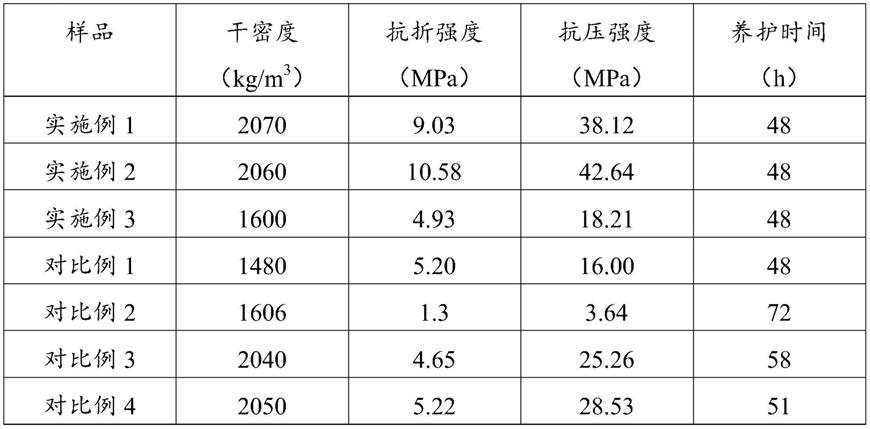
1.本发明涉及建筑材料技术领域,具体涉及一种混凝土砌块的制备方法及应用。
背景技术:2.砌块是工程建筑中的重要材料,目前市场上常用的砌块分为四大类,混凝土砌块、粉煤灰砌块、石膏砌块、复合砌块。而传统混凝土砌块具有质量重、价格高等缺点。
3.秸秆是成熟农作物茎叶(穗)部分的总称,通常指小麦、水稻、玉米、薯类、油菜、棉花、甘蔗或其它农作物在收获籽实后的剩余部分。秸秆是一种重要的生物资源,但目前很多秸秆资源未得到充分利用,部分地区甚至通过焚烧的方式进行处理,不仅是资源的浪费,还污染了环境。
4.现有技术中利用秸杆制备混凝土砌块,通常先将秸杆磨碎制成秸杆灰,再加入混凝土中,不仅制备工艺复杂,而且对砌块的抗折强度和抗压强度均产生较大的影响,且养护时间长。
技术实现要素:5.本发明提出一种混凝土砌块的制备方法及应用,以解决现有技术中存在的一个或多个技术问题,至少提供一种有益的选择或创造条件。
6.为克服上述技术问题,本发明采用的技术方案如下:
7.一种混凝土砌块的制备方法,包括以下步骤:
8.将秸杆加工成段至1
‑
3cm,加入碱性溶液中浸泡,经清洗、烘干后,制得预处理秸杆;
9.取海水、水泥和海砂混合,制得水泥砂浆;
10.将所述预处理秸杆和所述水泥砂浆混合,制得混合料;
11.将所述混合料经成型、养护后,制得混凝土砌块。
12.具体地,本发明通过将秸杆切成段,并控制切碎后的秸杆在1
‑
3cm长,利用其作为填充材料,既节省了秸杆的处理成本,也可在满足非承重结构构件强度要求的前提下利用更多的秸杆,更具环保价值。
13.将切成段后的秸杆加入碱性溶液中浸泡,碱性溶液可有效溶解秸杆纤维表面的蜡质层,该蜡质层不利于水泥的水化,经碱性溶液浸泡处理后的秸杆,有利于秸杆纤维与混凝土基体的粘合,同时有利于缓解秸杆对水泥水化的缓凝作用,从而提高混凝土砌块的抗压强度和抗折强度,并可缩短混凝土砌块的养护时间。
14.将经浸泡处理后的秸杆采用清水将秸杆表面的碱性溶液清洗,并将清洗后的秸杆烘干后,方完成了秸杆的预处理。
15.本发明水泥砂浆的主要原料为海水、水泥和海砂,在混合时同时添加减水剂,减水剂的作用主要是改善混凝土的流动性,使其结构更加稳定,提高强度,同时还能够保证在不改变混凝土强度的情况下,节省水泥的用量。
16.本发明的海水在使用前,无需进行淡化处理,因海水中少量的氯盐对砌体结构的影响较小,可省去高额的淡化处理成本。海砂在使用前,需进行振筛处理,以减少海砂中贝壳等对混凝土抗压强度的不利影响。
17.作为上述方案的进一步改进,所述海水、水泥和海砂的质量比为(0.25
‑
0.35):1:1。具体地,通过控制海水、水泥和海砂的质量比,可保障混凝土砌块的基本强度要求,过多或过少的海水加入,均不利于混凝土的成型与强度要求。
18.作为上述方案的进一步改进,所述预处理秸杆和所述水泥砂浆的质量比为(1
‑
4):100。具体地,选择加入合适重量比的预处理秸杆,可在保障混凝土砌块抗折强度和抗压强度的同时,达到轻质、隔热和保温的效果。
19.作为上述方案的进一步改进,所述碱性溶液选自氢氧化钠、氢氧化钾、氢氧化钙中至少一种。具体地,所述碱性溶液优选为强碱性溶液,采用强碱性溶液对秸杆进行浸泡处理,可使其更有效地将秸杆表面的蜡质层溶解完全,有利于秸杆纤维与混凝土基体的粘合,从而进一步提高砌砖的的强度,并减少养护时间。
20.作为上述方案的进一步改进,所述碱性溶液的浓度为2
‑
4%。具体地,选用合适浓度的碱性溶液,可保障去除秸杆表面蜡质层的同时,又不破坏除秸杆的纤维结构。
21.作为上述方案的进一步改进,所述碱性溶液浓度为3.5%,浸泡时间为12小时及以上。最少浸泡时间为12小时,足够的浸泡时间,可保障秸杆表面的蜡质层溶解完全。
22.作为上述方案的进一步改进,所述海砂的粒径为30
‑
60目。具体地,海砂的平均粒径相比河砂更细,但常含有少量的贝壳,因此,需在使用前对其进行振筛处理,并保证海砂可过30
‑
60目的筛。
23.作为上述方案的进一步改进,所述混合料成型采用模具成型。具体地,先选取一模具,并在模具内壁刷上一层润滑油,以防止混凝土与模具内壁的粘连,再将搅拌后的秸杆混凝土混合料装入模具中,并对混合料振捣并抹平表面,使其混合均匀。
24.作为上述方案的进一步改进,所述养护的步骤为:先在温度为18
‑
25℃、湿度为95%以上条件下养护24小时以上;然后在高温70
‑
80℃条件下养护24小时以上。
25.本发明还提供了一个技术方案是,采用上述混凝土砌块的制备方法制备的混凝土砌块在建筑领域的应用。尤其适用于建筑非承重墙的应用,非承重墙因不含钢筋,对氯盐及海砂细颗粒的影响较小,通过对海砂进行处理,减少海砂中贝壳等杂质对混凝土强度的不利影响,保证混凝土砌块的强度和耐久性要求。
26.本技术实施例提供的技术方案,至少具有如下技术效果或优点:
27.本发明合理利用秸秆资源和海水海砂资源,秸秆材料取材容易,成本低廉;海水、海砂资源丰富,本发明通过对海砂的净化处理,减少海砂中氯盐、贝壳等对混凝土的不利影响,达到可利用标准,保证混凝土砌块的强度、耐久性等。
28.相比于将秸秆磨碎成灰代替部分水泥及外加剂而大幅降低强度的现有技术,本发明通过将切段成1
‑
3cm的秸秆作为填充材料,既节省了秸秆处理成本,也能在达到非承重结构构件的强度要求的前提下,添加更多的秸秆,更具环保价值。同时,通过对秸秆进行碱性溶液浸泡处理,使其对拌合物之间的水化反应影响降低,增强了混凝土早期的强度,减小了养护时间。本发明制备的混凝土砌块,可满足作为非承重结构的基本强度要求,也达到了减轻砌块重量,并具有一定隔音隔热的效果。
具体实施方式
29.以下通过实施例对本发明进行具体描述,以便于所属技术领域的人员对本发明的理解,有必要在此特别指出的是,实施例只是用于对本发明做进一步说明,不能理解为对本发明保护范围的限制,所属领域技术人员,根据上述发明内容对本发明作出的非本质性的改进和调整,应仍属于本发明的保护范围,同时,下述所提及的原料未详细说明的,均为市售产品,未详细提及的工艺步骤或制备方法均为本领域技术人员所知晓的工艺步骤或制备方法。
30.实施例1
31.一种混凝土砌块,由以下材料构成:硅酸盐水泥0.75kg,海砂0.75kg,海水0.1655kg,聚羧酸减水剂(固含量为15%)0.053kg,秸秆掺量0.02kg,水胶比为0.28。
32.一种混凝土砌块的制备方法,包括以下步骤:
33.将秸杆加工成段至1cm,用质量分数为2%的氢氧化钠溶液浸泡秸秆48h后用清水冲洗,放置烘箱75℃烘干,48h后取出冷却,制得预处理秸杆;
34.将称量好的硅酸盐水泥和海砂干拌均匀后加入海水和聚羧酸减水剂,并充分搅拌,制得水泥砂浆;
35.将制得的预处理秸杆和水泥砂浆混合,并搅拌均匀,制得混合料;
36.将所述混合料装入40mm
×
40mm
×
160mm大小模具振捣并抹平表面成型,然后在温度为20℃,湿度为96%的条件下养护24h后,拆模并置于温度为70℃的烘箱养护24h。取出试样冷却,制得混凝土砌块。
37.实施例2
38.一种混凝土砌块,由以下材料构成:硅酸盐水泥0.75kg,海砂0.75kg,海水0.143kg,聚羧酸减水剂(固含量为15%)0.053kg,秸秆掺量0.03kg,水胶比为0.25。
39.一种混凝土砌块的制备方法,包括以下步骤:
40.将秸杆加工成段至1cm,用质量分数为4%的氢氧化钾溶液浸泡秸秆24h后用清水冲洗,放置烘箱80℃烘干,36h后取出冷却,制得预处理秸杆;
41.将称量好的硅酸盐水泥和海砂干拌均匀后加入海水和聚羧酸减水剂,并充分搅拌,制得水泥砂浆;
42.将制得的预处理秸杆和水泥砂浆混合,并搅拌均匀,制得混合料;
43.将所述混合料装入40mm
×
40mm
×
160mm大小模具振捣并抹平表面成型,然后在温度为25℃,湿度为96%的条件下养护24h后,拆模并置于温度为75℃的烘箱养护24h。取出试样冷却,制得混凝土砌块。
44.实施例3
45.一种混凝土砌块,由以下材料构成:硅酸盐水泥0.75kg,海砂0.75kg,海水0.2105kg,聚羧酸减水剂(固含量为15%)0.053kg,秸秆掺量0.02kg(用质量分数为4%的naoh溶液进行浸泡后烘干处理),水胶比为0.34。
46.一种混凝土砌块的制备方法,包括以下步骤:
47.将秸杆加工成段至1cm,用质量分数为3%的氢氧化钙溶液浸泡秸秆36h后用清水冲洗,放置烘箱75℃烘干,24h后取出冷却,制得预处理秸杆;
48.将称量好的硅酸盐水泥和海砂干拌均匀后加入海水和聚羧酸减水剂,并充分搅
拌,制得水泥砂浆;
49.将制得的预处理秸杆和水泥砂浆混合,并搅拌均匀,制得混合料;
50.将所述混合料装入40mm
×
40mm
×
160mm大小模具振捣并抹平表面成型,然后在温度为20℃,湿度为96%的条件下养护24h后,拆模并置于温度为70℃的烘箱养护24h。取出试样冷却,制得混凝土砌块。
51.对比例1
52.一种混凝土砌块,由以下材料构成:硅酸盐水泥0.75kg,海砂0.75kg,海水0.143kg,聚羧酸减水剂(固含量为15%)0.053kg,秸秆掺量0.03kg,水胶比为0.25。
53.一种混凝土砌块的制备方法,包括以下步骤:
54.将秸杆加工成段至1cm,制得预处理秸杆;
55.将称量好的硅酸盐水泥和海砂干拌均匀后加入海水和聚羧酸减水剂,并充分搅拌,制得水泥砂浆;
56.将制得的预处理秸杆和水泥砂浆混合,并搅拌均匀,制得混合料;
57.将所述混合料装入40mm
×
40mm
×
160mm大小模具振捣并抹平表面成型,然后在温度为20℃,湿度为96%的条件下养护24h后,拆模并置于温度为70℃的烘箱养护24h。取出试样冷却,制得混凝土砌块。
58.本对比例与实施例2的区别在于,秸杆仅进行成切段处理,未进行碱性溶液浸泡。
59.对比例2
60.一种海水海砂秸秆混凝土砌块,由以下材料构成:普通硅酸盐水泥0.75kg,海砂0.75kg,海水0.21kg,聚羧酸减水剂(固含量为15%)0.053kg,秸秆粉掺量0.04kg,水胶比为0.34。
61.一种混凝土砌块的制备方法,包括以下步骤:
62.将称量好的硅酸盐水泥和海砂干拌均匀后加入海水和聚羧酸减水剂,并充分搅拌,制得水泥砂浆;
63.将秸秆粉和水泥砂浆混合,并搅拌均匀,制得混合料;
64.将所述混合料装入40mm
×
40mm
×
160mm大小模具振捣并抹平表面成型,然后在温度为20℃,湿度为96%的条件下养护24h后,拆模并置于温度为70℃的烘箱养护48h。取出试样冷却,制得混凝土砌块。
65.本对比例与实施例2的最大区别在于,将秸杆加工成粉后作为填充材料添加。
66.对比例3
67.一种混凝土砌块,由以下材料构成:硅酸盐水泥0.75kg,海砂0.75kg,海水0.15kg,聚羧酸减水剂(固含量为15%)0.053kg,秸秆掺量0.025kg(用质量分数为4%的naoh溶液进行浸泡后烘干处理),水胶比为0.25。
68.一种混凝土砌块的制备方法,包括以下步骤:
69.将秸杆加工成段至0.5cm,用质量分数为3%的氢氧化钙溶液浸泡秸秆28h后用清水冲洗,放置烘箱75℃烘干,24h后取出冷却,制得预处理秸杆;
70.将称量好的硅酸盐水泥和海砂干拌均匀后加入海水和聚羧酸减水剂,并充分搅拌,制得水泥砂浆;
71.将制得的预处理秸杆和水泥砂浆混合,并搅拌均匀,制得混合料;
72.将所述混合料装入40mm
×
40mm
×
160mm大小模具振捣并抹平表面成型,然后在温度为20℃,湿度为96%的条件下养护28h后,拆模并置于温度为70℃的烘箱养护30h。取出试样冷却,制得混凝土砌块。
73.本对比例与实施例2的区别在于,秸杆加工成段至0.5cm
74.对比例4
75.一种混凝土砌块,由以下材料构成:硅酸盐水泥0.75kg,海砂0.75kg,海水0.15kg,聚羧酸减水剂(固含量为15%)0.053kg,秸秆掺量0.025kg(用质量分数为4%的naoh溶液进行浸泡后烘干处理),水胶比为0.25。
76.一种混凝土砌块的制备方法,包括以下步骤:
77.将秸杆加工成段至2cm,用质量分数为4%的氢氧化钠溶液浸泡秸秆18h后用清水冲洗,放置烘箱75℃烘干,28h后取出冷却,制得预处理秸杆;
78.将称量好的硅酸盐水泥和海砂干拌均匀后加入海水和聚羧酸减水剂,并充分搅拌,制得水泥砂浆;
79.将制得的预处理秸杆和水泥砂浆混合,并搅拌均匀,制得混合料;
80.将所述混合料装入40mm
×
40mm
×
160mm大小模具振捣并抹平表面成型,然后在温度为20℃,湿度为96%的条件下养护20h后,拆模并置于温度为70℃的烘箱养护31h。取出试样冷却,制得混凝土砌块。
81.本对比例与实施例2的区别在于,秸杆秸杆加工成段至2cm
82.性能测试
83.称量各实施例和对比例制得的混凝土砌块的质量并计算干密度,然后按照《水泥胶砂强度检测方法》(gb/t 17671
‑
1999)测定抗折强度和抗压强度。各实施例和对比例的干密度、测定抗折强度和抗压强度的值如下表1。
84.表1各实施例和对比例制得的混凝土性能参数对比表
[0085][0086]
从表1各实施例和对比例制得的混凝土砌块的性能参数可以看出:实施例1和2很好的说明了使用经强碱性溶液处理过的秸秆纤维制成的混凝土抗折和抗压强度明显优于未处理过秸秆制成的海砂秸秆混凝土。实施例3中由于水胶比相对较大,致使砌块干密度较小,但其抗折抗压强度低于实施例1和2,仍能满足非承重结构的强度要求。对比例1由于未
对秸秆纤维进行预处理,其实验强度相对实施例1明显降低,但能够基本满足抗折抗压强度要求。对比例2由于加入了秸秆粉末而非秸秆纤维,这是其未能满足非承重强度等级的最大原因。对比例3和4说明了在一定范围内改变秸秆的长度仍能满足砌块抗压强度的要求,但相较于将秸杆加工成段至1cm的抗压强度有所降低。
[0087]
显然,上述实施例仅是为清楚地说明所作的举例,而并非对实施方式的限定。对于所属领域的普通技术人员来说,在上述说明的基础上还可以做出其它不同形式的变化或变动。这里无需也无法对所有的实施方式予以穷举。而由此所引伸出的显而易见的变化或变动仍处于本发明的保护范围之中。