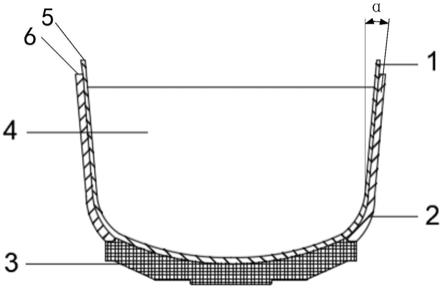
1.本实用新型一般涉及硅棒制备技术领域,具体涉及一种坩埚组合。
背景技术:2.为了应对未来化石能源的枯竭,全球各个国家已经开始重点发展光伏等可再生性能源。特别是近年来,单晶光伏行业得到了迅猛发展。单晶光伏首先需要将硅料融化,并通过引晶手段,将多晶硅料提炼成单晶硅棒。该环节的工作温度超过1400℃,同时工作区间充斥着大量的硅蒸汽。由于环境工况复杂,普通的耐高温材料很难持久工作,容易导致生产事故。
3.为了能持续的在高温环境下工作,以保证形成硅棒的拉晶工艺的顺利进行,采用复合结构的坩埚组合来对硅材料进行加热熔化。现有的复合结构的坩埚组合一般包括埚托,埚托上设置埚帮,埚帮内具有圆柱形的容腔,该容腔内设置外周面呈圆柱形的坩埚,坩埚的圆柱形外周面与埚帮的圆柱形内周面对应配合。
4.在工艺结束后,需要更换坩埚。由于埚帮一般为碳碳(carbon-carbon composite material;cc)埚帮,坩埚一般为石英坩埚,在上述较高的工作温度下,其会发生塑性形变,而紧紧的贴在cc埚帮上。在降温段,因为cc埚帮的热膨胀系数远大于石英坩埚的热膨胀系数,所以高温段膨胀的cc埚帮在冷却过程中,会受到内部石英坩埚的外撑作用。石英坩埚冷却至室温后,其变形也无法回到初始状态,这就导致cc埚帮被内部坩埚顶住,无法取下。现在的解决办法是,停炉降温后由员工手动重敲打石英坩埚,将其完全破坏,最后将cc埚帮取下。该过程一方面,耗时耗力,极难将cc埚帮取出;另一方面,由于需要重敲,则在敲打过程中也极有可能在埚帮上敲出裂纹,轻则影响cc埚帮寿命,重则引发生产事故。
技术实现要素:5.鉴于现有技术中的上述缺陷或不足,期望提供一种坩埚组合,用以解决现有技术中埚帮与坩埚不易分离,且易造成埚帮损坏,存在安全生产风险的问题。
6.本实用新型提供一种坩埚组合,包括:
7.埚托;
8.埚帮,设置于所述埚托上,所述埚帮具有自所述埚托向远离所述埚托方向逐渐增大的坩埚安装腔;
9.坩埚,设置于所述坩埚安装腔内,所述坩埚的外侧面为自所述埚托向远离所述埚托方向逐渐增大的外侧面,所述外侧面和所述坩埚安装腔的内侧面相对设置,且所述埚帮的软化温度大于所述坩埚的软化温度。
10.作为可实现的方式,所述埚帮的底部具有暴露所述埚托顶部的开口,所述坩埚的底部位于所述开口内,且所述坩埚的底部的下底面与所述埚托的顶面接触配合;或者,
11.所述埚帮的底部封闭,且支撑于所述埚托的顶面,所述埚帮的底部的上底面与所述坩埚的底部的下底面接触配合。
12.作为可实现的方式,所述坩埚安装腔的内侧面与所述坩埚的外侧面贴合配合或间隙配合。
13.作为可实现的方式,在所述坩埚安装腔的内侧面与所述坩埚的外侧面间隙配合的状态,所述坩埚安装腔的内侧面与所述坩埚的外侧面的间隙为d,且0mm<d≤4mm。
14.作为可实现的方式,所述坩埚安装腔为倒锥台形的坩埚安装腔,所述倒锥台的母线与其中心线的夹角为α,且1
°
≤α≤10
°
。
15.作为可实现的方式,所述坩埚的顶部高于所述埚帮的顶部。
16.作为可实现的方式,所述坩埚的壁厚为10mm-30mm和/或所述埚帮的壁厚为10mm-50mm。
17.作为可实现的方式,所述埚托的外周面为圆形,且其厚度大于20mm。
18.作为可实现的方式,所述埚托为碳碳埚托或石墨埚托;所述埚帮为碳碳埚帮或石墨埚帮;所述坩埚为石英坩埚或碳化硅坩埚。
19.作为可实现的方式,所述碳碳埚托及所述碳碳埚帮的密度为1.35g/cm3-1.5g/cm3;所述石墨埚托及所述石墨埚帮的密度为1.6g/cm3-2.33g/cm3。
20.本技术提供的上述方案,由于坩埚自所述埚托向远离所述埚托方向逐渐增大的外侧面对应于坩埚安装腔自所述埚托向远离所述埚托方向逐渐增大的内侧面,在拉晶工艺结束后,埚帮与坩埚降温收缩,坩埚的自所述埚托向远离所述埚托方向逐渐增大的外侧面与坩埚安装腔的自所述埚托向远离所述埚托方向逐渐增大的内侧面相贴合,坩埚的自所述埚托向远离所述埚托方向逐渐增大的外侧面受到坩埚安装腔的自所述埚托向远离所述埚托方向逐渐增大的内侧面垂直于坩埚自所述埚托向远离所述埚托方向逐渐增大的外侧面的正压力fn以及沿着坩埚自所述埚托向远离所述埚托方向逐渐增大的外侧面具有斜向下的摩擦力fs,那么在竖直方向y上坩埚受到一个向上的作用力σfy=fny-fsy,这样在埚帮及坩埚降温收缩的情况下,该作用力将使得坩埚向上运行,缓解埚帮与坩埚二者间的相互作用,避免二者出现抱死而无法分离的情况,因此不需要采用重敲的方式将二者进行敲击分离,可以避免重敲过程中造成埚帮损坏,存在安全生产风险的问题发生。
附图说明
21.通过阅读参照以下附图所作的对非限制性实施例所作的详细描述,本技术的其它特征、目的和优点将会变得更明显:
22.图1为本实用新型实施例提供的坩埚组合的结构示意图;
23.图2为本实用新型实施例提供的坩埚的结构示意图;
24.图3为本实用新型实施例提供的实施例提供的坩埚的受力示意图。
具体实施方式
25.下面结合附图和实施例对本技术作进一步的详细说明。可以理解的是,此处所描述的具体实施例仅仅用于解释相关实用新型,而非对该实用新型的限定。另外还需要说明的是,为了便于描述,附图中仅示出了与实用新型相关的部分。
26.需要说明的是,在不冲突的情况下,本技术中的实施例及实施例中的特征可以相互组合。下面将参考附图并结合实施例来详细说明本技术。
27.第一方面,如图1、图2所示,本实用新型实施例提供的坩埚组合,包括:
28.埚托3;使用时,埚托3放置在坩埚旋转托盘上,埚托3作为一个承托件,用于对埚帮2、坩埚1及坩埚1中所要放置的硅料4提供支撑的作用。坩埚旋转托盘带动埚托3旋转,埚帮2与坩埚1跟随埚托3同步旋转以进行拉晶作业。
29.埚帮2,设置于所述埚托3上,所述埚帮2具有自所述埚托向远离所述埚托方向逐渐增大的坩埚安装腔,且所述埚帮2的软化温度大于下述坩埚1的软化温度;埚帮2至少在轴向上对坩埚1起到支撑的作用,由于埚帮2的软化温度大于下述坩埚1的软化温度,可以防止坩埚1在高温环境时,因软化而导致内部的硅材料外流。
30.本文所指的自所述埚托向远离所述埚托方向逐渐增大是指小端向下,大端向上的结构,自所述埚托向远离所述埚托方向逐渐增大结构的侧边的斜率可以是线性的也可以是非线性的,在为线性的情况下,自所述埚托向远离所述埚托方向逐渐增大结构的侧边为直线,此时自所述埚托向远离所述埚托方向逐渐增大的结构为倒锥台,倒锥台是指小端向下,大端向上的锥台,锥台指的是圆锥或棱锥被两个平行平面所截后,位于两个平行平面之间的立体,也即这里的锥台可以是多棱的锥台,也可以是圆台;在为非线性的情况下,自所述埚托向远离所述埚托方向逐渐增大结构的侧边为弧线或椭圆弧线等;软化温度是指部件因受热发生塑性形变时的温度。
31.坩埚1,设置于所述坩埚安装腔内,所述坩埚1的外侧面为自所述埚托向远离所述埚托方向逐渐增大的外侧面201,所述外侧面201和所述坩埚安装腔的内侧面相对设置,也即坩埚1与埚帮2是通过自所述埚托向远离所述埚托方向逐渐增大的结构形式进行插套配合的。一般地,坩埚1的底部为弧形底部203,该弧形底部203通过弧形过渡段202与所述外侧面201进行平滑的连接。
32.本技术提供的上述方案,由于坩埚自所述埚托向远离所述埚托方向逐渐增大的外侧面201对应于坩埚安装腔的自所述埚托向远离所述埚托方向逐渐增大的内侧面,在拉晶工艺结束后,埚帮2与坩埚1降温收缩,坩埚1的自所述埚托向远离所述埚托方向逐渐增大的外侧面201与埚帮2的自所述埚托向远离所述埚托方向逐渐增大的内侧面相贴合,如图3所示,坩埚1的自所述埚托向远离所述埚托方向逐渐增大的外侧面201受到坩埚安装腔的自所述埚托向远离所述埚托方向逐渐增大的内侧面垂直于坩埚1的自所述埚托向远离所述埚托方向逐渐增大的外侧面201的正压力fn以及沿着坩埚1的自所述埚托向远离所述埚托方向逐渐增大的外侧面201具有斜向下的摩擦力fs,那么在竖直方向y上坩埚1受到一个向上的作用力σfy=fny-fsy,这样在埚帮2及坩埚1降温收缩的情况下,该作用力将使得坩埚1向上运行,缓解埚帮2与坩埚1二者间的相互作用,避免二者出现抱死而无法分离的情况,因此不需要采用重敲的方式将二者进行敲击分离,可以避免重敲过程中造成埚帮2损坏,存在安全生产风险的问题发生。
33.作为可实现的方式,所述埚帮2的底部具有暴露所述埚托3顶部的开口,所述坩埚1的底部位于所述开口内,且所述坩埚1的底部的下底面与所述埚托3的顶面接触配合,采用此种结构,埚帮2的底部是开放的,也即具有开口,利于在分离坩埚1时,将埚帮2倒放,即自所述埚托向远离所述埚托方向逐渐增大结构的小径端向上,在该开口内向下轻敲坩埚1,使坩埚1与埚帮2分离;或者,
34.所述埚帮2的底部封闭,且支撑于所述埚托3的顶面,所述埚帮2的底部的上底面与
所述坩埚1的底部的下底面接触配合。
35.作为可实现的方式,所述坩埚安装腔的侧面与所述坩埚1的外侧面贴合配合或间隙配合。一般优选坩埚安装腔的内侧面与坩埚1的外侧面间隙配合的方式,以利于将坩埚1装配到埚帮2内。
36.作为可实现的方式,在所述坩埚安装腔的内侧面与所述坩埚1的外侧面间隙配合的状态,所述坩埚安装腔的内侧面与所述坩埚1的外侧面的间隙为d,且0mm<d≤4mm。采用此间隙,既保证了坩埚1较便利的装配到埚帮2内,还可以保证在工作时,坩埚1发生较小的形变后即可贴合到埚帮2的内侧面上,由埚帮2对坩埚1的侧面起到较好的支撑作用,防止坩埚1软化变形而造成坩埚1内的硅材料外流。
37.作为可实现的方式,所述坩埚安装腔为倒锥台形的坩埚安装腔,所述倒锥台的母线与其中心线的夹角为α,且1
°
≤α≤10
°
。相应地,坩埚1的自所述埚托向远离所述埚托方向逐渐增大的外侧面201与其中心线的夹角为θ,且1
°
≤θ≤10
°
。采用此角度即可保证埚帮2与坩埚1较易的分离,又可避免角度过大时,埚帮2受到较大的向下的分力而造成埚帮2应力过大而损坏。
38.作为可实现的方式,所述坩埚1的顶部5高于所述埚帮2的顶部6,以防止在拉晶工作时,埚帮2的材料因处于高温环境下而造成脱落,掉落进坩埚1内而影响硅棒纯度的问题发生。
39.作为可实现的方式,所述坩埚1的壁厚为10mm-30mm和/或所述埚帮2的壁厚为10mm-50mm,使得坩埚1、埚帮2在满足必要的力学性能的情况下,尽量的降低制作坩埚1、埚帮2所使用的材料,以降低坩埚1、埚帮2的生产成本。
40.作为可实现的方式,所述埚托3的外周面为圆形,且其厚度大于20mm。
41.作为可实现的方式,所述埚托3为碳碳埚托或石墨埚托;所述埚帮2为碳碳埚帮或石墨埚帮;所述坩埚1为石英坩埚或碳化硅坩埚。
42.埚托3及埚帮2优选采用碳碳材质制作,即采用碳碳埚托及碳碳埚帮。采用碳碳材质,即可保证埚托3及埚帮2在高温条件下(例如大于1000℃)具有较佳的力学性能,同时,还具有较好的导热性能和较低的热膨胀性。
43.作为可实现的方式,所述碳碳埚托及所述碳碳埚帮的密度为1.35g/cm3-1.5g/cm3;所述石墨埚托及所述石墨埚帮的密度为1.6g/cm3-2.33g/cm3。采用上述的密度范围,既可以保证埚帮2及埚托3具有足够的强度,又可以满足其具有一定的经济性。过高的密度会带来成本的显著提高,但是其所对应的强度的提高已超出了本方案对强度的要求,因此,在上述密度范围内即满足了强度要求,又满足了经济性要求,利于产业化应用。
44.需要理解的是,上文如有涉及术语“中心”、“纵向”、“横向”、“上”、“下”、“前”、“后”、“左”、“右”、“竖直”、“水平”、“顶”、“底”、“内”、“外”等指示的方位或位置关系为基于附图所示的方位或位置关系,仅是为了便于描述本实用新型和简化描述,而不是指示或暗示所指的装置或元件必须具有特定的方位、以特定的方位构造和操作,因此不能理解为对本实用新型的限制。此外,术语“第一”、“第二”仅用于描述目的,而不能理解为指示或暗示相对重要性或者隐含指明所指示的技术特征的数量。由此,限定有“第一”、“第二”的特征可以明示或者隐含地包括一个或者更多个该特征。在本实用新型的描述中,除非另有说明,“多个”的含义是两个或两个以上。
45.以上描述仅为本技术的较佳实施例以及对所运用技术原理的说明。本领域技术人员应当理解,本技术中所涉及的实用新型范围,并不限于上述技术特征的特定组合而成的技术方案,同时也应涵盖在不脱离所述发明构思的情况下,由上述技术特征或其等同特征进行任意组合而形成的其它技术方案。例如上述特征与本技术中公开的(但不限于)具有类似功能的技术特征进行互相替换而形成的技术方案。