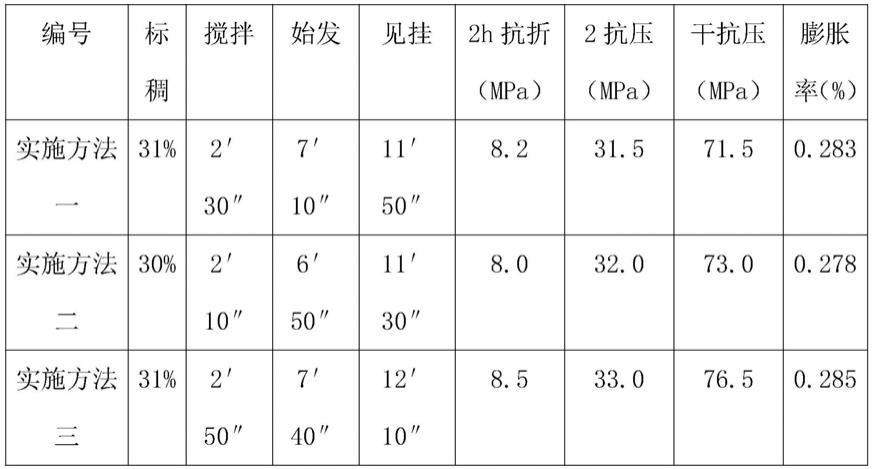
1.本发明涉及一种用天然石膏恒定加压制备超高强石膏粉的方法。
背景技术:2.目前生产高强石膏粉的方法,主要是干蒸压法,液相法和半干法,所有的这些工艺方法都是在加压的环境中完成的。干蒸压法和半干法生产出的高强粉的干抗压强度一般小于40mpa,对于干抗压强度大于50mpa的只有用液相法生产制备。高强石膏粉的生产产生的蒸汽必须用到蒸汽锅炉,而根据环保要求,供热蒸汽的锅炉不得小于10t。这在一定程度上阻碍了高强石膏粉的市场应用。
3.cn102992375 a公开了一种α型超高强石膏的制备方法,该发明是将脱硫石膏、天然石膏或其混合物加入到可溶盐的盐水溶液中,得到预混液;再将转晶剂加入上述的盐水溶液中,得到反应液;最后将反应液加热到60~100℃,在恒温、常压下进行转晶,并对转晶后的额反应液进行过滤得到α型超高强石膏。该发明专利存是在高浓度的盐溶液中进行的,水洗过程麻烦,很难完全去除掉高强石膏里面的可溶性盐,环保上也不允许。从目前的报道和专利来看该方法还停留在实验阶段,不具备工业化条件,该专利对原料的细度没有限制和涉及。
4.cn103951297 a公开了一种α型超高强石膏的制备方法,该方法是先用筛子筛掉石膏原料中的砂子、石子等杂质,将石膏原料加入水中,得到石膏的悬浮液,在上述悬浮液中加入转晶剂,经过搅拌,制成浆料,将配置好的浆料置于高压反应釜中进行水热反应,生成短柱状α石膏晶体,然后进行固液分离,将短柱状α石膏晶体在高温环境下干燥得到α石膏粉体,经过粉磨后得到α超强石膏粉。该专利存在生产过程中固液比含量低,生产效率低,导致生产能耗高,转晶得到的石膏晶体为短柱状,导致最后研磨出来的石膏粉强度2小时抗折在7mpa,绝干抗压在50~70mpa左右,远远满足不了高端市场的需求。该专利对细度要求为0.08~3mm。
5.cn 109761521 a公开了一种α
‑
超硬超高强石膏及其制备方法,该方法采用密闭不锈钢反应釜,通过加入晶型分散剂、转晶剂、晶体改性剂、水进行混合,于120~140℃的反应温度下,保持2~5小时,制备长柱状α
‑
石膏晶体,后采用旋风磨机进行研磨改性,得到2小时抗折强度可达到12mpa以上,绝干抗压强度可达到100mpa以上的超高强粉体。专利里提到的晶型分散剂按如下原料的摩尔数配比:甲基丙烯酸1~20摩尔、甲基丙烯酸甲酯1~10摩尔、甲基烯丙基磺酸钠0.5~5摩尔、h 2 o 2或过氧化苯甲酰0.1~3摩尔、甲基烯丙基醇0.5~5摩尔、聚乙二醇1~25摩尔、还原剂0.1~1.0摩尔、水5~25摩尔;按照上述配比,通入氮气,于60~65℃下回流,保持1~5小时。该专利制备得到的高强石膏2小时抗折强度可达到12mpa以上,绝干抗压强度可达到100mpa以上。但是制取的晶型分散剂工艺比较复杂繁琐,同时在如何保持恒压的工艺方法上没并没有涉及到,对于细度要求在1~10μm的细粉。
6.以上专利对石膏原材料的细度做了严格的限制或是未做任何规定,这对天然石膏来说达到这些专利所要求的细度除了环保问题,还有破碎设备的投入,能耗和成本都会提
高,而对细度不进行限制又不可能做出超高强石膏的。
7.因此,针对以上现状,迫切需要开发一种α
‑
超高强石膏,以克服当前实际应用中的不足。
8.干蒸压法:将石膏矿破碎成5
‑
13cm的块状,放入蒸压小车内,推入蒸压釜内,在0.13
‑
0.16mpa下,蒸压15h以上。由于此法加入的是块状石膏,受热不均匀,能耗高,转晶不完全,所以强度不高。
9.半干法:将石膏破碎锤成粉状,然后加入一定比例的转晶剂水溶液,进行充分混合,再分层装入蒸压釜内,在0.3
‑
0.5mpa压力下蒸压4
‑
8h。此法由于原料是粉状,而且加入了转晶剂,所以强度和转晶程度都比干法蒸压出来的强度要高,热效能也提高了不少。
10.液相法:将石膏破碎锤成粉状,然后在预混罐内加入一定比例的水和转晶剂与石膏粉混合,然后在密闭压力罐内,充分搅拌石膏浆液使其悬浮,同时充入0.25
‑
0.5mpa的蒸汽,蒸煮3
‑
5h,然后进行离心脱水,再在炒锅内进行干燥。此方法生产出来的高强粉无论是强度还是热效能都大大提高。
11.以上不论哪种生产方法都需要蒸汽锅炉产生热源,蒸汽锅炉是一种特种设备,蒸汽压力达到设定的压力是需要一定的时间的,而且规定小于10吨的锅炉一律不允许上该设备。本专利用细度在5mm以下的天然石膏作为原材料,用导热油作为热源,向压力罐内通入导热油加热压力反应罐内的水来产生蒸汽,不需要蒸汽锅炉,并在液相法基础上进行工艺技术改进,先加入超细晶型诱导剂,然后再加入转晶剂,恒定温度135℃,通过外加螺杆压缩机向压力罐内加入空气压力作为辅助,恒定压力0.35mpa,不仅反应压力稳定,而且反应的时间也稳定,通过本方法生产出的超高强石膏粉不仅强度高,膨胀小,而且能耗比普通的液相法低。
技术实现要素:12.本发明所要解决的技术问题是一种用天然石膏恒定加压制备超高强石膏粉的方法,对天然石膏原料进行了拣选冲洗,保证了石膏的品味,是生产出超高强石膏提供了前提,有效解决现有技术中存在的问题。
13.本发明是通过以下技术方案来实现的:一种用天然石膏恒定加压制备超高强石膏粉的方法,包括以下几个步骤:
14.s1、拣选水洗步骤:将纯度高的天然石膏矿选出,敲去石膏中的夹块,用水冲去泥沙;
15.s2、破碎步骤:选出的石膏块先用颚式破碎机破碎至12mm以下,然后再用锤式破碎机粉磨至5mm以下,装入吨袋备用;
16.s3、制浆诱导步骤:在压力反应罐中按石膏重量加入水,浓度为50%
‑
150%,并在压力反应罐的盘管中通入加热的导热油,当水温达到70℃时,加入超细的晶型诱导剂0.15
‑
0.4%,晶型诱导剂一般为普通β
‑
半水石膏或α
‑
高强熟石膏中的一种或是两种,然后加入已经破碎称重好的石膏粉原料,转速调到60
‑
120rad/min;
17.s4、恒压转晶步骤:加入0.2
‑
0.5%的转晶剂,转晶剂由多元羧酸或是多元羧酸盐的一种或是多种组成。密闭压力反应罐,恒温135℃,恒压0.35mpa的压力2
‑
5h;
18.当压力低于0.35mpa时,用螺杆压缩机产生的压力充入压力反应罐内,当压力高于
0.35mpa时,通过泄压阀泄压,使压力一直维持在0.35mpa下转晶;
19.s5、离心脱水步骤:转晶完成后,通过泄压,泵送至盘式离心机内甩干,整个离心甩干过程中浆料温度不得低于70℃;
20.s6、炒锅干燥步骤:当离心脱水的浆料含水率降到15%以下,通过板链输送机输送到预热的炒锅中,进行干燥脱水,当炒锅的温度达到130
‑
150℃,干燥完成并卸料;
21.s7、级配改性步骤:干燥后的石膏粉通过改性磨,进行级配。
22.本发明中,对天然石膏原料进行了拣选冲洗,保证了石膏的品味,是生产出超高强石膏提供了前提。在生产过程中,先加入了晶型诱导剂,石膏的晶体比较细小,晶体缺陷减小;转晶剂的加入阻碍了石膏c轴上的成长速度,使石膏晶体变成了短柱状;加热温度通过导热油精准控制(135
±
1)℃,在密闭的压力反应罐中压力通过螺杆压缩机加压或是泄压控制压力在(0.35
±
0.01)mpa,生产出来的超高强石膏粉标稠稳定,初凝时间波动很小;干燥后用改性磨进行级配后干燥强度大于70mpa。本发明按上述实施后对应的结果如表1所示:
[0023][0024]
表1。
[0025]
本发明的有益效果是:1、选择纯度高的石膏作为原料,并进行拣选和冲洗,更大限度的去污除杂。对于石膏原料的细度做了详细的要求;
[0026]
2、在蒸煮转晶前加入超细的晶型诱导剂,便于分散石膏晶体的成核,防止晶体成长过大,避免造成晶格缺陷,因此强度损失小;
[0027]
3、生产制备时,用导热油对压力反应罐中的水加热,通过导热油的温度控制水温始终在135℃上下。一般情况下,当水温在135℃时,压力反应罐中的水蒸气压是不饱和蒸气压,压力都是低于0.35mpa的,本发明技术用螺杆压缩机对压力进行补偿,防止压力过小或过大,使压力反应罐中压力始终维持在0.35mpa。
具体实施方式
[0028]
本说明书中公开的所有特征,或公开的所有方法或过程中的步骤,除了互相排斥的特征和/或步骤以外,均可以以任何方式组合。
[0029]
实施方法一:
[0030]
s1、拣选水洗:将纯度98%的纤维石膏矿选出,敲去石膏中的夹块,用水冲去泥沙;
[0031]
s2、破碎:选出的石膏块先用颚式破碎机破碎至12mm,然后再用锤式破碎机粉磨至4mm以下,装入吨袋备用;
[0032]
s3、制浆诱导:在压力反应罐中按石膏重量加入水,浓度为50%,并在压力反应罐的盘管中通入加热的导热油,当水温达到70℃时,加入晶型诱导剂400
‑
800目的高强熟石膏0.1%,然后加入已经破碎称重好的石膏粉原料,转速调到60rad/min;
[0033]
s4、恒压转晶:加入0.4%的转晶剂戊二酸及其盐,密闭压力反应罐,恒温135℃,恒压0.35mpa的压力2h,当压力低于0.35mpa时,用螺杆压缩机产生的压力充入压力反应罐内,当压力高于0.35mpa时,通过泄压阀泄压,使压力一直维持在0.35mpa下转晶;
[0034]
s5、离心脱水:转晶完成后,通过泄压,泵送至盘式离心机内甩干,整个离心甩干过程中浆料温度不得低于70℃;
[0035]
s6、炒锅干燥:当离心脱水的浆料含水率降到15%以下,通过板链输送机输送到预热的炒锅中,进行干燥脱水,当炒锅的温度达到130℃,完成干燥过程;
[0036]
s7、级配改性:干燥后的石膏粉通过球磨机改性,进行级配。
[0037]
实施方法二:
[0038]
s1、拣选水洗;将纯度98%的雪花石膏矿选出,敲去石膏中的夹块,用水冲去泥沙
[0039]
s2、破碎:选出的石膏块先用颚式破碎机破碎至10mm,然后再用锤式破碎机粉磨至3mm以下,装入吨袋备用。
[0040]
s3、制浆诱导:在压力反应罐中按石膏重量加入水,浓度为100%,并在压力反应罐的盘管中通入加热的导热油,当水温达到70℃时,加入晶型诱导剂400
‑
800目的普通β
‑
熟石膏0.2%,然后加入已经破碎称重好的石膏粉原料,转速调到90rad/min
[0041]
s4、恒压转晶:加入0.3%的转晶剂富马酸及其盐,密闭压力反应罐,恒温135℃,恒压0.35mpa的压力3h,当压力低于0.35mpa时,用螺杆压缩机产生的压力充入压力反应罐内,当压力高于0.35mpa时,通过泄压阀泄压,使压力一直维持在0.35mpa下转晶
[0042]
s5、离心脱水转晶完成后,通过泄压,泵送至盘式离心机内甩干,整个离心甩干过程中浆料温度不得低于70℃
[0043]
s6、炒锅干燥:当离心脱水的浆料含水率降到15%以下,通过板链输送机输送到预热的炒锅中,进行干燥脱水,当炒锅的温度达到140℃,完成干燥过程
[0044]
7、级配改性:干燥后的石膏粉通过针式磨改性,进行级配
[0045]
实施方法三:
[0046]
s1、拣选水洗:将纯度98%的蛋膏矿选出,用水冲去泥沙。
[0047]
s2、破碎:选出的石膏块先用颚式破碎机破碎至8mm,然后再用锤式破碎机粉磨至2mm以下,装入吨袋备用。
[0048]
s3、制浆诱导:在压力反应罐中按石膏重量加入水,浓度为150%,并在压力反应罐的盘管中通入加热的导热油,当水温达到70℃时,加入晶型诱导剂400
‑
800目的α
‑
高强熟石膏0.4%,然后加入已经破碎称重好的石膏粉原料,转速调到120rad/min。
[0049]
s4、恒压转晶:加入0.2%的转晶剂edta及其盐,密闭压力反应罐,恒温135℃,恒压0.35mpa的压力4h,当压力低于0.35mpa时,用螺杆压缩机产生的压力充入压力反应罐内,当压力高于0.35mpa时,通过泄压阀泄压,使压力一直维持在0.35mpa下转晶。
[0050]
s5、离心脱水:转晶完成后,通过泄压,泵送至盘式离心机内甩干,整个离心甩干过程中浆料温度不得低于70℃。
[0051]
s6、炒锅干燥:当离心脱水的浆料含水率降到15%以下,通过板链输送机输送到预热的炒锅中,进行干燥脱水,当炒锅的温度达到150℃,完成干燥过程
[0052]
s7、级配改性:干燥后的石膏粉通过球磨机改性,进行级配。
[0053]
本发明的有益效果是:1、选择纯度高的石膏作为原料,并进行拣选和冲洗,更大限度的去污除杂。对于石膏原料的细度做了详细的要求;
[0054]
2、在蒸煮转晶前加入超细的晶型诱导剂,便于分散石膏晶体的成核,防止晶体成长过大,避免造成晶格缺陷,因此强度损失小;
[0055]
3、生产制备时,用导热油对压力反应罐中的水加热,通过导热油的温度控制水温始终在135℃上下。一般情况下,当水温在135℃时,压力反应罐中的水蒸气压是不饱和蒸气压,压力都是低于0.35mpa的,本发明技术用螺杆压缩机对压力进行补偿,防止压力过小或过小,使压力反应罐中压力始终维持在0.35mpa。
[0056]
以上所述,仅为本发明的具体实施方式,但本发明的保护范围并不局限于此,任何不经过创造性劳动想到的变化或替换,都应涵盖在本发明的保护范围之内。因此,本发明的保护范围应该以权利要求书所限定的保护范围为准。