。我国工业固废的年产量基本维持在30亿吨左右,而利用率基本维持在22%~25%,工业固废总产量的同比增长率从2012年后基本维持不变,工业固废利用量的同比增长率逐年攀升,虽然工业固废利用量的增长率逐年增加,但每年依旧有近20亿吨的工业固废未被处置,其中个别工业固废成分复杂,利用难度极大,总新增存量270亿吨。铝灰是工业有害固体废物中的一种,主要产生在电解槽排出的铝液及铸造环节,其主要成分为al、al2o3、aln和一定量的氟化物、氯化物组成,在有水或者潮湿环境下会产生氨气,影响堆存场处周边生态安全。在一次铝工业生产中,每生产1吨铝要产生30-50千克铝灰,在二次铝工业生产过程中,每加工一吨铝仍将产生30-40千克铝灰,同时在消费环节每年将产生20-25万吨铝渣,因此每年以铝生产、铝加工、铝消费等各环节产生的铝灰在300万吨以上,加上前期铝工业发展过程中堆存的铝灰,铝灰的总量至少在2000万吨以上。现有铝灰回收和利用方法中,二次铝灰中铝的回收、热处理方法基本都存在回收效率与高能耗之间的矛盾,而冷处理方法虽然能耗较低,但铝回收率也低,同时二次污染较大。近年来,硫铝酸盐水泥成为国内外水泥行业研究发展的新方向,其水泥熟料具有生产所需要的热耗低、早期强度高、凝结时间短、极好的抗冻融性、碱度低等一系列优异性能,现被广泛的应用在抢修、抢建工程、冬季施工工程、抗腐蚀工程。现有技术中生产硫铝酸盐水泥所用的基本原材料是石灰石、铝矾土和石膏,石灰石作为钙质原料主要是提供硫铝酸盐水泥熟料形成过程中所需要的氧化钙成分,铝矾土作为铝制原料主要提供硫铝酸盐水泥熟料形成过程中所需要的氧化铝成分;石膏作为硫质原料主要提供硫铝酸盐水泥熟料形成过程中所需要的三氧化硫成分。据本发明的发明人了解,目前已有铝灰作为硫铝酸盐水泥制备过程中氧化铝原料的研究,然而,这些研究仅限于实验室研究及中试,并没有广泛应用在实际生成中。而在实际的生产中,确实有一些生产企业向原料中添加一定量铝灰替代铝矾土,降低原料成本。然而,经过本发明的发明人实际应用中发现,当采用铝灰代替部分铝矾土时,使得回转窑尾部更容易结圈、冷凝器堵塞,难以长时间运行,更无法将铝灰完全代替铝矾土。技术实现要素:为了解决现有技术的不足,本发明的目的是提供一种铝灰预处理的全固废制备硫铝酸盐水泥的方法及系统,能够使得回转窑尾部不易结圈、避免冷凝器堵塞,保证长时间运行,而且能够完全代替铝矾土。为了实现上述目的,本发明的技术方案为:一方面,一种利用铝灰制备硫铝酸盐水泥的方法,将铝灰加热至不低于900℃进行热处理,将热处理后的铝灰作为铝源制备硫铝酸盐水泥;所述铝灰包括二次铝灰或所述铝灰为二次铝灰。在实际生产中发现,直接采用铝灰代替部分铝矾土时,铝灰最多能代替30%的铝矾土,而当铝灰代替30%的铝矾土时,使得回转窑尾部更容易结圈及堵塞冷凝器。经过本发明的发明人研究发现,铝厂制备铝的工艺一般为电解法,因而铝厂产生的铝灰中存在氯化钠、氯化钾等盐,在回转窑中制备水泥时,在氯化钠、氯化钾等盐容易在煅烧过程被水蒸气、二氧化碳等气体带出,从而在回转窑尾部沉积,从而造成回转窑尾部更容易结圈。因而本发明的发明人在初始研究的主要工作是将铝灰中的氯化钠、氯化钾等盐去除,由于氯化钠、氯化钾易溶于水,因而优先选择溶液法(例如在水中进行均化等)。仅利用水进行均化后,可以完全去除氯化钠、氯化钾等盐,也能够增加铝灰代替铝矾土的量,但是,随着水均化后的铝灰量的增多,仍然容易出现结圈及堵塞冷凝器现象,而且随着铝灰量的增多,还会产生明显的刺激性气味,无法正常生产硫铝酸盐水泥。进一步研究发现,铝灰中还含有铝单质,铝单质的熔点较低,其在回转窑中先融化后造成结大块,造成窑炉出口下料困难。经过对刺激性气味气体的分析,该气体主要为氨气,对铝灰进行进一步研究发现,铝灰分为一次铝灰和二次铝灰,而铝厂一般会对一次铝灰进行在利用,导致其产生的铝灰中二次铝灰的含量更高,二次铝灰中存在氮化铝(aln)更多,采用水进行均化处理时,容易产生氨气,而铝灰量的增加,导致氮化铝的量增加,从而提高氨气的产生。因而为了去除铝单质和氮化铝,去除相应影响,一般会在添加化学试剂进行相应处理,从而解决相应问题。然而,经过更进一步研究发现,添加化学试剂后产生高盐废水,高盐废水难以处理,而且极大的增加的工序,增加企业成本。本发明采用不低于900℃的温度对包括二次铝灰的铝灰进行处理,经过研究发现,当处理温度为700℃时,氮化铝发生脱氮反应,逐渐变成氧化铝;而当温度为900℃以上时,能够不仅能够保证氮化铝基本转化成氧化铝,而且使得氯化钠、氯化钾等盐类气化,同时,铝单质也能够被处理成为氧化铝。经过不低于900℃热处理的包括二次铝灰的铝灰,基本以al2o3和mgal2o4矿物存在,从而完全代替铝矾土使用。经过实际操作发现,采用本发明热处理后的铝灰铝源完全代替铝矾土制备硫铝酸盐水泥,解决了回转窑生产过程中的尾部结圈、堵塞冷凝器的现象。由于目前工业固废(例如赤泥、脱硫石膏、电石渣等)存在难以处理的问题,同时热处理铝灰需要消耗大量的能量,为了对工业固废进行再利用及减少能量的消耗,本发明的另一方面,一种铝灰预处理的全固废制备硫铝酸盐水泥的方法,将铝灰加热至不低于900℃进行热处理,将热处理后的铝灰与赤泥、脱硫石膏、电石渣进行均化混合,利用热处理产生的热气体对混合后的物料进行干燥,再将干燥后的物料进行生粉配比粉磨,将生粉配比粉磨后的物料进行煅烧,获得硫铝酸盐水泥熟料;所述铝灰包括二次铝灰或所述铝灰为二次铝灰。本发明热处理铝灰过程中产生大量余热,例如热处理后的铝灰含有大量余热,热处理后产生的热气体(烟气热量、煅烧铝灰产生的废气热量),而赤泥、脱硫石膏、电石渣含有较多的水分,利用热处理铝灰过程中产生的余热对赤泥、脱硫石膏、电石渣进行干燥处理,增加了能源利用率、降低能耗,还能实现对工业固废的处理,将经济价值最低的废物转变为经济价值更高的硫铝酸盐水泥。为了实现上述铝灰预处理的全固废制备硫铝酸盐水泥,本发明的第三方面,一种实现上述铝灰预处理的全固废制备硫铝酸盐水泥的方法的系统,包括间接转筒加热炉、旋风冷凝器、干燥器、原料粉磨机、回转窑,间接转筒加热炉的进口设置为用于连接铝灰源,间接转筒加热炉的固相出口连接干燥器的物料进口,间接转筒加热炉的气相出口连接旋风冷凝器的进口,旋风冷凝器的气相出口连接干燥器的换热气体进口,干燥器的物料进口还设置为用于连接赤泥源、脱硫石膏源、电石渣源,干燥器的物料出口连接原料粉磨机的进口,原料粉磨机的出口连接回转窑进口。本发明采用间接转筒加热炉,对铝灰进行间接加热。与直接加热相比,间接加热能够防止燃料燃烧后产生的烟气将铝灰带出,若铝灰被烟气带出,则会导致铝灰难以与烟气中的烟尘分离,从而难以对铝灰进行再利用。同时,间接换热可以将钠、钾盐类气化的气体进行抽取,进入冷凝器冷凝收集。本发明的有益效果为:1.本发明对铝灰进行热处理能够大大降低铝灰中的氮化铝、氯化钠、氯化钾等杂质,采用热处理后的铝灰制备硫铝酸盐水泥能够使得回转窑尾部不易结圈、避免冷凝器堵塞。大幅度提高铝灰、赤泥等大宗工业固废的再生产品附加值,显著降低了工艺的控制难度。2.本发明对铝灰进行热处理能够大大提高制备硫铝酸盐水泥中铝灰的利用率,降低了二次铝灰处理的费用与能耗。3.本发明采用热处理后的余热与与赤泥、脱硫石膏、电石渣混合换热,余热再次进入原料系统中,更节能环保。4.本发明可从根本上更大程度地同时使危险工业固废和一般工业固废减量化、稳定化、无害化与资源化。附图说明构成本发明的一部分的说明书附图用来提供对本发明的进一步理解,本发明的示意性实施例及其说明用于解释本发明,并不构成对本发明的不当限定。图1为本发明实施例1的系统结构示意图;图2为本发明实施例1采用的铝灰未煅烧前的xrd图;图3为本发明实施例1采用的铝灰煅烧后的xrd图;其中,1.料斗,2.自动称量称,3.间接转筒加热炉,4.天然气,5.燃烧器喷嘴,6.赤泥储仓,7.脱硫石膏储仓,8.电石渣储仓,9.皮带输送机,10.下料管路,11.抽气器,12.旋风冷凝器,13.冷却风机,14.储盐仓,15.回转干燥筒,16.原料粉磨机,17.干原料仓,18.回转窑,19.材料粉磨机。具体实施方式应该指出,以下详细说明都是示例性的,旨在对本发明提供进一步的说明。除非另有指明,本文使用的所有技术和科学术语具有与本发明所属
技术领域:
的普通技术人员通常理解的相同含义。需要注意的是,这里所使用的术语仅是为了描述具体实施方式,而非意图限制根据本发明的示例性实施方式。如在这里所使用的,除非上下文另外明确指出,否则单数形式也意图包括复数形式,此外,还应当理解的是,当在本说明书中使用术语“包含”和/或“包括”时,其指明存在特征、步骤、操作、器件、组件和/或它们的组合。鉴于实际生产中铝灰难以完全代替铝矾土,且采用铝灰代替部分铝矾土时,存在回转窑尾部更容易结圈、冷凝器堵塞等问题,本发明提出了一种铝灰预处理的全固废制备硫铝酸盐水泥的方法及系统。本发明的一种典型实施方式,提供了一种利用铝灰制备硫铝酸盐水泥的方法,将铝灰加热至不低于900℃进行热处理,将热处理后的铝灰作为铝源制备硫铝酸盐水泥;所述铝灰包括二次铝灰或所述铝灰为二次铝灰。本发明采用不低于900℃的温度对包括二次铝灰的铝灰进行处理,经过研究发现,当处理温度为700℃时,氮化铝发生脱氮反应,逐渐变成氧化铝;而当温度为900℃以上时,能够不仅能够保证氮化铝基本转化成氧化铝,而且使得氯化钠、氯化钾等盐类气化,同时,铝单质也能够被处理成为氧化铝。经过不低于900℃热处理的包括二次铝灰的铝灰,基本以al2o3和mgal2o4矿物存在,从而完全代替铝矾土使用。经过实际操作发现,采用本发明热处理后的铝灰铝源完全代替铝矾土制备硫铝酸盐水泥,解决了回转窑生产过程中的尾部结圈、堵塞冷凝器的现象。本发明上述方法的目的在于在实际生产硫铝酸盐水泥中,将铝灰处理为可以代替铝矾土的铝源,采用热处理后的铝源可以代替任何现有技术中的硫铝酸盐水泥中的铝源;例如:1.现有生产中采用石灰石、铝矾土和石膏制备硫铝酸盐水泥(《硫铝酸盐水泥的生产与应用》刁江京,辛志军,张秋英著北京:中国建材工业出版社2006);2.现有利用含有铝灰生产硫铝酸盐水泥的制备(cn201810935060.0、cn201710159992.6、cn201710159979.0等);或者,其他现有记载的硫铝酸盐水泥的制备。该实施方式的一种或多种实施例中,热处理的温度为900~950℃。该实施方式的一种或多种实施例中,热处理铝灰的加热方式为间接加热。为了对热处理铝灰消耗的能量进行有效利用同时对工业固废的协同处理,本发明的另一种实施方式,提供了一种铝灰预处理的全固废制备硫铝酸盐水泥的方法,将铝灰加热至不低于900℃进行热处理,将热处理后的铝灰与赤泥、脱硫石膏、电石渣进行均化混合,利用热处理产生的热气体对混合后的物料进行干燥,再将干燥后的物料进行生粉配比粉磨,将生粉配比粉磨后的物料进行煅烧,获得硫铝酸盐水泥熟料;所述铝灰包括二次铝灰或所述铝灰为二次铝灰。本发明中所述的脱硫石膏为电厂脱硫后的副产石膏。本发明中所述的赤泥为氧化铝厂排放的废弃物赤泥。本发明中所述的电石渣为电石水解获取乙炔气后的以氢氧化钙为主要成分的废渣。本发明中所述的生粉配比粉磨为按比例添加干物料、混合、粉磨、均化。该实施方式的一种或多种实施例中,热处理的温度为900~950℃。原铝灰中含有大量的al、aln、al2o3、nacl等矿物,在经过900~950℃高温脱氮、脱盐反应后,铝灰中aln、nacl、al矿物基本消失,基本以al2o3和mgal2o4矿物存在,经处理后的铝灰可作为高品位铝矾土使用,减少了大量自然的使用,较大范围内降低原料成本。本发明热处理铝灰过程中产生大量余热,例如热处理后的铝灰含有大量余热,热处理后产生的热气体(烟气热量、煅烧铝灰产生的废气热量),而赤泥、脱硫石膏、电石渣含有较多的水分,利用热处理铝灰过程中产生的余热对赤泥、脱硫石膏、电石渣进行干燥处理,增加了能源利用率、降低能耗,还能实现对工业固废的处理,将经济价值最低的废物转变为经济价值更高的硫铝酸盐水泥。该实施方式的一种或多种实施例中,赤泥、脱硫石膏、电石渣、铝灰的质量比为15~25:20~30:30~40:15~25。能够减少干燥粉磨后的校正操作。该实施方式的一种或多种实施例中,干燥后物料的水分低于5%质量百分数。该实施方式的一种或多种实施例中,生粉配比粉磨后的物料粒径低于8μm。该实施方式的一种或多种实施例中,生粉配比粉磨后的成分,sio210~25wt%,cao20~30wt%,al2o320~30wt%,fe2o35~15wt%,so320~30wt%。该系列实施例中,碱度系数cm为0.90~1.05。其中,碱度系数的公式为:式中cao、sio2、al2o3、fe2o3、tio2、so3分别为相应化学成分所占的重量百分比。该实施方式的一种或多种实施例中,煅烧的温度为1230~1260℃。煅烧时间为30~50min。该实施方式的一种或多种实施例中,热处理铝灰的加热方式为间接加热。该系列实施例中,热处理产生的烟气直接对物料进行干燥,热处理铝灰产生的废气经过旋风分离后对物料进行干燥。该实施方式的一种或多种实施例中,采用天然气经燃烧器在回转窑内物料进行煅烧,过量空气系数控制在1.1~1.15之间。该实施方式的一种或多种实施例中,将硫铝酸盐水泥熟料与脱硫石膏混合粉磨获得硫铝酸盐水泥。为了实现上述铝灰预处理的全固废制备硫铝酸盐水泥,本发明的第三种实施方式,提供了一种实现上述铝灰预处理的全固废制备硫铝酸盐水泥的方法的系统,包括间接转筒加热炉、旋风冷凝器、干燥器、原料粉磨机、回转窑,间接转筒加热炉的进口设置为用于连接铝灰源,间接转筒加热炉的固相出口连接干燥器的物料进口,间接转筒加热炉的气相出口连接旋风冷凝器的进口,旋风冷凝器的气相出口连接干燥器的换热气体进口,干燥器的物料进口还设置为用于连接赤泥源、脱硫石膏源、电石渣源,干燥器的物料出口连接原料粉磨机的进口,原料粉磨机的出口连接回转窑进口。本发明采用间接转筒加热炉,对铝灰进行间接加热。与直接加热相比,间接加热能够防止燃料燃烧后产生的烟气将铝灰带出,若铝灰被烟气带出,则会导致铝灰难以与烟气中的烟尘分离,从而难以对铝灰进行再利用。该实施方式的一种或多种实施例中,包括储盐仓,所述旋风冷凝器的固相出口连接储盐仓。该实施方式的一种或多种实施例中,包括材料粉磨机,回转窑的出口连接材料粉磨机。该实施方式的一种或多种实施例中,包括除尘器,所述回转窑的烟气出口连接除尘器。该实施方式的一种或多种实施例中,干燥器为回转烘干器。能够直接利用热处理的空气余热对赤泥、脱硫石膏、电石渣进行换热,提高能量利用率。本发明所述的间接转筒加热炉,在转筒壁外侧设置燃烧器,燃烧器对转筒壁进行加热,通过对转筒壁的传热对转筒内的物料进行加热,例如回转焙烧炉等。为了使得本领域技术人员能够更加清楚地了解本发明的技术方案,以下将结合具体的实施例详细说明本发明的技术方案。实施例1铝灰预处理的全固废制备硫铝酸盐水泥的系统,如图1所示,料斗1、自动称量称2、间接转筒加热炉3、燃烧器喷嘴5、赤泥储仓6、脱硫石膏储仓7、电石渣储仓8、皮带输送机9、下料管路10、抽气器11、旋风冷凝器12、冷却风机13、储盐仓14、回转干燥筒15、原料粉磨机16、干原料仓17、回转窑18、材料粉磨机19。铝灰首先经过料斗1下料到自动称量称2,经皮带输送机送入到间接转筒加热炉3内,天然气4经过燃烧器喷嘴5对间接转筒加热炉3加热,实现对间接转筒加热炉3内的铝灰高温煅烧脱氮、脱盐,经高温煅烧脱氮、脱盐处理后的铝灰经下料管路10直接进入到回转干燥筒15内,赤泥储仓6、脱硫石膏储仓7、电石渣储仓8内的原料经过皮带输送机9输送至回转干燥筒15内,在回转干燥筒15热处理后的铝灰、赤泥、脱硫石膏、电石渣进行原料的预混合、预均化;间接转筒加热炉3产生的高温余热烟气,经引风机送入到回转干燥筒15内;间接转筒加热炉3内产生的含盐、含碱废气经抽气器11送入旋风冷凝器12,盐类、碱类的冷却后进入储盐仓14进行收集,而含有余热的废气经引风机送入到回转干燥筒15内,进行物料的烘干。在回转干燥筒15内经配料、均化后的原料,进行原料校核,校核后的原料送入原料粉磨机16中粉磨。粉磨后的一部分物料进入回转窑18进行高温煅烧获得硫铝酸盐熟料,另一部分物料进入干原料仓17中进行储存,硫铝酸盐熟料与脱硫石膏进入材料粉磨机19进行混合粉磨获得硫铝酸盐水泥,回转窑内产生的含有尘烟气经过除尘器除尘,达到环保标准在排放。间接回转加热炉将单一铝灰废弃物经间接煅烧脱氮、脱盐、脱碱处理后与赤泥、脱硫石膏、电石渣湿物料一起输送至回转干燥筒内。经间接加热的铝灰产生的脱氮、脱盐废气送入旋风冷凝器中。经加热间接脱氮的铝灰含有一定量的热量,送入回转干燥筒中与赤泥、脱硫石膏、电石渣等原料进行混合换热,同时自回转窑抽来的热量对回转干燥筒内物料进行继续换热,实现物料能量的多级利用。回转窑的产生的含有尘、二氧化硫的烟气进入回转烘干筒进行原料的烘干后再进入除尘器除尘。工艺流程如下:1.将按原料配比量的铝灰(赤泥、脱硫石膏、电石渣、铝灰的质量比为20:25:35:20)经自动给料系统送入间接回转加热器内,天然气经低氮燃烧器进行燃烧,燃气喷嘴进行交叉布置,燃烧燃气均匀的送入腔体内,对滚筒内的铝灰进行间接加热,当加热温度达到700℃以后,aln发生脱氮反应,逐渐转变成al2o3,当煅烧温度达到950℃,铝灰中的aln基本都转变成氧化铝,同时铝灰中含有氯化钠、氯化钾等盐类也都气化,最终废气中是含有氮气、氯化钠气体、氯化钾气体、部分工业固废的分解气体而组成的混合气体。2.通过脱氮、脱盐后的铝灰经下料口送入回转干燥筒内,与由称量好的其他原料赤泥、脱硫石膏、电石渣经混合换热后,水分控制在5%以下,经回转干燥筒出口排出,在与校正料混合后送入粉磨机,粉磨粒度小于8μm的原料进入原料仓。表1为铝灰在预处理前后的化学成分变化表,经950℃高温煅烧处理后的铝灰,氯、钠、钾元素降低非常明显。表1铝灰处理前后成分变化表成分al2o3mgosio2caoso3na2ofe2o3tio2k2ocl煅烧后71.2413.287.412.091.831.210.780.730.530.42原铝灰64.8310.835.321.652.873.910.670.692.386.62图2~3为铝灰经热处理前后的矿物相变化xrd图,表明经950℃煅烧后的铝灰,aln、al、nacl基本无峰值,可认为铝灰脱氮、脱盐、氧化过程较为彻底。3.通过铝灰间接加热器处理产生的含有氮气、氯化钠气体、氯化钾气体经抽气器送入旋转冷凝器内,使含盐气体冷凝相变,生成氯化钠、氯化钾盐类晶体,经旋转冷凝器下料口落入储盐池,将压滤生料通过干燥器干燥至自然水分消失为止,送入储料室。4.匹配好的原料成分及控制参数为sio28wt%,cao42wt%,al2o329wt%,fe2o35wt%,so316wt%。碱度系数cm为1.03。式中cao、sio2、al2o3、fe2o3、tio2、so3分别为相应化学成分所占的重量百分比。5.将储量仓的原料经传输设备送入煅烧回转窑内,进行原料的煅烧工艺,送入回转窑内,窑内最高温度控制在1250℃下,且进行高温煅烧40min左右。6.将天然气经燃烧器在回转窑内进行燃烧,过量空气系数控制在1.1~1.15之间。7.利用回转窑炉内产生的高温烟气对回转烘干筒内的原料进行烘干至达到含水率在4%以下,达到可进入磨机的最低要求。8.经过回转烘干筒产生的废气经除尘器、脱硫脱硝装置后,达到环保标准,排入大气。9.在回转窑产生的硫铝酸盐熟料,以硫铝酸钙(3cao·3al2o3·caso4)和硅酸二钙(2cao·sio2)和铁相为主要矿物物相。最后,熟料与脱硫石膏进行混合(熟料与石膏的质量比为100:5),送入水泥磨内粉磨成水泥。表3为全固废制备的硫铝酸盐胶凝材料的强度性能。表3强度性能测试结果以上所述仅为本发明的优选实施例而已,并不用于限制本发明,对于本领域的技术人员来说,本发明可以有各种更改和变化。凡在本发明的精神和原则之内,所作的任何修改、等同替换、改进等,均应包含在本发明的保护范围之内。当前第1页12