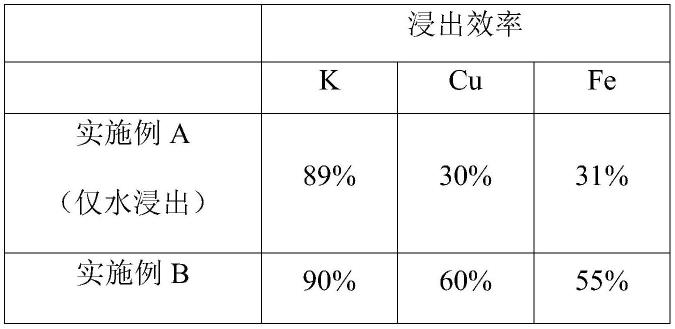
1.本发明涉及一种减少焙烧钼精矿(rmc)及由其获得的组合物中的杂质的方法,以及适用于实施该方法的rmc处理装置。
背景技术:2.在自然界中,钼主要以钼矿石辉钼矿(mos2)的形式存在。在钼的许多应用中,辉钼矿被氧化成氧化钼,然后主要用于生产含钼合金和催化剂。辉钼矿(mos2)氧化成氧化钼的方法有两种。第一种也是最常见的氧化方法是在空气存在下在焙烧炉中焙烧钼矿石。众所周知,矿石或精矿,优选钼(mos2)精矿,可以通过焙烧所述含钼矿石或精矿被加工成焙烧钼精矿。获得更高纯度氧化钼的第二种选择是通过湿化学途径氧化辉钼矿。这涉及在酸性环境中操作,并调整条件以使钼溶解最少,但杂质溶解程度更高。通过湿化学途径,辉钼矿在高压釜中的高浓度氧气(o2)气氛下和/或用硝酸(hno3)作为氧化剂被氧化。在硫酸(h2so4)的存在下这些反应也可以发生,硫酸是选择性添加的,但也在辉钼矿的氧化过程中形成。湿化学途径作为钼矿石氧化方法的缺点是其高能耗和高成本,因为浓氧比空气昂贵得多。此外,使用高压釜的操作非常精细,因为必须对所使用的辉钼矿进行脱油以防止在高压釜中爆炸,并且必须限制磨料脉石以防止损坏高压釜。
3.辉钼矿仍含有多种杂质,例如但不限于砷、磷、铁、铜和钾。根据所使用的氧化方法,这些杂质也可以或多或少地存在于所生产的氧化钼中。
4.特定的应用要求氧化钼的纯度高于仅通过焙烧或湿化学氧化所获得的纯度。更高纯度的氧化钼可以通过升华或通过湿化学途径获得,其中首先将氧化钼溶解在氨中以产生钼铵盐,例如但不限于二钼酸铵、四钼酸铵或其组合物。通过加热钼铵盐使其分解,可以得到高纯度的氧化钼。
5.在rmc向钼铵盐的转化过程中,由于钾浓度对最终产品的性能有显着影响,因此钾的存在是一个关键因素。钾不能从钼铵盐溶液中选择性去除,且通过钼铵盐分解获得的更高纯度氧化钼中的钾浓度只能通过用已经具有低钾含量的rmc操作来保持较低。因此,从rmc中除去那些可以溶解在氨中的杂质是很重要的,例如但不限于钾,因为它们不能从钼铵盐溶液中选择性地除去。
6.us3848049描述了用温水浸出rmc,温水的温度在10至100℃之间。或者,浸出步骤不使用温水,而是使用无机酸在热水中的溶液,优选硝酸,该无机酸的浓度可以为1%至10%,优选1%至5%。硝酸的使用导致硝酸盐最终与其他杂质一起进入浸出溶液。出于环境原因,应避免使用硝酸,因为硝酸盐是必须从废水中去除的污染物。因此,us3848049的一个缺点是使用硝酸作为无机酸对环境构成威胁,并且此酸比其他无机酸更昂贵。此外,us3848049中描述的浸出方法没有提供一种通过浸出进行纯化的方法,其中通过此方法钾和其他金属阳离子的浓度都大大降低。
7.us5271911描述了一种通过酸浸处理从三氧化钼中去除钾的方法。浸出溶液由无机酸和无机酸的铵盐组成。使用的无机酸优选为硝酸。us5271911中描述的浸出方法的一个
缺点是,它没有提供一种通过浸出进行纯化的方法,其中通过此方法钾和其他金属阳离子的浓度显着降低。此外,us5271911描述了硝酸溶液的使用,这是对环境不友好的,因为硝酸盐可能最终进入废水中,以及硝酸铵的使用,如果硝酸铵作为硝酸盐成为废水的一部分,也会造成环境问题,并且此外,硝酸铵在干燥时具有潜在的爆炸性,因此生产过程需要额外的安全措施。
8.us3932580描述了在进行热处理之前首先将rmc与硫酸混合的步骤(rmc首先从150到250℃烘烤,然后从300到600℃焙烧)。首先需要热处理,这对于提高rmc的处理能力很重要。热处理后,且在后续的研磨步骤之后,将获得的产品用温水浸出。温水浸出需要在50至85℃的温度下进行1至3小时。根据us3932580的浸出方法的一个缺点是该方法是能源和劳动密集型的,因为需要多次步骤热处理和造粒。
9.us4643884描述了一种从相对不纯的三氧化钼中除去钾的方法。三氧化钼在至少50℃的温度下,与主要由硝酸和硝酸铵组成的酸浸出溶液接触两次。在每个浸出步骤之间,将三氧化钼从浸出液中分离出来。根据此发明,大部分钾通过酸浸步骤浸出。任选地,在第一酸浸步骤和第二酸浸步骤之间,用水浸出三氧化钼,以除去任何残留杂质。us4643884中描述的方法的一个缺点是,钾的去除是通过使用含有硝酸和硝酸铵的溶液来实现的,如果它们作为硝酸盐成为废水的一部分,则会产生环境问题,并且此外,硝酸铵在干燥时具有潜在的爆炸性,因此生产过程需要额外的安全措施。us4643884中描述的方法的另一个缺点是,需要几个浸出步骤,因此这在工业规模上总体上是效率不高的,并且还需要几个分离步骤以从浸出物中分离三氧化钼,导致一种能量和劳动更密集型的去除钾的方法。
10.因此,需要一种改进的方法来降低焙烧钼精矿(rmc)中的杂质浓度,该方法劳动强度较低、成本较低以及能够有效去除杂质,且对环境和实施该方法的操作人员更安全。
技术实现要素:11.本发明特别旨在克服现有技术的这些缺点。更具体地,本发明的一目的是提供一种减少焙烧钼精矿(rmc)中杂质的方法。该方法劳动强度较低,成本较低,可有效去除杂质,且对环境和实施该方法的操作人员更安全。根据本发明的方法包括如下步骤:a.在第一处理反应时间内,在第一反应器或第一系列的反应器中,对至少一部分的rmc进行第一处理,以形成第一经处理的悬浮液,第一处理包括如下步骤:a.将至少一部分的rmc加入水溶液或水的溶液中,其中该第一经处理的悬浮液温度为10℃至100℃且第一ph值为至少2.1且优选至多5.0,优选至多4.0,优选至多3.0,优选至多2.8;b.在第二处理反应时间内,在第二反应器或第二系列的反应器中,对至少一部分的第一经处理的悬浮液进行第二处理,优选为其中第一经处理的悬浮液包括来自第一经处理的悬浮液的rmc固体,其中,第二处理包括如下步骤:将至少一部分的第一经处理的悬浮液添加到酸溶液中以形成第二经处理的悬浮液,其中,至少一部分的第一经处理的悬浮液的温度低于70℃,并且其中第二经处理的悬浮液的第二ph值在1.5和第一ph值之间;和c.在第二处理反应时间后,从第二反应器或第二系列的反应器中,分离至少一部分的第二经处理的悬浮液。根据本发明的减少焙烧钼精矿中杂质、特别是降低杂质浓度的方法的一个优点是,能够以更节能和成本效率更高的方式,以劳动强度较低的方式和以更环保的方式去除杂质,因为可以避免使用硝酸。出人意料地发现,如果包括酸性化合物的悬浮液是在温度低于约70℃,和ph值为约1.5至约2.3时添加的,则
钾和铜的去除比在温度高于70℃和ph值在上述范围之外时更有效。根据本发明的方法可以在不需要粉碎rmc的情况下进行。根据本发明的方法可以在不对rmc进行任何纯化的情况下进行。根据本发明的方法可以在rmc中铜含量高的情况下进行,优选重量百分比高达4.0%,优选重量百分比高达3.5%,优选重量百分比高达3.0%,优选重量百分比高达2.0%,优选重量百分比高达1.5%,优选重量百分比高达1.0%,优选重量百分比高达0.5%,重量百分比%表示为rmc的总重量。
12.根据本发明的一实施方案,酸溶液包括盐酸或硫酸,或它们的组合,优选硫酸。该实施方案的一个优点是硫酸和盐酸比其他酸例如硝酸在环境上更安全。在本发明的上下文中可以使用盐酸代替硫酸,但优选使用硫酸和硫酸溶液。使用硫酸而不是盐酸的一个优点是硫酸盐比氯化物更容易从废水中去除,从环保角度来说,这使其成为更好的选择。此外,硫酸对于用于实施该方法的工业设备的腐蚀是最小的。此外,使用硫酸所表现出的浸出效率高于使用盐酸时的浸出效率。
13.根据本发明的一优选实施方案,该方法包括如下步骤:在将至少一部分的第一经处理的悬浮液添加到酸溶液中以形成第二经处理的悬浮液的步骤之前,添加预定量的水至第一反应器、第一系列的反应器、第二反应器或第二系列的反应器,以使得至少一部分的第一经处理的悬浮液的温度低于70℃。除了前述实施方案的优点之外,本实施方案的另一优点是,与通过自然对流冷却相比,至少一部分的第一经处理的悬浮液的温度可以更容易且更快地降低到所需温度。此外,钾的浸出效率可以不受到影响,而其他杂质的浸出效率会有所提高。
14.根据本发明的一优选实施方案,在步骤a.中,第一经处理的悬浮液温度为至少60℃,优选至少75℃。除了前述实施方案的优点之外,本实施方案的另一优点是,钾杂质可以比在低于60℃的温度下更快地溶解。
15.根据本发明的一实施方案,步骤a中的反应器和步骤b中的反应器是相同的。
16.根据本发明的一实施方案,反应器、第一系列的反应器和第二系列的反应器是相同的。本实施方案的一优点是,根据本发明的方法可以以较小的规模进行,并且需要较少的设备,因此允许一种成本效率更高且劳动强度更低的方法。
17.根据本发明的一实施方案,提供了一种方法,该方法包括如下步骤:在进行第二处理之前,从第一经处理的悬浮液中过滤至少一部分第一经处理的悬浮液,其中传递给第二处理的至少一部分的第一经处理的悬浮液是rmc滤饼。除了前述实施方案的优点之外,本实施方案的另一优点是,通过去除含有溶解的k的滤液,消除了在第二处理期间在较低ph下沉淀k的危险。
18.根据本发明的一优选实施方案,提供了一种方法,该方法还包括如下步骤:将至少一部分的第一经处理的悬浮液从第一反应器或第一系列的反应器转移至至少一个后续反应器,其中至少一个后续反应器选自由第一反应器或第一系列的反应器和第二反应器或第二系列的反应器组成的组。该实施方案允许应用连续工艺来处理和浸出(即去除杂质)rmc,与其中第二处理步骤仅在第一处理步骤完成之后再进行的分批工艺相比,导致更高的浸出效率(即可以在更短的时间内处理更多的rmc)。根据本发明的本实施方案,减少rmc中杂质的时间效率更高,因为可以连续处理更大量的rmc。
19.根据本发明的一优选实施方案,提供了一种方法,该方法通过溢流进行转移步骤,
其中第一反应器或第一系列的反应器和后续反应器放置在至少一部分的第一和第二经处理的悬浮液的流动方向上。除了前述实施方案的优点外,本实施方案的另一优点是溢流过程是一种自然过程,不需要复杂的控制设备,是一种降低rmc中杂质(浓度)的具有成本效益的方法。
20.在本发明的一具体实施方案中,提供了一种方法,其中第二经处理的悬浮液的温度低于65℃,优选低于约55℃。发明人惊奇地发现,rmc中的钾杂质可以比在高于65℃的温度下更好地去除,因为钾的去除效率降低的较小。
21.在本发明的一优选实施方案中,第二次经处理的悬浮液的ph值在1.8和2.0之间,优选1.9。除了前述实施方案的优点之外,本实施方案的另一个优点是钾杂质从悬浮液中沉淀最少,当其他杂质从rmc中浸出时钾的浸出效率基本上没有降低。
22.在本发明的一具体实施方案中,第一处理反应时间为总反应时间的约20%至80%,优选约35%至60%,更优选约40%,其中总反应时间为第一处理反应时间和第二处理反应时间的总和。除了前述实施方案的优点之外,本实施方案的另一优点是钾和铜的浸出效率高于反应时间不在大约20%至80%之间时的浸出效率。
23.在本发明的一具体实施方案中,第二经处理的悬浮液的在质量上的液固比(l/s)为约2.0和3.0之间,优选为约2.6。除了前述实施方案的优点外,本实施方案的优点是铁杂质和铜杂质的去除效率更高。l/s比低于2.0会降低铁和铜等的去除效率。将l/s比提高到3.0以上,效率不会进一步显著提高,反而存在需要更大反应器的经济劣势。
24.本发明的另一方面涉及根据前述权利要求中任一项所述的一种降低rmc中的杂质浓度的焙烧钼精矿(rmc)处理装置,该装置包括:第一反应器或第一系列的反应器,其适于在第一处理反应时间内,在反应器或第一系列的反应器中,对至少一部分的rmc进行第一处理,以形成第一经处理的悬浮液,第一处理包括如下步骤:将至少一部分的rmc加入到水溶液或水的溶液中,其中,第一经处理的悬浮液温度为10℃至100℃且第一ph值为至少2.1,并优选至多5.0,优选至多4.0,优选至多3.0,优选至多2.8;第二反应器或第二系列的反应器,其适于在第二处理反应时间内,在第二反应器或第二系列的反应器中,对至少一部分的第一经处理的悬浮液进行第二处理,优选其中,一部分的第一经处理的悬浮液包括来自第一经处理的悬浮液的rmc固体,其中,第二处理包括如下步骤:将至少一部分的第一经处理的悬浮液加入酸溶液中以形成第二经处理的悬浮液,其中,至少一部分的第一经处理的悬浮液的温度低于70℃,并且第二经处理的悬浮液的第二ph值在1.5和第一ph值之间;以及分离装置,该装置适于在第二处理反应时间之后,从第二反应器或第二系列的反应器中,分离至少一部分的第二经处理的悬浮液。根据本发明的减少焙烧钼精矿中杂质的该实施方案的一个优点是可以有效地去除杂质。
25.根据本发明的一优选实施方案,第一和第二系列的一个或多个反应器是相同的。本实施方案的一优点是根据本发明的方法可以在较小的规模下进行。
26.根据本发明的一优选实施方案,提供了一种装置,该装置还包括如下设备,该设备用于将至少一部分的第一经处理的悬浮液从第一反应器或第一系列的反应器转移到后续反应器,其中后续反应器选自由第一反应器或第一系列的反应器和第二反应器或第二系列的反应器组成的组。该实施方案的一优点是本发明可以以连续工艺进行,使得减少焙烧钼精矿中杂质的时间效率更高,因为该方法可以不间断地进行。此外,溢流过程是一种不需要
复杂的控制设备的自然过程,因此具有成本效益。
27.根据本发明的一优选实施方案,提供了一种装置,其中用于转移的设备是溢流。该实施方案的一优点是在该实施方案中不需要用于转移的泵。
28.本发明还涉及通过根据前述权利要求中任一项的方法获得的经处理的rmc产品,其中,基于经处理的rmc产品的总重量,经处理的rmc产品含有浓度为重量百分比小于0.0864%、优选重量百分比小于0.0240%的钾;重量百分比小于0.24%、优选重量百分比小于0.08%的铜;以及重量百分比大于50.00%、优选重量百分比大于56.47%、优选重量百分比大于58.67%的钼。根据本发明描述的方法获得的纯化焙烧钼精矿的一优点是,它适用于其中可溶性钾的浓度必须最低的特定应用,而不需要进一步的纯化步骤。
附图说明
29.为了更好地展示本发明的特征,以下参考附图描述减少rmc中杂质的方法的至少一个优选实施方案,其仅作为一个示例并且不以任何方式限制,其中:
30.简称为图1(fig.1)的图1(figure 1)示出了根据本发明的减少rmc中杂质浓度的方法的浸出效率的柱状图,其中实施例a是不使用酸的情况,实施例b是仅使用盐酸的情况,实施例c为根据本发明的情况,先用水进行第一处理,再用硫酸进行第二处理;
31.简称为图2(fig.2)的图2(figure 2)示出了杂质的浸出效率与将酸添加到至少一部分的第一经处理的悬浮液中的时间的关系,该时间表示为总反应时间的百分比,其中实施例a是根据本发明的方法期间不使用酸的情况;
32.简称为图3(fig.3)的图3(figure 3)示出了在添加酸性化合物之后,杂质的浸出效率随第二经处理的悬浮液的温度的变化;
33.简称为图4(fig.4)的图4(figure 4)示出了根据本发明的减少rmc中杂质浓度的方法的步骤;
34.简称为图5(fig.5)的图5(figure 5)示出了通过连续工艺来实施根据本发明的方法的浸出装置。
35.具体说明
36.下面的详细说明旨在描述本发明的优选实施方案,而不是对本发明可以发生或应用的唯一实施方案的限制性表示。本说明旨在清楚地说明对于构建和实施本发明必要的功能和步骤。应该理解,其他实施方案可以获得相同或同等的功能和组件,并且这些也应落入本发明的保护范围内。所描述的附图仅仅是示意性的,而不是限制性的。
37.此外,说明书和权利要求中的术语第一、第二、第三、第四等用于区分相似的元素,而不一定用于在时间上、空间上、在排序上还是以任何其他方式描述序列。应当理解,如此使用的术语在适当的情况下是可互换的,并且本文描述的本发明的实施方案能够以除本文描述或示出之外的其他顺序操作。
38.申请人的公开在以下参考附图的描述中的优选实施方案中进行了描述,其中相同的数字代表相同或相似的元素。在整个说明书中对“一个实施方案”、“一实施方案”或类似用语的引用意味着结合实施方案描述的特定特征、结构或特性被包括在本发明的至少一个实施方案中。因此,在整个说明书中出现的短语“在一个实施方案中”、“在一实施方案中”和类似的用语可以但不一定都指代相同的实施方案。
39.本发明的所描述的特征、结构或特性可以在一个或多个实施方案中以任何合适的方式组合。在以下描述中,记载了许多具体细节以提供对本发明的实施方案的透彻理解。然而,相关领域的技术人员将认识到,本发明可以在没有一个或多个特定细节的情况下,或者使用其他方法、组件、材料等来实施。在其他情况中,未详细示出或描述众所周知的结构、材料或操作,以避免混淆本发明的各方面。
40.当在根据本发明的至少一个实施方案中提及术语“焙烧钼精矿”或“rmc”时,参考如“reach molybdenum consortium”(rmc sub id&classif.2015)所描述的物质。rmc可包括三氧化钼、二氧化钼或任何其它钼氧化物。平均而言,在根据本发明的实施例和测试中用作原材料的rmc的组合物包括以下浓度的杂质:基于rmc的总重量,重量百分比为0.1292%的钾、重量百分比为0.45%的铜、重量百分比为0.0052%的砷、重量百分比为0.0079%磷。根据本发明,基于rmc的总重量,rmc中也可以包括重量百分比高达4%的铜的浓度,优选重量百分比高达2%。
41.在根据本发明的实施例中,在本发明中形成的悬浮液的ph和温度是根据标准方法和使用标准仪器测量的。
42.当在根据本发明的至少一个实施方案中提及术语“第一ph值”时,是指第一经处理的悬浮液的ph值,其可以被认为是第一经处理的悬浮液的自然ph值,其中其是指仅将待悬浮固体(例如rmc)加入到水溶液或水的溶液中而获得的悬浮液的ph值。参考根据本发明的特定实施方案,该第一或自然ph值为至少2.1,优选在2.1和2.8之间。
43.根据本发明的一实施方案,该第一或自然ph值在2.1和5.0之间,优选在2.1和4.0之间,优选在2.1和3.0之间,优选在2.1和2.8之间。
44.当在根据本发明的一方面的至少一个实施方案中提及“减少rmc中杂质”时,其是指减少rmc中的杂质浓度。
45.当在根据本发明的至少一个实施方案中提及术语“浸出效率”时,其是指根据本发明的从初始rmc中浸出的杂质的最终重量与初始rmc中的杂质的初始重量之间的比,该重量比以百分比表示。
46.当在根据本发明的至少一个实施方案中提及术语“rmc滤饼”时,其是指在通过分离装置从第一经处理的悬浮液中分离之后获得的呈固体形式的纯化的rmc。
47.当在根据本发明的至少一个实施方案中提及术语“浆液”或“悬浮液”时,其是指至少部分悬浮在液体中的固体混合物。在本发明的上下文中,由于作为rmc的主要成分的氧化钼不溶于水,第一经处理的悬浮液和第二经处理的悬浮液是基于水的悬浮液,其中杂质和氧化钼悬浮以形成浆液。因此,对于本领域的技术人员来说清楚的是,使用术语“浆液”或“悬浮液”,是指第一或第二经处理的悬浮液。
48.当在根据本发明的至少一个实施方案中提及术语“浸出”时,其是指通过将杂质溶解在液体中而提取焙烧钼精矿中杂质的过程。
49.当在根据本发明的至少一个实施方案中提及术语“杂质”时,其是指溶解在水和/或氨中的不需要的化合物,例如但不限于钾、铁、磷、砷和铜的化合物。
50.在根据本发明的实施方案中提及“液固比(l/s)”时,其是指液体与添加到液体中的固体材料之间的质量比。
51.本发明提供了降低焙烧钼精矿(rmc)中杂质浓度的方法,以生产由大部分氧化钼
组成的rmc,其中该方法包括以下步骤:第一处理步骤、第二处理步骤和分离步骤。具体地,第一处理步骤包括在第一处理反应时间内,在第一反应器或第一系列的反应器中,对至少一部分的rmc进行处理,以形成第一经处理的悬浮液,第一处理包括将至少一部分的rmc添加到水溶液或水的溶液中的步骤,其中,第一经处理的悬浮液的温度为10℃至100℃。在第一经处理的悬浮液中,氧化钼颗粒和其他组分悬浮,因为它们基本上是不溶性于水。由于大部分氧化钼的存在,在将水或水溶液加入到rmc中后得到浆液,其中不溶性氧化钼颗粒和其它悬浮在第一经处理的悬浮液中。通常,与rmc的总重量相比,在第一处理步骤之前,焙烧钼精矿中的钾含量平均重量约为1600ppm,铜含量平均重量约为0.45%,然而,本发明的方法降低了rmc中的杂质浓度,甚至是更高浓度的这些杂质。第一处理步骤优选在剧烈搅拌下进行,目的是浸出大部分钾。在第一处理之后,与水接触的焙烧钼精矿将可能产生第一ph值为至少2.1且优选为至多5.0,优选为至多4.0,优选为至多3.0的,优选ph值在2.1和2.8之间的浆液。在杂质的存在使浆液的第一ph值低至2.1以下的情况下,优选将浆液的第一ph值提高到至少2.1。用水浸出还可以浸出部分铜、铁、砷和磷杂质。将包括rmc和水的悬浮液保持在至少60℃的温度下,优选至少75℃的温度下搅拌。然而,第一经处理的悬浮液可以具有10℃至100℃的温度,较高或较低的温度会影响浸出钾所需的总反应时间。在进一步加工过程中,例如在转化为钼铵盐之后,可能难以实现钾杂质的去除,因此,在这种处理之前去除大部分钾是很重要的。在第一处理步骤之后,进行第二处理步骤。如果存在多个反应器,则可将第一经处理的悬浮液转移到后续反应器中。第二处理步骤包括在第二处理反应时间内,在第二反应器或第二系列的反应器中,对至少一部分的第一经处理的悬浮液进行第二处理,其中第二处理包括将至少一部分的第一经处理的悬浮液加入到酸溶液中以形成第二经处理的悬浮液的步骤,其中至少一部分的第一经处理的悬浮液的温度低于70℃,并且其中第二经处理的悬浮液的第二ph值在1.5至2.3之间。在本发明的一具体实施方案中,第二经处理的悬浮液的第二ph值在1.8和2.0之间,并且温度优选低于55℃。令人惊奇地,如果将酸溶液加入到浆液中以形成第二经处理的悬浮液,其中第二经处理的悬浮液的温度低于70℃且第二ph值大约在1.5和2.3之间,则从溶液中沉淀出的钾更少,因此可以从rmc中浸出更高浓度的钾。发明人认为,大概在温度高于70℃且第二ph值低于1.5时,黄钾铁矾kfe3(oh)
6(
so4)2会沉淀。此外,当第二ph值高于2.3时,其他杂质(尤其是铜)的浸出效率降低。将包括rmc、水和酸的浆液保持在搅拌状态,并监测其ph值和温度,直到达到所需的浸出效率。然后,根据本发明的方法包括在第二处理反应时间之后,随后分离至少一部分的第二经处理的悬浮液。合适的分离方式可以是但不限于过滤和倾析。分离后,回收与杂质分离的rmc。
52.根据本发明的一实施方案,在将至少一部分的第一经处理的悬浮液添加到酸溶液以形成第二经处理的悬浮液的步骤之前,添加预定量的水的至第一反应器、第一系列的反应器、第二反应器或第二系列的反应器,使得至少一部分的第一经处理的悬浮液的温度低于70℃。添加预定量的水可以降低温度,而无需使用能耗更高的冷却方法或无需等待第一经处理的悬浮液的温度通过自然对流降低。水量可以通过现有技术中的公式来计算。
53.根据本发明的一实施方案,至少一部分的第一经处理的悬浮液的组成与第一经处理的悬浮液的组成相同。因此,在该实施方案中,取“至少一部分的第一经处理的悬浮液”意味着取一定重量或体积部分的悬浮液而不改变其组成。
54.根据本发明的一实施方案,至少一部分的第一经处理的悬浮液的是优选具有与第
一经处理的悬浮液相同的组成的悬浮液。
55.根据本发明的一实施方案,至少一部分的第一经处理的悬浮液的组成与第一经处理的悬浮液相比具有相同或增加的固体含量。
56.根据本发明的一实施方案,为了降低rmc的水溶液或水溶性的杂质的浓度,最好在总反应时间大于2小时,优选大于2.5小时的情况下进行。总反应时间是第一处理反应时间和第二处理反应时间的总和,因此不包括过滤时间。总反应时间超过2小时的一优点是可以更好地去除铜和铁。在本发明的上下文中,可以使用盐酸代替硫酸或硫酸的水溶液或它们的组合,但优选使用硫酸和硫酸溶液。当使用盐酸时,必须选择更高等级的材料来建造反应器。此外,使用盐酸的特点在于提供较低的浸出效率。
57.图1示出了根据本发明的钾、铁和铜杂质的浸出效率的柱状图。在图1中,浸出效率表示为沿y轴的百分比。所分析的每种杂质的矩形沿x轴分布,其高度与该特定杂质的浸出效率成比例。以三个不同的实施例a、b和c说明了钾、铁和铜杂质的浸出效率。实施例a、b和c已根据分批工艺进行。
58.批量实验
59.实施例a
60.将400g rmc放入1050ml水中以形成浆液。最初,将浆液的温度设置为约75℃,并在整个反应时间(即2.5小时)内保持该温度。2.5小时后,过滤滤饼,并用1050ml水在过滤器上洗涤。从图1中可以看出,钾的杂质大部分被浸出,而铁和铜的杂质则浸出很差。
61.实施例b
62.将400g rmc放入1050ml水中以形成浆液。在开始时,温度设置为75℃,且在整个反应时间都不改变,并且也从开始时,向浆液中加入盐酸溶液,使浆液的ph约为1.9。可以使用不同浓度的盐酸。反应时间为2.5小时。2.5小时后,过滤滤饼,并用1050ml水在过滤器上洗涤。从图1中可以看出,钾的杂质大部分被浸出,与实施例a相比,实施例b中的铁和铜的杂质浸出得更好。
63.实施例c
64.将400g rmc放入1050ml水中形成浆液,且因此液固质量比(l/s)为2.6:1。将rmc添加到水中会自然导致形成的浆液的第一ph值设置在大约2.3。总反应时间为2.5小时。开始时,温度设置为大约75℃。在总反应时间的40%后,即1小时后,温度降至约55℃。一旦达到较低温度,加入硫酸溶液并将第一ph值降低至大约1.9的第二ph值,并在搅拌下反应1个半小时(1.5小时)。可以使用不同浓度的硫酸。在用水浸出和加入硫酸之后没有过滤。因此,根据本发明,第一处理反应时间等于1小时,而第二处理反应时间为1个半小时(1.5小时)。在总反应时间结束时,过滤rmc滤饼,并用1050ml水在过滤器上洗涤。如图1所示,钾、铁和铜的浸出效率更高。相对于实施例b,在实施例c中,铜更好地被硫酸溶解。
65.实施例a、b和c的浸出效率结果如下表所示:
[0066][0067][0068]
从上表明显看出,根据本发明的方法对于钾的杂质(浸出效率90%)和铜的杂质(浸出效率97%)都可以获得高浸出效率。连续流动实验
[0069]
下表显示了关于实施例d1、d2和d3的杂质浸出效率。对于实施例d1、d2和d3,使用相同的rmc原料,该原料rmc具有以下杂质浓度:
[0070][0071]
*重量百分比[wt%]基于rmc的总重量。
[0072]
根据本发明,可通过连续流动降低rmc中杂质的浓度,其中多个反应器依次放置,并将rmc污泥连续添加到第一反应器中,混合物通过溢流从一个反应器移动到下一个反应器,且其中可能连续输出至少一部分的经处理的悬浮液。
[0073]
实施例d、d2、d3涉及连续流动过程。实施例d1、d2和d3的平均反应时间为2.5小时。浆液温度设置为约75℃,并在整个反应时间内保持该温度。
[0074]
实施例d1
[0075]
浸出是通过连续过程进行的,在此过程中每1050ml水添加400g rmc。浸出仅使用水、水溶液或水的溶液进行。
[0076]
实施例d2
[0077]
浸出采用与实施例d1相同的参数进行,但使用硫酸代替水。ph值设置为1.9。
[0078]
实施例d3
[0079]
在一系列反应器的第一反应器中,每400ml水添加400g rmc,水的温度为75℃。通过溢流,将至少一部分的第一经处理的悬浮液转移到一系列的反应器的第二反应器中,该反应器包括具有与第一反应器中的水相同温度的水溶液或水的溶液。此后,通过溢流将材料转移到一系列的三个反应器中,这些反应器包括ph值为1.9、温度为55℃的酸溶液(h2so4)。
[0080]
实施例d1、d2和d3的浸出效率结果如下表所示:
[0081][0082]
实施例d1、d2和d3的纯化后rmc中的杂质浓度如下表所示:
[0083][0084][0085]
*重量百分比[wt%]基于rmc的总重量。
[0086]
图2示出了杂质的浸出效率,如y轴所示,与向浆液中添加硫酸的时间有关,该时间表示为总反应时间的百分比,如x轴所示。总反应时间为2.5小时。“0%”测试意味着从反应开始仅进行酸浸出(参见实施例e)。在图2中,也显示了未添加酸的实施例a的结果。
[0087]
实施例e
[0088]
将400g rmc放入1050ml水中,并将温度设置为75℃且不改变。从一开始,用硫酸将悬浮液的ph值调节到1.9。反应时间为2.5小时。2.5小时后,过滤滤饼,并用1050ml水在过滤器上洗涤。
[0089]
如果在加入包括硫酸的溶液之前,根据本发明的纯化方法,先将rmc与水接触,然后与硫酸溶液接触,则钾的浸出效率提高,而铜和铁的浸出效率略微降低。已经发现,如果第一处理反应时间在总反应时间的大约35%至60%之间,优选大约40%,则可以改善钾的浸出而不显着降低铜和铁的浸出效率。
[0090]
图3示出了杂质的浸出效率相对于在添加包括硫酸的溶液之后的浆液温度的变化。图3示出了根据实施例f1、f2、f3获得的浸出效率结果。实施例f1、f2和f3的浸出效率如下表所示:
[0091][0092][0093]
实施例f1
[0094]
将400g rmc放入1050ml水中以形成浆液。在反应开始时,温度设置为75℃。在总反应时间(2.5小时)的40%(1小时)后,将温度降至55℃,且一旦达到较低温度,将ph降至1.9(使用硫酸)。在反应时间结束时,过滤滤饼,并用1050ml水在过滤器上洗涤。
[0095]
实施例f2
[0096]
实施例f2与实施例f1的不同之处在于,在总反应时间的40%后,在通过加入硫酸将ph调节至1.9之前,将温度降低至65℃。
[0097]
实施例f3
[0098]
实施例f3与f1和f2的不同之处在于,在总反应时间的40%之后,温度没有降低,而是保持恒定在75℃。
[0099]
从图3可以看出,加入硫酸后,随着浆液温度升高,钾的浸出效率降低。令人惊奇地,发现如果在低于70℃、优选低于55℃的温度下添加包括硫酸的溶液,则通过浸出去除k的效率更高。据信,在温度高于70℃且ph小于等于1.5时,黄钾铁矾kfe3(oh)6(so4)2会大量沉淀。在温度等于或高于55℃且ph小于或等于约1.8时,钾的沉淀和浸出效率的损失已经开始。
[0100]
根据本发明的纯化方法可以有利地以连续工艺进行。本发明还涉及一种浸出装置,用于实施根据本发明的其它实施方案的提纯焙烧钼精矿的方法,该装置包括第一和第二系列的反应器。将浆液连续添加到第一浸出容器中,并通过溢流将浆液从一个反应器转移到下一个反应器。一部分的第一经处理的悬浮液可优选通过溢流从第一系列的反应器中移除,并由后续反应器接收,其中后续反应器可以是来自第一系列的反应器或第二系列的反应器的反应器。
[0101]
图4示出了根据本发明的rmc纯化方法的步骤。根据本发明的获得纯化rmc的方法包括以下步骤:加工钼矿石以生产rmc 401,将rmc与更高温度的水接触形成浆液402,并首先去除杂质,主要但不限于k,在低温下将酸溶液加入rmc的浆液中403,并分离纯化的rmc404。
[0102]
图5示出了适于实施根据本发明的方法的rmc处理装置500的示例。可以设计不同的rmc处理装置500,并且它们适合于实施根据本发明的方法,例如通过改变反应器的数量,该数量可以从一个变化到获得所需的浸出效率所需的数量。根据本发明,rmc中的杂质浓度可以通过如图5所示的连续流动工艺或分批工艺来降低。
[0103]
当提及其中第一系列的反应器和第二系列的反应器相同的实施方案时,指的是分批工艺。
[0104]
当提及其中步骤a)中的反应器和步骤b中的反应器相同的实施方案时,指的是分批工艺。
[0105]
图5示出了rmc处理装置500,其包括第一系列511的一个或多个反应器505,适于在第一处理反应时间内对至少一部分的rmc进行第一处理,以形成第一经处理的悬浮液510;以及第二系列512的一个或多个反应器506,其适于在第二处理反应时间内,在第二系列的一个或多个反应器中对至少一部分的第一经处理的悬浮液进行第二处理。
[0106]
根据图5所示的实施方案,第一系列511和第二系列512各包括两个反应器,即第一系列511包括第一反应器505和第二反应器506,第二系列512包括第三反应器513和第四反应器514。在根据本发明的连续工艺中,反应器505、506、513、514依次放置,以允许进一步的第一处理,例如将材料从第一反应器505转移到第二反应器506;或进行第二处理,例如将材料从第二反应器转移到第三反应器513;或进行进一步的第二处理,例如,将材料从第三反应器513转移到第四反应器514。反应器的数量不限于图5所示的数量。
[0107]
根据本发明的一优选实施方案,第一系列511的一个或多个反应器可以由两个反应器组成,第二系列512的一个或多个反应器可以由三个反应器组成。该实施方案提供了一种降低rmc中杂质(浓度)的方法,其中第一处理反应时间为总反应时间的40%,第二处理反应时间为总反应时间的60%。
[0108]
其中第一系列511和第二系列512的一个或多个反应器是不相同或不同,即连续工艺,的优选实施方案的一个优点是,与分批工艺配置相比,可以在更短的时间范围内处理更
多的rmc材料,因为起始rmc材料502可以以连续方式或以比第一处理反应时间更短的特定时间间隔加入到第一反应器505中。
[0109]
将至少一部分的第一经处理的悬浮液510从反应器(例如第一反应器505)转移到后续反应器(例如第二反应器506),或来自至少一部分的第二经处理过的悬浮液通过溢流进行,而不限于此设备。通过溢流转移材料的优点在于,与使用转移装置(例如可以由计算机控制的泵)将材料从一个反应器转移到后续的反应器的装置相比,该方法被认为消耗更少的能量。根据本发明的一具体实施方案,将至少一部分的第一经处理的悬浮液510或第二经处理的悬浮液507从一个反应器转移到后续的反应器可以进行,但不限于溢流方法和其他转移方法的组合。
[0110]
在根据本发明的的一优选实施方案的装置500中,搅拌器509可以放置在反应器505、506、513、514中,以保持rmc颗粒的第一经处理的悬浮液510或第二经处理的悬浮液507存在。
[0111]
在图5所示的具体装置500中,可以将预定量的水501和rmc502添加到第一系列511的一个或多个反应器的第一反应器505中,以进行第一处理并形成第一经处理的悬浮液510。然后,通过例如溢流503将至少一部分的第一经处理的悬浮液510转移到后续的反应器506中,但不限于这种类型的转移。从后续的反应器506,可将至少一部分的第一经处理的溶液510转移到后续反应器,例如,用于第二处理的第二系列512的至少一个或多个反应器的第一反应器。因此,本领域技术人员可以理解,反应器沿悬浮液的流动方向放置,以便首先进行第一处理,其次进行第二处理,而不限于在转移503到第二系列512的反应器的一个或多个反应器之前,在第一系列511的反应器的一个或多个反应器中进行第一处理的实施方案。第二处理也可以在第二系列512的反应器的一个或多个反应器中进行。
[0112]
在第二处理反应时间之后,至少一部分的第二经处理的溶液507可以从第二系列的一个或多个反应器的反应器513、514中去除或分离504,优选最后的反应器514。
[0113]
根据本发明的一优选实施方案,第二系列512的一个或多个反应器的反应器513、514可以包括酸溶液。为了获得1.5至2.3,优选1.8至2.0,更优选1.9的所需ph值,第二系列512的一个或多个反应器适于接收酸溶液508。
[0114]
向该装置中的一个或多个反应器添加酸溶液508。在本发明的上下文中,且如图5所示,必须预期前两个反应器505、506属于第一系列511的反应器,其中可能发生基于水的浸出,而最后两个反应器513、514属于第二系列512的一个或多个反应器,其中可能发生基于酸的浸出。
[0115]
溢流503的过程是一个自然过程,不需要复杂的控制设备,因此是具有成本效益的过程。至少一部分的第一经处理的溶液或至少一部分的第二经处理的溶液的分离可通过过滤或倾析或任何其他适合于从悬浮液510、507中分离纯化rmc的悬浮颗粒的技术来进行,以便例如从装置500的第二系列512的一个或多个反应器中分离504至少一部分的第二经处理的悬浮液。该分离的504至少一部分的第二经处理的悬浮液包括纯化的rmc,且基于经处理的rmc产品的总重量,该纯化的rmc可以指含有浓度为重量百分比小于0.0864%、优选重量百分比小于0.0240%的钾;重量百分比小于0.24%、优选重量百分比小于0.08%的铜;以及重量百分比大于50.00%、优选重量百分比大于56.47%、优选重量百分比大于58.67%的钼的经处理的rmc产品。
[0116]
在rmc处理装置500需要更小的情况下,在rmc处理装置500中,第一系列511和第二系列512的一个或多个反应器是相同的,因此存在单个反应器。在这种情况下,rmc、水和酸溶液可以添加到同一反应器中,并且不存在后续反应器。该具体实施方案的一优点在于,根据本发明的方法可以在减少的空间内实施。此外,本实施方案的一优点在于根据本发明的方法可以在较小的规模下实施。
[0117]
本发明还涉及用于生产纯钼铵(adm)盐和moo3的纯化的焙烧钼精矿(rmc)的用途,其中纯化的rmc通过根据本发明的至少一个优选实施方案的方法获得。