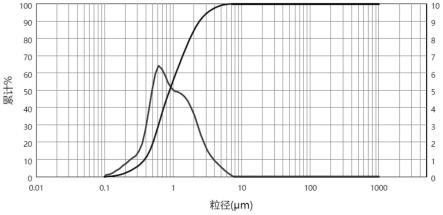
1.本发明涉及一种玻璃预处理液,主要是电子设备的玻璃屏膜预处理液。
背景技术:2.随着5g与柔性显示技术的迅速铺展,可折叠手机及其他便携式穿戴显示设备将迎来消费高潮。仅30至50um厚的超薄柔性玻璃utg(ultra thin glass)以其可折叠、柔韧性好,并具有光滑手感和良好均匀度的特点将成为未来盖板玻璃的完美解决方案。
3.超薄柔性玻璃utg(ultra thin glass)的出现将对减薄处理技术及工艺提出巨大挑战。目前,以氢氟酸为主料的兼顾经济性与效率性的化学湿式蚀刻仍为玻璃显示基板减薄处理的主流。然而,具有强腐蚀性的氢氟酸对于玻璃的各向同性腐蚀会严重放大玻璃基板原材凹点、划伤等缺陷,从而导致表观不良,只能通过后续研磨抛光修复。面对去除速率仅0.5至0.7um/min的研磨抛光工序,目前国内减薄厂商只能通过大量添加抛光设备来弥补整个减薄工序的效率降低,在增加设备成本的同时,人工成本、抛光辅料成本及抛光废料环境成本也急剧增加。
4.对于这一减薄工序中的
‘
短板效应’,目前减薄厂商通过来料玻璃基板研磨抛光或化学湿法预处理的方式来解决。来料玻璃基板研磨抛光仅是将原有部分后续研磨抛光前置于减薄主蚀刻工序之前,增加了制程成本,是一种折中方案。来料玻璃基板化学湿法预处理是通过化学的方式减小或修复来料凹陷、划伤等缺陷,具有明显的经济与效率优势,但技术门槛高。
5.目前,以氢氟酸为主料的兼顾经济性与效率性的化学湿式蚀刻仍为玻璃显示面板减薄处理的主流。然而,具有强腐蚀性的氢氟酸对于玻璃的各向同性腐蚀会严重放大未处理的玻璃基板凹点、划伤等缺陷,从而导致表观不良,只能通过后续研磨抛光修复。面对去除速率仅0.5至0.7um/min的研磨抛光工序,目前国内减薄厂商只能通过大量添加抛光设备来弥补整个减薄工序的效率降低,在增加设备成本的同时,人工成本、抛光辅料成本及抛光废料环境成本也急剧增加。化学湿法预处理均是使用低氢氟酸含量药液对玻璃基材进行微蚀,通过使用浓硫酸或其他化学品提高体系密度及粘度,抑制缺陷位点的各向同性蚀刻,进而消除或减小缺陷尺寸。此种方案缺点明显:抑制缺陷效果差;高密度粘度体系导致流体传质不均,从而导致大面板基材板厚差波动大;浓硫酸体系中氢氟酸挥发严重,操作环境恶劣;含氟废液污染严重。
技术实现要素:6.为了解决了传统氢氟酸体系预处理液对玻璃基材细微缺陷抑制效果差、制程中玻璃面板板厚差波动严重以及预处理高氟废液污染等问题。
7.为了解决现有玻璃化学湿法预处理技术中存在的缺点,首先本发明提供了一种采用微乳颗粒选择性填充玻璃基板微米级缺陷的方案。
8.其次,本发明提供了一种基于上述方案的新型无氟高效玻璃预处理液制备方法。
9.最后,本发明提供了上述预处理液的使用方法。
10.一种采用微乳颗粒选择性填充玻璃基板微米级缺陷的方案,包括以下五个重要步骤:
11.1.对氢氟酸具有惰性的物质颗粒的微米级稳定分散;
12.2.上述颗粒选择性进入玻璃基材微米级缺陷;
13.3.玻璃平整面残留保护颗粒的去除;
14.4.进入玻璃基材缺陷的保护颗粒破乳以及稳定粘附;
15.5.在含氢氟酸主蚀刻过程中,保护颗粒缓慢脱附及分解。
16.基于上述方案的新型无氟高效玻璃预处理液制备方法如下:所述的无氟微乳原液包括界面保护剂、乳化剂、渗透剂、ph调节剂及增溶剂。该组合物中的界面保护剂以水包油型微乳颗粒形式存在,状态稳定,使得预处理液的储存周期长,未开缸的原液在常温密封的条件下储存期在6个月以上。
17.无氟微乳型玻璃预处理液成分组成(质量比)如下:
18.界面保护剂 烷基聚甲基硅氧烷 12-25%;
19.2-丙烯酸甲酯均聚物 4-10%;
20.白炭黑 10-15%
21.乳化剂 异构十醇烷氧基化物 5-15%;
22.异构十三醇聚氧乙烯醚 2-8%
23.渗透剂 脂肪醇与环氧乙烷缩合物 1-5%
24.ph调节剂 三乙醇胺 1-8%;
25.二乙醇胺 1-5%
26.增溶剂 氢化蓖麻油聚氧乙烯醚 1-5%
27.去离子水 40-62%;
28.配制方法如下:
29.a.称取比例质量份界面保护剂,升温至55-85℃,使用均质机搅拌混合均匀;
30.b.向上述搅拌混合均匀界面保护剂中加入配比质量份乳化剂,搅拌混合均匀;
31.c.向上述搅拌混合均匀体系中加入配比质量份渗透剂,搅拌混合均匀;
32.d.向上述搅拌混合均匀体系中加入配比质量份去离子水,搅拌混合均匀;
33.e.向上述搅拌混合均匀体系中加入配比质量份ph调节剂,搅拌混合均匀;
34.f.上述搅拌混合均匀体系中加入配比质量份增溶剂,搅拌混合均匀。
35.【有益效果】
36.与传统的使用氢氟酸作为蚀刻剂,浓硫酸或其他化学品提高体系密度及粘度,抑制缺陷位点的各向同性蚀刻,进而消除或减小缺陷尺寸的化学湿法预处理液相比,本发明采用纳米及微米级惰性颗粒选择性填充及覆盖玻璃基板细微缺陷和划痕,充分保护基板细微缺陷的同时,摒弃氢氟酸或其他含氟物质,药液耗费量极少,安全环保;无浓硫酸或其他增粘成分,体系传质效率高,解决了传统预处理制程中造成板厚差的难题;同时,使用过程中,无氢氟酸或其他有害物质挥发,无刺激性气味,操作环境大为改善。
附图说明
37.图1为玻璃预处理液工作液乳液颗粒分布;
38.图2为无预处理与预处理液处理后玻璃基材缺陷形貌对比;
39.图3为无预处理与预处理液处理后玻璃基材缺陷尺寸对比;
40.图4.为传统浓硫酸体系预处理液与实例预处理液处理后主蚀刻玻璃基材缺陷尺寸对比。
具体实施方式
41.实施例1
42.a.称取配比质量份烷基聚甲基硅氧烷、2-丙烯酸甲酯均聚物、白炭黑,质量分数分别为12.5%、6%及白炭黑12.5%,升温至75℃,使用均质机搅拌混合均匀;
43.b.向上述搅拌混合均匀体系中加入配比质量份异构十醇烷氧基化物,质量分数5.5%,搅拌混合均匀;
44.c.向上述搅拌混合均匀体系中加入配比质量份异构十三醇聚氧乙烯醚,质量分数3.5%,搅拌混合均匀;
45.d.向上述搅拌混合均匀体系中加入配比质量份脂肪醇与环氧乙烷缩合物,质量分数2%,搅拌混合均匀;
46.e.向上述搅拌混合均匀体系中加入配比质量份去离子水,质量分数55.5%,搅拌混合均匀;
47.f.向上述搅拌混合均匀体系中加入配比质量份三乙醇胺,质量分数2%,搅拌混合均匀;
48.g.上述搅拌混合均匀体系中加入氢化蓖麻油聚氧乙烯醚,质量分数1.5%,搅拌混合均匀。
49.实施例2
50.a.称取配比质量份烷基聚甲基硅氧烷、白炭黑,质量分数分别为21%、10%,升温至75℃,使用均质机搅拌混合均匀;
51.b.向上述搅拌混合均匀体系中加入配比质量份异构十醇烷氧基化物,质量分数7.5%,搅拌混合均匀;
52.c.向上述搅拌混合均匀体系中加入配比质量份异构十三醇聚氧乙烯醚,质量分数4.5%,搅拌混合均匀;
53.d.向上述搅拌混合均匀体系中加入配比质量份脂肪醇与环氧乙烷缩合物,质量分数2%,搅拌混合均匀;
54.e.向上述搅拌混合均匀体系中加入配比质量份去离子水,质量分数51.5%,搅拌混合均匀;
55.f.向上述搅拌混合均匀体系中加入配比质量份三乙醇胺,质量分数2%,搅拌混合均匀;
56.g.上述搅拌混合均匀体系中加入氢化蓖麻油聚氧乙烯醚,质量分数1.5%,搅拌混合均匀。
57.实施例3
58.a.称取配比质量份烷基聚甲基硅氧烷、2-丙烯酸甲酯均聚物、白炭黑,质量分数分别为12%、8%及白炭黑13%,升温至75℃,使用均质机搅拌混合均匀;
59.b.向上述搅拌混合均匀体系中加入配比质量份异构十醇烷氧基化物,质量分数6.5%,搅拌混合均匀;
60.c.向上述搅拌混合均匀体系中加入配比质量份异构十三醇聚氧乙烯醚,质量分数5.5%,搅拌混合均匀;
61.d.向上述搅拌混合均匀体系中加入配比质量份脂肪醇与环氧乙烷缩合物,质量分数2%,搅拌混合均匀;
62.e.向上述搅拌混合均匀体系中加入配比质量份去离子水,质量分数49%,搅拌混合均匀;
63.f.向上述搅拌混合均匀体系中加入配比质量份二乙醇胺,质量分数2.5%,搅拌混合均匀;
64.g.上述搅拌混合均匀体系中加入氢化蓖麻油聚氧乙烯醚,质量分数1.5%,搅拌混合均匀。
65.基于上述预处理液的使用方法如下:
66.a.将上述预处理液以1:9质量比加入35-40℃去离子水中,搅拌均匀;
67.b.将人为打点缺陷(缺陷平均尺寸为24um)的高硼铝玻璃基板浸入上述38℃开稀后玻璃预处理工作液中,充分鼓泡10分钟;
68.c.将上述玻璃基材取出,浸入室温(25℃)去离子水中慢拉10秒出水;
69.d.将上述玻璃基材取出,浸入10%氢氟酸水溶液,室温,鼓泡,分别蚀刻2分钟、5分钟、10分钟、30分钟、60分钟及105分钟;
70.e.将上述玻璃基材取出,浸入室温(25℃)去离子水中鼓泡清洗30秒;
71.f.将上述玻璃基材取出,浸入室温(25℃)去离子水中慢拉20秒出水;
72.g.将上述玻璃基材取出,55℃热风吹干。
73.对比实验组,玻璃基材不进行预处理,处理方法如下:
74.a.将玻璃基材浸入38℃去离子水中,充分鼓泡10分钟;
75.b.将上述玻璃基材取出,浸入10%氢氟酸水溶液,室温,鼓泡,分别蚀刻2分钟、5分钟、10分钟、30分钟、60分钟及105分钟;
76.c.将上述玻璃基材(同样如上人为打点)取出,浸入室温(25℃)去离子水中鼓泡清洗30秒;
77.d.将上述玻璃基材取出,浸入室温(25℃)去离子水中慢拉20秒出水;
78.e.将上述玻璃基材取出,55℃热风吹干。
79.以上述实例1为例,玻璃预处理工作液中微乳颗粒分布结果如图1所示,可以看出微乳颗粒粒径主要分布于0.1至10um,平均粒径为1.2um,d50=0.88um,证明微乳颗粒进入尺寸为24um以上的玻璃基板缺陷空间尺寸可行。
80.未处理玻璃基材与无氟微乳型玻璃预处理液处理后基材,10%氢氟酸水溶液室温蚀刻过程中缺陷形貌改变如图2所示,图2为无预处理与实施例1中的预处理液处理后玻璃基材缺陷形貌对比结果,无预处理样品经10%氢氟酸水溶液蚀刻2分钟,缺陷处出现明显各向同性腐蚀,缺陷边缘呈圆弧形;30分钟后,缺陷形貌即变为圆形。经过预处理液处理,2分
钟后样品缺陷仍呈现尖锐裂缝,说明此处各向同性腐蚀不明显,预处理液中界面保护活性成分发挥作用;5分钟后缺陷处有少量雾状物质出现,即界面保护活性成分脱除,直至30分钟达到最大脱除量;60分钟后界面保护活性成分未见,说明预处理液中界面保护活性成分随氢氟酸水溶液纵向腐蚀玻璃已脱除或分解完毕。
81.图3为无预处理与预处理液处理后玻璃基材缺陷尺寸对比结果,无预处理玻璃基材原始缺陷尺寸为24um,于10%氢氟酸水溶液中蚀刻105分钟,缺陷尺寸扩大至150um;经过玻璃预处理液处理后,相同蚀刻条件,缺陷尺寸控制在75um,效果显著。
82.以上数据旨在揭示无氟微乳预处理液工作原理。
83.为对比传统浓硫酸体系预处理液,安排以下测试:
84.a.将上述预处理液以1:9质量比加入35-40℃去离子水中,搅拌均匀;
85.b.将人为打点缺陷(缺陷平均尺寸为18.5um/23.5um/30um/35.5um)的高硼铝玻璃基板浸入上述38℃开稀后玻璃预处理工作液中,充分鼓泡30分钟;
86.c.将上述玻璃基材取出,浸入室温(25℃)去离子水中慢拉10秒出水;
87.d.将上述玻璃基材取出,浸入10%氢氟酸水溶液,室温,鼓泡,蚀刻105分钟;
88.e.将上述玻璃基材取出,浸入室温(25℃)去离子水中鼓泡清洗30秒;
89.f.将上述玻璃基材取出,浸入室温(25℃)去离子水中慢拉20秒出水;
90.将上述玻璃基材取出,55℃热风吹干。
91.采用76%(质量比)浓硫酸加4.2%(质量比)氢氟酸作为对比样的浓硫酸体系预处理液,将上述b步骤更改为室温(25℃)原液充分鼓泡30分钟,后续c-f步骤与上述方法一致。
92.传统浓硫酸体系预处理液与实例预处理液处理后主蚀刻玻璃基材缺陷尺寸对比结果如图4所示,可明显发现实例1至3方案预处理后,其表面缺陷抑制效果明显优于传统方案。对于较小缺陷(18.5um以下),实例方案均可消除,而传统方案将其缺陷放大4倍;对于较大缺陷(35.5um以上),实例方案可将缺陷尺寸有效控制在2倍以内,而传统方案将其缺陷放大近4倍。